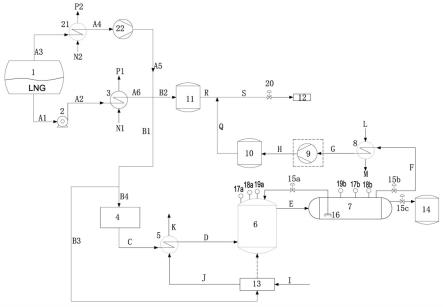
1.本发明涉及船舶工业装备体系技术领域,具体为一种催化热裂解近海设施及船舶短流程制氢方法、系统及其系统实现方法。
背景技术:2.气候恶化是一种危及人类生存的全球现象,目前世界各主要国家和地区与大量国际组织正在致力于全球范围内减少温室气体排放的相关工作。其中国际海事组织(imo)2020年第四次温室气体研究报告称,2018年全球航运能源需求接近11埃焦耳(ej)、导致约10亿吨二氧化碳(co2)排放到大气中。这导致国际海事组织对船舶领域、海洋工业领域的减排法规的升级制定。
3.目前化石能源提供了船舶与海洋工业最终能源需求的~99%。根据国际海事组织(imo)设定的目标,到2050年,航运业温室气体年排放量将比2008年减少50%以上。除此之外,为在21世纪内逐步实现国际船舶航运温室气体零排放的目标,即2030年国际航行船舶的碳排放量相较2008年的碳排量需降低至少40%,并力求2050年的碳排放强度比2008年的碳排放强度降低50%。
4.世界航运业正在努力寻找更加环保的能源解决方案,传统的船用能源为柴油、重油,用于推进和发电。液态天然气作为一种相对经济成熟的减排能源替代方案近年来被逐步广泛使用。然而,对于2030年和2050年的国际航运的碳排放新目标,仅靠lng和其他现有技术是无法满足法规要求。目前过渡性船舶新能源技术包括甲醇、氨等,而氢能被认为是终极燃料方案或进行燃烧后碳捕集。为了达到2030年比2008年基准减少40%的碳排放法规目标,现有技术最常见的方法是使用液化天然气作为燃料。然而,单靠液化天然气只能达到约20%的碳减排量。结合本专利中所描述的技术,可使得碳排放量进一步大幅减少,完全满足日趋严格的法规要求。相比于其他新型燃料,如甲醇或氨在使用中面临的成本高昂且危险性高,如果被现场作业人员吸入会对人体产生严重的毒副伤害。因此,本发明提供一种催化热裂解近海设施及船舶短流程制氢技术系统及其方法,有别于其他着重于二氧化碳的碳捕集技术,做到了直接捕集燃料中的元素碳。
技术实现要素:5.本发明的目的在于提供本发明提出了一种零碳/减碳的近海设施及船舶装置热催化分解制氢短流程技术,在经济性、实用性和安全性方面具有很强的可实现性。
6.为实现上述目的,本发明提供如下技术方案:一种催化热裂解近海设施及船舶短流程制氢方法,所述方法如下:包括前处理单元、催化热裂解反应单元、后处理单元:s1:部分和/或全部高温液态熔融催化剂通过管线输送;s2:所述前处理单元包含净化、调温、调压设施,在满足后续催化热裂解反应单元
原料要求的情况下,本单元部分取消或完全取消相关设施;s3:所述催化热裂解反应单元包含催化热裂解反应器、液态熔融催化剂或液态熔融金属或液态熔融合金、内件、衬里、出料管和燃烧器;所述催化热裂解反应单元包含催化热裂解反应器,催化热裂解反应器包含的布气元件,使进料气能均匀地进入反应器,增大进料气分散范围,增大与催化剂的接触概率;该反应器内装有催化剂,该催化剂在常温时为固相,加热到所需的反应温度下为液相,进料气穿过催化剂床层时发生反应;该反应器包含传热部件,该传热部件在反应器启动期间,为催化剂相变提供热量,在反应期间为反应提供反应热;该反应器器壁内设置组合的保温防腐防渗抗蚀结构,减少液态熔融催化剂、产品固体碳以及其他用于分离产品固体碳的化学助剂对器壁的腐蚀及磨蚀,阻止反应器内部高温催化剂的泄漏,同时将反应器外表面温度降至常规设计温度0-300℃,防止在反应器运行过程中发生人身安全事故;s4:所述后处理单元包含产品分离、调温、调压、缓冲、储存设施,在满足后续装备的前提下,本单元部分或完全取消相关设施;s5:上述s3,s4部分设施或设备具有结构设计和设施,以达到抗风浪摇摆自适应的效果,适应近海设施及船舶航运作业环境。
7.进一步地:一种制氢系统,采用上述所述一种催化热裂解近海设施及船舶短流程制氢方法,包括:燃料气流混合单元、燃料气流分解单元、燃料气流加热单元以及燃料气流燃烧单元,所述燃料气流混合单元、燃料气流分解单元、燃料气流加热单元以及燃料气流燃烧单元均通过管道实现相互连通;所述燃料气流混合单元包括:海上设施燃料储罐,所述海上设施燃料储罐下部空间连接有低温泵,所述海上设施燃料储罐上部空间连接有加热器,所述低温泵上连接有气化器并通过气化器得到燃料气a6,所述加热器上连接有燃料气压缩机并通过燃料气压缩机得到燃料气a5;燃料气a5和燃料气a6实现混合,混合后分成两股燃料气流b1和b2, 其中所述燃料气流b1的一部分燃料气流b3流经燃料气流加热单元,燃料气流b1的另一部分燃料气流b4流经燃料气流分解单元;所述燃料气流分解单元包括:原料气脱硫系统,所述原料气脱硫系统上连接有预加热器,所述预加热器上连接有分解反应器,所述分解反应器上连接有分离罐,所述分离罐通过高温阀二15b连接有冷却器,所述冷却器上连接有压缩机;其中所述分离罐通过高温阀三15c连接有固体碳收集罐14,所述分离罐通过高温泵和高温阀一15a反向连接分解反应器;所述燃料气流加热单元包括:燃烧器,所述燃烧器分别与分解反应器、预加热器及原料气脱硫系统连接;所述燃料气流燃烧单元包括:燃气缓冲罐、分解气缓冲罐和引擎系统,所述燃气缓冲罐和分解气缓冲罐均与引擎系统连接;所述燃料气流q最后通过分解气缓冲罐流出与流经燃气缓冲罐的燃料气流r混合为混合燃料s且一并通过控制阀后进入引擎系统燃烧后为引擎系统供能。
8.进一步说明的,所述加热器上设有乙二醇水入口n2和乙二醇水出口p2;所气化器
上设有乙二醇水入口n1和乙二醇水出口p1。
9.进一步说明的,所述分解反应器上连接有耐高温测液位仪表17a、耐高温测温系统18a及压力表19a;所述分离罐上连接有耐高温测液位仪表17b、耐高温测温系统18b及压力表19b。
10.进一步说明的,所述冷却器8上设有冷却水入口l和冷却水出口m。
11.具体地一种制氢实现方法,采用上述任意一项所述催化热裂解近海设施及船舶短流程制氢系统来实现,所述实现方法如下:s1:海上设施储罐用于储存碳氢化合物燃料,低温液化燃料气a1通过低温泵输送至气化器,利用乙二醇水为低温液化燃料气加热使其气化成气体,得到气化后的燃料气a6;s2:海上设施储罐上部气相空间存在气相低温燃料气a3,经加热器加热后进入燃料气压缩机,得到已经具备一定压力的燃料气a5;s3:燃料气a5与燃料气a6混合,混合后分成两股燃料气流b1和b2,其中燃料气流b1的一部分b4作为反应原料气进入后续的反应流程,另一部分燃料气流b3用于燃烧为反应器提供能量;s4:燃料气流b4经过原料气脱硫系统脱除原料气中的硫组分,得到纯净的原料气c,通过预加热器被加热,得到反应原料气d,进入分解反应器参与反应,经分解反应器后得到反应产物e,反应产物e中主要含有固体碳、氢气、未反应的原料气、少部分被夹带的催化剂,一并进入分离罐进行气、液、固三相分离,经分离得到的固体碳进入固体碳收集罐 ,气相分解气f经冷却器,利用冷却水对高温分解气进行冷却,冷却后经压缩机压缩后,输送至分解气缓冲罐中;s5:经分离罐分离出来的液相催化剂通过高温泵输送回分解反应器,仍作为反应所需的催化剂使用,部分燃料气流b3与空气i分别或混合进入燃烧器进行燃烧,燃烧产生的热量为分解反应器中的分解反应提供热能,燃烧产生的高温尾气j进入预加热器,用于加热原料气c;s6:燃料气流b2进入燃气缓冲罐,当引擎系统需要燃料时,燃气缓冲罐中流出的碳氢化合物燃料与分解气缓冲罐中流出的气体混合后作为混合燃料s且一并通过控制阀后进入引擎系统燃烧后为引擎系统供能。
12.进一步说明的,所述高温阀一15a、高温阀二15b、高温阀三15c由耐高温材料及密封结构组成,在高温300-1500℃下用于输送反应后的高温分解气,用于将高温催化剂从分离罐输送回分解反应器,用于将分离罐中分离出的高温固体碳输送至固体碳收集罐。
13.进一步说明的,所述高温泵为液下泵,由耐高温材料、流体通道结构、密封系统组成,在高温300-1500℃下用于输送液体催化剂。
14.进一步说明的,制氢实现方法中的步骤s3至步骤s6中所涉及高温液位测量是采用耐高温测液位仪表一17a和耐高温测液位仪表二17b,其原理为激光或雷达。
15.与现有技术相比,本发明的有益效果是:1、避免了储氢、储氨、储甲醇等方面的安全风险,实现了从lng到氢气的即时生产和消费。
16.2、本发明对作业人员没有毒副伤害,且没有排放限制,相较而言经济性更高;本方
案的副产品
‑‑
固体碳具有很高的商业价值,从而大大提高经济性。
17.3、本发明适用范围广:在船用发动机应用中,该技术将用作于内燃机、燃料电池、涡轮机或锅炉的部分或主要燃料或能源;在海洋船舶、平台、fpso、fsrus或海上驳船等应用场景中,该技术将用于实现零碳/低碳能源供应。
18.4、本发明采用短工艺流程,结合独创的液态催化剂及反应器设计,再加上下游的高效碳分离器,同时整体考虑抗风浪设计(具有风浪摇摆自适应性装置),投资低,空间占地小,操作周期长,检维修方便,适用于近海设施及船舶航运环境,同时兼具实用性及安全性。
19.5、本发明涉及的液态熔融金属催化剂及熔融合金催化剂相对于现有技术中的熔融盐催化剂有以下几点优势:(5.1)完全无需水或氧气参与反应,无氧元素引入,为无氧反应,本质安全;(5.2)不会因反应高温生成刺激性气体(熔盐高温会生成刺激性卤化氢副产物);(5.3)不需要结合下游工艺合成甲醇来减少燃烧提供反应热过程中的二氧化碳排放。
20.6、本发明应用后可大幅提高化石能源使用的经济性,同时大幅减少温室气体的排放,优化海洋工业整体节能减排表现,助力实现 "双碳 "目标。
附图说明
21.图1为本发明的流程示意图;图2为本发明应用实施例1流程示意图;图3为本发明应用实施例2流程示意图;图4-1为抗风浪摇摆自适应系统场景一示意图;图4-2为抗风浪摇摆自适应系统场景二示意图;图4-3为抗风浪摇摆自适应系统场景三示意图。
具体实施方式
22.下面将结合本发明实施例中的附图,对本发明实施例中的技术方案进行清楚、完整地描述,显然,所描述的实施例仅仅是本发明一部分实施例,而不是全部的实施例。基于本发明中的实施例,本领域普通技术人员在没有做出创造性劳动前提下所获得的所有其他实施例,都属于本发明保护的范围。
23.实施例方式请参阅图1,本发明提供一种技术方案:一种催化热裂解近海设施及船舶短流程制氢方法,所述方法如下:包括前处理单元、催化热裂解反应单元、后处理单元:s1:部分和/或全部高温液态熔融催化剂通过管线输送;s2:所述前处理单元包含净化、调温、调压设施,在满足后续催化热裂解反应单元原料要求的情况下,本单元部分取消或完全取消相关设施;s3:所述催化热裂解反应单元包含催化热裂解反应器、液态熔融催化剂或液态熔融金属或液态熔融合金、内件、衬里、出料管和燃烧器;所述催化热裂解反应单元包含催化热裂解反应器,催化热裂解反应器包含的布气元件,使进料气能均匀地进入反应器,增大进
料气分散范围,增大与催化剂的接触概率;该反应器内装有催化剂,该催化剂在常温时为固相,加热到所需的反应温度下为液相,进料气穿过催化剂床层时发生反应;该反应器包含传热部件,该传热部件在反应器启动期间,为催化剂相变提供热量,在反应期间为反应提供反应热;该反应器器壁内设置组合的保温防腐防渗抗蚀结构,减少液态熔融催化剂、产品固体碳以及其他用于分离产品固体碳的化学助剂对器壁的腐蚀及磨蚀,阻止反应器内部高温催化剂的泄漏,同时将反应器外表面温度降至常规设计温度0-300℃,防止在反应器运行过程中发生人身安全事故;s4:所述后处理单元包含产品分离、调温、调压、缓冲、储存设施,在满足后续装备的前提下,本单元部分或完全取消相关设施;s5:上述s3,s4部分设施或设备具有结构设计和设施,以达到抗风浪摇摆自适应的效果,适应近海设施及船舶航运作业环境。
24.一种制氢系统,包括:燃料气流混合单元、燃料气流分解单元、燃料气流加热单元以及燃料气流燃烧单元,所述燃料气流混合单元、燃料气流分解单元、燃料气流加热单元以及燃料气流燃烧单元均通过管道实现相互连通;所述燃料气流混合单元包括:海上设施燃料储罐1,所述海上设施燃料储罐1下部空间连接有低温泵2,所述海上设施燃料储罐1上部空间连接有加热器21,所述低温泵2上连接有气化器3并通过气化器3得到燃料气a6,所述加热器21上连接有燃料气压缩机22并通过燃料气压缩机22得到燃料气a5;燃料气a5和燃料气a6实现混合,混合后分成两股燃料气流b1和b2, 其中所述燃料气流b1的一部分燃料气流b3流经燃料气流加热单元,燃料气流b1的另一部分燃料气流b4流经燃料气流分解单元;所述燃料气流分解单元包括:原料气脱硫系统4,所述原料气脱硫系统4上连接有预加热器5,所述预加热器5上连接有分解反应器6,所述分解反应器6上连接有分离罐7,所述分离罐7通过高温阀二15b连接有冷却器8,所述冷却器8上连接有压缩机9;其中所述分离罐7通过高温阀三15c连接有固体碳收集罐14,所述分离罐7通过高温泵16和高温阀一15a反向连接分解反应器6;所述燃料气流加热单元包括:燃烧器13,所述燃烧器13分别与分解反应器6、预加热器5及原料气脱硫系统4连接;所述燃料气流燃烧单元包括:燃气缓冲罐11、分解气缓冲罐10和引擎系统12,所述燃气缓冲罐11和分解气缓冲罐10均与引擎系统12连接;所述燃料气流q最后通过分解气缓冲罐10流出与流经燃气缓冲罐11的燃料气流r混合为混合燃料s且一并通过控制阀20后进入引擎系统12燃烧后为引擎系统12供能。
25.一种制氢实现方法,海上设施储罐1用于储存碳氢化合物燃料,优选为lng储罐,低温液化燃料气a1通过低温泵2输送至气化器3,该气化器为一种换热器,利用乙二醇水为低温液化燃料气加热使其气化成气体,得到气化后的燃料气a6。海上设施储罐1上部气相空间存在气相低温燃料气a3,经加热器21加热后进入燃料气压缩机22,得到已经具备一定压力的燃料气a5,该气流与经气化的燃料气a6混合后分成两股燃料气流,其中燃料气流b1的一部分即b4作为反应原料气,进入后续的反应流程,另一部分b3用于燃烧,为反应器提供能量。燃料气b4经过原料气脱硫系统 4脱除原料气中的硫组分,得到纯净的原料气c,通过预
加热器5被加热,得到反应原料气d,进入分解反应器6参与反应,经分解反应器6后得到反应产物e,反应产物e中主要含有固体碳、氢气、未反应的原料气、少部分被夹带的催化剂,一并进入分离罐7进行气、液、固三相分离,经分离得到的固体碳进入固体碳收集罐 14,气相分解气f经冷却器8,利用冷却水对高温分解气进行冷却,冷却后经压缩机9(可选)压缩后,输送至分解气缓冲罐 10中。经分离罐7分离出来的液相催化剂通过高温泵16输送回分解反应器6,仍作为反应所需的催化剂使用。部分燃料气b3与空气i分别或混合进入燃烧器13进行燃烧,燃烧产生的热量为分解反应器6中的分解反应提供热能,燃烧产生的高温尾气j进入预加热器5,用于加热原料气c。一部分燃料气流b2进入燃气缓冲罐11,当引擎系统12需要燃料时,燃气缓冲罐11中流出的碳氢化合物燃料与分解气缓冲罐 10中流出的气体混合后作为混合燃料s一并通过控制阀20后进入引擎系统12燃烧后为引擎系统供能。
26.本方案主反应在分解反应器6内发生,该反应温度约300-1500℃。
27.其中,所述高温阀一15a、高温阀二15b、高温阀三15c由耐高温材料及密封结构组成,在高温300-1500℃下用于输送反应后的高温分解气,用于将高温催化剂从分离罐7输送回分解反应器6,用于将分离罐7中分离出的高温固体碳输送至固体碳收集罐14。
28.其中,所述高温泵16为液下泵,由耐高温材料、流体通道结构、密封系统组成,在高温300-1500℃下用于输送液体催化剂。
29.其中,制氢实现方法中所涉及高温液位测量是采用耐高温测液位仪表一17a和耐高温测液位仪表二17b,其原理为激光或雷达,在高温下测量分解反应器6和分离罐7内的液位高度。
30.其中,所述耐高温测温系统18a,18b,该测温系统由热点电偶、保护管等组成,通过保护管防止热电偶受到高温催化剂以及高温分解气的腐蚀,确保热电偶正常工作。
31.本发明采用短工艺流程,结合独创的液态催化剂及反应器设计,再加上下游的高效碳分离器,同时整体考虑抗风浪设计(具有风浪摇摆自适应性装置),投资低,空间占地小,操作周期长,检维修方便,适用于近海设施及船舶航运环境,同时兼具实用性及安全性。
32.此外,本方案还涉及主反应部分特殊的结构设计,该设计由特殊的耐高温(300-1500℃)耐腐蚀材料,特殊的密封系统结构设计、以及特殊的抗风浪摇摆及系统自适应结构(指在反应器内增加特殊的带孔格栅机构,以吸收液体催化剂因船体摇摆而生成的波的能量并阻止更大的波形成的机构)组成,用于高要求的海洋环境下。
33.附注:1 海上设施燃料储罐;2 低温泵;3 气化器;4 原料气脱硫系统;5 预加热器;6 分解反应器;7 分离罐;8 冷却器;9 压缩机;10 分解气缓冲罐;11 燃气缓冲罐;12 引擎系统;13 燃烧器;14 固体碳收集罐;15a,15b,15c 高温阀一、高温阀二、高温阀三;16 高温泵;17a,17b 耐高温测液位仪表一和耐高温测液位仪表二;18a,18b 耐高温测温系统;19a,19b 压力表;20 控制阀;21 加热器;22 燃料气压缩机。
34.a1 低温液化燃料气;a2 经低温泵输送至气化器的燃料气;a3 气相低温燃料气;a4 经加热的气相燃料气;a5 经压缩的燃料气;a6 经气化的燃料气;b1,b2,b3,b4 燃料气分气流;c 经脱硫的原料气;d 反应原料气;e 反应产物;f 分解气;g 经冷却的分解气;h 经压缩的分解气;i 空气;j 高温尾气;k 低温尾气;l 冷却水入口;m 冷却水出口;n1,n2 乙二醇水入口;p1,p2 乙二醇水出口;q 用于供能的分解气; r 气化后用于供能的部分燃料气;s 用于供能的混合燃料气。
35.附注:通过在反应器内增加特殊的抗风浪稳定器,以大幅削弱液体催化剂因船体摇摆而形成的液面纵向的振幅(图4-1、4-2、4-3中的中的δh代表风浪摇摆导致的液面差,δh2远小于δh1),使设备能够得以稳定安全运行。
36.抗风浪稳定器指:由特殊的耐高温(300-1500℃)耐腐蚀材料,特殊的密封系统结构设计、以及特殊的抗风浪摇摆及系统自适应结构(指在反应器内增加特殊的隔板机构,以大幅削弱液体催化剂因船体摇摆而形成的液面纵向的振幅,使设备能够得以稳定安全运行)组成,用于高要求的海洋环境下。
37.应用实施例1如图2所示本实施例用于船舶引擎供能系统船用lng储罐1a中的lng作为原料,低温a1通过低温泵2输送至气化器3,该气化器为一种换热器,利用乙二醇水为低温液化燃料气加热使使其气化成气体,得到气化后的燃料气a6。船用lng储罐1a上部空间存在气相低温燃料气a3,经加热器21加热后进入燃料气压缩机22的入口,经压缩后得到已经具备一定压力的燃料气a5,该气流与经气化的燃料气a6混合后作为燃料气b1,进入后续的反应流程。燃料气b4经过原料气脱硫系统 4脱除原料气中的硫组分,得到纯净的原料气c,通过预加热器5被加热,得到反应原料气d,进入分解反应器6参与反应,经分解反应器后得到反应产物e,反应产物e中主要含有固体碳、氢气、未反应的原料气、少部分被夹带的催化剂,一并进入分离罐7进行气、液、固三相分离,经分离得到的固体碳进入固体碳收集罐 14,气相分解气f经冷却器8(利用冷却水对高温分解气进行冷却)冷却后得到气流g,再经压缩机9压缩后,输送至分解气缓冲罐 10中。部分燃料气b3与空气i分别或混合进入燃烧器13进行燃烧,燃烧产生的热量为分解反应器6中的分解反应提供热能,燃烧产生的高温尾气j进入预加热器5,用于加热原料气c。当引擎系统12需要燃料时,分解气缓冲罐 10中流出的气体通过控制阀20后进入引擎系统12燃烧后为引擎系统供能。
38.附注:1a 船用lng储罐;2 低温泵;3 气化器;4 原料气脱硫系统;5 预加热器;6 分解反应器;7 分离罐;8 冷却器;9 压缩机;10 分解气缓冲罐;12 引擎系统;13 燃烧器;14 固体碳收集罐;15a,15b,15c 高温阀;16 高温泵;17a,17b 耐高温测液位仪表;18a,18b 耐高温测温系统;19a,19b 压力表;20 控制阀;21 加热器;22 燃料气压缩机。
39.a1 低温液化燃料气;a2 经低温泵输送至气化器的燃料气;a3 气相低温燃料气;a4 经加热的气相燃料气;a5 经压缩的燃料气;a6 经气化的燃料气;b1,b3,b4 燃料气分气流;c 经脱硫的原料气;d 反应原料气;e 反应产物;f 分解气;f1,f2 部分分解气气流 g 经冷却的分解气;h 经压缩的分解气;i 空气;j 高温尾气;k 低温尾气;l 冷却水入口;m 冷却水出口;n1,n2 乙二醇水入口;p1,p2 乙二醇水出口;q 用于供能的分解气。
40.应用实施例2如图3所示本实施例用于海上油气生产系统从海上油气生产平台23开采出来的油气t经油气处理设施24将原料分为伴生气b和其他产物u,其他产物u储存于其他的设施25中,原料气b分成两股气流b4及b3分别进入反应流程和燃烧流程,反应粗原料气b4经过原料气净化系统 4脱除原料气中的有害组分,得到纯净的原料气c,通过预加热器5被加热,得到反应原料气d,进入分解反应器6参与反应,
经分解反应器后得到反应产物e,反应产物e中主要含有固体碳、氢气、未反应的原料气、少部分被夹带的催化剂,一并进入分离罐7进行气、液、固三相分离,经分离得到的固体碳进入固体碳收集罐 14,气相分解气f经冷却器8(利用冷却水对高温分解气8进行冷却)冷却后进入发电设备或/及蒸汽发生设备26,发电或/及生产蒸汽。燃料气b3与空气i分别或混合进入燃烧器13进行燃烧,燃烧产生的热量为分解反应器6中的分解反应提供热能,燃烧产生的高温尾气j进入预加热器5,用于加热原料气c。
41.附注:4 原料净化系统;5 预加热器;6 分解反应器;7 分离罐;8 冷却器;13 燃烧器;14 固体碳收集罐;15a,15b,15c 高温阀;16 高温泵;17a,17b 耐高温测液位仪表;18a,18b 耐高温测温系统;19a,19b 压力表;23 海上油气生产平台;24 油气处理设施;25 其他设施;26发电设备或/以及蒸汽发生设备。
42.b3,b4 燃料气分气流;c 经脱硫的原料气;d 反应原料气;e 反应产物;f 分解气;g 经冷却的分解气;h 经压缩的分解气;i 空气;j 高温尾气;k 低温尾气;l 冷却水入口;m 冷却水出口;n1,n2 乙二醇水入口;p1,p2 乙二醇水出口;q 用于供能的分解气; r 气化后用于供能的部分燃料气;s 用于供能的混合燃料气;t 开采出来的油气;u 其他产物;b 经处理的原料气;v 蒸汽;w 电。
43.尽管已经示出和描述了本发明的实施例,对于本领域的普通技术人员而言,可以理解在不脱离本发明的原理和精神的情况下可以对这些实施例进行多种变化、修改、替换和变型,本发明的范围由所附权利要求及其等同物限定。