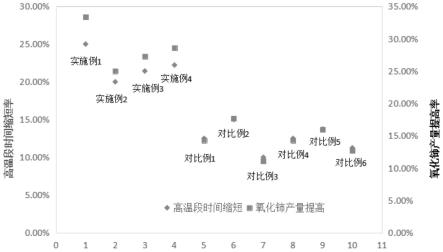
1.本发明涉及窑炉节能涂料领域,尤其是涉及一种氧化铈隧道窑节能方法。
背景技术:2.氧化铈应用领域非常广泛,可作为抛光粉、催化剂、电极材料、特种玻璃、陶瓷材料、探测材料等。2021年我国氧化铈产出量为11.03万吨,根据不同的应用领域所需求的铈化合物也不相同,纯度在99%以上的铈化合物主要以氧化铈、碳酸铈、醋酸铈、氯化铈等产品销售,铈化合物主要以氧化铈和碳酸铈为主流产品销售。
3.目前稀土分离企业采用隧道窑、梭式窑、转窑和悬浮式窑等灼烧设备,其中隧道窑包括辊道窑、台车式隧道窑、推板窑。转窑和悬浮式窑灼烧的氧化铈产品组分和粒度均匀,目前已在企业中得到应用。而采用隧道窑灼烧碳酸铈制备氧化铈时,隧道窑高温区温度控制在850℃-900℃,高温区停留时间根据隧道窑类型、装载量、高温区温度、碳酸铈含水量不同而不同;由于台车式隧道窑装载量较大,在高温区保温时间较长,而辊道窑装载量相对较少,在高温区保温时间相对较短;隧道窑中每个匣钵中装入的碳酸铈量较大,热量传递到匣钵中部时间较长,造成匣钵中间部位的碳酸铈分解较慢,所以通过升高灼烧温度和延长保温时间来实现中间部位碳酸铈完全分解。
4.灼烧窑产生的热量主要通过对流、传导和辐射来对物体进行加热,温度越高,辐射传热占比越大,尤其当温度大于800℃时,辐射传热占比达到80%以上,因此提高辐射传热效率对隧道窑高温灼烧节能至关重要。目前一些企业采用隧道窑灼烧氧化铈,存在着不足之处是:装有碳酸铈的匣钵在窑内摆放的位置不同,其受热反应温度有一定的差别,特别是匣钵中装满碳酸铈在灼烧过程中靠近匣钵边缘的原料优先分解,而匣钵中间的碳酸铈需要在高温区停留一定时间才能完全反应,这样就造成在窑内温度较高的区域和靠近匣钵边缘区域的氧化铈与其它区域相比颗粒较大,甚至出现过烧现象,造成同一个匣钵中不同位置的氧化铈粉体粒度不一致,氧化铈灼烧窑内温度控制对产品质量起着关键作用。目前企业解决办法是匣钵装满碳酸铈后,在碳酸铈中间扎几个洞,目的是提高匣钵中间碳酸铈分解速率及反应完全,提高氧化铈产品质量的均一性。
技术实现要素:5.有鉴于此,本发明旨在提出一种氧化铈隧道窑节能方法,以降低氧化铈灼烧过程中的能源消耗。
6.为达到上述目的,本发明的技术方案是这样实现的:
7.一种氧化铈隧道窑节能方法,该方法包括如下步骤:
8.1)将隧道窑内腔表面喷涂红外辐射材料,进行高温灼烧后得到具有红外辐射功能的隧道窑;其中,红外辐射材料由重量份数为100-200份的ceo2、10-30份的cepo4和180-220份的固含量为48%~58%al(h2po4)3溶液组成;
9.2)将装有碳酸铈的匣钵进入到红外辐射隧道窑中,通过预热区、高温区和冷却区,
得到灼烧后的氧化铈粉体。
10.本发明红外辐射材料采用为ceo2、粘结剂添加cepo4原因为采用ce的化合物可以避免引入稀土杂质,而引入al(h2po4)3和cepo4共同作用,可以使粘结强度更好,避免耐火材料的脱离,避免非稀土杂质的引入。
11.进一步,红外辐射材料由如下方法制备得到:
12.1)将ceo2、cepo4和分散剂加入水中高速分散,粉水质量比为(1~2):1,分散剂的量为浆料总量的1
‰‑5‰
,分散转速为800-1000r/min,分散完全后的浆料转移至砂磨机中砂磨,磨至粒径d
(90)
≤10.0μm;
13.2)再将经过砂磨后的浆料转移至分散机中,加入粘结剂al(h2po4)3溶液,搅拌后得到红外辐射材料。
14.进一步,分散剂为byk190、rt-8040、rt-8022中的一种或两种以上的混合物。
15.进一步,步骤1)中,在隧道窑内腔表面喷涂红外辐射材料前先隧道窑内腔耐火材料表面清除耐火泥和灰尘,喷涂之后,在室温干燥,按隧道窑的烘干程序升温,最高温度达到1200℃保温2h。
16.进一步,步骤2)中,隧道窑高温区温度通常控制在850℃-900℃。
17.进一步,所述隧道窑为台车式隧道窑或辊道窑。
18.进一步,喷涂厚度为0.2-0.4mm。喷涂厚度过小,影响发射率,喷涂厚度过大,涂层易开裂。
19.本发明得到的氧化铈粉体中稀土总量reo大于99%,灼减小于0.5%。
20.本发明得到的红外辐射隧道窑与常规隧道窑相比,通过高温区时间缩短了20%以上,灼烧氧化铈产量提高25%以上,生产每吨氧化铈节约能源20%以上。
21.喷涂红外辐射材料的隧道窑均具有全波长积分发射率大于0.90,喷涂红外辐射材料明显增强了隧道窑的辐射传热,同时也改善了窑内温度场强及均匀性,所以碳酸铈进入隧道窑就具有对流、传导和辐射方式传递热源,辐射材料发射的远红外线直接穿透到碳酸铈内部进行加热,实现了匣钵边缘和中间部位的碳酸铈均匀受热。随着隧道窑预热区温度逐渐升高,碳酸铈逐步脱出自由水和结晶水,脱水后形成的无水碳酸铈再缓慢分解释放出二氧化碳,在高温区碳酸铈完全分解形成氧化铈,辐射材料发射远红外线加速了匣钵中间碳酸铈转化为氧化铈反应速度,缩短了碳酸铈的分解时间,提高了匣钵通过窑体速度。
22.相对于现有技术,本发明所述的氧化铈隧道窑节能方法具有以下优势:
23.(1)本发明显著增强了隧道窑内的红外辐射发射率,改善了窑内温度场强及均匀性,与常规相同型号的隧道窑对比生产每吨氧化铈节约能源20%以上,氧化铈灼烧产量提高25%以上。
24.(2)本发明采用红外辐射材料,发射的远红外线直接穿透到碳酸铈内部进行加热,增强了匣钵中间部位碳酸铈分解反应能量,促进了中间部位碳酸铈加速分解,明显缩短了匣钵通过高温区时间,匣钵内氧化铈粉体粒度分布均匀,解决了靠近匣钵边缘区域的氧化铈粉体颗粒较大,甚至出现过烧现象。
25.(3)本发明在内腔耐火材料表面喷涂红外辐射材料与灼烧物料元素相同,明显阻隔了耐火材料中化合物对氧化铈的污染,不会影响氧化铈产品纯度,解决了氧化铈灼烧工艺非稀土杂质污染难题。
26.(4)本发明红外辐射材料在高温、还原和氧化环境中具有较高的稳定性,阻止了碳酸铈分解产生的气体对窑体的腐蚀,延长了隧道窑使用寿命。
27.(5)本发明红外辐射材料中高温黏结剂al(h2po4)3和cepo4在1200℃与ceo2和耐火材料紧密结合,高温下al(h2po4)3生成偏磷酸铝,ceo2、cepo4、偏磷酸铝与耐火材料共同作用生产一层致密陶瓷相结构釉面,红外辐射隧道窑烧制温度是1200℃,而氧化铈最高灼烧温度为900℃,所以铝和磷不会进入氧化铈中,确保了氧化铈产品纯度。
28.(6)本发明红外辐射材料中ceo2和cepo4具有很高的红外辐射发射率,隧道窑内每个匣钵中氧化铈产品的灼减量分析数据相近、粒度分布均匀。
附图说明
29.构成本发明的一部分的附图用来提供对本发明的进一步理解,本发明的示意性实施例及其说明用于解释本发明,并不构成对本发明的不当限定。在附图中:
30.图1为实施例1-4与对比例1-6高温段时间缩短率和氧化铈产量提高率的散点图。
具体实施方式
31.需要说明的是,在不冲突的情况下,本发明中的实施例及实施例中的特征可以相互组合。
32.下面将参考附图并结合实施例来详细说明本发明。
33.实施例1
34.一种氧化铈隧道窑节能方法,该方法包括如下步骤:
35.(1)红外辐射辊道窑:在40米长的辊道窑中,将辊道窑内腔耐火材料表面清除耐火泥和灰尘,将辊道窑内腔表面喷涂红外辐射材料,喷涂厚度0.3mm,在室温干燥后,按辊道窑的烘干程序升温,最高温度达到1200℃保温2h,得到具有红外辐射功能的辊道窑,红外辐射辊道窑在工作温度25℃-900℃范围内全波长积分发射率大于0.90;
36.红外辐射材料的制备方法为:将100份ceo2、10份cepo4和0.22份分散剂byk190加入110份水中高速分散,粉水比为1:1,分散剂的量为浆料总量的1
‰
,分散转速为1000r/min,分散完全后的浆料转移至砂磨机中砂磨,磨至粒径d
(90)
≤10.0μm;再将经过砂磨后的浆料转移至分散机中,加入200份固含量为50%al(h2po4)3溶液,制得红外辐射涂料;
37.(2)氧化铈制备:红外辐射辊道窑高温区温度控制在850℃,装有碳酸铈的匣钵进入到红外辐射辊道窑中,通过预热区、高温区和冷却区,得到的氧化铈粉体中稀土总量reo大于99%,灼减小于0.5%;
38.(3)节能对比分析:红外辐射辊道窑与常规氧化铈辊道窑相比,在辊道窑高温区温度为850℃下,通过高温区时间从4h降低到3h,时间缩短25.0%,红外辐射辊道窑灼烧氧化铈产量提高33.33%,生产每吨氧化铈节约能源25.0%。
39.实施例2
40.一种氧化铈隧道窑节能方法,该方法包括如下步骤:
41.(1)红外辐射辊道窑:在40米长的辊道窑中,将辊道窑内腔耐火材料表面清除耐火泥和灰尘,将辊道窑内腔表面喷涂红外辐射材料,喷涂厚度0.3mm,在室温干燥后,按辊道窑的烘干程序升温,最高温度达到1200℃保温2h,得到具有红外辐射功能的辊道窑,红外辐射
辊道窑在工作温度25℃-900℃范围内全波长积分发射率大于0.90;
42.红外辐射材料的制备方法为:将100份ceo2、10份cepo4和0.66份分散剂byk190加入110份水中高速分散,粉水比为1:1,分散剂的量为浆料总量的3
‰
,分散转速为800r/min,分散完全后的浆料转移至砂磨机中砂磨,磨至粒径d
(90)
≤10.0μm;再将经过砂磨后的浆料转移至分散机中,加入200份固含量为50%al(h2po4)3溶液,制得红外辐射涂料;
43.(2)氧化铈制备:红外辐射辊道窑高温区温度控制在880℃,装有碳酸铈的匣钵进入到红外辐射辊道窑中,通过预热区、高温区和冷却区,得到的氧化铈粉体中稀土总量reo大于99%,灼减小于0.5%;
44.(3)节能对比分析:红外辐射辊道窑与常规氧化铈辊道窑相比,在辊道窑高温区温度为880℃下,通过高温区时间从3h降低到2.4h,时间缩短20.0%,红外辐射辊道窑灼烧氧化铈产量提高25.0%,生产每吨氧化铈节约能源20.0%。
45.实施例3
46.一种氧化铈隧道窑节能方法,该方法包括如下步骤:
47.(1)红外辐射台车式隧道窑:在72米长的台车式隧道窑中,将台车式隧道窑内腔耐火材料表面清除耐火泥和灰尘,将窑内腔表面喷涂红外辐射材料,喷涂厚度0.3mm,在室温干燥后,按台车式隧道窑的烘干程序升温,最高温度达到1200℃保温2h,得到具有红外辐射功能的台车式隧道窑,红外辐射台车式隧道窑在工作温度25℃-900℃范围内全波长积分发射率大于0.90;
48.红外辐射材料的制备方法为:将100份ceo2、10份cepo4和0.83份分散剂byk190加入55份水中高速分散,粉水比为2:1,分散剂的量为浆料总量的5
‰
,分散转速为1000r/min,分散完全后的浆料转移至砂磨机中砂磨,磨至粒径d
(90)
≤5.0μm;再将经过砂磨后的浆料转移至分散机中,加入200份固含量为50%al(h2po4)3溶液,制得红外辐射涂料;
49.(2)氧化铈制备:红外辐射台车式隧道窑高温区温度控制在900℃,装有碳酸铈的匣钵摆放到台车上,然后进入到红外辐射台车式隧道窑中,通过预热区、高温区和冷却区,得到的氧化铈粉体中稀土总量reo大于99%,灼减小于0.5%;
50.(3)节能对比分析:红外辐射台车式隧道窑与常规氧化铈台车式隧道窑相比,在台车式隧道窑高温区温度为900℃下,通过高温区时间从7h降低到5.5h,时间缩短21.43%,红外辐射台车式隧道窑灼烧氧化铈产量提高27.27%,生产每吨氧化铈节约能源21.43%。
51.实施例4
52.一种氧化铈隧道窑节能方法,该方法包括如下步骤:
53.(1)红外辐射台车式隧道窑:在72米长的台车式隧道窑中,将台车式隧道窑内腔耐火材料表面清除耐火泥和灰尘,将窑内腔表面喷涂红外辐射材料,喷涂厚度0.3mm,在室温干燥后,按台车式隧道窑的烘干程序升温,最高温度达到1200℃保温2h,得到具有红外辐射功能的台车式隧道窑,红外辐射台车式隧道窑在工作温度25℃-900℃范围内全波长积分发射率大于0.90;
54.红外辐射材料的制备方法为:200份ceo2、20份cepo4和0.33份分散剂byk190加入110份水中高速分散,粉水比为1:1,分散剂的量为浆料总量的1
‰
,分散转速为1000r/min,分散完全后的浆料转移至砂磨机中砂磨,磨至粒径d
(90)
≤10.0μm。再将经过砂磨后的浆料转移至分散机中,加入200份固含量为50%al(h2po4)3溶液,制得红外辐射涂料;
55.(2)氧化铈制备:红外辐射台车式隧道窑高温区温度控制在880℃,装有碳酸铈的匣钵摆放到台车上,然后进入到红外辐射台车式隧道窑中,通过预热区、高温区和冷却区,得到的氧化铈粉体中稀土总量reo大于99%,灼减小于0.5%;
56.(3)节能对比分析:红外辐射台车式隧道窑与常规氧化铈台车式隧道窑相比,在台车式隧道窑高温区温度为880℃下,通过高温区时间从9h降低到7h,时间缩短22.22%,红外辐射台车式隧道窑灼烧氧化铈产量提高28.57%,生产每吨氧化铈节约能源22.22%。
57.对比例1
58.在上述实施例1的基础上,步骤(1)中红外辐射材料的制备方法为:110份ceo2和0.22份分散剂byk190加入110份水中高速分散,粉水比为1:1,分散剂的量为浆料总量的1
‰
,分散转速为1000r/min,分散完全后的浆料转移至砂磨机中砂磨,磨至粒径d
(90)
≤10.0μm;再将经过砂磨后的浆料转移至分散机中,加入粘结剂200份al(h2po4)3溶液,制得红外辐射涂料;
59.得到具有红外辐射功能的辊道窑,红外辐射辊道窑在工作温度25℃-900℃范围内全波长积分发射率大于0.86;
60.(2)氧化铈制备:红外辐射辊道窑高温区温度控制在850℃,装有碳酸铈的匣钵进入到红外辐射辊道窑中,通过预热区、高温区和冷却区,得到的氧化铈粉体中稀土总量reo大于99%,灼减小于0.5%;
61.(3)节能对比分析:红外辐射辊道窑与常规氧化铈辊道窑相比,在辊道窑高温区温度为850℃下,通过高温区时间从4h降低到3.5h,时间缩短了12.5%,红外辐射辊道窑灼烧氧化铈产量提高14.29%,生产每吨氧化铈节约能源12.5%。
62.对比例2
63.在上述实施例1的基础上,步骤(1)中红外辐射材料的制备方法为:110份cepo4和0.22份分散剂byk190加入110份水中高速分散,粉水比为1:1,分散剂的量为浆料总量的1
‰
,分散转速为1000r/min,分散完全后的浆料转移至砂磨机中砂磨,磨至粒径d
(90)
≤10.0μm;再将经过砂磨后的浆料转移至分散机中,加入200份al(h2po4)3溶液,制得红外辐射涂料;
64.得到具有红外辐射功能的辊道窑,红外辐射辊道窑在工作温度25℃-900℃范围内全波长积分发射率大于0.87;
65.(2)氧化铈制备:红外辐射辊道窑高温区温度控制在850℃,装有碳酸铈的匣钵进入到红外辐射辊道窑中,通过预热区、高温区和冷却区,得到的氧化铈粉体中稀土总量reo大于99%,灼减小于0.5%;
66.(3)节能对比分析:红外辐射辊道窑与常规氧化铈辊道窑相比,在辊道窑高温区温度为850℃下,通过高温区时间从4h降低到3.4h,时间缩短了15.0%,红外辐射辊道窑灼烧氧化铈产量提高17.65%,生产每吨氧化铈节约能源15.0%。
67.对比例3
68.在上述实施例1的基础上,步骤(1)中红外辐射材料的制备方法为:100份ceo2、10份cepo4和0.22份分散剂byk190加入110份水中高速分散,粉水比为1:1,分散剂的量为浆料总量的1
‰
,分散转速为1000r/min,分散完全后的浆料转移至砂磨机中砂磨,磨至粒径d
(90)
≤10.0μm;再将经过砂磨后的浆料转移至分散机中,加入300份al(h2po4)3溶液,制得红外辐
射涂料;
69.得到具有红外辐射功能的辊道窑,红外辐射辊道窑在工作温度25℃-900℃范围内全波长积分发射率大于0.85;
70.(2)氧化铈制备:红外辐射辊道窑高温区温度控制在850℃,装有碳酸铈的匣钵进入到红外辐射辊道窑中,通过预热区、高温区和冷却区,得到的氧化铈粉体中稀土总量reo大于99%,灼减小于0.5%;
71.(3)节能对比分析:红外辐射辊道窑与常规氧化铈辊道窑相比,在辊道窑高温区温度为850℃下,通过高温区时间从4h降低到3.6h,时间缩短了10.0%,红外辐射辊道窑灼烧氧化铈产量提高11.11%,生产每吨氧化铈节约能源10.0%。
72.对比例4
73.在上述实施例1的基础上,步骤(1)中红外辐射材料的制备方法为:100份ceo2、10份cepo4和0.22份分散剂byk190加入110份水中高速分散,粉水比为1:1,分散剂的量为浆料总量的1
‰
,分散转速为1000r/min,分散完全后的浆料转移至砂磨机中砂磨,磨至粒径d
(90)
≤10.0μm;再将经过砂磨后的浆料转移至分散机中,加入200份质量浓度30%的硅溶胶溶液,制得红外辐射涂料;
74.得到具有红外辐射功能的辊道窑,红外辐射辊道窑在工作温度25℃-900℃范围内全波长积分发射率大于0.86;
75.(2)氧化铈制备:红外辐射辊道窑高温区温度控制在850℃,装有碳酸铈的匣钵进入到红外辐射辊道窑中,通过预热区、高温区和冷却区,得到的氧化铈粉体中稀土总量reo大于99%,灼减小于0.5%;
76.(3)节能对比分析:红外辐射辊道窑与常规氧化铈辊道窑相比,在辊道窑高温区温度为850℃下,通过高温区时间从4h降低到3.5h,时间缩短了12.5%,红外辐射辊道窑灼烧氧化铈产量提高14.29%,生产每吨氧化铈节约能源12.5%。
77.对比例5
78.在上述实施例1的基础上,步骤(1)中红外辐射材料的制备方法为:90份ceo2、20份cepo4和0.22份分散剂byk190加入110份水中高速分散,粉水比为1:1,分散剂的量为浆料总量的1
‰
,分散转速为1000r/min,分散完全后的浆料转移至砂磨机中砂磨,磨至粒径d
(90)
≤10.0μm;再将经过砂磨后的浆料转移至分散机中,加入200份al(h2po4)3溶液,制得红外辐射涂料;
79.得到具有红外辐射功能的辊道窑,红外辐射辊道窑在工作温度25℃-900℃范围内全波长积分发射率大于0.86;
80.(2)氧化铈制备:红外辐射辊道窑高温区温度控制在850℃,装有碳酸铈的匣钵进入到红外辐射辊道窑中,通过预热区、高温区和冷却区,得到的氧化铈粉体中稀土总量reo大于99%,灼减小于0.5%;
81.(3)节能对比分析:红外辐射辊道窑与常规氧化铈辊道窑相比,在辊道窑高温区温度为850℃下,通过高温区时间从4h降低到3.45h,时间缩短了13.75%,红外辐射辊道窑灼烧氧化铈产量提高15.94%,生产每吨氧化铈节约能源13.75%。
82.对比例6
83.在上述实施例1的基础上,步骤(1)中红外辐射材料的制备方法为:105份ceo2、5份
cepo4和0.22份分散剂byk190加入110份水中高速分散,粉水比为1:1,分散剂的量为浆料总量的1
‰
,分散转速为1000r/min,分散完全后的浆料转移至砂磨机中砂磨,磨至粒径d
(90)
≤10.0μm;再将经过砂磨后的浆料转移至分散机中,加入200份al(h2po4)3溶液,制得红外辐射涂料;
84.得到具有红外辐射功能的辊道窑,红外辐射辊道窑在工作温度25℃-900℃范围内全波长积分发射率大于0.86;
85.(2)氧化铈制备:红外辐射辊道窑高温区温度控制在850℃,装有碳酸铈的匣钵进入到红外辐射辊道窑中,通过预热区、高温区和冷却区,得到的氧化铈粉体中稀土总量reo大于99%,灼减小于0.5%;
86.(3)节能对比分析:红外辐射辊道窑与常规氧化铈辊道窑相比,在辊道窑高温区温度为850℃下,通过高温区时间从4h降低到3.55h,时间缩短了11.25%,红外辐射辊道窑灼烧氧化铈产量提高12.68%,生产每吨氧化铈节约能源11.25%。
87.表1实施例1-4的结果比较
[0088][0089]
表2对比例1-6的结果比较
[0090]
[0091][0092]
通过上述比较可以发现,采用本发明的方法可以显著实现氧化铈隧道窑节能,通过高温段时间缩短20%以上,氧化铈产量提高25%以上,生产每吨氧化铈节约能源20%以上。本发明提出的红外辐射材料配方为最佳配方,改变ceo2、cepo4或者粘结剂的比例和种类,氧化铈通过窑炉高温段的时间缩短<20%,氧化铈产量提高<25%。这是因为,在本发明提出的材料配方中,al(h2po4)3在高温下与合适配比的ceo2、cepo4以及基材反应,生成具有致密陶瓷相的、高发射率釉层,提高氧化铈煅烧的反应效率,降低反应时间,实现隧道窑节能。以上所述仅为本发明的较佳实施例而已,并不用以限制本发明,凡在本发明的精神和原则之内,所作的任何修改、等同替换、改进等,均应包含在本发明的保护范围之内。