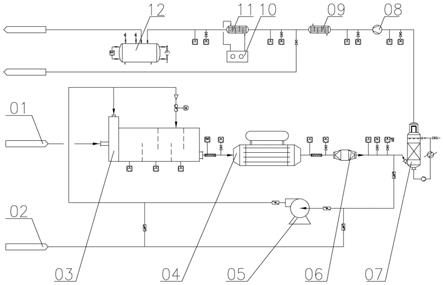
一种高氧燃烧硫磺循环冷却制取so2的装置
技术领域
1.本实用新型属于无机化工生产领域,尤其涉及金属或贵金属湿法冶炼、硫磺制酸行为、环保尾气脱so2等技术领域,具体地说是一种高氧燃烧硫磺循环冷却制取so2的装置。
背景技术:2.随着纯态so2或高浓度so2混合气体在冶金、化工、食品、造纸等行业的广泛应用,国内外市场对纯态so2或高浓度so2混合气体需求日益旺盛;传统工业制取纯态so2方法有:一是硫酸置换亚硫酸盐(铵、钠等)法,由于规模较小,副产大量硫酸盐导致生产成本较高,现在已少有应用;二是制取so3与反应釜内与硫磺加热反应法,由于需要先制取纯so3工艺复杂能耗大,设备腐蚀严重,安全生产控制风险大,上世纪六七年代曾有应用现在少见;三是纯氧表面燃烧法,燃烧so2气体中单质硫较多需要5~8道复杂过滤,虽可制取纯so2但装置易堵塞、作业率较低无法长周期连续生产其生产成本较高;四是有机溶剂(柠檬酸、醇胺类有机物如离子液等)吸收解吸法副产高浓度so2气体,通过净化压缩冷却生产纯液态so2产品,但因其生产过程中需要消耗大量的蒸汽及干燥硫酸,一般不能独立设置应用受限。因此需要解决纯态so2产品大型装置生产的瓶颈,作为应用技术课题攻关突破。
技术实现要素:3.本实用新型的目的是针对现有技术存在的问题,提供一种高氧燃烧硫磺循环冷却制取so2的装置;该装置采用高氧燃烧硫磺循环冷却生产高浓度so2气体并回收燃烧余热、高浓度so2气体通过压缩冷却液化生产液态纯so2产品。
4.本实用新型的目的是通过以下技术方案解决的:
5.一种高氧燃烧硫磺循环冷却制取so2的装置,包括焚硫炉,其特征在于:炉内温度为850~1080℃的焚硫炉的炉头上安装有至少一支与供应液态硫磺的管道连通的大喷角旋流雾化喷枪,焚硫炉的出口侧设有降温设备,降温设备能够将焚硫炉输出的高温炉气降为130℃~230℃的低温炉气;降温设备通过管道与净化除雾塔相连接以吸收净化低温炉气中的杂质、同时通过带有循环密封风机且连接供应高氧气体的管道的工艺气供应管与焚硫炉的炉头连通以向焚硫炉供应低温炉气和高氧气体混合而成的工艺气,低温炉气作为循环冷却气体、最重要的作用是维持焚硫炉内的炉温;净化除雾塔通过管道与加压设备、或者加压设备和冷却设备相连接,以将净化除雾塔输出的20℃~45℃的清洁炉气经加压或者加压冷却成高浓so2气体产品、或者清洁炉气加压以提升so2气体的液化温度并冷却成液态纯so2产品。
6.所述液态硫磺的温度为125℃~150℃、压力为1.0mpa~1.6mpa且纯度≥99.5%,大喷角旋流雾化喷枪能够将液态硫磺雾化为5μm~100μm的雾滴喷入焚硫炉内。
7.所述高氧气体的温度为30℃~80℃、压力为+20kpa(g)~300kpa(g);高氧气体中含氧气摩尔含量为75%~98%、含n2或惰性气体摩尔含量为2%~25%,氧气、n2或惰性气体的摩尔含量之和为100%。
8.高氧气体几乎不含水气,高氧气体采用变压吸附法、真空变压吸附法、深冷法或其它生产氧气方法制取或掺混所得,但不使用含量≥99%纯氧气。
9.所述的工艺气供应管与供应高氧气体的管道的连接点位于循环密封风机的前侧或后侧。
10.所述的工艺气供应管与焚硫炉的炉头连通且通过带控制阀的分支管连通焚硫炉的中后段。
11.所述的焚硫炉内维持炉内参与反应的氧气摩尔浓度为23%~3%,在蒸汽锅炉和/或换热设备的出口管道上安装气体在线分析仪控制液态硫磺或高氧气体的投入量,确保氧化气氛将喷入的雾化液态硫磺在足量反应时间内完全燃烧,无气态硫磺或升华硫磺移出焚硫炉;所述焚硫炉输出的高温炉气中的so2摩尔含量为70%~96%、o2摩尔含量为2%~10%、n2或惰性气体摩尔含量为2%~20%、余量为其它微量物质。
12.一个优选方案是:所述焚硫炉输出的高温炉气中的so2摩尔含量为75%~93%。
13.所述的降温设备通过管道与净化除雾塔相连接以输送低温炉气总气量的40%~15%作为高浓so2混合气体用以吸收净化制取so2产品、所述的降温设备通过带有循环密封风机的工艺气供应管向焚硫炉输送低温炉气总气量的60%~85%作为循环冷却气体和高氧气体混合而成的工艺气。
14.所述的降温设备包括蒸汽锅炉和/或换热设备,在焚硫炉后依序连接蒸汽锅炉和换热设备时,蒸汽锅炉能够将焚硫炉输出的高温炉气降温为300~450℃的中温炉气、换热设备能够将中温炉气降温为130℃~230℃的低温炉气。
15.所述的净化除雾塔采用浓度为91%~98%的浓硫酸对低温炉气进行吸收净化,净化除雾塔出口处的含高浓度so2的清洁炉气的温度为20℃~45℃;浓硫酸能够将来自高浓so2混合气体中的少量so3气体吸收,自生产硫酸且维持自平衡。
16.所述净化除雾塔的净化为金属丝网除雾器、纤维除雾器、吸附器除或电除雾器除去气体中酸雾。
17.所述的加压设备为压缩风机、冷却设备为一级冷却器时,压缩风机连通净化除雾塔的出口、且压缩风机的出口连通一级冷却器;净化除雾塔输出的温度为20℃~45℃的清洁炉气经压缩风机加压至0.05mpa~0.50mpa、温度升高为40℃~110℃,再经一级冷却器降温至20℃~50℃后输出高浓so2气体产品;或者所述的净化除雾塔输出的温度为20℃~45℃的清洁炉气经压缩风机加压至0.30mpa~0.65mpa、温度升高为100℃~160℃,再经一级冷却器降温至20℃~50℃后输出高浓so2气体产品。
18.所述的加压设备为压缩风机、冷却设备为依序连接的一级冷却器和带有制冷机组的二级冷却器时,净化除雾塔的出口连通压缩风机、压缩风机的出口连通一级冷却器、一级冷却器连通二级冷却器、二级冷却器的出口连通液态产品储罐,净化除雾塔输出的温度为20℃~45℃的清洁炉气经压缩风机加压至0.30mpa~0.65mpa、温度升高为100℃~160℃,再经一级冷却器降温至20℃~50℃,最后经带有制冷机组的二级冷却器深冷降温至-15℃~+35℃,使清洁炉气中的so2气体液化为液态纯so2产品输出至液态产品储罐。
19.本实用新型相比现有技术有如下优点:
20.本实用新型的装置采用高氧燃烧硫磺制取高浓度so2气体或进而生产纯态so2产品,因硫磺和高氧气体都非常易得,生产装置相对独立不受其它工序牵制;特别是随着vpsa
(真空变压吸附法)制氧技术的日臻成熟、装置大型化、作业高效,且制氧生产成本降低为制取高浓so2气体创造了有利条件。
21.本实用新型的焚硫炉燃烧强度为155~310kw/m3是纯氧表面燃烧硫磺法5~10倍,通过反应气体循环冷却既保持焚硫炉内的燃烧温度保持在850~1080℃(而一般纯氧表面燃烧法炉内有一熔硫池燃烧温度550~750℃)、且焚硫炉内维持过剩的氧气又保证足量反应时间(焚硫反应时间延长五倍左右),使硫磺燃烧充分,燃烧后混合气体中无气态单质硫,为后续清洁、便捷生产液态纯so2产品创造条件。
22.本实用新型的焚硫炉充分燃烧后排出的高温炉气中的so2摩尔含量为70%~96%、o2摩尔含量为2%~10%、n2或惰性气体摩尔含量为2%~20%、余量为其它微量物质,且摩尔含量之和为100%;高温炉气典型成分如:so
2-85%、o
2-3%、n
2-11%可以直接作为还原剂使用,可不必压缩冷却液化为液态纯so2、再加热气化应用。
23.本实用新型的焚硫炉后直接设火管锅炉和省煤器生产低压或中压蒸汽用于其它工序加热或发电,因循环密封风机的循环作用使得热能回收率高、品质高、经济价值显著。
24.本实用新型的装置因燃烧冷却后气体无单质液硫或固硫造成的堵塞故障,气体洗涤净化、压缩、冷却等工序简化,做好密封防泄漏,全流程自动化仪表检测及调节控制,保证人身及设备安全,适宜规模化生产。
附图说明
25.附图1为本实用新型的高氧燃烧硫磺循环冷却制取so2的装置的示意图。
26.其中:1—液态硫磺;2—高氧气体;3—焚硫炉;4—蒸汽锅炉;5—循环密封风机;6—省煤器或换热器;7—净化除雾塔;8—压缩风机;9—一级冷却器;10—制冷机组;11—二级冷却器;12—液态产品储罐。
具体实施方式
27.下面结合附图与实施例对本实用新型作进一步的说明。
28.如图1所示,一种高氧燃烧硫磺循环冷却制取so2的装置,包括焚硫炉3,炉内温度为850~1080℃的焚硫炉3的炉头上安装有至少一支与供应液态硫磺1的管道连通的大喷角旋流雾化喷枪,液态硫磺1的温度为125℃~150℃、压力为1.0mpa~1.6mpa且纯度≥99.5%,大喷角旋流雾化喷枪能够将液态硫磺1雾化为5μm~100μm的雾滴喷入焚硫炉3内,焚硫炉3内维持炉内参与反应的氧气摩尔浓度为23%~3%以保证氧气量过剩;焚硫炉3的出口侧依序连接有蒸汽锅炉4和换热设备(省煤器或换热器6),蒸汽锅炉4能够将焚硫炉3输出的高温炉气降温为300~450℃的中温炉气、换热设备能够将中温炉气降温为130℃~230℃的低温炉气;换热设备通过管道与净化除雾塔7相连接输送低温炉气总气量的40%~15%以通过净化除雾塔7吸收净化低温炉气中的杂质、同时通过带有循环密封风机5且连接供应高氧气体2的管道的工艺气供应管与焚硫炉3的炉头连通以向焚硫炉3供应低温炉气总气量的60%~85%作为循环冷却气体和高氧气体2混合而成的工艺气,高氧气体2的温度为30℃~80℃、压力为+20kpa(g)~300kpa(g);高氧气体2中含氧气摩尔含量为75%~98%、含n2或惰性气体摩尔含量为2%~25%,氧气、n2或惰性气体的摩尔含量之和为100%;净化除雾塔7通过管道依序连接压缩风机8、一级冷却器9和带有制冷机组10的二级冷却器11、液态产品储罐12,净化除
雾塔7采用浓度为91%~98%的浓硫酸对低温炉气进行吸收净化,净化除雾塔7出口处的含高浓度so2的清洁炉气的温度为20℃~45℃、压力<0.05mpa;清洁炉气经压缩风机8加压至0.05mpa~0.50mpa、温度升高为40℃~110℃,再经一级冷却器9降温至20℃~50℃后输出高浓so2气体产品;或者清洁炉气经压缩风机8加压至0.30mpa~0.65mpa、温度升高为100℃~160℃,再经一级冷却器9降温至20℃~50℃后输出高浓so2气体产品;或者清洁炉气经压缩风机8加压至0.30mpa~0.65mpa、温度升高为100℃~160℃,再经一级冷却器9降温至20℃~50℃,最后经带有制冷机组10的二级冷却器11深冷降温至-15℃~+35℃,使清洁炉气中的so2气体液化为液态纯so2产品输出至液态产品储罐12。
29.在本实用新型提供的装置中,工艺气供应管与供应高氧气体2的管道的连接点位于循环密封风机5的前侧或后侧,且根据需要,工艺气供应管与焚硫炉3的炉头连通且通过带控制阀的分支管连通焚硫炉3的中后段,即进行二次补风。净化除雾塔主要去除高浓so2混合气体中的so3、微量水分、微量粉尘,然后成为酸雾含量≤15mg/m3的清洁炉气。
30.本实用新型提供的高氧燃烧硫磺循环冷却制取so2的装置使用时,焚硫炉3输出的高温炉气中的so2摩尔含量为70%~96%、o2摩尔含量为2%~10%、n2或惰性气体摩尔含量为2%~20%、余量为其它微量物质。优选方案是,焚硫炉3输出的高温炉气中的so2摩尔含量为75%~93%。
31.如图1所示,本实用新型提供的一种高氧燃烧硫磺循环冷却制取so2的装置包括:供应液态硫磺1的加压泵和管道阀门、供应高氧气体2的管道阀门、带有至少一支大喷角旋流雾化喷枪的焚硫炉3、蒸汽锅炉4、循环密封风机5、作为换热设备的省煤器或换热器6、净化除雾塔7、为清洁炉气加压的压缩风机8、一级冷却器9、制冷机组10、二级冷却器11、液态产品储罐12。具体功能如下:加压泵所供的液态硫磺1需经固态粉状或片状硫磺经过熔化精密过滤并进入中间罐保温储存,根据焚硫工序,气体分析仪在线监测so2或o2浓度以调节泵送液态硫磺1的供应量;制氧如采用vpsa制氧机组所供氧气摩尔浓度在90%左右、含水露点温度低于-40℃,高氧气体2中除氧气外、还有n2或惰性气体中的一种,所供高氧气体2的温度为30℃~80℃、压力在+20kpa(g)~300kpa(g);焚硫炉3为钢q345r+刚玉耐火砖+粘土耐火砖+高强保温砖+外保温结构,应用的大喷角旋流雾化喷枪与炉头法兰连接,液硫机械雾化悬浮+旋流气体+高温环境等,硫磺与氧气强烈搅拌混合迅速完全燃烧;蒸汽锅炉4采用火管锅炉,锅炉与汽包一体化由上升管支撑汽包、锅炉前端应用刚玉套管及耐火料隔热浇筑防高温对管板烧蚀,锅炉两端为挠性管板、锅炉管为20g或耐热耐磨锅炉用合金换热钢管,可以生产1.25/2.5/4.2/6.0mpa的中低压饱和蒸汽;循环密封风机5采用变频循环耐蚀耐热密封风机,风机本体采用耐热合金重型制造,机械+空气或氮气密封保证无外泄漏,应用变频调速控制焚硫炉内燃烧温度;省煤器或换热器6连接在蒸汽锅炉4的后部,用于烟气显热进一步回收,控制循环冷却气体的出口温度,避免低温腐蚀,也可采用热管型换热器加热热水或其它介质;净化除雾塔7采用的浓硫酸炉气净化洗涤塔为钢衬瓷砖结构或特种合金结构或衬氟塑料结构,塔内有瓷梁填料布酸器精密高效除雾器等,主要用于洗涤炉气中微量颗粒物、吸收so3气体、吸收微量水分、并进一步降低低温炉气的温度(20℃~45℃)、除去低温炉气中的微量酸雾等,为后续so2产品提供品质保证;压缩风机8为活塞型或多级离心型或其它类风机转子(属无油类)型压缩风机,变频调速控制,主要为清洁炉气提供合适升压动力(如0.05mpa~0.50mpa、0.30mpa~0.65mpa),以便于清洁的so2炉气输送或冷却液化,
风机关键材质为耐震耐蚀合金或合金铸铁类,轴端多级机械和压气密封保证无泄漏;一级冷却器9常用循环水冷却或其它冷却介质,将炉气温度降至20~50℃,冷却器的换热面材质多为合金钢,且须按压力容器规范设计制造检验;制冷机组10专为清洁的so2炉气进一步冷却液化提供冷量,制冷为加压节流换热型或溴化锂蒸汽加热吸热型;二级冷却器11应用制冷机组10提供载冷量循环介质对清洁的so2炉气进一步冷却,并使清洁的so2气体冷却相变液化生成液态纯so2产品,为获得经济的so2液化率,可精确控制压缩机8的出口炉气压力及二级冷却器11的炉气出口冷却温度。液态产品储罐12用于液态纯so2储存并保冷(温),便于后续使用或装瓶罐外售。
32.在高氧燃烧硫磺循环冷却制取so2的装置中,温度为125℃~150℃、压力为1.0mpa~1.6mpa且纯度≥99.5%的液态硫磺1通过流量计计量控制进入与炉头法兰连接的大喷角旋流雾化喷枪,液态硫磺1呈微粒状雾化大喷角(~120
°
)与循环密封风机5送入的工艺气(20~300kpa)旋流悬浮膨张式搅拌混合后进入850~1080℃的焚硫炉3内,5μm~100μm的雾化悬浮微滴状液态硫磺1与工艺气旋流扩散激烈搅动并剧烈燃烧,焚硫炉3内维持炉内参与反应的氧气摩尔浓度为23%~3%(焚烧炉的前端气体体氧气浓度较高,如25%;沿炉体轴线方向随反应进程氧气浓度逐渐降低,如3%)以保证氧气量过剩,处于弱过剩状态,通过二次补风(主要控制炉内氧化保持弱氧化气氛,氧气浓度≥3%,保证硫磺彻底燃烧)、混合气折流挡墙(用于增加雾化硫磺与气体反应接触混合状态,防止硫磺液滴直接带出炉外)及炉内反应时间的设计保证炉内硫磺完全燃烧,循环冷却气体实际增加了反应时间,反应时间长硫磺焚烧更彻底。焚硫炉3上设在线温度检测点、红外视镜观察点、反应气后端气体成分(so2/o2)分析仪等用于检测焚硫炉3内燃烧温度及燃烧过剩氧量,通过调节液态硫磺1或高氧气体2的供应量及循环冷却气体的风量对炉内燃烧工艺参数进行精准控制;焚硫炉1内的液态硫磺1燃烧彻底后排出与作为蒸汽锅炉4的火管锅炉连接,高温炉气走管程加热管外锅炉水,通过炉水蒸发生产蒸汽,蒸发器内汽水混合物通过上升管进入汽包后汽水分离,饱和蒸汽通过丝网除雾器后控制输出使用,火管锅炉供除盐除氧水由界外提供、通过省煤器加热进行汽包补水,火管锅炉的出锅炉炉气温度300~450℃;出锅炉炉气再与省煤器或换热器6相连接,通过换热将炉气温度降至130~230℃成为低温炉气,低温炉气总气量的60%~85%作为循环冷却气体回到焚硫炉3继续参与反应、剩余部分作为高浓so2混合气体进入净化除雾塔7净化制取产品;供应净化除雾塔7的净化循环硫酸通过酸冷却器降温后送入塔内填料表面与高浓so2混合气体逆流充分接触传质传热并将炉气温度降至45℃以下,循环酸通过外界补酸或产酸外送维持循环平衡,通过喷淋浓硫酸(91%~98%)洗涤吸收炉气中的颗粒物、so3、h2o(g)等,再通过除雾器除去夹带的微量酸雾后排出净化除雾塔7;出净化除雾塔7的清洁炉气进入压缩风机8进行加压(如0.30mpa-0.65mpa),此时压缩风机8做功使清洁炉气温度亦上升(如100℃~160℃),加压升温后的清洁炉气进入水冷式的一级冷却器9进行冷却,初步将清洁炉气的温度降至50℃以下、再进入二级冷却器11,清洁炉气在二级冷却器11中进一步降温深冷(-15℃~+30℃、增压使得so2的液化温度升高),清洁炉气中的so2气体冷却发生液化相变生产液态纯so2产品。液态纯so2产品自流入作为液态产品储罐12的so2储槽/罐,部分不凝气(如氧气、氮气、二氧化碳、少量二氧化硫)等由储槽分离排出界外处理(如碱吸收或用于其它利用)后环保排空。
33.如图1所示的高氧燃烧硫磺循环冷却制取so2的装置运行时,具体步骤为:
34.a、高氧气体2与循环冷却气体混合为工艺气送入焚硫炉3,液态硫磺1雾化喷入焚硫炉3内与工艺气混合并旋流扩散充分燃烧,焚硫炉3内保持氧化气氛充分燃烧使无气态单质硫逸出;具体日下:
35.其中高氧气体2含氧气摩尔含量为75%~98%、含n2或惰性气体摩尔含量为2%~23%,氧气、n2或惰性气体的摩尔含量之和为100%;
36.循环冷却气体为步骤c中的低温炉气,130℃~230℃的低温炉气由循环密封风机5输送并与温度为30℃~80℃、压力为+20kpa(g)~300kpa(g)的高氧气体混合为工艺气送入温度为850~1080℃的焚硫炉3内用于焚硫燃烧和降低炉温,高氧气体2和循环冷却气体的混合点设置在循环密封风机5前或者循环密封风机5后;
37.在焚硫炉1的炉头上固定有连通液态硫磺1供应设备的大喷角旋流雾化喷枪,温度为125℃~150℃、压力为1.0mpa~1.6mpa且纯度≥99.5%的液态硫磺1经大喷角旋流雾化喷枪雾化为5μm~100μm的雾滴喷入焚硫炉3内,液态硫磺1的雾滴与工艺气在焚硫炉3内旋流膨胀式搅拌混合扩散并剧烈燃烧;
38.焚硫炉3燃烧时维持炉内参与反应的氧气摩尔浓度为23%~3%,保持焚硫炉3内的氧化气氛将喷入的雾化液态硫磺1在足量反应时间内完全燃烧,使无气态单质硫排出焚硫炉3;
39.b、焚硫炉3内充分燃烧后排出的高温炉气中的so2摩尔含量为70%~96%、o2摩尔含量为2%~10%、n2或惰性气体摩尔含量为2%~20%、余量为其它微量物质;
40.更适宜的一个范围是高温炉气中的so2摩尔含量为75%~93%;
41.c、高温炉气经蒸汽锅炉4和/或换热设备回收余热后,被冷却成130℃~230℃的低温炉气,低温炉气总气量的60%~85%作为循环冷却气体回到步骤a继续参与反应、低温炉气总气量的40%~15%作为高浓so2混合气体进入步骤d净化制取产品;
42.当蒸汽锅炉4和换热设备共用时,高温炉气经蒸汽锅炉4生产蒸汽并降温为300~450℃的中温炉气、中温炉气经换热设备回收余热后降温为130℃~230℃的低温炉气;
43.d、高浓so2混合气体经净化除雾塔7吸收净化降温为20℃~45℃、压力<0.05mpa的清洁炉气,净化除雾塔7采用的浓硫酸的浓度为91%~98%,浓硫酸能够将来自高浓so2混合气体中的少量so3气体吸收,自生产硫酸且维持自平衡;
44.清洁炉气经加压或者加压冷却成高浓so2气体产品,或者清洁炉气加压以提升so2气体的液化温度、并冷却成液态纯so2产品;具体是:清洁炉气经加压至0.05mpa~0.50mpa、温度为40℃~110℃,再经一级冷却器9降温至20℃~50℃后作为高浓so2气体产品使用;或者清洁炉气经加压至0.30mpa~0.65mpa、温度为100℃~160℃,再经一级冷却器9降温至20℃~50℃后作为高浓so2气体产品使用;或者清洁炉气经加压至0.30mpa~0.65mpa、温度为100℃~160℃,再着经一级冷却器9降温至20℃~50℃,最后经带有冷却机组10的二级冷却器11深冷降温至-15℃~+35℃,使清洁炉气中的so2气体液化为液态纯so2产品。
45.下面通过具体实施例来进一步阐述本实用新型提供的高氧燃烧硫磺循环冷却制取so2的装置。
46.实施例一
47.某贵金属回收工厂,冶炼工艺还原杂质需要折纯so2量~12.5t/h、so2摩尔浓度≥85%、o2摩尔浓度≤5%、so2气体温度≤60℃,气体压力~100kpa(g)。采用本实用新型提供的
高氧燃烧硫磺循环冷却制取so2的装置和工艺,原料硫磺(wt≥99.5%)经熔硫二级精制过滤后的液态硫磺1的温度为140℃、由泵加压至1.5mpa后送入两支大喷角旋流雾化喷枪,精硫泵变频调速控制液硫供应量~6.31t/h;真空变压吸附法(vpsa)制氧机组供高氧气体2(o
2-92%, n
2-8%)5040nm3/h、压力45kpa(g);循环风量26000 nm3/h,混合的工艺气与大喷角旋流雾化喷枪雾化的液态硫磺1的雾滴在焚硫炉3内燃烧,焚硫炉3的内径为2450mm、炉内长度为15000mm且内设四挡墙,焚硫炉3的炉内燃烧温度995℃;高温炉气经连接的蒸汽锅炉4降温回收余热生产饱和蒸汽(4.2mpa,252℃)24t/h,出蒸汽锅炉4的中温炉气温度400℃;中温炉气再进入省煤器(热管)对蒸汽锅炉4给水进行加热由103℃升至245℃,中温炉气的温度则降至145℃成为低温炉气;出省煤器的低温炉气总气量的60%~85%作为循环冷却气体回到焚硫炉3继续参与反应、剩余部分作为高浓so2混合气体进入净化除雾塔7,其塔直径1200mm、应用93%硫酸进行循环(q=20m3/h)冷却,入塔酸温40℃,出塔的清洁炉气压力38kpa、温度42℃、酸雾含量≤15mg/m3;净化后的清洁炉气进入两台离心式压缩机进行增压,增压至120kpa、温度升高至90℃,再经水冷却器冷却至50℃;水冷却器出口处的清洁炉气温度50℃、压力118kpa、so2摩尔浓度87.5%、o2摩尔浓度3.5%,完全符合湿法冶炼要求,直接送湿法冶炼工序使用,不再另行深冷液化。据估算,采用本实用新型的高氧燃烧硫磺循环冷却制取so2的装置投资比柠檬酸吸收解吸法节省26%、运行综合费用节约40%,装置布置简洁占地少运行控制自动化,达到了节省投资降低生产运行成本目的。
48.实施例二
49.某铜钴冶炼厂,冶炼还原提钴工艺需要折纯so2量~8.75t/h、so2摩尔浓度≥80%、o2摩尔浓度≤5%、so2气体温度≤60℃,气体压力~300kpa(g),且部分生产液态纯so2储存备用。采用本实用新型提供的高氧燃烧硫磺循环冷却制取so2的装置和工艺,原料硫磺(wt≥99.5%)经熔硫二级精制过滤后的液态硫磺1的温度为135℃、由泵加压至1.35mpa后送入两支大喷角旋流雾化喷枪,精硫泵变频调速控制液硫供应量~4.45t/h;真空变压吸附法(vpsa)制氧机组供高氧气体2(o
2-85%, n
2-15%)3900nm3/h、压力40kpa(g);循环风量17500nm3/h,混合的工艺气与大喷角旋流雾化喷枪雾化的液态硫磺1的雾滴在焚硫炉3内燃烧,焚硫炉3的内径2200mm、炉内长度14000mm且内设三挡墙,焚硫炉3的炉内燃烧温度1050℃,高温炉气经连接的蒸汽锅炉4降温回收余热生产饱和蒸汽(4.2mpa,252℃)16.65t/h, 出蒸汽锅炉4的中温炉气温度410℃,中温炉气再进入省煤器(热管)对蒸汽锅炉4给水进行加热由103℃升至235℃,中温炉气的温度则降至160℃成为低温炉气;出省煤器的低温炉气总气量的60%~85%作为循环冷却气体回到焚硫炉3继续参与反应、剩余部分作为高浓so2混合气体进入净化除雾塔7,其塔直径1100mm、应用94%硫酸进行循环(q=20m3/h)冷却,入塔酸温40℃,出塔的清洁炉气压力33kpa、温度41℃、酸雾含量≤10mg/m3;净化后的清洁炉气进入两台离心式压缩机进行增压,增压至340kpa(g)、温度升高至140℃,再经水冷却器冷却至45℃;水冷却器出口处的清洁炉气温度45℃、压力338kpa、so2摩尔浓度80.5%、o2摩尔浓度3.6%,符合湿法冶炼直接利用要求,可以直接送湿法冶炼工序使用。考虑应急备用需要储存300吨液态so2产品,后续深度冷却液化按25%负荷进行设计,制冷机组10的制冷量350kw,二级冷却器11出口处的温度约-13℃,故清洁炉气中的气态so2的液化率为90%,产能2.0t/h,设两台直径3500mm、长16500mm的储罐进行保冷(温)储存,需要时通过汽化器汽化后送湿法冶炼使用,少量不凝气体送湿法冶炼预还原使用。据估算,采用本实用新型的高氧燃烧硫磺
循环冷却制取so2的装置投资比so3还原硫磺法节省15%、运行综合费用节约20%,装置布置简洁占地少运行控制自动化,达到了节省投资降低生产运行成本目的,故适宜推广使用。
50.本实用新型的装置采用高氧燃烧硫磺制取高浓度so2气体或进而生产纯态so2产品,因硫磺和高氧气体都非常易得,生产装置相对独立不受其它工序牵制;特别是随着vpsa(真空变压吸附法)制氧技术的日臻成熟、装置大型化、作业高效,且制氧生产成本降低为制取高浓so2气体创造了有利条件;130℃~230℃的低温炉气由循环密封风机5输送并与温度为30℃~80℃、压力为+20kpa(g)~300kpa(g)的高氧气体混合为工艺气送入温度为850~1080℃的焚硫炉3内用于焚硫燃烧和降低炉温,且燃烧后混合气体中无气态单质硫,为后续清洁、便捷生产液态纯so2产品创造条件;该工艺流程简洁、生产效率高、更适宜大型化生产,投资节省20%、生产过程安全经济。
51.以上实施例仅为说明本实用新型的技术思想,不能以此限定本实用新型的保护范围,凡是按照本实用新型提出的技术思想,在技术方案基础上所做的任何改动,均落入本实用新型保护范围之内;本实用新型未涉及的技术均可通过现有技术加以实现。