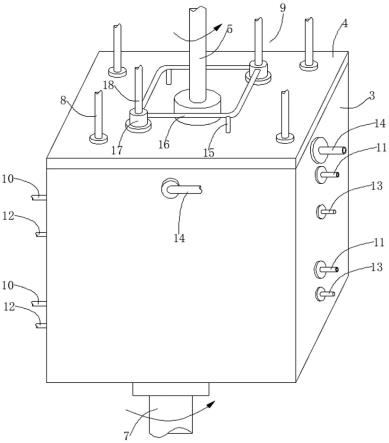
1.本发明涉及硅片拉晶生产技术领域,具体涉及能够有效降低硅片中碳杂质含量的加热装置及方法。
背景技术:2.硅片,是制作集成电路的重要材料,通过对硅片进行光刻、离子注入等手段,可以制成各种半导体器件,用硅片制成的芯片有着惊人的运算能力,科学技术的发展不断推动着半导体的发展,随着自动化和计算机等技术发展,使硅片(集成电路)这种高技术产品的造价已降到十分低廉的程度,这使得硅片已广泛应用于航空航天、工业、农业和国防,甚至悄悄进入每一个家庭,一种新的生产生活方式"和家庭办公室正在产生,将来,坐在家里操作机器、指挥生产、管理公司和工厂,将再不久的将来正对推进实现。
3.硅片拉晶生产过程中,由于生产设备需要进行高温-低温-高温三步实施内吸杂工艺,使得硅材料晶体的内部或背面产生缺陷,可以使吸引材料表面的杂质在缺陷处沉淀,后序通过切除晶锭缺陷处沉淀杂质即可,从而在晶体表面得到无杂质、无缺陷得洁净区,生产设备的温控范围可以达到1350℃以上,而生产设备中保温坩埚、石墨加热件以及保温盖等容易挥发碳材料渗入硅材料的溶解液中,而碳材料结构件表面会通过与炉内高温环境中的残余氧、氧化硅甚至与石英接触反应释放一氧化碳气体,一氧化碳进而与硅熔体反应释放碳,从而造成硅熔体的碳污染,使铸造硅片材料中碳含量增高。
4.现有技术中,如图10和11所示,硅熔体是置于石英坩埚1中生产,石英坩埚1外部包裹整体板件2a,整体板件2a为石墨材料,通过整体板件2a对石英坩埚进行加热生产使用,但在实际生产过程中存在以下缺陷:一是采用整体板件2a对石英坩埚1产生的加热区范围较广,造成加热资源投入较多,且通过保护气短管8a向石英坩埚1的硅熔体液面喷入氩气或氮气保护气体时,容易与高温硅熔体液面发生温度梯度变化,引起硅熔体液面涡流翻滚,容易引起硅熔体液面晶转生长的晶片厚度不均匀或者出现枝晶的情况;二是采用整体板件2a使得石英坩埚1在垂直度上温度均匀一致,热对流减少,降低了石英坩埚1底部熔硅上升速率;三是石英坩埚1外部设置有保温坩埚3,顶部设置有保温盖4,保温坩埚3和保温盖4均设计为中空结构,均分别便于通过冷却进风管10和冷却出风管11向其中空结构腔内循环输送冷却风,保证石英坩埚1内晶转成型的硅锭进行冷却退火使用,同时可以对保温坩埚3和保温盖4起到隔热作用,但向整体板件2a冷却效率低下,且容易造成冷却温度损失至外界环境中,造成冷却资源的浪费;四是保温坩埚3正对晶锭芯棒6的四周侧面上设置有侧向排气管14,将石英坩埚1内部上升的杂质往外排除,但是由于石英坩埚1在熔硅阶段是处于闭合状态,侧向排气管14无法更好的排出石英坩埚1内上升的碳杂质,上升的碳杂质位于晶转硅锭上部时,影响晶转硅锭的质量。
技术实现要素:5.本发明的目的在于提供能够有效降低硅片中碳杂质含量的加热装置及方法,用于
解决石英坩埚加热及冷却效果的问题,以及用于降低石英坩埚生产过程中较多上升的碳杂质影响晶转硅锭的问题。
6.本发明的目的可以通过以下技术方案实现:能够有效降低硅片中碳杂质含量的加热装置,包括石英坩埚,所述石英坩埚的外壁上紧贴设有可调节加热组件,所述可调节加热组件包括有上加热件和下加热件,上加热件套设在石英坩埚的顶部,下加热件套设在石英坩埚的底部,所述上加热件和下加热件的两侧分别连接有输入电极杆和输出电极杆,所述上加热件和下加热件内均设置有封闭的冷却腔,冷却腔的两侧分别连接有冷却进风管和冷却出风管,所述输入电极杆、输出电极杆、冷却进风管和冷却出风管均分别贯穿保温坩埚伸出,所述保温坩埚的顶口端密封连接保温盖,所述保温盖的四角位置处分别插设连接保护气长管,保护气长管伸入至石英坩埚的熔硅液中,且所述保护气长管的伸入管段上均布开设有多个射孔,所述保温盖上设置有排气管组件。
7.作为本发明进一步的方案:所述上加热件和下加热件均采用石墨材料制得,且上加热件和下加热件之间通过多个隔热柱连接。
8.作为本发明进一步的方案:所述上加热件上设置有若干间隔设置的上加热片,下加热片上设置有若干间隔设置的下加热片。
9.作为本发明进一步的方案:所述排气管组件包括有位于晶转轴四周设置的竖向排气管,一对角设置的竖向排气管插设连接集渣盒,另一对角设置的竖向排气管焊接连接横向连通管,横向连通管与集渣盒的侧壁插设连接。
10.作为本发明进一步的方案:所述集渣盒的顶壁上插设连接排气主管。
11.作为本发明进一步的方案:所述石英坩埚的内表面、可调节加热组件的表面、保温坩埚的内表面、保温盖的底面以及保护气长管的伸入管段上均分别喷涂设有碳化硅涂层。
12.作为本发明进一步的方案:所述保温坩埚上设置有中空结构的内腔,其中空内腔中填充有保温层一,保温层一采用二氧化硅气凝胶材料。
13.作为本发明进一步的方案:所述保温盖上设置有中空结构的内腔,其中空内腔中填充有保温层二,保温层二采用二氧化硅气凝胶材料。
14.作为本发明进一步的方案:所述保温盖底部设有一体结构的密封台部,密封台部的轮廓与保温坩埚的内口径一致,且在密封台部上开设有用于卡合石英坩埚顶口端的卡槽。
15.能够有效降低硅片中碳杂质含量的加热装置的方法,包括以下步骤:步骤一、表面预处理:石英坩埚的内表面、可调节加热组件的表面、保温坩埚的内表面、保温盖的底面以及保护气长管的伸入管段进行表面预处理,表面预处理是通过碳化硅涂层喷涂或涂覆,随后在氮气炉中600℃-1500℃烧结10-20h;步骤二、熔硅料添加:将熔硅料投入石英坩埚内,并在石英坩埚顶口端密封安装保温盖;步骤三、加热熔硅料:石英坩埚内预先通过侧向排气管和排气管组件抽真空,并由保护气长管向石英坩埚内输入氮气或氩气,再通过可调节加热组件包括的上加热件和下加热件进行通电加热,上加热件通电功率在80-90kw,下加热件通电功率在50-60kw,直至石英坩埚的温度达到1350℃,保温20-30min;
步骤四、晶体退火生长:分为三步退火,第一步退火是由上加热件通电功率在60-70kw,下加热件通电功率在30-40kw,石英坩埚的温度在1150℃-1250℃退火5-10h;第二步退火是由上加热件通电功率在30-40kw,关停下加热件通电,并向上加热件的中空内腔中输入冷却风流,石英坩埚的温度在600℃-750℃退火15-20h;第三步退火是由上加热件通电功率在50-60kw,下加热件通电功率在20-30kw,石英坩埚的温度在950℃-1050℃退火15-20h;步骤五、冷却取料:在晶体退火生长完成后,关停上加热件和下加热件通电,均分别向上加热件和下加热件的中空内腔中输入冷却风流,石英坩埚温度达到室温时,打开保温盖,取出晶锭成品。
16.本发明的有益效果:(1)通过将可调节加热组件设计成上加热件和下加热件两段,改变石英坩埚整体式加热方法,上加热件和下加热件通电加热功率不同,使得石英坩埚内部产生垂直方向上的温度梯度,使得石英坩埚底部熔硅液上升速率增大,加快熔硅液面由晶锭芯棒在晶转轴旋转作用拉晶成型;(2)上加热件和下加热件在对石英坩埚进行退火加热时,可以分别进行通电控制,可以适应调节石英坩埚的加热区,石英坩埚的加热中心根据生产需求上下调节,可以随熔硅液降低的液面进行调节加热,满足生产工艺需求;(3)通过将保护气长管的伸入管段伸入至熔硅液中,在输入氮气或氩气保护气体时,由多个射孔均匀喷入熔硅液中,可以随熔硅液加热温度上升至石英坩埚顶部,对晶锭芯棒拉晶成型的硅锭进行气氛保护,有助于降低氧含量,同时输入的保护气可以避免与高温硅熔体液面发生温度梯度变化,避免引起硅熔体液面涡流翻滚,满足硅熔体液面晶转生长的晶片厚度均匀的工艺需求;(4)通过在保温盖上布设排气管组件,在保温盖与石英坩埚处于闭合状态加热熔硅时,所挥发至晶转硅锭上部不利于进入侧向排气管中排出,使得上升的碳杂质便于进入竖向排气管内,并进入集渣盒内或由横向连通管进入集渣盒内,从而排出位于晶锭上部的碳杂质,降低晶锭表面碳杂质含量。
附图说明
17.下面结合附图对本发明作进一步的说明。
18.图1是本发明加热装置的结构示意图;图2是本发明加热装置的截面示意图;图3是本发明加热装置的上加热件和下加热件连接示意图;图4是图3中的上加热件展平状态示意图;图5是图3中的下加热件展平状态示意图;图6是本发明加热装置的集渣盒截面示意图;图7是本发明加热装置的保温坩埚截面示意图;图8是本发明加热装置的保温盖截面示意图;图9是本发明加热装置的保温盖仰视图;图10是现有技术中硅片生产用加热装置的结构示意图;图11是现有技术中硅片生产用加热装置的截面示意图。
19.图中:1、石英坩埚;2、可调节加热组件;2a、整体板件;20、上加热件;200、上加热片;21、下加热件;210、下加热片;3、保温坩埚;30、保温层一;4、保温盖;40、密封台部;41、卡槽;42、保温层二;5、晶转轴;6、晶锭芯棒;7、坩埚轴;8、保护气长管;8a、保护气短管;80、射孔;9、排气管组件;10、冷却进风管;11、冷却出风管;12、输入电极杆;13、输出电极杆;14、侧向排气管;15、竖向排气管;16、横向连通管;17、集渣盒;18、排气主管;19、隔热柱。
具体实施方式
20.下面将结合本发明实施例中的附图,对本发明实施例中的技术方案进行清楚、完整地描述,显然,所描述的实施例仅仅是本发明一部分实施例,而不是全部的实施例。基于本发明中的实施例,本领域普通技术人员在没有作出创造性劳动前提下所获得的所有其它实施例,都属于本发明保护的范围。
21.在本发明的描述中,需要理解的是,指示方位或位置关系的术语为基于附图所示的方位或位置关系,仅是为了便于描述本发明和简化描述,而不是指示或暗示所指的设备或元件必须具有特定的方位、以特定的方位构造和操作,因此不能理解为对本发明的限制;在本发明的描述中,“多个”、“若干”的含义是至少两个,例如两个、三个等,除非另有明确具体的限定。
22.实施例1请参阅图1-9所示,本发明为能够有效降低硅片中碳杂质含量的加热装置,包括石英坩埚1,石英坩埚1的外壁上紧贴设有可调节加热组件2,可调节加热组件2包括有上加热件20和下加热件21,上加热件20套设在石英坩埚1的顶部,下加热件21套设在石英坩埚1的底部,上加热件20和下加热件21的两侧分别连接有输入电极杆12和输出电极杆13,上加热件20和下加热件21内均设置有封闭的冷却腔,冷却腔的两侧分别连接有冷却进风管10和冷却出风管11,输入电极杆12、输出电极杆13、冷却进风管10和冷却出风管11均分别贯穿保温坩埚3伸出。
23.通过将可调节加热组件2设计成上加热件20和下加热件21两段,改变石英坩埚1整体式加热方法,上加热件20和下加热件21通电加热功率不同,使得石英坩埚1内部产生垂直方向上的温度梯度,使得石英坩埚1底部熔硅液上升速率增大,加快熔硅液面由晶锭芯棒6在晶转轴5旋转作用拉晶成型。
24.上加热件20和下加热件21在对石英坩埚1进行退火加热时,可以分别进行通电控制,可以适应调节石英坩埚1的加热区,石英坩埚1的加热中心根据生产需求上下调节,可以随熔硅液降低的液面进行调节加热,满足生产工艺需求。
25.本实施例中,上加热件20和下加热件21均采用石墨材料制得,且上加热件20和下加热件21之间通过多个隔热柱19连接,使得上加热件20和下加热件21一体连接方便,并通过多个隔热柱19进行隔断加热使用。
26.本实施例中,上加热件20上设置有若干间隔设置的上加热片200,下加热片210上设置有若干间隔设置的下加热片210,设置的上加热片200和下加热片210用于加热材料,且便于减少适应坩埚内熔硅液横向对流,降低熔硅液与石英坩埚1反应速率。
27.保温坩埚3的顶口端密封连接保温盖4,保温盖4的四角位置处分别插设连接保护气长管8,保护气长管8伸入至石英坩埚1的熔硅液中,且保护气长管8的伸入管段上均布开
设有多个射孔80,通过将保护气长管8的伸入管段伸入至熔硅液中,在输入氮气或氩气保护气体时,由多个射孔80均匀喷入熔硅液中,可以随熔硅液加热温度上升至石英坩埚1顶部,对晶锭芯棒6拉晶成型的硅锭进行气氛保护,有助于降低氧含量,同时输入的保护气可以避免与高温硅熔体液面发生温度梯度变化,避免引起硅熔体液面涡流翻滚,满足硅熔体液面晶转生长的晶片厚度均匀的工艺需求。
28.保温盖4上设置有排气管组件9,排气管组件9包括有位于晶转轴5四周设置的竖向排气管15,一对角设置的竖向排气管15插设连接集渣盒17,另一对角设置的竖向排气管15焊接连接横向连通管16,横向连通管16与集渣盒17的侧壁插设连接,现有技术中是通过保温坩埚3四周正对晶锭芯棒6设置的侧向排气管14进行排出加热过程中上升的杂质,而本技术通过在保温盖4上布设排气管组件9,在保温盖4与石英坩埚1处于闭合状态加热熔硅时,所挥发至晶转硅锭上部不利于进入侧向排气管14中排出,使得上升的碳杂质便于进入竖向排气管15内,并进入集渣盒17内或由横向连通管16进入集渣盒17内,从而排出位于晶锭上部的碳杂质,降低晶锭表面碳杂质含量。
29.本实施例中,集渣盒17的顶壁上插设连接排气主管18,使得集渣盒17内沉降的碳杂质便于通过排气主管18抽离,避免回流至石英坩埚1中造成污染。
30.本实施例中,石英坩埚1的内表面、可调节加热组件2的表面、保温坩埚3的内表面、保温盖4的底面以及保护气长管8的伸入管段上均分别喷涂设有碳化硅涂层,在高温加热熔硅过程中,涂覆在各部件的碳材料器件表面,可有效地消除一氧化碳的产生,从而降低铸锭多晶硅中的杂质及杂质衍生的位错,同时可以阻止碳元素进入硅锭晶体中,有效降低碳杂质的含量,提升硅片生产质量。
31.本实施例中,保温坩埚3上设置有中空结构的内腔,其中空内腔中填充有保温层一30,保温层一30采用二氧化硅气凝胶材料;保温盖4上设置有中空结构的内腔,其中空内腔中填充有保温层二42,保温层二42采用二氧化硅气凝胶材料,保温坩埚3和保温盖4的中空内腔中分别填充二氧化硅气凝胶材料,进行保温隔热作用,避免热量损失,同时可以减少对可调节加热组件2冷却资源的投入。
32.本实施例中,保温盖4底部设有一体结构的密封台部40,密封台部40的轮廓与保温坩埚3的内口径一致,且在密封台部40上开设有用于卡合石英坩埚1顶口端的卡槽41,设置的密封台部40加强保温盖4密封安装作用,且密封台部40与石英坩埚1的顶口端错位卡合,避免可调节加热组件2和保温坩埚3所挥发的碳材料渗入至石英坩埚1内部,可以进一步降低硅片生产中所掺杂的碳杂质含量。
33.实施例2请参阅图1-9所示,能够有效降低硅片中碳杂质含量的加热装置的方法,包括以下步骤:步骤一、表面预处理:石英坩埚1的内表面、可调节加热组件2的表面、保温坩埚3的内表面、保温盖4的底面以及保护气长管8的伸入管段进行表面预处理,表面预处理是通过碳化硅涂层喷涂或涂覆,随后在氮气炉中600℃-1500℃烧结10-20h,通过在各碳材料部件表面喷涂碳化硅,阻隔与熔硅液接触反应,可有效地消除一氧化碳的产生,从而降低铸锭多晶硅中的杂质及杂质衍生的位错,同时可以阻止碳元素进入硅锭晶体中,有效降低碳杂质的含量,提升硅片生产质量;
步骤二、熔硅料添加:将熔硅料投入石英坩埚1内,并在石英坩埚1顶口端密封安装保温盖4;步骤三、加热熔硅料:石英坩埚1内预先通过侧向排气管14和排气管组件9抽真空,并由保护气长管8向石英坩埚1内输入氮气或氩气,输入的保护气体氛围中可以降低硅片生产的氧含量,再通过可调节加热组件2包括的上加热件20和下加热件21进行通电加热,上加热件20通电功率在80-90kw,下加热件21通电功率在50-60kw,直至石英坩埚1的温度达到1350℃,保温20-30min,在加热过程中可以通过坩埚轴7带动石英坩埚1旋转,使得石英坩埚1受热均匀,使得石英坩埚1底部所加热熔化的硅溶液浓度较多,同时石英坩埚1内部产生垂直方向上的温度梯度,使得石英坩埚1底部熔硅液上升速率增大,加快熔硅液面由晶锭芯棒6在晶转轴5旋转作用拉晶成型,可以保证石英坩埚1底部熔硅液持续上升进行拉晶生产;步骤四、晶体退火生长:分为三步退火,第一步退火是由上加热件20通电功率在60-70kw,下加热件21通电功率在30-40kw,石英坩埚1的温度在1150℃-1250℃退火5-10h;第二步退火是由上加热件20通电功率在30-40kw,关停下加热件21通电,并向上加热件20的中空内腔中输入冷却风流,石英坩埚1的温度在600℃-750℃退火15-20h;第三步退火是由上加热件20通电功率在50-60kw,下加热件21通电功率在20-30kw,石英坩埚1的温度在950℃-1050℃退火15-20h,上加热件20和下加热件21在对石英坩埚1进行退火加热时,可以分别进行通电控制,同时可以适应调节石英坩埚1的加热区,石英坩埚1的加热中心根据生产需求上下调节,可以随熔硅液降低的液面进行调节加热,满足生产工艺需求;步骤五、冷却取料:在晶体退火生长完成后,关停上加热件20和下加热件21通电,均分别向上加热件20和下加热件21的中空内腔中输入冷却风流,使得石英坩埚1冷却高效,石英坩埚1温度达到室温时,打开保温盖4,取出晶锭成品。
34.以上对本发明的一个实施例进行了详细说明,但所述内容仅为本发明的较佳实施例,不能被认为用于限定本发明的实施范围。凡依本发明申请范围所作的均等变化与改进等,均应仍归属于本发明的专利涵盖范围之内。