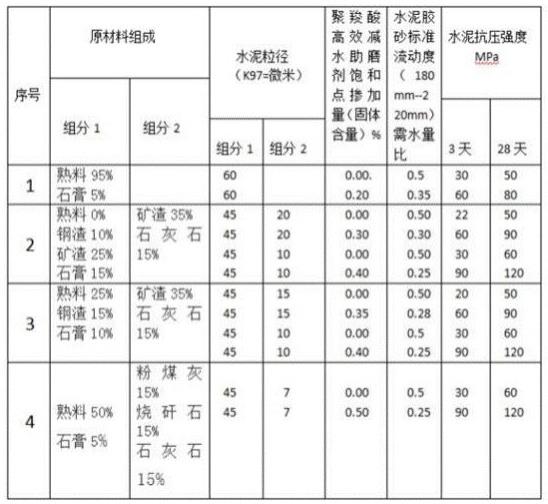
1.本发明涉及建筑材料领域,尤其指一种高性能环保水泥及生产方法。
背景技术:2.众所周知,硅酸盐水泥作为一种建筑材料广泛应用于国民经济的各个领域,对人类文明进步起到重要基础作用。据统计,2018年世界每生产一吨硅酸盐水泥熟料约消耗120千克标准煤及65千瓦时电,能耗巨大。每生产一吨水泥熟料,平均约排放1吨二氧化碳,水泥熟料生产过程中所释放的二氧化碳约占人类所产生二氧化碳总量的7﹪。并且硅酸盐水泥配置的混凝土还有如下缺点:一般强度仅能达到骨料强度的1/2左右,抗渗性、抗腐蚀性、抗碱集料反应能力、不良的界面过渡区不能满足混凝土50年以上耐久性要求,泌水性、离析性、填充性不适应泵送自流平混凝土施工性要求。
技术实现要素:3.本发明所要解决的问题在于,提供一种高性能环保水泥及生产方法,以解决现有技术中水泥熟料大量应用造成的污染以及现有硅酸盐水泥配置的混凝土性能较低的技术问题。
4.本发明解决其技术问题所采用的技术方案为:一种高性能环保水泥,所述水泥原料(重量比)按硅酸盐水泥熟料0%—50%、混合材45%—85%、石膏5%—15%、聚羧酸高效减水助磨剂(固体含量)0.0%—0.6%组成,水泥熟料、石膏、部分混合材粒径小于(d97=60微米),部分(占水泥总重量的30%以上)混合材粒径小于(d97=20微米),水泥胶砂标准流动度饱合点需水量比小于0.3。
5.一种高性能环保水泥的生产方法:取占水泥总重量30%以上的混合材、聚羧酸高效减水助磨剂按配方量混合后单独粉磨到粒径小于(d97=20微米),剩余的混合材、熟料、石膏、聚羧酸高效减水助磨剂按配方量混合后单独粉磨到粒径小于(d97=60微米),最后将两者按配方量混合均匀即得成品。
6.这里需要说明的是,本技术所述“饱和点”为以下意义:本研究试验发现,在水泥净浆、砂浆、混凝土中,随着减水剂的增加,有一个在减水剂加到此点后,减水率不再明显减少的点,此点称为“饱和点”,此时的减水率称为“饱和点减水率”,此时的掺加量称为“饱和点掺加量”,此时的需水量称为“饱和点需水量”,此时的需水量比称为“饱和点需水量比”,此时的水泥胶砂标准流动度需水量比称为“水泥胶砂标准流动度饱和点需水量比”。
7.这里还需要说明的是,本技术所述“(d97=60微米)”表示60微米以下占重量比97%、“(d97=20微米)”表示20微米以下占重量比97%,其余类推。
8.另外需要指出的是,本技术所称熟料是常规硅酸盐水泥熟料、性能必须符合所在国国家标准对硅酸盐水泥熟料的要求,混合材是常规混合材、性能必须符合所在国国家标准硅酸盐水泥或混凝土中对混合材的要求的所有种类的混合材,石膏是常规石膏、性能必须符合所在国国家标准硅酸盐水泥或混凝土中对石膏的要求的所有种类的石膏,减水助磨
剂是常规减水助磨剂、性能必须符合所在国国家标准硅酸盐水泥或混凝土中对减水助磨剂的要求的所有种类的减水助磨剂。
9.本发明的有益效果是:研究和实践发现,泵送自流平混凝土不产生明显泌水,离析的水泥中必须有80%以上20微米以下颗粒,否则自流平混凝土的自填充性无法实现,常规水泥混合粉磨方法生产粒径80%以上20微米以下颗粒的水泥时,造成水泥需水量大量增加,经时效应变差,混凝土成本大大增高,质量降低。采用水泥分别粉磨工艺,把熟料,石膏,部分混合材单独粉磨到粒径小于(d97=60微米),部分混合材(占水泥总重量的30%以上)单独粉磨到粒径小于(d97=20微米)后再混合均匀解决了此问题,并且发现了以下多种意想不到的效果。
10.1、小粒径的混合材较大的减少了混凝土的泌水,离析,较大的改善了混凝土的填充性,这些性能是泵送自流平混凝土必须的施工性要求,也是常规硅酸盐水泥无法实现的性能。
11.2、小粒径的混合材填充在大粒径的硅酸盐水泥空隙中,占据了原来水的空间,小粒径的混合材球形度提高,增加了水泥浆体的润滑作用,结果使水泥胶砂标准流动度饱合点减水率提高到40%以上,混凝土饱合点用水量降低到120kg/m3以下,这也是常规硅酸盐水泥无法实现的性能。
12.3、小粒径的混合材满足了改善混凝土骨料界面的四个条件,1降低水的表面张力,2增大混凝土的粘度,3硅质材料和钙质材料有一定比例,4硅质材料和钙质材料有基本相同的水化速度,这也是常规硅酸盐水泥无法实现的性能。
13.4、由于混凝土施工性的改善,单方用水量的减少,界面的改善,使混凝土3天抗压强度提高3-4倍,28天抗压强度提高2倍以上,混凝土强度超过了骨料强度,达到了混凝土强度的极限。
14.5、由于混凝土单方用水量减少,界面改善,钙硅比合理,使水泥石强度、抗渗性大于骨料,混凝土耐久性大于骨料,千年混凝土成为现实。
具体实施方式
15.为了使本发明所要解决的技术问题、技术方案及有益效果更加清楚明白,以下结合具体实施例,对本发明进行进一步详细说明。应当理解,此处所描述的具体实施例仅仅用以解释本发明,并不用于限定本发明。
16.首先,设置1、2、3、4四组水泥,其中1号水泥为传统硅酸盐水泥,2、3、4号水泥为本发明所提供的高性能环保水泥不同的实施例。
17.然后将四组水泥分别配置,并记录其性能参数制成表—1,将1号和4号水泥制成混凝土并记录其相应混凝土性能参数制成表—2。
18.阅读表—1,对比序号1、2、3、4号水泥,可以看出水泥强度和水泥中熟料含量相关性不大,这一发现颠覆了传统硅酸盐水泥按水泥中熟料含量分类和认为熟料矿物组成决定了水泥性能的概念,由于传统水泥行业主要能源消耗和环境污染都源自熟料烧成用热和碳酸钙分解,降低水泥中熟料含量从根本上降低了水泥工业能耗和二氧化碳排放,同时能够大量综合利用其他行业工业废渣。还可以看出,无论水泥用什么原材料、按什么比例、粒径变化多大,对水泥强度的影响不超过60mpa,但改变水泥胶砂标准流动度需水量比小于0.25
就能使水泥3天强度提高3倍以上达到90mpa,28天强度达到120mpa,这就是说“水”对水泥性能的影响很大,但成本很小,“泥”对水泥性能的影响有限,但成本很大。
19.阅读表—2,对比序号1传统硅酸盐水泥、序号4高性能环保水泥配制的混凝土,可见序号1传统硅酸盐水泥不能满足泵送自流平混凝土的施工性要求,混凝土耐久性不能满足国家标准对最苛刻环境条件下耐久性50年混凝土的全部性能要求。序号4高性能环保水泥由于有小粒径的混合材,完全能够满足泵送自流平混凝土砼的施工性要求,而且由于小粒径的混合材填充在大粒径熟料的空隙中,小粒径混合材球形度提高,增大了水泥浆体的润滑作用,使混凝土单方用水量减少(160—120)=40kg,结果使混凝土28天强度增加(123—76)=47mpa,混凝土强度超过了骨料强度,达到混凝土强度极限,混凝土耐久性超过了国家标准对最苛刻环境条件下耐久性100年混凝土的全部性能要求。
20.表—1 表—2
应当理解的是,本发明的应用不限于上述的举例,对本领域普通技术人员来说,可以根据上述说明加以改进或变换,所有这些改进和变换都应属于本发明所附权利要求的保护范围。