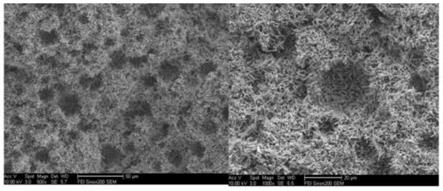
一种氮化硅
‑
石英空心球陶瓷及制备方法
技术领域:
1.本发明属于氮化硅陶瓷技术领域,更具体地涉及氮化硅
‑
石英空心球陶瓷及制备方法。
背景技术:2.氮化硅既是优良的高温结构材料,又是新型的陶瓷材料,有“全能冠军”之称。而多孔氮化硅陶瓷兼有氮化硅和多孔陶瓷两者的优异性,除了具有高比强、高比模、抗氧化、耐高温等优点外,还具有密度低,介电性能优良等特性。
3.目前,多孔氮化硅陶瓷材料分为泡沫结构、添加造孔剂的通孔结构、纳米柱状晶结构及闭孔结构。泡沫结构、添加造孔剂的通孔结构的多孔氮化硅陶瓷材料在制备过程中由于使用有机添加剂而容易存在残炭的现象,而且材料中气孔率大于50%后,材料的强度很低,不能满足使用要求。闭孔结构的多孔氮化硅陶瓷材料制备过程较难,工艺不好控制。纳米孔柱状晶结构的多孔氮化硅陶瓷材料气孔率很难达到50%以上。
4.专利号为cn101591191a的国家发明专利公开了一种氧化锆增强氮化硅/石英基陶瓷复合材料及其制备方法,利用了石英粉、氮化硅粉等,压制成型制成素坯,在氮气气氛保护下无压烧成。宽耐温性、耐烧蚀性好,并且具有良好的力学性能和介电性能,强度大。但是由于石英粉反应后并不能留下较大尺寸的空隙,整体材料气孔率较低。
技术实现要素:5.为解决上述问题,克服现有技术的不足,本发明提供了一种氮化硅
‑
石英空心球陶瓷及制备方法,解决的
6.第一个技术问题是:石英粉反应后并不能留下较大尺寸的空隙,整体材料气孔率较低;
7.第二个技术问题是:石英粉粒度小反应活性大,与氮化硅容易形成玻璃相,相同容积下,石英粉的添加量越大越容易产生玻璃相,而玻璃相的产生会破坏长柱状晶体,进而影响介电性能;
8.第三个技术问题是:玻璃相的产生影响长柱状晶体的长径比,插接效果较差,气孔率降低。
9.本发明解决上述技术问题的具体技术方案为:氮化硅
‑
石英空心球陶瓷,包括以下组份(质量份数):氮化硅粉体80
‑
90份,稀土氧化物粉体5
‑
10份,石英粉体5
‑
10份。
10.进一步的,所述的石英粉体为石英空心粉体。
11.进一步的,所述组份还添加有增塑剂。
12.进一步的,所述增塑剂为聚乙烯醇。
13.进一步的,所述氮化硅粉体的α相含量大于95%(重量百分比),铁含量小于0.5%(重量百分比)。
14.进一步的,所述石英空心粉比率大于90%,空心球粉体粒径为10
‑
30μm,空心球壁
厚0.3
‑
1μm,抗压强度大于50mpa。
15.进一步的,所述稀土氧化物粉体是氧化钇或氧化镧或氧化钐的一种或两种以上的混合物。
16.一种氮化硅
‑
石英空心球陶瓷制备方法,根据所述组份制备,包括如下步骤:
17.步骤一.将物料氮化硅粉体、稀土氧化物粉体、石英空心粉体,以酒精作为介质溶液混合,物料与酒精比例为1:(1
‑
2),并添加增塑剂溶液;加热搅拌至溶液无流动性、烘干;
18.步骤二.混合料含水率控制在3
‑
7%范围内取出,过50目筛后预压;
19.步骤三.将预压料装入模具中进行冷等静压成型,成型压力控制在35
‑
40mpa;
20.步骤四.将成型好的坯体进行干燥,条件是常压下30
‑
50℃温度段保温5
‑
10小时,100℃保温24
‑
48小时;
21.步骤五.将坯体在氮气保护下1700
‑
1750℃温度条件下烧成,保温(2
‑
5)h,得到氮化硅
‑
石英空心球陶瓷。
22.进一步的,所述增塑剂溶液中聚乙烯醇:水=1:(30
‑
40),增塑剂的添加量为氮化硅粉体、稀土氧化物粉体和石英粉体总质量的0.3
‑
0.5%。
23.进一步的,所述聚乙烯醇的分子量为500
‑
30000。
24.本发明的有益效果是:
25.本发明研制的氮化硅
‑
石英空心球陶瓷具有低密度、高气孔率、耐高温、高强度、介电常数低以及介质损耗小等特性,制备工艺相比过程简单,便于操作,工艺参数可控。
26.本发明创造性的引入石英空心球,石英空心球与氮化硅反应,生长为长径比较大的长柱状晶体,制备的材料具有实质性的优势,密度仅为1.45g/
‑
1.65g/cm3,强度可达≥70mpa,介电常数为:2.5
‑
3.5,介电损耗≤0.003:
27.其一长柱状晶体搭接成空间网络结构,石英空心球反应后留下较大尺寸的空隙,使整体材料气孔率达到50%以上;
28.其二石英空心球避免了因石英粉粒度小,反应活性大,与氮化硅容易形成玻璃相,石英粉的添加量越大越容易产生玻璃相,而玻璃相的产生会破坏长柱状晶体,进而影响介电性能;
29.其三玻璃相的产生也会影响长柱状晶体的长径比,插接效果较差,气孔率降低。
附图说明:
30.附图1是本发明氮化硅
‑
石英空心球陶瓷显微结构图:
31.附图2是本发明氮化硅
‑
石英空心球陶瓷工艺流程图:附图中:
具体实施方式:
32.在本发明的描述中具体细节仅仅是为了能够充分理解本发明的实施例,但是作为本领域的技术人员应该知道本发明的实施并不限于这些细节。另外,公知的结构和功能没有被详细的描述或者展示,以避免模糊了本发明实施例的要点。对于本领域的普通技术人员而言,可以具体情况理解上述术语在本发明中的具体含义。
33.本发明的具体实施方式:
34.一种氮化硅
‑
石英空心球陶瓷制备方法,包括以下步骤:将氮化硅粉、石英空心球、
稀土氧化物,以工业纯酒精作为介质混合,加入增塑剂溶液边搅拌边加热,至混合溶液无流动性;烘干,过筛成预压料;对预压料进行冷等静压成型,压制成素坯;对素坯进行气氛无压烧结,制备毛坯;毛坯加工,制出成品。
35.实施例1
36.称取氮化硅粉8千克,氧化钇(y2o3)1千克,石英空心球粉体1千克,酒精12升,聚乙烯醇(pva)溶液1.7升混合,加热并搅拌。待混合溶液无流动性后,放入烘箱50℃烘干6小时。取出测含水率4%后,过50目筛制出预压料。将预压料装入模具中,40mpa等静压成型。将成型好的素坯50℃烘5小时,100℃烘48小时。烘好后的素坯在氮气保护下1700℃温度,保温3h,得到氮化硅
‑
石英空心球陶瓷。
37.实施例2
38.称取氮化硅粉8.3千克,氧化钇(y2o3)0.7千克,石英空心球粉体1千克,酒精12升,聚乙烯醇(pva)溶液1.7升混合,加热并搅拌。待混合溶液无流动性后,放入烘箱50℃烘干6小时。取出测含水率4.3%后,过50目筛制出预压料。将预压料装入模具中,35mpa等静压成型。将成型好的素坯50℃烘6小时,100℃烘43小时。烘好后的素坯在氮气保护下1750℃温度,保温4小时烧成,得到氮化硅
‑
石英空心球陶瓷。
39.实施例3
40.称取氮化硅粉9.4千克,氧化镱(yb2o3)0.6千克,石英空心球粉体1千克,酒精15升,聚乙烯醇(pva)溶液1.8升混合,加热并搅拌。待混合溶液无流动性后,放入烘箱60℃烘干9小时。取出测含水率5.1%后,过50目筛制出预压料。将预压料装入模具中,35mpa等静压成型。将成型好的素坯50℃烘8小时,100℃烘40小时。烘好后的素坯在氮气保护下1750℃,保温5小时烧成,得到氮化硅
‑
石英空心球陶瓷。
41.实施例4
42.称取氮化硅粉8.9千克,氧化钐(sm2o3)0.6千克,石英空心球粉体0.5千克,酒精12升,聚乙烯醇(pva)溶液1.7升混合,加热并搅拌。待混合溶液无流动性后,放入烘箱60℃烘干5小时。取出测含水率3.9%后,过50目筛制出预压料。将预压料装入模具中,35mpa等静压成型。将成型好的素坯50℃烘8小时,100℃烘40小时。烘好后的素坯在氮气保护下1720℃,保温5小时烧成,得到氮化硅
‑
石英空心球
‑
陶瓷。
43.实施例5
44.称取氮化硅粉8.5千克,氧化镱(yb2o3)1千克,石英空心球粉体0.5千克,酒精13升,聚乙烯醇(pva)溶液1.7升混合,加热并搅拌。待混合溶液无流动性后,放入烘箱60℃烘干6小时。取出测含水率3.7%后,过50目筛制出预压料。将预压料装入模具中,35mpa等静压成型。将成型好的素坯50℃烘10小时,100℃烘36小时。烘好后的素坯在氮气保护下1730℃,保温3小时烧成,得到氮化硅
‑
石英空心球陶瓷。
45.表1、本发明不同实施例的性能指标
[0046] 密度(g/cm3)抗弯强度(mpa)介电常数介电损耗实施例一1.50722.80.001实施例二1.56942.910.0017实施例三1.54953.10.0015实施例四1.59863.20.002
实施例五1.60853.30.0018
[0047]
性能测试结果表明,按照本发明的工艺过程制备的氮化硅
‑
石英空心球陶瓷,密度仅为1.45
‑
1.65g/cm3,强度可达70
‑
95mpa,介电常数为:2.5
‑
3.5,介电损耗为≤0.003,性能指标满足低密度、高气孔率、较高强度、低介电陶瓷的要求。
[0048]
为了更加直观的展现本发明的石英空心球的工艺优势,特以本发明制备的氮化硅
‑
石英空心球陶瓷的方法和相同工艺采用等效替换的方法进行对比,
[0049]
对比例一:
[0050]
制备方法同实施例,所不同的是:本对比例的制备过程中,将石英空心粉体替换成石英空心球等质量的石英粉;
[0051]
对比例二:
[0052]
制备方法同实施例,所不同的是:本对比例的制备过程中,将石英空心粉体替换成与石英空心球等体积的石英粉;
[0053]
对比例三:
[0054]
制备方法同实施例,所不同的是:本对比例的制备过程中,将石英空心粉体替换成石英空心球等体积的粉煤灰空心微珠球;
[0055]
上述对比例获得陶瓷,按照相同方法进行检测,得出的结论与本发明的性能指标对比可知:
[0056]
具体如下:
[0057]
对比例一与本发明相比,气孔率远远低于本发明,这是由于等质量的石英粉反应后并不能留下较大尺寸的空隙,整体材料气孔率较低,
[0058]
对比例二与本发明相比,气孔率远远低于本发明,且介电性能远远差于本发明,这是由于与石英空心球等体积的石英粉的质量远远大于石英空心球,增加了石英与氮化硅的比例,石英粉的添加量越大越容易产生玻璃相,而玻璃相的产生会破坏长柱状晶体,进而影响介电性能;
[0059]
对比例三与本发明相比,气孔率稍低于本发明,但介电损耗高于本发明,
[0060]
这是由于粉煤灰空心微珠球能够起到一定的成孔剂的效果,但是由于粉煤灰并不能与氮化硅反应,生长为长径比较大的长柱状晶体,而长柱状晶体搭接成空间网络结构,石英空心球反应后留下较大尺寸的空隙,使整体材料气孔率达到50%以上;
[0061]
因此,对比例三虽然加入了煤灰空心微珠球,能够起到了成孔剂的效果一定程度上增加了气孔率,由于粉煤灰并不能与氮化硅反应,生长为长径比较大的长柱状晶体,在一定程度上影响了气孔率,更为重要的是本质上没有长柱状晶体的产生,严重影响了影响介电性能。
[0062]
综上所述:
[0063]
本发明创造性的引入石英空心球,石英空心球与氮化硅反应,生长为长径比较大的长柱状晶体,制备的材料具有实质性的优势,密度仅为1.45g/
‑
1.65g/cm3,强度可达≥70mpa,介电常数为:2.5
‑
3.5,介电损耗≤0.003:长柱状晶体的产生与石英空心球的具有实质性的意义:
[0064]
其一长柱状晶体搭接成空间网络结构,石英空心球反应后留下较大尺寸的空隙,使整体材料气孔率达到50%以上;
[0065]
其二石英空心球避免了因石英粉粒度小,反应活性大,与氮化硅容易形成玻璃相,石英粉的添加量越大越容易产生玻璃相,而玻璃相的产生会破坏长柱状晶体,进而影响介电性能;
[0066]
其三玻璃相的产生也会影响长柱状晶体的长径比,插接效果较差,气孔率降低。