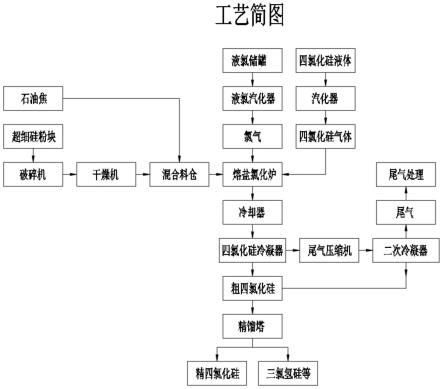
1.本发明涉及一种生产四氯化硅技术领域,具体涉及一种综合利用超细硅粉废弃物生产四氯化硅的工艺。
背景技术:2.制作太阳能电池过程中,需要用金刚石线将多晶硅棒切割成薄片,切割过程中,有近一半的多晶硅以“锯末”的形式形成超细硅粉废料,细度达8000目左右。在多晶硅生产过程中的冷氢化工序中,也能产生大量超细硅粉。这两种超细硅粉都含有大量的单质硅。
3.虽然超细硅粉和氯气能发生反应生成四氯化硅,但由以下原因导致硅粉难以应用。
4.超细硅粉粒度太小,颗粒之间的静电力较大,导致硅粉流动性极差,无法使用气力输送设备进行输送,也无法与氯气形成流化床或固定床反应,又极易被反应气流带走。
5.超细硅粉表面有氧化层,导致硅粉的二氧化硅含量随储存时间持续增长,使其越来越难与氯气反应。
6.超细硅粉真密度为2330kg/m3,堆积密度400~700kg/m3,夹杂大量空气,在高温下反应时,容易产生副反应:si+o2=sio2和3si+2n2=si3n4,sio2、si3n4是高熔点的固体,且不能直接与氯气反应,导致设备堵塞、反应不能持续进行、氯气不能充分反应等问题。
7.目前,这种超细硅粉主要有以下用途:
8.替代硅铁作为还原剂用作炼钢脱氧剂。
9.用作铝合金添加剂,用于生产硬铝合金。
10.上述两种用途虽然使硅粉获得了利用,但产品附加值低,且因硅粉中含有二氧化硅导致应用效果变差。
11.用于冶炼金属硅,获得的金属硅性能与工业硅类似,冶炼过程中能耗低于常规方法。但存在诸多问题,一是冶炼过程中,为了除去硅粉中含有的二氧化硅需要加入石灰石作为造渣剂,最终生成大量硅酸钙废弃物,污染环境;二是单质硅回收率约为70~95%,浪费了大量宝贵的单质硅。三是冶炼的过程需要在高达1300~1800℃的反应炉内用电加热进行,能耗较大。
12.现有技术中存在下述缺点:
13.1.超细硅粉颗粒极细是它的一个缺点,导致反应不完全、设备堵塞等问题;
14.2.二氧化硅不能直接与氯气反应导致反应不完全、设备堵塞的问题;
15.3.现有工艺需保持硅粉和氯气的流量稳定,流量的波动将大大降低原料利用率。
技术实现要素:16.本发明提供了一种综合利用超细硅粉废弃物生产四氯化硅的工艺,目的是解决现有技术中氯化工艺中的氯气和硅粉都不能充分反应、氯化炉及后续设备容易堵塞的问题。
17.为解决上述技术问题,本发明所采用的技术方案是:
18.一种综合利用超细硅粉废弃物生产四氯化硅的工艺,包括如下步骤:
19.s1.破碎:将结块的超细硅粉破碎成粉末;
20.s2.烘干:采用干燥机在真空下加热获得干燥的超细硅粉;
21.s3.配料:向料仓内加入石油焦粉,加入量为超细硅粉质量的1%-12%,启动料仓的搅拌装置,使石油焦粉与超细硅粉混合均匀;
22.s4.氯气预处理:液氯经汽化器蒸发后进入缓冲罐进行稳压;
23.s5.氯化:氯化反应在氯化炉内进行,氯化炉内装有熔融的氯化物混合盐,将硅粉与石油焦粉的混合物从氯化炉侧面的加料口加入,使之悬浮在熔融的混合盐内,氯气从炉底部进口通入氯化炉内发生放热的氯化反应;
24.s6.降温:氯化反应产生的高温产物气体进入换热器,与导热油换热后降温至100~350℃;
25.s7.冷凝:将除尘后的工艺气体通入换热器冷却,使气体中的四氯化硅冷凝成液体,剩余气体中的氯硅烷含量降低;
26.s8.尾气压缩:尾气进入压缩机压缩,为尾气利用、处理和回收氯硅烷提供条件;
27.s9.尾气二次冷凝:压缩后的尾气再次冷凝回收氯硅烷;
28.s10.尾气处理:当尾气中氯气含量低于氯化反应所需时,将尾气通入吸收塔进行环保处理。
29.进一步限定,在料仓内加入石油焦粉的量为超细硅粉质量的2~7%。
30.进一步限定,硅粉及石油焦粉的混合物与氯气物质的质量分数配比为:硅粉及石油焦粉的混合物:氯气=1:4.5-5.1。
31.进一步限定,氯气通入缓冲罐稳压后的表压为30~600kpa。
32.进一步限定,氯气从炉底部进口通入氯化炉内发生放热的氯化反应,反应温度为200-1500℃。
33.进一步限定,尾气(一氧化碳、二氧化碳、少量四氯化硅与过量氯气的混合气体)进入压缩机进行压缩,使尾气的表压升高至10-300kpa。
34.进一步限定,混合熔盐的主要成分是氯化钠和氯化钾,氯化钾除作为反应介质外,还起到促进二氧化硅与石油焦、氯气反应的作用,同时具有稳定氯化铁,防止氯化铁挥发的作用,氯化钠除作为反应介质外,也和氯化钾一样能起到稳定氯化铁、防止氯化铁挥发的作用。
35.进一步限定,氯化钾与氯化钠物质的量配比为:氯化钾:氯化钠=1:1。
36.进一步限定,按质量分数计,混合熔盐中还添加有氯化铁0.1~15%,氯化铜0.1~10%,氯化铁及氯化铜用于促进硅的氯化和熔盐对氯气的溶解吸收。
37.进一步限定,氯气从炉底部进口通入氯化炉内发生放热的氯化反应时的表压为-20~120kpa。
38.与现有技术相比,本发明具有以下有益效果:
39.本发明在实际的使用过程中,先将硅粉进行破碎处理,在晶体硅切割过程中,硅粉是以滤饼的形式产生的,经自然干燥后,滤饼是块状的,有一定的含水率,若不进行破碎,大块的硅粉难以充分干燥,且其在熔盐中无法均匀分散,对后续的反应不利,所以需要将结块的超细硅粉破碎成粉末;破碎后的硅粉以单个或数十个颗粒聚集体的形式进行烘干,获得
干燥的超细硅粉;再将石油焦粉与干燥的超细硅粉进行充分搅拌,与此同时对氯气进行预处理,液化氯气经过气化、稳压后通入氯化炉中,并将硅粉通入到氯化炉内,氯化反应在氯化炉内进行,氯化炉内装有熔融的氯化物混合盐,将硅粉与石油焦粉的混合物从氯化炉侧面的加料口加入,使之悬浮在熔融的混合盐内,氯气从炉底部进口通入氯化炉内发生放热的氯化反应生产四氯化硅、一氧化碳、二氧化碳及氯气的混合气体;四氯化硅、氯气的混合气体进入到换热器中进行降温,降温后进行第一次冷凝,使混合气体中的四氯化硅冷凝成液体,液态四氯化硅进行收集,未完全冷凝的四氯化硅气体及氯气进入到压缩机中进行压缩,提升压力,为尾气利用、处理和回收氯硅烷提供条件;随后对压缩后的四氯化硅气体及氯气进行二次冷凝,最后将液态的四氯化硅进行收集,收集完毕后,剩余的氯气进行环保处理,液态的四氯化硅经过精馏后将纯四氯化硅液体进行收集,这样做的好处是有利于超细硅粉颗粒均匀、稳定地悬浮在熔盐中,添加了石油焦粉能够让硅粉表面的二氧化硅参与反应,转化为四氯化硅,并且向氯化炉添加硅粉和石油焦的过程中不需要用稳定的添加速度加料,甚至可以间歇式加料工艺操作较为简单。
附图说明
40.为了更清楚地说明本发明实施方式的技术方案,下面将对实施方式中所需要使用的附图作简单地介绍,应当理解,以下附图仅示出了本发明的某些实施例,因此不应被看作是对范围的限定,对于本领域普通技术人员来讲,在不付出创造性劳动的前提下,还可以根据这些附图获得其他相关的附图。
41.图1为本发明的工艺流程图。
42.图2为本发明的氯化炉的结构示意图。
43.图中,101-外壳,102-电极,103-加料口,104-出口,105-排盐口,106-料斗,107-通氯口。
具体实施方式
44.下面结合实施例对本发明作进一步的描述,所描述的实施例仅仅是本发明一部分实施例,并不是全部的实施例。基于本发明中的实施例,本领域的普通技术人员在没有做出创造性劳动前提下所获得的其他所用实施例,都属于本发明的保护范围。
45.实施例一
46.请参阅图1所示,本实施例公开了一种综合利用超细硅粉废弃物生产四氯化硅的工艺,包括如下步骤:
47.s1.破碎:将结块的超细硅粉破碎成粉末;
48.s2.烘干:采用干燥机在真空下加热获得干燥的超细硅粉;
49.s3.配料:向料仓内加入石油焦粉,加入量为超细硅粉质量的1%-12%,启动料仓的搅拌装置,使石油焦粉与超细硅粉混合均匀;
50.s4.氯气预处理:液氯经汽化器蒸发后进入缓冲罐进行稳压;
51.s5.氯化:氯化反应在氯化炉内进行,氯化炉内装有熔融的氯化物混合盐,将硅粉与石油焦粉的混合物从氯化炉侧面的加料口加入,使之悬浮在熔融的混合盐内,氯气从炉底部进口通入氯化炉内发生放热的氯化反应;
52.s6.降温:氯化反应产生的高温产物气体进入换热器,与导热油换热后降温至100~350℃;
53.s7.冷凝:将除尘后的工艺气体通入换热器冷却,使气体中的四氯化硅冷凝成液体,剩余气体中的氯硅烷含量降低;
54.s8.尾气压缩:尾气进入压缩机压缩,为尾气利用、处理和回收氯硅烷提供条件;
55.s9.尾气二次冷凝:压缩后的尾气再次冷凝回收氯硅烷;
56.s10.尾气处理:当尾气中氯气含量低于氯化反应所需时,将尾气通入吸收塔进行环保处理;
57.本发明在实际的使用过程中,先将硅粉进行破碎处理,在晶体硅切割过程中,硅粉是以滤饼的形式产生的,经自然干燥后,滤饼是块状的,有一定的含水率,若不进行破碎,大块的硅粉难以充分干燥,且其在熔盐中无法均匀分散,对后续的反应不利,所以需要将结块的超细硅粉破碎成粉末;破碎后的硅粉以单个或数十个颗粒聚集体的形式进行烘干,获得干燥的超细硅粉;再将石油焦粉与干燥的超细硅粉进行充分搅拌,与此同时对氯气进行预处理,液化氯气经过气化、稳压后通入氯化炉中,并将硅粉通入到氯化炉内,氯化反应在氯化炉内进行,氯化炉内装有熔融的氯化物混合盐,将硅粉与石油焦粉的混合物从氯化炉侧面的加料口加入,使之悬浮在熔融的混合盐内,氯气从炉底部进口通入氯化炉内发生放热的氯化反应生产四氯化硅、一氧化碳、二氧化碳及氯气的混合气体;四氯化硅、氯气的混合气体进入到换热器中进行降温,降温后进行第一次冷凝,使混合气体中的四氯化硅冷凝成液体,液态四氯化硅进行收集,未完全冷凝的四氯化硅气体及氯气进入到压缩机中进行压缩,提升压力,为尾气利用、处理和回收氯硅烷提供条件;随后对压缩后的四氯化硅气体及氯气进行二次冷凝,最后将液态的四氯化硅进行收集,收集完毕后,剩余的氯气进行环保处理,液态的四氯化硅经过精馏后将纯四氯化硅液体进行收集,这样做的好处是有利于超细硅粉颗粒均匀、稳定地悬浮在熔盐中,添加了石油焦粉能够让硅粉表面的二氧化硅参与反应,转化为四氯化硅,并且向氯化炉添加硅粉和石油焦的过程中不需要用稳定的添加速度加料,甚至可以间歇式加料工艺操作较为简单。
58.进一步限定,加入石油焦粉的量为超细硅粉的2~7%,在实际的使用中,硅粉在储存时会接触氧气生成二氧化硅,故硅粉中会混有二氧化硅,二氧化硅不与氯气直接反应,而在石油焦粉(主要成分是碳)作用下,二氧化硅能够发生氯化反应,具体化学反应方程式为:sio2+2c+2cl2=sicl4+2co和sio2+c+2cl2=sicl4+co2,这样设置的目的是使得硅粉中的二氧化硅也参与反应,防止其在熔盐中积累下来影响反应的持续进行。
59.进一步限定,硅粉及石油焦粉的混合物与氯气的质量分数配比为:硅粉及石油焦粉的混合物:氯气=1:4.5-5.1,氯化在高温下进行,发生的化学反应主要有:
60.si+2cl2=sicl4;
61.sio2+2c+2cl2=sicl4+2co;
62.sio2+c+2cl2=sic4+co2;
63.进一步限定,氯气通入缓冲罐稳压后的表压为30~600kpa,在实际的使用过程中,氯气稳压后的表压具体为200~300kpa。
64.进一步限定,氯气从炉底部进口通入氯化炉内发生放热的氯化反应,反应温度为200-1500℃,在实际应用中,反应温度具体为950~1150℃,工作人员可以通过控制进入氯
化炉的四氯化硅气体的流量来控制反应温度,在实际的使用过程中,反应温度过高时,工作人员可以通过提高通入的四氯化硅气体流量使反应温度降低,反之,也可以通过降低四氯化硅气流量使得反应温度升高,这样设置的好处是可以通过控制进入氯化炉的四氯化硅气体的流量来控制反应温度。
65.进一步限定,使尾气(一氧化碳、二氧化碳、少量四氯化硅与过量氯气的混合气体)进行压缩,使尾气的表压升高至10-300kpa。
66.进一步限定,混合熔盐的主要成分是氯化钠和氯化钾,氯化钾除作为反应介质外,还起到促进二氧化硅与石油焦、氯气反应的作用,同时具有稳定氯化铁,防止氯化铁挥发的作用,氯化钠除作为反应介质外,也和氯化钾一样能起到稳定氯化铁、防止氯化铁挥发的作用。
67.进一步限定,氯化钾与氯化钠物质的量配比为:氯化钾:氯化钠=1:1。
68.进一步限定,按质量分数计,混合熔盐中还添加有氯化铁0.1~15%,氯化铜0.1~10%,氯化铁及氯化铜用于促进硅的氯化和熔盐对氯气的溶解吸收;
69.混合熔盐的主要成分是氯化钠和氯化钾,按物质的量份数计,氯化钾:氯化钠=1:1;按质量分数计,混合熔盐中还添加有氯化铁0.1~15%,氯化铜0.1~10%,两种盐促进硅的氯化和熔盐对氯气的溶解吸收,发生如下两组循环反应:
70.(1)si+4fecl3=sicl4+4fecl2;
71.2fecl2+cl2=2fecl3;
72.(2)si+4cucl2=sicl4+4cucl;
73.2cucl+cl2=2cucl2;
74.混合盐的主要成分氯化钾除作为反应介质外,还起到促进二氧化硅与石油焦、氯气反应的作用,同时具有稳定氯化铁,防止氯化铁挥发的作用:
75.其反应方程式为:kcl+fecl3=kfecl4;
76.主要成分氯化钠除作为反应介质外,也和氯化钾一样能起到稳定氯化铁、防止氯化铁挥发的作用:
77.其反应方程式为:nacl+fecl3=nafecl4;
78.并且熔盐温度会随着氯化反应的进行而升高,为使熔盐维持在合适的温度,向熔盐底部通入气化的四氯化硅。
79.进一步限定,氯气从炉底部进口通入氯化炉内发生放热的氯化反应时的表压为-20~120kpa。
80.本发明还公开了一种综合利用超细硅粉废弃物生产四氯化硅的设备,包括包括破碎机、干燥机、料仓、螺旋送料器、精馏塔、汽化器、缓冲罐、氯化炉、第一冷凝机、压缩机、第二冷凝机、尾气缓冲罐及粗四氯化硅罐;
81.破碎机与干燥机连接,干燥机与料仓连接,料仓内部设置有搅拌装置,料仓上的入料口连接有破碎机,破碎机能够将结块的超细硅粉破碎成粉末后并使得经过破碎后的硅粉进入到料仓内部,螺旋送料器的一端与料仓下端的出料口连接,另一端与氯化炉连接;第一汽化器与第一缓冲罐连接,第二汽化器与第二缓冲罐连接,第一缓冲罐及第二缓冲罐均与氯化炉的进料端连接,氯化炉的出料端与换热器连接,换热器与旋风除尘器连接,旋风除尘器与文丘里洗涤器连接,文丘里洗涤器与第一冷凝机连接,第一冷凝器上的出料端分别与
粗四氯化硅罐及压缩机连接,压缩机的出气端与第二冷凝机连接,第二冷凝器的出料端分别与粗四氯化硅罐及尾气缓冲罐连接,粗四氯化硅罐与精馏塔连接,尾气缓冲罐与氯化炉连接。
82.在实际的使用过程中,工作人员先将硅粉送至破碎机中进行破碎处理,在晶体硅切割过程中,硅粉是以滤饼的形式产生的,经自然干燥后,滤饼是块状的,有一定的含水率,若不进行破碎,大块的硅粉难以充分干燥,且其在熔盐中无法均匀分散,对后续的反应不利,所以需要将结块的超细硅粉破碎成粉末;破碎成粉末形成单个或数十个颗粒聚集体的形式进入到桨叶干燥及中进行真空加热,以获得干燥的超细硅粉;再向料仓中加入干燥的超细硅粉及石油焦粉,启动搅拌装置使得石油焦粉与超细硅粉混合均匀,与此同时对液化氯气进行预处理,形成气态的氯气,在将氯气通入氯化炉中之前,需要在氯化炉中加入固态混合盐,并对固态的混合盐进行融化,呈液态,之后再将氯气通入到氯化炉中,与此同时使得硅粉从螺旋送料器中进入到氯化炉内,将硅粉与石油焦粉的混合物从氯化炉侧面的加料口加入,使之悬浮在熔融的混合盐内,氯气从炉底部进口通入氯化炉内发生放热的氯化反应生产四氯化硅、一氧化碳、二氧化碳及氯气的混合气体;四氯化硅、氯气的混合气体进入通过换热器进行冷却,完成冷却后的四氯化硅气体进入到第一冷凝器中进行冷却,使混合气体中的四氯化硅冷凝成液体,形成四氯化硅液体进入到粗四氯化硅罐中进行储存,最后通过精馏塔进行精馏,将纯四氯化硅液体分离开后进行收集,而在第一冷凝器中的尾气(未变成液态的四氯化硅气体及氯气的混合气体)再次进入压缩机中进行压缩,压缩完成后经过第二冷凝器进行二次冷却,液化的四氯化硅进入到粗四氯化硅罐中储存,残留的尾气进入到尾气缓冲罐中进行稳压后重新返回氯化炉实现尾气的再利用;生产中添加了石油焦粉能够让硅粉表面的二氧化硅参与反应,转化为四氯化硅,并且向氯化炉添加硅粉和石油焦的过程中不需要用稳定的添加速度加料,甚至可以间歇式加料工艺操作较为简单。
83.进一步优化,破碎机为颚式破碎机、反击式破碎机、旋回破碎机、圆锥式破碎机、辊式破碎机、锤式破碎机或立轴冲击式破碎机,在本实施例中,破碎机具体为锤式破碎机。
84.实施例二
85.请参阅图2所示,本实施例是在实施例一的基础上进一步优化,在本实施例中,氯化炉包括外壳101、电极102、加料口103、通氯口107、出口104、排盐口105及料斗108,电极102设置在外壳101内,电极102用于对固态的混合盐放电后发出热量使得熔盐混合物液化,加料口103设置在外壳101中间位置,加料口103与所述料仓连接,出口104设置在外壳101的上方,出口104与第一冷凝器连接,通氯口107设置在外壳101的底部,通氯口107与缓冲罐连接,排盐口105设置在外壳101上并位于加料口103与通氯口107之间,料斗108设置在排盐口105的下方,料斗108用于承装排出的熔盐混合物;
86.在实际的使用过程中,氯化炉采用金属外壳内衬耐火砖结构,二者之间加蒽油密封剂,保护钢壳不接触内部介质,防止腐蚀,内部耐火材料衬里能够耐受高温和氯气侵蚀,氯化炉底部的石墨电极102用于在设备启动阶段加热混合盐至熔融状态。
87.尽管已描述了本发明的优选实施例,但本领域内的技术人员一旦得知了基本创造性概念,则可对这些实施例作出另外的变更和修改。所以,所附权利要求意欲解释为包括优选实施例以及落入本发明范围的所有变更和修改。以上所述仅为本发明的较佳实施例而已,并不用以限制本发明,应当指出的是,凡在本发明的精神和原则之内所作的任何修改、
等同替换和改进等,均应包含在本发明的保护范围之内。