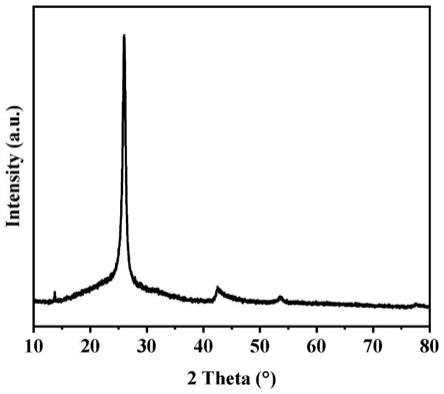
1.本发明涉及石墨烯材料技术领域,尤其涉及一种石墨烯的制备方法。
背景技术:2.自2004年石墨烯材料发现以来,石墨烯以其原子级厚度、独特的电性能、高机械强度、高导热性和高比表面积而受到广泛研究。基于这些优势,目前石墨烯材料以石墨烯、氧化石墨烯、还原氧化石墨烯和cvd生长薄膜等产品形式在能源领域、电子器件领域、导电薄膜和复合材料等方面均有一定商业化应用。然而,受石墨烯产量及产品质量制约,仍未实现大规模工业化生产和应用。
技术实现要素:3.本发明的目的在于提供一种石墨烯的制备方法,所述制备方法简单,可实现工业化生产。
4.为了实现上述发明目的,本发明提供以下技术方案:
5.本发明提供了一种石墨烯的制备方法,包括以下步骤:
6.将有机碳源和还原性金属混合后,在保护气氛中依次进行第一煅烧和第二煅烧,得到所述石墨烯;
7.所述第一煅烧的温度为500~650℃;
8.所述第二煅烧的温度为700~1200℃。
9.优选的,所述有机碳源包括三聚氰胺、双氰胺、葡萄糖、聚酰亚胺和聚氯乙烯中的一种或几种。
10.优选的,所述还原性金属包括镁、铝和锌中的一种或几种。
11.优选的,所述有机碳源与还原性金属的质量比为(1~3):1。
12.优选的,升温至所述第一煅烧温度的升温速率为5~55℃/min。
13.优选的,所述第一煅烧的时间为60~180min。
14.优选的,所述第二煅烧的温度是由所述第一煅烧的温度为起始温度进行升温得到的;
15.所述升温的升温速率为5~20℃/min。
16.优选的,所述第二煅烧的时间为20~60min。
17.优选的,所述第二煅烧完成后,还包括依次进行的第一清洗、抽滤、第二清洗和干燥。
18.优选的,所述第一清洗的方式为超声清洗,所述第一清洗采用的清洗剂为盐酸;
19.所述第二清洗包括依次采用水和乙醇进行清洗。
20.本发明提供了一种石墨烯的制备方法,包括以下步骤:将有机碳源和还原性金属混合后,在保护气氛中依次进行第一煅烧和第二煅烧,得到所述石墨烯;所述第一煅烧的温度为500~650℃;所述第二煅烧的温度为700~1200℃。本发明所述的制备方法中直接将有
机碳源和还原性金属进行混合,为后续有机碳源转变为非晶碳或碳化物中间体后还能保证所述中间体与还原性金属粉充分接触提供条件,同时,在整个反应过程中不需要任何的溶剂参与反应,第一煅烧使有机碳源煅烧后生成非晶碳或碳化物中间体,第二煅烧使还原性金属与中间体反应,脱去中间体中的杂元素变为金属盐,中间体发生石墨化反应变成高结晶石墨烯。
附图说明
21.图1为实施例1制备得到的石墨烯的xrd图;
22.图2为实施例1制备得到的石墨烯的总谱的xps图;
23.图3为实施例1制备得到的石墨烯的sem图;
24.图4为实施例1制备得到的石墨烯的tem图;
25.图5为实施例1制备得到的石墨烯分散在硅片上的afm图;
26.图6为实施例1~4制备得到的石墨烯的拉曼光谱图;
27.图7为实施例1和4制备得到的石墨烯的xrd图;
28.图8为实施例1和4制备得到的石墨烯的xps图;
29.图9为实施例1制备得到的石墨烯和对比例1~3在不同压强下的电导率曲线;
30.图10为实施例4、6~7和12~13制备得到的石墨烯的拉曼光谱图;
31.图11为实施例4~5和实施例8~9制备得到的石墨烯的拉曼光谱图;
32.图12为实施例4、10和11制备得到的石墨烯的拉曼光谱图;
33.图13为实施例4、14、15和16制备得到的石墨烯的拉曼光谱图。
具体实施方式
34.本发明提供了一种石墨烯的制备方法,包括以下步骤:
35.将有机碳源和还原性金属混合后,在保护气氛中依次进行第一煅烧和第二煅烧,得到所述石墨烯;
36.所述第一煅烧的温度为500~650℃;
37.所述第二煅烧的温度为700~1200℃。
38.在本发明中,若无特殊说明,所有制备原料均为本领域技术人员熟知的市售产品。
39.在本发明中,在整个反应过程中不需要任何的溶剂参与反应,
40.在本发明中,所述有机碳源优选包括三聚氰胺、双氰胺、葡萄糖、聚酰亚胺和聚氯乙烯中的一种或几种;当所述有机碳源为上述具体选择中的两种以上时,本发明对上述具体物质的配比没有任何特殊的限定,案任意配比进行混合即可。
41.在本发明中,所述有机碳源优选为粉末形式;所述有机碳源的粒径优选为50~400目,更优选为300~400目。
42.在本发明中,所述还原性金属优选包括镁、铝和锌中的一种或几种;当所述还原性金属为上述具体选择中的两种以上时,本发明对上述具体物质的配比没有任何特殊的限定,按任意配比进行混合即可。
43.在本发明中,所述还原性金属优选为粉末状;所述还原性金属的粒径优选为50~400目,更优选为100~200目。
44.在本发明中,所述有机碳源与还原性金属的质量比优选为(1~3):1,更优选为(1.8~2.2):1,更优选为2:1。
45.本发明对所述混合的方式没有任何特殊的限定,采用本领域技术人员熟知的方式进行并能够保证所述三聚氰胺和镁混合均匀即可。在本发明的实施例中,所述混合的方式为震荡摇匀。
46.在本发明中,所述保护气氛优选为惰性气氛,更优选为氩气气氛。
47.在本发明中,所述第一煅烧的温度为500~650℃,优选为530~560℃,最优选为550℃;时间优选为60~180min,更优选为85~95min,最优选为90min。在本发明中,升温至所述第一煅烧温度的升温速率优选为5~55℃/min,更优选为48~52℃/min,最优选为50℃/min。
48.在本发明中,所述第二煅烧的温度优选是由所述第一煅烧的温度为起始温度进行升温得到的;所述第二煅烧的温度为700~1200℃,优选为900~1200℃,最优选为1000~1200℃;时间优选为20~60min,更优选为25~35min,最优选为30min。在本发明中,升温至所述第二煅烧的温度的升温速率优选为5~20℃/min,更优选为12~13℃/min,最优选为12.5℃/min。
49.在本发明中,所述第一煅烧和第二煅烧优选采用刚玉舟作为容器并置于管式炉中进行。
50.所述第二煅烧完成后,本发明还优选包括冷却;所述冷却优选为自然冷却,所述冷却后的终止温度优选为室温。
51.冷却至室温后,本发明还优选包括依次进行的第一清洗、抽滤、第二清洗和干燥;所述第一清洗的方式优选为超声清洗,所述第一清洗采用的清洗剂优选为盐酸;所述盐酸的浓度优选为0.5m。本发明对所述超声清洗的频率没有任何特殊的限定,采用本领域技术人员熟知的频率使其在20min内清洗干净即可。
52.本发明对所述抽滤的过程没有任何特殊的限定,采用本领域技术人员熟知的过程进行即可。
53.在本发明中,所述第二清洗优选包括依次采用水和乙醇进行清洗;本发明对所述清洗的过程没有任何特殊的限定,采用本领域技术人员熟知ide过程进行即可。
54.在本发明中,所述干燥优选为真空干燥;所述真空干燥的温度优选为45℃,本发明对所述真空干燥的时间没有任何特殊的限定,采用本领域技术人员熟知的时间能够保证制备得到的石墨烯完全干燥即可。
55.下面结合实施例对本发明提供的石墨烯的制备方法进行详细的说明,但是不能把它们理解为对本发明保护范围的限定。
56.实施例1
57.将1000mg三聚氰胺和500mg镁粉(粒径为100~200目)震荡摇匀得到混合粉末;
58.将所述混合粉末转移至刚玉舟内置于管式炉中,在氩气气氛中,以50℃/min的升温速率升温至550℃保温90min后,再以12.5℃/min的升温速率升温至1200℃保温30min后,自然冷却至室温,将得到的粗产物置于0.5m盐酸中超声清洗20min,抽滤,再依次用200ml去离子水和200ml乙醇进行清洗后,45℃真空干燥,得到石墨烯。
59.实施例2
60.将1000mg三聚氰胺和500mg镁粉(粒径为100~200目)震荡摇匀得到混合粉末;
61.将所述混合粉末转移至刚玉舟内置于管式炉中,在氩气气氛中,以50℃/min的升温速率升温至550℃保温90min后,再以12.5℃/min的升温速率升温至1000℃保温30min后,自然冷却至室温,将得到的粗产物置于0.5m盐酸中超声清洗20min,抽滤,再依次用200ml去离子水和200ml乙醇进行清洗后,45℃真空干燥,得到石墨烯。
62.实施例3
63.将1000mg三聚氰胺和500mg镁粉(粒径为100~200目)震荡摇匀得到混合粉末;
64.将所述混合粉末转移至刚玉舟内置于管式炉中,在氩气气氛中,以50℃/min的升温速率升温至550℃保温90min后,再以12.5℃/min的升温速率升温至900℃保温30min后,自然冷却至室温,将得到的粗产物置于0.5m盐酸中超声清洗20min,抽滤,再依次用200ml去离子水和200ml乙醇进行清洗后,45℃真空干燥,得到石墨烯。
65.实施例4
66.将1000mg三聚氰胺和500mg镁粉(粒径为100~200目)震荡摇匀得到混合粉末;
67.将所述混合粉末转移至刚玉舟内置于管式炉中,在氩气气氛中,以50℃/min的升温速率升温至550℃保温90min后,再以12.5℃/min的升温速率升温至700℃保温30min后,自然冷却至室温,将得到的粗产物置于0.5m盐酸中超声清洗20min,抽滤,再依次用200ml去离子水和200ml乙醇进行清洗后,45℃真空干燥,得到石墨烯。
68.实施例5
69.将1000mg三聚氰胺和600mg镁粉(粒径为100~200目)震荡摇匀得到混合粉末;
70.将所述混合粉末转移至刚玉舟内置于管式炉中,在氩气气氛中,以50℃/min的升温速率升温至550℃保温90min后,再以12.5℃/min的升温速率升温至700℃保温30min后,自然冷却至室温,将得到的粗产物置于0.5m盐酸中超声清洗20min,抽滤,再依次用200ml去离子水和200ml乙醇进行清洗后,45℃真空干燥,得到石墨烯。
71.实施例6
72.将1000mg聚氯乙烯和500mg镁粉(粒径为100~200目)震荡摇匀得到混合粉末;
73.将所述混合粉末转移至刚玉舟内置于管式炉中,在氩气气氛中,以50℃/min的升温速率升温至550℃保温90min后,再以12.5℃/min的升温速率升温至700℃保温30min后,自然冷却至室温,将得到的粗产物置于0.5m盐酸中超声清洗20min,抽滤,再依次用200ml去离子水和200ml乙醇进行清洗后,45℃真空干燥,得到石墨烯。
74.实施例7
75.将1000mg双氰胺和500mg镁粉(粒径为100~200目)震荡摇匀得到混合粉末;
76.将所述混合粉末转移至刚玉舟内置于管式炉中,在氩气气氛中,以50℃/min的升温速率升温至550℃保温90min后,再以12.5℃/min的升温速率升温至700℃保温30min后,自然冷却至室温,将得到的粗产物置于0.5m盐酸中超声清洗20min,抽滤,再依次用200ml去离子水和200ml乙醇进行清洗后,45℃真空干燥,得到石墨烯。
77.实施例8
78.将1000mg三聚氰胺和400mg镁粉(粒径为100~200目)震荡摇匀得到混合粉末;
79.将所述混合粉末转移至刚玉舟内置于管式炉中,在氩气气氛中,以50℃/min的升温速率升温至550℃保温90min后,再以12.5℃/min的升温速率升温至700℃保温30min后,
自然冷却至室温,将得到的粗产物置于0.5m盐酸中超声清洗20min,抽滤,再依次用200ml去离子水和200ml乙醇进行清洗后,45℃真空干燥,得到石墨烯。
80.实施例9
81.将1000mg三聚氰胺和700mg镁粉(粒径为100~200目)震荡摇匀得到混合粉末;
82.将所述混合粉末转移至刚玉舟内置于管式炉中,在氩气气氛中,以50℃/min的升温速率升温至550℃保温90min后,再以12.5℃/min的升温速率升温至700℃保温30min后,自然冷却至室温,将得到的粗产物置于0.5m盐酸中超声清洗20min,抽滤,再依次用200ml去离子水和200ml乙醇进行清洗后,45℃真空干燥,得到石墨烯。
83.实施例10
84.将1000mg三聚氰胺和500mg铝粉(粒径为100~200目)震荡摇匀得到混合粉末;
85.将所述混合粉末转移至刚玉舟内置于管式炉中,在氩气气氛中,以50℃/min的升温速率升温至550℃保温90min后,再以12.5℃/min的升温速率升温至700℃保温30min后,自然冷却至室温,将得到的粗产物置于0.5m盐酸中超声清洗20min,抽滤,再依次用200ml去离子水和200ml乙醇进行清洗后,45℃真空干燥,得到石墨烯。
86.实施例11
87.将1000mg三聚氰胺和500mg锌粉(粒径为100~200目)震荡摇匀得到混合粉末;
88.将所述混合粉末转移至刚玉舟内置于管式炉中,在氩气气氛中,以50℃/min的升温速率升温至550℃保温90min后,再以12.5℃/min的升温速率升温至700℃保温30min后,自然冷却至室温,将得到的粗产物置于0.5m盐酸中超声清洗20min,抽滤,再依次用200ml去离子水和200ml乙醇进行清洗后,45℃真空干燥,得到石墨烯。
89.实施例12
90.将1000mg聚酰亚胺和500mg镁粉(粒径为100~200目)震荡摇匀得到混合粉末;
91.将所述混合粉末转移至刚玉舟内置于管式炉中,在氩气气氛中,以50℃/min的升温速率升温至550℃保温90min后,再以12.5℃/min的升温速率升温至700℃保温30min后,自然冷却至室温,将得到的粗产物置于0.5m盐酸中超声清洗20min,抽滤,再依次用200ml去离子水和200ml乙醇进行清洗后,45℃真空干燥,得到石墨烯。
92.实施例13
93.将1000mg葡萄糖和500mg镁粉(粒径为100~200目)震荡摇匀得到混合粉末;
94.将所述混合粉末转移至刚玉舟内置于管式炉中,在氩气气氛中,以50℃/min的升温速率升温至550℃保温90min后,再以12.5℃/min的升温速率升温至700℃保温30min后,自然冷却至室温,将得到的粗产物置于0.5m盐酸中超声清洗20min,抽滤,再依次用200ml去离子水和200ml乙醇进行清洗后,45℃真空干燥,得到石墨烯。
95.实施例14
96.将1000mg三聚氰胺和500mg镁粉(粒径为100~200目)震荡摇匀得到混合粉末;
97.将所述混合粉末转移至刚玉舟内置于管式炉中,在氩气气氛中,以50℃/min的升温速率升温至500℃保温90min后,再以12.5℃/min的升温速率升温至700℃保温30min后,自然冷却至室温,将得到的粗产物置于0.5m盐酸中超声清洗20min,抽滤,再依次用200ml去离子水和200ml乙醇进行清洗后,45℃真空干燥,得到石墨烯。
98.实施例15
99.将1000mg三聚氰胺和500mg镁粉(粒径为100~200目)震荡摇匀得到混合粉末;
100.将所述混合粉末转移至刚玉舟内置于管式炉中,在氩气气氛中,以50℃/min的升温速率升温至600℃保温90min后,再以12.5℃/min的升温速率升温至700℃保温30min后,自然冷却至室温,将得到的粗产物置于0.5m盐酸中超声清洗20min,抽滤,再依次用200ml去离子水和200ml乙醇进行清洗后,45℃真空干燥,得到石墨烯。
101.实施例16
102.将1000mg三聚氰胺和500mg镁粉(粒径为100~200目)震荡摇匀得到混合粉末;
103.将所述混合粉末转移至刚玉舟内置于管式炉中,在氩气气氛中,以50℃/min的升温速率升温至650℃保温90min后,再以12.5℃/min的升温速率升温至700℃保温30min后,自然冷却至室温,将得到的粗产物置于0.5m盐酸中超声清洗20min,抽滤,再依次用200ml去离子水和200ml乙醇进行清洗后,45℃真空干燥,得到石墨烯。
104.对比例1
105.商用导电剂乙炔黑(购于合肥科晶材料技术有限公司)。
106.对比例2
107.商用导电剂科琴黑(购于合肥科晶材料技术有限公司)。
108.对比例3
109.商用导电剂superp(购于合肥科晶材料技术有限公司)。
110.测试例
111.将实施例1制备得到的石墨烯进行xrd测试,测试结果如图1所示,由图1可知,实施例1制备得到的石墨烯的峰与石墨烯结构的标准pdf卡片no.75-1621吻合较好,尖锐的(002)晶面峰表明石墨烯产物的高结晶度;
112.将实施例1制备得到的石墨烯进行xps测试,测试结果如图2所示,其中图2为xps总谱,由图2可知,所述石墨烯主要由c组成,只含有极少量的n与o;
113.将实施例1制备得到的石墨烯进行sem测试,测试结果如图3所示;将实施例1制备得到的石墨烯进行tem测试,测试结果如图4所示,由图3~4可知,所述石墨烯主要由透明、薄片状石墨烯组成,片径约为1μm;所述石墨烯呈六方排列的碳原子;
114.将实施例1制备得到的石墨烯分散在硅片上进行原子力显微镜分析,测试结果如图5所示,由图5可知,所述石墨烯的厚度约为3nm,由于单层石墨烯的厚度约为0.35nm,因此制备得到的石墨烯的层数约为8~9层;
115.石墨烯的拉曼光谱有三个主峰,位于1350cm-1
的d峰,主要与石墨烯中的缺陷含量相关;位于1580cm-1
的g峰,来源于石墨烯中sp2碳原子的面内振动;以及位于2700cm-1
附近的2d峰,2d峰是d峰的二阶模式。通常用d峰和g峰的强度比(id/g)来表征石墨烯材料的缺陷密度。在上述基础上,将实施例1~4制备得到的石墨烯进行拉曼光谱测试,测试结果如图6所示,由图6可知,随着第二煅烧过程中的温度的逐步升高id/g逐步降低,表明缺陷含量显著减少,在1000~1200℃达到最优。从2d峰的峰形及i2d/g随着脱氮温度升高的实验结果中也可以得出更高的脱氮温度导致更高的石墨烯结晶度;
116.将实施例1和4制备得到的石墨烯进行xrd测试,测试结果如图7所示,由图7可知,在1200℃下合成的石墨烯的xrd(002)晶面峰具有更窄的峰形,这表明实施例4的石墨烯产物具有更高的结晶程度;
117.将实施例1和4制备得到的石墨烯进行xps测试,测试结果如图8所示,由图8可知,xps总谱中可以明显看出1200℃下的产物的氧含量更低,表明1200℃下得到的石墨烯具有更高的质量;
118.将实施例1制备得到的石墨烯和对比例1~3在不同压强下进行电导率测试,测试结果如图9所示,由图9可知,在25℃下,随着压强从2mpa提高到10mpa,实施例1制备得到的石墨烯电导率从14.8s/cm提高到41.5s/cm。在10mpa压力下压实粉末后,所述石墨烯的电导率是常见商用导电剂乙炔黑,科琴黑以及superp的4倍左右;
119.将实施例4、6~7、12~13制备得到的石墨烯进行拉曼光谱测试,测试结果如图10所示,由图10可知,三聚氰胺前体相比其余含氮前驱体所合成的石墨烯具有更低的缺陷密度以及更高的结晶度,得益于三聚氰胺相比其他含氮前驱体具有更高聚合度的三嗪结构,所合成的c3n4中间体具有更大的晶粒与更高的结晶度,从而在经过镁粉脱氮还原后所得到的石墨烯纳米片具有更高的质量;
120.将实施例4~5和实施例8~9制备得到的石墨烯进行拉曼光谱测试,测试结果如图11所示,由图11可知,相对于实施例4~5和实施例9来说,实施例8制备得到的石墨烯缺陷高,结晶程度低,其结果是由于缺量的镁粉含量在脱氮还原步骤不能充分还原c3n4,所得到的石墨烯含有更多的缺陷;相对于实施例4~5和实施例8来说,实施例9采用更多的镁粉,但是在反应完成后混合产物中含有过多的未反应镁粉,导致在盐酸清洗步骤汇总镁粉与盐酸反应放出过多的热,导致空气气氛下混合在其中的石墨烯的晶型结构被破坏产生缺陷。
121.将实施例4、10、11制备得到的石墨烯进行拉曼光谱测试,测试结果如图12所示,由图12可知,随着还原性金属原料的还原性增强(mg》al》zn),所得到的石墨烯产物的缺陷密度越小,结晶程度越高。
122.将实施例4、14、15、16制备得到的石墨烯进行拉曼光谱测试,测试结果如图13所示,由图13可知,第一煅烧温度在500~650℃的范围内都可以得到较好质量的石墨烯产物,综合缺陷含量及结晶程度,550℃条件较优。
123.以上所述仅是本发明的优选实施方式,应当指出,对于本技术领域的普通技术人员来说,在不脱离本发明原理的前提下,还可以做出若干改进和润饰,这些改进和润饰也应视为本发明的保护范围。