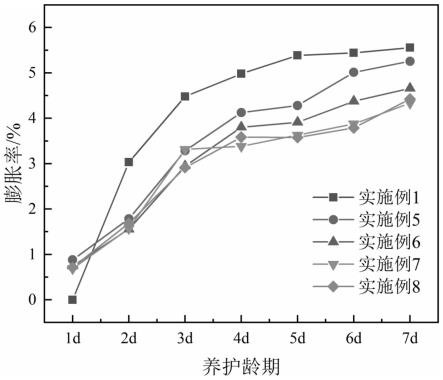
1.本发明涉及煤矿充填技术领域,具体而言,涉及一种煤矿隅角充填用膏体及充填煤矿隅角的方法。
背景技术:2.神东矿区多数矿井开采煤层均为ι类容易自燃煤层,采高大,工作面长,上、下顺槽三角区一般垮落不严。在特厚煤层开采时,不论是放顶煤开采还是大采高工艺,工作面两端顺槽附近顶煤往往很难回收,两道附近采空区遗煤较多,自燃危险性大。随着下层煤的陆续开采和大采高工艺的不断升级,公司矿井防灭火形势越来越严峻,急需研发一种移动方便、工艺简单、快速高效、价格低廉的防灭火材料、配套设备和工艺,能够在回采工作面上、下隅角快速堆积,覆盖遗煤、封堵两道漏风,以达到预防工作面两道遗煤自燃的目的。
3.目前神东公司各矿井工作面采空区预防自然发火主要采取预防性注浆和上、下隅角封堵的措施。但是目前预防性注浆存在浆液浓度低易拉沟、覆盖充填效果差等问题;上、下隅角封堵主要采取施工风障和黄土袋封堵并喷涂高分子材料的措施,存在施工进度慢,封堵不严密和高分子材料高温发热的问题。
技术实现要素:4.本发明的主要目的在于提供一种煤矿隅角充填用膏体及充填煤矿隅角的方法,以解决现有技术中煤矿隅角充填用材料存在的或覆盖充填效果差、或封堵不严密、或成本较高等问题。
5.为了实现上述目的,根据本发明的一个方面,提供了一种煤矿隅角充填用膏体,该煤矿隅角充填用膏体包括粉煤灰、炉渣、速凝剂及水;且煤矿隅角充填用膏体的固含量为77~80%。
6.进一步地,煤矿隅角充填用膏体中,粉煤灰和炉渣的重量比为1:(3~4.5)。
7.进一步地,粉煤灰包括35.0~37.0wt%的cao、24.0~26.0wt%的sio2、16.0~18.0wt%的so3、9.0~10.5wt%的al2o3、4.0~5.0wt%的fe2o3、1.5~2.0wt%的na2o、0.8~1.2wt%的mgo、0.6~0.8wt%的k2o、0.4~0.6wt%的tio2、0.1~0.3wt%的sro、0.01~0.02wt%的mno及余量不可避免的杂质;炉渣包括56.0~58.0wt%的cao、15.0~16.0wt%的sio2、12.0~12.5wt%的so3、5.0~5.5wt%的al2o3、5.0~5.5wt%的fe2o3、1.0~1.2wt%的mgo、0.6~0.8wt%的tio2、0.3~0.5wt%的sro、0.3~0.5wt%的k2o、0.2~0.4wt%的na2o、0.1~0.3wt%的mno及余量不可避免的杂质。
8.进一步地,速凝剂选自j85速凝剂。
9.进一步地,按重量份数计,膏体包括15~16份的粉煤灰、62~63份的炉渣,0.8~1.2份的j85速凝剂及20.5~22.5份的水。
10.进一步地,粉煤灰为颗粒状,粉煤灰的平均粒径为25~30μm;优选地,炉渣为颗粒状,炉渣的平均粒径为135~145μm。
11.进一步地,炉渣的孔隙率为60~65%;优选地,粉煤灰的孔隙率为55~60%。
12.进一步地,炉渣的不均匀系数为8~9,粉煤灰的不均匀系数为4.5~5;优选地,炉渣的曲率系数为2~3,粉煤灰的曲率系数为0.5~1.5。
13.根据本发明的另一方面,提供了一种充填煤矿隅角的方法,方法包括:采用移动式充填泵将前述的煤矿隅角充填用膏体输送至煤矿井下采空区隅角以进行充填。
14.进一步地,以每立方米采空区隅角的体积计,煤矿隅角充填用膏体的用量为1.9~2.1t。
15.应用本发明的技术方案,有效解决了煤矿回采工作面上、下隅角充填时水泥用量高导致的高成本问题,解决了现有常规充填材料覆盖充填效果差,上、下隅角封堵不严密的问题。基于上述特定组分的煤矿隅角充填用膏体,本发明在较低成本的基础上即实现了在回采工作面上、下隅角快速堆积,覆盖遗煤、封堵两道漏风,以实现预防工作面两道遗煤自燃的目的,防灭火效果更优。而且,本发明上述组分中不采用高分子材料,从而还有效避免了因高分子材料高温发热而带来的大安全性问题。
附图说明
16.构成本技术的一部分的说明书附图用来提供对本发明的进一步理解,本发明的示意性实施例及其说明用于解释本发明,并不构成对本发明的不当限定。在附图中:
17.图1示出了本发明一种实施方式中充填煤矿隅角的方法流程图;以及
18.图2示出了本发明实施例1、实施例5至8中煤矿隅角充填用膏体的膨胀率(7d)测试图。
具体实施方式
19.需要说明的是,在不冲突的情况下,本技术中的实施例及实施例中的特征可以相互组合。下面将参考附图并结合实施例来详细说明本发明。
20.正如本发明背景技术部分所描述的,现有技术中煤矿隅角充填用材料存在的或覆盖充填效果差、或封堵不严密、或成本较高等问题。为了解决这一问题,本发明提出了一种煤矿隅角充填用膏体,其包括粉煤灰、炉渣、速凝剂及水;且煤矿隅角充填用膏体的固含量为77~80%。
21.首先,本发明将上述煤矿隅角充填用膏体的固含量控制在77~80%,可以使得膏体在具有优异充填性能及较低成本的基础上,还具有适宜的塌落度、扩散度及稠度。这样的膏体更易在后续应用过程中通过移动式充填泵泵送的方式进行隅角充填,以在回采工作面上、下隅角快速完成堆积,以覆盖遗煤、封堵两道漏风。基于此,上述膏体的充填作业可在井下检修班时进行,与井下各项生产工作不相冲突,且其工艺简单便捷。当膏体的固含量低于此范围时,其无法在隅角处进行自然堆积,进而也不能实现充填作用;而高于此范围时,其则无法通过移动式充填泵泵送的方式进行隅角充填。在一些可选的实施方式中,上述煤矿隅角充填用膏体的固含量可以为77%、78%、79%或80%。
22.其次,相较于本领域常规采用水泥作为膏体的胶凝材料而言,本发明以粉煤灰及炉渣作为煤矿隅角充填用材料组分,在较少膏体用量的基础上即可达到十分优异的覆盖充填效果,且成本更低。这是由于以下原因:
23.其一,炉渣和粉煤灰均属于碱性材料,且具备部分活性,有利于水化反应,故而可以使膏体材料具有胶凝属性,加入速凝剂后可快速凝固形成具有可塑性的膏体状充填材料。这样,充填材料在后续应用过程中可以具有十分优异的填充稳定性。
24.其二,基于上述特定组分的充填材料还具有一定的自膨胀性,更有利于充填后的接顶,从而无需额外加入任何膨胀剂,且在较少用量的基础上即可达到优异的覆盖充填效果及封堵严密性。
25.其三,粉煤灰及炉渣的价格远低于水泥,从而大幅度地降低了充填成本,充填成本可降低约30%。而且,上述粉煤灰及炉渣均来源于煤燃烧废料,基于此,本发明还可以实现废弃物的再利用,减少废弃物的排放,以达到绿色环保的要求,符合持续发展理念。
26.综上,本发明有效解决了煤矿回采工作面上、下隅角充填时水泥用量高导致的高成本问题,解决了现有常规充填材料覆盖充填效果差,上、下隅角封堵不严密的问题。基于上述特定组分的煤矿隅角充填用膏体,本发明在较低成本的基础上即实现了在回采工作面上、下隅角快速堆积,覆盖遗煤、封堵两道漏风,以实现预防工作面两道遗煤自燃的目的,防灭火效果更优。而且,本发明上述组分中不采用高分子材料,从而还有效避免了因高分子材料高温发热而带来的大安全性问题。
27.为了进一步提高煤矿隅角充填用膏体的上述优异性能,优选煤矿隅角充填用膏体中,粉煤灰和炉渣的重量比为1:(3~4.5),例如可以为1:3、1:3.5、1:4或1:4.5。炉渣属于粗骨料,过量会导致膏体管道输送时沉降堵管;而粉煤灰属于细颗粒黏性大,过量则会导致膏体管道输送时阻力较大。
28.在一种优选的实施方式中,上述粉煤灰、炉渣均取自神东矿区附近电厂。粉煤灰为燃煤电厂煤燃烧后排出的烟气中收捕下来的细灰,其含有以下组分:35.0~37.0wt%的cao、24.0~26.0wt%的sio2、16.0~18.0wt%的so3、9.0~10.5wt%的al2o3、4.0~5.0wt%的fe2o3、1.5~2.0wt%的na2o、0.8~1.2wt%的mgo、0.6~0.8wt%的k2o、0.4~0.6wt%的tio2、0.1~0.3wt%的sro、0.01~0.02wt%的mno及余量不可避免的杂质。炉渣为火电厂燃煤燃烧后排出的固体废渣,其含有以下组分:56.0~58.0wt%的cao、15.0~16.0wt%的sio2、12.0~12.5wt%的so3、5.0~5.5wt%的al2o3、5.0~5.5wt%的fe2o3、1.0~1.2wt%的mgo、0.6~0.8wt%的tio2、0.3~0.5wt%的sro、0.3~0.5wt%的k2o、0.2~0.4wt%的na2o、0.1~0.3wt%的mno及余量不可避免的杂质。
29.在一种优选的实施方式中,本发明上述组分的速凝剂为j85型速凝剂,其为铝氧熟料、纯碱、增稠剂等多种组份经改性配制而成的灰色粉状产品。j85型速凝剂协同粉煤灰及炉渣协同作为煤矿隅角充填用材料组分,对炉渣与粉煤灰中的活性材料具有速凝快硬和增强减水作用,从而可以促使膏体能够迅速凝结硬化,使充填材料具有较高的力学性能,并能保持活性材料的其他优异性能(诸如降低水化热)。
30.为了进一步提高煤矿隅角充填用膏体的上述优异性能,按重量份数计,优选膏体包括15~16份的粉煤灰、62~63份的炉渣,0.8~1.2份的j85速凝剂及20.5~22.5份的水。
31.在一种优选的实施方式中,粉煤灰为颗粒状,粉煤灰的平均粒径为25~30μm;炉渣为颗粒状,炉渣的平均粒径为135~145μm。炉渣的孔隙率为60~65%;粉煤灰的孔隙率为55~60%。炉渣的不均匀系数为8~9;炉渣的曲率系数为2~3。粉煤灰的不均匀系数为4.5~5;粉煤灰的曲率系数为0.5~1.5。
32.本发明还提供了一种充填煤矿隅角的方法,该方法包括:采用移动式充填泵将前述的煤矿隅角充填用膏体输送至煤矿井下采空区隅角以进行充填。
33.在一种优选的实施方式中,如图1所示,本领域技术人员可先在地表上的混凝土搅拌站按上述膏体配比充分搅拌后得到煤矿隅角充填用膏体,再通过混凝土搅拌车将上述膏体经过斜坡道运输至移动式充填泵(充填泵为含实心轮胎的托泵)处以为后续充填做准备。作业区通过充填管路铺设灌浆主管,移动式充填泵经过充填管路,沿灌浆主管排深至内顺槽顶部尖角位置,并延伸至紧挨三角区后方的垮落带处进行隅角充填,该充填位置所需膏体更少,封堵效果更好。该方法利用地表原有搅拌站制作膏体取代了现有常规作业中的井下制浆工序,并且上述充填可在井下检修班时进行充填,与井下各项生产工作不相冲突,其工艺简单便捷,使得膏体浇注后形成的膏体充填体能够在回采工作面上、下隅角快速堆积,覆盖遗煤、封堵两道漏风。在一种优选的实施方式中,以每立方米采空区隅角的体积计,煤矿隅角充填用膏体的用量为1.9~2.1t,例如以每立方米采空区隅角的体积计,煤矿隅角充填用膏体的用量为2040kg。
34.以下结合具体实施例对本技术作进一步详细描述,这些实施例不能理解为限制本技术所要求保护的范围。
35.实施例1
36.先将粉煤灰、炉渣按照重量比1:4配比加入搅拌机中;再继续将水(普通自来水)、j85型速凝剂加入到上述搅拌机中充分混合,即得到煤矿隅角充填用膏体。其中:
37.粉煤灰包括以下组分:粉煤灰包括36.77wt%的cao、25.76wt%的sio2、17.68wt%的so3、10.32wt%的al2o3、4.88wt%的fe2o3、1.87wt%的na2o、1.14wt%的mgo、0.76wt%的k2o、0.55wt%的tio2、0.25wt%的sro、0.01wt%的mno及余量不可避免的杂质。
38.粉煤灰经实验室样本实测粒径范围分别为:0~18.7μm占比为50.7%;18.7~35.3μm占比为25.15%;35.3~76.0μm占比为20.69%;76.0~111.0μm占比为3.63%;>111μm占比为0.46%。粉煤灰经实验室实测的比重为1.95t/m3,松散干密度为0.80g/cm3,孔隙率为58.97%,平均粒径为d
cp
=27.26μm,不均匀系数cu=4.83,曲率系数cc=0.96。
39.炉渣包括以下组分:炉渣包括57.69wt%的cao、15.75wt%的sio2、12.41wt%的so3、5.36wt%的al2o3、5.29wt%的fe2o3、1.18wt%的mgo、0.77wt%的tio2、0.46wt%的sro、0.44wt%的k2o、0.38wt%的na2o、0.26wt%的mno及余量不可避免的杂质。
40.炉渣经实验室样本实测粒径范围分别为:0~18.7μm占比为13.21%;18.7~35.3μm占比为6.31%;35.3~76.0μm占比为16.55%;76.0~111.0μm占比为20.27%;>111μm占比为43.66%。炉渣经实验室实测的比重为2.28t/m3,松散干密度为0.85g/cm3,孔隙率为62.72%,平均粒径为d
cp
=140.76μm,不均匀系数cu=8.36,曲率系数cc=2.44。
41.按重量份数计,膏体包括15.41份的粉煤灰、61.66份的炉渣,0.93份的j85速凝剂及22份的水。
42.制得膏体的固含量为78%。
43.实施例2
44.和实施例1的区别仅在于:调控膏体的固含量为77.5%。
45.实施例3
46.和实施例1的区别仅在于:调控膏体的固含量为78.5%。
47.实施例4
48.和实施例1的区别仅在于:调控膏体的固含量为79%。
49.实施例5
50.和实施例1的区别仅在于:额外添加uea型膨胀剂,添加量为粉煤灰量的0.5%。
51.实施例6
52.和实施例1的区别仅在于:额外添加csa型膨胀剂,添加量为粉煤灰量的10%。
53.实施例7
54.和实施例1的区别仅在于:额外添加钠基膨润土型膨胀剂,添加量为粉煤灰量的10%。
55.实施例8
56.和实施例1的区别仅在于:额外添加钙基膨润土型膨胀剂,添加量为粉煤灰量的10%。
57.性能表征:
58.(一)将实施例中的材料置入塌落度桶中测试其塌落度值、扩散度值和稠度值。测试结果如表1所示。
59.表1
[0060] 塌落度/cm扩散度/cm稠度/cm实施例118.231.68.4实施例223.541.59.8实施例314.127.76.4实施例48.622.35.3
[0061]
通过表1可以发现,将膏体的固含量控制在77~80%的范围内,可使膏体具有适宜的塌落度、扩散度及稠度,在封堵效果更佳的基础上更利于管道输送。最优选膏体的固含量为78%,这样,膏体塌落度的区间范围在16~20cm之间,是最利于管道输送的同时在隅角处形成自然堆积。
[0062]
(二)对实施例中的煤矿隅角充填用膏体进行膨胀率测试。膨胀率测量与计算方法:使用符合国家标准的游标卡尺对达到养护龄期要求的圆柱形充填体试件进行外观变化尺寸测量,如下图1所示。测量其圆柱体长轴与短轴方向的尺寸变化量,即测量其高度h与直径d的变化量,上述每组数据须测量3次并取均值,根据圆柱体的体积公式计算出其变化后的体积v。充填体变化后的体积v减去其脱模后的初始体积v0,除以其初始体积v0,并乘上百分百,即可求得对应充填体的膨胀率α。具体计算公式如下:
[0063]
h=h1+h2+h3[0064]
d=d1+d2+d3[0065][0066]
[0067][0068]
测试结果如表2所示,7d膨胀率测试结果如图2所示。
[0069]
表2
[0070] 1d2d3d4d5d6d7d实施例10.0003.0314.4794.9805.3845.4435.558实施例50.8831.7843.2864.1254.2815.0135.256实施例60.7461.5552.9483.8053.9114.3744.662实施例70.6871.5723.3153.3833.6273.8784.330实施例80.7151.6892.9143.5843.5763.7884.423
[0071]
通过表2可以发现,在额外添加不同种类膨胀剂的情况下,膨胀效果并不明显,甚至膨胀效果会有所下降,相反不添加任何膨胀剂的实施例1相对其它实施例效果更好,因此本发明前述炉渣基膏体充填体无需额外添加任何膨胀剂,该种材料具有自膨胀性。
[0072]
以上仅为本发明的优选实施例而已,并不用于限制本发明,对于本领域的技术人员来说,本发明可以有各种更改和变化。凡在本发明的精神和原则之内,所作的任何修改、等同替换、改进等,均应包含在本发明的保护范围之内。