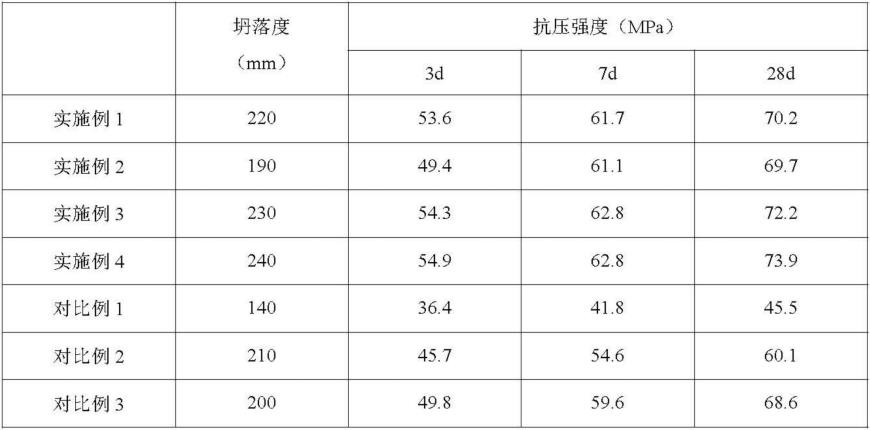
1.本发明涉及建筑技术领域,具体为一种利用建筑垃圾制备的高强混凝土及其制备方法。
背景技术:2.混凝土作为世界上最大宗的建筑材料被广泛应用各类建筑结构中,混凝土建筑已成为我国建筑领域的主流。虽然相较于木质结构与钢质结构的建筑,混凝土建筑有着耐久价廉的优点,但随着时间的推移,混凝土建筑也会出现各种问题,并最终导致出现安全隐患而进行废弃处理。在混凝土建筑废弃处理后,便成为了人们口中的建筑垃圾,并且与生活垃圾相比,建筑垃圾有着数量巨大,无法降解的特点,同时也无法依靠焚烧处理,只能使用掩埋的方式将其丢弃。同时在现有的建筑垃圾再利用过程中,由于破碎后的建筑垃圾表面仍吸附由大量的水化后的水泥砂浆,将其破碎再利用后,这些多孔的水泥砂浆附着会使由建筑垃圾制备的骨料吸水率较大,同时由于破碎过程中的外力破坏作用,会使骨料中伴有大量的微小裂隙,造成其强度下降,使建筑出现安全隐患。因此目前大多数的建筑垃圾生产的骨料只能用于低强度的混凝土,用于地面砖、垫层等,无法制备高强度混凝土,大大限制了建筑垃圾的再利用范围。
技术实现要素:3.本发明的目的在于提供一种利用建筑垃圾制备的高强混凝土及其制备方法,以解决上述背景技术中提出的问题。
4.为了解决上述技术问题,本发明提供如下技术方案:一种利用建筑垃圾制备的高强混凝土的制备方法包括以下步骤:
5.s1.制备再生骨料:
6.s11.将建筑垃圾破碎成粒径为10-25mm的连续级配的再生骨料颗粒,经过磁选与浮选后去除再生骨料颗粒中的铁质材料、木质材料与塑料,晾干;
7.s12.将硅灰、粉煤灰、矿渣、萘系减水剂和水混合搅拌制备为低浓度浸泡液,将晾干后的再生骨料颗粒浸泡在低浓度浸泡液中,缓慢加入氢氧化钠调节ph值至10.5-11.5,利用真空浸渍的方式浸泡15-30min后,取出晾干;
8.s13.将硅灰、粉煤灰、矿渣、萘系减水剂和水混合搅拌制备为高浓度浓度浸泡液,再次浸泡再生骨料颗粒,浸泡缓慢加入氢氧化钠调节ph值至10.5-11.5,浸泡时长为 20-40min,浸泡结束后,取出晾干;
9.s14.将晾干后的再生骨料颗粒移入密闭容器内,通入co2循环加热,加热2-3h后,得到再生骨料;
10.s2.将水泥、活性掺合料、强化纤维与细骨料混合均匀后,加入天然粗骨料,混合均匀后,加入再生粗骨料搅拌混合,得到混凝土集料;
11.s3.将减水剂溶于拌合水后,一块加入搅拌机内,与混凝土集料搅拌均匀后,倒出
成型固化,得到高强度混凝土。
12.建筑垃圾制备的骨料中,往往在其表面含有较多的硬化水泥砂浆,其中含有大量的微孔,会使得其与拌合水接触时吸收过量的拌合水,使的利用建筑垃圾制备的混凝土的水灰比变大,影响混凝土强度;同时再生骨料在制备过程中,伴有大量的破碎过程,在外力的作用下,会使其内部伴有大量的微孔裂隙,使其强度下降,造成混凝度的强度损失。同时建筑垃圾中还含有大量的钢筋以及木质材料与塑料材料等,制备混凝土的过程中,这些杂质会影响骨料的整体强度的弱点,最终导致混凝土的强度缺陷。
13.本发明在利用建筑垃圾制备再生骨料是,首先将建筑垃圾破碎为颗粒级配连续的骨料颗粒,之后利用磁吸的方式去除建筑垃圾中的钢筋等铁质元素,之后又利用密度不同的特点,浮选去除捡出垃圾中常见的木材以及塑料等杂质,纯化骨料颗粒的同时,也可以去除骨料破碎是吸附的砂浆粉末,防止在后续处理与制备混凝土时,砂浆粉末会影响减水剂效果。
14.之后本发明配置了低浓度浸泡液与高浓度浸泡液,浸泡液内使用的材料为硅灰、粉煤灰与矿渣,均为具有高反应活性的玻璃态物质,在外界环境激发下会发生水化反应,生成水化硅酸钙相物质。本发明首先配置使用的低浓度浸泡液,在减水剂的表面活性作用下,浸泡液会浸入再生骨料中的微小缝隙内,在在外界添加的碱激发下,其内部组分中含有的硅灰、粉煤灰与矿渣会迅速水化,生成水化硅酸钙相填充密实再生骨料的缝隙,从而达到增强再生骨料强度的目的,同时为了避免浸泡时,生成的生成水化硅酸钙相物质晶粒生长过程中体积膨胀,造成缝隙进一步扩大,本发明将浸泡液分为了低浓度与高浓度,首先用低浓度液填充内部微小孔隙,再使用高浓度浸泡液填充较大的孔隙与缺陷。在弥补再生骨料强度的同时,生成的水化硅酸钙相也会填充并密实再生骨料表面的砂浆中的微小孔洞,降低拌合中微小孔洞的吸水率。
15.在经过浸泡液浸泡后,再生骨料表面会生成大量的水化硅酸钙相,本发明此时利用高温co2养护,会加速水化硅酸钙生成碳酸钙,致密再生骨料的表面,并提高再生骨料的表观密度,提升其力学性能。
16.ca(oh)2+co2→
caco3+h2o
17.c-s-h+co2→
caco3+sio2·
nh2o;
18.进一步的,步骤s12中,按重量比例计,所述硅灰、粉煤灰、矿渣、萘系减水剂和水的比例为(0.1-0.15)(0.1-0.12)∶(0.1-0.12)∶(0.005-0.01)∶1。
19.进一步的,步骤s13中,按重量比例计,所述硅灰、粉煤灰、矿渣、萘系减水剂和水的比例为(0.3-0.4)∶(0.2-0.3)∶(0.2-0.3)∶(0.01-0.03)∶1。
20.进一步的,步骤s14中,加热温度为75-85℃,co2浓度为30-50%,加热湿度为30-40%。
21.进一步的,按重量份数计,所述高强度混凝土包括以下组分:450-550份天然粗骨料、 500-600份再生粗骨料、600-680份细骨料、水泥300-350份、活性掺合料210-260份、减水剂5.1-15份、强化纤维50-80份、290-340份拌合水。
22.进一步的,所述天然粗骨料为粒径在10-25mm的连续级配的石子;所述细骨料为粒径在1-3mm的河砂。
23.进一步的,所述活性掺合料为硅灰、粉煤灰与高炉矿渣的混合物,其中,按重量比
例计,所述的硅灰、粉煤灰、高炉矿渣的掺加比例为(2-3)∶(1-1.5)∶(0.5-0.8)。
24.进一步的,所述减水剂为磺系减水剂、萘系减水剂中的任一种,所述强化纤维为经硝酸溶液浸泡洗净干燥后的pva纤维,其中pva纤维直径在10-50μm,长度为20-30mm。
25.与现有技术相比,本发明所达到的有益效果是:本发明对再生骨料进行了筛除杂质,之后利用活性掺合料与减水剂制备的低浓度浸泡液与高浓度浸泡液,浸泡处理再生骨料颗粒,并利用氢氧化钠调节浸泡液ph值,碱激发活性掺合料,使其发生火山灰反应生成水化硅酸钙相物质填充再生骨料内部的微小缝隙弥补强度,并填充覆盖再生骨料表面砂浆孔洞减少再生骨料吸水率,之后又利用二氧化碳气体在高温下加速与水化硅酸钙相物质反应,生成碳酸钙,密实再生骨料表面。经处理后,再生骨料强度得到弥补,并且降低了再生骨料的吸水率从而降低了混凝土的水灰比,增强了混凝土的施工性能与强度。
具体实施方式
26.下面将对本发明实施例中的技术方案进行清楚、完整地描述,显然,所描述的实施例仅仅是本发明一部分实施例,而不是全部的实施例。基于本发明中的实施例,本领域普通技术人员在没有做出创造性劳动前提下所获得的所有其他实施例,都属于本发明保护的范围。
27.实施例1.
28.一种利用建筑垃圾制备的高强混凝土,制备方法包括以下步骤:
29.s1.制备再生骨料:
30.s11.将建筑垃圾破碎成粒径为10-25mm的连续级配的骨料颗粒,经过磁选与浮选后去除骨料颗粒中的铁质材料、木质材料与塑料,晾干;
31.s12.将硅灰、粉煤灰、矿渣、萘系减水剂和水混合搅拌制备为低浓度浸泡液,其中按重量比例计,所述硅灰、粉煤灰、矿渣、萘系减水剂和水的比例为0.15∶0.1∶0.1∶0.01∶1,将晾干后的骨料颗粒浸泡在低浓度浸泡液中,浸泡液没过骨料颗粒2-3cm,缓慢加入氢氧化钠调节ph值为11.5,利用真空浸渍的方式浸泡30min后,取出晾干;
32.s13.将硅灰、粉煤灰、矿渣、萘系减水剂和水混合搅拌制备为高浓度浓度浸泡液,其中按重量比例计,所述硅灰、粉煤灰、矿渣、萘系减水剂和水的比例为0.4∶0.2∶0.2∶ 0.03∶1,再次浸泡骨料颗粒,浸泡液没过骨料颗粒2-3cm,缓慢加入氢氧化钠调节ph值至11,浸泡时长为40min,浸泡结束后,取出晾干;
33.s14.将晾干后的骨料颗粒移入密闭容器内,通入co2循环加热,加热温度为75℃, co2浓度为30%,加热湿度为30%;加热2h后,得到再生骨料;
34.s2.按重量份数计,将300份水泥、210份活性掺合料105份硅灰、79份粉煤灰、26 份高炉矿渣、50份pva纤维与600份细骨料混合均匀后,加入450份天然粗骨料,混合均匀后,加入600份再生粗骨料搅拌混合,得到混凝土集料;
35.s3.将10份萘系减水剂溶于310份拌合水后,一块加入搅拌机内,与混凝土集料搅拌均匀后,倒出成型固化,得到高强度混凝土。
36.实施例2.
37.与实施例1相比,本实施例降低了步骤s12与步骤s13中的ph值;
38.一种利用建筑垃圾制备的高强混凝土,制备方法包括以下步骤:
39.s1.制备再生骨料:
40.s11.将建筑垃圾破碎成粒径为10-25mm的连续级配的骨料颗粒,经过磁选与浮选后去除骨料颗粒中的铁质材料、木质材料与塑料,晾干;
41.s12.将硅灰、粉煤灰、矿渣、萘系减水剂和水混合搅拌制备为低浓度浸泡液,其中按重量比例计,所述硅灰、粉煤灰、矿渣、萘系减水剂和水的比例为0.15∶0.1∶0.1∶0.01∶1,将晾干后的骨料颗粒浸泡在低浓度浸泡液中,浸泡液没过骨料颗粒2-3cm,缓慢加入氢氧化钠调节ph值为10.5,利用真空浸渍的方式浸泡30min后,取出晾干;
42.s13.将硅灰、粉煤灰、矿渣、萘系减水剂和水混合搅拌制备为高浓度浓度浸泡液,其中按重量比例计,所述硅灰、粉煤灰、矿渣、萘系减水剂和水的比例为0.4∶0.2∶0.2∶ 0.03∶1,再次浸泡骨料颗粒,浸泡液没过骨料颗粒2-3cm,缓慢加入氢氧化钠调节ph值至10.5,浸泡时长为40min,浸泡结束后,取出晾干;
43.s14.将晾干后的骨料颗粒移入密闭容器内,通入co2循环加热,加热温度为75℃, co2浓度为30%,加热湿度为30%;加热2h后,得到再生骨料;
44.s2.按重量份数计,将300份水泥、210份活性掺合料105份硅灰、79份粉煤灰、26 份高炉矿渣、50份pva纤维与600份细骨料混合均匀后,加入450份天然粗骨料,混合均匀后,加入600份再生粗骨料搅拌混合,得到混凝土集料;
45.s3.将10份萘系减水剂溶于310份拌合水后,一块加入搅拌机内,与混凝土集料搅拌均匀后,倒出成型固化,得到高强度混凝土。
46.实施例3.
47.与实施例1相比,本实施例增加了步骤s14中co2的浓度;
48.一种利用建筑垃圾制备的高强混凝土,制备方法包括以下步骤:
49.s1.制备再生骨料:
50.s11.将建筑垃圾破碎成粒径为10-25mm的连续级配的骨料颗粒,经过磁选与浮选后去除骨料颗粒中的铁质材料、木质材料与塑料,晾干;
51.s12.将硅灰、粉煤灰、矿渣、萘系减水剂和水混合搅拌制备为低浓度浸泡液,其中按重量比例计,所述硅灰、粉煤灰、矿渣、萘系减水剂和水的比例为0.15∶0.1∶0.1∶0.01∶1,将晾干后的骨料颗粒浸泡在低浓度浸泡液中,浸泡液没过骨料颗粒2-3cm,缓慢加入氢氧化钠调节ph值为11.5,利用真空浸渍的方式浸泡30min后,取出晾干;
52.s13.将硅灰、粉煤灰、矿渣、萘系减水剂和水混合搅拌制备为高浓度浓度浸泡液,其中按重量比例计,所述硅灰、粉煤灰、矿渣、萘系减水剂和水的比例为0.4∶0.2∶0.2∶ 0.03∶1,再次浸泡骨料颗粒,浸泡液没过骨料颗粒2-3cm,缓慢加入氢氧化钠调节ph值至11,浸泡时长为40min,浸泡结束后,取出晾干;
53.s14.将晾干后的骨料颗粒移入密闭容器内,通入co2循环加热,加热温度为75℃, co2浓度为50%,加热湿度为30%;加热2h后,得到再生骨料;
54.s2.按重量份数计,将300份水泥、210份活性掺合料105份硅灰、79份粉煤灰、26 份高炉矿渣、50份pva纤维与600份细骨料混合均匀后,加入450份天然粗骨料,混合均匀后,加入600份再生粗骨料搅拌混合,得到混凝土集料;
55.s3.将10份萘系减水剂溶于310份拌合水后,一块加入搅拌机内,与混凝土集料搅拌均匀后,倒出成型固化,得到高强度混凝土。
56.实施例4.
57.与实施例1相比,本实施例增加了步骤s14的加热时间;
58.一种利用建筑垃圾制备的高强混凝土,制备方法包括以下步骤:
59.s1.制备再生骨料:
60.s11.将建筑垃圾破碎成粒径为10-25mm的连续级配的骨料颗粒,经过磁选与浮选后去除骨料颗粒中的铁质材料、木质材料与塑料,晾干;
61.s12.将硅灰、粉煤灰、矿渣、萘系减水剂和水混合搅拌制备为低浓度浸泡液,其中按重量比例计,所述硅灰、粉煤灰、矿渣、萘系减水剂和水的比例为0.15∶0.1∶0.1∶0.01∶1,将晾干后的骨料颗粒浸泡在低浓度浸泡液中,浸泡液没过骨料颗粒2-3cm,缓慢加入氢氧化钠调节ph值为11.5,利用真空浸渍的方式浸泡30min后,取出晾干;
62.s13.将硅灰、粉煤灰、矿渣、萘系减水剂和水混合搅拌制备为高浓度浓度浸泡液,其中按重量比例计,所述硅灰、粉煤灰、矿渣、萘系减水剂和水的比例为0.4∶0.2∶0.2∶0.03∶1,再次浸泡骨料颗粒,浸泡液没过骨料颗粒2-3cm,缓慢加入氢氧化钠调节ph值至11,浸泡时长为40min,浸泡结束后,取出晾干;
63.s14.将晾干后的骨料颗粒移入密闭容器内,通入co2循环加热,加热温度为75℃, co2浓度为30%,加热湿度为30%;加热3h后,得到再生骨料;
64.s2.按重量份数计,将300份水泥、210份活性掺合料105份硅灰、79份粉煤灰、26 份高炉矿渣、50份pva纤维与600份细骨料混合均匀后,加入450份天然粗骨料,混合均匀后,加入600份再生粗骨料搅拌混合,得到混凝土集料;
65.s3.将10份萘系减水剂溶于310份拌合水后,一块加入搅拌机内,与混凝土集料搅拌均匀后,倒出成型固化,得到高强度混凝土。
66.对比例1.
67.与实施例1相比,本对比例未对骨料颗粒进行步骤s12-s14的处理;
68.一种利用建筑垃圾制备的高强混凝土,制备方法包括以下步骤:
69.s1.制备再生骨料:
70.s11.将建筑垃圾破碎成粒径为10-25mm的连续级配的骨料颗粒,经过磁选与浮选后去除骨料颗粒中的铁质材料、木质材料与塑料,晾干得到再生骨料;
71.s2.按重量份数计,将300份水泥、210份活性掺合料105份硅灰、79份粉煤灰、26 份高炉矿渣、50份pva纤维与600份细骨料混合均匀后,加入450份天然粗骨料,混合均匀后,加入600份再生粗骨料搅拌混合,得到混凝土集料;
72.s3.将10份萘系减水剂溶于310份拌合水后,一块加入搅拌机内,与混凝土集料搅拌均匀后,倒出成型固化,得到高强度混凝土。
73.对比例2.
74.与实施例1相比,本对比例未低浓度浸泡液处理骨料颗粒;
75.一种利用建筑垃圾制备的高强混凝土,制备方法包括以下步骤:
76.s1.制备改性再生骨料:
77.s11.将建筑垃圾破碎成粒径为10-25mm的连续级配的骨料颗粒,经过磁选与浮选后去除骨料颗粒中的铁质材料、木质材料与塑料,晾干;
78.s12.将硅灰、粉煤灰、矿渣、萘系减水剂和水混合搅拌制备为高浓度浓度浸泡液,
其中按重量比例计,所述硅灰、粉煤灰、矿渣、萘系减水剂和水的比例为0.4∶0.2∶0.2∶ 0.03∶1,再次浸泡骨料颗粒,浸泡液没过骨料颗粒2-3cm,缓慢加入氢氧化钠调节ph值至11,浸泡时长为40min,浸泡结束后,取出晾干;
79.s13.将晾干后的骨料颗粒移入密闭容器内,通入co2循环加热,加热温度为75℃, co2浓度为30%,加热湿度为30%;加热2h后,得到改性再生骨料;
80.s2.按重量份数计,将300份水泥、210份活性掺合料105份硅灰、79份粉煤灰、26 份高炉矿渣、50份pva纤维与600份细骨料混合均匀后,加入450份天然粗骨料,混合均匀后,加入600份再生粗骨料搅拌混合,得到混凝土集料;
81.s3.将10份萘系减水剂溶于310份拌合水后,一块加入搅拌机内,与混凝土集料搅拌均匀后,倒出成型固化,得到高强度混凝土。
82.对比例3.
83.与实施例1相比,本对比例未对骨料颗粒进行步骤s14处理;
84.一种利用建筑垃圾制备的高强混凝土,制备方法包括以下步骤:
85.s1.制备改性再生骨料:
86.s11.将建筑垃圾破碎成粒径为10-25mm的连续级配的骨料颗粒,经过磁选与浮选后去除骨料颗粒中的铁质材料、木质材料与塑料,晾干;
87.s12.将硅灰、粉煤灰、矿渣、萘系减水剂和水混合搅拌制备为低浓度浸泡液,其中按重量比例计,所述硅灰、粉煤灰、矿渣、萘系减水剂和水的比例为0.15∶0.1∶0.1∶0.01∶1,将晾干后的骨料颗粒浸泡在低浓度浸泡液中,浸泡液没过骨料颗粒2-3cm,缓慢加入氢氧化钠调节ph值为11.5,利用真空浸渍的方式浸泡30min后,取出晾干;
88.s13.将硅灰、粉煤灰、矿渣、萘系减水剂和水混合搅拌制备为高浓度浓度浸泡液,其中按重量比例计,所述硅灰、粉煤灰、矿渣、萘系减水剂和水的比例为0.4∶0.2∶0.2∶ 0.03∶1,再次浸泡骨料颗粒,浸泡液没过骨料颗粒2-3cm,缓慢加入氢氧化钠调节ph值至11,浸泡时长为40min,浸泡结束后,取出晾干,得到改性再生骨料;
89.s2.按重量份数计,将300份水泥、210份活性掺合料105份硅灰、79份粉煤灰、26 份高炉矿渣、50份pva纤维与600份细骨料混合均匀后,加入450份天然粗骨料,混合均匀后,加入600份再生粗骨料搅拌混合,得到混凝土集料;
90.s3.将10份萘系减水剂溶于310份拌合水后,一块加入搅拌机内,与混凝土集料搅拌均匀后,倒出成型固化,得到高强度混凝土。
91.根据《gb/t50080》和《gb/t50081》对实施例1-4和对比例1-3制备的混凝土进行检测,检测结果见下表:
[0092][0093]
通过实施例1-2的对比可以发现,早对再生骨料进行处理时,浸泡液的ph的大小对混凝土早期强度影响较大,高ph值可以加速浸泡液中的活性掺合料的水化,形成水化硅酸钙相填充再生骨料颗粒中的微小裂缝,弥补强度并减少再生骨料的吸水性;通过实施例 1、3、4的对比可以发现,再生骨料的炭化,可以提高混凝土的强度与坍落度,减少再生骨料的吸水,增加施工性能;通过实施例1与对比例1的对比可以发现,未经过处理的再生骨料颗粒强度低,吸水性强;通过实施例1与对比例2的对比可以发现,直接使用高浓度浸泡液虽然可以提升再生骨料强度,但提升效果较小;通过实施例1与对比例3的对比,可以发现再生骨料的炭化工艺可以有效提升再生骨料的表面致密度,降低吸水率。
[0094]
最后应说明的是:以上所述仅为本发明的优选实施例而已,并不用于限制本发明,尽管参照前述实施例对本发明进行了详细的说明,对于本领域的技术人员来说,其依然可以对前述各实施例所记载的技术方案进行修改,或者对其中部分技术特征进行等同替换。凡在本发明的精神和原则之内,所作的任何修改、等同替换、改进等,均应包含在本发明的保护范围之内。