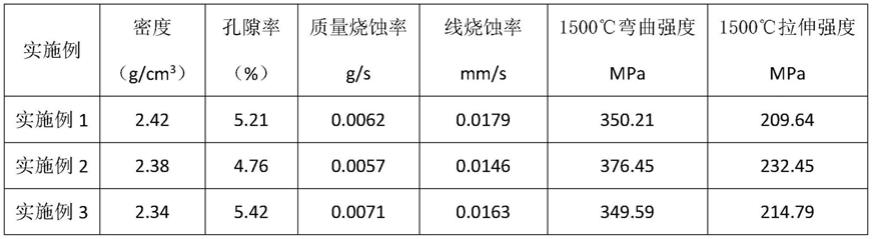
1.本发明涉及陶瓷基复合材料制备领域,特别涉及一种超高温碳化硅陶瓷基复合材料的制备方法及一种超高温碳化硅陶瓷基复合材料。
背景技术:2.为了满足新型航空航天器热端部件如超音速飞行器头锥、翼前缘及航空发动机等愈加苛刻的服役环境,需要发展更长寿命、耐更高温度和结构功能一体化的超高温陶瓷基复合材料。目前,世界范围内研究最多、应用最成功和最广泛的便是碳化硅陶瓷基复合材料(sic matrix ceramic composites,cmc
–
sic)。
3.但是,在1500℃以上,sic氧化产物sio2的抗氧化保护作用被严重削弱。为提高cmc
–
sic复合材料的耐高温、抗烧蚀和抗氧化性能,以满足其在高超音速飞行器及航空发动机上的应用,需对其进行基体改性。
4.目前对基体的改性尚缺乏成功将hf、zr、ta等抗烧蚀组元引入碳化硅陶瓷基以提高碳化硅陶瓷基复合材料的耐高温能力的方法和手段。
技术实现要素:5.本发明公开了一种超高温碳化硅陶瓷基复合材料的制备方法,该方法提高了制成的碳化硅陶瓷基复合材料的抗氧化性能和抗烧蚀性能。
6.一种超高温碳化硅陶瓷基复合材料的制备方法,包括以下步骤:
7.①
将二维平纹碳化硅纤维布裁剪为方形;
8.②
将裁剪好的碳化硅纤维布叠层,并用碳化硅纤维缝合线缝合为一整体,定型得到碳化硅纤维预制体;
9.③
将碳化硅纤维预制体放入化学气相沉积炉中进行化学气相沉积,制备热解碳界面层;
10.④
将含有抗烧蚀组元的陶瓷粉体与前驱体溶液配制成浸渍浆料,其中陶瓷粉体含量为2~20wt%,粘度为50~400mpa
·
s;
11.⑤
将
③
中的预制件在
④
中的浸渍液中真空高压浸渍;
12.⑥
将
⑤
中的预制件取出沥干后高压固化;
13.⑦
将
⑥
高压固化后的预制件高温裂解,在氮气气氛中以5~10℃/min的升温速率升至1000~1200℃,保温60~120min,自然降温至室温;
14.⑧
反复进行
⑤
~
⑦
步,直至预制体的重量变化小于目标值或设定值。
15.在本技术的一个或多个具体地实施方式中,所述
③
中,化学气相沉积反应中,先驱体为:丙烷,沉积温度:800~1150℃,保温时间:8~16h,炉内压力:1~2kpa,界面厚度为:60~800nm。
16.在本技术的一个或多个具体地实施方式中,所述抗烧蚀组元为si3n4、sic、zrb2、
zrc、hfc、hfb2、bn和b4c中的一种或多种。
17.在本技术的一个或多个具体地实施方式中,所述抗烧蚀组元其颗粒粒径小于100nm。
18.在本技术的一个或多个具体地实施方式中,所述前驱体溶液为聚碳硅烷溶液。
19.在本技术的一个或多个具体地实施方式中,所述真空高压浸渍中:真空度为-0.09mpa,保真空1~3h;2~6mpa,保压1~3h。
20.在本技术的一个或多个具体地实施方式中,所述高压固化中,固化温度:200~400℃,固化压力:2~4mpa,固化时间:2~8h。
21.在本技术的一个或多个具体地实施方式中,所述高温裂解中,在氮气气氛中以5~10℃/min的升温速率升至1000~1200℃,保温60~120min,自然降温至室温。
22.在本技术的一个或多个具体地实施方式中,所述目标值或设定值为1%。
23.本发明还提供一种浸渍浆料。
24.一种超高温碳化硅陶瓷基复合材料,所述超高温碳化硅陶瓷基复合材料为上述的超高温碳化硅陶瓷基复合材料的制备方法制备而成。
25.发明原理及有益效果:
26.本技术通过化学气相沉积热解碳界面层,在将浸渍浆料制备时将含有抗烧蚀组元的陶瓷粉体引入前驱体溶液,真空高压浸渍等手段,制成的碳化硅陶瓷基复合材料中zrb2和zrc颗粒均匀地弥散在sic连续相中,形成了zrb
2-zrc-sic复相陶瓷基体。由于zrb2、zrc颗粒与sic紧密地结合在一起,可在高温氧化环境中产生协同效应,有利于提高复合材料的抗氧化性能和抗烧蚀性能。而且,在碳化硅陶瓷基复合材料中,sic相均匀遍布于基体中,形成了连续相,zrb2和zrc纳米颗粒均匀弥散在基体中。而且粒径小于100nm的zrb2和zrc颗粒有利于显著提高复合材料基体中各相的比表面积和陶瓷活性,并在超高温氧化环境应用时产生强烈的协同效应。
具体实施方式
27.下面将对本发明作进一步说明。
28.一种超高温碳化硅陶瓷基复合材料的制备方法,包括以下步骤:
29.①
将二维平纹碳化硅纤维布裁剪为300mm*250mm的长方形;
30.②
将裁剪好的碳化硅纤维布叠层为厚度为2~5mm,并用碳化硅纤维缝合线缝合为一整体,采用石墨模具进行定型得到碳化硅纤维预制体;
31.③
将碳化硅纤维预制体放入化学气相沉积炉中制备热解碳界面层,先驱体为:丙烷,沉积温度:800~1150℃,保温时间:8~16h,炉内压力:1~2kpa,界面厚度为:60~800nm;
32.④
将含有抗烧蚀组元的陶瓷粉体,如si3n4、sic、zrb2、zrc、hfc、hfb2、bn和b4c中的一种或多种与聚碳硅烷前驱体溶液配制成浸渍浆料,其中陶瓷粉体含量为2~20wt%,粘度控制在50~400mpa
·
s;
33.⑤
将
③
中的预制件放入真空高压浸渍罐中,注入
④
中的浸渍液淹没预制件,抽真空至-0.09mpa,保真空1~3h,加压至2~6mpa,保压1~3h;真空压力浸渍使得浸渍浆料完全浸润多孔疏松的预制件。
34.⑥
将
⑤
中的预制件取出沥干模具表面浸渍液,装入高压固化炉进行固化,固化温度:200~400℃,固化压力:2~4mpa,固化时间:2~8h;
35.⑦
将
⑥
中的预制件装入高温裂解炉裂解中,在氮气气氛中以5~10℃/min的升温速率升至1000~1200℃,保温60~120min,自然降温至室温;
36.⑧
反复进行
⑤
~
⑦
步,直至预制体的重量变化小于1%,完成复合材料的制备。
37.实施例1
38.①
将二维平纹碳化硅纤维布裁剪为300mm*250mm的长方形;
39.②
将裁剪好的碳化硅纤维布叠层为厚度为2~5mm,并用碳化硅纤维缝合线缝合为一整体,采用石墨模具进行定型得到碳化硅纤维预制体;
40.③
将碳化硅纤维预制体放入化学气相沉积炉中制备热解碳界面层,先驱体为:丙烷,沉积温度:1000℃,保温时间:10h,炉内压力:1.2kpa,丙烷界面厚度为:100nm;
41.④
将zrb2陶瓷粉体与聚碳硅烷前驱体溶液(溶剂为二甲苯)配制成浸渍浆料,其中陶瓷粉体含量为10wt%,粘度控制在80mpa
·
s;
42.⑤
将
③
中的预制件放入真空高压浸渍罐中,注入
④
中的浸渍液淹没预制件,抽真空至-0.09mpa,保真空3h,加压至4mpa,保压2h;
43.⑥
将
⑤
中的预制件取出沥干模具表面浸渍液,装入高压固化炉进行固化,固化温度:300℃,固化压力:3mpa,固化时间:6h;
44.⑦
将
⑥
中的预制件装入高温裂解炉裂解中,在氮气气氛中以5℃/min的升温速率升至1200℃,保温120min,自然降温至室温;
45.⑧
反复进行
⑤
~
⑦
步,直至预制体的重量变化小于1%,完成复合材料的制备。
46.实施例2
47.①
将二维平纹碳化硅纤维布裁剪为300mm*250mm的长方形;
48.②
将裁剪好的碳化硅纤维布叠层为厚度为2~5mm,并用碳化硅纤维缝合线缝合为一整体,采用石墨模具进行定型得到碳化硅纤维预制体;
49.③
将碳化硅纤维预制体放入化学气相沉积炉中制备热解碳界面层,先驱体为:丙烷,沉积温度:1000℃,保温时间:10h,炉内压力:1.2kpa,丙烷界面厚度为:100nm;
50.④
将zrc陶瓷粉体与聚碳硅烷前驱体溶液(溶剂为二甲苯)配制成浸渍浆料,其中陶瓷粉体含量为10wt%,粘度控制在80mpa
·
s;
51.⑤
将
③
中的预制件放入真空高压浸渍罐中,注入
④
中的浸渍液淹没预制件,抽真空至-0.09mpa,保真空3h,加压至4mpa,保压2h;
52.⑥
将
⑤
中的预制件取出沥干模具表面浸渍液,装入高压固化炉进行固化,固化温度:300℃,固化压力:3mpa,固化时间:6h;
53.⑦
将
⑥
中的预制件装入高温裂解炉裂解中,在氮气气氛中以5℃/min的升温速率升至1200℃,保温120min,自然降温至室温;
54.⑧
反复进行
⑤
~
⑦
步,直至预制体的重量变化小于1%,完成复合材料的制备。
55.实施例3
56.①
将二维平纹碳化硅纤维布裁剪为300mm*250mm的长方形;
57.②
将裁剪好的碳化硅纤维布叠层为厚度为2~5mm,并用碳化硅纤维缝合线缝合为一整体,采用石墨模具进行定型得到碳化硅纤维预制体;
58.③
将碳化硅纤维预制体放入化学气相沉积炉中制备热解碳界面层,先驱体为:丙烷,沉积温度:1000℃,保温时间:10h,炉内压力:1.2kpa,丙烷界面厚度为:100nm;
59.④
将hfc陶瓷粉体与聚碳硅烷前驱体溶液(溶剂为二甲苯)配制成浸渍浆料,其中陶瓷粉体含量为10wt%,粘度控制在80mpa
·
s;
60.⑤
将
③
中的预制件放入真空高压浸渍罐中,注入
④
中的浸渍液淹没预制件,抽真空至-0.09mpa,保真空3h,加压至4mpa,保压2h;
61.⑥
将
⑤
中的预制件取出沥干模具表面浸渍液,装入高压固化炉进行固化,固化温度:300℃,固化压力:3mpa,固化时间:6h;
62.⑦
将
⑥
中的预制件装入高温裂解炉裂解中,在氮气气氛中以5℃/min的升温速率升至1200℃,保温120min,自然降温至室温;
63.⑧
反复进行
⑤
~
⑦
步,直至预制体的重量变化小于1%,完成复合材料的制备。
64.将实施例1-3制成的的陶瓷基复合材料参照gjb 323a-96、gb/t14390-2008等标准测试密度、孔隙率、烧蚀及1500℃强度等性能,结果如下表1。
65.表1
[0066][0067]
以上所述仅为本发明的优选实施例而已,并不用于限制本发明,对于本领域的技术人员来说,本发明可以有各种更改和变化。凡在本发明的精神和原则之内,所作的任何修改、等同替换、改进等,均应包含在本发明的保护范围之内。