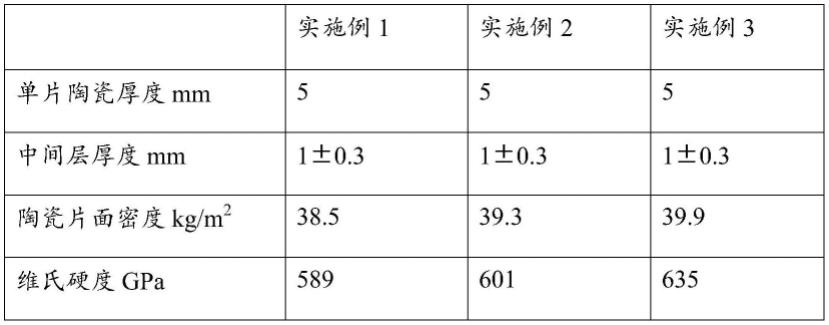
1.本发明涉及新材料技术领域,具体涉及一种防弹陶瓷复合材料。
背景技术:2.一直以来金属都是人们用来制作防护装备的唯一选择,直至90年代,高强度陶瓷的出现和应用促进了防弹产业中产品和技术的革新,陶瓷防弹插板开始风靡整个防弹装备市场,成为了防弹市场上的主流产品。
3.陶瓷和金属的防弹机理有很大的不同,金属是由于塑性变形而吸收射弹的动能,而陶瓷是由于其破裂而吸收射弹的动能。对于防弹陶瓷来说,影响性能的因素非常多,例如:密度和气孔率、硬度、断裂韧性、杨氏模量、声速、机械强度等。
4.通常硬度越高的材料,其易碎性越大。虽然防弹陶瓷有超强的硬度,但是陶瓷脆性大,容易出现碎裂的情况,在撞击陶瓷板的同时,巨大的撞击力会使防弹陶瓷板碎裂产生裂痕,有裂痕的部位是无法再次抵抗袭击的,因此提高防弹陶瓷的韧性是值得研究的课题。现有技术中主要是通过纤维增强陶瓷来降低陶瓷的脆性,以增加防弹陶瓷的韧性,但是目前制备的纤维增强陶瓷材料制备方法复杂,并且成本也较高,与同等防御级别的防弹钢板相比,陶瓷板的价格至少高出200%,限制了防弹陶瓷的加工和使用。
技术实现要素:5.发明目的,针对现有技术中的不足之处,本发明提供了一种防弹陶瓷复合材料。并提供了相应的制备方法。
6.技术方案:本发明提供了一种防弹陶瓷复合材料,所述的防弹陶瓷复合材料包括陶瓷基体和有机弹性体,所述的有机弹性体为聚脲弹性体;所述的陶瓷基体由碳化硼、氧化钛、氧化铝、碳化硅晶须组成,配比为:碳化硼50~60份、氧化钛2-3份、氧化铝10~15份、碳化硅晶须30~50份。具有的,所述的聚脲弹性体配方为:异氰酸酯预聚体10-20份、聚四氢呋喃二醇10-20份、端氨基聚氧化丙烯5-10份、二乙基甲苯二胺2-5份、辛酸亚锡1-5份、硅丙乳液10-20份。
7.具体的,所述的防弹陶瓷复合材料为三层结构,依次包括陶瓷基体、有机弹性体、陶瓷基体。当弹头射入时,与陶瓷碰撞,弹头变形吸收一部分动能,陶瓷碎裂吸收一部分被转化为震动的动能;弹头继续侵入破碎的陶瓷,与陶瓷发生磨削作用,弹头被粉碎,损失大部分动能;弹头碎屑及破碎陶瓷的残余动能被弹性体的弹性形变所吸收,剩余的动能可以被最后一层陶瓷所阻挡。
8.本发明所述的防弹陶瓷复合材料,按如下方法制备得到:将碳化硼、氧化钛、氧化铝、碳化硅晶须混合,将n-β-(氨乙基)-γ-氨丙基三甲氧基硅烷与甲苯的混合液加入并淹没球料,进行球磨,球磨后的混合粉料,进行过筛,选取粒径小于100微米的混合粉料,与间苯二酚和甲醛一起加入反应基础液中,粉料完全浸没于液体中,搅拌后,过滤,得到包覆了酚醛树脂涂层的混合粉料,干燥后进行压制,压制成型后,进行烧结,最后冷却至室温,得到
陶瓷基体;在密闭空间内,将陶瓷基体的一侧,浸润于聚脲弹性体中,延缓其固化时间,于未固化之前取出;两片陶瓷基体将浸润的一面互相贴合,进行热压,即制备得到所述的防弹陶瓷复合材料。
9.本发明颗粒包覆了酚醛树脂涂层,在烧结时会形成纳米级厚度的碳涂层,并且,过调混合粉体的与间苯二酚和甲醛的之间的比例可以实现对颗粒外部碳涂层厚度的控制。本发明原料粉粒包覆碳涂层能够显著降低碳化硼、氧化铝和碳化硅晶须之间的界面结合强度,使其保持在一个适当的强度,保证陶瓷材料内部载荷的有效传递。
10.本发明采用碳化硅晶须,当复合陶瓷基体产生裂纹,裂纹扩展到达晶须时,被迫沿晶须偏转,这意味着裂纹的前行路径更长,裂纹尖端的应力强度减少,裂纹偏转的角度越大,能量释放率就越低,断裂韧性就提高。裂纹扩展遇到高强度晶须时,在裂纹尖端附近晶须与晶面上存在较大的剪切应力,该应力极易造成晶须与晶界的分裂,晶须可以从基体中拔出,因界面摩擦而消耗外界载荷的能量而达到增韧的目的,同时晶须从基体中拔出会产生微裂纹来吸收更多的能量,防弹效果更好。
11.本发明通过湿法球磨可以使各个原料的粉末均匀的分散,尽量减少局部团聚,此外本发明是将改性与球磨相结合,使得改性效果更好。本发明通过n-β-(氨乙基)-γ-氨丙基三甲氧基硅烷对粉状混合颗粒进行表面改性后,可以增加混合颗粒在水和无水乙醇中的分散性,同时颗粒的表面带有大量氨基基团,有利于后续进行酚醛树脂的原位聚合,并且这些氨基基团可以有效粘结颗粒与和酚醛树脂涂层。
12.具体的,所述的球磨,球料比为10:1,转速为200-400r/min,球磨5-8h,。
13.具体的,所述的反应基础液由30-35份无水乙醇、1-2份氨水、100份水组成。
14.具体的,所述的烧结为:以5℃/min的速率升高烧结温度到50℃,保温30-60min,随后升高温度至900℃,保温100-120min,再次升高温度至1200℃后,同时加压至30mpa,恒温恒压保持100-120min,。
15.具体的,间苯二酚、甲醛、基础反应液的质量比例为,间苯二酚40-50份、甲醛50-60份、基础反应液100份。
16.本发明所述的防弹陶瓷复合材料的制备方法,具体的包括如下步骤:
17.步骤1,将碳化硼50~60份、氧化钛2-3份、氧化铝10~15份、碳化硅晶须30~50份混合,球料比为10:1,将n-β-(氨乙基)-γ-氨丙基三甲氧基硅烷与甲苯的混合液加入至球磨罐,淹没球料,进行球磨,转速为200-400r/min,球磨5-8h,球磨后的混合粉料,进行过筛,选取粒径小于100微米的混合粉料。
18.步骤2,将上述步骤得到的混合粉料与间苯二酚和甲醛一起加入反应基础液(30-35份无水乙醇、1-2份氨水、100份水)中,粉料完全浸没于液体中,搅拌20-24h后,过滤,得到包覆了酚醛树脂涂层的混合粉料。
19.步骤3,将上述混合粉料干燥后进行压制,压力为60-80兆帕,压制成型后,进行烧结,以5℃/min的速率升高烧结温度到50℃,保温30-60min,随后升高温度至900℃,保温100-120min,再次升高温度至1200℃后,同时加压至30mpa,恒温恒压保持100-120min,最后冷却至室温,得到陶瓷基体。
20.步骤4,在密闭空间内,将陶瓷基体的一侧,浸润于聚脲弹性体中,聚脲弹性体的配方为:间苯二酚、甲醛、基础反应液的质量比例为,间苯二酚40-50份、甲醛50-60份、基础反
应液100份,延缓其固化时间,于未固化之前取出;两片陶瓷基体将浸润的一面互相贴合,进行热压,即制备得到所述的防弹陶瓷复合材料。
21.进一步的,本发明的最佳方案为:
22.步骤1,将碳化硼40份、氧化钛3份、氧化铝12份、碳化硅晶须40份混合,球料比为10:1,将n-β-(氨乙基)-γ-氨丙基三甲氧基硅烷与甲苯的混合液加入至球磨罐,淹没球料,进行球磨,转速为300r/min,球磨6h,球磨后的混合粉料,进行过筛,选取粒径小于100微米的混合粉料。
23.步骤2,将上述步骤得到的混合粉料与间苯二酚和甲醛一起加入反应基础液(32份无水乙醇、2份氨水、100份水)中,粉料完全浸没于液体中,搅拌24h后,过滤,得到包覆了酚醛树脂涂层的混合粉料。
24.步骤3,将上述混合粉料干燥后进行压制,压力为60-80兆帕,压制成型后,进行烧结,以5℃/min的速率升高烧结温度到50℃,保温60min,随后升高温度至900℃,保温120min,再次升高温度至1200℃后,同时加压至30mpa,恒温恒压保持120min,最后冷却至室温,得到陶瓷基体。
25.步骤4,在密闭空间内,将陶瓷基体的一侧,浸润于聚脲弹性体中,聚脲弹性体的配方为:间苯二酚、甲醛、基础反应液的质量比例为,间苯二酚45份、甲醛55份、基础反应液100份,延缓其固化时间,于未固化之前取出;两片陶瓷基体将浸润的一面互相贴合,进行热压,即制备得到所述的防弹陶瓷复合材料。
26.有益效果:本发明的陶瓷基体受到子弹的冲击后,防弹材料自身形变、碎裂吸收子弹的动能,同时利用自身硬度改变弹头或破片的形状消耗子弹的动能;聚脲弹性体通过材料的拉伸变形、断裂等方式消耗弹头的动能。
27.本发明所提供的陶瓷基复合材料,具有较好的强度和韧性,具有较好的防弹性能。
具体实施方式
28.下面是实施例对本发明方案进行详细说明,但是本发明的保护范围不局限于所述实施例。本技术中所述的份数均指质量份数(明确说明的除外)。
29.实施例1
30.步骤1,将碳化硼50份、氧化钛2份、氧化铝10份、碳化硅晶须30份混合,球料比为10:1,将n-β-(氨乙基)-γ-氨丙基三甲氧基硅烷与甲苯的混合液加入至球磨罐,淹没球料,进行球磨,转速为200r/min,球磨5h,球磨后的混合粉料,进行过筛,选取粒径小于100微米的混合粉料。
31.步骤2,将上述步骤得到的混合粉料与间苯二酚和甲醛一起加入反应基础液(30份无水乙醇、1份氨水、100份水)中,粉料完全浸没于液体中,搅拌20-24h后,过滤,得到包覆了酚醛树脂涂层的混合粉料。
32.步骤3,将上述混合粉料干燥后进行压制,压力为60-80兆帕,压制成型后,进行烧结,以5℃/min的速率升高烧结温度到50℃,保温30min,随后升高温度至900℃,保温100min,再次升高温度至1200℃后,同时加压至30mpa,恒温恒压保持100min,最后冷却至室温,得到陶瓷基体。
33.步骤4,在密闭空间内,将陶瓷基体的一侧,浸润于聚脲弹性体中,聚脲弹性体的配
方为:间苯二酚、甲醛、基础反应液的质量比例为,间苯二酚40份、甲醛50份、基础反应液100份,延缓其固化时间,于未固化之前取出;两片陶瓷基体将浸润的一面互相贴合,进行热压,即制备得到所述的防弹陶瓷复合材料。
34.实施例2
35.步骤1,将碳化硼60份、氧化钛3份、氧化铝15份、碳化硅晶须50份混合,球料比为10:1,将n-β-(氨乙基)-γ-氨丙基三甲氧基硅烷与甲苯的混合液加入至球磨罐,淹没球料,进行球磨,转速为400r/min,球磨8h,球磨后的混合粉料,进行过筛,选取粒径小于100微米的混合粉料。
36.步骤2,将上述步骤得到的混合粉料与间苯二酚和甲醛一起加入反应基础液(35份无水乙醇、2份氨水、100份水)中,粉料完全浸没于液体中,搅拌24h后,过滤,得到包覆了酚醛树脂涂层的混合粉料。
37.步骤3,将上述混合粉料干燥后进行压制,压力为80兆帕,压制成型后,进行烧结,以5℃/min的速率升高烧结温度到50℃,保温30min,随后升高温度至900℃,保温100min,再次升高温度至1200℃后,同时加压至30mpa,恒温恒压保持120min,最后冷却至室温,得到陶瓷基体。
38.步骤4,在密闭空间内,将陶瓷基体的一侧,浸润于聚脲弹性体中,聚脲弹性体的配方为:间苯二酚、甲醛、基础反应液的质量比例为,间苯二酚50份、甲醛60份、基础反应液100份,延缓其固化时间,于未固化之前取出;两片陶瓷基体将浸润的一面互相贴合,进行热压,即制备得到所述的防弹陶瓷复合材料。
39.实施例3
40.步骤1,将碳化硼40份、氧化钛3份、氧化铝12份、碳化硅晶须40份混合,球料比为10:1,将n-β-(氨乙基)-γ-氨丙基三甲氧基硅烷与甲苯的混合液加入至球磨罐,淹没球料,进行球磨,转速为300r/min,球磨6h,球磨后的混合粉料,进行过筛,选取粒径小于100微米的混合粉料。
41.步骤2,将上述步骤得到的混合粉料与间苯二酚和甲醛一起加入反应基础液(32份无水乙醇、2份氨水、100份水)中,粉料完全浸没于液体中,搅拌24h后,过滤,得到包覆了酚醛树脂涂层的混合粉料。
42.步骤3,将上述混合粉料干燥后进行压制,压力为60-80兆帕,压制成型后,进行烧结,以5℃/min的速率升高烧结温度到50℃,保温60min,随后升高温度至900℃,保温120min,再次升高温度至1200℃后,同时加压至30mpa,恒温恒压保持120min,最后冷却至室温,得到陶瓷基体。
43.步骤4,在密闭空间内,将陶瓷基体的一侧,浸润于聚脲弹性体中,聚脲弹性体的配方为:间苯二酚、甲醛、基础反应液的质量比例为,间苯二酚45份、甲醛55份、基础反应液100份,延缓其固化时间,于未固化之前取出;两片陶瓷基体将浸润的一面互相贴合,进行热压,即制备得到所述的防弹陶瓷复合材料。
44.对实施例1-实施例3所得产品进行性能测试。数据如下表所示:
[0045][0046][0047]
下表为不同子弹在相同环境下,对于实施例3所制备得到产品测试时的凹陷数据。
[0048]
弹头类型m8056式普通弹ss109弹头质量/k9.67.93.95弹速(m/s)839701915最大凹陷/mm211715是否穿透未穿透未穿透未穿透
[0049]
从上面的试验可以看出,本发明所提供的陶瓷基复合材料,具有较好的强度和韧性,具有较好的防弹性能。以上所述仅为本技术的优选实施例而已,并不用于限制本技术。