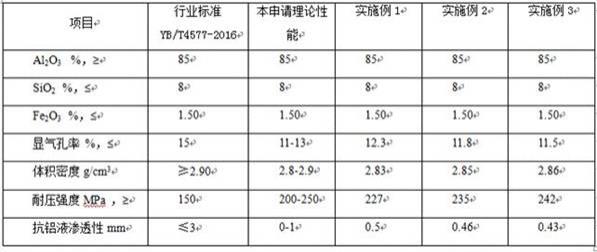
1.本发明涉及熔铝炉耐火砖技术领域,尤其是涉及一种抗铝液渗透耐火砖及其制备方法。
背景技术:2.熔铝炉用砖需要耐火砖具备优秀抗铝液渗透性能,铝液渗透进入耐火材料中,金属铝及其他金属元素与耐火砖中各组分会发生反应,严重破坏耐火材料结构,影响其使用寿命增加生产成本。
3.目前,熔铝炉使用的耐火砖多为加入硫酸钡作为结合剂,提高抗铝液渗透性能,但在使用温度高于1150℃时,硫酸钡就会分解,耐火砖的抗铝液渗透性能会大幅下降。由于冶金行业生产需要,冶炼原料中加入了废铝,冶炼温度需要高于1150℃才能达到生产要求,所以现在急需一种使用温度在1150℃以上并具有优秀抗铝液渗透性能的耐火砖。
技术实现要素:4.为了克服背景技术中的不足,本发明公开了一种抗铝液渗透耐火砖。
5.为实现上述发明目的,本发明采用如下技术方案:一种抗铝液渗透耐火砖,按质量份含以下组分:3-1mm烧结高铝料30-40份、1-0mm烧结高铝料15-25份、氧化铝微粉20-30份、黏土5-10份、镁铝络合物结合剂2-5份、氮化硼2-5份。
6.进一步地,所述烧结高铝料al2o3含量要大于88%,fe2o3含量小于1.5%,体积密度大于3.25g/cm3,吸水率要小于2.5%。
7.进一步地,所述氧化铝微粉为百分比含量≥99%,粒度为500目。
8.进一步地,所述黏土为180-200目的细粉。
9.进一步地,制备方法如下,配料:按3-1mm烧结高铝料30-40份、1-0mm烧结高铝料15-25份、氧化铝微粉20-30份、黏土5-10份、镁铝络合物结合剂2-5份、氮化硼2-5份进行配料,先加入3-1mm、1-0mm烧结高铝料进行搅拌,加入3-6份水搅拌3-5分钟,再加入镁铝络合物结合剂、氮化硼搅拌3-5分钟,最后加入氧化铝微粉、黏土搅拌5-8分钟;成型:将混合后的物料加入模具内压制成型;干燥:将成型后的半成品进行干燥处理;烧制:将干燥处理后的半成品经热处理,得到抗铝液渗透耐火砖。
10.进一步地,所述热处理为将干燥后的砖坯进行热处理,升温温度室温-100℃,加热时间24h,保持温度110
±
10℃,保持时间5h,升温温度110-600℃,升温时间24h,保持温度600
±
10℃,保持时间24h。
11.进一步地,所述成型为使用1000t摩擦压力机压制成型。
12.进一步地,所述干燥处理为升温温度室温-50℃,升温时间10h,保持温度50
±
5℃,
保持时间5h,升温温度50-70℃,升温时间4h,保持温度70℃,保持时间5h,升温温度70-110℃,升温时间8h,保持温度110℃,保持时间10h。
13.由于采用如上所述的技术方案,本发明具有如下有益效果:1、本发明通过镁铝络合物结合剂与氮化硼结合使用,通过合适的比例增加泥料的润滑性,使泥料塑性性能提升,易于成型,克服泥料的粘板现象,有效降低半成品内裂废品率,成型后半成品强度提高一倍,即使不干燥也会保持强度,干燥后强度上升,有效提升产品合格率。
14.2、本发明具备1150℃以上的使用温度,满足了目前铝冶炼行业的需要,解决了实际生产问题,降低了其更换耐火砖频率,节省了客户的使用成本。
15.3、本发明通过降低热处理温度,大幅降低能耗,复合绿色低碳环保的生产要求,在保证产品性能的同时,降低了自身生产成本,较传统1200℃烧制每吨砖可节约500-700元烧制成本。
16.4、本发明首次在铝硅系耐火砖中搭配使用镁铝络合物与氮化硼,通过特定搭配使用镁铝络合物与氮化硼比例与加入量的范围,保证产品高温性能的同时,大幅提升了抗铝液渗透性能。结合剂的加入时,先用水润湿颗粒表面,然后加入镁铝络合物使其产生粘合性,最后加入氮化硼,使其骨料产生塑性,易于成型。在热处理过程中,会生成陶瓷结构,有效促进骨料和基质的结合,增强了成型过程致密性,减少了贯通气孔,减少了气孔数量,同时减小了气孔孔径,这样减少了铝液渗透通道,阻塞铝液的渗透。通过表1可以看出本发明耐压强度,气孔率均优于行业标准,同时表2显示出本发明在铝液渗透实验中物质变化小,抗铝液渗透能力强,传统抗渗透耐火砖铝液铝液渗透深度在1-3mm,本发明铝液渗透厚度仅在0-1mm,因此本发明具备优秀的抗铝液渗透性能。
具体实施方式
17.所述的一种抗铝液渗透耐火砖及其制备方法,按质量份含以下组分:3-1mm烧结高铝料30-40份、1-0mm烧结高铝料15-25份、氧化铝微粉20-30份、黏土5-10份、镁铝络合物结合剂2-5份、氮化硼2-5份。制备方法如下,配料:按质量份3-1mm烧结高铝料30-40份、1-0mm烧结高铝料15-25份、氧化铝微粉20-30份、黏土5-10份、镁铝络合物结合剂2-5份、氮化硼2-5份进行配料,先加入3-1mm、1-0mm烧结高铝料进行搅拌,加入3-6份水搅拌3-5分钟,再加入镁铝络合物结合剂、氮化硼搅拌3-5分钟,最后加入氧化铝微粉、黏土搅拌5-8分钟;成型:将混合后的物料加入模具内使用1000t摩擦压力机压制成型;干燥:将成型后的半成品进行干燥处理升温温度室温-50℃,升温时间10h,保持温度50
±
5℃,保持时间5h,升温温度50-70℃,升温时间4h,保持温度70℃,保持时间5h,升温温度70-110℃,升温时间8h,保持温度110℃,保持时间10h;烧制:将干燥处理后的半成品进行热处理,升温温度室温-100℃,加热时间24h,保持温度110
±
10℃,保持时间5h,升温温度110-600℃,升温时间24h,保持温度600
±
10℃,保持时间24h,得到抗铝液渗透耐火砖。
18.实施例1
配料:按质量份3-1mm烧结高铝料40份、1-0mm烧结高铝料25份、氧化铝微粉30份、黏土10份、镁铝络合物结合剂5份、氮化硼5份进行配料,先加入3-1mm、1-0mm烧结高铝料进行搅拌,加入6份水搅拌5分钟,再加入镁铝络合物结合剂、氮化硼搅拌5分钟,最后加入氧化铝微粉、黏土搅拌8分钟;成型:将混合后的物料加入模具内压制成型;干燥:将成型后的半成品进行干燥,在升温温度室温-50℃,升温时间10h,保持温度50
±
5℃,保持时间5h,升温温度50-70℃,升温时间4h,保持温度70℃,保持时间5h,升温温度70-110℃,升温时间8h,保持温度110℃,保持时间10h;烧制:将干燥处理后的半成品进行热处理,升温温度室温-100℃,加热时间24h,保持温度110
±
10℃,保持时间5h,升温温度110-600℃,升温时间24h,保持温度600
±
10℃,保持时间24h,得到抗铝液渗透耐火砖。
19.实施例2配料:按质量份3-1mm烧结高铝料30份、1-0mm烧结高铝料15份、氧化铝微粉20份、黏土5份、镁铝络合物结合剂2.5份、氮化硼2.5份进行配料,先加入3-1mm、1-0mm烧结高铝料进行搅拌,加入3份水搅拌3分钟,再加入镁铝络合物结合剂、氮化硼搅拌3分钟,最后加入氧化铝微粉、黏土搅拌5分钟;成型:将混合后的物料加入模具内压制成型;干燥:将成型后的半成品进行干燥,升温温度室温-50℃,升温时间10h,保持温度50
±
5℃,保持时间5h,升温温度50-70℃,升温时间4h,保持温度70℃,保持时间5h,升温温度70-110℃,升温时间8h,保持温度110℃,保持时间10h。;烧制:将干燥处理后的半成品进行热处理,升温温度室温-100℃,加热时间24h,保持温度110
±
10℃,保持时间5h,升温温度110-600℃,升温时间24h,保持温度600
±
10℃,保持时间24h,得到抗铝液渗透耐火砖。
20.实施例3配料:按质量份3-1mm烧结高铝料35份、1-0mm烧结高铝料20份、氧化铝微粉25份、黏土8份、镁铝络合物结合剂4份、氮化硼4份进行配料,先加入3-1mm烧结高铝料、黏土进行搅拌,先加入3-1mm、1-0mm烧结高铝料进行搅拌,加入4.5份水搅拌4分钟,再加入镁铝络合物结合剂、氮化硼搅拌4分钟,最后加入氧化铝微粉、黏土搅拌7分钟;成型:将混合后的物料加入模具内压制成型;干燥:将成型后的半成品进行干燥,升温温度室温-50℃,升温时间10h,保持温度50
±
5℃,保持时间5h,升温温度50-70℃,升温时间4h,保持温度70℃,保持时间5h,升温温度70-110℃,升温时间8h,保持温度110℃,保持时间10h。;烧制:将干燥处理后的半成品进行热处理,升温温度室温-100℃,加热时间24h,保持温度110
±
10℃,保持时间5h,升温温度110-600℃,升温时间24h,保持温度600
±
10℃,保持时间24h,得到抗铝液渗透耐火砖。
21.以上实施例1-3抗铝液渗透耐火砖性能检测结果如下表1-2所示:
表1表2本发明未详述部分为现有技术,对于本领域技术人员而言,显然本发明不限于上述示范性实施例的细节,而且在不背离本发明的精神或基本特征的情况下,能够以其他的具体形式实现本发明;因此,无论从哪一点来看,均应将实施例看作是示范性的,而且是非限制性的,本发明的范围由所附权利要求而不是上述说明限定,因此旨在将落在权利要求的等同要件的含义和范围内的所有变化囊括在本发明内,不应将权利要求中的任何标记视为限制所涉及的权利要求。