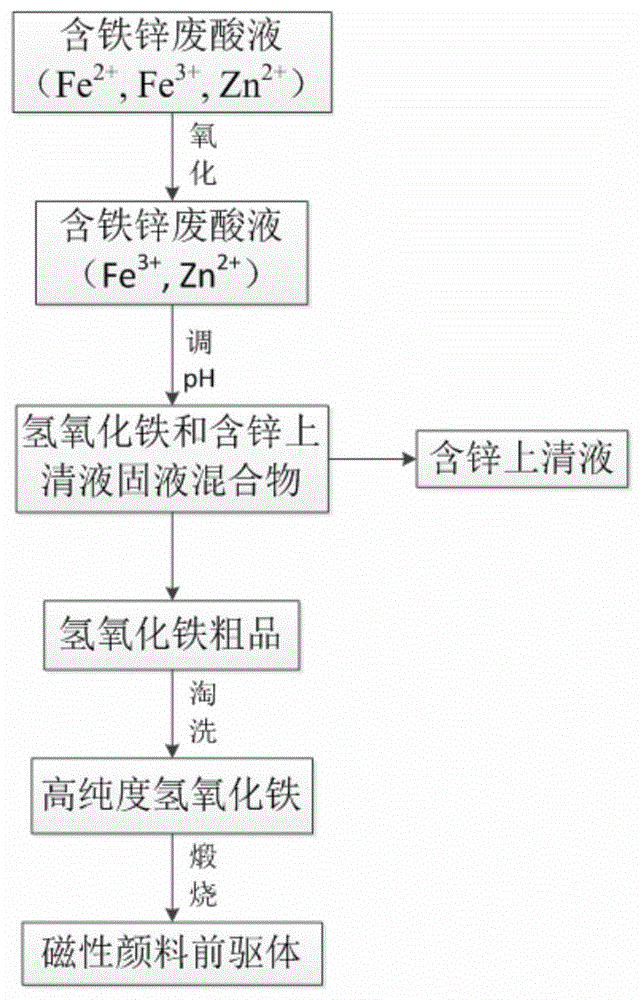
本发明涉及一种含铁锌废酸液的处理工艺,特别是涉及一种含铁锌废酸液的除锌提纯工艺,应用于工业废酸液处理及资源回收利用
技术领域:
。
背景技术:
:目前我国钢铁产量居世界首位,在中国制造2025规划中,特殊钢铁制造依旧将成为推动制造业发展的中坚力量。钢铁锻造的冷轧过程中,需要对产品的表面氧化物进行处理,大多数企业会采用盐酸对金属表面的油污和氧化物反复冲洗以去除杂质。而但盐酸中的金属离子浓度超出酸洗液中金属离子浓度要求时,就将含金属离子的废酸液弃用成为污染物。目前国内外针对含铁锌废液主要采取以下几种方法:一是许多中小企业采用投加石灰等碱性药剂去中和游离酸并沉淀金属离子的方法处理废酸液,这种方法工艺简单,成本低廉,但是管理繁琐,不易控制,容易产生大量含重金属泥渣,后续处理处置困难且耗费高,并且在此过程中废酸液中的多种重金属未得到有效利用,资源浪费明显。二是采用蒸馏蒸发技术,得到低浓度盐酸再浓缩后回用,但该方法无法回收金属盐,并且残留的金属盐混合残渣只能作为危险废物处理。三是利用废酸液进行聚合反应得到聚合氯化铁,聚合硫酸氯化铁等净水剂再次使用,但由于国家对水处理药剂标准的提升,这一类净水剂中含有的其它金属杂质,如锌、铅等,使其难以获得市场和政府的认可。四是高温喷雾焙烧工艺,酸和铁的回收率都较高,但操作条件苛刻,建设运营成本高,经济适用性差。公开号为cn107265513a的专利文献公开了利用钛白废酸液制备氧化铁红的方法,虽然锌与钛、铝、钒等与铁的物化性质类似,但锌的处理分离资源化难度更大,这限制了含铁锌废酸液的回收再利用,也增加了环境的负担。经调查发现,制备颜料前驱体的方法主要有湿法空气氧化法、苯胺法、直接氧化法、氢氧化亚铁氧化法以及干法铁红法,湿法铁红法等。其中干法铁红法对煅烧原料锌残留量要求较高,锌的残余量直接影响干法铁红的品质和颜料前驱体的用途;而其他方法制备的颜料前驱体质量也不理想。技术实现要素:为了解决现有技术问题,本发明的目的在于克服已有技术存在的不足,提供一种利用含铁锌废酸液制备磁性颜料前驱体的方法,得到的磁性颜料前驱体纯度高,品质好,能作为化工颜料生产的原材料,在减少环境污染的同时,达到了变废为宝,节约了资源,进一步提高了热镀锌厂等的产品附加值,为利用含铁锌废酸液制备磁性颜料前驱体的方法产业化提供了保证,提高含铁锌废酸液资源化能力和水平。为达到上述目的,本发明创造采用如下发明构思:因含铁锌废酸液含有大量铁离子和锌离子,直接干化得到的固体沉淀物由于大量锌的存在,会导致制备磁性颜料前驱体困难且磁性颜料前驱体的品质下降。所以需要对废酸液进行处理得到高纯度氢氧化铁沉淀。利用含铁锌废酸液制备磁性颜料前驱体时,使用了煅烧工艺,对煅烧原料锌残留量要求较高,因此需要进行多级处理,来降低锌的含量。本发明通过对含铁锌废酸液预处理得到含锌量极低的氢氧化铁沉淀,对制备的铁产物进行逐级提纯,并对铁产物进行逐级降锌,再通过湿法提纯结合固相反应,对氢氧化铁沉淀高温煅烧处理,得到磁性颜料前驱体。将含铁锌废酸液转化为有利用价值化工原材料产品,同时消除了废酸液的酸危害以及重金属对环境和生态的破坏。本发明操作过程方便易行,适用于工业化生产;得到的资源化产品可以作为化工颜料生产的原材料,在减少环境污染的同时,达到了变废为宝,节约了资源,降低生产成本的目的,提高了热镀锌厂等的产品附加值,为产业化提供了保证。根据上述发明构思,本发明采用如下技术方案:一种利用含铁锌废酸液制备磁性颜料前驱体的方法,对制备的铁产物进行逐级提纯,并对铁产物进行逐级降锌,通过湿法提纯结合固相反应,制备磁性颜料前驱体,包括如下步骤:a.预处理:采用氧化剂,将待处理的含铁锌废酸液中的二价铁全部氧化成三价铁,得到三价铁锌废酸液,待后续处理;b.铁离子沉淀工艺:向在步骤a中制备所得的含三价铁锌废酸液中投加碱性物质,并调节三价铁锌废酸液的ph为3.5-5.0,使得三价铁锌废酸液中的三价铁离子完全生成沉淀物,得固液混合物,然后进行固液分离,得到粗氢氧化铁沉淀;优选粗氢氧化铁沉淀的锌含量不低于1%;进行固液分离的方法优选采用抽滤、压滤及离心中至少一种;c.氢氧化铁沉淀纯化工艺:采用ph为4.0-5.0的酸性水溶液,对在所述步骤b中所得到的粗氢氧化铁沉淀进行洗涤,并进行固液分离;d.继续至少重复1次所述步骤c的氢氧化铁沉淀纯化工艺操作,得到高纯度氢氧化铁,进行干燥,得到高纯度氢氧化铁粉料;优选高纯度氢氧化铁的锌含量低于1%;e.煅烧处理:将在所述步骤d中得到的高纯度氢氧化铁粉料置入煅烧炉中,进行高温煅烧处理,发生固相化学反应,得到固体煅烧产物,然后将固体煅烧产物磨成粉末,得到磁性颜料前驱体。在进行高温煅烧处理时,优选控制煅烧温度为80–800℃,优选控制煅烧时间为0.5-2h。优选得到磁性颜料前驱体为氧化铁红和氧化铁黄中至少一种。上述煅烧炉优选采用马弗炉或回转窑。在所述步骤a中,上述氧化剂优选采用h2o2、na2s2o8、naclo、naclo3中至少一种。在所述步骤b中,上述碱性物质优选采用naoh、ca(oh)2、koh、氨水、生石灰中至少一种碱剂材料。在所述步骤c中,上述酸性水溶液优选采用由盐酸、硝酸和硫酸中至少一种酸剂与蒸馏水配制的ph为4.0-5.0的酸性液体。本发明方法向含铁锌废酸液中投加氧化剂使二价铁全部氧化为三价铁;再添加碱液调节含铁锌废酸液的ph至3.5-5.0,使得三价铁沉淀完全,而锌离子仍留在液体中;为进一步去除氢氧化铁固体间隙中的锌,采用ph为4.0-4.5的酸洗水溶液反复冲洗氢氧化铁固体并固液分离,多次重复操作,从而得到高纯度氢氧化铁原料。然后将处理得到的氢氧化铁沉淀置于马弗炉中,在80-800℃条件下煅烧0.5-2h。煅烧得到的固体物磨成粉末后即为磁性颜料前驱体。此外,本发明方法预处理方法得到高纯度氢氧化铁沉淀物还能作为原料再制备净水剂中使用。本方法利用含铁锌废酸液制备磁性颜料前驱体,处理了废酸液这种危险废物外还将其转化为可供利用的原材料。本发明与现有技术相比较,具有如下显而易见的突出实质性特点和显著优点:1.本发明方法采用本发明方法预处理方法得到高纯度氢氧化铁沉淀物,能作为制备磁性颜料前驱体的原料,也使得到高纯度氢氧化铁沉淀物作为铁矿物直接回收利用;2.本发明通过多级降锌,使氢氧化铁的纯度显著提高,为制备高品质磁性颜料前驱体提高有效保证;此外,通过对制备的铁产物进行逐级提纯,并对铁产物进行逐级降锌,再通过湿法提纯结合固相反应,有效地降解工业废酸液,实现废弃物资源化;3.本发明方法工艺简单,控制和操作便捷,易于推广应用。附图说明图1为本发明各实施例方法的工艺流程图。图2为本发明实施例一方法的煅烧产物x射线衍射图谱。图3为本发明实施例二方法的煅烧产物x射线衍射图谱。图4为本发明实施例三方法的煅烧产物x射线衍射图谱。图5为本发明实施例四方法的煅烧产物x射线衍射图谱。具体实施方式以下结合具体的实施例子对上述方案做进一步说明,本发明的优选实施例详述如下:实施例一:在本实施例中,参见图1,一种含铁锌废酸液成分如表1所示,待处理的含铁锌废酸液:表1.实施例一含铁锌废酸液成分一览表(浓度单位:mg/l)组分fe2+zn2+fe3+nihcl浓度13000021000100010030000在本实施例中,一种利用本实施例含铁锌废酸液制备磁性颜料前驱体的方法,对制备的铁产物进行逐级提纯,并对铁产物进行逐级降锌,通过湿法提纯结合固相反应,制备磁性颜料前驱体,包括如下步骤:a.预处理:采用naclo3作为氧化剂,向含铁锌废酸液中加入足量naclo3,将待处理的含铁锌废酸液中的二价铁全部氧化成三价铁,得到预处理后的三价铁锌废酸液,待后续处理;b.铁离子沉淀工艺:向在步骤a中制备所得的含三价铁锌废酸液中缓慢滴加naoh溶液,并调节三价铁锌废酸液的ph为3.5-5.0,使得三价铁锌废酸液中的三价铁离子完全生成沉淀物,得固液混合物,然后将所得固液混合物放入离心机中离心,分离得到上清液和粗氢氧化铁沉淀,其中粗氢氧化铁沉淀的锌含量不低于1%;c.氢氧化铁沉淀纯化工艺:采用ph为4.0-5.0的酸性水溶液,将在所述步骤b中所得到的粗氢氧化铁沉淀取出置于烧杯中,向烧杯中加入与在所述步骤b中所得上清液等量的ph为4.0-5.0的盐酸酸性水溶液,搅拌均匀,再次固液分离;d.继续至少重复3次所述步骤c的氢氧化铁沉淀纯化工艺操作,得到高纯度氢氧化铁,进行干燥,得到高纯度氢氧化铁粉料;所得高纯度氢氧化铁的锌含量低于1%;e.煅烧处理:将在所述步骤d中得到的高纯度氢氧化铁粉料置入马弗炉中,在500℃温度条件下进行高温煅烧处理2h,发生固相化学反应,得到固体煅烧产物,然后将固体煅烧产物磨成粉末,得到磁性颜料前驱体。如图2所示,得到磁性颜料前驱体为氧化铁红。本实施例通过对含铁锌废酸液预处理得到含锌量极低的氢氧化铁沉淀,对制备的铁产物进行逐级提纯,并对铁产物进行逐级降锌,再通过湿法提纯结合固相反应,对氢氧化铁沉淀高温煅烧处理,得到磁性颜料前驱体。将含铁锌废酸液转化为有利用价值化工原材料产品,同时消除了废酸液的酸危害以及重金属对环境和生态的破坏。本实施例操作过程方便易行,适用于工业化生产;得到的资源化产品可以作为化工颜料生产的原材料,在减少环境污染的同时,达到了变废为宝,节约了资源,降低生产成本的目的,提高了热镀锌厂等的产品附加值,为产业化提供了保证。本实施例通过湿法提纯结合固相反应,有效地降解工业废酸液,实现废弃物资源化。实施例二:本实施例与实施例一基本相同,特别之处在于:在本实施例中,参见图1,一种含铁锌废酸液成分如表2所示,待处理的含铁锌废酸液:表2实施例二含铁锌废酸液成分一览表(浓度单位:mg/l)组分fe2+zn2+fe3+nihcl浓度11000015000100010030000在本实施例中,一种利用本实施例含铁锌废酸液制备磁性颜料前驱体的方法,对制备的铁产物进行逐级提纯,并对铁产物进行逐级降锌,通过湿法提纯结合固相反应,制备磁性颜料前驱体,包括如下步骤:a.预处理:采用h2o2作为氧化剂,向含铁锌废酸液中加入足量h2o2,将待处理的含铁锌废酸液中的二价铁全部氧化成三价铁,得到预处理后的三价铁锌废酸液,待后续处理;b.铁离子沉淀工艺:向在步骤a中制备所得的含三价铁锌废酸液中缓慢滴加氨水溶液,并调节三价铁锌废酸液的ph为3.5-5.0,使得三价铁锌废酸液中的三价铁离子完全生成沉淀物,得固液混合物,然后将所得固液混合物放入离心机中离心,分离得到上清液和粗氢氧化铁沉淀,其中粗氢氧化铁沉淀的锌含量不低于1%;c.氢氧化铁沉淀纯化工艺:采用ph为4.0-5.0的酸性水溶液,将在所述步骤b中所得到的粗氢氧化铁沉淀取出置于烧杯中,向烧杯中加入与在所述步骤b中所得上清液等量的ph为4.0-5.0的硝酸酸性水溶液,搅拌均匀,再次固液分离;d.继续至少重复4次所述步骤c的氢氧化铁沉淀纯化工艺操作,得到高纯度氢氧化铁,进行干燥,得到高纯度氢氧化铁粉料;所得高纯度氢氧化铁的锌含量低于1%;e.煅烧处理:将在所述步骤d中得到的高纯度氢氧化铁粉料置入马弗炉中,在700℃温度条件下进行高温煅烧处理2h,发生固相化学反应,得到固体煅烧产物,然后将固体煅烧产物磨成粉末,得到磁性颜料前驱体。如图3所示,得到磁性颜料前驱体为氧化铁红。本实施例通过对含铁锌废酸液预处理得到含锌量极低的氢氧化铁沉淀,对制备的铁产物进行逐级提纯,并对铁产物进行逐级降锌,再通过湿法提纯结合固相反应,对氢氧化铁沉淀高温煅烧处理,得到磁性颜料前驱体。将含铁锌废酸液转化为有利用价值化工原材料产品,同时消除了废酸液的酸危害以及重金属对环境和生态的破坏。本实施例操作过程方便易行,适用于工业化生产;得到的资源化产品可以作为化工颜料生产的原材料,在减少环境污染的同时,达到了变废为宝,节约了资源,降低生产成本的目的,提高了热镀锌厂等的产品附加值,为产业化提供了保证。本实施例通过湿法提纯结合固相反应,有效地降解工业废酸液,实现废弃物资源化。实施例三:本实施例与前述实施例基本相同,特别之处在于:在本实施例中,参见图1,一种含铁锌废酸液成分如表3所示,待处理的含铁锌废酸液:表3.实施例三含铁锌废酸液成分一览表(浓度单位:mg/l)组分fe2+zn2+fe3+nihcl浓度1400002500010010030000在本实施例中,一种利用本实施例含铁锌废酸液制备磁性颜料前驱体的方法,对制备的铁产物进行逐级提纯,并对铁产物进行逐级降锌,通过湿法提纯结合固相反应,制备磁性颜料前驱体,包括如下步骤:a.预处理:采用na2s2o8作为氧化剂,向含铁锌废酸液中加入足量na2s2o8,将待处理的含铁锌废酸液中的二价铁全部氧化成三价铁,得到预处理后的三价铁锌废酸液,待后续处理;b.铁离子沉淀工艺:向在步骤a中制备所得的含三价铁锌废酸液中缓慢滴加naoh溶液,并调节三价铁锌废酸液的ph为3.5-5.0,使得三价铁锌废酸液中的三价铁离子完全生成沉淀物,得固液混合物,然后将所得固液混合物放入离心机中离心,分离得到上清液和粗氢氧化铁沉淀,其中粗氢氧化铁沉淀的锌含量不低于1%;c.氢氧化铁沉淀纯化工艺:采用ph为4.0-5.0的酸性水溶液,将在所述步骤b中所得到的粗氢氧化铁沉淀取出置于烧杯中,向烧杯中加入与在所述步骤b中所得上清液等量的ph为4.0-5.0的硫酸酸性水溶液,搅拌均匀,再次固液分离;d.继续至少重复4次所述步骤c的氢氧化铁沉淀纯化工艺操作,得到高纯度氢氧化铁,进行干燥,得到高纯度氢氧化铁粉料;所得高纯度氢氧化铁的锌含量低于1%;e.煅烧处理:将在所述步骤d中得到的高纯度氢氧化铁粉料置入马弗炉中,在700℃温度条件下进行高温煅烧处理1h,发生固相化学反应,得到固体煅烧产物,然后将固体煅烧产物磨成粉末,得到磁性颜料前驱体。如图4所示,得到磁性颜料前驱体为氧化铁红。本实施例通过对含铁锌废酸液预处理得到含锌量极低的氢氧化铁沉淀,对制备的铁产物进行逐级提纯,并对铁产物进行逐级降锌,再通过湿法提纯结合固相反应,对氢氧化铁沉淀高温煅烧处理,得到磁性颜料前驱体。将含铁锌废酸液转化为有利用价值化工原材料产品,同时消除了废酸液的酸危害以及重金属对环境和生态的破坏。本实施例操作过程方便易行,适用于工业化生产;得到的资源化产品可以作为化工颜料生产的原材料,在减少环境污染的同时,达到了变废为宝,节约了资源,降低生产成本的目的,提高了热镀锌厂等的产品附加值,为产业化提供了保证。本实施例通过湿法提纯结合固相反应,有效地降解工业废酸液,实现废弃物资源化。实施例四:本实施例与前述实施例基本相同,特别之处在于:在本实施例中,一种含铁锌废酸液成分与实施例一相同,作为待处理的含铁锌废酸液。在本实施例中,参见图1,一种利用本实施例含铁锌废酸液制备磁性颜料前驱体的方法,对制备的铁产物进行逐级提纯,并对铁产物进行逐级降锌,通过湿法提纯结合固相反应,制备磁性颜料前驱体,包括如下步骤:a.预处理:采用naclo作为氧化剂,向含铁锌废酸液中加入足量naclo,将待处理的含铁锌废酸液中的二价铁全部氧化成三价铁,得到预处理后的三价铁锌废酸液,待后续处理;b.铁离子沉淀工艺:向在步骤a中制备所得的含三价铁锌废酸液中缓慢滴加koh溶液,并调节三价铁锌废酸液的ph为3.5-5.0,使得三价铁锌废酸液中的三价铁离子完全生成沉淀物,得固液混合物,然后将所得固液混合物放入离心机中离心,分离得到上清液和粗氢氧化铁沉淀,其中粗氢氧化铁沉淀的锌含量不低于1%;c.氢氧化铁沉淀纯化工艺:采用ph为4.0-5.0的酸性水溶液,将在所述步骤b中所得到的粗氢氧化铁沉淀取出置于烧杯中,向烧杯中加入与在所述步骤b中所得上清液等量的ph为4.0-5.0的盐酸酸性水溶液,搅拌均匀,再次固液分离;d.继续至少重复3次所述步骤c的氢氧化铁沉淀纯化工艺操作,得到高纯度氢氧化铁,进行干燥,得到高纯度氢氧化铁粉料;所得高纯度氢氧化铁的锌含量低于1%;e.煅烧处理:将在所述步骤d中得到的高纯度氢氧化铁粉料置入马弗炉中,在800℃温度条件下进行高温煅烧处理0.5h,发生固相化学反应,得到固体煅烧产物,然后将固体煅烧产物磨成粉末,得到磁性颜料前驱体。如图5所示,得到磁性颜料前驱体为氧化铁红。本实施例通过对含铁锌废酸液预处理得到含锌量极低的氢氧化铁沉淀,对制备的铁产物进行逐级提纯,并对铁产物进行逐级降锌,再通过湿法提纯结合固相反应,对氢氧化铁沉淀高温煅烧处理,得到磁性颜料前驱体。将含铁锌废酸液转化为有利用价值化工原材料产品,同时消除了废酸液的酸危害以及重金属对环境和生态的破坏。本实施例操作过程方便易行,适用于工业化生产;得到的资源化产品可以作为化工颜料生产的原材料,在减少环境污染的同时,达到了变废为宝,节约了资源,降低生产成本的目的,提高了热镀锌厂等的产品附加值,为产业化提供了保证。本实施例通过湿法提纯结合固相反应,有效地降解工业废酸液,实现废弃物资源化。实施例五:本实施例与前述实施例基本相同,特别之处在于:在本实施例中,一种含铁锌废酸液成分与实施例一相同,作为待处理的含铁锌废酸液。在本实施例中,参见图1,一种利用本实施例含铁锌废酸液制备磁性颜料前驱体的方法,对制备的铁产物进行逐级提纯,并对铁产物进行逐级降锌,通过湿法提纯结合固相反应,制备磁性颜料前驱体,包括如下步骤:a.预处理:采用naclo作为氧化剂,向含铁锌废酸液中加入足量naclo,将待处理的含铁锌废酸液中的二价铁全部氧化成三价铁,得到预处理后的三价铁锌废酸液,待后续处理;b.铁离子沉淀工艺:向在步骤a中制备所得的含三价铁锌废酸液中缓慢滴加naoh溶液,并调节三价铁锌废酸液的ph为3.5-5.0,使得三价铁锌废酸液中的三价铁离子完全生成沉淀物,得固液混合物,然后将所得固液混合物放入离心机中离心,分离得到上清液和粗氢氧化铁沉淀,其中粗氢氧化铁沉淀的锌含量不低于1%;c.氢氧化铁沉淀纯化工艺:采用ph为4.0-5.0的酸性水溶液,将在所述步骤b中所得到的粗氢氧化铁沉淀取出置于烧杯中,向烧杯中加入与在所述步骤b中所得上清液等量的ph为4.0-5.0的盐酸酸性水溶液,搅拌均匀,再次固液分离;d.继续至少重复3次所述步骤c的氢氧化铁沉淀纯化工艺操作,得到高纯度氢氧化铁,进行干燥,得到高纯度氢氧化铁粉料;所得高纯度氢氧化铁的锌含量低于1%;e.煅烧处理:将在所述步骤d中得到的高纯度氢氧化铁粉料置入马弗炉中,在80℃温度条件下进行高温煅烧处理2h,发生固相化学反应,得到固体煅烧产物,然后将固体煅烧产物磨成粉末,得到磁性颜料前驱体。得到磁性颜料前驱体为氧化铁黄。本实施例通过对含铁锌废酸液预处理得到含锌量极低的氢氧化铁沉淀,对制备的铁产物进行逐级提纯,并对铁产物进行逐级降锌,再通过湿法提纯结合固相反应,对氢氧化铁沉淀高温煅烧处理,得到磁性颜料前驱体。将含铁锌废酸液转化为有利用价值化工原材料产品,同时消除了废酸液的酸危害以及重金属对环境和生态的破坏。本实施例操作过程方便易行,适用于工业化生产;得到的资源化产品可以作为化工颜料生产的原材料,在减少环境污染的同时,达到了变废为宝,节约了资源,降低生产成本的目的,提高了热镀锌厂等的产品附加值,为产业化提供了保证。本实施例通过湿法提纯结合固相反应,有效地降解工业废酸液,实现废弃物资源化。上面对本发明实施例结合附图进行了说明,但本发明不限于上述实施例,还可以根据本发明的发明创造的目的做出多种变化,凡依据本发明技术方案的精神实质和原理下做的改变、修饰、替代、组合或简化,均应为等效的置换方式,只要符合本发明的发明目的,只要不背离本发明利用含铁锌废酸液制备磁性颜料前驱体的方法的技术原理和发明构思,都属于本发明的保护范围。当前第1页12