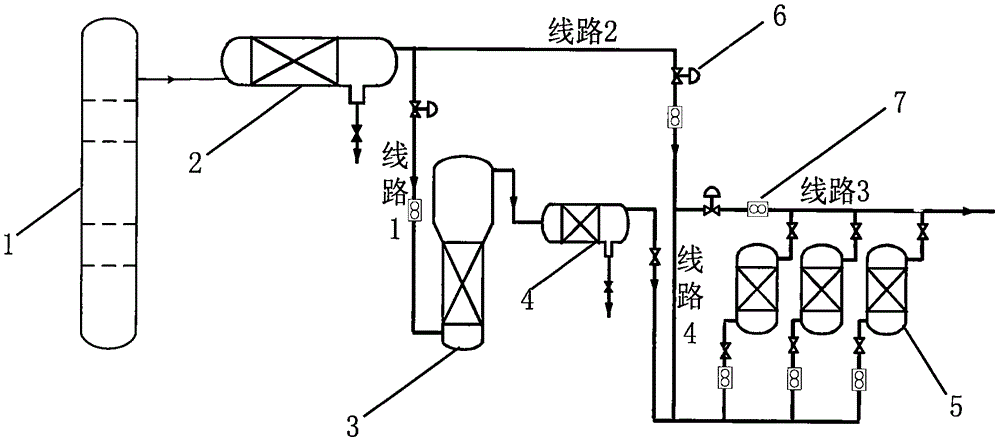
本实用新型涉及蒽醌法制备过氧化氢用工作液的再生装置。
背景技术:
:过氧化氢是一种重要的精细化工原料,应用广泛。过氧化氢分解后产生水和氧气,对环境没有二次污染,绿色环保。现有技术中,通常通过蒽醌法来制备过氧化氢。蒽醌法制取过氧化氢是以2-烷基蒽醌(例如:2-乙基蒽醌、2-叔戊基蒽醌)为载体,以重芳烃、磷酸三辛酯、四丁基脲、醋酸甲基环己酯和二异丁基甲醇中的两种或三种作为混合溶剂,配制成具有一定组成的溶液(以下简称“工作液”)。工作液与氢气一起进入装有钯催化剂的氢化塔内,在一定压力、温度下进行氢化反应,得到相应的烷基蒽氢醌溶液(简称“氢化液”)。氢化液在氧化塔中被空气氧化,溶液中的烷基蒽氢醌恢复成原来的烷基蒽醌,同时生成过氧化氢。利用过氧化氢在水和工作液中的溶解度不同,以及工作液与水的密度差,在萃取塔中用纯水萃取含有过氧化氢的工作液(简称“氧化液”),得到一定浓度的过氧化氢水溶液。过氧化氢水溶液经芳烃净化,即可得到浓度27.5w%~35w%的过氧化氢产品。纯水萃取后的工作液(简称“萃余液”)再生处理后再回到氢化工序,完成一个周期循环。工作液在循环过程中会产生蒽酮、羟基蒽酮、环氧蒽醌、八氢蒽醌等降解物,这些降解物会随着装置的运行不断增加,如不及时处理会影响工作液质量,从而影响过氧化氢的萃取过程和产品质量,还可能会产生安全隐患。因此,在生产过程中循环的工作液必须进行再生处理,以减少降解物,保证装置的正常运行。专利文献cn205973795公开了一种工作液再生方法,通过碱溶液处理和闪蒸相结合的方式对工作液进行再生,工艺过程复杂,因闪蒸工艺仅起脱水作用,没有对蒽醌再生的作用。且萃余液的主要成分为芳烃等有机溶剂,同时还含有过氧化氢等加热容易分解的物质,在闪蒸过程中存在形成气相爆炸性混合物的风险,工艺过程存在安全隐患。技术实现要素:本实用新型要解决的技术问题是提供一种蒽醌法生产过氧化氢用工作液的再生装置,该再生装置再生效果好,设备投资低,原材料消耗少。本实用新型的技术方案是,一种蒽醌法生产过氧化氢用工作液的再生装置,包括萃余分离器2、干燥塔3、碱分离器4及白土床5;萃余分离器2进料端连接萃取塔1,出料端分为线路1和线路2两条支路,线路1依次连接干燥塔3、碱分离器4、白土床5;线路2分为线路3、线路4两条支路,线路4连接白土床5底部,白土床5顶部出口管路与线路3合并后连接于氢化工序。萃余分离器的工作液入口设于萃余分离器的下部,出口设于萃余分离器的上部,萃余分离器底部设有放料口。干燥塔的工作液入口设于干燥塔的下部,出口设于干燥塔的上部,底部设有放料口。线路1、线路2、线路3、线路4为管道。萃余分离器中优选装填聚四氟乙烯填料或不锈钢填料。进一步地,干燥塔进口、白土床入口及线路3均设置有流量计;线路1、线路2和线路3均设置有气动阀。干燥塔内装填有碱液,碱液为质量百分浓度为20%~50%的碳酸钾水溶液、质量百分浓度为20%~50%的碳酸钾和碳酸氢钾混合水溶液或质量百分浓度1%~10%氢氧化钾和氢氧化钙混合水溶液。通过优化碱的浓度和种类,可提高干燥塔的再生效率,使工作液中残留的过氧化氢分解更加彻底,提高工作液碱度,有利于提高白土床对工作液中蒽醌降解物的再生转化率。本实用新型装置通过设置萃余分离器,降低了工作液中的水分和过氧化氢含量,可以很好地维持氢化塔触媒的活性,保证氢化塔的安全。本实用新型通过设置干燥塔,进一步降低了工作液中过氧化氢含量,为白土床再生提供碱性环境,更有利于保持稳定的氢化效率,延长催化剂使用寿命,同时保证氢化塔的安全。本实用新型所述的蒽醌法生产过氧化氢用工作液的再生装置,所述白土床一般为1~4个并联,优选为3个。使用本实用新型所述装置对工作液进行再生的方法是,在蒽醌法生产过氧化氢工艺流程中从萃取塔出来的工作液经萃余分离器分离后分为两路,线路1中工作液送入干燥塔干燥,再经过碱分离器后流入白土床;线路2中的工作液部分通过线路4进入白土床,另外部分工作液通过线路3和经白土床处理后的工作液合并后,进入过氧化氢生产工艺流程中循环。进一步地,所述从萃取塔出来的工作液经萃余分离器分离后,其中体积百分比5%~60%的工作液流经线路1,体积百分比40%~95%的工作液流经线路2。流经线路2的工作液分别进入线路3和线路4,其中体积百分比5%~50%的工作液流经线路3。本实用新型所述的干燥塔、碱分离器、白土床等设备和线路1、线路2、线路3、线路4等线路中的工作液全部通过重力方式自流,无需额外增加动力设备。进一步地,所述的蒽醌法生产过氧化氢用工作液的再生处理方法,根据经萃余分离器分离后工作液中降解物的含量,依据下述原则分配为两路:当降解物的含量<10g/l时,流经线路1的工作液为萃余分离器分离后工作液总体积的10%以下;当降解物的含量10-20g/l时,流经线路1的工作液为萃余分离器分离后工作液总体积的10%~30%;当降解物的含量20-35g/l时,流经线路1的工作液为萃余分离器分离后工作液总体积的30%~60%。所述工作液包含非极性芳烃溶剂、极性溶剂和蒽醌,其中非极性芳烃溶剂是指烷基取代的芳烃或其混合物,极性溶剂为四丁基脲、磷酸三辛酯、醋酸甲基环己酯或其混合物;工作液中蒽醌是指2-乙基蒽醌、2-戊基蒽醌或其混合物,和它们相应的四氢蒽醌或其混合物。本实用新型所述的装置,通过设置萃余分离器、干燥塔、碱分离器、白土床旁路(线路3)等,简化了工艺流程,减少了设备投资,并通过优化碱溶液的浓度和种类,调整不同线路中工作液流量,提高了再生效率,降低了原材料消耗,延长了白土床使用寿命,提高了工艺稳定性、安全性。以10万吨/a27.5w%过氧化氢制造装置为例:本实用新型通过减少闪蒸系统,工作液再生设备投资降低了20%以上,降低动力消耗5%,并提高了设备运行的安全性。通过优化碱的浓度和种类,提高了干燥塔和白土床的再生效率,使工作液中残留的过氧化氢分解更加彻底,降低碱消耗,生产1t27.5%过氧化氢的碱定额消耗由1kg降调到0.9kg以下;降低了氧化铝消耗,生产1t27.5%过氧化氢的氧化铝定额消耗由5.0kg降调到4.0kg以下。根据工作液中总降解物含量和酸度来调节干燥塔流量,通过调节线路3的流量,使线路4的酸性溶液和线路1经过干燥塔的碱性工作液中和,从而使进入白土床的工作液为弱碱性,以增强氧化铝再生蒽醌的能力,延长白土床更换周期,可以使白土床的使用寿命增加20%以上,由45天的更换周期提高到55天以上;调节线路3流量和线路1的流量,从而使得从白土床出来的工作液为中性或弱酸性,这些中性或弱酸性工作液和线路3酸性工作液合并后变为弱酸性,仅产生很少的盐类物质,避免了工作液中酸性物质的过多累积,不会影响后续工艺中氢化塔中催化剂活性,同时降低了系统磷酸消耗,生产1t27.5%过氧化氢的磷酸定额消耗由0.9kg降调到0.8kg以下;干燥塔进口、每台白土床入口及线路3均设置工作液流量计,线路1和线路3采用气动阀控制流量,线路2采用气动阀控制萃余分离器液位,可以确保干燥塔流量稳定,不会出现因流量波动造成带碱;最终可以将工作液中降解物含量稳定的维持在30g/l以下,保证装置的安全稳定运行。附图说明图1是本实用新型包含三个白土床的工作液再生装置示意图图中:1.萃取塔2.萃余分离器3.干燥塔4.碱分离器5.白土床6.气动阀7.流量计。具体实施方式下面结合附图和实施例对本实用新型做进一步详细说明。实施例1如图1所示,一种蒽醌法生产过氧化氢用工作液的再生装置,包括萃余分离器2,干燥塔3,碱分离器4及白土床5;萃余分离器2进料端连接萃取塔1,出料端分为线路1和线路2两条支路,线路1依次连接干燥塔3、碱分离器4、白土床5;线路线路2分为线路3、线路4两条支路,线路4连接白土床5底部,白土床5顶部出口管路与线路3合并后连接与氢化工序。萃余分离器的工作液入口设于萃余分离器的下部,出口设于萃余分离器的上部,萃余分离器底部设有放料口。干燥塔的工作液入口设于干燥塔的下部,出口设于干燥塔的上部,底部设有放料口。连线路1、线路2、线路3、线路4为管道。白土床为三个并联。干燥塔内碱液为质量百分浓度48%的碳酸钾水溶液。萃余分离器中装填有聚四氟乙烯填料。干燥塔进口、白土床入口及线路3均设置有流量计,线路1、线路2和线路3均设置有气动阀。干燥塔、碱分离器、白土床等设备和线路1、线路2、线路3、线路4等线路中的工作液全部通过重力方式自流,无需额外增加动力设备。蒽醌法生产过氧化氢用工作液的再生方法为:在蒽醌法生产过氧化氢工艺流程中从萃取塔出来的工作液经萃余分离器分离后分为两路,线路1中工作液送入干燥塔处理,接着再经过碱分离器后流入白土床,线路2中部分工作液直接进入白土床,另外一部分工作液通过线路3和经白土床处理后的工作液合并后,进入过氧化氢生产工艺流程中循环。依据经萃余分离器分离后工作液中降解物的含量,进行线路1和线路2分配;当降解物的含量<10g/l时,萃余工作液经萃余分离器分离后送入干燥塔的通过线路1的工作液体积百分比为为萃余工作液总体积的8%;当降解物的含量10-20g/l时,萃余工作液经萃余分离器分离后送入干燥塔的通过线路1的工作液体积百分比为为萃余工作液总体积的26%;当降解物的含量20-35g/l时,萃余工作液经萃余分离器分离后送入干燥塔的通过线路1的工作液体积百分比为为萃余工作液总体积的57%。在本工艺条件控制下,整个过氧化氢装置可以平稳运行。工作液中非极性溶剂为芳烃混合物、极性溶剂为四丁基脲、磷酸三辛酯酯和醋酸甲基环己酯的混合物,蒽醌为2-乙基蒽醌和2-乙基四氢蒽醌的混合物。从萃取塔出来的工作液经萃余分离器分离后,其中体积百分比10%~58%的工作液流经线路1,体积百分比42%~90%的工作液流经线路2。线路2中的工作液的体积百分比5%~48%流经线路3。本实施例应用于10万吨/a27.5w%过氧化氢制造装置为例:与具有闪蒸系统的后处理设备相比,降低了工作液再生设备投资的25%,降低动力消耗5%,并提高了设备运行的安全性。通过优化碱的浓度和种类,提高了干燥塔和白土床的再生效率,使工作液中残留的过氧化氢分解更加彻底,降低了碱消耗,生产1t27.5%过氧化氢的碱定额消耗由1kg降调到0.7kg;降低了氧化铝消耗,生产1t27.5%过氧化氢的氧化铝定额消耗由5.0kg降调到3.8kg。根据工作液中总降解物含量和酸度来调节干燥塔流量,通过调节线路3的流量,使线路4的酸性溶液和线路1经过干燥塔的碱性工作液中和,从而使进入白土床的工作液为弱碱性,以增强氧化铝再生蒽醌的能力,延长白土床更换周期,可以使白土床的使用寿命增加30%以上,由45天的更换周期提高到68天;调节线路3流量和线路1的流量,从而使得从白土床出来的工作液为中性或弱酸性,这些中性或弱酸性工作液和线路3酸性工作液合并后变为弱酸性,仅产生很少的盐类物质,避免了工作液中酸性物质的过多累积,不会影响后续工艺中氢化塔中催化剂活性,同时降低了系统磷酸消耗,生产1t27.5%过氧化氢的磷酸定额消耗由0.9kg降调到0.6kg;干燥塔进口、每台白土床入口及线路3均设置工作液流量计,线路1和线路3采用气动阀控制流量,线路2采用气动阀控制萃余分离器液位,可以确保干燥塔流量稳定,不会出现因流量波动造成带碱;最终可以将工作液中降解物含量稳定的维持在30g/l以下,保证装置的安全稳定运行。实施例2一种蒽醌法生产过氧化氢用工作液的再生装置,白土床为并列两个,所述干燥塔内碱液为质量百分浓度45%的碳酸钾和碳酸氢钾混合溶液(其中碳酸钾质量分数为40%,碳酸氢钾碳酸钾质量分数为5%),萃余分离器中装填有不锈钢填料,其他同实施例1。再生方法同实施例1。萃余工作液经萃余分离器分离后,依据工作液中降解物的含量进行分配;当降解物的含量<10g/l时,萃余工作液经萃余分离器分离后送入干燥塔的通过线路1的工作液体积百分比为为萃余工作液总体积的3%;当降解物的含量10-20g/l时,萃余工作液经萃余分离器分离后送入干燥塔的通过线路1的工作液体积百分比为为萃余工作液总体积的13%;当降解物的含量20-35g/l时,萃余工作液经萃余分离器分离后送入干燥塔的通过线路1的工作液体积百分比为为萃余工作液总体积的34%。在本工艺条件控制下,整个过氧化氢装置可以平稳运行。所述工作液中非极性溶剂为芳烃混合物、极性溶剂为四丁基脲和磷酸三辛酯的混合物,蒽醌为2-乙基蒽醌和2-乙基四氢蒽醌的混合物。所述从萃取塔出来的工作液经萃余分离器分离后,其中体积百分比15~50%的工作液流经线路1,体积百分比50~85%的工作液流经线路2,体积百分比6~40%的工作液流经线路3。本实施例应用于10万吨/a27.5w%过氧化氢装制造置为例:与具有闪蒸系统的后处理设备相比,降低了工作液再生设备投资的28%,降低动力消耗5%,并提高了设备运行的安全性。通过优化碱的浓度和种类,提高了干燥塔和白土床的再生效率,使工作液中残留的过氧化氢分解更加彻底,降低了碱消耗,生产1t27.5%过氧化氢的碱定额消耗由1kg降调到0.8kg;降低了氧化铝消耗,生产1t27.5%过氧化氢的氧化铝定额消耗由5.0kg降调到3.9kg。根据工作液中总降解物含量和酸度来调节干燥塔流量,通过调节线路3的流量,使线路4的酸性溶液和线路1经过干燥塔的碱性工作液中和,从而使进入白土床的工作液为弱碱性,以增强氧化铝再生蒽醌的能力,延长白土床更换周期,可以使白土床的使用寿命增加20%以上,由45天的更换周期提高到60天;调节线路3流量和线路1的流量,从而使得从白土床出来的工作液为中性或弱酸性,这些中性或弱酸性工作液和线路3酸性工作液合并后变为弱酸性,仅产生很少的盐类物质,避免了工作液中酸性物质的过多累积,不会影响后续工艺中氢化塔中催化剂活性,同时降低了系统磷酸消耗,生产1t27.5%过氧化氢的磷酸定额消耗由0.9kg降调到0.8kg;干燥塔进口、每台白土床入口及线路3均设置工作液流量计,线路1和线路3采用气动阀控制流量,线路2采用气动阀控制萃余分离器液位,可以确保干燥塔流量稳定,不会出现因流量波动造成带碱;最终可以将工作液中降解物含量稳定的维持在30g/l以下,保证装置的安全稳定运行。实施例3一种蒽醌法生产过氧化氢用工作液的再生装置,白土床为并列四个,所述干燥塔内碱液为质量百分浓度8%氢氧化钾和氢氧化钙混合溶液(其中氢氧化钾质量分数为7.85%,氢氧化钙质量分数为0.15%),萃余分离器中装填有不锈钢填料,其他同实施例1。再生方法同实施例1。萃余工作液经萃余分离器分离后,依据工作液中降解物的含量进行分配;所述的蒽醌法生产过氧化氢的工作液后处理方法,萃余工作液经萃余分离器分离后,依据工作液中降解物的含量进行分配;当降解物的含量<10g/l时,萃余工作液经萃余分离器分离后送入干燥塔的通过线路1的工作液体积百分比为为萃余工作液总体积的7%;当降解物的含量10-20g/l时,萃余工作液经萃余分离器分离后送入干燥塔的通过线路1的工作液体积百分比为为萃余工作液总体积的28%;当降解物的含量20-35g/l时,萃余工作液经萃余分离器分离后送入干燥塔的通过线路1的工作液体积百分比为为萃余工作液总体积的46%。在本工艺条件控制下,整个过氧化氢装置可以平稳运行。所述工作液中非极性溶剂芳烃混合物、极性溶剂为四丁基脲、磷酸三辛酯酯,蒽醌为2-乙基蒽醌,2-乙基四氢蒽醌,2-戊基蒽醌和2-戊基四氢蒽醌的混合物。所述从萃取塔出来的工作液经萃余分离器分离后,其中体积百分比18~52%的工作液流经线路1,体积百分比48~82%的工作液流经线路2,体积百分比8~50%的工作液流经线路3。本实施例应用于10万吨/a27.5w%过氧化氢装制造置为例:与具有闪蒸系统的后处理设备相比,降低了工作液再生设备投资的21%,通过取消闪蒸系统,降低动力消耗5%,并提高了设备运行的安全性。通过优化碱的浓度和种类,提高了干燥塔和白土床的再生效率,使工作液中残留的过氧化氢分解更加彻底,降低了碱消耗,生产1t27.5%过氧化氢的碱定额消耗由1kg降调到0.8kg;降低了氧化铝消耗,生产1t27.5%过氧化氢的氧化铝定额消耗由5.0kg降调到4.0kg。根据工作液中总降解物含量和酸度来调节干燥塔流量,通过调节线路3的流量,使线路4的酸性溶液和线路1经过干燥塔的碱性工作液中和,从而使进入白土床的工作液为弱碱性,以增强氧化铝再生蒽醌的能力,延长白土床更换周期,可以使白土床的使用寿命增加20%以上,由45天的更换周期提高到56天;调节线路3流量和线路1的流量,从而使得从白土床出来的工作液为中性或弱酸性,这些中性或弱酸性工作液和线路3酸性工作液合并后变为弱酸性,仅产生很少的盐类物质,避免了工作液中酸性物质的过多累积,不会影响后续工艺中氢化塔中催化剂活性,同时降低了系统磷酸消耗,生产1t27.5%过氧化氢的磷酸定额消耗由0.9kg降调到0.8kg;干燥塔进口、每台白土床入口及线路3均设置工作液流量计,线路1和线路3采用气动阀控制流量,线路2采用气动阀控制萃余分离器液位,可以确保干燥塔流量稳定,不会出现因流量波动造成带碱;最终可以将工作液中降解物含量稳定的维持在30g/l以下,保证装置的安全稳定运行。实施例4一种蒽醌法生产过氧化氢用工作液的再生装置,白土床为并列三个,所述干燥塔内碱液为质量百分浓度30%的碳酸钾溶液,萃余分离器中装填有不锈钢填料,其他同实施例1。再生方法同实施例1。萃余工作液经萃余分离器分离后,依据工作液中降解物的含量进行分配;当降解物的含量<10g/l时,萃余工作液经萃余分离器分离后送入干燥塔的通过线路1的工作液体积百分比为为萃余工作液总体积的3%;当降解物的含量10-20g/l时,萃余工作液经萃余分离器分离后送入干燥塔的通过线路1的工作液体积百分比为为萃余工作液总体积的12%;当降解物的含量20-35g/l时,萃余工作液经萃余分离器分离后送入干燥塔的通过线路1的工作液体积百分比为为萃余工作液总体积的33%。在本工艺条件控制下,整个过氧化氢装置可以平稳运行。所述工作液中非极性溶剂为芳烃混合物、极性溶剂为四丁基脲和磷酸三辛酯酯的混合物,蒽醌为2-乙基蒽醌和2-乙基四氢蒽醌的混合物。所述从萃取塔出来的工作液经萃余分离器分离后,其中体积百分比14~50%的工作液流经线路1,体积百分比50~86%的工作液流经线路2,体积百分比5~45%的工作液流经线路3。本实施例应用于10万吨/a27.5w%过氧化氢装制造置为例:通过减小干燥塔、白土床系统,降低了工作液再生设备投资的25%,通过取消闪蒸系统,降低动力消耗5%,并提高了设备运行的安全性。通过优化碱的浓度和种类,提高了干燥塔和白土床的再生效率,使工作液中残留的过氧化氢分解更加彻底,降低了碱消耗,生产1t27.5%过氧化氢的碱定额消耗由1kg降调到0.9kg;降低了氧化铝消耗,生产1t27.5%过氧化氢的氧化铝定额消耗由5.0kg降调到3.9kg。根据工作液中总降解物含量和酸度来调节干燥塔流量,通过调节线路3的流量,使线路4的酸性溶液和线路1经过干燥塔的碱性工作液中和,从而使进入白土床的工作液为弱碱性,以增强氧化铝再生蒽醌的能力,延长白土床更换周期,可以使白土床的使用寿命增加20%以上,由45天的更换周期提高到58天;调节线路3流量和线路1的流量,从而使得从白土床出来的工作液为中性或弱酸性,这些中性或弱酸性工作液和线路3酸性工作液合并后变为弱酸性,仅产生很少的盐类物质,避免了工作液中酸性物质的过多累积,不会影响后续工艺中氢化塔中催化剂活性,同时降低了系统磷酸消耗,生产1t27.5%过氧化氢的磷酸定额消耗由0.9kg降调到0.7kg;干燥塔进口、每台白土床入口及线路3均设置工作液流量计,线路1和线路3采用气动阀控制流量,线路2采用气动阀控制萃余分离器液位,可以确保干燥塔流量稳定,不会出现因流量波动造成带碱;最终可以将工作液中降解物含量稳定的维持在30g/l以下,保证装置的安全稳定运行。实施例5一种蒽醌法生产过氧化氢用工作液的再生装置,白土床为并列两个,所述干燥塔内碱液为质量百分浓度45%碳酸钾溶液,萃余分离器中装填有聚四氟乙烯填料,其他同实施例1。再生方法同实施例1。萃余工作液经萃余分离器分离后,依据工作液中降解物的含量进行分配;当降解物的含量<10g/l时,萃余工作液经萃余分离器分离后送入干燥塔的通过线路1的工作液体积百分比为为萃余工作液总体积的6%;当降解物的含量10-20g/l时,萃余工作液经萃余分离器分离后送入干燥塔的通过线路1的工作液体积百分比为为萃余工作液总体积的12%;当降解物的含量20-35g/l时,萃余工作液经萃余分离器分离后送入干燥塔的通过线路1的工作液体积百分比为为萃余工作液总体积的35%。在本工艺条件控制下,整个过氧化氢装置可以平稳运行。所述工作液中非极性溶剂芳烃混合物、极性溶剂为四丁基脲、磷酸三辛酯酯,蒽醌为2-戊基蒽醌和2-戊基四氢蒽醌的混合物。所述从萃取塔出来的工作液经萃余分离器分离后,其中体积百分比18~50%的工作液流经线路1,体积百分比50~82%的工作液流经线路2,体积百分比6~45%的工作液流经线路3。本实施例应用于33万吨/a27.5w%过氧化氢装制造置为例:通过减小干燥塔、白土床系统,降低了工作液再生设备投资的28%,通过取消闪蒸系统,降低动力消耗5%,并提高了设备运行的安全性。通过优化碱的浓度和种类,提高了干燥塔和白土床的再生效率,使工作液中残留的过氧化氢分解更加彻底,降低了碱消耗,生产1t27.5%过氧化氢的碱定额消耗由1kg降调到0.8kg;降低了氧化铝消耗,生产1t27.5%过氧化氢的氧化铝定额消耗由5.0kg降调到4.0kg。根据工作液中总降解物含量和酸度来调节干燥塔流量,通过调节线路3的流量,使线路4的酸性溶液和线路1经过干燥塔的碱性工作液中和,从而使进入白土床的工作液为弱碱性,以增强氧化铝再生蒽醌的能力,延长白土床更换周期,可以使白土床的使用寿命增加20%以上,由45天的更换周期提高到56天;调节线路3流量和线路1的流量,从而使得从白土床出来的工作液为中性或弱酸性,这些中性或弱酸性工作液和线路3酸性工作液合并后变为弱酸性,仅产生很少的盐类物质,避免了工作液中酸性物质的过多累积,不会影响后续工艺中氢化塔中催化剂活性,同时降低了系统磷酸消耗,生产1t27.5%过氧化氢的磷酸定额消耗由0.9kg降调到0.7kg;干燥塔进口、每台白土床入口及线路3均设置工作液流量计,线路1和线路3采用气动阀控制流量,线路2采用气动阀控制萃余分离器液位,可以确保干燥塔流量稳定,不会出现因流量波动造成带碱;最终可以将工作液中降解物含量稳定的维持在30g/l以下,保证装置的安全稳定运行。对比例1以目前10万吨/a27.5w%过氧化氢制造装置为例:生产1t27.5%过氧化氢的碱定额消耗为1kg,氧化铝定额消耗为5.0kg,磷酸定额消耗为0.9kg,白土床更换周期为45天。表1生产1t27.5%过氧化氢原材料定额消耗和白土床更换周期对比原材料定额消耗实施例1实施例2实施例3实施例4实施例5对比例1碱,kg0.70.80.80.90.81.0氧化铝,kg3.83.94.03.94.05.0磷酸,kg0.60.80.80.70.70.9白土床更换周期,天686056585645当前第1页12