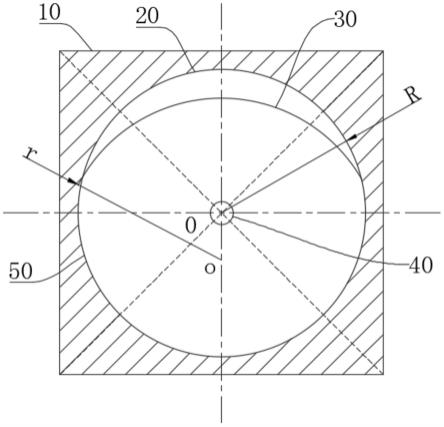
1.本发明属于直拉单晶技术领域,尤其是涉及一种适于熔接时埚位确定方法。
背景技术:2.针对直拉单晶生长过程中熔接工步通过界面辅助工具坐标格进行定埚位,受导流筒安装位置、ccd视野框调节标准、集控界面视野清晰度及人员判断能力等影响因素影响,熔接过程定埚位,埚位一致性差,影响成晶区及成晶过程温度一致性,从而影响成晶率,从而影响生产效率。同时现阶段为人员通过系统提示定埚位节点进行手动调整埚升的方式进行熔接定埚位,占用集控人员大量工作精力进行操作。
技术实现要素:3.本发明提供一种适于熔接时埚位确定方法,尤其是适用于熔接时石英坩埚埚位的确定,解决了现有技术中因通过人工提示对埚位调整而导致的成晶率差且工作效率低的技术问题。
4.为解决上述技术问题,本发明采用的技术方案是:
5.一种适于熔接时埚位确定方法,步骤包括:
6.执行对主室内导流筒下沿面及石英坩埚内液面的倒影成像,以获得所述导流筒下沿面与所述石英坩埚液面同在一个图形界面中;
7.执行所述导流筒下沿面的投影形成的圆弧面一的圆心与所述石英坩埚液面的投影形成的圆弧面二的圆心位于所述图形界面中的同一纵向线上;
8.再测算所述导流筒下沿面至所述石英坩埚内液面的距离。
9.进一步的,所述圆弧面一和所述圆弧面二的圆心均置于所述图形界面对角线交点所在的纵向线上。
10.进一步的,所述圆弧面一的圆心与所述图形界面对角线交点重叠。
11.进一步的,所述圆弧面一和所述圆弧面二同位于籽晶在所述图形界面中的位置同一侧。
12.进一步的,所述籽晶在所述图形界面中的位置为所述图形界面对角线交点所在位置。
13.进一步的,所述圆弧面一的两个端点和所述圆弧面二的两个端点均位于所述图形界面内投影圆的边缘上;且所述圆弧面一位于所述图形界面内投影圆的边缘上。
14.进一步的,所述圆弧面二置于所述圆弧面一内侧;所述圆弧面二和所述圆弧面一均相对于垂直于所述图形界面对角线交点所在的纵向中心线对称设置。
15.进一步的,所述测算所述导流筒下沿面至所述石英坩埚内液面距离的步骤包括:
16.基于置于所述主室外侧ccd摄像机的镜头照射角度及所述摄像机像素;
17.获得所述导流筒下沿面至所述石英坩埚内液面中的最低点距离,即为所述石英坩埚埚位值。
18.进一步的,还包括:获取所述导流筒下沿面至所述石英坩埚内液面中最大高度和最小高度差值的绝对值;
19.当所述导流筒下沿面至所述石英坩埚内液面中最大高度和最小高度差值的绝对值位于0-1.2mm范围内时,所述导流筒位置设置正确;
20.当所述导流筒下沿面至所述石英坩埚内液面中最大高度和最小高度差值的绝对值大于1.2mm时,表示所述导流筒位置设置倾斜;再调整所述导流筒位置。
21.进一步的,所述摄像机投射角度相对于所述石英坩埚液面75
°
。
22.采用本发明设计的方法,可快速确定熔接时石英坩埚埚位的位置,并准确计算出埚位尺寸,同时还可精准确定导流筒与石英坩埚的同轴位置,并能是导流筒快速调整,以满足熔接需要,亦为后续拉晶做好准备。
附图说明
23.图1是本发明一实施例的投影图形界面的示意图;
24.图2是本发明一实施例的熔接时主室内的结构示意图。
25.图中:
26.10、图形界面
ꢀꢀꢀꢀꢀꢀꢀꢀꢀꢀꢀ
20、圆弧面一
ꢀꢀꢀꢀꢀꢀꢀꢀꢀ
30、圆弧面二
27.40、籽晶投影
ꢀꢀꢀꢀꢀꢀꢀꢀꢀꢀꢀ
50、投影圆
ꢀꢀꢀꢀꢀꢀꢀꢀꢀꢀꢀ
60、主室
28.70、摄像机
ꢀꢀꢀꢀꢀꢀꢀꢀꢀꢀꢀꢀꢀ
80、导流筒
ꢀꢀꢀꢀꢀꢀꢀꢀꢀꢀꢀ
90、石英坩埚
29.100、籽晶
具体实施方式
30.下面结合附图和具体实施例对本发明进行详细说明。
31.本实施例提出一种适于熔接时埚位确定方法,如图1-2所示,步骤包括:
32.s1、执行对主室60内的导流筒80下沿面及石英坩埚90内液面的倒影成像,以获得导流筒80下沿面与石英坩埚90液面同在一个图形界面10中。
33.具体地,在主室60内,夹有籽晶100的重锤被钢绳倒装悬挂,其贯穿导流筒80后浸入石英坩埚90内的液面中。置于主室60外壁上的ccd摄像机70朝主室60内投射,以观察石英坩埚90内液面熔接情况。
34.其中,摄像机70的照射角度为倾斜设置,其相对于石英坩埚90液面的角度为75
°
,拍摄的角度可完全将导流筒80的下沿面全部投影到与其电连接的外设终端设备屏幕中形成如图1所示的图形界面10上;而且摄像机70还可完全拍摄到籽晶100熔接的画面,并可观察到石英坩埚90内液面的情况,而且还不会影响籽晶100引晶。
35.摄像机70投射后再在图形界面10上会显示一投影圆50,其中导流筒80下沿面的投影和石英坩埚90内液面的投影都在该投影圆50上和内部显示。其中,图形界面10外形框为正多边形结构,其对角线交点与投影圆50的圆心o重叠设置。
36.s2、执行导流筒80下沿面的投影形成的圆弧面一20的圆心o与石英坩埚90液面的投影形成的圆弧面二30的圆心o位于图形界面10中的同一纵向线上。
37.具体地,先调整导流筒80下沿面的投影,形成圆弧面一20。
38.调整摄像机70的焦距,获得导流筒80的下沿面的投影,其在图形界面10上的位置
是圆弧面一20。且其位于投影圆50的边缘上,并圆弧面一20的圆心o与投影圆50的圆心o在同一纵向轴线上。
39.再调整石英坩埚90内液面的投影,形成圆弧面二30。
40.调整摄像机70的焦距,并获得石英坩埚90的液面的投影,其在图形界面10上的位置是圆弧面二30,其位于投影圆50内侧,且位于导流筒50下沿面在图形界面10中的投影圆弧面一20的内侧。
41.当然,调整导流筒80的下沿面的投影与调整石英坩埚90内液面的投影的顺序可以互换。
42.最后,调整圆弧面一20的圆心o与圆弧面二30的圆心o均位于同一纵向线上。
43.圆弧面一20的圆心o和圆弧面二30的圆心o均置于图形界面10的对角线交点所在的纵向线上,也即是位于图形界面中心纵向轴线上。
44.优选地,圆弧面一20的圆心o与图形界面10的对角线交点重叠;且圆弧面二30的圆心o位于圆弧面一20圆心的下方o。
45.且圆弧面一20和圆弧面二30均位于籽晶100在图形界面10中的位置同一侧,也即是从图1中可以看出,均位于图形界面10的上段部。其中,籽晶100在图形界面10中的位置为图形界面10对角线交点所在位置,也即是籽晶100的投影点位于图形界面10内中心点处。
46.进一步的,圆弧面一20的两个端点和圆弧面二30的两个端点均位于图形界面10内投影圆的边缘上;且圆弧面一20位于图形界面10内投影圆的边缘上。
47.优选地,圆弧面二30置于圆弧面一20的内侧;圆弧面二30和圆弧面一20均相对于垂直于图形界面10对角线交点所在的纵向中心线对称设置。
48.s3、测算导流筒50下沿面至石英坩埚90内液面距离h。
49.基于置于主室10外侧ccd摄像机70的镜头照射角度及摄像机70的像素,系统可以自动捕捉到石英坩埚90内液面中的最低点的位置和最高点的位置。根据摄像机70的像素与摄像机70所拍摄的直径的关系,可获得一系数,再根据该系数和石英坩埚90内液面中的最低点的位置和最高点的位置所对应的像素值,从而可计算出导流筒50的下沿面至石英坩埚90内液面中的最低点和最高点的距离,这种计算方法为系统内自己计算而获得的,不再详述。
50.其中,获得导流筒80下沿面至石英坩埚90内液面中的最低点距离,即为石英坩埚90的埚位值h。
51.进一步的,为了确定导流筒80位置设置的准确性,可根据获取的导流筒80的下沿面至石英坩埚90内液面中最大高度和最小高度差值的绝对值。
52.当导流筒80下沿面至石英坩埚90内液面中最大高度和最小高度差值的绝对值位于0-1.2mm范围内时,表示导流筒80的位置设置正确。
53.当导流筒80下沿面至石英坩埚90内液面中最大高度和最小高度差值的绝对值大于1.2mm时,表示导流筒80位置设置倾斜。若监测到导流筒80位置倾斜,则需要停炉,调整导流筒80的轴向位置,再重新开始熔接,确认石英坩埚90的埚位值。
54.采用本发明设计的方法,可快速确定熔接时石英坩埚埚位的位置,并准确计算出埚位尺寸,同时还可精准确定导流筒与石英坩埚的同轴位置,并能是导流筒快速调整,以满足熔接需要,亦为后续拉晶做好准备。
55.以上对本发明的实施例进行了详细说明,所述内容仅为本发明的较佳实施例,不能被认为用于限定本发明的实施范围。凡依本发明申请范围所作的均等变化与改进等,均应仍归属于本发明的专利涵盖范围之内。