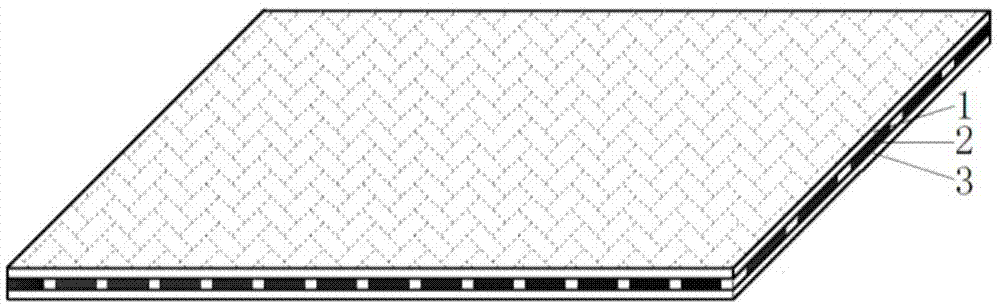
本发明涉及一种钢质管道表面修复领域的一种聚酰亚胺纤维预浸料及其制备方法以及应用。
背景技术:
管道运输是油气运输方式中最为理想的一种方式。据统计,目前我国陆上长输油气管道总里程已达到12万公里以上。但这些埋地管道通常会因土壤腐蚀、机械损伤、电偶腐蚀等原因产生许多缺陷,随着服役时间的延长,这些缺陷还会不断发展,管道的承压能力逐渐下降,从而给管道的安全运行造成威胁,严重影响在役管道的输送能力和使用寿命。如何对这些含缺陷管道进行有效地修复补强或增强是确保油气管线安全运行和提高油气集输效益的关键技术措施。目前,国内外对缺陷管道进行修复补强通常采取的方法可概括为三大类:1)焊接:堆焊、补疤、打套筒;2)夹具:夹具注环氧、夹具;3)粘贴纤维复合材料:玻璃纤维或碳纤维等复合材料修复体系。焊接类修复方法对施工工艺要求严格,具有焊穿和氢脆等风险,并且油气管线需要停输特别是气管线需要排空才能进行修复,从而产生巨大的经济损失;夹具类修复方法主要适用于对已发生泄漏的管线进行临时抢修,成本高昂;复合材料修复技术作为一种新型的缺陷管道永久性修复方法,具有不动火、不停输、现场施工简便、修复时间短、工程成本较低、适用于各种作业环境、耐腐蚀性和可设计强等优点,得到国内外油气公司的逐渐关注,近年来已在管道领域得到广泛的应用并且加固效果比较理想。含缺陷管道复合材料修复技术主要分为三种:预成型法、湿缠绕法、预浸渍法。前两种修复方法是国内外各个修复补强公司研究开发和在实际应用中使用较多的管道修复补强方式。预成型法是采用树脂和增强纤维在工厂预制成复合材料套筒,材料自身刚度较大,现场施工时难与钢管紧密贴合,影响整体的修复效果,并且只能修复直管不能修复异型件;湿缠绕法是在施工现场将树脂体系涂刷在柔性纤维布上,然后在钢管上进行绕包并固化,因为需要在现场配制胶液并对纤维进行浸渍,受制于施工人员熟练程度、施工环境等原因,容易出现胶黏剂搅拌不均、涂刷不均匀、树脂对纤维的浸润不好,树脂与纤维的比例不可控等问题,这就造成固化后复合材料的力学性能不稳定,修复层的有效性和持久性具有很大的不确定性。预浸渍法能够完美解决上述问题,实现修补质量、适用范围和效率三者的统一,预浸渍法是以增强纤维和可固化聚合物为原料,采用预浸机使可固化聚合物处于溶液状态或加热熔融状态,在一定温度、速度和压力下对纤维进行浸润,得到表面由聚合物包裹的纤维增强体,此时预浸料中的聚合物还处于未固化状态,在一定的加热、加压条件下可最终固化成为复合材料。在现有技术中,修复补强用复合材料中的增强纤维主要采用碳纤维、玻璃纤维和芳纶纤维,能够有效恢复缺陷管道的原承压能力。但是,在使用过程中,玻璃纤维密度较高,比强度和比模量较低,同样修复补强条件下所需的修复层厚度较大;而碳纤维具有优异的导电性能,容易产生电偶腐蚀对管道造成二次腐蚀破坏;芳纶纤维的耐水性较差,在湿环境中容易吸收水份(吸湿率可达7%),水份的存在使纤维结构变得松散从而加速复合材料的失效,导致修复后的管道使用寿命无法得到保障,另外芳纶纤维的耐紫外辐照性能差从而也限制其在管道补强修复方面的应用。技术实现要素:本发明解决的技术问题是提供一种有效提高管道修复效果的一种聚酰亚胺纤维预浸料。本发明解决其技术问题所采用的技术方案是:一种聚酰亚胺纤维预浸料,包括增强材料和可固化聚合物;所述可固化聚合物按质量份数包括:液体环氧树脂40~80份,固体环氧树脂20~60份,改性双酚a环氧树脂10~30份,煅烧法氧化铝粉30~100份,潜伏性固化剂6~12份,固化促进剂1~5份;所述增强材料为聚酰亚胺纤维布。该申请利用可固化聚合物与增强材料相结合形成用于修复管道的聚酰亚胺纤维预浸料,该预浸料可在工厂进行自动化生产,减少了人为因素的影响,生产效率较高,同时树脂体系对纤维的浸润性好,修补材料的质量稳定性好,从而能充分发挥材料的性能,保证了修补的质量。此外,聚酰亚胺纤维具有优异的耐高低温性能、高比强度、高比模量、高抗蠕变性、高尺寸稳定性、高电绝缘性、耐紫外辐照、低吸水率和耐腐蚀性等特性,能有效保证对缺陷管道的修复效果,可作为一种永久性修复方法。进一步的是,所述煅烧法氧化铝粉的粒径为200-1250目;所述聚酰亚胺纤维布为双向聚酰亚胺纤维布。进一步的是,所述聚酰亚胺纤维布进行提高与树脂结合性能的有机纤维表面改性处理。一种聚酰亚胺纤维预浸料的制备方法,所述制备步骤如下:a)根据权利要求1所述的一种聚酰亚胺纤维预浸料进行原材料的准备;b)将液体环氧树脂和固体环氧树脂混合并加热搅拌均匀形成胶液,加热温度为70~90℃;c)将煅烧法氧化铝粉填料加入步骤b)生成的胶液中并充分搅拌均匀;d)将潜伏性固化剂加入步骤c)生成的胶液中并搅拌均匀;e)将步骤d)生成的胶液温度降低至50~70℃,加入固化促进剂并搅拌均匀;f)将改性双酚a型环氧树脂加入步骤e)生产产品中,搅拌均匀后制得可固化聚合物;g)将聚酰亚胺纤维布进行有机纤维表面改性处理;h)将步骤f)生成的可固化聚合物,根据实际需求进行涂胶设备的参数设置,制得一种可固化聚合物胶膜;i)根据实际需求进行浸胶设备的参数设置,将步骤g)处理完成的聚酰亚胺纤维布和步骤h)得到的可固化聚合物胶膜通过浸胶设备进行复合,制得一种聚酰亚胺纤维预浸料。一种采用聚酰亚胺纤维预浸料的应用,其操作步骤如下:a)清理待修复管道的表面,采用机械打磨或喷砂的方式除去管道表面的氧化物和杂质,对于腐蚀严重的管道可采用除锈剂对管壁进行除锈之后用砂纸做表面处理;b)利用专用补强腻子对因腐蚀、机械损伤造成的体积型缺陷处进行填平处理;c)在管道需要修复的区域涂刷抗阴极剥离底漆;d)根据管道的缺陷类型和程度,参照asmepcc-2或iso/ts24817标准计算修复管道所需的预浸料层数,然后利用聚酰亚胺纤维预浸料在管道待修复区进行相应的缠绕或铺贴;e)对聚酰亚胺纤维预浸料进行加热和真空辅助固化,抽真空时间为10~40min,待可固化聚合物初步固化后即可停止抽真空,在温度为80~120℃的条件下进行时间为1~3小时的固化操作;f)对聚酰亚胺纤维复合材料的表面采用外防腐材料进行防腐处理,管道修复完成。进一步的是,所述步骤b)中的专用补强腻子由组分a和组分b组成,所述专用补强腻子按质量份数包括:组分a为3~5份,所述组分b为1份;所述组分a按质量百分比包括:双酚a环氧树脂25~45%,酚醛环氧树脂15~25%,煅烧法氧化铝粉20~40%,沉淀法硫酸钡10~20%,气相法二氧化硅3~10%,碳化硅10~20%;所述组分b按质量百分比包括:改性酯环胺固化剂20~40%,改性酰胺固化剂40~55%,硅烷偶联剂5~8%,固化催化剂(dmp-30)10~15%。进一步的是,所述煅烧法氧化铝粉的粒径为200~1250目,所述沉淀法硫酸钡的粒径为800~1250目,所述碳化硅的粒径为800~1250目。进一步的是,所述步骤c)中的抗阴极剥离底漆由组分a和组分b组成,所述抗阴极剥离底漆按质量份数包括:组分a为3~5份,所述组分b为1份;所述组分a按质量百分比包括:双酚a环氧树脂35~55%,酚醛环氧树脂15~25%,绢云母10~30%,玻璃鳞片15~25%,聚硅氧烷类消泡剂0.2~0.5%;所述组分b按质量百分比包括:改性芳胺固化剂60~85%,咪唑改性胺固化剂10~35%硅烷偶联剂5~15%。进一步的是,所述绢云母的粒径为800~1250目;所述玻璃鳞片的粒径为200~400目。进一步的是,所述步骤f)中的外防腐材料为聚乙烯冷缠带、聚丙烯冷缠带、压敏胶热收缩带、聚氨酯或聚脲防腐涂料等。本发明的有益效果是:1、该预浸料易于实现在工厂进行自动化生产,减少了人为因素的影响,生产效率较高,同时树脂体系对纤维的浸润性好,修补材料的质量稳定性好,从而能充分发挥材料的性能,保证了修补的质量,此外,聚酰亚胺纤维作为一种高性能纤维,具有高比强度、高比模量、耐高低温、耐紫外辐照、低吸水率和优异的介电性能等特性,有效提高了管道修复质量;2、纤维表面改性处理使聚酰亚胺纤维的力学性能保持率在93%以上,与环氧树脂的界面剪切强度提高30%~40%,有效提高了产品质量;3、本发明采用热熔胶膜法制备聚酰亚胺纤维预浸料,减少了溶剂的使用,有利于生产人员的身体健康和环保;预浸料中挥发含量较低,制备复合材料空隙缺陷小,有利于高品质复合材料的成型;可更精确控制预浸料中树脂含量,树脂分布均匀,力学性能更好,同时易于实现高效率生产;4、本发明专用补强腻子中的氧化铝粉、沉淀法硫酸钡和碳化硅都属于刚性填料,浸润填料所需的环氧树脂较少,填充量较高,可增加修复腻子的粘度和固化后的压缩强度,有效传递管道载荷;5、绢云母和玻璃鳞片都属于片状填料,能够显著提高抗阴极剥离底漆的致密性,极大的降低外界腐蚀性介质到达抗阴极剥离底漆与钢管界面的能力,从而使涂层表现出良好的抗阴极剥离性能;6、本聚酰亚胺纤维预浸料在10℃~35℃温度下具有一定的粘性,但不流动,可保证在铺贴过程中,预浸料层与层之间以及预浸料与管体外表面之间较好地粘贴性,避免空鼓和气泡的产生,保证修复质量;7、本发明中采用加热加压方式对预浸料进行固化,能够确保在各种恶劣外界施工条件下复合材料的性能,保证了对管道修复补强或增强的效果,提高了对管道特别是油气管道进行修复补强的可靠性;综上所述,本发明采用纤维复合材料体系(聚酰亚胺纤维预浸料、专用补强腻子、抗阴极剥离底漆)对管道进行低成本、高效率、高质量修复补强或增强,不仅能为缺陷管道提供一个高质量的修复方法,同时也提供了一个完善的管道腐蚀防护解决方案。附图说明图1本发明一种聚酰亚胺纤维预浸料及其制备方法以及应用方法的聚酰亚胺纤维预浸料的结构示意图;图2本发明一种聚酰亚胺纤维预浸料及其制备方法以及应用方法的含缺陷管道修复补强后径向剖视图;图3本发明一种聚酰亚胺纤维预浸料及其制备方法以及应用方法的含缺陷管道环向缠绕补强材料结构图;图4本发明一种聚酰亚胺纤维预浸料及其制备方法以及应用方法的含缺陷管道环向两段式搭接缠绕补强材料结构图;图5本发明一种聚酰亚胺纤维预浸料及其制备方法以及应用方法的含缺陷管道环向三段式搭接缠绕补强材料结构图;图6本发明一种聚酰亚胺纤维预浸料及其制备方法以及应用方法的含缺陷管道螺旋缠绕补强材料结构图;图中标记为:上层可固化聚合物1,增强纤维2,下层可固化聚合物3,外防腐材料4,聚酰亚胺纤维复合材料5,抗阴极剥离底漆6,专用补强腻子7,管道8。具体实施方式下面结合附图和具体实施方式对本发明进一步说明。本发明用于对含缺陷油气输送管道进行修复补强的预浸料修复材料体系主要包括:修复补强用聚酰亚胺纤维预浸料、对管道缺陷处进行修复补强的专用补强腻子、抗阴极剥离底漆。修复补强用聚酰亚胺纤维预浸料幅宽优选为300mm,其中增强纤维2用聚酰亚胺纤维布为双向编织纤维布,其弹性模量为100-150gpa,抗拉强度为2500-4000mpa,单位面积重量为50-400g/m2,延伸率为2.0%至4.5%。可固化聚合物优选配方为:液体环氧树脂60份、固体环氧树脂40份、改性双酚a环氧树脂10份、煅烧法氧化铝粉50份、潜伏性固化剂8份、固化促进剂3份。可固化聚合物1和3与增强纤维2充分结合,从而形成将增强纤维2完全包裹的聚酰亚胺纤维预浸料。该聚酰亚胺纤维预浸料的制备步骤如下:a)根据上述内容进行原材料的准备;b)将液体环氧树脂和固体环氧树脂混合并加热搅拌均匀,加热温度为80℃;c)将煅烧法氧化铝粉填料加入步骤b)生成的胶液中并充分搅拌均匀;d)将潜伏性固化剂加入步骤c)生成的胶液中并搅拌均匀;e)将步骤d)生成的胶液温度降低至60℃,加入固化促进剂并搅拌均匀;f)将改性双酚a型环氧树脂加入步骤e)生产产品中,搅拌均匀后制得可固化聚合物;g)将聚酰亚胺纤维布采用碱液进行有机纤维表面改性处理;h)将步骤f)生成的可固化聚合物,根据实际需求进行涂胶设备的参数设置,制得一种合适厚度的可固化聚合物胶膜;i)根据实际需求进行浸胶设备的参数设置,将步骤g)处理完成的聚酰亚胺纤维布和步骤h)得到的可固化聚合物胶膜通过浸胶设备进行复合,制得一种聚酰亚胺纤维预浸料。该预浸料固化后形成聚酰亚胺纤维复合材料5的平均厚度为0.30mm。对缺陷管道8具体的修复补强过程如下:a)对管道8的缺陷处和缺陷周围的金属表面进行处理,参照gb/t8923.1-2011标准要求,使用电动除锈工具打磨管道表面,达到st3级的除锈要求;使用喷砂工具进行除锈,达到sa2.5的除锈要求。b)管道8的缺陷处填充专用补强腻子7,修补至缺陷表面平整。该专用腻子由组分a和组分b组成,按质量则组分a:组分b=4:1。组分a和组分b的配方按质量份数如下所示:c)待专用补强腻子7初步固化后,在管体8的修复区域表面涂刷抗阴极剥离底漆6,涂刷厚度为0.2mm,有效防止腐蚀介质对管体表面的渗透。抗阴极剥离底漆6由组分a和组分b组成,按质量则组分a:组分b=4:1。组分a和组分b的配比按质量份数如下所示:组分b:改性芳胺固化剂70份咪唑改性胺固化剂20份硅烷偶联剂10份。d)待抗阴极剥离底漆6初步固化后,根据asmepcc-2标准计算所得的修复缺陷管道所需的修复厚度和长度,在管体表面铺设或缠绕相应层数的聚酰亚胺纤维预浸料。e)修复层外缠绕透气隔离布等真空辅助固化装置,然后采用中频感应加热装置进行加热固化,抽真空时间为30min,加热温度为100℃,固化时间为3h。f)预浸料固化后,拆除加热设备及隔离布等真空辅助固化装置,现场施工时可选择性的对修复补强材料进行防腐处理,所采用的防腐外材料4为聚乙烯冷缠带。根据asmepcc-2标准要求,由管道参数、补强材料性能参数和缺陷尺寸的不同计算得到所需的修复长度和厚度。当缺陷轴向长度较大时,因修复补强材料幅宽有限,简单的包覆已不能达到理想的修复补强效果。因此针对上述问题,以下列具体实施例并结合附图来说明本发明采用聚酰亚胺纤维预浸料修复材料体系对缺陷管道进行修复补强的方法。实施例1:修复补强试验管道的相关参数如表1-1所示,自制缺陷相关参数如表2-1所示。表1-1项目管道直径管道长度管道实际壁厚管道材质参数指标457mm3500mm11mml415n表2-1管材代号缺陷环向长度缺陷轴向长度缺陷深度管壁减薄程度l415n30mm30mm5.5mm50%本发明优选的修复补强材料幅宽为300mm,根据asmepcc-2-2015设计标准要求,计算得到的修复补强层数为6层、补强层轴向总长度为300mm,因本发明的修复补强材料幅宽能满足对缺陷管道进行修复补强后补强边界宽度的要求。如图3所示可直接对缺陷处进行环向缠绕、直至缠绕至计算需要的修复层数,管道8的缺陷处于修复材料中间位置;当具有环向搭接时,环向搭接宽度要求为200mm;缠绕时要施加合适的预紧力使每层之间能够紧密贴合,另外每层缠绕完成后使用脱泡罗拉排除气泡使层与层之间粘结更好,特别是对于焊缝位置要反复滚压多次避免空鼓的产生。实施例2:修复补强试验管道的相关参数如表1-2所示,自制缺陷相关参数如表2-2所示。表1-2项目管道直径管道长度管道实际壁厚管道材质参数指标457mm3500mm11mml415n表2-2管材代号缺陷环向长度缺陷轴向长度缺陷深度管壁减薄程度l415n30mm150mm5.5mm50%本发明优选的修复补强材料幅宽为300mm,根据asmepcc-2-2015设计标准要求,计算得到的修复补强层数为6层、补强层轴向总长度为420mm,如按实施例1的环向缠绕方式对缺陷管道进行修复补强后的补强边界宽度不能满足标准的要求,因此设计了两种环向缠绕方式。图4为对含缺陷管道进行环向两段式搭接缠绕结构图。修复补强材料幅宽为300mm,如图所示缺陷处于修复材料中间位置。先在左边缺陷位置处沿着管道环向缠绕足够层数的补强材料,然后在另一边缠绕相同层数的补强材料,搭接宽度为150mm。缠绕每层补强材料时要施加合适的预紧力使每层之间能够紧密贴合,每层缠绕完成后使用脱泡罗拉沿着纤维方向反复滚压多次,确保没有空鼓现象的产生。特别是对于搭接位置,因为左边缠绕完补强材料后的管体与右边管体具有厚度差,更要仔细反复滚压多次使补强材料之间、补强材料与管体之间紧密贴合,没有空鼓产生。当具有环向搭接时,环向搭接宽度要求为200mm。图5为对含缺陷管道进行环向三段式搭接缠绕结构图。修复补强材料幅宽为300mm,如图所示缺陷处于修复材料中间位置。首先在缺陷位置的左边沿着管道环向缠绕补强材料至要求层数,然后在右边相邻位置环向缠绕同样层数的补强材料,缠绕时要施加合适的预紧力使补强材料与管体、补强材料之间能够紧密贴合,每层缠绕完成后使用脱泡罗拉反复滚压多次避免空鼓的产生,左边和右边的补强材料要紧密贴合但没有搭接。最后以前两段缠绕补强材料的相邻位置为中线缠绕相应层数的补强材料。当具有环向搭接时,环向搭接宽度要求为200mm。实施例3:修复补强试验管道的相关参数如表1-3所示,自制缺陷相关参数如表2-3所示。表1-3项目管道直径管道长度管道实际壁厚管道材质参数指标457mm3500mm11mml415n表2-3当需要修复的管道出现轴向长度较大的腐蚀缺陷时,修复补强材料幅宽为300mm,根据asmepcc-2-2015设计标准要求,计算得到的修复补强层数为6层、补强层轴向总长度为570mm,推荐使用螺旋缠绕方式对缺陷管道进行补强修复,如图6所示。具体缠绕步骤如下:1)首先在修复区域的一端(距离缺陷位置轴向距离不低于150mm处)沿着管道环向完全缠绕一层补强材料;2)完成第一圈缠绕后,向修复区域另一端螺旋缠绕补强材料直至完全包裹修复区域(缠绕结束的终点位置距离缺陷处的轴向距离最少不低于150mm)。螺旋缠绕时补强材料边缘之间紧密相贴但没有搭接,并且缠绕时要对补强材料施加一定的拉紧力使其与管道能够紧密贴合;3)每层缠绕完成后可使用脱泡罗拉沿纤维方向滚压多次,排除层间气泡避免空鼓的产生。当有环向接头时,环向搭接宽度必须在200mm以上;4)从相反方向开始第二层缠绕,在起始端沿着管道环向完全缠绕一层补强材料,然后向管道另一端螺旋缠绕补强材料直至管道修复区域被完全缠绕,相邻补强材料之间紧密贴合但没有搭接;5)需要粘贴两层以上补强材料时,重复1-4步骤。以上所述的具体实施例,对本发明的目的、技术方案和有益效果进行了进一步详细说明,所应理解的是,以上所述仅为本发明的具体实施例而已,并不用于限制本发明,凡在本发明的精神和原则之内,所做的任何修改、等同替换、改进等,均应包含在本发明的保护范围之内。当前第1页12