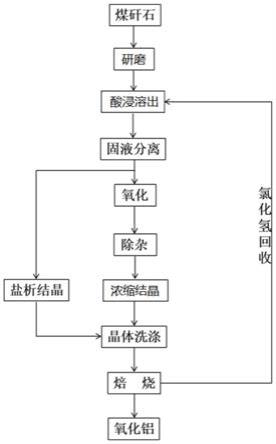
1.本发明属于煤炭领域,具体涉及用于从煤矸石中回收氧化铝的方法。
背景技术:2.煤矸石是采煤、洗煤过程中产生的固体废物,以内蒙古鄂尔多斯市准格尔旗黑岱沟露天矿为例,生产3000万吨/年煤炭,矸石排放量高达1400万吨/年。未被利用的煤矸石不仅占用土地,污染环境,而且当温度达到可燃物的燃烧点时,煤矸石堆中的残煤还会自燃,存在安全隐患。因此,针对不同地区煤矸石的物理化学特性,研究煤矸石高值化利用技术迫在眉睫。
3.黑岱沟露天矿煤矸石中主要矿物组成为高岭石和勃姆石,主要化学成分为al2o3和sio2,还含有少量的fe2o3、tio2、cao、mgo、p2o5、k2o和na2o等,其中al2o3含量可达50%,是优质的提铝原料。
4.cn 112897560 a提供了一种煤矸石制备高纯氧化铝的方法,该方法将煤矸石研磨、750℃焙烧、硫酸浸取、铵明矾结晶、晶体溶解,三次氯化氢盐析结晶制备99.95%的氧化铝,此方法存在焙烧耗能、反应过程中引入大量铵盐环保处理成本高和三次氯化氢盐析结晶制备成本高,相应的解析设备昂贵、产率低等缺点。cn 109516484 b公开了一种用电石泥粉煤灰和煤矸石烧结法生产氧化铝的方法。该方法含有生料配置、熟料烧结、熟料溶出、赤泥分离与洗涤、赤泥脱碱、粗液脱硅、晶种的制备、精液碳酸化分解、氢氧化铝分离与洗涤、氢氧化铝焙烧和母液蒸发等工序,存在工艺流程长,耗能,提铝残渣剩余大等缺点。cn 107473353 a使用氢氧化钠与煤矸石、硫铁矿烧渣1150℃一起活化1.5h,活化物与25%的盐酸以1:7的比例混合,在106℃下酸浸3h,然后在37℃下熟化36h得到聚合氯化铝铁,该方法使煤矸石中氧化铝的浸出率增大,但是活化温度过高,制备过程中对酸碱的消耗量也增加,并且盐酸浓度达到25%,熟化时间太长。cn 112811453 a公开了一种煤矸石为原料用微波水热法制备聚合氯化铝的方法,该方法包含焙烧、微波酸浸、聚合等工艺。微波加热,耗能,成本高不适合产业化应用。
5.目前,以煤矸石为原料制备氧化铝时,存在较多问题,尤其是成本高,不适合产业化应用。
技术实现要素:6.本发明的目的在于提供一种用于从煤矸石中回收氧化铝的方法,该方法成本低,工艺简单稳定。
7.为实现本发明的目的,采用以下的技术方案:
8.一种用于从煤矸石中回收氧化铝的方法,所述方法包括以下步骤:
9.(1)研磨:将煤矸石研磨成粉末状,得到粉末状煤矸石;
10.(2)酸浸:将步骤(1)所得粉末状煤矸石与酸和水混合进行酸浸溶出反应,然后对所得溶出料浆进行固液分离,得到含有氯化铝和氯化亚铁的酸浸液和固体残渣;
11.(3)结晶:通过方法一和/或方法二将步骤(2)所得酸浸液中的氯化铝结晶析出,得到氯化铝粗晶体;其中,
12.方法一包括以下步骤:
13.①
氧化:向步骤(2)所得酸浸液中加入氧化剂以发生氧化反应,得到含有氯化铝和氯化铁的氧化酸浸液;
14.②
分离:将步骤
①
所得氧化酸浸液通过阴离子交换树脂,以吸附除去其中的氯化铁,得到氯化铝精制液;
15.③
浓缩结晶:将步骤
②
所得氯化铝精制液加热浓缩后冷却结晶,然后固液分离,得到氯化铝粗晶体和分离液;
16.方法二包括以下步骤:
17.向步骤(2)所得酸浸液中通入氯化氢气体以发生盐析反应,得到氯化铝粗晶体;
18.(4)洗涤:对步骤(3)所得氯化铝粗晶体进行洗涤和过滤,得到氯化铝晶体;
19.(5)焙烧:对步骤(4)所得氯化铝晶体进行焙烧热解,得到氧化铝和氯化氢气体。
20.在一种实施方式中,步骤(1)中,将煤矸石研磨至粒度为50-300目,优选100-300目,比如150目、200目和250目。
21.本领域技术人员理解,可采用本领域常用的研磨设备进行研磨,比如球磨机。
22.为了提高溶出率,在一种实施方式中,步骤(2)中,所述粉末状煤矸石与所述酸的质量比为1:(1.5-5),比如1:2、1:2.5、1:3、1:3.5、1:4和1:4.5;优选所述酸为无机酸,优选为盐酸、硝酸和硫酸中中的任一种或多种的组合,进一步优选盐酸。在一种实施方式中,步骤(2)中,粉末状煤矸石、酸和水混合所得的混合液中,固含量为220-280g/l。
23.为了进一步提高溶出率,在一种实施方式中,步骤(2)中,溶出温度为120-200℃,比如130℃、140℃、150℃、160℃、170℃、180℃和190℃;溶出时间为1-5h,比如1.5h、2h、2.5h、3h、3.5h、4h和4.5h。
24.在一种实施方式中,步骤(3)所述方法一的步骤
①
中,所述氧化反应的反应温度为60-80℃,比如62℃、64℃、66℃、68℃、70℃、72℃、74℃、75℃、76℃和78℃,从而使氧化反应顺利进行,以将步骤(2)所得酸浸液中的亚铁离子fe
2+
氧化为铁离子fe
3+
。
25.在一种实施方式中,步骤(3)所述方法一的步骤
①
中,所述氧化剂的用量为步骤(2)所得酸浸液中的氯化亚铁完全转化为氯化铁时所需氧化剂的理论用量的1.0-1.8倍,比如1.1倍、1.2倍、1.3倍、1.4倍、1.5倍、1.6倍和1.7倍。
26.在一种实施方式中,步骤(3)所述方法一的步骤
①
中,所述氧化剂为硝酸、臭氧、次氯酸钠和氯气中的任一种或多种的组合,优选为臭氧或氯气,进一步优选为臭氧;进一步优选臭氧的进气量为2-6g/h,比如2.5g/h、3g/h、3.5g/h、4g/h、4.5g/h、5g/h和5.5g/h;进一步优选进气流量为1-3l/min,比如1.2l/min、1.4l/min、1.5l/min、1.6l/min、1.8l/min、2l/min、2.2l/min、2.4l/min、2.5l/min、2.6l/min和2.8l/min。
27.本领域技术人员理解,臭氧是采用空气或者氧气制备的,并不是纯的臭氧,其中含有部分空气或氧气。
28.在一种实施方式中,步骤(3)所述方法一的步骤
②
中,吸附温度为60-80℃,比如62℃、64℃、66℃、68℃、70℃、72℃、74℃、75℃、76℃和78℃;
29.优选地,步骤(3)所述方法一的步骤
②
中,所述氧化酸浸液的体积流速为2-3倍(比
如2.1倍、2.2倍、2.3倍、2.4倍、2.5倍、2.6倍、2.7倍、2.8倍和2.9倍)所述阴离子交换树脂的体积/h。
30.比如,阴离子交换树脂的体积为100ml时,所述氧化酸浸液的体积流速为200-300ml/h。
31.在一种实施方式中,步骤(3)所述方法一的步骤
②
中,所述阴离子交换树脂为季胺型阴离子交换树脂,比如201*7、d201和d202。
32.季胺型阴离子交换树脂为强碱性阴离子交换树脂,是指含功能基团为季铵基(-n
+
r3)的带不同反电荷离子的一类树脂。在铵化时功能基团为三甲胺(-n
+
(ch3)3)时得到的树脂是强碱i型阴离子交换树脂,如国产的201*7、d201等;用二甲基乙醇胺(-n
+
(ch3)2c2h4oh)铵化时得到的树脂是强碱ii型阴离子交换树脂,如d202等。
33.在一种实施方式中,所述氧化酸浸液在通过所述阴离子交换树脂时,过柱方式为下进上出或者上进下出,优选所述阴离子交换树脂的树脂柱为单柱或双柱串联。
34.在一种实施方式中,步骤(3)所述方法一的步骤
③
中,浓缩温度为80-150℃,比如85℃、90℃、95℃、100℃、105℃、110℃、115℃、120℃、125℃、130℃、135℃、140℃和145℃,从而便于稳定、快速地将步骤
②
所得氯化铝精制液浓缩至合适的浓度,有利于其中的氯化铝冷却结晶;
35.优选地,步骤(3)所述方法一的步骤
③
中,所述氯化铝精制液浓缩至其中氯化铝的浓度为30-70wt%,比如35wt%、40wt%、45wt%、50wt%、55wt%、60wt%和65wt%,从而利于其中的氯化铝冷却结晶。
36.在一种实施方式中,步骤(3)所述方法一的步骤
③
中,所得分离液返混至步骤
②
所得氯化铝精制液中进行循环浓缩结晶,从而将分离液中的氯化铝尽可能多地回收并循环浓缩,提高氯化铝的结晶率;
37.优选地,步骤(3)所述方法一的步骤
③
中,所得分离液返混至步骤
②
所得氯化铝精制液中进行循环浓缩结晶,至所得分离液中杂质镁或硅的浓度≥1g/l(即所得分离液中镁单质和硅单质中任一项的浓度≥1g/l)。
38.在一种实施方式中,步骤(3)所述方法二中,所述盐析反应的反应温度为45-70℃,比如50℃、55℃、60℃和65℃;反应时间为3-5h,比如3.5h、4h和4.5h,从而使氯化铝晶体缓慢析出,减少杂质夹带,降低杂质析出率,提高晶体质量;优选所述盐析反应在双玻璃反应器的内层进行,可以起到保温作用。
39.优选地,步骤(3)所述方法二中,待料液的酸度为20-31wt%(比如21wt%、22wt%、23wt%、24wt%、25wt%、26wt%、27wt%、28wt%、29wt%和30wt%时,停止氯化氢气体的通入,反应结束。
40.在一种实施方式中,步骤(3)所述方法二中,所述盐析反应是在搅拌下进行,优选搅拌速率为45-135转/分钟,比如50转/分钟、55转/分钟、60转/分钟、65转/分钟、70转/分钟、75转/分钟、80转/分钟、85转/分钟、90转/分钟、95转/分钟、100转/分钟、105转/分钟、110转/分钟、115转/分钟、120转/分钟、125转/分钟和130转/分钟。
41.在一种实施方式中,步骤(3)所述方法二中,在通入氯化氢气体的同时,还通入空气,且是将氯化氢气体和空气混合后所得的混合气体通入步骤(2)所得酸浸液中;优选空气和氯化氢气体的流量分别为0.3-1.5l/min,比如0.4l/min、0.5l/min、0.6l/min、0.7l/min、
0.8l/min、0.9l/min、1.0l/min、1.1l/min、1.2l/min、1.3l/min和1.4l/min。
42.通入氯化氢气体的同时通入空气,能够稀释氯化氢气体,从而降低反应速率,使氯化铝晶体析出时杂质夹带比较小,降低杂质随氯化铝晶体的析出率,提高氯化铝晶体的质量。
43.在一种实施方式中,步骤(3)所述方法二包括以下步骤:
44.取步骤(2)所得酸浸液置于双玻璃反应器的内层;然后在恒温水浴和搅拌的情况下,将所述双玻璃反应器内层的料液升温至45-70℃,比如50℃、55℃、60℃和65℃;然后通入空气和氯化氢气体的混合气至所述双玻璃反应器内层的料液内,以发生盐析反应3-5h,比如3.5h、4h和4.5h;待料液的酸度为20-31wt%(比如21wt%、22wt%、23wt%、24wt%、25wt%、26wt%、27wt%、28wt%、29wt%和30wt%)时,停止通入气体,对反应后的料浆进行固液分离,得到氯化铝粗晶体;
45.优选搅拌速率为45-135转/分钟,比如50转/分钟、55转/分钟、60转/分钟、65转/分钟、70转/分钟、75转/分钟、80转/分钟、85转/分钟、90转/分钟、95转/分钟、100转/分钟、105转/分钟、110转/分钟、115转/分钟、120转/分钟、125转/分钟和130转/分钟;优选空气和氯化氢气体的流量分别为0.3-1.5l/min,比如0.4l/min、0.5l/min、0.6l/min、0.7l/min、0.8l/min、0.9l/min、1.0l/min、1.1l/min、1.2l/min、1.3l/min和1.4l/min。
46.在一种实施方式中,空气和氯化氢气体的流量通过本领域常用的流量计控制,比如转子流量计。
47.在一种实施方式中,步骤(4)中,所述洗涤为用盐酸淋洗,优选淋洗所用盐酸与氯化铝粗晶体的质量比为(0.5-2.5):1,比如0.75:1、1:1、1.1:1、1.2:1、1.25:1、1.3:1、1.4:1、1.5:1、1.75:1、2:1和2.25:1;优选淋洗所用盐酸的浓度为26-32wt%,比如27wt%、28wt%、29wt%、30wt%和31wt%。
48.步骤(4)中,所述过滤可以为本领域常用的过滤方式,比如抽滤。
49.在一种实施方式中,步骤(5)中,焙烧温度为750-1200℃,比如775℃、800℃、825℃、850℃、875℃、900℃、925℃、950℃、975℃、1000℃、1025℃、1050℃、1075℃、1100℃、1125℃、1150℃和1175℃;优选焙烧时间为2-4h,比如2.5h、3h和3.5h。
50.在一种实施方式中,所述方法还包括步骤(6),将步骤(5)中焙烧所产生的氯化氢气体返送至步骤(2)中。
51.本发明的有益效果在于:
52.本发明的用于从煤矸石中回收氧化铝的方法,成本低、工艺简单稳定、结晶方法可根据需要灵活选择,能够制备得到氧化铝,且所得氧化铝的纯度可达到99.4wt%以上,达到了冶金级氧化铝的标准(纯度达到98.6wt%)。
附图说明
53.图1是本发明用于从煤矸石中回收氧化铝的方法中在一种实施方式中的流程图。
具体实施方式
54.以下结合具体实施方式/实施例对本发明的技术方案及其效果做进一步说明。以下实施方式/实施例仅用于说明本发明的内容,发明并不仅限于下述实施方式或实施例。应
用本发明的构思对本发明进行的简单改变都在本发明要求保护的范围内。
55.以下实施例中,原料煤矸石来源于准能黑岱沟露天矿选煤厂,其中的主要成分含量如表1所示。
56.表1煤矸石样品的主要成分(ω(b)/10-2
)
[0057][0058][0059]
其他原料来源如下:
[0060]
盐酸:盐酸含量为36wt%,购自内蒙古康诚化工有限公司;
[0061]
阴离子交换树脂:d201,廊坊圣泉化工有限公司。
[0062]
实施例1
[0063]
如图1所示,一种用于从煤矸石中回收氧化铝的方法,包括以下步骤:
[0064]
(1)研磨:将煤矸石在球磨机中研磨至粒度为150目,得到粉末状煤矸石;
[0065]
(2)酸浸:将步骤(1)所得粉末状煤矸石与盐酸和水混合后于搅拌下进行酸浸溶出反应,然后对所得溶出料浆进行固液分离,得到含有氯化铝和氯化亚铁的酸浸液和固体残渣;其中,所述粉末状煤矸石与所述酸的质量比为1:2.5,溶出温度为160℃,溶出时间为2h,搅拌速率为90转/分钟;
[0066]
(3)结晶:通过方法一将步骤(2)所得酸浸液中的氯化铝结晶析出,得到氯化铝粗晶体;其中,
[0067]
方法一包括以下步骤:
[0068]
①
氧化:向步骤(2)所得酸浸液中通入臭氧以发生氧化反应,得到含有氯化铝和氯化铁的氧化酸浸液;其中,所述氧化反应的反应温度为70℃,臭氧进气量为3g/h,气体流量为2l/min;
[0069]
②
分离:将步骤
①
所得氧化酸浸液通过100ml阴离子交换树脂d201,以吸附除去其中的氯化铁,得到氯化铝精制液;其中,吸附温度为80℃,所述氧化酸浸液的体积流速为300ml/h;过柱方式为下进上出,树脂柱为单柱;
[0070]
③
浓缩结晶:将步骤
②
所得氯化铝精制液加热浓缩至其中氯化铝的浓度为40wt%后冷却结晶,然后固液分离,得到氯化铝粗晶体和分离液,将所得分离液返混至步骤
②
所得氯化铝精制液中进行循环浓缩结晶,至所得分离液中杂质镁或硅的浓度≥1g/l;其中,浓缩温度为120℃;
[0071]
(4)洗涤:对步骤(3)所得氯化铝粗晶体进行洗涤和过滤,得到氯化铝晶体;其中,所述洗涤为用盐酸淋洗,具体是将步骤(3)所得氯化铝粗晶体置于布氏漏斗的滤布表面,采用盐酸淋洗;淋洗所用盐酸与氯化铝粗晶体的质量比为1:1,淋洗所用盐酸的浓度为30wt%;
[0072]
(5)焙烧:对步骤(4)所得氯化铝晶体进行焙烧热解,得到氧化铝产品a1和氯化氢气体;其中,焙烧温度为1050℃,焙烧时间为3h;
[0073]
(6)将步骤(5)所得氯化氢气体返送至步骤(2)中。
[0074]
实施例2
[0075]
与实施例1相比,仅有以下区别:
[0076]
步骤(1)中,研磨至粒度为200目;
[0077]
步骤(2)中,所述粉末状煤矸石与所述酸的质量比为1:3.5,溶出温度为150℃,搅拌速率为160转/分钟;
[0078]
步骤(3)所述方法一中的步骤
①
中,臭氧进气量为6g/h;
[0079]
步骤(3)所述方法一的步骤
②
中,阴离子交换树脂为zg513,所述氧化酸浸液的体积流速为200ml/h;
[0080]
步骤(4)中,淋洗所用盐酸与氯化铝粗晶体的质量比为1:1.5;
[0081]
最终得氧化铝产品a2。
[0082]
实施例3
[0083]
与实施例1相比,仅有以下区别:
[0084]
步骤(2)中,溶出温度为200℃,溶出时间为1h;
[0085]
不含步骤(6);
[0086]
最终得氧化铝产品a3。
[0087]
实施例4
[0088]
与实施例1相比,仅有以下区别:
[0089]
步骤(3)是通过方法二将步骤(2)所得酸浸液中的氯化铝结晶析出,得到氯化铝粗晶体;其中,
[0090]
方法二包括以下步骤:
[0091]
向步骤(2)所得酸浸液中通入氯化氢气体以发生盐析反应,得到氯化铝粗晶体;其中,具体过程如下:
[0092]
取550ml步骤(2)所得酸浸液,装入双玻璃反应器的内层;然后在60℃恒温水浴和搅拌速率为45
±
5转/分钟的情况下将双玻璃反应器内层的料液升温至约60℃;然后将流量分别为0.4l/min的空气和氯化氢气体进料至缓冲瓶中混合,然后将混合气通入至双玻璃反应器内层的料液内(即料液液面下方)于约60℃下进行盐析反应3h以上;待料液的酸度为29wt%时,停止空气和氯化氢气体的通入,结束反应;将双玻璃反应器内层的料液取出并对其进行抽滤,得到氯化铝粗晶体;
[0093]
步骤(5)中,焙烧温度为1000℃;
[0094]
最终得氧化铝产品a4。
[0095]
实施例5
[0096]
与实施例4的区别仅在于:
[0097]
步骤(3)所述方法二中,搅拌速率为90
±
5转/分钟;待料液的酸度为30wt%时,停止空气和氯化氢气体的通入,结束反应;
[0098]
步骤(4)中,淋洗所用盐酸与氯化铝粗晶体的质量比为1:1.5;
[0099]
最终得氧化铝产品a5。
[0100]
实施例1-5的结果:
[0101]
1、实施例1-5中步骤(2)中经酸浸溶出后所得固体残渣的主要成分见表2;
[0102]
表2实施例1-5中步骤(2)所得固体残渣的主要成分及其含量
[0103][0104][0105]
其中,loi是指烧失量,是指干燥的固体残渣在1000-1100℃灼烧后失去的重量百分比。
[0106]
2、实施例1-5中,煤矸石中氧化铝的溶出率和所得氧化铝产品的纯度见表3,所得氧化铝的主要杂质成分及含量见表4;
[0107]
表3实施例1-5中煤矸石中氧化铝的溶出率和所得氧化铝产品的纯度
[0108]
实施例煤矸石中氧化铝的溶出率(wt%)所得氧化铝产品的纯度(wt%)18999.9288.799.5388.1399.4488.799.6588.4799.4
[0109]
表4实施例1-5中所得氧化铝产品的主要杂质成分及其含量
[0110]