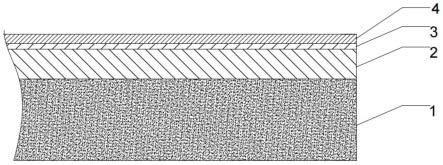
1.本发明涉及陶瓷技术领域,特别涉及一种仿真微水泥陶瓷砖及其制备方法。
背景技术:2.瓷砖的纹理是影响瓷砖视觉效果的重要因素,是重要的视觉设计元素。不同纹理的瓷砖给人以不同的视觉感受,如大理石纹、木纹、布纹、仿金属纹、仿水磨石纹、仿水泥等瓷砖,具有不同的质感,给到消费者不同的视觉感受。其中,仿水泥瓷砖因模拟微水泥的特质,具有哑光效果,质感细腻,备受消费者喜欢。然而,现有仿水泥瓷砖的质感相较于真实的微水泥,依然差异较大,存在质感不够细腻、仿真效果不够理想、发色不够纯正的缺陷。
3.可见,现有技术还有待改进和提高。
技术实现要素:4.鉴于上述现有技术的不足之处,本发明的目的在于提供一种仿真微水泥陶瓷砖及其制备方法,旨在解决现有技术中仿微水泥质感的陶瓷砖质感不够细腻、发色较差的缺陷。
5.为了达到上述目的,本发明采取了以下技术方案:
6.一种仿真微水泥陶瓷砖,其中,所述陶瓷砖由下至上依次包括坯体层、底釉层、纹理色彩层和面釉层;所述底釉层的化学成分按质量百分比计包括:sio
2 59~63%、al2o
3 17~20%、k2o 2~3%、na2o 3~4%、cao 3~5%、mgo 0~0.5%、zno 3~5%、bao 0.5~1%、zro
2 4~6%、灼减≤3%;所述面釉层的化学成分按质量百分比计包括:sio
2 48~50%、al2o
3 19~20%、k2o 0.5~1.5%、na2o 2~4%、cao 12~14%、mgo 2~3%、zno 4~6%、bao 4~6%、zro2≤0.1%、灼减≤4%。
7.所述仿真微水泥陶瓷砖中,所述底釉层由底釉层釉料制备得到,所述底釉层釉料按质量百分比计由92~96%的生料和4~8%的熔块组成。
8.所述仿真微水泥陶瓷砖中,所述熔块的化学成分按质量百分比计包括:sio
2 48~51%、al2o
3 7~12%、k2o 4~6%、na2o 1~3%、cao 7~12%、mgo 0.8~1.2%、zno 5~7%、bao 13~15%、b2o
3 2~3%、zro2≤0.3%、其它杂质及灼减≤1%。
9.所述仿真微水泥陶瓷砖中,所述生料包括钾长石、钠长石、煅烧高岭土、氧化铝粉末、霞石、硅灰石、气刀土、石英粉、氧化锌及硅酸锆。
10.所述仿真微水泥陶瓷砖中,所述生料中还包括球土。
11.所述仿真微水泥陶瓷砖中,所述底釉层釉料按质量百分比计包括:煅烧高岭土9~13%、气刀土4~6%、球土2~4%、钾长石16~20%、钠长石16~20%、霞石6~10%、硅灰石3~6%、石英粉12~15%、氧化铝1~3%、氧化锌2~4%、熔块4~8%、硅酸锆6~10%。
12.所述仿真微水泥陶瓷砖中,所述底釉层釉料按质量百分比计包括:煅烧高岭土12%、气刀土5%、球土3%、钾长石19%、钠长石17%、霞石7%、硅灰石5%、石英粉13%、氧化铝2%、氧化锌3%、熔块6%、硅酸锆8%。
13.一种如上所述的仿真微水泥陶瓷砖的制备方法,其中,所述制备方法包括步骤:
≤0.1%、灼减≤4%,所述面釉层具有哑光效果,可使砖面光泽度在3~8之间,质感细腻且光滑,具有微水泥的效果。同时,所述面釉层又具有较好的透光性,能使纹理色彩层较好呈现,并且,由于面釉层设于纹理色彩层上,一方面可保护纹理色彩层免受磨损,经久耐用,另一方面,所述面釉层可避免墨水在烧制的过程中受烧制环境的影响,提高墨水的发色能力,使墨水发色更纯正,特别是红色和黄色,弥补底釉层的不足,再一方面,所述面釉层与底釉层共同作用,使纹理色彩层呈现出质地细腻柔和、具有底蕴的微水泥效果。
33.上述仿真微水泥陶瓷砖中,所述底釉层由底釉层釉料制备得到,所述底釉层釉料按质量百分比计由92~96%的生料和4~8%的高温流动性好的熔块组成。
34.具体的,所述熔块的化学成分按质量百分比计包括:sio
2 48~51%、al2o
3 7~12%、k2o 4~6%、na2o 1~3%、cao 7~12%、mgo 0.8~1.2%、zno 5~7%、bao 13~15%、b2o
3 2~3%、zro2≤0.3%、其它杂质及灼减≤1%所述熔块通过1500℃的高温煅烧,再经水淬制备得到。所述熔块由于经过高温煅烧,成分稳定且气泡少,化学稳定性好,并且由于熔块中含有较多量的k2o、na2o、b2o3高温助熔剂,可以降低釉料的熔融温度和降低釉料高温熔体的高温粘度,提高釉料的高温流动性。由于底釉层釉料中的生料为柔光性釉料原料,未经过煅烧,因此在高温烧结时会有气体产生,容易形成缺陷。对此,本发明通过在生料中添加高温流动性好及高温粘度低的熔块,能在烧结时使气泡移动合并,形成大气泡,进而上升、爆破,因此可避免小气泡残留于釉料中形成缺陷,进而使底釉层表面更为平整细腻,具有更好的微水泥质感。
35.具体的,所述底釉层釉料中,所述生料为柔光性釉料原料,包括钾长石、钠长石、氧化铝粉末、煅烧高岭土、霞石、硅灰石、气刀土、石英粉、氧化锌及硅酸锆,所述生料与熔块通过烧制,可形成具有微水泥效果的釉面,质感细腻且柔和。
36.更具体的,所述生料中,所述钾长石、钠长石可引入助熔剂氧化钾和氧化钠,以及二氧化硅和氧化铝;所述煅烧高岭土可引入氧化铝和二氧化硅;所述霞石为含钠和钙的碳酸盐-铝硅酸盐,加入霞石可使釉面质感更加丰富、细腻柔和;所述硅灰石可作为助熔剂,提高底釉层的白度和强度,降低烧制温度,扩大烧成范围,减少釉面针孔,使釉面更加细腻,提高釉面的微水泥质感;所述氧化锌为强助熔剂,可拓宽底釉层烧成温度范围,有助于墨水发色,尤其是有利于红色发色,优选的,当氧化锌含量为2%~4%时,发色性能较好;所述气刀土可提高釉桨的悬浮性、分散性,由于钾长石、钠长石、煅烧高岭土、霞石、硅灰石、石英均为脊性料,使得釉桨的悬浮性差,容易出现沉淀现象,使得釉桨不均匀,影响底釉层质量,通过添加气刀土,可提高各成分在釉桨中的分散性、悬浮性及流动性,使浆料成分均匀稳定,进而提高产品质量;所述石英粉可引入二氧化硅,提高二氧化硅的含量;所述硅酸锆为乳浊剂,可提高底釉层的乳浊效果,增强底釉层遮盖坯体颜色的能力,使纹理色彩层的颜色受到的干扰少。
37.作为一种优选的实施方式,所述底釉层釉料中,所述钾长石的添加量为16%~20%、钠长石的添加量为16%~20%、氧化铝的添加量为1~3%、煅烧高岭土的添加量为9%~13%,能使底釉层的发色性能、熔融温度等物理化学性能达到最优。这是因为,虽然钾长石、钠长石及氧化铝粉末均能引入氧化铝,但是,由于钾长石和钠长石中含有氧化钾和氧化钠,而氧化钾和氧化钠为助熔剂,其在底釉层釉料中的含量不可太高,太高容易导致釉料熔融温度过低,使得面釉层釉料融入底釉层中,致使砖面过于平滑,形成反光发亮的现象,
进而无法得到微水泥的柔光效果。而直接添加氧化铝粉末,虽然能提高底釉层釉料中氧化铝的含量,但是氧化铝粉末会对纹理色彩层墨水的发色产生较大影响,特别是红色,会使得其发色不正。对此,本技术通过降低钾长石、钠长石及氧化铝粉末的含量,添加煅烧高岭土来提高生料中氧化铝的含量,具有发色性能好,熔融温度适中的特点。并且,由于煅烧高岭土为高温煅烧后的高岭土,与未煅烧高岭土相比,其结合水的含量减少,二氧化硅和三氧化铝含量均增大,能使活性点增加,同时,通过煅烧,使高岭土的结构发生变化,粒径较小且均匀,在釉桨中的分散性更好。因此,本发明通过调整钾长石、钠长石、煅烧高岭土及氧化铝粉末的配比,得到具有发色性能好,熔融温度较宽的底釉层釉料。
38.在另一种优选的实施方式中,所述底釉层釉料中还包括球土,所述球土同样可提高脊性料的分散性、悬浮性,使釉桨中各成分的分散更为均匀,性能更为稳定。
39.作为一种更优选的实施方式,所述仿真微水泥陶瓷砖中,所述底釉层釉料按质量百分比计包括煅烧高岭土9~13%、气刀土4~6%、球土2~4%、钾长石16~20%、钠长石16~20%、霞石6~10%、硅灰石3~6%、石英粉12~15%、氧化铝1~3%、氧化锌2~4%、熔块4~8%、硅酸锆6~10%,具有釉面质感细腻,感光柔和,发色纯正的特点。
40.作为一种优选的实施例,所述仿真微水泥陶瓷砖中,所述底釉层釉料按质量百分比计包括:煅烧高岭土12%、气刀土5%、球土3%、钾长石19%、钠长石17%、霞石7%、硅灰石5%、石英粉13%、氧化铝2%、氧化锌3%、熔块6%、硅酸锆8%。所述釉料制备得到的底釉层,质感更为细腻,微水泥的效果更为逼真。
41.上述仿真微水泥陶瓷砖,通过底釉层、面釉层共同作用,可使纹理色彩层的发色更为纯正,使砖面表观效果呈现出细腻柔和的质感,具有逼真的微水泥效果。
42.本技术还公开了如上所述的仿真微水泥陶瓷砖的制备方法,所述制备方法包括步骤:
43.步骤一:压制生坯并干燥,得坯体。具体的,所述生坯通过陶瓷压砖机压制而成,然后进入干燥窑中干燥,干燥温度为180~250℃,干燥时间为50~70min,干燥后的坯体水分为0.5~0.8%。
44.步骤二:采用钟罩淋釉在坯体上淋底釉层釉料,底釉层釉料的雷氏粘度为32~38s,淋釉量为400~530g/m2。通过采用钟罩淋釉,可使釉面更为平整细腻;通过设置特定的淋釉量,使底釉层的厚度能遮挡坯体颜色,同时具有较好的底蕴;通过调整底釉层釉料的雷氏粘度,使其流动性好,釉料均匀,并且不会出现沉淀现象。
45.步骤三:采用喷墨打印机在底釉层上喷墨打印纹理色彩层,颜色墨水的墨量为0.5~10ml/m2。所述颜色墨水的墨量会影响着色效果,不同的颜色采用不同的墨量,具体可根据实际需要调整,以便于发色纯正。
46.步骤四:在纹理色彩层表面喷施面釉层釉料,所述面釉层釉料的喷釉量为260~330g/m2。所述面釉层釉料的喷釉量小于底釉层釉料的淋釉量,并且采用喷釉设备喷制,可使面釉面薄且均匀,并且不会冲击纹理色彩层,使纹理色彩层的图案不会变形。
47.步骤五:将喷施面釉后的坯体送入窑炉烧制,烧成温度为1190~1230℃,烧成时间为50~80min。所述烧成温度和烧制时间是影响釉面表观效果的关键因素,本发明通过调整底釉层成分,具有较宽的烧成温度,在1190~1230℃,烧制50~80min,可得到发色纯正、表面平整、质感细腻柔和的仿微水泥陶瓷砖。
48.步骤六:对砖体进行磨边,得成品。
49.作为一种优选的实施方式,所述步骤四中,采用高压喷釉设备喷施面釉层釉料,所述高压喷釉设备的喷枪设有3~6个喷芯孔,所述喷芯孔的孔径为0.42~0.52mm,喷釉时,设置喷枪压力为4~8bar,具有釉浆颗粒小,釉料喷施均匀的效果。
50.进一步的,所述步骤四中,所述面釉层釉料的比重为1.35~1.50g/ml,通过调整面釉层釉料的比重,在喷枪的作用下,可形成更为细小的釉料颗粒,进而能更均匀的喷施于纹理色彩层中,使瓷砖表面更为平整,对纹理色彩层的影响越小。
51.上述仿真微水泥陶瓷砖的制备方法,采用钟罩淋釉的方式淋底釉层釉料,能使釉面的平整度更高,烧制后质感更为细腻;采用喷枪喷施面釉,能使面釉更为均匀,并且不会影响纹理色彩层效果;通过采用特定的烧制温度,可使纹理色彩层发色纯正,使釉面质感细腻柔和,具有微水泥的效果。
52.为进一步的阐述本发明提供的一种仿真微水泥陶瓷砖及其制备方法,提供如下实施例。
53.实施例1
54.一种仿真微水泥陶瓷砖,所述陶瓷砖由下至上依次包括坯体层、底釉层、纹理色彩层和面釉层。
55.所述底釉层的化学成分按质量百分比计包括:sio
2 61%、al2o
3 18%、k2o 2.5%、na2o 3.5%、cao 4%、mgo 0.2%、zno 4%、bao 0.8%、zro
2 5%、灼减1%。
56.所述面釉层的化学成分按质量百分比计包括:sio
2 49%、al2o
3 19%、k2o 1%、na2o 3%、cao 13%、mgo 2.5%、zno 5%、bao 5%、zro
2 0.1%、灼减2.4%。
57.所述面釉层由底釉层釉料制备得到,所述底釉层釉料按质量百分比计包括煅烧高岭土12%、气刀土5%、球土3%、钾长石19%、钠长石17%、霞石7%、硅灰石5%、石英粉13%、氧化铝2%、氧化锌3%、熔块6%、硅酸锆8%。
58.所述熔块的化学成分按质量百分比计包括:sio
2 50.34%、al2o
3 10.16%、k2o 4.52%、na2o 1.26%、cao 9.86%、mgo 0.93%、zno 5.56%、bao 14.29%、b2o
3 2.44%、zro
2 0.23%、其它杂质及灼减0.41%。
59.所述仿真微水泥陶瓷砖由以下步骤制备得到:
60.步骤一:压制生坯并将生坯在温度为220℃干燥炉中干燥,60min,干燥后的坯体水分为0.6%。
61.步骤二:采用钟罩淋釉的方式在坯体上淋底釉层釉料,底釉层釉料的雷氏粘度为35s,淋釉量为500g/m2。
62.步骤三:采用喷墨打印机在底釉层上喷墨打印纹理色彩层,颜色墨水的墨量为6ml/m2。
63.步骤四:通过喷釉设备在纹理色彩层表面喷施面釉层釉料,所述面釉层釉料过325目标准筛余为0.8g/100ml,面釉层釉料的比重为1.40g/ml,喷枪压力为6bar,喷釉量为300g/m2。
64.步骤五:将喷施面釉后的坯体送入窑炉烧制,烧成温度为1200℃,烧成时间为56min。
65.步骤六:对砖体进行磨边,得成品。
66.实施例2
67.一种仿真微水泥陶瓷砖,所述陶瓷砖由下至上依次包括坯体层、底釉层、纹理色彩层和面釉层。
68.所述底釉层的化学成分按质量百分比计包括:sio
2 59%、al2o
3 20%、k2o 3%、na2o 3%、cao 3%、mgo 0.5%、zno 5%、bao 1%、zro
2 4%、灼减1.5%。
69.所述面釉层的化学成分按质量百分比计包括:sio
2 48%、al2o
3 20%、k2o 0.5%、na2o 4%、cao 12%、mgo 3%、zno 4%、bao 6%、zro2≤0.1%、灼减≤2.4%。
70.所述面釉层由底釉层釉料制备得到,所述底釉层釉料按质量百分比计包括煅烧高岭土13%、气刀土6%、球土2%、钾长石20%、钠长石16%、霞石10%、硅灰石3%、石英粉15%、氧化铝1%、氧化锌4%、熔块4%、硅酸锆6%。
71.所述熔块的化学成分按质量百分比计包括:sio
2 48%、al2o
3 12%、k2o 4%、na2o 1%、cao 12%、mgo 1.2%、zno 5%、bao 13%、b2o
3 3%、zro
2 0.3%、其它杂质及灼减0.5%。
72.所述仿真微水泥陶瓷砖由以下步骤制备得到:
73.步骤一:压制生坯并将生坯在温度为180℃干燥炉中干燥,70min,干燥后的坯体水分为0.5%。
74.步骤二:采用钟罩淋釉的方式在坯体上淋底釉层釉料,底釉层釉料的雷氏粘度为32s,淋釉量为530g/m2。
75.步骤三:采用喷墨打印机在底釉层上喷墨打印纹理色彩层,颜色墨水的墨量为0.5ml/m2。
76.步骤四:通过喷釉设备在纹理色彩层表面喷施面釉层釉料,所述面釉层釉料的喷釉量为330g/m2,所述面釉层釉料的比重为1.35g/ml,喷枪压力为4bar。
77.步骤五:将喷施面釉后的坯体送入窑炉烧制,烧成温度为1190℃,烧成时间为80min。
78.步骤六:对砖体进行磨边,得成品。
79.实施例3
80.一种仿真微水泥陶瓷砖,所述陶瓷砖由下至上依次包括坯体层、底釉层、纹理色彩层和面釉层。
81.所述底釉层的化学成分按质量百分比计包括:sio
2 63%、al2o
3 17%、k2o 2%、na2o 4%、cao 3%、zno 3%、bao 0.5%、zro
2 6%、灼减1.5%。
82.所述面釉层的化学成分按质量百分比计包括:sio
2 50%、al2o
3 19%、k2o 1.5%、na2o 2%、cao 14%、mgo 2%、zno 6%、bao 4%、zro
2 0.05%、灼减1.45%。
83.所述面釉层由底釉层釉料制备得到,所述底釉层釉料按质量百分比计包括煅烧高岭土9%、气刀土4%、球土4%、钾长石16%、钠长石20%、霞石6%、硅灰石6%、石英粉12%、氧化铝3%、氧化锌2%、熔块8%、硅酸锆10%。
84.所述熔块的化学成分按质量百分比计包括:sio
2 51%、al2o
3 7%、k2o 6%、na2o 3%、cao 7%、mgo 0.8%、zno 7%、bao 15%、b2o
3 2%、zro
2 0.2%、其它杂质及灼减1%。
85.所述仿真微水泥陶瓷砖由以下步骤制备得到:
86.步骤一:压制生坯并将生坯在温度为250℃干燥炉中干燥,50min,干燥后的坯体水
分为0.8%。
87.步骤二:采用钟罩淋釉的方式在坯体上淋底釉层釉料,底釉层釉料的雷氏粘度为38s,淋釉量为400g/m2。
88.步骤三:采用喷墨打印机在底釉层上喷墨打印纹理色彩层,颜色墨水的墨量为10ml/m2。
89.步骤四:通过喷釉设备在纹理色彩层表面喷施面釉层釉料,所述面釉层釉料的喷釉量为260g/m2,所述面釉层釉料的比重为1.50g/ml,喷枪压力为8bar。
90.步骤五:将喷施面釉后的坯体送入窑炉烧制,烧成温度为1210℃,烧成时间为50min。
91.步骤六:对砖体进行磨边,得成品。
92.对比例1
93.一种仿真微水泥陶瓷砖,所述陶瓷砖的层状结构及制备方法与实施例1相同,其面釉层、纹理色彩层及坯体层的成分组成均与实施例1相同,区别在于,所述底釉层与实施例1不同。具体为,所述底釉层按质量百分比计由以下成分制备得到:高岭土12%、气刀土5%、球土3%、钾长石19%、钠长石17%、霞石7%、硅灰石5%、石英粉13%、氧化铝2%、氧化锌3%、熔块6%、硅酸锆8%。
94.对比例2
95.一种仿真微水泥陶瓷砖,所述陶瓷砖的层状结构及制备方法与实施例1相同,其面釉层、纹理色彩层及坯体层的成分组成均与实施例1相同,区别在于,所述底釉层与实施例1不同。具体为,所述底釉层按质量百分比计由以下成分制备得到:煅烧高岭土12%、气刀土6%、钾长石21%、钠长石18.5%、霞石8.5%、硅灰石5%、石英粉13%、氧化铝5%、氧化锌3%、硅酸锆8%。
96.对比例3
97.一种仿真微水泥陶瓷砖,所述陶瓷砖的层状结构及制备方法与实施例1相同,其底釉层、纹理色彩层及坯体层的成分组成均与实施例1相同,区别在于,所述面釉层与实施例1不同。具体为,所述面釉层的化学成分按质量百分比计包括:sio
2 53%、al2o
3 25%、k2o 2%、na2o 3%、cao 10%、mgo 1%、zno 2%、bao 2%、zro
2 0.5%、灼减1.5%。
98.对比例4
99.一种仿真微水泥陶瓷砖,所述陶瓷砖的层状结构及各层状结构的成分配比与实施例1相同,其制备方法也与实施例1基本相同,区别在于,所述步骤四中,采用钟罩淋釉的方式淋面釉,并且淋釉量与实施例1的相同。
100.性能比对
101.对实施例1-3和对比例1-4的釉桨性能、砖面光泽度、砖面质感及发色情况进行比对,具体情况如表1所示。
102.表1.性能比对表
[0103][0104]
由表1可知,实施例1-3因采用特殊成分配比的底釉层和面釉层,能使釉桨性能较优,分散性好,不易沉淀,淋釉后釉面平整均匀,烧制后砖面光滑细腻,呈现哑光效果,并且质感柔和,发色纯正,具有微水泥的效果。
[0105]
而对比例1,由于其底釉层采用高岭土而不是煅烧高岭土,易产生气孔,使得手感不够细腻,同时氧化铝含量低,发色深。而对比例2中,由于底釉层釉料中未添加熔块,使得生料在烧成时产生气孔,并且熔融温度高,面釉层釉料流至底釉层,同时,由于未添加球土,其分散性不足,导致质感粗糙,并且由于氧化铝含量高,使得发色浅。而对比例3中,虽然底釉层与实施例1相同,但是由于其面釉层的化学成分不同,使得表面亮光,无哑光效果,不具微水泥的质感。对比例4中,由于在步骤四中采用钟罩淋釉,因此在淋釉时会对冲击图案层的纹理,出现颜料分布不均的,图案变形的现象。
[0106]
综上所述,本发明所述仿真微水泥陶瓷砖,通过采用特殊化学成分的底釉层和面釉层,以及特殊的制备工艺,能使纹理色彩层发色纯正,具有哑光效果,手感光滑细腻,质感柔和,具有微水泥的效果。
[0107]
可以理解的是,对本领域普通技术人员来说,可以根据本发明的技术方案及其发明构思加以等同替换或改变,而所有这些改变或替换都应属于本发明所附的权利要求的保护范围。