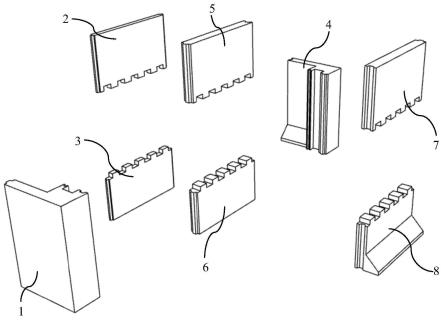
1.本发明属于窑炉壁制备方法技术领域,涉及耐火材料制备的技术领域,具体涉及一种耐高温、高强度装配窑炉壁的制备方法。
背景技术:2.窑炉壁是防止窑炉热源流失、使窑炉保持温度的有效部件,被广泛应用于生产石墨电极、炭砖(块)、炭糊、炭纤维、碳素阳极等领域,在我国现代制造产业和工业发展中具有重要地位。在窑炉壁的服役过程中,基于节能环保的需求,其保温效果和使用寿命已经成为窑炉壁的两个关键指标。
3.目前,生产石墨电极等产品的碳素厂窑炉壁所使用的材料大部分是耐火砖,其主要是通过将耐火砖垒砌成窑炉壁。然而,垒砌形成的窑炉壁的密闭性较差,保温效果差,会导致大量的热源流失及废气外溢,使得能耗增加,同时会造成环境污染,此外,垒砌而成的窑炉壁由于强度低极易发生损坏,影响碳素工艺正常生产。在后续的维修过程中,其安装施工周期长、安装环境要求高。这些问题已经成为制约碳素工艺节能环保、高效低碳生产的关键因素。
4.中国发明专利公开文本cn107344861a公开了一种窑炉内壁用高温耐火材料及其制备方法,通过对高铝料进行设置,结合对锆英砂等进行添加,得到耐火度高和粘结强度高的耐火材料,但是首先该技术方案并没有对高铝料进行具体的熟料处理过程进行改进,同时其配比不尽完善,从而导致其强度只能作为内壁使用而无法形成一体的窑炉壁。
技术实现要素:5.为了解决上述问题,本发明提供一种耐高温、高强度装配窑炉壁的制备方法,该方法制备的装配窑炉壁具有耐高温、高强度、保温效果好、使用寿命长的优点,且该装配窑炉壁为一次直接成型,可大幅度提高原材料的利用率并缩短窑炉壁的制备周期,具有显著的材料成本和时间成本优势,适用于工业大规模生产。
6.为达到上述目的,本发明采用了如下的技术方案:
7.一种耐高温、高强度窑炉壁的制备方法,包括如下步骤:
8.(1)配置铝矾土a和铝矾土b,所述铝矾土a为氧化铝含量为60~65wt%的铝矾土,所述铝矾土b为氧化铝含量为70~75wt%的铝矾土,将铝矾土a和铝矾土b分别置入到煅烧炉内均在1200~1350℃的温度下煅烧72~120h,然后将煅烧后的铝矾土a熟料进行破碎,破碎至最大颗粒的粒径小于等于10mm,然后对其进行筛分,筛分得到粒径为0~1mm的熟料i、粒径为1~3mm的熟料ii、粒径为3~5mm的熟料iii以及粒径为5~10mm的熟料iv;同时将煅烧后的铝矾土b熟料进行球磨,然后筛分得到粒径为1~74μm的细粉铝矾土b熟料。
9.(2)将15~25重量份的熟料i、10~20重量份的熟料ii、10~20重量份的熟料iii、15~25重量份的熟料iv、12~20重量份的细粉铝矾土b熟料、2~6重量份的硅灰、6~14重量份的高铝水泥、0.1~0.2重量份的水分保持剂a、0.01~0.06重量份的水分保持剂b以及
0.008~0.012重量份的防爆纤维置入到搅拌装置中进行搅拌,然后通过喷嘴向混合物料中喷入物料总量6~12wt.%的水,然后继续搅拌3~5min。
10.(3)预先设置模具,然后将步骤(2)混合均匀的料浆在10~50℃的温度下直接浇注到模具中,然后振动成型,振动时间为3~5min,然后在20~60℃的温度下进行固化,固化完成后,脱模得到窑炉壁产品。
11.作为优选,制备得到的窑炉壁的体积密度为2.50~2.95g/cm3,110℃下保温24h的耐压强度为60~100mpa、抗折强度为7~13mpa,1300℃下保温4h的耐压强度为80~120mpa、抗折强度为9~16mpa,常温磨损量为5~9cc,1300℃下保温4h的烧后线性变化为
±
0.3%,900℃水冷条件下的热震稳定性为20~25次。
12.作为优选,所述水分保持剂a为三聚磷酸钠,所述水分保持剂b为六偏磷酸钠。
13.作为优选,步骤(2)中的搅拌为在20~30℃的温度下进行搅拌。
14.作为优选,步骤(3)中的固化时间为6~10h。
15.作为优选,所述硅灰的平均粒径为80~280nm,且其中粒径小于120nm的硅灰的占比为82~95wt%。
16.作为优选,所述高铝水泥的平均粒径是硅灰平均粒径的85~102倍。
17.一种耐高温、高强度的窑炉壁,其特征在于,所述窑炉壁采用上述的制备方法制备得到。
18.一种耐高温、高强度的窑炉的装配方法,包括如下步骤:
19.i,采用权利要求1~7任一项所述的制备方法制备得到耐高温、高强度的窑炉壁。
20.ii,制作窑炉立柱和窑炉基座的模具,采用1~7任一项所述制备方法的步骤(1)和步骤(2)制备得到的料浆,将料浆温度设置为30~50℃,然后将30~50℃温度的料浆直接浇注窑炉立柱和窑炉基座的模具中,然后振动成型,振动时间为3~5min,然后在20~60℃的温度下进行固化,固化时间为7~12h,然后去模,得到窑炉立柱和窑炉基座。
21.iii,将步骤i制备得到的耐高温、高强度的窑炉壁进行吊装拼接于步骤ii制备得到的窑炉立柱和窑炉基座上。
22.iv,在各个窑炉壁和窑炉立柱之间设置填充耐火隔热棉,然后在窑炉内外砌体的连接处涂抹耐火泥,得到耐高温、高强度的窑炉。
23.作为优选,步骤ii所述的窑炉立柱和窑炉基座为一体结构设置。
24.本发明的具有以下有益效果:
25.(1)与耐火砖堆砌的窑炉壁相比,本发明采用了料浆浇注固化的工艺,通过合理设置原料预处理及混料参数,通过对设置各物料的比例以及各物料的粒径以及配合水体的加入量和水分保持剂的设置,使料浆中的各成分充分混合均匀且保持相对良好的流动性,这可以保证料浆能够高效填充不同尺寸及形状的模具内部(模具某些部位比较精细),经过合理设置浇注及固化步骤,可直接成型得到不同尺寸及形状的窑炉壁产品,无需后续垒砌操作,生产成本低,适用于大规模工业化生产。
26.(2)本发明通过合理设置原料,使得保持较高耐火性能的情况下能够具有良好流动性而实现了窑炉壁的一次成型,配合本发明特定的装配工艺,使得最终成型的窑炉壁不存在垒砌缝隙,保温效果得到大幅度提升,有效阻止了热源流失及废气的溢出,达到了节能环保的效果。
27.(3)本发明通过设置不同粒径的具体氧化铝含量的铝矾土a进行具体比例的配制、结合特定氧化铝含量的铝矾土b的特定粒径作为主料进行搭配,尤其是对铝矾土a和铝矾土b进行特定的温度和时间的煅烧使其熟化程度与本发明设置的特定粒度比例进行协调搭配,粗粒径的铝矾土a可以起骨架支撑作用,合理设置的细粒径的铝矾土a和铝矾土b进行孔隙的填充,通过本发明特定比例和特定粒径的搭配使得固化后的窑炉壁内部气孔更少、密度更高,同时组织更加均匀,最终强化了得到产品的耐压强度和抗折强度。由于本发明直接设置的是一体成型的窑炉壁,因此对于耐压强度和抗折强度有更高的要求,因此本发明上述这样的设置更加符合本发明最终产品的应用。同时通过调节各物料比例、搅拌时间、浇注温度、固化温度及固化时间等参数,强化了最终得到窑炉壁的耐压强度、抗折强度及耐火性得到增强,得到的产品具有密度高、耐高温、强度高、使用寿命长的特点。
28.(4)本发明对于辅料的合理设定,尤其是对于硅灰粒径和粒径分布情况进行合理设定,通过硅灰与高铝水泥的协调配合,使得最终窑炉壁的抗拉、抗压强度得到增强;虽然现有技术中硅灰的粒径均设置的较小,但是本发明通过对硅灰进行特定粒径的配置以及对其与高铝水泥的粒径进行配合设置,使得硅灰的浸润性和防结团性得到了最优配置,从而强化了本发明料浆的流动性,从而在保证强度的前提下强化了料浆能够完全的进入到异形模具的各精细部位,从而使得一体成型成为可能。
29.(5)本发明通过具体设置原料和制备工艺以及具体的装配工艺,使得最终得到的窑炉产品耐高温性得到了大幅提升,现有石墨电极炉的电极距离炉壁设置一般不低于1080mm,但是通过本发明的具体设置得到的窑炉能够在相同使用时长的情况下,将电极距离炉壁的距离缩短至700~800mm;并且现有炉壁的内壁上一般均需要涂抹耐火层,但是本发明通过具体设置原料和制备工艺得到的窑炉壁无需涂抹耐火层,从而可以大大的降低耐火材料的使用量,从而大大的降低了生产成本。
附图说明
30.图1是本发明一种实施方式各样品的结构示意图。
31.其中,1是左窑头结构砌体,2是窑头上内砌块,3是窑头下内砌块,4是右窑头结构砌体,5是窑头上外砌块,6是窑头下外砌块,7是墙体上砌块,8是墙体下砌块。
具体实施方式
32.本说明书中公开的任一特征,除非特别叙述,均可被其他等效或具有类似目的的替代特征加以替换。除非特别叙述,每个特征只是一系列等效或者类似特征中的一个例子而已。所述仅仅是为了帮助理解本发明,不应该视为对本发明的具体限制。
33.下面以具体实施方式对本发明作进一步详细的说明。
34.实施例1:
35.将100kg氧化铝含量为60wt.%的铝矾土a在1200℃下煅烧72h,将煅烧后的物料进行破碎、筛分,得到粒度为0~1mm(熟料i)、1~3mm(熟料ii)、3~5mm(熟料iii)、5~10mm(熟料iv)的四种铝矾土熟料,将100kg氧化铝含量为70wt.%的铝矾土b也在1200℃下煅烧72h,将煅烧后的物料进行球磨、筛分,得到粒度为1~74μm的高铝细粉。称取粒径为0~1mm的熟料i 20kg、粒径为1~3mm的熟料ii 15kg、粒径为3~5mm的熟料iii 15kg、粒径为5~10mm的
熟料iv 20kg、粒径为1~74μm的铝矾土b(高铝细粉)16kg、硅灰4kg、高铝水泥10kg、三聚磷酸钠0.1kg、六偏磷酸钠0.01kg、防爆纤维0.01kg通过输送带加入搅拌机中,其中本实施例硅灰的平均粒径为约180nm,且其中粒径小于120nm的硅灰的占比为85wt%。且本实施例高铝水泥的平均粒径是硅灰平均粒径的95倍。将8kg的水加入搅拌机中,在室温下搅拌3min。将混合均匀的料浆在10℃下灌入模具中,振动3min,然后将浇注好的窑炉壁在10℃下固化6h,得到窑炉壁产品。最终窑炉壁产品的体积密度为2.50g/cm3,110℃下保温24h的耐压强度为60mpa、抗折强度7mpa,1300℃下保温4h的耐压强度为80mpa、抗折强度9mpa,常温磨损量为9cc,1300℃下保温4h的烧后线性变化为
±
0.3%,900℃水冷条件下的热震稳定性为25次。
36.实施例2:
37.将100kg氧化铝含量为65wt.%的铝矾土a(a料)在1300℃下煅烧100h,将煅烧后的物料进行破碎、筛分,得到粒度为0~1mm(熟料i)、1~3mm(熟料ii)、3~5mm(熟料iii)、5~10mm(熟料iv)的四种铝矾土熟料,将100kg氧化铝含量为72wt.%的铝矾土b也在1300℃下煅烧100h,将煅烧后的物料进行球磨、筛分,得到粒度为1~74μm的高铝细粉。称取粒径为0~1mm的a料15kg、粒径为1~3mm的a料20kg、粒径为3~5mm的a料20kg、粒径为5~10mm的a料15kg、粒径为1~74μm的b料12kg、硅灰6kg、高铝水泥12kg、三聚磷酸钠0.15kg、六偏磷酸钠0.03kg、防爆纤维0.01kg通过输送带加入搅拌机中,将10kg的水加入搅拌机中,在室温下搅拌4min。然后将混合均匀的料浆在30℃下灌入模具中,振动5min,然后将浇注好的窑炉壁在30℃下固化7h,得到窑炉壁产品。最终窑炉壁产品的体积密度为2.75g/cm3,110℃下保温24h的耐压强度为70mpa、抗折强度8mpa,1300℃下保温4h的耐压强度为90mpa、抗折强度11mpa,常温磨损量为7cc,1300℃下保温4h的烧后线性变化为
±
0.3%,900℃水冷条件下的热震稳定性为25次。
38.实施例3:
39.将100kg氧化铝含量为63wt.%的铝矾土a在1350℃下煅烧120h,将煅烧后的物料进行破碎、筛分,得到粒度为0~1mm、1~3mm、3~5mm、5~10mm的四种铝矾土熟料,将100kg氧化铝含量为75wt.%的铝矾土b也在1350℃下煅烧120h,将煅烧后的物料进行球磨、筛分,得到粒度为1~74μm的高铝细粉。称取粒径为0~1mm的a料25kg、粒径为1~3mm的a料10kg、粒径为3~5mm的a料10kg、粒径为5~10mm的a料25kg、粒径为1~74μm的b料20kg、硅灰4kg、高铝水泥6kg、三聚磷酸钠0.15kg、六偏磷酸钠0.06kg、防爆纤维0.01kg通过输送带加入搅拌机中,将12kg的水加入搅拌机中,在室温下搅拌4min。然后将混合均匀的料浆在30℃下灌入模具中,振动5min,然后将浇注好的窑炉壁在50℃下固化10h,得到窑炉壁产品。最终窑炉壁产品的体积密度为2.90g/cm3,110℃下保温24h的耐压强度为90mpa、抗折强度12mpa,1300℃下保温4h的耐压强度为100mpa、抗折强度14mpa,常温磨损量为6cc,1300℃下保温4h的烧后线性变化为
±
0.3%,900℃水冷条件下的热震稳定性为25次。
40.实施例4:
41.本实施例示例耐高温、高强度的窑炉的装配方法,包括如下步骤:
42.i,采用实施例1的制备方法制备得到耐高温、高强度的窑炉壁;如图1所示,其中窑头上内砌块、窑头下内砌块、窑头上外砌块、窑头下外砌块、墙体上砌块和墙体下砌块均为制备得到的耐高温、高强度的窑炉壁。其中所述墙体上砌块和墙体下砌块的高度之比为
(1.03~2.3):1。例如本实施例为2300mm:2200mm,满足上述比例要求。通过对该墙体上砌块和墙体下砌块的高度比例进行具体设置,使得墙体的稳定性得到了保证,同时由于使用过程中石墨电极的高度处的温度热量最为集中,通过合理设置墙体分块儿处的高度比例,可以使得石墨电极处于墙体上砌块的高度位置,从而在维修的时候可以只拆掉一部分墙体而进行维修,无需整体拆除,大大降低了维修成本。
43.ii,制作窑炉立柱和窑炉基座的模具,采用实施例1所述制备方法的步骤(1)和步骤(2)制备得到的料浆,将料浆温度设置为35℃,然后将35℃温度的料浆直接浇注窑炉立柱和窑炉基座的模具中,然后振动成型,振动时间为3.5min,然后在35℃的温度下进行固化,固化时间为9h,然后去模,得到窑炉立柱和窑炉基座;将步骤i制备得到的耐高温、高强度的窑炉壁进行吊装拼接于步骤ii制备得到的窑炉立柱和窑炉基座上;如图1中左窑头结构砌体和右结构砌体(即窑炉立柱)。
44.iv,在各个窑炉壁和窑炉立柱之间设置填充耐火隔热棉,然后在窑炉内外砌体的连接处涂抹耐火泥,得到耐高温、高强度的窑炉。
45.实施例5:
46.本实施例示例耐高温、高强度的窑炉的装配方法,与实施例4的不同之处在于步骤ii中制作窑炉立柱和窑炉基座的模具为窑炉立柱和窑炉基座的一体结构的模具。
47.对比例1
48.本对比例的其它设置方式与实施例1相同,不同之处在于没有铝矾土a,经过相同的制备步骤制备得到窑炉壁后与实施例1得到的窑炉壁进行各项指标对比发现本对比例的体积密度为3.10g/cm3,110℃下保温24h的耐压强度为40mpa、抗折强度5mpa,1300℃下保温4h的耐压强度为50mpa、抗折强度6mpa,常温磨损量为11cc,1300℃下保温4h的烧后线性变化为
±
2.5%,900℃水冷条件下的热震稳定性为6次。这是由于粗粒径的铝矾土a主要起骨架支撑作用,不添加铝矾土a虽然能提高产品的体积密度,但其高温烧结的变形量大,且易导致裂纹出现,因此耐压强度、抗折强度及热振稳定性差。
49.对比例2
50.本对比例的其它设置方式与实施例1相同,不同之处在于铝矾土a没有分成不同粒径的熟料i、ii、iii、iv的不同具体的添加量来添加,而是统一按照混合粒度70kg总量进行添加,经过相同的制备步骤制备得到窑炉壁后与实施例1得到的窑炉壁进行各项指标对比发现本对比例的体积密度为2.3g/cm3,110℃下保温24h的耐压强度为50mpa、抗折强度5mpa,1300℃下保温4h的耐压强度为60mpa、抗折强度7mpa,常温磨损量为10cc,1300℃下保温4h的烧后线性变化为
±
0.5%,900℃水冷条件下的热震稳定性为18次。铝矾土a分成具体的不同粒径的熟料i、ii、iii、iv且按照具体的添加量来添加的目的主要是使粗细颗粒的堆积密度达到最高最优,由于本对比例2中未按照比例要求添加铝矾土a,其堆积密度低,导致窑炉壁产品的体积密度降低,内部含量大量孔隙,最终使得耐压强度、抗折强度及热振稳定性等性能下降。
51.对比例3
52.本对比例的其它设置方式与实施例1相同,不同之处在于采用高岭土替代实施例1中的铝矾土b,经过相同的制备步骤制备得到窑炉壁后与实施例1得到的窑炉壁进行各项指标对比发现本对比例的体积密度为2.5g/cm3,110℃下保温24h的耐压强度为58mpa、抗折强
度6mpa,1300℃下保温4h的耐压强度为75mpa、抗折强度8mpa,常温磨损量为9cc,1300℃下保温4h的烧后线性变化为
±
0.6%,900℃水冷条件下的热震稳定性为20次。由于高岭土中含有大量的二氧化硅,其氧化铝的含量要远低于铝矾土b,制备得到的窑炉壁产品的耐高温性能要低于铝矾土b,因此,高温烧结后的烧后线性变化大、热震稳定性差。
53.对比例4
54.本对比例的其它设置方式与实施例1相同,不同之处在于铝矾土b的粒径设置为1~3mm,经过相同的制备步骤制备得到窑炉壁后与实施例1得到的窑炉壁进行各项指标对比发现本对比例的体积密度为1.9g/cm3,110℃下保温24h的耐压强度为30mpa、抗折强度3mpa,1300℃下保温4h的耐压强度为40mpa、抗折强度4mpa,常温磨损量为12cc,1300℃下保温4h的烧后线性变化为
±
0.3%,900℃水冷条件下的热震稳定性为12次。这是由于铝矾土b的粒径增加后,很难填充满铝矾土a形成骨架空隙,导致窑炉壁产品的体积密度大幅度下降,从而使耐压强度、抗折强度及热振稳定性等性能严重下降。
55.对比例5
56.本对比例的其它设置方式与实施例1相同,不同之处在于铝矾土a和铝矾土b均没有经过煅烧而是直接破碎、研磨之后进行添加。经过相同的制备步骤制备得到窑炉壁后与实施例1得到的窑炉壁进行各项指标对比发现本对比例的体积密度为2.5g/cm3,110℃下保温24h的耐压强度为40mpa、抗折强度5mpa,1300℃下保温4h的耐压强度为60mpa、抗折强度7mpa,常温磨损量为9cc,1300℃下保温4h的烧后线性变化为
±
1.2%,900℃水冷条件下的热震稳定性为5次。这是由于未经过煅烧后的铝矾土a和铝矾土b中含量大量的结晶水,虽然可制备得到密度基本一致的窑炉壁产品,但在高温烧结过程中会发生脱水反应,易导致产品开裂,因此其热震稳定性等性能差。
57.对比例6
58.本对比例的其它设置方式与实施例3相同,不同之处在于步骤(2)中将30kg的熟料i、6kg的熟料ii、5kg的熟料iii、10kg的熟料iv、25kg的细粉铝矾土b熟料、10kg的硅灰、3kg的高铝水泥、0.5kg的水分保持剂a(水分保持剂b和防爆纤维加入量和实施例3相同,但是其它物料的配比量均不在本发明限定的范围内)置入到搅拌装置中进行搅拌。经过相同的制备步骤制备得到窑炉壁后与实施例3得到的窑炉壁进行各项指标对比发现本对比例的体积密度为2.90g/cm3,110℃下保温24h的耐压强度为80mpa、抗折强度10mpa,1300℃下保温4h的耐压强度为85mpa、抗折强度12mpa,常温磨损量为7cc,1300℃下保温4h的烧后线性变化为
±
0.5%,900℃水冷条件下的热震稳定性为19次,即虽然使用的物料和物料粒径等指标都采用本发明设置的,但是添加量不在本发明设置的配比量范围内,使得最终得到的产品线性变化较大,并且热震稳定性也相对较小,从而证明了本发明各物料的配比是最优配比。
59.对比例7
60.本对比例的其它设置方式与实施例3相同,不同之处在于将铝矾土a和铝矾土b进行互换处理。经过相同的制备步骤制备得到窑炉壁后与实施例3得到的窑炉壁进行各项指标对比发现本对比例的各项指标与实施例3的基本相同,但是物料成本上升了15个百分点,这是由于高氧化铝含量的铝矾土成本相对较高,但是本发明通过研究发现合理设置低氧化铝含量的铝矾土a的不同粒径的搭配即可在相对低成本的情况下达到相对好的性能指标。