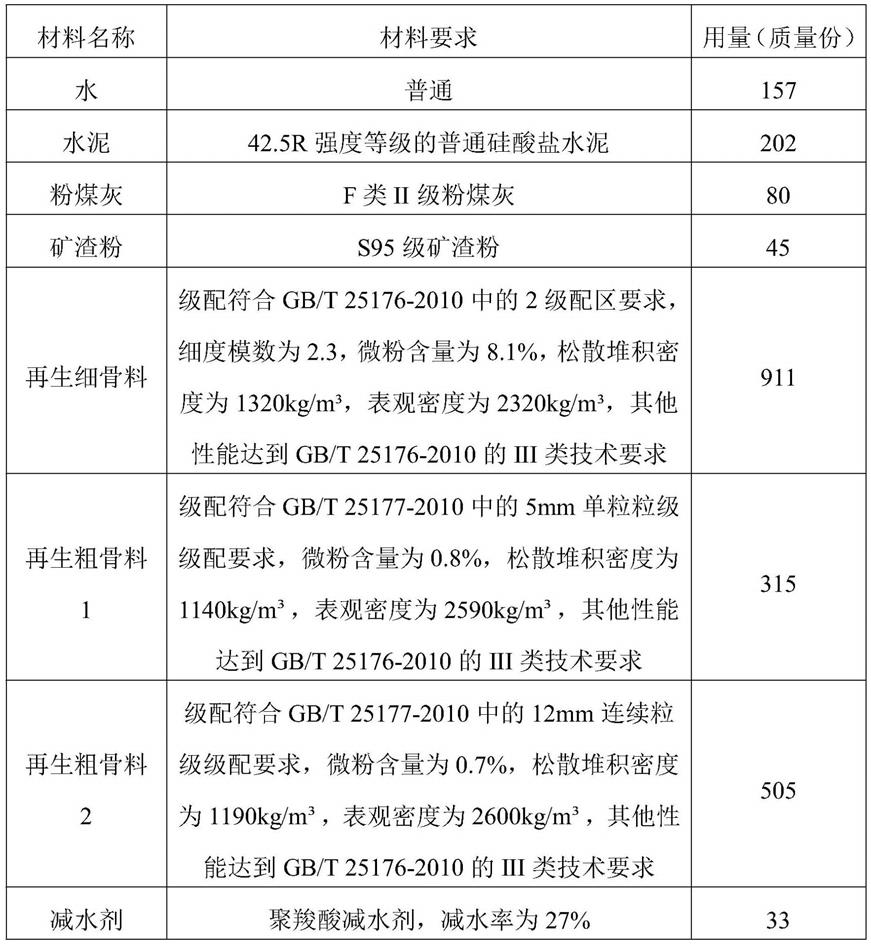
1.本发明涉及混凝土技术领域,尤其涉及一种全再生骨料的混凝土 以及制备方法。
背景技术:2.随着我国经济的迅速发展和城市化的大力发展,原有的自然生态 体系受到了极大的冲击与破坏。要全力推进“资源全面节约和循环利 用和加强固体废弃物和垃圾处置”等实施方略。
3.随着工业化、城市化的加速,也伴随着建筑业的快速发展,这些 给我们带来了高效便捷的生活方式的同时,也产生了一定的负面效 应。如大量建筑垃圾的产生不仅占用宝贵的耕地资源,也给我们的生 产生活环境带来及较为严重的污染,直接或间接的危害到大气环境、 土壤环境与地下水环境,后患无穷。据统计现阶段我国的建筑垃圾的 数量已经占到城市垃圾总量的1/3以上,每年建筑垃圾产量超过35亿 吨,且以每年10%的速度增长。其中仅拆除建筑垃圾所占超18亿吨。 如此大体量的建筑垃圾,如何妥善处理处置、化害为利、变废为宝、 保护环境、实现建筑垃圾的资源化利用,已成为我们的燃眉之急。
4.如何合理有效的利用建筑废弃物已成为十分严峻的问题。其中利 用建筑垃圾循环利用制备绿色建筑材料,得到了国内外研究学者以及 产业化人员以及政策制定者的一致关注,2012年住建部将深圳市列 为首个“建筑废弃物减排与综合利用试点城市”,2017年科技部相继 将“工业与城市大宗固废制备绿色建材关键技术研究与应用”和“建 筑垃圾资源化全产业链高效利用关键技术研究与应用”列入国家重点 研发计划“绿色建筑与建筑工业化”重点专项。关于建筑固体废弃物 的工业化利用已经成为我们现阶段对于建筑固体废弃物处置的着力 点。
5.查阅现有的文献资料,对建筑废弃物再生骨料的综合回收利用已 有一定的研究,分析这些文献,主要包括以下内容:
6.1.对建筑废弃物再生骨料的不同预处理,在再生骨料的综合利 用环节中,再生骨料的质量品质对再生骨料混凝土的性能有较大影 响,业内也对再生骨料的预处理进行了不同路线的探究,主要处理对 象为再生骨料表面的复杂界面结构(旧骨料—旧浆料、旧骨料—新浆 料、旧浆料—新浆料),处理方式主要包括有物理强化、化学强化、 以及复合强化等,物理强化主要通过加热研磨、偏心装置研磨、颚式 破碎机破碎、球磨机球磨、转筒式搅拌机干拌等方法,其核心在于通 过上述一系列物理作用使得再生骨料表面松散砂浆脱落,能形成表面 致密且能与后拌和砂浆形成紧密咬合的再生骨料界面。
7.化学强化则是通过浸渍或喷淋水泥净浆、聚乙烯醇溶液、水玻璃 溶液、纳米二氧化硅溶液、渗透结晶材料、废弃pe塑料等,利用上述 材料对再生骨料粗糙表面和所存在的微细裂纹进行修补,从而改善再 生骨料性能,复合强化则是通过物理与化学相结合的办法强化骨料性 能。
8.2.对建筑废弃物再生骨料取代率的探究,在现有研究中,考虑再 生骨料对混凝土工作性能的影响,现阶段各实施案例较为复杂,分别 有部分取代、全部取代、单一取代和复
合取代等,jgj/t240-2011《再 生骨料应用技术规程》中对再生骨料的取代率进行阐述,对i、ii、iii 型的再生骨料应用场景进行了一定的限制。故在一定程度上限制了再 生骨料的利用率。
9.专利文献201110336012.8公开了一种建筑垃圾再生骨料素砼桩, 主要由水泥、建筑垃圾粗骨料和建筑垃圾细骨制备,建筑垃圾粗骨料 粒径为5~40毫米,建筑垃圾细骨料的粒径为2~5毫米。水泥、建筑 垃圾粗骨料和建筑垃圾细骨料的混合重量比为1:(3~5):(1.5~3), 这种混凝土虽然添加了羟甲基纤维素钠,但是其强度仍然较低,工作 性能和耐久性能较差。
技术实现要素:10.鉴于此,有必要提供一种全再生骨料的混凝土以及制备方法,有 利于提升高混凝土的工作性能和耐久性能。
11.本发明第一方面提供一种全再生骨料的混凝土,其特征在于,所 述混凝土包括以下重量份的组分:水泥为200-350份,粉煤灰为80-100 份,矿渣粉为40-100份,再生细骨料为800-1000份,再生粗骨料1 为200-400份,再生粗骨料2为500-600份,混凝土外加剂为30-50 份,其中,再生细骨料性:(再生粗骨料性1+再生粗骨料性2)为1: (0.80-1.0),再生粗骨料性1:再生粗骨料性2为1:(1.5-2.1), 再生细骨料细度模数为2.3-3.0,再生细骨料1的颗粒粒径为 5mm-10mm,再生粗骨料性2颗粒粒径为10mm-25mm,外加剂为聚 羧酸减水剂并且其减水率不小于27%。
12.本发明第二方面提供一种用于制备所述的全再生骨料的混凝土 的方法,将上述原料除外加剂外,按照确定比例加入搅拌容器中预先 搅拌均匀,然后加入外加剂和水进行搅拌1min-5min,然后静置 1min-5min,最后再搅拌1min-5min既得所述全再生骨料的高性能混 凝土。
13.相较于现有技术,本发明采用全再生骨料,不需要使用天然骨料 (例如砂石)即可实现混凝土的制备,所制备的混凝土具有优异的工 作性能和耐久性能。
具体实施方式
14.下面将对本发明实施例中的技术方案进行清楚、完整地描述,显 然,所描述的实施例仅仅是本发明一部分实施例,而不是全部的实施 例。基于本发明的实施例,本领域普通技术人员在没有做出创造性劳 动的前提下所获得所有其他实施例,都属于本发明的保护范围。
15.本发明提供以下实施例和对比例。
16.实施例1
[0017][0018]
实施例1的混凝土制备方法如下:
[0019]
将上述原料除外加剂外,按照确定比例加入搅拌容器中预先搅拌 均匀,然后加入外加剂和水进行搅拌5min,然后静置5min,最后再 搅拌3min,得到混凝土。
[0020]
实施例1的混凝土性能如下:
[0021][0022]
实施例2
[0023][0024]
实施例2的混凝土制备方法如下:
[0025]
将上述原料除外加剂外,按照确定比例加入搅拌容器中预先搅拌 均匀,然后加入外加剂和水进行搅拌2min,然后静置3min,最后再 搅拌5min,得到混凝土。
[0026]
实施例2的混凝土性能如下:
[0027][0028]
实施例3
[0029][0030]
实施例3的混凝土制备方法如下:
[0031]
将上述原料除外加剂外,按照确定比例加入搅拌容器中预先搅拌 均匀,然后加入外加剂和水进行搅拌5min,然后静置5min,最后再 搅拌5min,得到混凝土。
[0032]
实施例3的混凝土性能如下:
[0033][0034]
对比例1
[0035]
材料名称材料要求用量(质量份)水普通157水泥44r强度等级的普通硅酸盐水泥202粉煤灰f类ii级粉煤灰80
矿渣粉s95级矿渣粉45再生细骨料细度模数为3911再生粗骨料单粒粒级30mm911减水剂聚羧酸减水剂,减水率为20%33
[0036]
将上述原料除外加剂外,按照确定比例加入搅拌容器中预先搅拌 均匀,然后加入外加剂和水进行搅拌5min,得到混凝土。
[0037]
对比例1的混凝土性能如下:
[0038][0039]
对比例2
[0040][0041]
[0042]
将上述原料除外加剂外,按照确定比例加入搅拌容器中预先搅拌 均匀,然后加入外加剂和水进行搅拌5min,得到混凝土。
[0043]
对比例2的混凝土性能如下:
[0044][0045]
以上对比例1和对比例2的测试结果可知,拌合物在1小时后即没 有任何塌落度和扩展度,流动性以及和易性很差,无法用于施工成型, 无法测试强度数值。
[0046]
通过以上实施例1-3和对比例1-2可知,本发明所提供的全再生骨 料的混凝土,有利于提升高混凝土的工作性能和耐久性能。发明人研 究认为,主要原因如下:本发明通过选用全再生骨料,包括特定粒径 要求的再生细骨料、再生粗骨料1、再生粗骨料2,并且再生细骨料性: (再生粗骨料性1+再生粗骨料性2)为1:(0.80-1.0),再生粗骨料 性1:再生粗骨料性2为1:(1.5-2.1),外加剂选用减水率不小于27% 的聚羧酸减水剂。可以实现再生骨料之间的复配,可以实现再生骨料 之间的紧密堆积,能实现浆料对全再生骨料旧骨料—旧浆料界面结构 进行包裹修复,高流动度浆料可浸入到旧骨料—旧浆料间的缝隙孔洞 中进行有效填充,同时高流动度浆料也可有效实现旧浆料—新浆料间 的填充包裹,从整体上降低全再生骨料混凝土的孔隙率,具有良好的 塌落度和扩展度,利于工程运输、浇筑与成型,可以提升混凝土工作 性和耐久性;另外,由于全再生骨料具有较高的吸水率,骨料开口孔 隙较多,因而在拌和过程中高流动度浆料会不断填充挤压孔隙内部气 体释放,造成拌合物内部孔隙率较高,本发明通过控制拌合过程,预 先搅拌1-5min后采取静置1-5min的方式,充分释放再生骨料内部开口 孔隙气体,实现浆料对再生骨料复杂界面的充分包裹修复,后再搅拌 1-5min,释放出前期高流动度浆料从再生骨料中置换处并悬浮在混凝 土拌合物中的气体,实现混凝土拌合物的匀质密实,降低混凝体内部 孔隙率,同时选用减水率不小于27%的聚羧酸减水剂,使得混凝土获 得大流动度的同时具有优异的保水性和凝聚性。可以克服现有建筑废 弃物再生骨料吸水率较高、压碎值等物理指标不稳定且离散型较差、 内部结构缺陷较多且与其后胶结料咬合性较差等问题。
[0047]
上述实施例为本发明较佳的实施方式,但本发明的实施方式并不 受上述实施例的限制,以上实施方式仅是用于解释权利要求书。然本 发明的保护范围并不局限于说明书。任何熟悉本技术领域的技术人员 在本发明披露的技术范围内,可轻易想到的变化或者替换,都包含在 本发明的保护范围之内。