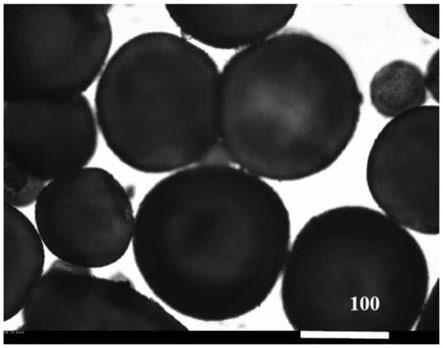
1.本发明涉及水泥基自修复材料领域,涉及一种基于油溶性胺微胶囊的水泥基自修复材料的制备方法。
背景技术:2.水泥基材料是目前用量最大的建筑材料,其最大缺点是脆性大,在服役期间内部极易产生微裂纹,加速有害离子的侵蚀,缩短钢筋混凝土结构的服役寿命。长期以来,水泥基材料裂缝的修复一直是国内外学术界和工程界所研究的重要课题之一,而水泥基材料自修复技术作为裂缝修补的新方法,能有效解决传统修复方法繁杂、成本高昂和时限有限的问题。微胶囊技术是实现水泥基材料自修复的有效方法之一。
3.基于环氧树脂体系的水泥基自修复材料表现出微胶囊与水泥基具有良好的相容性及修复效果。常用的环氧树脂固化剂有乙二胺、改性胺、硫醇、咪类等。张鸣以e
‑
51环氧树脂为修复剂,mc120d为固化剂制备了一种水泥基自修复材料,mc120d为e
‑
51质量的20%时,修复剂的固化反应活化能最低,有利于在水泥基材料中常温固化。胡宏林研究了基于加成聚合的环氧树脂微胶囊/乙二胺微胶囊二元自修复体系,最佳环氧树脂微胶囊与乙二胺微胶囊含量为12%和8%,呈现80.4%的修复效率,并通过修复前后断裂面的sem图片证明了成功实现了自修复过程。研究者多采用水溶性胺作为环氧树脂固化剂,很难保证其在水泥基材料中的贮存稳定性,不能排除微胶囊破裂后固化剂与水泥基材料孔隙中的水反应从而影响自修复效果。
技术实现要素:4.本发明针对以上问题将一种油溶性胺微胶囊化与环氧树脂、水泥、水溶性纤维和混凝土外加剂拌合生产出一种基于油溶性胺微胶囊的水泥基自修复材料。
5.一种基于油溶性胺微胶囊的水泥基自修复材料的制备方法,其特征在于,包括以下步骤:
6.1)在去离子水中加入十二烷基苯磺酸钠按质量比100:1~3制得水相溶液。
7.2)将二甲硫基甲苯二胺与硬脂酸甘油酯按质量比2~4:1混合加热制得油相溶液。
8.所述加热方式为水浴加热,加热温度为70℃.
9.所述硬脂酸甘油酯为单硬脂酸甘油酯或者三硬脂酸甘油酯其中一种。
10.3)将步骤2)所制得的油相溶液在搅拌过程中分散于步骤1)制得的水相溶液中,制得乳液,60℃恒温10min。乳液中油相的质量分数为5.6%
‑
23.8%。
11.4)向步骤3)所制得的乳液中加去离子水降至室温后加入水泥继续搅拌10min。水泥的质量分数为乳液的1%
‑
5%。
12.所述水泥为普通硅酸盐水泥。
13.5)将步骤4)所得产物用去离子水进行筛洗,风干,得到油溶性胺微胶囊。所述筛为孔径125μm的标准检验筛。
14.6)将步骤5)得到的油溶性胺微胶囊与环氧树脂、普通硅酸盐水泥、水、聚羧酸减水剂、水溶性纤维按如下质量比拌合:
[0015][0016]
上述各组分用量之和为100%
[0017]
所述环氧树脂可以直接分散于水泥基体中或者制备成环氧树脂微胶囊分散于水泥基体中。
[0018]
7)在模具内将步骤6)得到的拌合物浇筑成型,并养护24~48h后脱模。
[0019]
以上所述的环氧树脂微胶囊的制备步骤如下:
[0020]
8)将去离子水中依次加入聚(乙烯
‑
alt
‑
马来酸酐)、尿素、氯化铵和间苯二酚混合,用氢氧化钠溶液调节ph至3.50,制得水相;
[0021]
所述去离子水、聚(乙烯
‑
alt
‑
马来酸酐)、尿素、氯化铵、间苯二酚的质量比为500:2.5:10:1:1;
[0022]
所述氢氧化钠溶液的浓度为0.01~1mol/l;
[0023]
9)将环氧树脂与suprasec 2644按质量比9:1混合制得芯材;
[0024]
10)将步骤9)中制得的芯材在搅拌过程中分散于步骤1)制得的水相中,制得乳液,乳液中油相的质量分数为9%~25%;
[0025]
11)向步骤10)中制得的乳液中加入37wt%甲醛溶液,并在55℃下保温4h,37wt%甲醛溶液与水相中尿素质量比为4:1。将产物用去离子水清洗4
‑
5次后过滤、风干,得到环氧树脂微胶囊;
[0026]
本发明将以油溶性胺微胶囊与环氧树脂、水泥、混凝土外加剂、水溶性纤维拌合生产出一种基于油溶性胺微胶囊的水泥基自修复材料。
附图说明
[0027]
图1为实施例1制得的油溶性胺微胶囊的光学显微镜图。
[0028]
图2为实施例1制得的油溶性胺微胶囊的电子扫描显微镜图。
[0029]
图3为实施例1制得的油溶性胺微胶囊的粒径分布图。
[0030]
图4为实施例的水泥基自修复材料的抗压强度图。
具体实施方式
[0031]
为更进一步阐述本发明为达预定目的所采用的技术手段及功效,下面结合实施例与附图对本发明作进一步详细说明,但本发明并不仅限于此。
[0032]
实施例1
[0033]
在100ml去离子水中加入1gsdbs,放置到60℃恒温水浴锅中搅拌溶解作为水相溶液。将4g二甲硫基甲苯二胺与2g单硬脂酸甘油酯混合,放置到70℃恒温水浴锅中磁力搅拌溶解作为油相溶液。将溶解充分的油相溶液与水相溶液混合,以300rpm乳化10min,乳液中油相的质量分数为5.6%。向乳液中加入150ml去离子水,同时向恒温水浴锅中加入去离子水使水温降到室温,向降温后的乳液中加入质量5g普通硅酸盐水泥(p.o 42.5)继续搅拌10min,得到的产物在孔径125um的标准检验筛上用去离子水洗涤至水溶液澄清,风干得到二甲硫基甲苯二胺微胶囊。
[0034]
将质量分数70%的普通硅酸盐水泥(p.o 42.5),质量分数21.9%的水、质量分数2%的二甲硫基甲苯二胺微胶囊、质量分数4%的环氧树脂、质量分数0.1%的巴斯夫聚羧酸减水剂(2651f)和质量分数2%的pva纤维拌合,并于20
×
20
×
20mm的模具中浇筑成型,标准养护24h后脱模,得到基于油溶性胺微胶囊的水泥基自修复材料,继续标准养护至28d龄期,测试其28d抗压强度为初始抗压强度,然后以初始抗压强度的40%对试件进行预损伤,恒压保持3min后卸载,然后将试件标准养护14d,测试其修复后的抗压强度。当预损伤程度为40%时,基于油溶性胺微胶囊的水泥基自修复材料的抗压强度修复率为11%。
[0035]
实施例2
[0036]
在100ml去离子水中加入2gsdbs,放置到60℃恒温水浴锅中搅拌溶解作为水相溶液。将12g二甲硫基甲苯二胺微胶囊与4g三硬脂酸甘油酯混合,放置到70℃恒温水浴锅中磁力搅拌溶解作为油相溶液。将溶解充分的油相溶液与水相溶液混合,以600rpm乳化10min,乳液中油相的质量分数为13.6%。向乳液中加入150ml去离子水,同时向恒温水浴锅中加入去离子水使水温降到室温,向降温后的乳液中加入10g普通硅酸盐水泥(p.o 42.5)继续搅拌10min,得到的产物在孔径125um的标准检验筛上用去离子水洗涤至水溶液澄清,风干得到二甲硫基甲苯二胺微胶囊。
[0037]
将去离子水、聚(乙烯
‑
alt
‑
马来酸酐)、尿素、氯化铵和间苯二酚按质量比500:2.5:10:1:1混合,并用0.1mol/l的氢氧化钠溶液调节ph至3.50作为水相。将e
‑
51环氧树脂和supraec 2644按质量比9:1混合作为油相。将油相与水相混合,以300rpm乳化,得到乳液,乳液中油相的质量分数为16%。然后向乳液中加入质量为水相中尿素质量4倍的37wt%甲醛溶液,升温至55℃保温4h,将产物用去离子水清洗5次后过滤、风干,得到环氧树脂微胶囊。
[0038]
将质量分数45%的普通硅酸盐水泥(p.o 42.5),质量分数21.95%的水、质量分数10%的二甲硫基甲苯二胺微胶囊、质量分数20%的环氧树脂微胶囊、质量分数0.05%的巴斯夫聚羧酸减水剂(2651f)和质量分数3%的pva纤维拌合,并于20
×
20
×
20mm的模具中浇筑成型,养护24h后脱模,得到基于油溶性胺微胶囊的水泥基自修复材料,继续标准养护至28d龄期,测试其28d抗压强度为初始抗压强度,然后以初始抗压强度的60%对试件进行预损伤,恒压保持3min后卸载,然后将试件标准养护14d,测试其修复后的抗压强度。当预损伤程度为60%时,基于油溶性胺微胶囊的水泥基自修复材料的抗压强度修复率为30%。
[0039]
实施例3
[0040]
在100ml去离子水中加入3gsdbs,放置到60℃恒温水浴锅中搅拌溶解作为水相溶液。将18g二甲硫基甲苯二胺与6g三硬脂酸甘油酯混合,放置到70℃恒温水浴锅中磁力搅拌
溶解作为油相溶液。将溶解充分的油相溶液与水相溶液混合,以900rpm乳化10min,乳液中油相的质量分数为18.9%。向乳液中加入150ml去离子水,同时向恒温水浴锅中加入冷水使水温降到室温,向降温后的乳液中加入20g普通硅酸盐水泥(p.o 42.5)继续搅拌10min,得到的产物用去离子水洗涤4
‑
5次,风干得到二甲硫基甲苯二胺微胶囊。
[0041]
将去离子水、聚(乙烯
‑
alt
‑
马来酸酐)、尿素、氯化铵和间苯二酚按质量比500:2.5:10:1:1混合,并用0.1mol/l的氢氧化钠溶液调节ph至3.50作为水相。将e
‑
51环氧树脂和supraec 2644按质量比9:1混合作为油相。将油相与水相混合,以900rpm乳化,得到乳液,乳液中油相的质量分数为16%。然后向乳液中加入质量为水相中尿素质量4倍的37wt%甲醛溶液,升温至55℃保温4h,将产物用去离子水清洗5次后过滤、风干,得到环氧树脂微胶囊。
[0042]
将质量分数55%的普通硅酸盐水泥(p.o 42.5),质量分数28.45%的水、质量分数5%的二甲硫基甲苯二胺微胶囊、质量分数10%的环氧树脂微胶囊、质量分数0.05%的巴斯夫聚羧酸减水剂(2651f)和质量分数1.5%的pva纤维拌合,并于20
×
20
×
20mm的模具中浇筑成型,养护24h后脱模,得到基于油溶性胺微胶囊的水泥基自修复材料,继续标准养护至28d龄期,测试其28d抗压强度为初始抗压强度,然后以初始抗压强度的80%对试件进行预损伤,恒压保持3min后卸载,然后将试件标准养护14d,测试其修复后的抗压强度。当预损伤程度为80%时,基于油溶性胺微胶囊的水泥基自修复材料经的抗压强度修复率为31%。