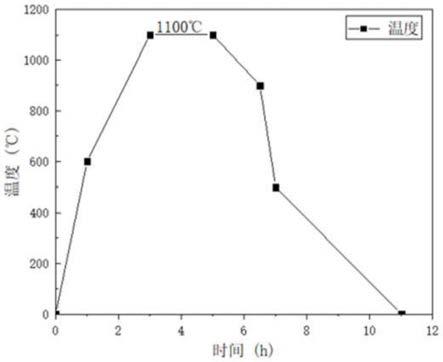
1.本发明属于生物医用材料技术领域,具体涉及一种原位掺杂石墨烯增强磷酸钙复合陶瓷及其制备方法和应用。
背景技术:2.磷酸钙生物陶瓷具有良好的生物相容性、成骨活性和骨诱导性等被应用于骨修复领域,但由于其天然脆性和低断裂韧性而不能应用于承重骨或节段骨等需要较大力学支撑强度的骨修复领域。因此,在不影响磷酸钙陶瓷骨诱导能力的基础上,提高其力学生物性能具有重要的意义。然而,材料骨诱导提高和材料力学强度增强是一对客观存在的矛盾统一体,如何解决这一矛盾已然成为磷酸钙陶瓷骨缺损修复材料研究的主要瓶颈。
3.复合第二增强相是一种提高磷酸钙陶瓷力学性能的常用方法,如中国专利cn200610013334.8公开了一种cao
‑
p2o5‑
na2o
‑
mgo玻璃增强多孔β
‑
磷酸三钙生物陶瓷制备方法,然而添加掺杂相会对陶瓷的生物学性能产生影响。由于石墨烯极佳的力学性能(已知强度最高的材料之一,理论杨氏模量达1.0tpa),同时其具有生物相容性,基于石墨烯的复合材料是石墨烯应用领域中的重要研究方向,选择石墨烯作为陶瓷复合第二相被广泛研究。近期,中国专利cn201710159945.1公开了一种石墨烯/羟基磷灰石复合陶瓷材料的制备方法,将氧化石墨烯作为增强相添加到通过化学沉淀法制备的羟基磷灰石中利用微波烧结制备得到石墨烯/羟基磷灰石复合陶瓷材料,获得耐磨性能好、无毒副作用、韧性大、生物相容性好的复合陶瓷材料。专利cn103656752.a采用选择性激光烧结技术制备了石墨烯/生物陶瓷材料,利用石墨烯优异的力学性能大幅度提高陶瓷的强度和韧性,激光烧结能够避免长时间高温作用对石墨烯带来的结构损伤,添加石墨烯的陶瓷人工骨压缩强度和断裂韧性得到明显提高。但该制备方法得到的多孔陶瓷受模具限制,不能根据需求制备特定结构。根据所需骨诱导材料的需求同时实现多孔磷酸钙陶瓷骨诱导活性和力学强度提高,目前仍缺乏行之有效的制备方法。因此,如何实现磷酸钙陶瓷在保持优异骨诱导活性的同时,进一步提高其力学性能,解决现有技术中多孔磷酸钙陶瓷面临的骨诱导优化与力学强度提高相互矛盾的难题,满足临床部分承力骨缺损再生修复的需求,是目前多孔磷酸钙陶瓷亟需解决的技术问题。
技术实现要素:4.本发明解决的技术问题是:提供一种原位掺杂石墨烯增强磷酸钙复合陶瓷及其制备方法和应用,突破多孔陶瓷制备受限的瓶颈,解决现有技术中磷酸钙陶瓷面临的骨诱导优化与力学强度提高相互矛盾的难题。
5.本发明制成的原位掺杂石墨烯增强磷酸钙复合陶瓷具有优异的生物活性。
6.本发明采用的技术方案如下:
7.本发明所述的一种原位掺杂石墨烯增强磷酸钙复合陶瓷的制备方法,将磷酸钙初始粉体按比例掺杂少层石墨烯,经湿法球磨混匀后,进行干燥筛分,分不同批次分别进行成
型,后陶瓷生胚进行真空烧结即可得致密和多孔增强磷酸钙复合陶瓷。
8.所述制备方法具体的包括以下步骤:
9.步骤1.配置一定不同比例的少层石墨烯磷酸钙初始混合粉体,粉体进行混匀,乙醇湿法球磨充分分散;
10.步骤2.将球磨后浆料进行烘干、破碎、过150目筛得石墨烯复合陶瓷粉体;
11.步骤3.粉体分别进行模压
‑
冷等静压成型,或者3d打印成型、或为发泡成型,得不同比例石墨烯混合陶瓷生胚;
12.步骤4.陶瓷生胚进行真空烧结,保温一段时间后取出得石墨烯增强磷酸钙复合陶瓷。
13.所述磷酸钙陶瓷基体为羟基磷灰石、磷酸三钙的单相或两相组成;优选地,所述致密磷酸钙陶瓷的相对密度>90%,多孔磷酸钙陶瓷的孔隙率≥50%。
14.所述掺杂石墨烯为少层石墨烯(flg),其比单层石墨烯要更加稳定。优选地,所述掺杂单层石墨烯的比例为所取磷酸钙初始粉体质量分数的0.5%~5%,更优选的,其掺杂质量分数为0.5%~1%。
15.本发明的部分实施方案中,所述湿法球磨介质为无水乙醇,行星式球磨转速为200~450rpm,球磨时间为4~42h,优选的,所述转速为350~450rpm,球磨时间为14~42h。
16.本发明的部分实施方案中,致密磷酸钙陶瓷采用压制成型,先模压再冷等静压,模压表压为1~6mpa,保压时间为10~60s,冷等静压表压为20~30mpa,保压时间为2~8min,得生胚.
17.优选地,模压所得生胚相对密度>30%,冷等静压后生胚相对密度>50%;
18.优选地,3d打印成型所得生胚孔隙率>50%。
19.本发明的部分实施方案中,所述磷酸钙陶瓷的烧结方式为真空烧结;烧结温度为900~12000,保温时间1~8h,优选的,所述烧结温度为1050~1100温,保温时间为2~4h,最优的真空烧结工艺参数为先缓慢升温(10℃0min)至800℃,稳定30min,后缓慢升温(5℃后min)至1100℃保温2h,降温分两步冷却,先降至800℃(5℃0min),后随炉冷却。
20.本发明所述的制备方法制成的石墨烯原位掺杂增强磷酸钙复合陶瓷,抗弯强度为12.37mpa~24.64mpa,抗压强度为130.90mpa~252.17mpa。作为骨缺损修复材料。
21.与现有技术相比,本发明具有以下有益效果:
22.本发明设计科学,方法简单,操作简便,通过掺杂球磨、粉体成型、真空烧结后即得到石墨烯原位增强磷酸钙复合陶瓷。本发明的石墨烯原位增强磷酸钙复合陶瓷不仅具有优异的力学强度,而且具有较好的生物学性能,且该方法对多孔磷酸钙陶瓷同样适用,满足临床部分承力骨缺损修复与再生的要求。
23.本发明通过掺杂不同质量分数石墨烯的选择,可以实现石墨烯物相的调控,从而制备得具有不同生物力学性能的复合陶瓷结构,满足临床的不同场景的需求。
24.本发明通过不同胚体成型工艺的选择,可以分别制备具有石墨烯相的致密和多孔磷酸钙复合陶瓷,制备具有不同力学性能和生物学活性的骨诱导磷酸钙陶瓷,满足临床骨缺损修复的多样化需求。
25.采用本发明方法制成的原位掺杂石墨烯增强磷酸钙复合陶瓷,不仅具有优异的力学强度(最大抗压强252.17mpa,最大抗弯强度24.64mpa),还能具有三维贯通的多孔结构,
有利于血管和骨组织的迁移生长,实现快速的骨再生,可以满足临床部分承力骨缺损修复与再生的要求。
附图说明
26.图1为本发明实施例1~8制备的原位掺杂石墨烯增强磷酸钙复合陶瓷的真空烧结温度曲线示意图(flg指代少层石墨烯)。
27.图2a为本发明实施例3中制备的原位掺杂石墨烯增强磷酸钙复合陶瓷的接触角图;
28.图2b为本发明实施例7中制备的原位掺杂石墨烯增强磷酸钙复合陶瓷的接触角图;
29.图3a为本发明实施例1~5、实施例7中制备的原位掺杂石墨烯增强磷酸钙复合陶瓷抗弯强度力学性能图;
30.图3b为本发明实施例1~5、实施例7中制备的原位掺杂石墨烯增强磷酸钙复合陶瓷抗压强度力学性能图。
具体实施方式
31.以下通过实施例形式的具体实施方式,对本发明的上述内容作进一步的详细说明。但不应将此理解为本发明上述主题的范围仅限于以下实施例。
32.本发明实施例中所述的磷酸钙初始粉体为采用化学沉淀法制备得到,制备方法见journal of american ceramic society2006:2295
‑
2297(effect of co
‑
precipitation on the low
‑
temperature sintering of biphasic calcium phosphate)。该磷酸钙初始陶瓷粉体也可采用溶胶凝胶法、模板法等方法制得,同时也可选用市售商品级磷酸钙陶瓷粉体。
33.本发明实施例中所述的抗压强度的测试方法按gb/t 8489
‑
2006的规定进行,抗弯强度的测试方法按gb/t 6569
‑
2006的规定进行。
34.本发明实施例中所述的球磨为乙醇介质湿法球磨。所述液固比为体积质量比,其中体积单位为ml时,质量单位为g。
35.本发明实施例中所述的烘干为采用常规烘箱烘干。
36.实施例1~8制备的原位掺杂石墨烯增强磷酸钙复合陶瓷的真空烧结温度曲线,如图1所示,flg指代少层石墨烯。
37.实施例1
38.(1)称取6g羟基磷灰石磷酸钙陶瓷粉体,按质量分数0.5%称量少层石墨烯,均匀分散石墨烯磷酸钙陶瓷混合粉体。将混合粉体加入石英球磨罐中,用无水乙醇进行超声分散,固定液固比为40:1,随后进行行星式球磨,转速为450rpm,球磨时间14h。
39.(2)将球磨后的浆料转移至干燥皿当中,在烘箱中60℃烘干,干料进行研磨筛分过150目筛后得混合粉体。
40.(3)称取掺杂石墨烯的混合陶瓷初始粉体0.6g进行压片成型,表压6mpa,保压15s,脱模后得陶瓷生胚,随后生胚进行冷等静压,将生胚置入气球中,利用真空泵将气球抽真空,将样品放入冷等静压机中,介质为高压耐磨机油,冷等静压机表压为30mpa,保压5min,
后取出得到致密度>50%的复合陶瓷生胚。
41.(4)复合陶瓷生胚放入氧化铝坩埚中,进行真空烧结,开始升温速率为10℃/min,到600℃后升温速率减慢,升温2h至1100℃,烧结保温2h,后缓慢降温至900℃,随后可快速降温至500可,后随炉冷却得复合陶瓷。
42.本实施例制得的制成的原位掺杂石墨烯增强磷酸钙复合陶瓷微观形貌,其掺杂石墨烯呈薄片状,断裂方式为穿晶断裂。
43.本实施例制得的制成的原位掺杂石墨烯增强磷酸钙复合陶瓷的抗弯强度图3a所示,相对于没有掺杂石墨烯作为第二相的磷酸钙初始陶瓷(抗弯强度为9mpa),掺杂石墨烯的磷酸钙复合陶瓷的抗弯强度有显著的提升,其抗弯强度为35mpa。抗压强度力学性能如图3b。
44.实施例2
45.(1)称取6g羟基磷灰石磷酸钙陶瓷粉体,按质量分数1%称量少层石墨烯,均匀分散石墨烯磷酸钙陶瓷混合粉体。将混合粉体加入石英球磨罐中,用无水乙醇进行超声分散,固定液固比为40:1,随后进行行星式球磨,转速为450rpm,球磨时间14h。
46.(2)将球磨后的浆料转移至干燥皿当中,在烘箱中60球烘干,干料进行破碎筛分过150目筛后得混合粉体。
47.(3)称取掺杂石墨烯的混合陶瓷初始粉体0.6g进行压片成型,表压6mpa,保压15s,脱模后得陶瓷生胚,随后生胚进行冷等静压,将生胚置入气球中,利用真空泵将气球抽真空,将样品放入冷等静压机中,介质为高压耐磨机油,冷等静压机表压为30mpa,保压5min,后取出得到致密度>50%的复合陶瓷生胚。
48.(4)复合陶瓷生胚放入氧化铝坩埚中,进行真空烧结,开始升温速率为10速率为生胚,到600率后升温速率减慢,升温2h至1100率,烧结保温2h,后缓慢降温至900慢,随后可快速降温至500可,后随炉冷却得复合陶瓷。
49.本实施例制得的制成的原位掺杂石墨烯增强磷酸钙复合陶瓷微观形貌,其掺杂石墨烯呈薄片状,在陶瓷基体中分散均匀,断裂方式亦为穿晶断裂。本实施例制得的制成的原位掺杂石墨烯增强磷酸钙复合陶瓷的抗弯强度如图3a所示,相对于实施例1的磷酸钙初始陶瓷(抗弯强度为35mpa),随着掺杂石墨烯的量增加,磷酸钙复合陶瓷的抗弯强度有一定的提升,其抗弯强度为45mpa。
50.实施例3
51.(1)称取6g羟基磷灰石磷酸钙陶瓷粉体,按质量分数0.1%称量少层石墨烯,均匀分散石墨烯磷酸钙陶瓷混合粉体。将混合粉体加入石英球磨罐中,用无水乙醇进行超声分散,固定液固比为40:1,随后进行行星式球磨,转速为450rpm,球磨时间14h。
52.(2)将球磨后的浆料转移至干燥皿当中,在烘箱中60球烘干,干料进行破碎筛分过150目筛后得混合粉体。
53.(3)称取掺杂石墨烯的混合陶瓷初始粉体0.6g进行压片成型,表压6mpa,保压15s,脱模后得陶瓷生胚,随后生胚进行冷等静压,将生胚置入气球中,利用真空泵将气球抽真空,将样品放入冷等静压机中,介质为高压耐磨机油,冷等静压机表压为30mpa,保压5min,后取出得到致密度>50%的复合陶瓷生胚。
54.(4)复合陶瓷生胚放入氧化铝坩埚中,进行真空烧结,开始升温速率为10合陶瓷生
胚,到600陶后升温速率减慢,升温2h至1100率,烧结保温2h,后缓慢降温至900慢,随后可快速降温至500可,后随炉冷却得复合陶瓷。
55.(5)复合陶瓷进行打磨抛光,测量接触角。
56.本实施例制得的制成的原位掺杂石墨烯增强磷酸钙复合陶瓷接触角测量如图2a所示,与不掺杂少层石墨烯的磷酸钙陶瓷相比(接触角63
°
)接触角为88
°
,亲水性下降。
57.实施例4
58.(1)称取20g羟基磷灰石磷酸钙陶瓷粉体,按质量分数1%称量少层石墨烯,均匀分散石墨烯磷酸钙陶瓷混合粉体。将混合粉体加入石英球磨罐中,用无水乙醇进行超声分散,固定液固比为20:1,随后进行球磨,转速为450rpm,球磨时间14h。
59.(2)将球磨后的浆料转移至干燥皿当中,在烘箱中60球烘干,干料进行破碎筛分,过150目筛后得混合粉体。
60.(3)称取掺杂石墨烯的混合陶瓷初始粉体15g,与光固化树脂混合配置成固含量45%的陶瓷浆料,利用光固化3d打印机按照设计好的多孔模型进行打印,其中模型的孔隙率≥其0%,清洗烘干后得到复合多孔陶瓷生胚。
61.(4)复合陶瓷生胚放入氧化铝坩埚中,进行真空烧结,开始升温速率为10合陶瓷生胚,到600陶后升温2h至1100瓷,烧结保温2h,后缓慢降温至900慢,随后可快速降温至500可,后随炉冷却得多孔复合陶瓷。
62.实施例5
63.(1)称取6g羟基磷灰石磷酸钙陶瓷粉体,按质量分数0.05%称量少层石墨烯,均匀分散石墨烯磷酸钙陶瓷混合粉体。将混合粉体加入石英球磨罐中,用无水乙醇进行超声分散,固定液固比为40:1,随后进行行星式球磨,转速为450rpm,球磨时间14h。
64.(2)将球磨后的浆料转移至干燥皿当中,在烘箱中60球烘干,干料进行破碎筛分过150目筛后得混合粉体。
65.(3)称取掺杂石墨烯的混合陶瓷初始粉体0.6g进行压片成型,表压6mpa,保压15s,脱模后得陶瓷生胚,随后生胚进行冷等静压,将生胚置入气球中,利用真空泵将气球抽真空,将样品放入冷等静压机中,介质为高压耐磨机油,冷等静压机表压为30mpa,保压5min,后取出得到致密度>50%的复合陶瓷生胚。
66.(4)复合陶瓷生胚放入氧化铝坩埚中,进行真空烧结,开始升温速率为10合陶瓷生胚,到600陶后升温速率减慢,升温2h至1100率,烧结保温2h,后缓慢降温至900慢,随后可快速降温至500可,后随炉冷却得复合陶瓷。
67.实施例6
68.(1)称取6g羟基磷灰石磷酸钙陶瓷粉体,按质量分数0.05%称量少层石墨烯,均匀分散石墨烯磷酸钙陶瓷混合粉体。将混合粉体加入石英球磨罐中,用无水乙醇进行超声分散,固定液固比为40:1,随后进行行星式球磨,转速为450rpm,球磨时间14h。
69.(2)将球磨后的浆料转移至干燥皿当中,在烘箱中60球烘干,干料进行破碎筛分过150目筛后得混合粉体。
70.(3)称取掺杂石墨烯的混合陶瓷初始粉体0.6g进行压片成型,表压10mpa,保压60s,脱模后得陶瓷生胚,得到致密度>30%的复合陶瓷生胚。
71.(4)复合陶瓷生胚放入氧化铝坩埚中,进行真空烧结,开始升温速率为10合陶瓷生
胚,到600陶后升温速率减慢,升温2h至1100率,烧结保温2h,后缓慢降温至900慢,随后可快速降温至500可,后随炉冷却得复合陶瓷。
72.本实施例制得的骨诱导磷酸钙陶瓷与经过冷等静压的磷酸钙复合陶瓷相比,其相对密度有所下降,仅有90%。
73.实施例7
74.(1)称取6g羟基磷灰石磷酸钙陶瓷粉体。将羟基磷灰石粉体加入石英球磨罐中,用无水乙醇进行超声分散,固定液固比为40:1,随后进行行星式球磨,转速为450rpm,球磨时间14h。
75.(2)将球磨后的浆料转移至干燥皿当中,在烘箱中60球烘干,干料进行破碎筛分过150目筛后得混合粉体。
76.(3)称取羟基磷灰石陶瓷初始粉体0.6g进行压片成型,表压6mpa,保压15s,脱模后得陶瓷生胚,随后生胚进行冷等静压,将生胚置入气球中,利用真空泵将气球抽真空,将样品放入冷等静压机中,介质为高压耐磨机油,冷等静压机表压为30mpa,保压5min,后取出得到致密度>50%的陶瓷生胚。
77.(4)陶瓷生胚放入氧化铝坩埚中,进行真空烧结,开始升温速率为10中,进行真,到600,后升温速率减慢,升温2h至1100率,烧结保温2h,后缓慢降温至900慢,随后可快速降温至500可,后随炉冷却得磷酸钙陶瓷。
78.实施例7中制备的原位掺杂石墨烯增强磷酸钙复合陶瓷的接触角如图2b所示。
79.实施例8
80.(1)称取6g双相磷酸钙陶瓷粉体(质量比ha:β
‑
tcp=8:2)。将粉体加入石英球磨罐中,用无水乙醇进行超声分散,固定液固比为40:1,随后进行行星式球磨,转速为450rpm,球磨时间14h。
81.(2)将球磨后的浆料转移至干燥皿当中,在烘箱中60球烘干,干料进行破碎筛分过150目筛后得混合粉体。
82.(3)称取陶瓷初始粉体0.6g进行压片成型,表压6mpa,保压15s,脱模后得陶瓷生胚,随后生胚进行冷等静压,将生胚置入气球中,利用真空泵将气球抽真空,将样品放入冷等静压机中,介质为高压耐磨机油,冷等静压机表压为30mpa,保压5min,后取出得到致密度>50%的陶瓷生胚。
83.(4)陶瓷生胚放入氧化铝坩埚中,进行真空烧结,开始升温速率为10瓷生胚放入,到600生后升温速率减慢,升温2h至1100℃,烧结保温2h,后缓慢降温至900慢,随后可快速降温至500可,后随炉冷却得磷酸钙陶瓷。
84.上述实施例仅例示性说明本发明的原理及其功效,而非用于限制本发明。任何熟悉此技术的人士皆可在不违背本发明的精神及范畴下,对上述实施例进行修饰或改变。因此,举凡所属技术领域中具有通常知识者在未脱离本发明所揭示的精神与技术思想下所完成的一切等效修饰或改变,仍应由本发明的权利要求所涵盖。