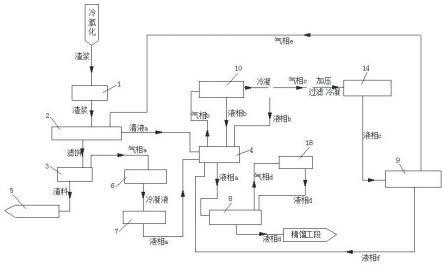
1.本发明涉及多晶硅生产中渣浆处理技术领域,具体涉及一种多晶硅生产渣浆处理工艺。
背景技术:2.目前,在多晶硅生产的冷氢化工段中,冷氢化工段所产渣浆料(主要包括氯硅烷与硅粉)先通过简易过滤器过滤后,清液送至精馏工段进行沉降处理,而过滤器得到的干渣定期开环外排。再经沉降后得到的上清液送至高沸塔进行进一步处理,沉降处理后底部得到的渣料再进行水解处理,水解处理后的饱和污水送至下游公辅工段进一步处理。
3.采用前述传统渣浆处理工艺存在以下问题:1、由于冷氢化工段产生渣浆料中硅粉夹带量较大,硅粉含量可达到2%及以上,导致传统渣浆处理系统中的送料系统环节存在的堵塞、回收率低的问题;2、传统渣浆处理系统中,因渣浆外送量较大,固体含量较高,每日需四人配合清理5-7个篮式过滤器,单个过滤器每次清理时长约1-2小时,清理高沸物及硅粉300-500kg/天,且现场频繁开环,对地面及设备污染较大,同时人员工作负荷较高,高沸物处理还存在一定安全风险、人员工作量大;3、传统渣浆处理系统中,因渣浆料中组分的本身特性原因,对其处理中使用的过滤器的过滤精度有一定要求,精度过高渣料外送困难且过滤器清理频次高,精度过低无法起到过滤作用,因此,虽然安装有过滤器,但仍有一定量高沸及硅粉送至下游工段,堵塞下游工段过滤器及高沸塔,影响下游工段生产运行,且导致下游工段生产不平稳从而影响公司大系统平衡的问题。
4.当前,于2020年4月3日公开了一件申请号为“cn201911199865.4”,名称为“一种多晶硅渣浆无水化处理工艺”的发明专利申请,公开了一种多晶硅渣浆无水化处理工艺,包括以下步骤:(1)来自上游的多晶硅渣浆经固液气分离,得到液体和气体a及固体a;液体和气体a处理后收集得到液体a;(2)固体a经蒸汽加热搅拌,得到干燥后的固体产物以及以气体方式存在的四氯化硅和部分三氯氢硅;以气体方式存在的四氯化硅和部分三氯氢硅经处理后收集得到液体b;(3)干燥后的固体产物经热解炉加热,得到固体废物和气态形式的高沸物;气态形式的高沸物经催化裂解得到气体b和液体c;(4)固体废物依次通过锁气罐、冷却螺旋、固体料仓排放到包装和外送单元;(5)液体a、b、c和气体b经分离后,得到四氯化硅和三氯氢硅产品以及剩余的高沸物和部分固体b。该文献中的公开了一种对多晶硅渣浆的处理工艺,该工艺中将渣浆处理废气直接对空排放,造成氯硅烷浪费的同时对环境造成污染。
技术实现要素:5.本发明的目的在于提供一种多晶硅生产渣浆处理工艺,解决现有的多晶硅生产中渣浆处理工艺中存在过滤器清理频次较多,存在安全隐患的问题;同时,突破多晶硅渣浆处理技术瓶颈的问题,提高渣浆以及高沸物的处理能力,提高渣浆中的氯硅烷回收率,降低产
品中金属杂质含量。
6.本发明通过下述技术方案实现:一种多晶硅生产渣浆处理工艺,包括以下步骤:a、收集冷氢化工段的渣浆至收集罐,并将收集罐中的物料冷却至30℃及以下,再将收集罐中的渣浆送至真空转鼓过滤机进行吸附过滤处理,得到滤饼和清液a,所述滤饼送至干燥机进行干燥处理,清液a送至缓冲罐i,暂存;b、滤饼经步骤a中干燥机干燥处理后得到渣料和气相a,渣料送至水解子系统进一步处理,气相a输送至换热器i中进一步降温处理后,得到氯硅烷冷凝液,并将氯硅烷冷凝液暂存至缓冲罐ii中;c、再将步骤b的缓冲罐ii中的氯硅烷冷凝液加压后继续输送至缓冲罐i中,所述缓冲罐i后端连接有真空泵,使缓冲罐i中的压力处于-30kpa~-70kpa,温度为15-25℃;d、再将缓冲罐i中的液相a泵送至缓冲罐iii进一步处理,将缓冲罐i中的气相b经冷凝处理后,得到的液相b返回至缓冲罐i中;得到的气相c进一步经过滤、加压、冷凝后得到的液相c,并将液相c输送至尾气冷凝罐中;e、经步骤d中的缓冲罐iii处理后得到的液相d经加压处理后的物流部分送至精馏工段,经缓冲罐iii处理后得到的气相d进一步冷凝后得到的液相e返回至缓冲罐iii中;f、经尾气冷凝罐处理后,得到的气相e送至真空转鼓过滤机进一步循环,得到的液相f送至缓冲罐ii中进一步循环。
7.进一步地,所述步骤d中,气相b经换热器ii冷凝后,温度控制为5-15℃,压力控制为-40~-60kpa,得到的液相返回至缓冲罐i中,得到的气相再经真空泵后,得到气相c和液相,液相返回至缓冲罐i中。
8.进一步地,所述步骤d中,将气相c送至空气过滤器进行过滤后,再经泵i真空度抽至-40~-65kpa后,继续输送至换热器iii进一步冷凝,得到液相c。
9.进一步地,所述空气过滤器为t型过滤器,滤芯为金属烧结滤芯,过滤精度为50-80目。
10.进一步地,步骤a中,所述收集罐采用具有冷却水夹套的收集罐,使收集罐向真空转鼓过滤机输送的物流不超过30℃。
11.进一步地,所述真空转鼓过滤机中的滤布为两层及以上层数的滤布,每层滤布的孔隙大小不同,外层滤布规格型号为透气性为250-300l
·
m2/s,内层滤布规格型号为透气性为150-200 l
·
m2/s。
12.进一步地,步骤b中,所述水解子系统包括渣料储罐、水解池和淋洗塔i,渣料储罐底部通过下料管线连接水解池,下料管线上设有调节阀i,水解池连接有补水管线,水解池内设有用于检测水解池内温度的温度传感器和用于检测水解池内压力的压力传感器,渣料经水解池处理后产生的气体a输送至淋洗塔i进一步处理,处理后得到的气体b经放空管线外排,放空管线上设有调节阀ii,调节阀ii与压力传感器控制连接,温度传感器分别与调节阀i、下料管线上设有的调节阀iii控制连接。
13.进一步地,所述缓冲罐i、缓冲罐ii、缓冲罐iii的气相出口均连接有尾气深冷子系统,尾气深冷子系统包括淋洗塔ii,所述淋洗塔ii采用氯硅烷清液作为淋洗液,淋洗液从淋洗塔ii的底部输送至换热器iii冷却至-20~-35℃后,送回至淋洗塔ii内用于淋洗进入尾气
深冷子系统的气体,经淋洗液洗涤、冷却后得到的液相氯硅烷进行回收利用,得到的不凝气送至废气处理系统进一步处理。
14.进一步地,所述真空转鼓过滤机采用涂覆有吸附层的滤网对物流中的硅粉及高沸物进行拦截,所述吸附层采用氯硅烷与硅藻土混合而成的涂料涂覆而成,涂料厚度为80-100mm。
15.进一步地,所述换热器i、换热器ii、换热器iii连接的下液管线为直管,所述干燥机下料管线弯头内侧涂有耐磨层。
16.本发明与现有技术相比,具有以下优点及有益效果:一、本发明中,采用本工艺相比原渣浆工艺,渣浆处理(转鼓过滤机)技术在现有工艺上进一步优化,突破多晶硅生产中渣浆处理工艺中-高沸物处理工艺的瓶颈,提高渣浆以及高沸物的处理能力,解决堵塞问题,并减轻后系统渣浆处理负荷。
17.二、本发明中,与现有技术相比,采用新工艺后可减少过滤器清理频次,原流程清理过滤器 6个/天,每个过滤器需四人配合清理,采用新工艺后,6个月清理1个过滤器,因此,可降低开环导致的安全风险及环境污染问题,明显降低水解风险且减少人员工作量。
18.三、本发明中,采用本工艺后,减少进入水解子系统的渣料,提高渣浆中的氯硅烷回收率,回收率可达96%以上,减轻下游渣浆处理负荷,回收部分氯硅烷以平衡原料系统,减少外购tcs投入,同时减轻废水处理系统的负荷,能有效减少氯硅烷的水解量,降低污水中氯离子浓度。同时采用本转鼓工艺后,明显降低回收利用的氯硅烷中的金属杂质含量,使产品金属杂质由原来的10-20万ppbm降低到2万ppbm内,提高产品质量。
19.四、本发明中,由于尾气中氯硅烷含量较高,采用本工艺后将原放空尾气通过深冷系统回收利用,减少对空排放降低环保压力的同时,将尾气中氯硅烷进行回收利用,增加项目收益。
20.五、本发明中,采用本工艺后,转鼓出口带出的高沸及部分未过滤杂质通过过滤器及换热器降温过滤,真空泵入口的杂质带入量降低,与现有技术对比,延长转鼓运行时间。
21.六、本发明中,所述真空转鼓过滤机中的滤布为两层及以上层数的滤布,每层滤布的孔隙大小不同,外层滤布规格型号为透气性为250-300l
·
m2/s,内层滤布规格型号为透气性为150-200 l
·
m2/s,提高真空转鼓过滤机的过滤、吸附效果。
22.七、本发明中,原渣浆工艺中,渣料经干燥机处理后暂存于渣料储罐中,需经工作人员手动外排。手动外排的处理步骤大致为:先需要利用惰性气体进行置换后,再现场开环,开环过程中会对现场环境造成一定污染,同时外排后的渣料需要人员转送至水解池进行手动水解,而水解反应较为剧烈且效率低下,存在一定的安全风险。而本方案中的水解子系统为全封闭式,可以有效的解决上述问题。渣料经渣料储罐后直接进入水解池进行水解,同时水解后尾气经过淋洗塔i淋洗处理后放空,水解池单独连接有补水管线进行补水、外排口进行排渣处理,防止设备发生堵塞及水质饱和。同时,水解池内设有用于检测水解池内温度的温度传感器和用于检测水解池内压力的压力传感器,温度传感器、压力传感器分别与相应阀门控制连接,联锁调节相应阀门的开闭或开度,防止水解池超温、超压。
23.八、本发明中,原渣浆处理工艺中的转鼓预涂、渣料储罐需要定期向淋洗系统排放尾气,因淋洗系统压力较高,真空转鼓过滤机正常运行时压力为20-30kpa,转鼓尾气无法正常进入淋洗系统且导致憋压,憋压状态影响真空转鼓过滤机正常运行。在前处理工艺中,转
鼓尾气放空至淋洗塔,利用液相氯硅烷洗涤气体,便于回收气相中夹带的氯硅烷,但淋洗塔需同时接收压缩机氢封、氮封等放空气,负荷较大,导致淋洗塔频繁出现塔顶放空冒白烟、喷水等现象,影响周边环境。本工艺中新增尾气深冷子系统进行处理回收后,将尾气中的氯硅烷由气相凝为液相进行回收,之后将得到的不凝气再送至下游废气压缩机进行回收利用,减少环境污染,降低水系统负荷,回收尾气。
24.九、本发明中,所述真空转鼓过滤机采用涂覆有吸附层的滤网对物流中的硅粉及高沸物进行拦截,所述吸附层采用氯硅烷与硅藻土混合而成的涂料涂覆而成,涂料厚度为80-100mm。均为了较高效地拦截物流中的硅粉及高沸物。
25.十、本发明中,所述换热器i、换热器ii、换热器iii连接的下液管线为直管,防止出现u型管因静压差过大易造成液封下液困难等问题,下液管线管径优选议dn50-dn150管径的管道,由于物流中夹带有硅粉等小颗粒,在高温且流速较大的条件下,对管线弯头等结构冲刷效果较明显,相应结构的磨损较严重。本方案中的干燥机下料管线弯头内侧涂有碳化硅或氮化硅的耐磨层,可解决前述问题,增加相应结构组件、设备的使用寿命。
附图说明
26.图1为本发明的工艺流程图。
27.图2是另一种实施方式的示意图。
28.图3是尾气深冷工艺的示意图。
29.图4是水解子系统的示意图。
30.其中,1、收集罐;2、真空转鼓过滤机;3、干燥机;4、缓冲罐i;5、水解子系统;6、换热器i;7、缓冲罐ii;8、缓冲罐iii;9、尾气冷凝罐;10、换热器ii;11、真空泵;12、空气过滤器;13、泵i;14、换热器iii;15、温度传感器;16、压力传感器;17、尾气深冷子系统;18、换热器iv;5.1、渣料储罐;5.2、水解池;5.3、淋洗塔i;5.4、下料管线;5.5、调节阀i;5.6、补水管线;5.7、放空管线;5.8、调节阀ii;17.1、淋洗塔ii;17.2、换热器v;17.3、泵ii;17.4、进料管。
具体实施方式
31.下面结合实施例对本发明作进一步地详细说明,但本发明的实施方式不限于此。
32.实施例1本实施例为最基本的实施方式,属于多晶硅生产中的渣浆处理技术领域,参考图1,一种多晶硅生产渣浆处理工艺,包括以下步骤:a、收集冷氢化工段的渣浆至收集罐1,并将收集罐1中的物料冷却至30℃及以下,再将收集罐1中的渣浆送至真空转鼓过滤机2进行吸附过滤处理,得到滤饼和清液a,所述滤饼送至干燥机3进行干燥处理,清液a送至缓冲罐i4,暂存。
33.本实施例中,由于将从冷氢化工段收集的渣浆温度一般大于40℃,其中的金属氯化物一般呈气相混在氯硅烷气相中,传统技术中一般直接将该部分渣浆送至真空转鼓过滤机2中进行处理。混有金属氯化物的物流进入真空转鼓过滤机2内部,在设备的低压、低温状态下,金属氯化物又被冷却成固态,且聚集成大颗粒,由于真空转鼓过滤机2内的滤布孔隙非常细,导致这部分颗粒粘附在滤布上,从而导致设备易故障,需要频繁开环清理真空转鼓过滤机2的过滤机构(滤布等),且这使得金属氯化物又进入后端管线中,导致后期回收的氯
硅烷中的金属杂质含量较高的问题。采用本方案后,再将收集罐1中的物料冷却至30℃及以下,使得金属氯化物冷却、聚集成大颗粒,经真空转鼓过滤机2处理后,大部分金属氯化物被截留形成滤饼,进入后端的渣料处理工段中。明显减少真空转鼓过滤机2的清理次数,延长设备连续使用时间,后端回收的氯硅烷中的金属杂质含量也显著减少。
34.b、滤饼经步骤a中干燥机3干燥处理后得到渣料和气相a,渣料送至水解子系统5进一步处理,气相a输送至换热器i6中进一步降温处理后,温度控制为5-15℃,得到氯硅烷冷凝液,并将氯硅烷冷凝液暂存至缓冲罐ii7中;c、再将步骤b的缓冲罐ii7中的氯硅烷冷凝液加压后继续输送至缓冲罐i4中,所述缓冲罐i4后端连接有真空泵11,使缓冲罐i4中的压力处于-30kpa~-70kpa,温度控制为15-25℃;d、再将缓冲罐i4中的液相a泵送至缓冲罐iii8进一步处理,将缓冲罐i4中的气相b经冷凝处理后,得到的液相b返回至缓冲罐i4中;得到的气相c进一步经过滤、加压、冷凝后得到的液相c,并将液相c输送至尾气冷凝罐9中;e、经步骤d中的缓冲罐iii8处理后得到的液相d经加压处理后的物流部分送至精馏工段,经缓冲罐iii8处理后得到的气相d进一步冷凝后得到的液相e返回至缓冲罐iii8中;f、经尾气冷凝罐9处理后,得到的气相e送至真空转鼓过滤机2进一步循环,得到的液相f送至缓冲罐ii7中进一步循环。
35.实施例2本实施例以本公司一条多晶硅生产渣浆处理线为例,进一步说明本方案。
36.一种多晶硅生产渣浆处理工艺,属于多晶硅生产中渣浆处理技术领域,参考图2,包括以下步骤:a、收集冷氢化工段的渣浆至收集罐1,并将收集罐1中的物料冷却至30℃及以下,再将收集罐1中的渣浆送至真空转鼓过滤机2进行吸附过滤处理,得到滤饼和清液a,所述滤饼送至干燥机3进行干燥处理,清液a送至缓冲罐i4,暂存;本实施例中,所述真空转鼓过滤机2采用涂覆有吸附层的滤网对物流中的硅粉及高沸物进行拦截,所述吸附层采用氯硅烷与硅藻土质量比为9:1混合而成的涂料涂覆而成,涂料厚度为100mm。实际生产中,可根据具体情况,适当调整原料比例或更换涂料的原料。
37.本实施例中,在收集罐1的外侧设有夹套,采用7℃水夹套冷却收集罐1中的物流,保证收集罐1中的物料冷却至30℃及以下,解决了传统技术中由于进入转鼓的渣料温度过高导致渣料中的高沸物大量析出,堵塞转鼓滤布,影响真空度及渣浆料处理效果的问题。而在目前多晶硅生产行业中,几乎都忽略了转鼓前端缓冲罐中温度对工艺的影响。
38.b、滤饼经步骤a中干燥机3干燥处理后得到渣料和气相a,渣料送至水解子系统5进一步处理,气相a输送至换热器i6中进一步降温处理后,得到氯硅烷冷凝液,并将氯硅烷冷凝液暂存至缓冲罐ii7中;c、再将步骤b的缓冲罐ii7中的氯硅烷冷凝液加压后继续输送至缓冲罐i4中,所述缓冲罐i4后端连接有真空泵11,使缓冲罐i4中的压力处于-40kpa左右,温度控制为20℃,缓冲罐i4中的压力环境、温度环境与真空转鼓过滤机2中环境一致,该步骤中的缓冲罐i4中的中压力一般稳定在-30kpa~-70kpa范围内,负压高于70kpa,会导致过量硅粉与高沸物附着
滤布,堵塞滤布,同时可能造成真空转鼓过滤机2的鼓面硬化严重,刮刀运行受阻,负压低于30kpa,容易导致硅藻土吸附力较弱,鼓面涂层易脱落。
39.d、再将缓冲罐i4中的液相a泵送至缓冲罐iii8进一步处理,将缓冲罐i4中的气相b经换热器ii10冷凝处理后,控制物流温度为10℃左右,压力为-40 kpa,得到的液相b返回至缓冲罐i4中;再经真空泵11后,得到的液相也返回至缓冲罐i4中,经真空泵11后仍为气态的气相c进一步经空气过滤器12进行过滤,再经泵i13进行加压,然后经换热器iii14,冷凝后得到的液相c,并将液相c输送至尾气冷凝罐9中。
40.本实施例中,气相b经换热器ii10冷凝处理后,控制物流温度为5-15℃为宜,压力为-40~-65 kpa为宜。
41.本实施例中,所述空气过滤器12为t型过滤器,滤芯为金属烧结滤芯,过滤精度优选为50-80目为宜,当选用过滤精度高于80目的滤芯,易出现过滤器堵塞频次较高,真空泵11与转鼓真空度压差过高,真空泵11运行负荷较大,转鼓真空度偏低的问题,当选择低于50目的滤芯,由于孔径较大的原因,又会导致高沸物及其他物质无法过滤,未起到过滤作用,堵塞真空泵11,影响设备运行的问题。本方案中,为进一步考察空气过滤器12的过滤精度对过滤器过滤效果的影响,分别选用50目、60目、70目、80目的滤芯安装在空气过滤器12上,检测过滤器后方管线上物流中固体的含量,结果参考表1所示。 过滤前粒子的含量(%)过滤后物料的含量(%)过滤器连续使用时长50目1.00.62060目1.00.41570目1.00.31080目1.00.27
42.由表1可知,随着过滤器的过滤精度越高,虽过滤效果增强但会导致过滤器运行周期较短,需要频繁清理过滤器的问题;精度过低则过滤效果不佳。
43.e、经步骤d中的缓冲罐iii8处理后得到的液相d经加压处理后的物流部分送至精馏工段,经缓冲罐iii8处理后得到的气相d进一步冷凝后得到的液相e返回至缓冲罐iii8中;f、经尾气冷凝罐9处理后,得到的气相e送至真空转鼓过滤机2进一步循环,得到的液相f送至缓冲罐ii7中进一步循环。
44.进一步的,所述真空转鼓过滤机2中的滤布为两层及以上层数的滤布,每层滤布的孔隙大小不同,外层滤布规格型号为透气性为250-300l
•
m2/s,内层滤布规格型号为透气性为150-200 l
•
m2/s。本实施例中,采用本方案后,所述渣浆中的氯硅烷回收率可达到95%及以上,明显优于采用传统渣浆处理技术(传统工艺中氯硅烷的回收率为85%-90%),提高了5%以上,明显降低原料成本,减小后端的氯硅烷处理压力。
45.本实施例中,在真空泵11前增设换热器ii10,提前将气相中氯硅烷冷凝,通过真空泵11的真空罐回流至缓冲罐ii7中,防止真空泵11带液工作影响系统运行与设备寿命。同时,在真空泵11的后端加设空气过滤器12,防止由于抽真空,将真空转鼓过滤机2中的硅粉、硅藻土等颗粒代入至后端的工艺设备中,导致后端的物流中的粒子夹带率高,且影响后端的加压泵等设备的正常运行。
46.实施例3
本实施例与实施例2相比,区别在于,所述缓冲罐i4、缓冲罐ii7、缓冲罐iii8的气相出口均连接有尾气深冷子系统17,参考图3,尾气深冷子系统17包括淋洗塔ii17.1,所述淋洗塔ii17.1采用氯硅烷清液作为淋洗液,淋洗液从淋洗塔ii17.1的底部输送至换热器v17.2进行冷却至-5~-25℃后,送回至淋洗塔ii17.1内用于淋洗从进料管17.4进入尾气深冷子系统17的气体,经淋洗液洗涤、冷却后得到的液相氯硅烷进行回收利用,得到的不凝气从淋洗塔ii17.1顶部的出口送至废气处理系统进一步处理。
47.本实施中,对经各个缓冲罐(包括缓冲罐i4、缓冲罐ii7、缓冲罐iii8)处理后得到气相进行收集后,集中进行深冷处理,进一步回收这部分气相中混有的氯硅烷。即将这部分气体降温至-5~-15℃,回收液相(主要为氯硅烷),最后的不凝气(主要为氢气)再送至废气处理系统进一步处理。
48.以本公司月处理量8500吨的渣浆生产线为例,采用实施例2方案可以回收渣浆中95%的氯硅烷,采用实施例3的方案,可多回收0.5-1%的氯硅烷,可节约100-200万元/月的原料成本。与现有的渣浆处理工艺比较,可多回收10-13%的氯硅烷,相当于下游水解工段可少处理这部分,可减少水处理费用20万元/月,降低现场淋洗塔对空排放造成的安全环保压力。
49.优选的,本实施例中,所述换热器i6、换热器ii10、换热器iii14均为氟利昂换热器;所述换热器i6、换热器ii10、换热器iii14连接的下液管线为直管,因本工艺运行压力较低,若采用u型管设计,易造成液封现象导致下液困难。
50.优选的,所述干燥机3下料管线5.4弯头内侧涂有氮化硅的耐磨层,因干燥后的渣料中含有大量硅粉,下料期间对管线造成一定磨损,设计耐磨层防护。
51.实施例4本实施例是在实施例1-3的基础上进一步优化工艺,在步骤b中,参考图4,所述水解子系统5包括渣料储罐5.1、水解池5.2和淋洗塔i5.3,渣料储罐5.1底部通过下料管线5.4连接水解池5.2,下料管线5.4上设有调节阀i5.5,水解池5.2连接有补水管线5.6,水解池5.2内设有用于检测水解池5.2内温度的温度传感器15和用于检测水解池5.2内压力的压力传感器16,渣料经水解池5.2处理后产生的气体a输送至淋洗塔i5.3进一步处理,处理后得到的气体b经放空管线5.7外排,放空管线5.7上设有调节阀ii5.8,调节阀ii5.8与压力传感器16控制连接,温度传感器15分别与调节阀i5.5、下料管线5.4上设有的调节阀i5.5控制连接。
52.本实施例中,所述渣料储罐5.1收集从干燥机3中的渣料,通过下料管线5.4输送至水解池5.2中,进行水解。
53.原渣浆处理系统需每天人工外排约1-2吨渣料,送至辅助工段进行人工水解处理,现场设备及地面污染较大,设备维保费用增加50万元/年,人员工作量增加4500工时/年,通过本水解系统处理后,前述部分成本通过本工艺可全部节省。
54.以上所述,仅是本发明的较佳实施例,并非对本发明做任何形式上的限制,凡是依据本发明的技术实质对以上实施例所作的任何简单修改、等同变化,均落入本发明的保护范围之内。