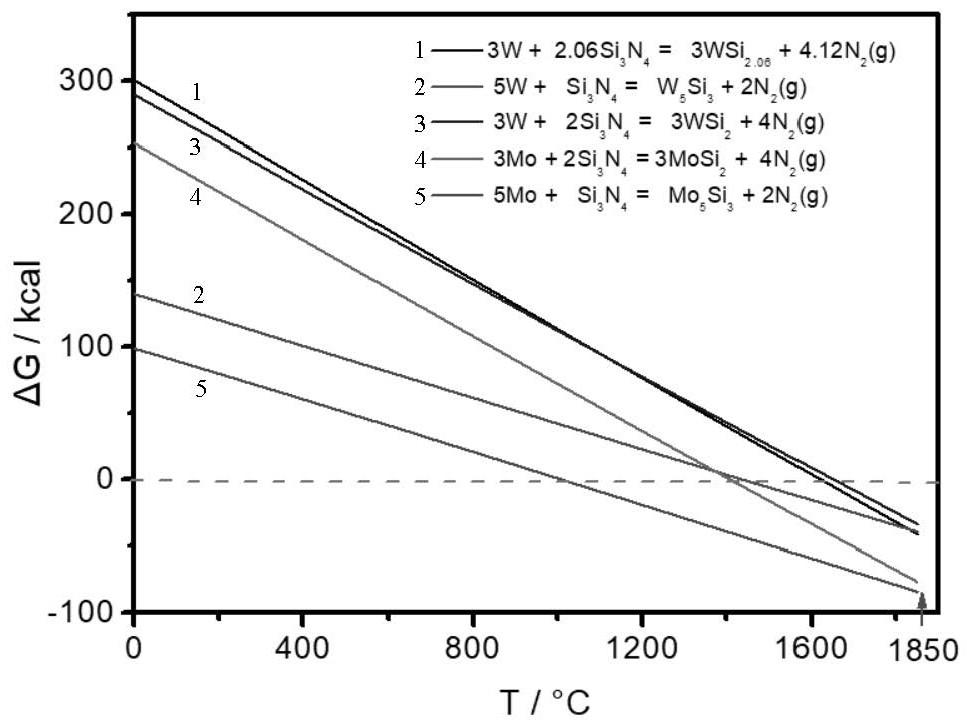
1.本发明涉及一种氮化硅/钨高温共烧陶瓷基板的制备方法,属于功率器件封装技术领域。
背景技术:2.随着电子技术的日益发展,电力电子器件逐渐向高集成度、大功率、高耗能等方向发展。电力电子器件作为电子设备中的数电转化中心,信号传播通路,应用领域涵盖了能源、交通、基础工业等各个领域。大功率化、高频化、集成化的特点导致其功率可达gw级别。因能量密度高而导致发热严重,严重影响器件的工作稳定性和寿命的问题也日益突出。因此获得更高散热性能的陶瓷基板成为一种十分合理的选择。目前氧化铝和氮化铝是常用的陶瓷基板材料。但是氧化铝热导率比较低,达不到与日俱增的散热要求;而氮化铝陶瓷尽管热导率比较高,但是力学性能差,无法承担因热冲击、碰撞等应用环境对基板带来的力学性能方面的挑战。氮化硅陶瓷具备高可靠性的优势,并且随着对高导热氮化硅陶瓷的研究日益成熟,其热导率问题逐渐得到解决。因此氮化硅陶瓷是目前非常有优势的候选材料。但是基于氮化硅陶瓷金属化的研究目前鲜少见到报道,这直接限制了氮化硅陶瓷在电力电子器件方面的应用。因此,本发明提出一种氮化硅陶瓷基板的金属化方法,为其在电力电子器件领域的应用提供借鉴。
技术实现要素:3.本发明的目的在于提供一种氮化硅陶瓷基板金属化的方法,以解决高功率密度电子器件对基板材料带来的发热、工作稳定性问题。
4.一方面,本发明提供了一种氮化硅/钨高温共烧陶瓷的制备方法,包括:(1)以硅粉/氮化硅粉作为原料粉体,稀土氧化物和碱土金属氧化物作为复合烧结助剂,与溶剂进行一次球磨混合,再加入塑性剂和粘结剂进行二次球磨,最后经真空脱泡,得到混合浆料;(2)采用流延成型设备将混合浆料流延成型,制备得到生料带;(3)以金属w浆料作为印刷导电浆料,通过丝印机在流延膜上绘制导电图形,待干燥后,得到印刷有导电图形的生料带;(4)将所得印刷有导电图形的生料带经切割、叠层后得到需要厚度的氮化硅膜片,再经真空脱粘和气压烧结,得到氮化硅/钨高温共烧陶瓷。
5.在前期探究过程中,本发明人通过研究(如图3所示)发现,钨和钼相比,在高温下钼与氮化硅的热力学反应倾向更大。但是本发明人又发现,金属层与基体相间结合强度不应由金属功能相提供,过度的界面反应会对金属层导电性能产生负面影响。因此,本发明人选择金属钨。进一步,本发明还存在以下技术难点:(1)使用含有硅粉的原料来制备高导热氮化硅,主要通过优化烧结助剂比例、控制反应烧结与后烧结工艺技术来提高氮化硅的热导率;(2)实现钨金属层与氮化硅基体之间良好的界面结合,以实现烧结匹配与金属层导电
性能。主要通过球磨对粉体进行前处理,得到更细的粉体原料;通过优化浆料的固含量,减少基体与金属层在脱粘后的孔隙率;在流延工艺所得陶瓷生瓷片上使用丝网印刷技术得到合适的钨金属化膜;最终达到较小的烧结收缩率,实现二者的收缩率匹配。以实现烧结匹配与金属层导电。本发明实现金属层导电,并给出测试数据。
6.较佳的,所述溶剂为乙醇、乙酸乙酯、2-丁酮或者乙醇/丁酮、乙酸乙酯/丁酮的混合物。
7.较佳的,所述稀土氧化物为氧化铒、氧化钐中至少一种;所述碱土金属氧化物为mgo、cao中的至少一种;其中碱土金属氧化物和稀土氧化物质量比含量(20~40):(60~80)。
8.较佳的,原料为硅粉、氮化硅粉中的至少一种,当硅粉含量>0%时,硅粉的质量皆计为完全氮化后的质量,且烧结助剂质量含量基于该计算方式后所得总粉体质量所得。
9.较佳的,当硅粉和氮化硅共同作为原料,其中所述烧结助剂的质量含量为5%~13%。优选地,硅粉的含量≥0wt%(更优选为20~100wt%),硅粉和氮化硅粉的总质量记为100wt%。
10.较佳的,所述硅粉体的粒径范围为0.5~20μm,氧含量为0.42wt%;所述氮化硅粉体的粒径在0.3~2μm。
11.较佳的,所述粘结剂为聚乙烯醇缩丁醛、聚甲基丙烯酸甲酯、聚碳酸亚丙酯中的一种。
12.较佳的,所述分散剂为三油酸甘油酯、蓖麻油磷酸酯和松油醇中的一种。
13.较佳的,所述塑性剂为邻苯二甲酸丁苄酯、邻苯二甲酸二辛酯和聚乙二醇400中的至少一种,例如邻苯二甲酸丁苄酯-聚乙二醇400或者邻苯二甲酸二辛酯-聚乙二醇400。
14.较佳的,所述真空脱泡的真空度为15~400pa,脱泡时间为15~40min。
15.较佳的,所述流延成型的参数包括:刮刀高度为100μm~1.00mm;所述每片生料带的厚度为50μm~0.50mm。
16.较佳的,所述丝印机设置参数包括:橡胶刮板呈30~50
°
,版距为1~10mm,升降行程为100~200mm,印刷速度与回墨速度分别为10%和30%。
17.较佳的,所述切割后的印刷有导电图形的生料带的尺寸为50mm
×
50mm;所述叠层的数量至少为10片,压力为2~30mpa,时间为15~40min。
18.较佳的,所述脱粘的温度为400~700℃,真空条件,时间为1~6小时;优选地,所述真空脱粘的升温速率为1~5℃/min。
19.较佳的,所述气压烧结的温度为1800~1950℃,200~900kpa氮气压力,保温时间为2~24小时;优选地,所述气压烧结的升温速率为1~5℃/min。
20.较佳的,当原料中含有硅粉时,在气压烧结前,将脱粘后的氮化硅膜片再进行氮化处理;所述氮化处理的温度为1350~1550℃,保温时间是2~24小时;优选地,所述氮化处理的升温速率为1~5℃/min。
21.再一方面,本发明提供了一种根据上述制备方法制备的氮化硅/钨高温共烧陶瓷。
22.有益效果:本发明提供一种氮化硅陶瓷基板的流延成型制备方法:以所述混合溶剂、硅粉及所述烧结助剂、粘结剂与塑性剂为原料,制备混合均匀的硅流延浆料,通过流延成型获得强
度塑性合适的可蜷曲生坯;本发明使用商用aln钨金属化浆料为墨,通过丝网印刷工艺,在上述生坯表面涂布厚度均匀,清晰的金属化电路。并经过激光切割、叠层热压得到硅/钨多层生坯。后经过共同脱粘、氮化、烧结工艺处理,得到w金属层光滑无翘曲,界面结合稳定,氮化硅基板性能稳定的氮化硅/钨高温共烧陶瓷;本发明提出了一种质量可靠的氮化硅陶瓷基板,并在其上成功实现氮化硅陶瓷基板的金属化。这为氮化硅陶瓷基板在多层共烧组件中的应用提供了实验依据,有利于拓展氮化硅陶瓷在电子行业的应用。
附图说明
23.图1为含w多层烧结样品表面图;图2为含w多层烧结样品侧面图;图3为w/mo与si3n4基板在0-1850℃的反应吉布斯能变化;图4为实施例中氮化硅多层组件烧结体断面的xrd图。
具体实施方式
24.以下通过下述实施方式进一步说明本发明,应理解,下述实施方式仅用于说明本发明,而非限制本发明。
25.本发明以氮化硅/硅粉为原料,通过流延成型得到氮化硅素坯,脱粘后进行氮化和烧结制备氮化硅陶瓷基片。采用氮化硅/硅粉作为原料进行反应烧结,采用硅粉可以避免高纯氮化硅原料成本高、易因潮解受限制等问题,实现氮化硅陶瓷的低成本制备,推动氮化硅陶瓷的大量生产。且硅粉具备氧含量低的优点,易获得热导率更高的氮化硅基板。
26.本发明使用流延成型技术制备氮化硅素坯,以氮化硅/硅粉作为原料粉体,稀土氧化物re2o3和金属氧化物mgo/cao作为复合烧结助剂,得到混合粉体。与所述分散剂,溶剂经一次球磨混合后,再加入所述粘结剂与分散剂,经过二次球磨混合、脱泡获得浆料,通过流延成型获得素坯。再经过脱粘、氮化、烧结获得氮化硅陶瓷基片。
27.本发明提出的氮化硅陶瓷基板金属化技术,以所述流延成型技术得到的素坯作为基板,以商用钨金属化浆料为墨,进行丝网印刷制备氮化硅/钨共烧素坯。
28.流延成型:以氮化硅/硅粉为原料,稀土氧化物re2o3和碱金属氧化物(mgo/cao)作为复合烧结助剂。以乙醇、乙酸乙酯、2-丁酮或者乙醇/丁酮、乙酸乙酯/丁酮的混合物作为溶剂,三油酸甘油酯、蓖麻油磷酸酯和松油醇中的一种作为分散剂,聚乙烯醇缩丁醛、聚甲基丙烯酸甲酯、聚碳酸亚丙酯中的一种作为粘结剂,邻苯二甲酸丁苄酯、邻苯二甲酸二辛酯中的一种作为塑性剂ⅰ,聚乙二醇400作为塑性剂ⅱ。先将溶剂、分散剂、氮化硅/硅粉、烧结助剂进行一次球磨,24-36h后加入粘结剂、塑性剂二次球磨,48-72h后得到混合均匀的浆料,脱泡后,使用流延机进行流延。
29.流延成型工艺所得氮化硅陶瓷素坯,钨金属化浆料。
30.使用丝网印刷设备,在上述氮化硅陶瓷素坯上印刷厚度均匀的钨浆料。将室温晾干后的素坯裁切成大小相同的方块进行多层等压叠压,得到厚度需求的多层素坯。优选,使用激光切割方法,得到尺寸为50mm
×
50mm的方块,并进行叠压。
31.作为一个丝网印刷的示例,包括:在设置好丝印机参数以后,通过丝印机在素坯上进行丝网印刷。设置丝印机参数如下,橡胶刮板呈30-50
°
,版距为1-10mm,升降行程为100-200mm,印刷速度与回墨速度分别为10%和30%。然后经过激光切割得到50mm
×
50mm相同大小的方片,每次10-20片,在2-30mpa压力下叠压15-40min得到厚度均一的方块,然后进行脱粘、氮化和烧结。
32.脱粘、氮化和烧结。首先进行脱粘工艺,脱粘温度通常在400-700℃,真空条件,保温1-6小时,升温速率1-5℃/分钟。若书原料中含有硅粉,脱粘结束后进行氮化处理,氮化温度为1350-1550℃,升温速率1-5℃/分钟,保温时间是2-24小时。嘴周采用气压烧结工艺进行烧结,气氛为氮气气氛,温度为1800-1950℃,气压为200-900kpa,时间2-24小时,所述烧结的升温速率为1-5℃/分钟。
33.本发明中,使用流延成型方法制备氮化硅陶瓷基片,使用丝网印刷工艺在氮化硅陶瓷素坯上印刷钨浆料,然后在裁切叠压后进行共同脱粘、氮化与烧结。在具备传统氮化硅基板性能的基础上,更具备成本低、热导率更高、生产效率高的优势,是一种具备大批量生产优势的制备方案。
34.本发明采用阿基米德排水方法测得氮化硅陶瓷基片材料的相对密度为90-97%。采用激光热导仪方法测得氮化硅陶瓷基片材料的热导率为65~70w/m
·
k。采用三点弯曲法测得所述氮化硅陶瓷基片材料的抗弯强度为700~900mpa。经过测量,以100wt%硅粉为原料,烧结收缩率为8%~12%。以100wt%氮化硅为原料,烧结收缩率为15%~20%。当硅粉含量发生变化时,其烧结收缩率为8%~20%不等。经过测量,共烧后金属化层的厚度为7~10μm。采用x射线衍射分析得到共烧后氮化硅/w界面有w5si3相生成。采用四方电阻法测得金属层的方阻为0.8~1.0ω/sq。
35.下面进一步例举实施例以详细说明本发明。同样应理解,以下实施例只用于对本发明进行进一步说明,不能理解为对本发明保护范围的限制,本领域的技术人员根据本发明的上述内容作出的一些非本质的改进和调整均属于本发明的保护范围。下述示例具体的工艺参数等也仅是合适范围中的一个示例,即本领域技术人员可以通过本文的说明做合适的范围内选择,而并非要限定于下文示例的具体数值。
36.实施例1以硅粉为原料(107.67g),以78wt%乙酸乙酯和22wt%2-丁酮的共沸混合物作为溶剂,mgo和er2o3作为烧结助剂,mgo含量为3wt%,er2o3含量为9wt%。三油酸甘油酯为分散剂。将上述溶剂、分散剂与粉体进行一次球磨,时长为24h。以聚碳酸亚丙酯为粘结剂,邻苯二甲酸丁苄酯与聚乙二醇400作为塑性剂,加入后进行二次球磨,时长为48h,得到混合均匀的浆料,在脱泡25-30min后,使用流延机进行流延,刮刀高度为0.4mm,流延速度为120mm/min。流延膜干燥后卷轴取出。使用丝网印刷机进行钨浆料的印刷,设置橡胶刮板呈45,版距为2mm,升降行程为150mm,印刷速度与回墨速度分别为10%和30%。在上述所得氮化硅素坯上印刷钨浆料,室温晾干。将流延膜裁剪成尺寸为50mm
×
50mm矩形,每次取10片,在手动液压机下保压1min后,放入60℃烘箱保温30min,取出后继续对模具施加同样的压力,自然冷却后从模具中取出样品。在真空脱粘炉中600℃保温1h。脱粘后在1450℃,氮气气氛下保温2h。氮化后进一步将产品升温到1830℃,保温2h完成烧结。结束后随炉冷却,制备出w金属层光滑无翘曲,界面结合稳定,氮化硅基板性能稳定的氮化硅/钨高温共烧陶瓷。
37.实施例2本实施例2中,氮化硅/钨高温共烧陶瓷的制备过程参照实施例1,区别仅在于:选择si粉和si3n4粉作为原料(总107.67g),其中si粉含量为80%。制备出w金属层光滑无翘曲,界面结合稳定,氮化硅基板性能稳定的氮化硅/钨高温共烧陶瓷。
38.实施例3本实施例3中,氮化硅/钨高温共烧陶瓷的制备过程参照实施例1,区别仅在于:选择si粉和si3n4粉作为原料(总107.67g),其中si粉含量为60%。制备出w金属层光滑无翘曲,界面结合稳定,氮化硅基板性能稳定的氮化硅/钨高温共烧陶瓷。
39.实施例4本实施例4中,氮化硅/钨高温共烧陶瓷的制备过程参照实施例1,区别仅在于:选择si粉和si3n4粉作为原料(总107.67g),其中si粉含量为40%。制备出w金属层光滑无翘曲,界面结合稳定,氮化硅基板性能稳定的氮化硅/钨高温共烧陶瓷。
40.实施例5本实施例5中,氮化硅/钨高温共烧陶瓷的制备过程参照实施例1,区别仅在于:选择si粉和si3n4粉作为原料(总107.67g),其中si粉含量为0%;为保证烧结致密,需以78wt%乙酸乙酯和22wt%2-丁酮的共沸混合物作为溶剂,mgo和er2o3作为烧结助剂,mgo含量为3wt%,er2o3含量为9wt%。制备出w金属层光滑无翘曲的共烧陶瓷,但是金属层图案收缩出现不一致现象。
41.经过实验探究,在氮化硅流延成型过程中改变粉体中si/si3n4比例,金属层方阻的结果如下。选择si粉和si3n4粉作为原料(总107.67g),其中si粉含量为100%时,金属层方阻为0.89ω/sq。si粉含量为80%时,金属层方阻为1.22ω/sq。si粉含量为60%时,金属层方阻为1.09ω/sq。si粉含量为40%时,金属层方阻为1.14ω/sq。si粉含量为20%时,金属层方阻为1.47ω/sq。si粉含量为0%时,金属层方阻为1.21ω/sq。此外,金属与陶瓷界面结合强度缺乏精确的测试手段。宏观上表现出无翘曲、脱层、剥落等缺陷的烧结匹配结果。