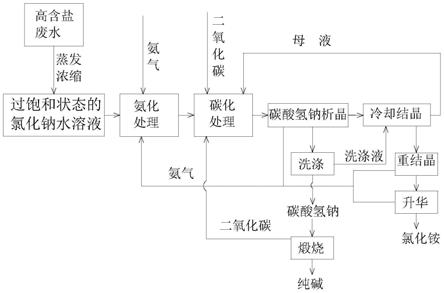
1.本发明涉及一种碳酸氢钠、氯化钠和氯化铵分离的工艺方法,具体为一种侯氏联合制碱过程中碱盐高效分离回收的资源化利用技术。
背景技术:2.近年来,工业副产废盐的产生量越来越大,这些化工副产废盐渣成分中含有大量的杂质盐与有毒有害有机物,随意处置会对环境造成极大破坏。
3.以氯化钠为原料生产纯碱工艺主要有氨碱法和联碱法,氨碱法存在原料氯化钠利用率低(钠的利用率约75%、氯的利用率为0%),制碱废液(含有大量氯化钙、氯化钠)排出系统量极大,浪费资源、形成新的环境污染。联碱法有“冷法”和“热法”之分。冷法联碱法以固体氯化钠为原料,经冷冻降温-盐析分离得到氯化铵,该法虽已实现大规模生产,但原料必需选用优质的固体盐,原料成本高,水不平衡的问题时有出现,冷析盐析结晶氯化铵电能消耗高,析铵母液循环量大。热法”回收氯化铵,经蒸发浓缩-结晶分离得到氯化铵,该法蒸发过程中耗水量大,能耗较大,成本较高,且氯化铵溶液对设备产生极强的腐蚀。上述两种工艺在实际生产中应用都有局限性。高温处理法是将废盐用于高温焰烧,温度在800℃以上,使用热设备,如回转窑和沸腾炉,使废盐中所含的有机物质在高温下分解为气体,达到去除目的。此法最难以解决的是盐在高温(高于盐的熔点)下发生熔融、结圈、结块,致使设备无法正常运行等工程问题,难以实现工业化。
4.中国专利cn101244829a报道了从制碱母液中通过真空多效逆流蒸发回收氯化铵和氯化钠,能耗较高,且多效分离氯化钠由于温度较高对离心机腐蚀较强,目前仍未见其工业化成功的报道。
5.专利cn 110372007 a报道了一种连续分离氯化铵和氯化钠的装置和方法,在混合盐连续洗涤器和多级串联连续分离器,氯化铵母液经浓缩蒸馏、降温析晶连续分离得到氯化钠和氯化铵产品。该法虽采用连续法操作,提高了操作效率,但也存在分离产品质量不高,浓缩能耗高等问题。
6.专利cn102153113 a报道了一种以芒硝型卤水与氨、二氧化碳为原料进行复分解反应后经高温脱氨、纳滤膜分离、蒸发分离得到联产碳酸钠、氯化钠、硫酸钠和氯化铵产品,该法采用液体卤水芒硝型为原料,工艺适应强,主副产品质量高,闭路循环无三废排放等特点,但该工艺高温蒸发浓缩盐硝母液中蒸汽能耗和生产成本偏高,分离效率不高,难以规模化生产。
7.cn 112723381 a公开了一种氯化铵和氯化钠混盐的资源化方法,该方法以氯化钠、氯化铵的混合固体废物为原料,采用加液碱反应、回收氨气、浓缩结晶等工艺处理该固体废弃物,回收得到洁净的氨水溶液,同时又得到氯化钠固体,实现了氯化铵和氯化钠的有效分离。该工艺以固体废弃物为原料,操作简单,能耗较低,减少了环境污染,但分离效果不高,产品纯度和质量不高,氯化钠单程转化率较低,氯化钠产品中nh
4+
离子残留过多,品质不高。
8.专利cn 102260002公开了一种采用微滤和纳滤方法处理氯化钠和氯化铵混合溶液的方法。此方法通过微滤、纳滤实现氯化钠和氯化铵的浓缩,同时,经过电解,产生氯气、氢气和氨气。此方法虽可产生清洁的能源,但是纳滤膜和微滤膜容易富集污染物,运行成本较高,一般企业难以接受。
技术实现要素:9.为了克服上述现有技术中的问题,本发明提供一种侯氏联合制碱过程中碱盐高效分离回收的方法。该方法具有原料成本低,流程较简单,投资少的优点,其生产环境好,无污染,经济效益较好,在处理过程中不产生废液、废渣,可将废盐分全部转化为有用成分,碱盐分离效果高,产品纯度高,达到资源最大化回收利用的目的,为实现废盐零排放提供了一种可行的工艺途径,有很好的推广前景。
10.为了实现本发明目的,所采用的技术方案为:一种侯氏联合制碱中化学升华-变温结晶分离碱盐的方法,按照下述步骤进行:
11.(1)将氯化钠经高纯水超声溶解配制成过饱和状态的氯化钠水溶液,经计量泵输送至氨化塔中,连续通入氨气进行氨化工序吸收成铵化高盐溶液,再经计量泵输送至碳化塔中,连续通入二氧化碳气体进行碳化工序处理成含碳酸氢盐的混合溶液;
12.(2)将含碳酸氢盐的混合溶液,经过滤、洗涤得到含有碳酸氢钠和氯化铵的碱盐粗品,碳酸氢钠经高温煅烧工序分解得到碳酸钠产品,煅烧过程产生的二氧化碳尾气,经洗涤、加压后循环套用至上述碳化塔中;氯化铵粗品经化学升华、凝华工序和干燥得到氯化铵产品,化学升华后释放出的氨气收集后循环套用至上述氨化塔中;
13.(3)过滤后的母液为含有氯化铵、氯化钠的水溶液,经高温结晶工序析出氯化钠粗品,经重结晶、脱色和干燥工序进一步精制为氯化钠产品;再经低温结晶工序析出氯化铵粗品,经重结晶、脱色和干燥工序进一步精制为氯化铵产品,使其中的氯化钠杂质含量降低到50ppm以下;高温结晶过程中释放的氨气收集后循环套用至上述氨化塔中,低温结晶和重结晶后的余液为溶有氯化钠、氯化铵的水溶液,循环套用至上述碳化塔中。
14.所述步骤(1)所述氨化工序是氯化钠饱和水溶液通过计量泵经氨化塔顶部喷淋流入,与从塔底鼓入的氨气进行逆流化学吸收,氯化钠饱和水溶液与氨气气体发生充分混合反应,气体从废气管道切向从塔顶部引入塔内循环处理,塔内侧顶部安装有喷淋装置;通过流速控制氯化钠饱和水溶液在氨化塔内的停留时间,化学吸收后的铵化高盐溶液从塔顶溢流口流出;所述氯化钠饱和水溶液浓度为20~50%(质量浓度),氨气与氯化钠的摩尔比为1.0~2.0:1,氨化温度为30~50℃,氨化时间0.5~1h,压力0.1~0.5mpa;
15.步骤(1)所述碳化工序是铵化高盐溶液通过计量泵经碳化塔顶部喷淋流入,与从塔底鼓入的二氧化碳进行逆流化学吸收,铵化高盐溶液与二氧化碳气体发生充分混合反应,气体从废气管道切向从塔顶部引入塔内循环处理,塔内侧顶部安装有喷淋装置;通过流速控制铵化高盐溶液在碳化塔内的停留时间,化学吸收后的铵化高盐溶液从塔顶溢流口流出;所述二氧化碳气体与铵化高盐溶液的摩尔比为1.0~1.5∶1,碳化温度为20~45℃,碳化时间0.5~1h,压力0.1~0.5mpa。
16.所述步骤(2)所述高温煅烧工序是在管式炉中连续进行,通过控温系统调节炉膛内的温度,程序升温(升温速率,10℃/min),含有碳酸氢钠和氯化铵的碱盐粗品经机械输送
连续进入管式炉腔体内进行高温煅烧,碳酸氢钠粗品分解得到碳酸钠产品,所述煅烧温度200~280℃,煅烧时间0.5~1h。
17.步骤(2)所述化学升华、凝华工序是在升华—凝华分离系统中进行,该系统是由原料缓冲罐、进料泵、出料泵、升华釜、凝华釜、预热器、冷凝器和循环泵依次连接组成,其中升华釜中放置有惰性粒子,防止固体爆沸,氯化铵粗品经升华系统热解为生成nh3和hcl气体,再经冷凝系统nh3和hcl两种气体迅速反应再次生成细小的nh4cl晶体,所述升华温度340~360℃,凝华温度65~70℃,压力0.1~0.5mpa。所述的惰性粒子包括玻璃珠、玛瑙珠、陶瓷片、石英砂、活性炭、分子筛、填料(鲍尔环、拉西环)、纤维球等一种或几种组成;形状为球形、圆柱形、正六面体形、四面体形、片状、椭圆形、针状、条形、环形、鞍形、栅板、波纹板等一种或几种组成;直径1~10mm。
18.所述步骤(3)所述高温结晶工序和低温结晶工序是在双温区结晶反应器和结晶分离器中连续进行,通过控温系统调节反应器内不同区域的温度变化,采用“分区控制、分段进料”的方式进行氯化钠和氯化铵的高效分离,通过程序变温来调节区域温度(高温区温升速率,2℃/min,低温区温降速率,1℃/min),含有氯化铵、氯化钠的母液在结晶反应器内进行高温区析晶和低温区析晶,经分离器分别得到氯化钠和氯化铵晶体,所述高温结晶区温度控制为20~30℃,低温结晶区温度为10~15℃。
19.进一步的,步骤(1)中氨化工序条件优选为控制氯化钠饱和水溶液浓度30~40%(质量浓度),氨气与氯化钠的摩尔比为1.0~1.5∶1,氨化温度为30~40℃,氨化时间0.6~0.8h,压力0.2~0.3mpa;碳化工序条件优选为控制二氧化碳气体与铵化高盐溶液的摩尔比为1.0~1.2∶1,碳化温度为30~40℃,碳化时间0.5~0.6h,压力0.2~0.4mpa。
20.进一步的,步骤(2)中高温煅烧工序条件优选为煅烧温度250~260℃,煅烧时间0.6~0.8h。步骤(2)中化学升华、凝华工序条件优选为升华温度340~350℃,凝华温度68~70℃,压力0.2~0.3mpa。
21.进一步的,步骤(3)高温结晶工序和低温结晶工序条件优选为高温结晶区温度控制为20~25℃,低温结晶区温度为10~12℃。
22.本发明提供的一种侯氏联合制碱过程中碱盐高效分离回收的方法,与现有技术相比具有如下技术优势:氯化钠的单程转化率提高达90%以上,氯化钠的总转化率超过95%,氨的总转化率达98%以上,碳酸钠收率>90%,氯化铵收率>90%,碳酸钠纯度>99%,氯化铵纯度>99%,使循环物料减少80%以上,大幅度的降低了物料和能量损耗,提高了经济效益,且对环境友好,采用化学升华对不同固相物质进行分离和纯化,分离效率高,产品纯度高,不产生三废,显著提升了盐产品价值和降低转化成本,解决废盐出路问题,实现危废近零排放。
附图说明
23.图1为本发明侯氏联合制碱中化学升华-变温结晶分离碱盐的工艺流程图。
具体实施方式
24.本发明不局限于下列具体实施方法,本领域一般技术人员根据本发明公开的内容,可以采用其他多种具体实施方式实施本发明的,或者凡是采用本发明的设计结构和思
路,做简单变化或更改的,都落入本发明的保护范围。需要说明的是,在不冲突的情况下,本发明中的实施例及实施例中的特征可以相互组合。下面结合具体实施案例,对本发明实施例中的技术方案进一步说明。
25.实施例1
26.一种侯氏联合制碱中化学升华-变温结晶分离碱盐的方法,包括如下步骤:
27.(1)将氯化钠经高纯水超声溶解配制成饱和状态的氯化钠水溶液,其中,氯化钠质量浓度为20%,在氨化塔连续通入氨气吸收成铵化高盐溶液,其中,氨气与氯化钠的摩尔比为1:1,铵化反应温度为30℃,铵化时间为0.5h,反应压力为0.1mpa。将铵化高盐溶液经计量泵输送至碳化塔,连续通入二氧化碳气体处理成含碳酸氢盐的混合溶液,其中碳化反应中二氧化碳与氯化钠的摩尔比为1:1,碳化反应温度为20℃,碳化时间为0.5h,反应压力为0.1mpa;
28.(2)将含有碳酸氢盐的混合溶液,在55℃的析晶温度下析出碳酸氢钠结晶;将碳酸氢钠结晶在250℃温度下,煅烧0.6h,得到碳酸钠产品,产生的二氧化碳气体搜集后循环套用;氯化铵粗品经化学升华、凝华工序和干燥得到氯化铵产品,其中,升华温度为340℃,凝华温度为68℃,过程中压力为0.2mpa,高温结晶温度20℃,低温结晶温度为10℃。氯化铵产品中氯化钠杂质含量降低到50ppm以下。化学升华后释放出的氨气收集后循环套用至上述氨化塔中;
29.本实施例制备得到的产品中碳酸钠收率为88.2%,氯化铵收率为89.2%,碳酸钠纯度为99.5%,氯化铵纯度为99.2%,氯化钠利用率为89.2%。
30.实施例2
31.一种侯氏联合制碱中化学升华-变温结晶分离碱盐的方法,包括如下步骤:
32.(1)将氯化钠经高纯水超声溶解配制成饱和状态的氯化钠水溶液,其中,氯化钠质量浓度为30%,在氨化塔连续通入氨气吸收成铵化高盐溶液,其中,氨气与氯化钠的摩尔比为1.5:1,铵化反应温度为40℃,铵化时间为1h,反应压力为0.3mpa。将铵化高盐溶液经计量泵输送至碳化塔,连续通入二氧化碳气体处理成含碳酸氢盐的混合溶液,其中碳化反应中二氧化碳与氯化钠的摩尔比为1.2:1,碳化反应温度为35℃,碳化时间为0.6h,反应压力为0.3mpa;
33.(2)将含有碳酸氢盐的混合溶液,在65℃的析晶温度下析出碳酸氢钠结晶;将碳酸氢钠结晶在250℃温度下,煅烧0.8h,得到碳酸钠产品,产生的二氧化碳气体搜集后循环套用;氯化铵粗品经化学升华、凝华工序和干燥得到氯化铵产品,其中,升华温度为350℃,凝华温度为68℃,过程中压力为0.3mpa,高温结晶温度20℃,低温结晶温度为12℃。氯化铵产品中氯化钠杂质含量降低到50ppm以下。化学升华后释放出的氨气收集后循环套用至上述氨化塔中;
34.本实施例制备得到的产品中碳酸钠收率为92.4%,氯化铵收率为93.6%,碳酸钠纯度为99.8%,氯化铵纯度为99.7%,氯化钠利用率为94.8%。
35.实施例3
36.一种侯氏联合制碱中化学升华-变温结晶分离碱盐的方法,包括如下步骤:
37.(1)将氯化钠经高纯水超声溶解配制成饱和状态的氯化钠水溶液,其中,氯化钠质量浓度为40%,在氨化塔连续通入氨气吸收成铵化高盐溶液,其中,氨气与氯化钠的摩尔比
为2:1,铵化反应温度为50℃,铵化时间为1h,反应压力为0.3mpa。将铵化高盐溶液经计量泵输送至碳化塔,连续通入二氧化碳气体处理成含碳酸氢盐的混合溶液,其中碳化反应中二氧化碳与氯化钠的摩尔比为1.5:1,碳化反应温度为45℃,碳化时间为1h,反应压力为0.3mpa;
38.(2)将含有碳酸氢盐的混合溶液,在75℃的析晶温度下析出碳酸氢钠结晶;将碳酸氢钠结晶在250℃温度下,煅烧1h,得到碳酸钠产品,产生的二氧化碳气体搜集后循环套用;氯化铵粗品经化学升华、凝华工序和干燥得到氯化铵产品,其中,升华温度为350℃,凝华温度为70℃,过程中压力为0.3mpa,高温结晶温度22℃,低温结晶温度为12℃。氯化铵产品中氯化钠杂质含量降低到50ppm以下。化学升华后释放出的氨气收集后循环套用至上述氨化塔中;
39.本实施例制备得到的产品中碳酸钠收率为92.1%,氯化铵收率为91.2%,碳酸钠纯度为99.7%,氯化铵纯度为99.5%,氯化钠利用率为93.8%。
40.实施例4
41.一种侯氏联合制碱中化学升华-变温结晶分离碱盐的方法,包括如下步骤:
42.(1)将氯化钠经高纯水超声溶解配制成饱和状态的氯化钠水溶液,其中,氯化钠质量浓度为50%,在氨化塔连续通入氨气吸收成铵化高盐溶液,其中,氨气与氯化钠的摩尔比为2:1,铵化反应温度为50℃,铵化时间为1h,反应压力为0.5mpa。将铵化高盐溶液经计量泵输送至碳化塔,连续通入二氧化碳气体处理成含碳酸氢盐的混合溶液,其中碳化反应中二氧化碳与氯化钠的摩尔比为1.2:1,碳化反应温度为40℃,碳化时间为0.6h,反应压力为0.4mpa;
43.(2)将含有碳酸氢盐的混合溶液,在85℃的析晶温度下析出碳酸氢钠结晶;将碳酸氢钠结晶在250℃温度下,煅烧0.8h,得到碳酸钠产品,产生的二氧化碳气体搜集后循环套用;氯化铵粗品经化学升华、凝华工序和干燥得到氯化铵产品,其中,升华温度为340℃,凝华温度为70℃,过程中压力为0.2mpa,高温结晶温度25℃,低温结晶温度为10℃。氯化铵产品中氯化钠杂质含量降低到50ppm以下。化学升华后释放出的氨气收集后循环套用至上述氨化塔中;
44.本实施例制备得到的产品中碳酸钠收率为92.4%,氯化铵收率为91.5%,碳酸钠纯度为99.6%,氯化铵纯度为99.6%,氯化钠利用率为94.1%。
45.实施例5
46.一种侯氏联合制碱中化学升华-变温结晶分离碱盐的方法,包括如下步骤:
47.(1)将氯化钠经高纯水超声溶解配制成饱和状态的氯化钠水溶液,其中,氯化钠质量浓度为40%,在氨化塔连续通入氨气吸收成铵化高盐溶液,其中,氨气与氯化钠的摩尔比为2:1,铵化反应温度为40℃,铵化时间为1h,反应压力为0.2mpa。将铵化高盐溶液经计量泵输送至碳化塔,连续通入二氧化碳气体处理成含碳酸氢盐的混合溶液,其中碳化反应中二氧化碳与氯化钠的摩尔比为1.2:1,碳化反应温度为40℃,碳化时间为0.6h,反应压力为0.3mpa;
48.(2)将含有碳酸氢盐的混合溶液,在75℃的析晶温度下析出碳酸氢钠结晶;将碳酸氢钠结晶在255℃温度下,煅烧0.6h,得到碳酸钠产品,产生的二氧化碳气体搜集后循环套用;氯化铵粗品经化学升华、凝华工序和干燥得到氯化铵产品,其中,升华温度为350℃,凝
华温度为68℃,过程中压力为0.3mpa,高温结晶温度20℃,低温结晶温度为12℃。氯化铵产品中氯化钠杂质含量降低到50ppm以下。化学升华后释放出的氨气收集后循环套用至上述氨化塔中;
49.本实施例制备得到的产品中碳酸钠收率为93.4%,氯化铵收率为93.5%,碳酸钠纯度为99.8%,氯化铵纯度为99.8%,氯化钠利用率为94.5%。
50.实施例6
51.一种侯氏联合制碱中化学升华-变温结晶分离碱盐的方法,包括如下步骤:
52.(1)将氯化钠经高纯水超声溶解配制成饱和状态的氯化钠水溶液,其中,氯化钠质量浓度为40%,在氨化塔连续通入氨气吸收成铵化高盐溶液,其中,氨气与氯化钠的摩尔比为2:1,铵化反应温度为50℃,铵化时间为1h,反应压力为0.5mpa。将铵化高盐溶液经计量泵输送至碳化塔,连续通入二氧化碳气体处理成含碳酸氢盐的混合溶液,其中碳化反应中二氧化碳与氯化钠的摩尔比为1.2:1,碳化反应温度为40℃,碳化时间为0.6h,反应压力为0.4mpa;
53.(2)将含有碳酸氢盐的混合溶液,在75℃的析晶温度下析出碳酸氢钠结晶;将碳酸氢钠结晶在260℃温度下,煅烧0.6h,得到碳酸钠产品,产生的二氧化碳气体搜集后循环套用;氯化铵粗品经化学升华、凝华工序和干燥得到氯化铵产品,其中,升华温度为350℃,凝华温度为68℃,过程中压力为0.3mpa,高温结晶温度20℃,低温结晶温度为10℃。氯化铵产品中氯化钠杂质含量降低到50ppm以下。化学升华后释放出的氨气收集后循环套用至上述氨化塔中;
54.本实施例制备得到的产品中碳酸钠收率为92.6%,氯化铵收率为92.8%,碳酸钠纯度为99.6%,氯化铵纯度为99.7%,氯化钠利用率为94.9%。
55.实施例7
56.一种侯氏联合制碱中化学升华-变温结晶分离碱盐的方法,包括如下步骤:
57.(1)将氯化钠经高纯水超声溶解配制成饱和状态的氯化钠水溶液,其中,氯化钠质量浓度为40%,在氨化塔连续通入氨气吸收成铵化高盐溶液,其中,氨气与氯化钠的摩尔比为1.5:1,铵化反应温度为40℃,铵化时间为0.8h,反应压力为0.1mpa。将铵化高盐溶液经计量泵输送至碳化塔,连续通入二氧化碳气体处理成含碳酸氢盐的混合溶液,其中碳化反应中二氧化碳与氯化钠的摩尔比为1.2:1,碳化反应温度为40℃,碳化时间为0.6h,反应压力为0.4mpa;
58.(2)将含有碳酸氢盐的混合溶液,在65℃的析晶温度下析出碳酸氢钠结晶;将碳酸氢钠结晶在260℃温度下,煅烧0.6h,得到碳酸钠产品,产生的二氧化碳气体搜集后循环套用;氯化铵粗品经化学升华、凝华工序和干燥得到氯化铵产品,其中,升华温度为350℃,凝华温度为68℃,过程中压力为0.3mpa,高温结晶温度20℃,低温结晶温度为10℃。氯化铵产品中氯化钠杂质含量降低到50ppm以下。化学升华后释放出的氨气收集后循环套用至上述氨化塔中;
59.本实施例制备得到的产品中碳酸钠收率为94.5%,氯化铵收率为93.8%,碳酸钠纯度为99.7%,氯化铵纯度为99.9%,氯化钠利用率为95.4%。
60.以上所述,仅为本发明较佳的具体实施方式,但本发明的保护范围并不局限于此,任何熟悉本技术领域的技术人员在本发明揭露的技术范围内,根据本发明的技术方案及其
构思加以等同替换或改变,都应涵盖在本发明的保护范围之内。