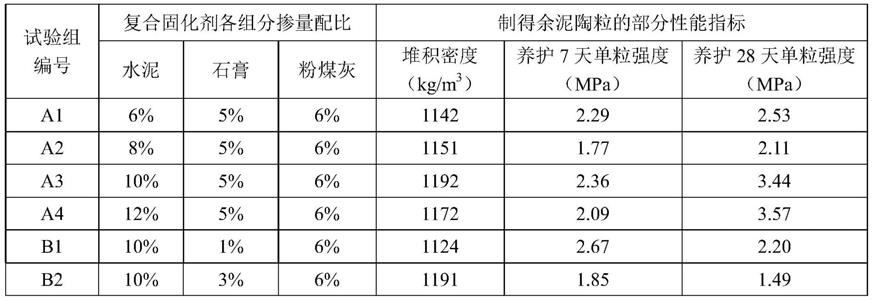
1.本发明属于废弃泥浆处理技术领域,尤其涉及一种利用工程泥浆制备轻质骨料的生产工艺。
背景技术:2.近年来随着城市化进程的不断推进,
3.中国城市化建设步伐加快,市政交通快速发展,地下空间建设突飞猛进。目前除了北上广深以外,沈阳、武汉、杭州、大连、青岛、西安等20余座城市也掀起了大规模修建地铁的热潮,在施工过程中会产生大量的工程渣土和泥浆。工程泥浆具有总量大、含水率高、呈液体状态难以运输,堆放消纳价格过高,排放占用大量土地,污染河流、湖泊、地下水、渗漏导致市政管道堵塞等问题,给政府和施工企业带来了很大的困扰。如何有效地再次利用这些废弃的工程泥浆,实现变废为宝,成为当前的一个棘手的难题。
4.另一方面,传统的保温材料中,大量采用陶粒作为轻质骨料。传统的陶粒制备主要以页岩、黏土或膨润土等不可再生自然资源为原料烧结而成,为了满足日益增长的陶粒生产的需要,就必须开采大量的优质黏土和页岩矿山等自然资源,造成耕地面积下降,土地荒漠化、盐渍化及水土流失等自然灾害。随着国家对环保、能耗的重视,大量消耗能源、污染环境的烧结工艺已被淘汰,因此,近年来此类陶粒生产加工企业已被全面叫停,轻质骨料缺乏成为当前城市化建设发展面临的另一个难题。
5.综上所述,市场迫切要求提供一种更加环保和经济的新型轻质骨料。
技术实现要素:6.本发明的目的在于克服上述缺陷,提供一种利用工程泥浆制备轻质骨料的方法,实现利用废弃的工程泥浆制造免烧结陶粒。
7.本发明利用工程泥浆制备轻质骨料的方法是这样实现的,包括以下步骤:
8.(1)将工程泥浆制成泥饼;
9.(2)把泥饼投入搅拌设备中并掺入降水剂和复合固化剂,然后搅碎搅均制成余泥粉料,所述降水剂为生石灰,所述复合固化剂由石膏、粉煤灰和水泥按一定配比组成;
10.(3)将余泥粉料作为原料投入造粒机,余泥粉料在造粒机中被固结制成余泥陶粒;
11.(4)对余泥陶粒进行养护,养护结束后即得到最终轻质骨料。
12.需要指出的是,为进一步提高所制备轻质骨料的的强度和耐水性,还可以对步骤(3)制得的余泥陶粒进行裹壳强化处理,具体的,在步骤(3)制成的余泥陶粒表面包裹粉状胶凝材料,实现余泥陶粒的裹壳强化处理,对裹壳强化处理后的余泥陶粒进行养护,养护结束后即得到最终轻质骨料。
13.当前造粒设备生产过程中对物料的含水率要求通常在20%左右,一般情况下,工程泥浆经压滤脱水后制得的所述泥饼的含水率在25%-40%,为满足造粒工序要求,生石灰的掺入量相对泥饼的质量百分比为4.8%-25%,具体应根据泥饼的含水率进行调整,使泥
饼的最终含水率为18%-22%;相应的,所掺入的复合固化剂中各主要成分相对泥饼的质量百分比依次为:石膏1%-7%,粉煤灰4%-10%,水泥6%-12%。优选的,所掺入的复合固化剂中各主要成分相对泥饼的质量百分比依次为:石膏5%,粉煤灰8%,水泥10%。
14.一般情况下,步骤(4)中余泥陶粒的养护条件为:在温度为20
±
2℃,相对湿度为95%的标准养护条件下养护至少7天。
15.裹壳强化后的余泥陶粒的养护条件为:在温度为20
±
2℃,相对湿度为95%的标准养护条件下养护至少7天。
16.余泥陶粒的裹壳强化处理过程中,可以选用的粉状胶凝材料多种多样,例如,粉状胶凝材料可以为水泥粉、或粉煤灰与水泥粉的复合粉料等等;此外,可以在雾化喷水的条件下在余泥陶粒表面包裹粉状胶凝材料。
17.本发明一种利用工程泥浆制备轻质骨料的方法,简单易行,其优点表现在:(1)将工程泥浆经压滤、固化、造粒、裹壳后制备免烧结陶粒,突破了废弃泥浆资源化利用瓶颈,为工程泥浆资源化利用、变废为宝提供技术途径;(2)利用固结机理制备免烧结陶粒,改变传统烧结工艺,降低了能耗和污染,更加环保和经济;(3)压滤脱水或固化后的泥饼中sio2、al2o3、fe2o3等化学成分组成与黏土相似,具有可部分甚至全部替代黏土生产陶粒的基础条件,采用本发明利用工程泥浆制备轻质骨料的方法,利用固化后的余泥制备免烧结陶粒,除了用于生产保温建材外,还可以用于部分或全部取代天然砂石骨料制备非承重再生建材产品,例如空心砌块、植挡块、草皮砖等,进而减少矿山开采,缓解资源短缺,实现工程泥浆变废为宝和升级再生利用。
附图说明
18.图1为实施例一中本发明一种利用工程泥浆制备轻质骨料的方法的工艺流程示意图。
19.图2为实施例一中水泥掺量对筒压强度的影响分析示意图。
20.图3为实施例一中石膏掺量对筒压强度的影响分析示意图。
21.图4为实施例一中粉煤灰掺量对筒压强度的影响分析示意图。
22.图5为实施例二中本发明一种利用工程泥浆制备轻质骨料的方法的工艺流程示意图。
23.图6为实施例二中裹壳强化处理前后余泥陶粒的筒压强度对照示意图。
24.图7为实施例二中裹壳强化处理前后余泥陶粒的吸水率对照示意图。
具体实施方式
25.实施例一
26.下面结合实施例对本发明一种利用工程泥浆制备轻质骨料的方法做进一步的详细说明。
27.如图1所示本发明一种利用工程泥浆制备轻质骨料的方法的工艺流程示意图,包括如下步骤:
28.(1)将工程泥浆制成泥饼;
29.(2)把泥饼投入搅拌设备中并掺入降水剂和复合固化剂,然后搅碎搅均制成余泥
粉料,所述降水剂为生石灰,所述复合固化剂由石膏、粉煤灰和水泥按一定配比组成;
30.(3)将余泥粉料作为原料投入造粒机,余泥粉料在造粒机中被固结制成余泥陶粒;
31.(4)对余泥陶粒进行养护,养护结束后即得到最终轻质骨料。
32.其中,步骤(1)中,当前最常用的工艺是利用压滤设备将工程泥浆制成泥饼,现有压滤设备所制成泥饼的含水率一般在25%-40%之间;
33.由于现有造粒机所采用物料的含水率一般需要控制在20%左右,因此在步骤(2)中需要填加降水剂(即生石灰),利用生石灰将泥饼的含水率控制在18%-22%,这样可以很好的满足造粒的使用要求,为实现这一目标,表1给出了泥饼含水率与生石灰掺量对照关系,在实际应用时,可以根据泥饼的实际含水率,选择适宜的生石灰掺量。
34.泥饼含水率25%28%31%34%37%40%生石灰掺量4.8%6.2%8.9%15.6%19.4%25%
35.表1泥饼含水率与生石灰掺量对照关系(注:生石灰掺量为生石灰相对泥饼的质量百分比)
36.此外,为了论证复合固化剂各组分掺量对产品性能的影响,如表2所示复合固化剂各组分掺量配比与制得余泥陶粒的部分性能指标对照表所示检测结果,可以看出,制得的余泥陶粒的堆积密度介于1124-1199kg/m3,和固化剂各组分的掺量无明显关联规律,根据规范《轻集料及其试验方法第一部分:轻集料》(gb/t 17431.1-2010),各试验组均满足轻集料堆积密度低于1200kg/m3的要求。另外还可以看出,所制得余泥陶粒的单粒强度离散性较大,和固化剂各组分掺量无明显的关联规律,28天单粒强度值介于1.49-3.57mpa。
[0037][0038][0039]
表2复合固化剂各组分掺量配比与制得余泥陶粒的部分性能指标对照表(注:复合固化剂各组分掺量为各组分相对泥饼的质量百分比)
[0040]
但是,由表3水泥掺量对筒压强度(简称:强度)的影响分析较图表可以看出,最初阶段随着水泥掺量的提升,余泥陶粒产品的筒压强度有明显提高,当水泥掺量达到10%以后,随着水泥掺量进一步提高,筒压强度的增长趋势明显变缓,其中,28天养护后产品的筒压强度甚至出现了回落。
[0041][0042]
表3水泥掺量对筒压强度的影响分析图表(石膏掺量:5%;粉煤灰掺量:6%)
[0043]
由表4石膏掺量对筒压强度的影响分析图表可以看出,最初阶段随着石膏掺量的提升,余泥陶粒产品的筒压强度有明显提高,当石膏掺量达到5%以后,随着石膏掺量进一步提高,14天养护后产品的筒压强度的增长趋势明显变缓,7天和28天养护后产品的筒压强度甚至出现明显下降。
[0044][0045]
表4石膏掺量对筒压强度的影响分析图表(水泥掺量:10%;粉煤灰掺量:6%)
[0046]
由表5粉煤灰掺量对筒压强度的影响分析图表可以看出,最初阶段随着粉煤灰掺量的提升,余泥陶粒产品的筒压强度有明显提高,当粉煤灰掺量达到8%以后,随着粉煤灰掺量进一步提高,产品的筒压强度呈全面下降趋势,综上所述,复合固化剂的各组分掺量最佳配比为:水泥掺量10%,石膏掺量5%,粉煤灰掺量8%,对应c3试验组;c3试验组余泥陶粒的软化系数可以按照如下过程进行测定:称取适量的c3试验组陶粒,浸水1h制备饱和面干试样,经测定,饱和面干筒压强度值为9.03mpa,与上述浸水前c3组28天强度值10.89mpa的比值为余泥陶粒的软化系数,经计算该余泥陶粒软化系数为0.83。
[0047][0048]
表5粉煤灰掺量对筒压强度的影响分析图表(水泥掺量:10%;石膏掺量:5%)
[0049]
另外,需要说明的是,本实施例图3-图6所示各试验组样件的制备过程中,步骤(2)的搅拌设备具体采用了科尼乐cqm倾斜式高效强力搅拌机;步骤(3)中造粒机具体选用了平模挤压造粒机;在步骤(4)中余泥陶粒的养护条件为:在温度为20
±
2℃,相对湿度为95%的标准养护条件下养护至少7天,本实施例图3-图6中所示各试验组样件的制备均采用该养护条件。
[0050]
本发明一种利用工程泥浆制备轻质骨料的方法,简单易行,其优点表现在:(1)将工程泥浆经压滤、固化、造粒后制备免烧结陶粒,突破了废弃泥浆资源化利用瓶颈,为工程泥浆资源化利用、变废为宝提供技术途径;(2)利用固结机理制备免烧结陶粒,改变传统烧结工艺,降低了能耗和污染,更加环保和经济;(3)压滤脱水或固化后的泥饼中sio2、al2o3、
fe2o3等化学成分组成与黏土相似,具有可部分甚至全部替代黏土生产陶粒的基础条件,采用本发明利用工程泥浆制备轻质骨料的方法,利用固化后的余泥制备免烧结余泥陶粒,除了用于生产保温建材外,还可以用于部分或全部取代天然砂石骨料制备非承重再生建材产品,例如空心砌块、植挡块、草皮砖等,进而减少矿山开采,缓解资源短缺,实现工程泥浆变废为宝和升级再生利用。
[0051]
实施例二
[0052]
如图5所示本发明一种利用工程泥浆制备轻质骨料的方法的工艺流程示意图,包括如下步骤:
[0053]
(1)将工程泥浆制成泥饼;
[0054]
(2)把泥饼投入搅拌设备中并掺入降水剂和复合固化剂,然后搅碎搅均制成余泥粉料,所述降水剂为生石灰,所述复合固化剂由石膏、粉煤灰和水泥按一定配比组成;
[0055]
(3)将余泥粉料作为原料投入造粒机,余泥粉料在造粒机中被固结制成余泥陶粒;
[0056]
(4)在余泥陶粒表面包裹粉状胶凝材料,实现余泥陶粒的裹壳强化处理;
[0057]
(5)对裹壳强化处理后余泥陶粒进行养护,养护结束后即得到最终轻质骨料。
[0058]
与实施例一中所述本发明一种利用工程泥浆制备轻质骨料的方法的区别在于,在制得余泥陶粒后,对余泥陶粒增加了裹壳强化处理工序,即在余泥陶粒表面包裹粉状胶凝材料;对裹壳强化后的余泥陶粒进行养护后即得到最终的轻质骨料。需要说明的是,本发明中所述粉状胶凝材料多种多样,包括水泥粉、或粉煤灰与水泥粉的复合粉料等等;此外,裹壳强化后的余泥陶粒的养护条件为:在温度为20
±
2℃,相对湿度为95%的标准养护条件下养护至少7天,本例所述各试验组样件的养护均是基于该养护条件制备。
[0059]
为了便于对本例所述技术方案的技术效果进行说明,本例中仍以c3试验组余泥陶粒为基础,以水泥粉作为粉状胶凝材料为例,利用圆盘造粒机,采用边雾化喷水边加水泥粉的方式实现对余泥陶粒的裹壳强化处理。此外,为了论证余泥陶粒与裹壳用粉状胶凝材料之间的最佳质量比,如表6所示,设计四种不同的余泥陶粒与水泥粉的质量比(1:0.15、1:0.25、1:0.35、1:0.45)进行裹壳强化处理试验,对应样件的试验组编号分别为d1-d4,为了方便说明,将余泥陶粒与水泥粉的质量比简称为核壳质量比。通过与c3试验组未裹壳强化处理的余泥陶粒进行对比可以看出,裹壳强化处理后得到的不同龄期的余泥陶粒,其筒压强度(简称:强度)相比同龄期未裹壳强化处理的余泥陶粒都有明显提升,并且在最初阶段,随水泥粉用量的增加强度也呈明显的增大趋势,总体上核壳质量比在1:0.35之前增长趋势都较明显,从1:0.35增加到1:0.45时,强度增长幅度趋于变缓,考虑到继续增加水泥粉用量会增加经济成本,因此,选取核壳质量比1:0.35为最优核壳质量比,经计算,核壳质量比为1:0.35的d3试验组余泥陶粒经28天养护后筒压强度相对于同龄期未裹壳的c3试验组余泥陶粒提高14.6%。
[0060]
[0061]
表6裹壳强化处理前后余泥陶粒的筒压强度对照图表
[0062]
如表7所示d1-d4试验组样件经养护28天后测得的单粒强度指标,其单粒强度数值范围为3.64-6.06mpa,由表2可知未裹壳强化处理的相同龄期c3试验组余泥陶粒的单粒强度数值为3.46mpa,相比之下可以看出,经过裹壳强化处理的余泥陶粒的单粒强度总体呈增大趋势,但是,经裹壳强化处理后余泥陶粒的单粒强度同样存在较大离散性,其单粒强度与水泥粉的用量并非呈线性关系。
[0063]
试验组编号核壳质量比单粒强度mpa(养护28d)d11:0.154.32d21:0.253.64d31:0.356.06d41:0.455.77
[0064]
表7裹壳强化处理后余泥陶粒的单粒强度统计表
[0065]
参照实施例一中提及的软化系数测定方式,称取适量的28天龄期d3试验组余泥陶粒,浸水1h制备饱和面干试样,测定饱和面干筒压强度值为11.23mpa,与浸水前d3试验组余泥陶粒强度值12.48mpa的比值为0.9,所以裹壳强化处理后余泥陶粒的软化系数为0.9。与未裹壳强化处理的c3试验组余泥陶粒软化系数0.83相比可知,用水泥粉裹壳强化处理后在余泥陶粒表面形成的壳体明显增强了余泥陶粒的耐水性。
[0066]
如表8所示裹壳强化处理前后余泥陶粒的吸水率对照图表,由该图表中罗列的数据可知,余泥陶粒经裹壳强化处理后1h和24h吸水率都明显降低,且吸水率随水泥粉用量的增加而逐渐降低,说明裹壳强化处理后,在余泥陶粒表面形成了致密的耐水壳体,明显改善了余泥陶粒的耐水性。
[0067]
试验组编号核壳质量比1h吸水率24h吸水率c3未裹壳17.5%19.0%d11:0.1516.4%18.1%d21:0.2514.5%15.7%d31:0.3511.8%12.6%d41:0.4510.9%11.5%
[0068]
表8裹壳强化处理前后余泥陶粒的吸水率对照图表
[0069]
如表9所示裹壳强化处理后余泥陶粒的堆积密度统计表,由其中数据可知,裹壳强化处理后余泥陶粒的堆积密度介于1074-1111kg/m3,随水泥粉用量的增加,堆积密度相差不大;与裹壳强化处理前的c3试验组余泥陶粒的堆积密度对比可以发现,裹壳强化处理后余泥陶粒的堆积密度降低,原因是裹壳强化处理后余泥陶粒尺寸变大,自然堆积空隙率变大,使得堆积密度略微降低。
[0070]
试验组编号核壳质量比堆积密度(kg/m3)d11:0.151111d21:0.251074d31:0.351078d41:0.451083
[0071]
表9裹壳强化处理后余泥陶粒的堆积密度统计表
[0072]
综上所述,与实施例一相比,本例所述本发明一种利用工程泥浆制备轻质骨料的方法的优势在于,由于增加了裹壳强化处理工序,按照这种方法制备的轻质骨料的单粒强度、筒压强度和耐水性都得到了显著提高,产品综合性能更加出色,性价比更高;此外,经裹壳强化处理后的余泥陶粒相对于未裹壳强化处理的余泥陶粒还具有粒型更好,外观更光滑圆润的优点。
[0073]
需要指出的是,本发明中的实施例仅为更好说明本发明的技术方案,并不应视为对本发明的限制,其中许多实施例中的技术特征也可以交叉使用,基于本发明技术原理,本领域技术人员可以对上述实施例所述技术方案重新进行组合或利用同类技术对其中某些材料进行简单替换,只要基于本发明的技术原理,都在本发明要求的保护范围中。