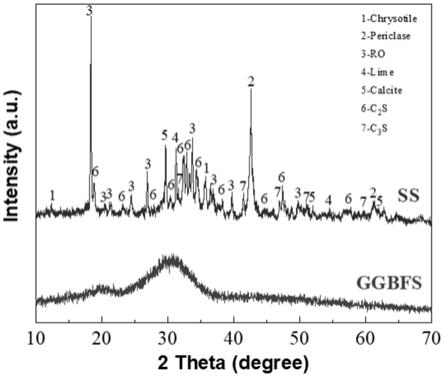
1.本发明涉及一种路基材料,具体涉及一种无水泥路基材料及其制备方法,属于固体废物资源化利用技术领域。
背景技术:2.道路分位路基和路面两部分,路基是指直接铺在路面基层下,需要承受路面荷载,并将荷载传递到地基深处的土工构筑物。通常路基材料采用天然碎石和水泥,但水泥制造时会产生大量的粉尘污染和固体废物,对环境极不友好。并且,随着节能减排的全面要求,路基材料常常面临着原材料不充足的情况,在这种情况下,可通过对固体废物经过处理用来制备路基基层材料,使固化材料满足路基材料的基本性能要求,减少自然资源的消耗,降低对水泥的需求量,且减少对环境产生的污染。
3.中国专利(申请号202011416388.5)公开了一种市政污泥的路基材料制备方法,通过添加水泥,粉煤灰减水剂等物质制备而成,可以替代传统路基材料,用于次干道和支路的道路铺设。中国专利(申请号202110931112.9)公开了一种磷石膏稳定红黏土的路基材料制备方法,通过添加水泥、磷石膏、红黏土和水玻璃制备而成,可以用于红黏土地区的公路建设。虽然这些路基材料中采用了固废作为路基材料的原料,但这些路基材料或多或少都需要添加水泥来提供强度,无法完全摆脱对水泥的依赖。因此需要探索开发出一种全新的路基材料,完全减少对水泥的依赖,并有效促进固体废物的资源化利用,减少堆存造成的环境和社会威胁。
技术实现要素:4.针对现有技术中存在问题,本发明的第一个目的在于提供一种无水泥路基材料。该无水泥路基材料的原料全部为固废材料,无需添加水泥,在实现传统路基材料替代作用的同时,又可以消纳大宗工业固体废物,增大固体废物资源化利用程度,符合“无废城市”理念。
5.本发明的第二个目的在于提供一种无水泥路基材料的制备方法,该制备方法工艺简便,成本低廉,所得产品具有较高的机械强度,可达32~46mpa,且该制备方法全程无二次污染,对环境友好,符合“以废治废”理念。
6.为实现上述技术目的,本发明提供了一种无水泥路基材料,包含以下质量百分比组分:高炉矿渣为40~65%、钢渣为15~25%、固废石膏5~15%和尾矿砂15~30%。本发明所采用的高炉矿渣和钢渣均为钢铁冶炼时排放的固体废物,石膏为脱硫脱硝等工业活动所产生的副产物,尾矿砂为矿石冶炼产生的固体废物。高炉矿渣为路基材料提供活性硅铝骨架,钢渣提供碱度环境,并且钢渣中的钙、镁、铁等元素可以增强矿渣的硅铝骨架结构强度,固废石膏提供硫酸盐,作为激活矿渣和钢渣的激发剂,尾矿砂作为填充骨料,对路基材料的整体强度起支撑作用,能有效增强路基材料的抗压强度。
7.以往的路基材料往往需要添加水泥来增强材料的力学强度,但本发明所采用的矿
渣和钢渣中的活性硅酸钙,铝酸钙和铁酸钙等物质,经过硫酸盐激发,可以产生水化产物从而大幅增强材料强度,而采用尾矿作为填充骨料,又可以进一步增强路基材料的强度和耐磨性。本发明通过合理级配,将粗细尾矿砂与矿渣钢渣和石膏紧密结合,使得活性硅铝骨架和钙、镁、铁等增强骨架效应以及硫酸盐激发都得到放大,满足紧密堆积密度,最大效果增进路基材料整体强度。因此,本发明无需添加水泥也可达到较高的力学强度。
8.作为一项优选的方案,所述高炉矿渣的主要成分及各主要成分的质量百分比含量为:活性氧化硅28~32%,氧化铝12~16%;所述钢渣的主要成分及各主要成分的质量百分比含量为:硅酸二钙26~28%,硅酸三钙15~19%,铁锰镁的氧化物21~26%。
9.作为一项优选的方案,所述固废石膏为脱硫石膏、磷石膏和氟石膏中的至少一种。石膏中的硫酸根可以有效激发钢渣和矿渣的活性组分,加速活性硅铝键的断裂和重排,使其产生高强度的硅铝骨架。
10.作为一项优选的技术方案,所述尾矿砂由尾矿细骨料和尾矿粗骨料按照质量比1:1~3组成,所述尾矿细骨料粒径为0.5mm~10mm,尾矿粗骨料粒径为0.5cm~2cm。
11.作为一项优选的技术方案,所述尾矿砂的主要成分及各主要成分的质量百分比含量为:白云石48~52%,方解石8~10%,石英30~34%,硅酸盐矿物5~6%。
12.本发明还提供了一种无水泥路基材料的制备方法,包括方案a和方案b;
13.方案a:将矿渣、钢渣和脱硫石膏混磨后,与尾矿砂混合均匀,再掺入混合物料总质量9~15%的水,挤压成型,养护即得;
14.方案b:将矿渣、钢渣和脱硫石膏混磨后,与尾矿砂混合均匀,再掺入混合物料总质量20~30%的水,浇筑成型,养护即得。
15.作为一项优选的方案,所述混磨采用翻转球磨方式;所述球磨的时间为5~10分钟,转速为30~80r/min。
16.作为一项优选的方案,所述养护的温度为18~22℃,湿度为94~96%。
17.相对现有技术,本发明带来的有益技术效果:
18.1、本发明的无水泥路基材料,其原料全部为固废材料,无需添加水泥,可以有效替代传统水泥基路基材料,不仅可以提升路基材料的力学性能,还加大了工业固体废物的综合利用率,减少堆存带来的风险。
19.2、本发明提供的无水泥路基材料的制备工艺,操作简单,成本低廉,工艺所需生产设备也均为环境友好型设备,在处理大宗固废材料的同时不产生二次污染,达到了“以废治废”的技术效果和技术目的。
附图说明
20.图1为实施例所用原材料的xrd图谱。
21.图2为实施例所用尾矿砂的xrd图谱。
22.图3为各实施例所制备固化体的抗压强度。
23.具体实施案例
24.下面结合具体实施案例对本发明进行进一步的描述,但发明的保护范围并不仅限于此。
25.本发明实施例采用的高炉矿渣的主要成分及主要成分的质量比含量为活性氧化
硅30%,氧化铝14%;钢渣的主要成分及主要成分的质量比含量为硅酸二钙27%,硅酸三钙17%和铁锰镁的氧化物23%;尾矿砂由尾矿细骨料和尾矿粗骨料混合所得,二者质量比例为1:1~3,其主要成分及各主要成分质量比含量为白云石50%、方解石9%,石英32%和硅酸盐矿物5%,固废石膏中硫酸钙含量93%。
26.以下实施案例中矿渣、钢渣和工业副产物石膏的不同复合配比均经过混磨拌合5分钟,尾矿分为粗骨料和细骨料两种,其中粗骨料粒径分布为0.5cm~2cm,细骨料粒径分布为0.5mm~10mm.
27.实施例1
28.现将矿渣、钢渣、工业副产物石膏和尾矿骨料以上表案例1的配比混合均匀
29.案例矿渣钢渣脱硫石膏氟石膏磷石膏尾矿粗骨料尾矿细骨料155201000105250200100101034025001015104252520002010
30.后,分别添加混合粉体质量12%的水用于半干法挤压成型和添加混合粉体质量25%的水用于浇筑成型,分别在3天、7天和28天检测其抗压强度。
[0031][0032]
实施例2
[0033]
现将矿渣、钢渣、工业副产物石膏和尾矿骨料以上表案例2的配比混合均匀后,分别添加混合粉体质量11%的水用于半干法挤压成型和添加混合粉体质量21%的水用于浇筑成型,分别在3天、7天和28天检测其抗压强度。
[0034][0035][0036]
实施例3
[0037]
现将矿渣、钢渣、工业副产物石膏和尾矿骨料以上表案例3的配比混合均匀后,分别添加混合粉体质量11%的水用于半干法挤压成型和添加混合粉体质量20%的水用于浇筑成型,分别在3天、7天和28天检测其抗压强度。
[0038]
编号成型方法混合粉体水3天抗压7天抗压28天抗压a3挤压成型111%15.5526.5932.71b3浇筑成型120%2.0411.5334.04
[0039]
实施例4
[0040]
现将矿渣、钢渣、工业副产物石膏和尾矿骨料以上表案例4的配比混合均匀后,分别添加混合粉体质量10%的水用于半干法挤压成型和添加混合粉体质量20%的水用于浇筑成型,分别在3天、7天和28天检测其抗压强度。
[0041]