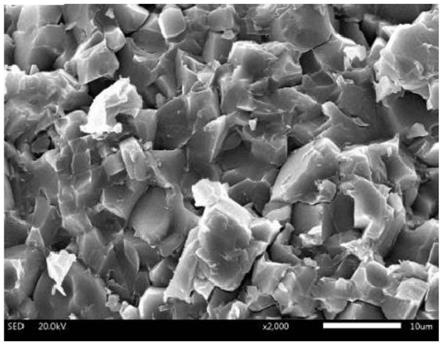
1.本发明属于全固态电池技术领域,涉及一种全固态电池用电解质膜及其制备方法和应用。
背景技术:2.全固态电池是指电池正负极之间没有浸润电解液,仅仅包含一种隔离膜的电池。这种电池的隔离膜中含有固态电解质,除了聚合物系电池,这种电池的隔离膜与现有隔离膜材料差异非常大。li离子二次电池的代表性电池摇椅型电池(也称为羽毛球型电池),与传统的铅酸、镍氢、镍镉电池相比,由于不需要发生电解液与电极间的氧化还原反应,所以从原理上来说本身就是不需要电解液的。现有的锂离子二次电池使用电解液(液态)仅仅是作为li离子在电极间往返的通路,而全固态电池则是通过包含固体电解质的隔离膜直接实现了li离子的往返通过。全固态电池的优点是安全性高(电解液漏液或挥发、以及起火的危险消失),能实现80~90%充电的超快速充电,电池设计自由度增加,可能实现多层化,可在基材上使用能实现表面封装的原材料与零件。
3.最为大家所了解的固体电解质包括:聚合物电解质,氧化物固体电解质,硫化物固体电解质。在氧化物电解质中,latp,lagp,llzo,llto的室温离子电导率达到>10
‑4s.cm
‑1的级别,最为接近常规液态电解质的水平,是实用化的电解质的代表。特别是latp因其原料成本低廉,粉体密度较轻,对空气和水稳定性高,是最可能实现商业化的电解质材料,故对其研究是非常有必要的。
4.目前虽然latp电解质材料制备合成的已经相当成熟了,但对于latp电解质膜片的制备,尤其是100~200μm厚度的电解质膜片的制备仍是难点,要保证高离子电导率,高抗弯曲强度,就必须尽可能的降低晶界阻抗,降低孔隙率,而常规的胶态成型法,如流延成型(tape casting)、注射成型(injecting molding)、凝胶注模成型(gel casting)都会先制备latp粉体,再制备成一定的粘度的浆料进行成型(这个过程中会加入溶剂、分散剂、粘结剂等有毒性有机物,在后续的烧结过程中难免有杂质残留),成型后进行排胶烧结等热处理(这有机物的挥发难免会残留气孔),且最根本的粉体颗粒是经过粉体工程先合成再物理加工的方法制备的(这个过程首先会非常复杂,如固相法,共沉淀法,溶胶凝胶法,其次会对合成好的粉料进行破碎研磨造成颗粒形貌不规则,比表面积呈指数级增长)。这些都会带来晶界的增多,阻抗的增加,难以制备高致密度的latp膜片,不可能发挥出latp电解质材料的最大潜质。
5.cn108615934a公开了一种制备锂离子电池用固体电解质磷酸钛锂铝的方法,步骤如下:将li2co3、al2o3、tio2、nh3h2po4和氧化硼混合,置入球磨罐,加入无水乙醇,在行星球磨机中以250r/min的速度球磨3~4h,球磨后所得粉末在干燥箱中65~75℃干燥11~13h,干燥后的粉末置入石英舟中,于烧结炉中氩气氛围370~390℃煅烧2.5~3.5h,所得物质再次球磨后在27~29mpa压力下压制成直径为15mm、厚度为2mm的圆片,圆片在850~870℃下烧结6h,冷却即得。
6.cn108428935a公开了一种固态电解质膜制备方法及锂电池,固态电解质膜制备方法包括以下步骤:步骤1,将聚氧化乙烯和导电锂盐混合并加入乙腈溶剂中形成混合液,所述混合液在15℃~25℃下搅拌4~16小时至所述导电锂盐完全溶解,形成电解质胶质。步骤2,往所述电解质胶质中加入无机电解质,所述电解质胶质中的无机电解质的质量分数为1%~30%;所述无机电解质包括li
1+x
al
x
ti2–
x
(po4)3(latp),其中0.2≤x≤0.4。步骤3,在15℃~25℃搅拌6~24小时至所述无机电解质完全溶解,形成凝胶态复合电解质。步骤4,将所述凝胶态复合电解质涂覆于基板上并压制平整,在20℃~25℃真空干燥,去除溶剂乙腈,制成固态电解质膜。
7.上述文献中的制备方法无一例外均是先制备latp粉体,再对粉体进行加工处理,添加溶剂、分散剂、粘结剂等制成料浆,再通过刮刀或模具成型,而后对坯体进行排胶烧结热处理得到烧结体,最后再对烧结体进行精细机械加工得到latp片材,这些过程中引入了共沸溶剂、粘结剂、凝胶原料等有毒试剂,操作者必须佩戴防毒用品,谨慎操作各种窑炉,第一步与第二步之间衔接不紧密,造成制备周期非常长,不适合连续化生产,更重要的是latp片材的各项性能指标都会在这个过程中大打折扣。
8.因此,如何提高latp的各种性质以利于其在全固态电池中的应用,是亟待解决的技术问题。
技术实现要素:9.本发明的目的在于提供一种全固态电池用电解质膜及其制备方法和应用。本发明通过对latp电解质膜的原料进行混合后进行熔融和晶化反应,冷却后进行机械处理,取代胶态/液态制浆成型方式,得到了具有高致密度以及高室温电导率的latp电解质膜,且制备过程简单,无残留杂质,没有反复的热处理过程,降低了周转操作的周期和难度,绿色环保,适合量产。
10.为达到此发明目的,本发明采用以下技术方案:
11.第一方面,本发明提供一种全固态电池用电解质膜的制备方法,所述制备方法包括以下步骤:
12.(1)将锂源、铝源、第一钛源和磷源进行混合,得到混合物,然后对混合物进行熔融,得到液态玻璃;
13.(2)将步骤(1)所述液态玻璃与成核剂进行晶化反应,得到电解质块;
14.(3)对步骤(2)所述的电解质块进行机械处理,得到所述全固态电池用电解质膜。
15.本发明通过对原料进行混合后进行熔融和晶化反应,冷却后进行机械处理,取代胶态/液态制浆成型方式,得到了具有高致密度以及高室温电导率的latp电解质膜,且制备过程简单,无残留杂质,没有反复的热处理过程,降低了周转操作的周期和难度,绿色环保,适合量产。
16.优选地,步骤(1)所述混合物中还包括掺杂源。
17.优选地,所述掺杂源的颗粒细度≤325目,例如325目、300目、275目、250目、225目、200目、175目、150目、125目或100目等。
18.本发明中,掺杂源的颗粒细度过大,不利于搅拌,充分浸润,系统成分保持一致。
19.优选地,所述掺杂源包括硅材料和/或二氧化锗。
20.本发明中,硅材料可选自硅微粉或单质硅等各种形态。
21.优选地,步骤(1)所述锂源包括碳酸锂和/或氢氧化锂。
22.优选地,步骤(1)所述铝源包括氧化铝、氢氧化铝、勃姆石或拟薄水铝石中的任意一种或至少两种的组合。
23.优选地,步骤(1)所述第一钛源包括金红石二氧化钛和/或锐钛矿二氧化钛。
24.优选地,步骤(1)所述磷源包括磷酸二氢铵、五氧化二磷或磷酸铝中的任意一种或至少两种的组合。
25.优选地,步骤(1)所述熔融的温度为800~1400℃,例如800℃、850℃、900℃、950℃、1000℃、1050℃、1100℃、1150℃、1200℃、1250℃、1300℃、1350℃或1400℃等。
26.优选地,步骤(1)所述熔融的时间为4~6h,例如4h、4.5h、5h、5.5h或6h等。
27.优选地,步骤(2)所述成核剂包括第二钛源。
28.本发明中,依然选用钛源作为成核剂,因为钛元素是主要最终产物的主要元素,对整体的变量影响较小,可以减少添加导致的计量误差。
29.优选地,以步骤(1)所述第一钛源和第二钛源的总和为100%计,所述第二钛源的质量占比≤5%,例如0.1%、0.5%、0.8%、1%、1.5%、2%、2.5%、3%、3.5%、4%、4.5%或5%等,优选为1~5%。
30.本发明中,第二钛源的质量占比在1~5%,效果更好,如果其质量占比过小,不利于系统快速结晶,反应时间过长,能耗过大,而质量占比过大,又会导致结晶速度过快,未来得及搅拌均匀,均布已开始晶化沉降。
31.优选地,所述第二钛源包括金红石二氧化钛和/或锐钛矿二氧化钛。
32.优选地,步骤(2)所述晶化反应包括:
33.对步骤(1)所述液态玻璃进行一次搅拌,然后加入成核剂进行二次搅拌,冷却,得到电解质块。
34.本发明中,通过搅拌,可以消除液态玻璃中的气孔,形成更为致密的均质体,且先对液态玻璃进行搅拌,再加入成核剂,更利于气泡上浮、破裂、消除,如果不进行一次搅拌,则会出现气泡残留在结晶体中,局部结晶形貌变差,影响结晶体强度。
35.优选地,步骤(3)所述机械处理包括对步骤(2)所述电解质块依次进行机械切割和研磨。
36.作为优选的技术方案,所述制备方法包括以下步骤:
37.(1)将锂源、铝源、第一钛源、磷源和颗粒细度≤325目的掺杂源进行混合,得到混合物,然后对混合物在800~1400℃下进行熔融4~6h,得到液态玻璃;
38.(2)对步骤(1)所述液态玻璃进行一次搅拌,然后加入成核剂进行二次搅拌,冷却,得到电解质块,得到电解质块;
39.(3)对步骤(2)所述的电解质块依次进行机械切割和研磨,得到所述全固态电池用电解质膜;
40.其中,步骤(2)所述成核剂包括第二钛源;以步骤(1)所述第一钛源和第二钛源的总和为100%计,所述第二钛源的质量占比为1~5%。
41.第二方,本发明提供一种全固态电池用电解质膜,所述电解质膜由如第一方面所述的全固态电池用电解质膜的制备方法制备得到,所述全固态电池用电解质膜的化学通式
为li
1+x
al
x
ti2‑
x
(po4)3,0<x<1,例如0.1、0.2、0.3、0.4、0.5、0.6、0.7、0.8或0.9等。
42.优选地,所述电解质膜中还包括硅元素和/或锗元素。
43.本发明中,当电解质膜中掺杂有其他元素时,化学通式可以为li
1+m+3z
al
m
(ti,ge)2‑
m
si
3z
p3‑
z
o
12
,其中包括主晶相li
1+m
al
m
ge
y
ti2‑
m
‑
y
p3o
12
,以及副晶相li
1+m+3z
al
m
(ge,ti)2‑
m
(si
z
po4)3和alpo4,0<m≤0.7,0<y≤0.1,0<z≤0.1。
44.例如,所述m可以为0.1、0.2、0.3、0.4、0.5、0.6或0.7等,所述y可以为0.01、0.02、0.03、0.04、0.05、0.06、0.07、0.08、0.09或0.1等,所述z可以为0.01、0.02、0.03、0.04、0.05、0.06、0.07、0.08、0.09或0.1等。
45.第三方面,本发明还提供一种全固态电池,所述全固态电池包括如第二方面所述的全固态电池用电解质膜。
46.相对于现有技术,本发明具有以下有益效果:
47.本发明通过对latp电解质膜的原料进行混合后进行熔融和晶化反应,冷却后进行机械处理,取代胶态/液态制浆成型方式,得到了具有高致密度以及高室温电导率的latp电解质膜,且制备过程简单,无残留杂质,没有反复的热处理过程,降低了周转操作的周期和难度,绿色环保,适合量产,最终得到的latp电解质膜致密度在96.9%以上,气孔率在3.1%以下,抗弯曲强度在130n*mm
‑2以上,其室温下的离子电导率可达4.12
×
10
‑4s.cm
‑1以上。
附图说明
48.图1为实施例1所提供的全固态电池用电解质膜的sem图。
49.图2为实施例2所提供的制备方法的流程图。
50.图3为对比例1所提供的全固态电池用电解质膜的sem图。
51.图4为对比例1所提供的制备方法的流程图。
52.图5为对比例2所提供的全固态电池用电解质膜的sem图。
53.图6为对比例2所提供的制备方法的流程图。
54.图7为对比例3所提供的全固态电池用电解质膜的sem图。
55.图8为对比例3所提供的制备方法的流程图。
具体实施方式
56.下面通过具体实施方式来进一步说明本发明的技术方案。本领域技术人员应该明了,所述实施例仅仅是帮助理解本发明,不应视为对本发明的具体限制。
57.实施例1
58.本实施例提供一种化学通式为li
1.3
al
0.3
ti
1.7
(po4)3的全固态电池用电解质膜。
59.所述电解质膜的制备方法如下:
60.(1)按li
1.3
al
0.3
ti
1.7
(po4)3的化学计量比称量碳酸锂、勃姆石、金红石二氧化钛和磷酸二氢铵,在混料机中混合均匀,各个原料的颗粒细度控制在300目以下,得到混合物;
61.(2)然后将步骤(1)所述混合物缓慢倒入耐火融炉中,炉中温度控制在1350℃,高温熔融5h,待原料全部融化,得到液态玻璃;
62.(3)用刚玉棒缓慢搅拌液态玻璃,直至液态玻璃中的气泡完全浮出,液面不再有气泡涌出破裂,将金红石二氧化钛缓慢倒入液态玻璃中,引发液态玻璃晶态成核反应,并缓慢
将液态玻璃倒入耐火模具中,边成核边冷却成块,得到化学通式为li
1.3
al
0.3
ti
1.7
(po4)3的电解质块,其中,成核剂占所有金红石二氧化钛的总质量的5%;
63.(4)将冷却的电解质块,用金刚石线切割设备加工成板材,再用磨床,研磨机进行精加工处理,得到厚度为150μm的li
1.3
al
0.3
ti
1.7
(po4)3电解质膜。
64.实施例2
65.本实施例提供一种化学通式为li
1.3
al
0.3
ge
0.05
ti
1.65
(po4)3的全固态电池用电解质膜。
66.所述电解质膜的制备方法如下(流程如图2所示):
67.(1)按li
1.3
al
0.3
ge
0.05
ti
1.65
(po4)3的化学计量比称量氢氧化锂、氧化铝、金红石二氧化钛、磷酸铝和二氧化锗,在混料机中混合均匀,各个原料的颗粒细度控制在325目以下,得到混合物;
68.(2)然后将步骤(1)所述混合物缓慢倒入耐火融炉中,炉中温度控制在800℃,高温熔融6h,待原料全部融化,得到液态玻璃;
69.(3)用刚玉棒缓慢搅拌液态玻璃,直至液态玻璃中的气泡完全浮出,液面不再有气泡涌出破裂,将金红石二氧化钛(成核剂)缓慢倒入液态玻璃中,引发液态玻璃晶态成核反应,并缓慢将液态玻璃倒入耐火模具中,边成核边冷却成块,得到化学通式为li
1.3
al
0.3
ge
0.05
ti
1.65
(po4)3的电解质块,其中,成核剂占所有金红石二氧化钛的总质量的3%;
70.(4)将冷却的电解质块,用金刚石线切割设备加工成板材,再用磨床,研磨机进行精加工处理,得到厚度为140μm的li
1.3
al
0.3
ge
0.05
ti
1.65
(po4)3电解质膜。
71.实施例3
72.本实施例提供一种化学通式为li
1.26
al
0.2
ge
0.05
ti
1.75
si
0.06
(po4)3的全固态电池用电解质膜。
73.所述电解质膜的制备方法如下:
74.(1)按li
1.26
al
0.2
ge
0.05
ti
1.75
si
0.06
(po4)3的化学计量比称量碳酸锂、拟薄水铝石、锐钛矿二氧化钛、磷酸二氢铵、二氧化锗和硅微粉,在混料机中混合均匀,各个原料的颗粒细度控制在280目以下,得到混合物;
75.(2)然后将步骤(1)所述混合物缓慢倒入耐火融炉中,炉中温度控制在1400℃,高温熔融4h,待原料全部融化,得到液态玻璃;
76.(3)用刚玉棒缓慢搅拌液态玻璃,直至液态玻璃中的气泡完全浮出,液面不再有气泡涌出破裂,将锐钛矿二氧化钛缓慢倒入液态玻璃中,引发液态玻璃晶态成核反应,并缓慢将液态玻璃倒入耐火模具中,边成核边冷却成块,得到化学通式为li
1.26
al
0.2
ge
0.05
ti
1.75
si
0.06
(po4)3的电解质块,其中,成核剂占所有锐钛矿二氧化钛的总质量的1%;
77.(4)将冷却的电解质块,用金刚石线切割设备加工成板材,再用磨床,研磨机进行精加工处理,得到厚度为130μm的li
1.26
al
0.2
ge
0.05
ti
1.75
si
0.06
(po4)3电解质膜。
78.实施例4
79.本实施例与实施例1的区别为,本实施例步骤(3)中直接将金红石二氧化钛缓慢倒入液态玻璃中进行搅拌,不提前对液态玻璃进行搅拌。
80.其余制备方法与参数与实施例1保持一致。
81.实施例5
82.本实施例与实施例1的区别为,本实施例步骤(3)中,成核剂的质量占比为6%。
83.其余制备方法与参数与实施例1保持一致。
84.实施例6
85.本实施例与实施例2的区别为,本实施例步骤(1)中二氧化锗的颗粒细度为350目。
86.其余制备方法与参数与实施例1保持一致。
87.对比例1
88.流程如图4所示,预先将碳酸锂、氧化铝、二氧化钛、磷酸二氢氨混合均匀,采用高温固相法在1400℃条件下合成latp固体电解质粉,将粉体研磨至中位粒径为1
‑
5μm后,添加有机溶剂、分散剂、粘结剂、增塑剂等制备成一定粘度的浆料,浆料通过流延机烘道以80℃的温度上进行烘干成膜,在将膜坯剥离下来进行排胶、烧结、精加工处理得到latp电解质膜。
89.对比例2
90.流程如图6所示,预先将氢氧化锂、氧化铝、二氧化钛、磷酸二氢氨混合均匀,采用高温固相法在1350℃条件下合成latp固体电解质粉,将粉体研磨至中位粒径为3
‑
5μm后,添加石蜡、分散剂、聚丙烯等制备成注射喂料,在115℃下喂料通过注射机射入模腔成为片状膜坯,将膜坯剥离下来进行排胶、烧结、精加工处理得到latp电解质膜。
91.对比例3
92.流程如图8所示,预先将碳酸锂、拟薄水铝石、二氧化钛、磷酸二氢氨混合均匀,采用高温固相法在1380℃条件下合成latp固体电解质粉,将粉体研磨至中位粒径为2
‑
5μm后,添加去离子水、分散剂、单体、交联剂、引发剂、催化剂等制备成凝胶浆料,倒入注浆模具内,在70℃下干燥成为片状膜坯,将膜坯剥离下来进行排胶、烧结、精加工处理得到latp电解质膜。
93.图1为实施例1所提供的全固态电池用电解质膜的sem图,图3为对比例1所提供的全固态电池用电解质膜的sem图,图5为对比例2提供的全固态电池用电解质膜的sem图,图7为对比例3提供的全固态电池用电解质膜的sem图。
94.经过对比,可以看出图3、图5、图7中的电解质膜有着明显的气孔,电解质粉体颗粒之间堆积不够密实,缺陷较多,给离子迁移带来阻碍,实际应用时也更容易破裂,而实施例1中的电解质膜气孔较少,颗粒堆积更好,更容易形成高致密高电导率的组件。
95.表1中列出了实施例1
‑
6与对比例1
‑
3所提供的全固态电池用电解质膜的各种性质。
96.表1
97.[0098][0099]
从实施例1与实施例4的数据结果可知,当不提前对液态玻璃进行搅拌,而是直接加入成核剂进行搅拌时,会出现气孔率增多,致密度下降,离子电导率下降。
[0100]
从实施例1与实施例5的数据结果可知,成核剂过多,不利于晶化反应以适当速度进行,熔融物电导率值与理论值相差较大。
[0101]
从实施例2与实施例6的数据结果可知,掺杂源的颗粒细度过大,会导致晶化未完成彻底,局部致密度不足,整体缺陷较多,离子电导率与理论值相差较大。
[0102]
从实施例1与对比例1
‑
3的数据结果可知,相比于采用传统的制备方法制备得到的latp电解质膜,本发明所提供的latp电解质膜气孔率明显降低,室温离子电导率和抗弯曲强度等有明显提升,带来的可加工性也更加极限。
[0103]
综上所述,本发明通过对latp电解质膜的原料进行混合后进行熔融和晶化反应,冷却后进行机械处理,取代胶态/液态制浆成型方式,得到了具有高致密度以及高室温电导率的latp电解质膜,且制备过程简单,无残留杂质,没有反复的热处理过程,降低了周转操作的周期和难度,绿色环保,适合量产,最终得到的latp电解质膜致密度在96.9%以上,气孔率在3.1%以下,抗弯曲强度在130n*mm
‑2以上,其室温下的离子电导率可达4.12
×
10
‑4s.cm
‑1以上。
[0104]
申请人声明,以上所述仅为本发明的具体实施方式,但本发明的保护范围并不局限于此,所属技术领域的技术人员应该明了,任何属于本技术领域的技术人员在本发明揭露的技术范围内,可轻易想到的变化或替换,均落在本发明的保护范围和公开范围之内。