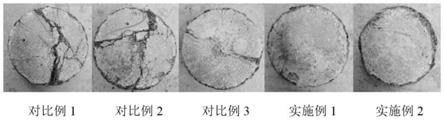
1.本发明属于建筑材料领域,尤其涉及到一种生态型抗冲击超高性能混凝土及其应用。
背景技术:2.超高性能混凝土(ultra
‑
highperformance concrete)具有超高强度、高韧性和较好的耐久性等优异的特点。目前,已有不少学者针对不同组分对混凝土抗冲击性能的影响进行了一定的研究,包括不同掺量的钢纤维、混掺纤维和不同粗骨料对混凝土抗冲击性能的影响,并得到了相关的研究结果。例如,有人研究了不同钢纤维对混凝土抗冲击性能的影响,结果表明长直纤维的作用效果优于端钩纤维,钢纤维优于有机纤维,同时粗骨料的种类也会对混凝土抗冲击性能产生正负影响。然而,超高性能混凝土内不含粗骨料,通过钢纤维提高抗冲击性能的方式需在混凝土内添加大量钢纤维,会提高成本以及超高性能混凝土的容重。
技术实现要素:3.本发明发现具有多孔结构物质在受到作用力时会有一定的变形,因而利用多孔的陶砂替代部分天然河砂,利用多孔结构变形能吸收冲击能量的性质提高超高性能混凝土的韧性以对冲击力的缓冲作用,据此,本发明提供如下技术方案:
4.第一方面,本发明提供一种生态型抗冲击超高性能混凝土,按重量计,每立方米包括如下组分:水泥700~800kg,硅灰140~150kg,石粉200kg,细集料850~950kg,聚羧酸高效减水剂30~40kg,钢纤维78~195kg,水200~220kg;细集料由体积比为1:3.5~5的陶砂和河砂组成,陶砂的粒径≥0.6mm。
5.以上技术方案利用陶砂的多孔结构在受到冲击力时会产生微变形、对冲击能量具有一定的吸收作用,将细集料中的一部分河砂替换成生态型多孔陶砂,制备成对冲击力具有缓冲作用的超高性能混凝土,该超高性能混凝土具有较高的抗冲击性能以及韧性。陶砂在细集料和超高性能混凝土中必须具有一定的占比,才能吸收一定的冲击能量,达到提高超高性能混凝土抗冲击性能的目的。陶砂的粒径不宜过小,一方面是因为陶砂粒径越小、吸水率越高、筒压强度也越低;另一方面陶砂粒径越小,受到作用力时变形量越小,缓冲作用就小,无法实现提高超高性能混凝土抗冲击性能的目的。
6.优选地,细集料的粒径≤1.25mm,将细集料的粒径控制为≤1.25mm,有助于减少混凝土内部宏观缺陷,提高超高性能混凝土的密实度,进而提高超高性能混凝土的抗压强度;
7.优选地,粒径<0.6mm的部分与粒径为0.6
‑
1.25mm的部分体积比为3.5~5:1,重量比为4~6:1。对细集料级配进行限定,砂的级配良好不仅可以节约水泥,而且混凝土拌合物和易性较好,还可提高混凝土密实度和强度。
8.在上述技术方案的基础上,用陶砂取代等体积的河砂,粒径为0.6
‑
1.25mm的细集料中,陶砂所占体积比为75%~100%。更进一步地,细集料由体积比为1:3.5~4的陶砂和
河砂组成,既能提高抗冲击性能,又能降低超高性能混凝土容重。
9.优选地,陶砂是密度为700~800kg/m3、筒压强度不低于4.0mpa、吸水率小于10%的黏土陶砂、页岩陶砂或煤矸石陶砂。
10.在上述技术方案的基础上,每立方米生态型抗冲击超高性能混凝土包括:水泥740~760kg,硅灰140~145kg,石粉200kg,粒径<0.6mm的河砂760~780kg,粒径为0.6
‑
1.25mm的陶砂140~145kg,聚羧酸高效减水剂30~35kg,钢纤维150~160kg,水170~190kg。该配比更接近最优配合比和水胶比,超高性能混凝土的各项性能更好。更进一步地,每立方米生态型抗冲击超高性能混凝土包括:水泥750kg,硅灰144kg,石粉200kg,粒径<0.6mm的河砂770kg,粒径为0.6
‑
1.25mm的陶砂142kg,聚羧酸高效减水剂35kg,钢纤维156kg,水180kg。该配比为最优配合比,在该配合比下,超高性能混凝土具有最大堆积密度,抗压性能和抗冲击性能最好。
11.第二方面,本发明提供上述生态型抗冲击超高性能混凝土在制备桥面铺装面、防撞护栏、桥墩外包防护、复合装甲、抗侵彻与爆炸结构、大坝泄水溢流面、海上结构、核反应堆防护罩、核废料储存容器中的应用。
12.与现有技术相比,本发明的优点如下:
13.本发明提供的生态型抗冲击超高性能混凝土具有较好的抗冲击性能和较优的韧性,容重降低,对环境十分友好,且制备方法简单,实用性强。
附图说明
14.图1展示了各试样不同龄期的抗压强度对比;
15.图2展示了各试样的正面抗冲击结果;
16.图3展示了各试样的背面抗冲击结果。
具体实施方式
17.为使本发明实施例的目的、技术方案和优点更加清楚,下面将结合本发明实施例中的附图,对本发明实施例中的技术方案进行清楚、完整地描述,显然,所描述的实施例是本发明的一部分实施例,而不是全部的实施例。基于本发明中的实施例,本领域普通技术人员在没有做出创造性劳动的前提下所获得的所有其他实施例,都属于本发明保护的范围。
18.本发明设计生态型抗冲击超高性能混凝土时,首先进行如下操作:
19.(1)对实验所需要的粉料及骨料进行粒径分布测试;
20.(2)通过修正的安德森和安德烈森紧密堆积模型,得出各原料在紧密堆积下的体积分布;
21.(3)通过各原料的密度和每立方米混凝土的重量估算出各原料的重量;
22.(4)确定减水剂掺量及水胶比,得出配合比。
23.由此本发明提供一种生态型抗冲击超高性能混凝土,每立方米包括如下组分:水泥700~800kg,硅灰140~150kg,石粉200kg,细集料850~950kg,聚羧酸高效减水剂30~40kg,钢纤维78~195kg,水200~220kg;细集料中,陶砂占100~150kg,其余为河砂。每立方米生态型抗冲击超高性能混凝土的固体重量为2100~2200kg。
24.在上述技术方案的基础上,聚羧酸高效减水剂的掺量为3.0%~3.5%,水胶比的
范围为0.20~0.30。
25.在上述技术方案的基础上,细集料的粒径≤1.25mm,其中,粒径<0.6mm的部分与粒径为0.6
‑
1.25mm的部分体积比为3.5~5:1。
26.在上述技术方案的基础上,陶砂的粒径为0.6
‑
1.25mm;粒径为0.6
‑
1.25mm的细集料中,陶砂所占体积比为75%~100%。
27.在上述技术方案的基础上,细集料由体积比为1:3.5的陶砂和河砂组成。
28.在上述技术方案的基础上,陶砂可由各类黏土、板岩、页岩、煤矸石及工业固体废弃物等多种原料经过高温烧结而成,优选为密度为700~800kg/m3、筒压强度不低于4.0mpa、吸水率小于10%的黏土陶砂、页岩陶砂或煤矸石陶砂,使用前无需预浸湿,但需根据吸水率调整用水量。
29.在上述技术方案的基础上,陶砂占全部细集料的10wt%~16wt%。
30.在上述技术方案的基础上,细集料的粒径≤1.25mm,其中,粒径<0.6mm的部分与粒径为0.6
‑
1.25mm的部分重量比为4~6:1。
31.在上述技术方案的基础上,陶砂的粒径为0.6
‑
1.25mm;粒径为0.6
‑
1.25mm的细集料中,陶砂占比60wt%~100wt%。
32.在上述技术方案的基础上,每立方米生态型抗冲击超高性能混凝土包括:水泥740~760kg,硅灰140~145kg,石粉200kg,粒径<0.6mm的河砂760~780kg,粒径为0.6
‑
1.25mm的陶砂140~145kg,聚羧酸高效减水剂30~35kg,钢纤维150~160kg,水170~190kg。
33.在上述技术方案的基础上,每立方米生态型抗冲击超高性能混凝土包括:水泥750kg,硅灰144kg,石粉200kg,粒径<0.6mm的河砂770kg,粒径为0.6
‑
1.25mm的陶砂142kg,聚羧酸高效减水剂35kg,钢纤维156kg,水180kg。
34.以下实施例中,采用的水泥为p
·
o 42.5及以上等级普通硅酸盐水泥;采用的硅灰的sio2含量≥94%,其他性能满足《砂浆和混凝土用硅灰》(gb/t 27690
‑
2011)的相关规定;采用的石粉为石灰石粉,28d活性指数≥60%;采用的河砂分为粒径在0
‑
0.6mm范围内的细砂、0.6
‑
1.25mm范围的粗砂;采用的陶砂粒径在0.6
‑
1.25mm范围内;采用的聚羧酸高效减水剂为液体减水剂,减水率≥25%;采用的钢纤维直径0.18
‑
0.22mm,长度12
‑
14mm;采用的陶砂是密度为750kg/m3、筒压强度为6.0mpa、吸水率为4%的页岩陶砂。
35.本发明生态型抗冲击超高性能混凝土的制备方法是:
36.为了更加直观地展示陶砂的使用带来的改善效果,本发明提供两个不同组分的实施例和三个对比例,通过对比来展现本发明提供的生态型抗冲击超高性能混凝土的性能,下面结合表格中的数据对本发明作进一步详细说明。
37.实施例
38.1.按表1所示配合比准备p
·
o52.5普通硅酸盐水泥、硅灰、石粉、天然的河砂、陶砂、水、聚羧酸高效减水剂、钢纤维。
39.表1对比例和实施例的配合比
[0040][0041]
因陶砂粒径越小吸水率越高,筒压强度越低,受到作用力时变形量越小,优选为用陶砂取代0.6
‑
1.25mm河砂。此外,因陶砂密度较小,在以上实施例和对比例中用等体积的陶砂取代等体积的0.6
‑
1.25mm河砂,陶砂对粒径为0.6
‑
1.25mm的河砂的体积取代率:对比例1为0;对比例2为25%;对比例3为50%;实施例1为75%;实施例2为100%。如表1所示,随着体积取代率提高,超高性能混凝土的容重逐渐降低。
[0042]
2.根据配合比将粉料加入到搅拌锅中低速搅拌30s后,然后在15s内将粗砂细砂加入搅拌锅中,继续低速慢搅45s,接着加入水与聚羧酸高效减水剂,待成浆后开启自动搅拌模式240s,自动搅拌结束后开启低速慢搅,加入钢纤维,继续低速搅拌60s;将搅拌好的浆体倒入模具中成型,待其硬化后拆模进行养护。
[0043]
3.养护好的生态型抗冲击超高性能混凝土的性能测试实验以及结果如下:
[0044]
(1)抗压强度
[0045]
实验采用gb/t 17671
‑
1999对各实施例和对比例制得的混凝土试样进行抗压强度测试。将新鲜拌制的砂浆倒在40mm
×
40mm
×
160mm的长方体模具中,硬化24h后拆模后放入恒温养护室中进行养护,分别测量试样3d、7d和28d的抗压强度,测试结果如图1所示。
[0046]
由图1可以看出,各对比例和实施例的混凝土试样在抗压强度上均表现出较优异的强度,此现象说明通过调整陶砂的含量对其静态力学性能(即抗压强度)不会产生不良的影响。
[0047]
(2)抗冲击性能
[0048]
实验采用高空落球实验对制得不同组的混凝土试样的抗冲击性能进行评估。将新鲜拌制的砂浆倒入直径100mm、高度为50mm的圆柱形模具中,硬化24h后拆模养护28d,用长3m的塑料管道作为钢球的路径,将1.1kg的铁球垂直砸下,循环100次后观察uhpc试块的变化,并通过能量公式计算钢球的能量转换情况。
[0049]
由图2可以看出,经过100次落球实验,实施例1和实施例2的试样正面的裂纹条数和裂纹宽度均小于对比例1
‑
3;通过观察由图3可以看出,陶砂对粒径为0.6
‑
1.25mm的河砂体积取代率≤50%时,抗冲击性能提升不够明显,对比例1和对比例2两组试样背面出现贯穿试样的裂纹,对比例3背面也有明显的裂纹,实施例1和实施例2中陶砂对粒径为0.6
‑
1.25mm的河砂体积取代率≥75%,两组试样背面几乎没有出现裂纹,抗冲击性能得到显著提升。表2计算出了各实施例和对比例制备的试样产生第一条裂纹时所需的能量。
[0050]
表2抗冲击能量计算
[0051][0052]
由表2中数据也可以看出,实施例2表面出现第一条裂纹时所进行的冲击次数最多,所需要的能量越大,实施例2表现出比对比例1和3更加优异的抗冲击性能。
[0053]
由上述数据可以得出,本发明提供的生态型抗冲击超高混凝土不仅保持了优异的抗压强度,还极大地改善了超高性能混凝土的抗冲击性能。
[0054]
以上所述仅是本发明的具体实施方式,使本领域技术人员能够理解或实现本发明。对这些实施例的多种修改对本领域的技术人员来说将是显而易见的,本文中所定义的一般原理可以在不脱离本发明的精神或范围的情况下,在其它实施例中实现。因此,本发明将不会被限制于本文所示的这些实施例,而是要符合与本文所申请的原理和新颖特点相一致的最宽的范围。