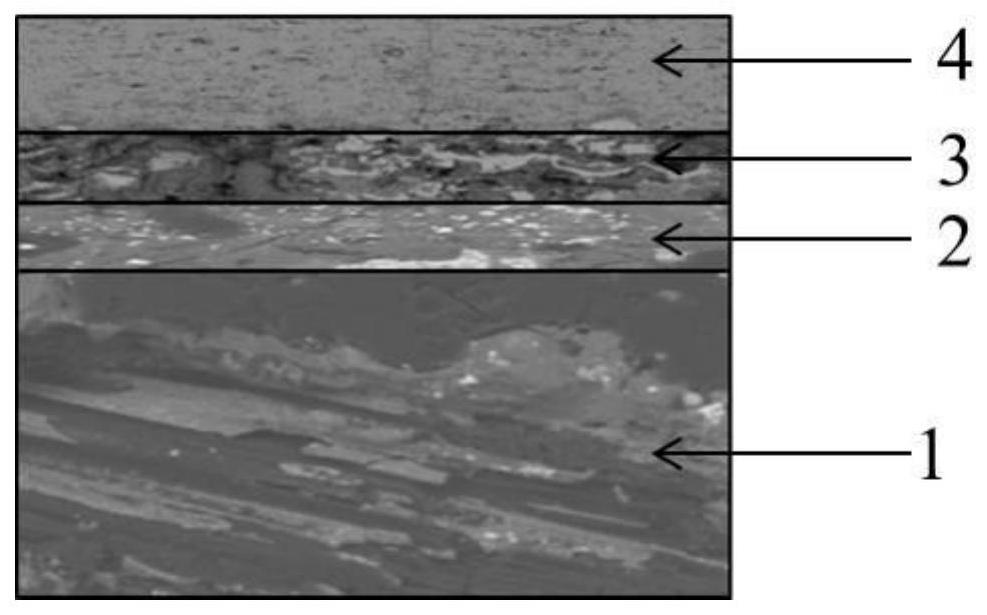
1.本发明涉及超高温热防护涂层制备技术领域,尤其涉及一种陶瓷基复合材料的热防护涂层及其制备方法和应用。
背景技术:2.目前陶瓷基复合材料已经广泛应用于航空、航天飞行器的燃烧室、调节片、翼前缘等高温部件,长时间工作温度已经提高到2200℃甚至更高。由于无防护涂层的陶瓷基复合材料在高温及水氧环境中性能将严重退化,因此超高温热防护涂层对于陶瓷基复合材料的超高温应用十分必要。
3.cn111718208a公开了一种陶瓷基复合材料用耐高温涂层的制备方法,以正硅酸乙酯和n,n-二甲基甲酰胺分别作为抗凝胶剂和分散剂,采用浸渍-模压低温凝胶化-高温裂解工艺在陶瓷基复合材料表面得到涂层。该涂层仅适用于平板或者规则结构的复合材料表面的热防护,无法应用于复杂结构的样件。该涂层主要成分为碳化硅,有效使用温度不超过2200℃。
4.cn109987971a公开了碳纤维增强碳化硅陶瓷基复合材料表面中高温长时间抗氧化涂层,采用化学气相沉积工艺在碳化硅陶瓷基复合材料表面沉积碳化硅内层;以氧化硼、硼化锆、碳化硅、二氧化硅和氧化铝为涂层原料,硅溶胶为粘接剂,采用涂刷-烧结工艺在碳化硅内层上制备zrb
2-sic基中间层;再利用化学气相沉积工艺在中间层表面制备sic外层,最终得到sic/zrb
2-sic/sic复合抗氧化涂层。该涂层主要应用于复合材料的抗氧化,主要成分为碳化硅,有效使用温度不超过2200℃。
5.cn114773075a公开了具有la/y掺杂zrc-sic涂层的超高温陶瓷基复合材料,采用梯度包埋法,将不同成分的包埋粉进行梯度设置,利用硅锆合金熔体与碳基体的反应及硅锆合金熔体与氧化镧/氧化钇(la2o3/y2o3)和碳粉混合物之间的反应,一步反应制备了具有la/y掺杂zrc-sic涂层的c/zrc-sic超高温陶瓷基复合材料,得到的材料基体具有多种超高温陶瓷组分,同时材料表面原位反应生成耐烧蚀涂层。该涂层主要成分为碳化硅,有效使用温度不超过2500℃,涂层较薄,不耐高温冲刷。
6.综上,目前陶瓷基复合材料表面有bsas(bao-sro-al2o
3-sio2)涂层、稀土硅酸盐涂层等,工作温度不高于2500℃,且工作寿命很短。
技术实现要素:7.鉴于现有技术中存在的问题,本发明提供一种陶瓷基复合材料的热防护涂层及其制备方法和应用,把功能不同的封孔、抗氧化、隔热耐烧层结合起来,发挥各自优势,形成三层结构的复合涂层体系,本发明的超高温热防护涂层可应用于陶瓷基复合材料超高温部件的热防护。
8.为达此目的,本发明采用以下技术方案:
9.第一方面,本发明提供一种陶瓷基复合材料的热防护涂层,所述热防护涂层包括
依次设置在陶瓷基复合材料表面的封孔层、硅基抗氧化粘接层和隔热耐烧层;
10.所述封孔层中含有w、si、y和hf;
11.所述硅基抗氧化粘接层中含有金属组分,所述金属组分包括zr元素和/或y元素;
12.所述隔热耐烧层为yb2o3和cao共掺杂的hfo2材料层。
13.本发明提供的热防护涂层首先包括封孔层,这是由于陶瓷基复合材料中一般含有多孔结构,经高温热处理后w-si-y-hf封孔层,可大幅减少陶瓷基复合材料表面的开孔率,解决陶瓷基复合材料普遍存在的封闭腔体结构贯穿孔缺陷的问题;而进一步采用包括zr元素和/或y元素的硅基抗氧化粘接层能够改善陶瓷基体与后续隔热耐烧成之间的界面匹配性,提高了涂层与基体的结合强度,同时具备高温下阻止氧原子的扩散和侵入、防止基体元素逸出的功能;稀土氧化钇(yb2o3)和氧化钙(cao)共掺杂氧化铪(hfo2)隔热耐烧层降低了陶瓷基复合材料表面温度,通过选择yb2o3和cao共掺杂的hfo2材料层,能够防止hfo2在高温下发生相变导致体积发生变化,而且能够防止喷涂过程中粉化喷涂效果不佳的情况,隔热耐烧层能够防止陶瓷基复合材料高温条件下性能退化,减少了涂层在高速气流中的烧蚀损失,且可阻止氧元素向涂层体系内部扩散渗透。
14.优选地,所述封孔层中w:si:y:hf的质量比为1:1.5~2.5:0.9~1.1:0.9~1.1,例如可以是1:1.5:0.9:0.9、1:2.5:0.9:0.9、1:1.8:0.9:0.9、1:1.5:1.1:0.9、1:1.5:0.9:1.0、1:1.5:0.9:1.1、1:1.8:1.0:0.9、1:1.7:0.9:0.9或1:1.5:1.1:0.9等。
15.本发明进一步优选封孔层中w:si:y:hf的质量比在上述范围内,一方面更有利于将封孔层的材料通入陶瓷基体材料的孔隙中;另一方面,其与硅基抗氧化粘接层更具相容性。
16.优选地,所述硅基抗氧化粘接层中金属组分的质量分数为40~55%,例如可以是40%、42%、43%、45%、47%、48%、50%、51%、52%或55%等。
17.优选地,所述硅基抗氧化粘接层中锆与钇的摩尔比为0.8~0.9:1,例如可以是0.8:1、0.82:1、0.83:1、0.84:1、0.85:1、0.86:1、0.87:1、0.88:1或0.9:1等。
18.本发明进一步优选硅基抗氧化粘接层中锆与钇的摩尔比为0.8~0.9:1,将二者的配比严格控制,能够更好地与封孔层和隔热耐烧层相容,提高涂层的耐热性能。
19.优选地,所述隔热耐烧层中yb2o3的摩尔分数为8~10%,例如可以是8%、8.3%、8.5%、8.7%、8.9%、9.2%、9.4%、9.6%、9.8%或10%等,但不限于所列举的数值,该范围内其他未列举的数值同样适用。
20.优选地,所述隔热耐烧层中cao的摩尔分数为3~5%,例如可以是3%、3.3%、3.5%、3.7%、3.9%、4.2%、4.4%、4.6%、4.8%或5%等,但不限于所列举的数值,该范围内其他未列举的数值同样适用。
21.优选地,所述隔热耐烧层中yb2o3和cao的摩尔比为1.9~2.5:1,例如可以是1.9:1、2.0:1、2.1:1、2.2:1、2.4:1或2.5:1等,但不限于所列举的数值,该范围内其他未列举的数值同样适用。
22.本发明进一步优选隔热耐烧层中yb2o3和cao的摩尔分数在上述范围并优选二者的摩尔比为1.9~2.5:1,具有更佳的耐热隔热效果。以hfo2为主要隔热耐烧物质,但hfo2在高温下容易出现晶相转变,而这种晶相的转变易导致体积的变化,从而引起隔热耐烧层的开裂等情况,而yb2o3和cao复配作为稳定剂,优选摩尔比为1.9~2.5:1,更有利于在超高温条
件下稳定hfo2,最终提高隔热耐烧层的耐热温度,而且需要考虑到与硅基抗氧化粘接层的相容性,选择yb2o3和cao复配作为稳定剂协同效果更佳。
23.优选地,所述隔热耐烧层中hfo2的摩尔分数为85~89%,例如可以是85%、85.5%、85.9%、86.4%、86.8%、87.3%、87.7%、88.2%、88.6%或89%等,但不限于所列举的数值,该范围内其他未列举的数值同样适用。
24.优选地,所述陶瓷基复合材料的组成包括碳纤维增强陶瓷材料。
25.本发明对所述碳纤维增强陶瓷材料的碳纤维增强方式等没有特殊限制,采用本领域技术人员熟知的碳纤维增强陶瓷材料即可,具体可参考文献dewei ni,yuan cheng,jiaping zhang,ji-xuan liu,ji zou,bowen chen,haoyang wu,hejun li,shaoming dong,jiecai han,xinghong zhang,qiangang fu,guo-jun zhang.advances in ultra-high temperature ceramics,composites,and coatings[j].先进陶瓷(英文),2022,11(1):1-56,例如可以采用t300增强陶瓷材料、t700增强陶瓷材料或t800增强陶瓷材料等,或者是采用cn 111454073 a或cn113526972a中记载的碳纤维增强陶瓷材料。
[0026]
优选地,所述陶瓷材料包括碳化硅、碳化锆、碳化铪、碳化钽、硼化钽、硼化锆或硼化铪中的任意一种或至少两种的组合,其中典型但非限制性的组合为碳化硅和碳化锆的组合,碳化铪和碳化锆的组合,碳化硅和碳化铪的组合,碳化钽和碳化锆的组合,硼化钽和硼化铪的组合。
[0027]
本发明所述涂层更优适用于碳纤维增强陶瓷的陶瓷基复合材料,优选组成的硅基抗氧化粘接层与碳纤维增强陶瓷更具相容性。
[0028]
优选地,所述封孔层的厚度为0.1~0.2mm,例如可以是0.1mm、0.12mm、0.13mm、0.14mm、0.15mm、0.16mm、0.17mm、0.18mm、0.19mm或0.2mm等,但不限于所列举的数值,该范围内其他未列举的数值同样适用。
[0029]
优选地,所述硅基抗氧化粘接层的厚度为0.1~0.2mm,例如可以是0.1mm、0.12mm、0.13mm、0.14mm、0.15mm、0.16mm、0.17mm、0.18mm、0.19mm或0.2mm等,但不限于所列举的数值,该范围内其他未列举的数值同样适用。
[0030]
优选地,所述隔热耐烧层的厚度为0.2~0.5mm,例如可以是0.2mm、0.24mm、0.27mm、0.3mm、0.34mm、0.37mm、0.4mm、0.44mm、0.47mm或0.5mm等,但不限于所列举的数值,该范围内其他未列举的数值同样适用。
[0031]
第二方面,本发明提供一种第一方面所述的陶瓷基复合材料的热防护涂层的制备方法,所述制备方法包括如下步骤:
[0032]
(1)在陶瓷基复合材料的表面第一喷涂封孔层并经热处理;
[0033]
(2)在所述封孔层的表面第二喷涂硅基抗氧化粘接层;
[0034]
(3)在所述硅基抗氧化粘接层的表面第三喷涂隔热耐烧层。
[0035]
本发明第二方面提供的制备方法仅通过采用喷涂即可制得热防护涂层,制备工艺简单,流程短;而且通过依次喷涂封孔层、硅基抗氧化粘接层和隔热耐烧层,显著提高了陶瓷基复合材料的耐烧性能。
[0036]
优选地,步骤(1)中所述第一喷涂的方式包括大气等离子喷涂。
[0037]
优选地,所述第一喷涂采用的粉末的粒径为40~150μm,例如可以是40μm、53μm、65μm、77μm、89μm、102μm、114μm、126μm、138μm或150μm等,但不限于所列举的数值,该范围内其
他未列举的数值同样适用。
[0038]
优选地,所述第一喷涂的功率为25~35kw,例如可以是25kw、27kw、28kw、29kw、30kw、31kw、32kw、33kw、34kw或35kw等,但不限于所列举的数值,该范围内其他未列举的数值同样适用。
[0039]
优选地,所述第一喷涂的送粉速率35~45g/min,例如可以是35g/min、37g/min、38g/min、39g/min、40g/min、41g/min、42g/min、43g/min、44g/min或45g/min等,但不限于所列举的数值,该范围内其他未列举的数值同样适用。
[0040]
优选地,所述第一喷涂的距离为80~120mm,例如可以是80mm、85mm、89mm、94mm、98mm、103mm、107mm、112mm、116mm或120mm等,但不限于所列举的数值,该范围内其他未列举的数值同样适用。
[0041]
优选地,所述热处理的温度为1000~1500℃,例如可以是1000℃、1050℃、1110℃、1160℃、1220℃、1270℃、1330℃、1380℃、1440℃或1500℃等,但不限于所列举的数值,该范围内其他未列举的数值同样适用。
[0042]
优选地,步骤(2)中所述第二喷涂的方式包括大气等离子喷涂。
[0043]
优选地,所述第二喷涂采用的粉末的粒径为40~150μm,例如可以是40μm、53μm、65μm、77μm、89μm、102μm、114μm、126μm、138μm或150μm等,但不限于所列举的数值,该范围内其他未列举的数值同样适用。
[0044]
优选地,所述第二喷涂中金属组分的硅粉的体积分数为40~60%,例如可以是40%、43%、45%、47%、49%、52%、54%、56%、58%或60%等,但不限于所列举的数值,该范围内其他未列举的数值同样适用。
[0045]
本发明进一步优选除钨外其他金属元素的硅粉末的体积分数在上述范围,具有提高粘接层氧化后的高温粘度,降低粘接层与隔热耐烧层的热膨胀不匹配产生的应力的效果,当zr元素或y元素含量过高时,具有粘接层不抗氧化、热膨胀系数不匹配等现象,当zr元素或y元素含量过低时,具有粘接层氧化产物高温粘度低造成局部产生孔洞的问题,隔热耐烧层局部会因热应力过大而失效。
[0046]
优选地,步骤(2)中所述喷涂中粉末包括硅钨粉末粉末和其他金属的硅粉末。
[0047]
优选地,所述其他金属的硅粉末包括硅锆粉末和/或硅钇粉末。
[0048]
本发明优选采用硅钨粉末粉末和其他金属的硅粉末进行喷涂,相较于采用硅钨粉末粉末和金属单质粉末进行喷涂而言,本发明的基体为钨元素,其他主要元素为硅元素,在钨硅基中掺杂锆或钇,通过硅基粉末进行送粉和喷涂,与陶瓷基体材料具有更佳的相容性。
[0049]
优选地,所述第二喷涂的功率为25~30kw,例如可以是25kw、27kw、28kw、29kw、30kw、31kw、32kw、33kw、34kw或35kw等,但不限于所列举的数值,该范围内其他未列举的数值同样适用。
[0050]
优选地,所述第二喷涂的送粉速率30~40g/min,例如可以是30g/min、32g/min、33g/min、34g/min、35g/min、36g/min、37g/min、38g/min、39g/min或40g/min等,但不限于所列举的数值,该范围内其他未列举的数值同样适用。
[0051]
优选地,所述第二喷涂的距离为80~120mm,例如可以是80mm、85mm、89mm、94mm、98mm、103mm、107mm、112mm、116mm或120mm等,但不限于所列举的数值,该范围内其他未列举的数值同样适用。
[0052]
优选地,步骤(3)中所述第三喷涂的方式包括大气等离子喷涂。
[0053]
优选地,所述第三喷涂采用的粉末的粒径为40~150μm,例如可以是40μm、53μm、65μm、77μm、89μm、102μm、114μm、126μm、138μm或150μm等,但不限于所列举的数值,该范围内其他未列举的数值同样适用。
[0054]
优选地,所述第三喷涂的功率为35~40kw,例如可以是35kw、36kw、37kw、38kw、39kw或40kw等,但不限于所列举的数值,该范围内其他未列举的数值同样适用。
[0055]
优选地,所述第三喷涂的送粉速率35~45g/min,例如可以是35g/min、37g/min、38g/min、39g/min、40g/min、41g/min、42g/min、43g/min、44g/min或45g/min等,但不限于所列举的数值,该范围内其他未列举的数值同样适用。
[0056]
优选地,所述第三喷涂的距离为80~100mm,例如可以是80mm、83mm、85mm、87mm、89mm、92mm、94mm、96mm、98mm或100mm等,但不限于所列举的数值,该范围内其他未列举的数值同样适用。
[0057]
优选地,步骤(3)中所述送粉中粉末包括yb2o3粉末、cao粉末和hfo2粉末。
[0058]
优选地,所述制备方法还包括:在对陶瓷基复合材料表面进行喷涂之前,对陶瓷基复合材料的喷涂面进行预处理。
[0059]
优选地,所述预处理包括先采用压缩空气清理所述喷涂面,再进行喷砂处理。
[0060]
优选地,所述压缩空气的压力为0.15~0.25mpa,例如可以是0.15mpa、0.16mpa、0.17mpa、0.18mpa、0.19mpa、0.2mpa、0.21mpa、0.22mpa、0.23mpa或0.25mpa等。
[0061]
优选地,所述喷砂处理采用-80目至+325目的金刚砂。
[0062]
优选地,所述喷砂处理的喷枪与试片的喷砂角度为50
°
~60
°
,例如可以是50
°
、51
°
、52
°
、53
°
、54
°
、55
°
、57
°
、58
°
或60
°
等。
[0063]
作为本发明优选地技术方案,所述制备方法包括如下步骤:
[0064]
(1)在陶瓷基复合材料的表面第一喷涂封孔层,喷涂的功率为25~35kw,送粉速率35~45g/min,喷涂的距离为80~120mm,并经1000~1500℃热处理;
[0065]
(2)在所述封孔层的表面第二喷涂硅基抗氧化粘接层,喷涂的功率为25~30kw,送粉速率30~40g/min,喷涂的距离为80~120mm;
[0066]
(3)在所述硅基抗氧化粘接层的表面第三喷涂隔热耐烧层,喷涂的功率为35~40kw,送粉速率35~45g/min,喷涂的距离为80~100mm。
[0067]
第三方面,本发明提供一种第一方面所述的陶瓷基复合材料的热防护涂层在航空航天、飞行器、调节片或翼前缘领域中的用途。
[0068]
本发明提供的热防护涂层由于能够耐2700℃高温,因此在上述用途中能够起到隔热耐烧的作用。
[0069]
与现有技术相比,本发明至少具有以下有益效果:
[0070]
(1)本发明提供的陶瓷基复合材料的热防护涂层把功能不同的封孔、抗氧化、隔热、耐烧蚀涂层结合起来,发挥各自优势,形成三层结构的复合涂层体系,优选条件下在2700℃条件下放置300s仍然能够保持良好的基体和涂层结构完整,耐温效果佳;
[0071]
(2)本发明提供的陶瓷基复合材料的热防护涂层的制备方法流程短,制备工艺简单,适合大规模生产;
[0072]
(3)本发明提供的陶瓷基复合材料的热防护涂层可应用于陶瓷基复合材料超高温
部件的热防护,适用于应用在航空航天、飞行器、调节片或翼前缘领域中。
附图说明
[0073]
图1是本发明实施例1提供的热防护涂层的结构示意图。
[0074]
图2是本发明实施例1制得的热防护涂层经2700℃烧蚀后的表面图。
[0075]
图中:1-陶瓷基复合材料;2-封孔层;3-硅基抗氧化粘接层;4-隔热耐烧层。
具体实施方式
[0076]
下面结合附图并通过具体实施方式来进一步说明本发明的技术方案。
[0077]
下面对本发明进一步详细说明。但下述的实例仅仅是本发明的简易例子,并不代表或限制本发明的权利保护范围,本发明的保护范围以权利要求书为准。
[0078]
需要说明的是,在本发明的描述中,除非另有明确的规定和限定,术语“设置”、“相连”、“连接”应做广义理解,例如,可以是固定连接,也可以是可拆卸连接,或一体连接;可以是机械连接,也可以是电连接;可以是直接相连,也可以通过中间媒介间接相连,可以是两个元件内部的连通。对于本领域的普通技术人员而言,可以通过具体情况理解上述术语在本发明中的具体含义。
[0079]
作为本发明的一个具体实施方式,提供一种陶瓷基复合材料的热防护涂层,所述热防护涂层包括依次设置在陶瓷基复合材料表面的封孔层、硅基抗氧化粘接层和隔热耐烧层;所述封孔层中含有w、si、y和hf;所述硅基抗氧化粘接层中含有金属组分,所述金属组分包括zr元素和/或y元素;所述隔热耐烧层为yb2o3和cao共掺杂的hfo2材料层。
[0080]
所述封孔层中w:si:y:hf的质量比为1:1.5~2.5:0.9~1.1:0.9~1.1。所述隔热耐烧层中yb2o3的摩尔分数为8~10%,cao的摩尔分数为3~5%,hfo2的摩尔分数为85~89%。
[0081]
所述陶瓷基复合材料的组成包括碳纤维增强碳化硅或碳纤维增强碳化锆。
[0082]
所述封孔层的厚度为0.1~0.2mm;所述硅基抗氧化粘接层的厚度为0.1~0.2mm;所述隔热耐烧层的厚度为0.2~0.5mm。
[0083]
作为本发明的另一个具体实施方式,提供一种陶瓷基复合材料的热防护涂层的制备方法,所述制备方法包括如下步骤:
[0084]
(1)在陶瓷基复合材料的表面第一喷涂封孔层,喷涂的功率为25~35kw,送粉速率35~45g/min,喷涂的距离为80~120mm,并经1000~1500℃热处理;
[0085]
(2)在所述封孔层的表面第二喷涂硅基抗氧化粘接层,喷涂的功率为25~30kw,送粉速率30~40g/min,喷涂的距离为80~120mm;
[0086]
(3)在所述硅基抗氧化粘接层的表面第三喷涂隔热耐烧层,喷涂的功率为35~40kw,送粉速率35~45g/min,喷涂的距离为80~100mm。
[0087]
下面对本发明进一步详细说明。但下述的实例仅仅是本发明的简易例子,并不代表或限制本发明的权利保护范围,本发明的保护范围以权利要求书为准。
[0088]
实施例1
[0089]
本实施例提供一种陶瓷基复合材料的热防护涂层,如图1所示,所述热防护涂层包括依次设置在陶瓷基复合材料1表面的封孔层2、硅基抗氧化粘接层3和隔热耐烧层4;所述
封孔层中含有w、si、y和hf;所述硅基抗氧化粘接层中含有金属组分,所述金属组分包括zr元素和/或y元素;所述隔热耐烧层为yb2o3和cao共掺杂的hfo2材料层。
[0090]
所述封孔层中w:si:y:hf的质量比为1:2.0:1.0:1.0。所述隔热耐烧层中yb2o3的摩尔分数为9%,cao的摩尔分数为4%,hfo2的摩尔分数为87%。
[0091]
所述陶瓷基复合材料的组成包括碳纤维增强碳化硅硼化锆复合材料(具体可参考文献sun q,zhang h f,huang c b,zhang w g*.fabrication of c/c
–
sic
–
zrb
2 ultra-high temperature composites through liquid
–
solid chemical reaction[j].crystals,2021,11(11):1352.)。
[0092]
所述封孔层的厚度为0.15mm;所述硅基抗氧化粘接层的厚度为0.15mm;所述隔热耐烧层的厚度为0.3mm。
[0093]
本实施例还提供所述陶瓷基复合材料的热防护涂层的制备方法,所述制备方法包括如下步骤:
[0094]
(1)用干燥清洁的压缩空气清理陶瓷基复合材料表面,使用吸入式干喷砂机对材料喷涂面进行喷砂预处理,用-80目至100目的金刚砂,喷枪与试片的喷砂角度为55
°
,空气压缩机的压力为0.16mpa;
[0095]
在陶瓷基复合材料的表面第一喷涂封孔层,封孔层中喷涂钨硅合金粉(钨含量54wt%)、硅钇合金粉(钇含量45wt%)和硅铪合金粉(铪含量52wt%),粉末的粒径为40~120μm,喷涂的功率为28kw,送粉速率38g/min,喷涂的距离为100mm,并经1200℃热处理;
[0096]
(2)在所述封孔层的表面第二喷涂硅基抗氧化粘接层,基础粉末为硅钨粉末,掺有硅锆粉末(锆含量42wt%)和硅钇粉末(钇含量45wt%)(锆与钇摩尔比0.85:1),硅锆粉末和硅钇粉末的体积占比达55%,粉末的粒径为70~150μm,喷涂的功率为28kw,送粉速率30g/min,喷涂的距离为100mm;
[0097]
(3)在所述硅基抗氧化粘接层的表面第三喷涂隔热耐烧层,粉末为9%的yb2o3,4%的cao,其余为hfo2的混合粉末,粉末的粒径为40~100μm,喷涂的功率为35kw,送粉速率35g/min,喷涂的距离为100mm。
[0098]
如图2所示,经历2700℃、300s等离子烧蚀后,涂层表面有氧化铪熔体铺展开,经空气冷却后虽有纵向裂纹产生,但涂层整体仍保持完整不脱落。
[0099]
实施例2
[0100]
本实施例提供一种陶瓷基复合材料的热防护涂层,所述热防护涂层包括依次设置在陶瓷基复合材料表面的封孔层、硅基抗氧化粘接层和隔热耐烧层;所述封孔层中含有w、si、y和hf;所述硅基抗氧化粘接层中含有金属组分,所述金属组分包括zr元素和/或y元素;所述隔热耐烧层为yb2o3和cao共掺杂的hfo2材料层。
[0101]
所述封孔层中w:si:y:hf的质量比为1:2.5:1.1:1.1。所述隔热耐烧层中yb2o3的摩尔分数为8%,cao的摩尔分数为4%,hfo2的摩尔分数为88%。
[0102]
所述陶瓷基复合材料的组成包括碳纤维增强硼化锆碳化硅复合材料(具体可参考文献wu h t,xie c m,zhang j h,zhang w g.fabrication and properties of 2d c/c-zrb
2-zrc-sic composites by hybrid precursor infiltration and pyrolysis.adv.appl.ceram.,2013,112:366-373)。
[0103]
所述封孔层的厚度为0.1mm;所述硅基抗氧化粘接层的厚度为0.2mm;所述隔热耐
烧层的厚度为0.2mm。
[0104]
本实施例还提供所述陶瓷基复合材料的热防护涂层的制备方法,所述制备方法包括如下步骤:
[0105]
(1)用干燥清洁的压缩空气清理陶瓷基复合材料表面,使用吸入式干喷砂机对材料喷涂面进行喷砂预处理,用-80目至+325目的金刚砂,喷枪与试片的喷砂角度为50
°
,空气压缩机的压力为0.20mpa;
[0106]
在陶瓷基复合材料的表面第一喷涂封孔层,封孔层中喷涂钨硅合金粉(钨含量52wt%)、硅钇合金粉(钇含量44wt%)和硅铪合金粉(铪含量50wt%),粉末的粒径为50~150μm,喷涂的功率为35kw,送粉速率35g/min,喷涂的距离为120mm,并经1500℃热处理;
[0107]
(2)在所述封孔层的表面第二喷涂硅基抗氧化粘接层,基础粉末为硅钨粉末,掺有硅锆粉末(锆含量40wt%)和硅钇粉末(钇含量44wt%)(锆与钇摩尔比0.9:1),硅锆粉末和硅钇粉末的体积占比达60%,粉末的粒径为40~120μm,喷涂的功率为25kw,送粉速率40g/min,喷涂的距离为120mm;
[0108]
(3)在所述硅基抗氧化粘接层的表面第三喷涂隔热耐烧层,粉末为8%的yb2o3,4%的cao,其余为hfo2的混合粉末,粉末的粒径为40~150μm,喷涂的功率为35kw,送粉速率45g/min,喷涂的距离为90mm。
[0109]
实施例3
[0110]
本实施例提供一种陶瓷基复合材料的热防护涂层,所述热防护涂层包括依次设置在陶瓷基复合材料表面的封孔层、硅基抗氧化粘接层和隔热耐烧层;所述封孔层中含有w、si、y和hf;所述硅基抗氧化粘接层中含有金属组分,所述金属组分包括zr元素和/或y元素;所述隔热耐烧层为yb2o3和cao共掺杂的hfo2材料层。
[0111]
所述封孔层中w:si:y:hf的质量比为1:1.5:0.9:0.9。所述隔热耐烧层中yb2o3的摩尔分数为10%,cao的摩尔分数为4.5%,hfo2的摩尔分数为85.5%。
[0112]
所述陶瓷基复合材料的组成包括碳纤维增强碳化硅碳化铪复合材料(具体可参考文献jiewen li,xi wei,min ge,weigang zhang.preparation and microstructure characterizations of novel c/c-zr(hf)b
2-zr(hf)c-sic composites.materials science forum,2014,788:593-597.)。
[0113]
所述封孔层的厚度为0.2mm;所述硅基抗氧化粘接层的厚度为0.1mm;所述隔热耐烧层的厚度为0.5mm。
[0114]
本实施例还提供所述陶瓷基复合材料的热防护涂层的制备方法,所述制备方法包括如下步骤:
[0115]
(1)用干燥清洁的压缩空气清理陶瓷基复合材料表面,使用吸入式干喷砂机对材料喷涂面进行喷砂预处理,用-80目至+325目的金刚砂,喷枪与试片的喷砂角度为60
°
,空气压缩机的压力为0.25mpa;
[0116]
在陶瓷基复合材料的表面第一喷涂封孔层,封孔层中喷涂钨硅合金粉(钨含量52wt%)、硅钇合金粉(钇含量40wt%)和硅铪合金粉(铪含量48wt%),粉末的粒径为50~120μm,喷涂的功率为25kw,送粉速率45g/min,喷涂的距离为80mm,并经1000℃热处理;
[0117]
(2)在所述封孔层的表面第二喷涂硅基抗氧化粘接层,基础粉末为硅钨粉末,掺有硅锆粉末(锆含量40wt%)和硅钇粉末(钇含量40wt%)(锆与钇摩尔比0.85:1),硅锆粉末和
硅钇粉末的体积占比达50%,粉末的粒径为40~150μm,喷涂的功率为30kw,送粉速率30g/min,喷涂的距离为80mm;
[0118]
(3)在所述硅基抗氧化粘接层的表面第三喷涂隔热耐烧层,粉末为10%的yb2o3,5%的cao,其余为hfo2的混合粉末,粉末的粒径为50~150μm,喷涂的功率为40kw,送粉速率40g/min,喷涂的距离为85mm。
[0119]
实施例4
[0120]
本实施例提供一种陶瓷基复合材料的热防护涂层,所述热防护涂层除硅基抗氧化粘接层中仅掺有硅锆粉末外,将硅钇粉末替换为硅锆粉末,其余均与实施例1相同。
[0121]
实施例5
[0122]
本实施例提供一种陶瓷基复合材料的热防护涂层,所述热防护涂层除锆与钇摩尔比为1.2:1外,其余均与实施例1相同。
[0123]
实施例6
[0124]
本实施例提供一种陶瓷基复合材料的热防护涂层,所述热防护涂层除锆与钇摩尔比为0.5:1外,其余均与实施例1相同。
[0125]
实施例7
[0126]
本实施例提供一种陶瓷基复合材料的热防护涂层,所述热防护涂层除cao的摩尔分数为3%,致使yb2o3与cao的摩尔比为3:1外,外,其余均与实施例1相同。
[0127]
实施例8
[0128]
本实施例提供一种陶瓷基复合材料的热防护涂层,所述热防护涂层除cao的摩尔分数为5%,致使yb2o3与cao的摩尔比为1.8:1外,外,其余均与实施例1相同。
[0129]
实施例9
[0130]
本实施例提供一种陶瓷基复合材料的热防护涂层,其制备方法中除掺杂锆粉、钇粉和钨粉,保持元素配比和元素的含量不变,其余均与实施例1相同。
[0131]
对比例1
[0132]
本对比例提供一种陶瓷基复合材料的热防护涂层,所述热防护涂层除隔热耐烧层不添加cao,其含量替换为yb2o3外,其余均与实施例1相同。
[0133]
对比例2
[0134]
本对比例提供一种陶瓷基复合材料的热防护涂层,所述热防护涂层除隔热耐烧层不添加yb2o3,其含量替换为cao外,其余均与实施例1相同。
[0135]
对比例3
[0136]
本对比例提供一种陶瓷基复合材料的热防护涂层,所述钨硅基抗氧化粘接层不添加zr和y外,其余均与实施例1相同。
[0137]
对比例4
[0138]
本对比例提供一种陶瓷基复合材料的热防护涂层,所述钨硅基抗氧化粘接层中zr和y全部替换为锰外,其余均与实施例1相同。
[0139]
对比例5
[0140]
本对比例提供一种陶瓷基复合材料的热防护涂层,所述钨硅基抗氧化粘接层中zr和y全部替换为钴外,其余均与实施例1相同。
[0141]
对比例6
[0142]
本对比例提供一种陶瓷基复合材料的热防护涂层,除不设置封孔层外,其余均与实施例1相同。
[0143]
测试方法:将上述制得的材料在2700℃条件下放置300s,观察其烧蚀表面的情况。
[0144]
以上实施例和对比例的测试结果如表1所示。
[0145]
表1
[0146][0147][0148]
从表1可以看出如下几点:
[0149]
(1)综合实施例1~3可以看出,本发明提供的陶瓷基复合材料的热防护涂层在2700℃条件下放置300s仍然能够保持烧蚀后表面完整无脱落,耐受情况良好;
[0150]
(2)综合实施例1和实施例4可以看出,实施例1在硅基抗氧化粘接层中同时掺杂硅锆粉末和硅钇粉末,相较于实施例4中仅掺杂有硅锆粉末而言,实施例1中烧蚀后表面形貌仅轻微熔融,且涂层仍然完整无脱落现象,而实施例4中出现烧蚀中心部分脱落的情况,难以耐烧2700℃高温,由此表明,本发明优选同时掺杂锆和钇,进一步提升了涂层的隔热耐烧性能;
[0151]
(3)综合实施例1和实施例5~6可以看出,实施例1中锆与钇摩尔比为0.85:1,相较
于实施例5~6中摩尔比分别为1.2:1和0.5:1而言,实施例1中热防护涂层经2700℃烧蚀后的表面形貌明显优于实施例5~6,由此表明,本发明优选将锆与钇摩尔比控制在特定范围,更好地提高了硅基抗氧化粘接层与封孔层以及隔热耐烧层的相容性,从而进一步提升了整体热防护涂层的隔热耐烧性能;
[0152]
(4)综合实施例1和实施例7~8可以看出,隔热耐烧层中yb2o3与cao的摩尔比对于涂层的耐烧蚀性能影响显著,本发明优选控制yb2o3与cao的摩尔比,能够避免2700℃条件下涂层严重烧蚀出现孔洞的情况,优化了热防护涂层的性能;
[0153]
(5)综合实施例1和实施例9可以看出,实施例1中采用钨锆粉末、钨钇粉末进行喷涂,相较于实施例9中采用相同配比的锆粉、钇粉和钨粉进行喷涂而言,实施例1中烧蚀后涂层完整无脱落现象,而实施例9中涂层整体脱落,不耐受2700℃高温,由此表明,除了各层的配比外,在喷涂硅基抗氧化粘接层中采用钨锆粉末、钨钇粉末才能得到更加均匀分布且各组分相容性良好的硅基抗氧化粘接层,保障最终热防护涂层不脱落;
[0154]
(6)综合实施例1和对比例1~2可以看出,隔热耐烧层中同时掺杂cao和yb2o3才能耐2700℃高温;同样综合实施例1和对比例3~5可以看出,硅基抗氧化粘接层中不添加zr和y,或者替换为其他元素后,均出现涂层直接脱落的情况,由此表明,本发明通过优化隔热耐烧层和硅基抗氧化粘接层的组成,提高了热防护涂层的耐热效果;
[0155]
(7)综合实施例1和对比例6可以看出,对比例6中不设置封孔层,导致硅基抗氧化粘接层难以与多孔的陶瓷复合材料良好相接,经2700℃烧蚀后出现涂层脱落现象。
[0156]
申请人声明,本发明通过上述实施例来说明本发明的详细工艺流程,但本发明并不局限于上述详细工艺流程,即不意味着本发明必须依赖上述详细工艺流程才能实施。所属技术领域的技术人员应该明了,对本发明的任何改进,对本发明产品各原料的等效替换及辅助成分的添加、具体方式的选择等,均落在本发明的保护范围和公开范围之内。