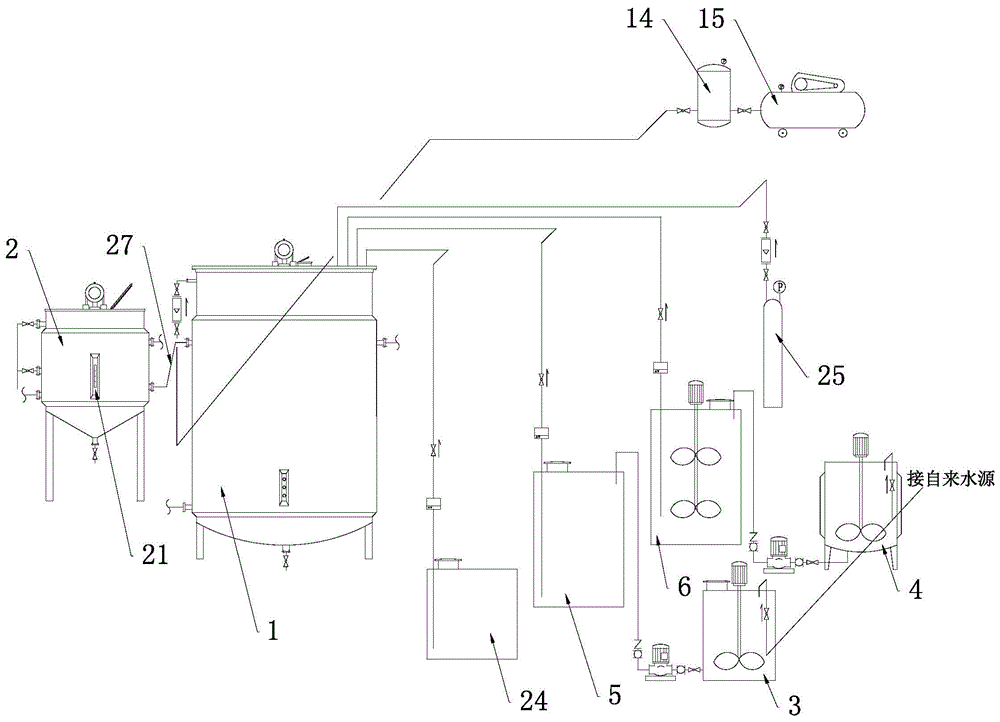
本发明涉及细菌菌剂生产
技术领域:
,尤其涉及一种硝化细菌生产工艺及装置。
背景技术:
:随着含氮化合物排放量的增加,氨氮污染对人体健康造成了严重威胁,当水体中氨浓度超过0.2mg/L,会导致鱼类血液中的蛋白质变性、造成鱼类急性死亡进而破坏生态坏境。硝化细菌制剂是一种用于控制养殖池水自生氨浓度的处理剂,不仅使用相当方便,而且能发挥立竿见影的效果,对水环境修复具有重要作用。然而,硝化细菌制剂一般以无机碳为碳源,生长缓慢,对生产条件的变化敏感,对生存条件要求较为苛刻,不易保存,现有技术中缺少可连续、高效生产硝化细菌的生产线及装置,实际应用中亟需一种设计合理的硝化细菌生产工艺及生产线,在高效获得硝化细菌产品的基础上,快速实现生产便利性和商业化。技术实现要素:本发明为了弥补现有技术的不足,提供了一种硝化细菌生产工艺及装置,工艺科学、合理,大大提高了硝化细菌生产效率,解决了现有技术中存在的问题。本发明是通过如下技术方案实现的:一种硝化细菌生产工艺,包括如下操作步骤:1)配料:(1)按工艺水:发酵媒介A:氨水:亚硝酸钠=5000-8000:70-140:2-8:5-8的重量比,配备各成分;所述发酵媒介A包括:盐酸、硼酸、氯化锰、硫酸锌、硫酸铜;(2)流加料配制,所述流加料包括30%-50%质量浓度的K2CO3溶液和碳源;2)发酵向发酵罐内加入工艺水,然后依次加入步骤(1)的发酵媒介A、亚硝酸钠和氨水,调节pH7.4-8.0,于25-30℃罐温条件下,按发酵罐定容体积1-5%的接种量,接入硝化细菌菌种;控制发酵溶氧20%-90%;与此同时,进行流加料的连续流加;3)指标检测及补料发酵过程中,控制pH7.4-8.0,并检测氨氮和SV10;在NH4-N和NO2-N下降到50ppm以下时,流加氨水;在SV10达到10-20%时,开始补加工艺水及发酵媒介B;所述发酵媒介B包括:盐酸、磷酸氢二钾、硫酸镁、氯化钙和氯化铁;(4)产物富集及沉淀发酵产物富集后经发酵罐上的溢流管路流至沉淀罐内,经沉淀罐沉淀得硝化菌产物。步骤1)所述碳源为CO2;步骤2)所述硝化细菌菌种为市售硝化菌;碳源流加速率为30-100L/h,K2CO3溶液流加速率为60-160ml/min;步骤3)氨水流加速率从5ml/min开始,每1小时提高一次,氨水流速最终为60ml/min;工艺水补加速率80-160L/h;发酵媒介B补加流速30-80ml/min;SV10每天检测一次。优选的,所述发酵媒介A包括以下重量份的原料:盐酸450--610份、硼酸130-160份、氯化锰72-98份、硫酸锌3-16份、硫酸铜2-9份;所述发酵媒介B包括以下重量份的原料:盐酸10份、磷酸氢二钾6600-6900份、硫酸镁3790-3850份、氯化钙1820-1870份、氯化铁770-795份。步骤1)的亚硝酸钠在加入步骤2)的发酵罐前,先用水溶解。上述工艺用装置,包括发酵罐、流加装置和沉淀罐;所述流加装置包括补料罐;所述发酵罐经管路与所述流加装置和沉淀罐相连;在发酵罐上还连接空气管路及碳源罐;在发酵罐及沉淀罐外侧壁上均设有换热夹套。所述碳源罐为二氧化碳气瓶。所述流加装置还包括配料罐,所述配料罐设于补料罐上方,配料罐接收提升机输送的物料、配置后直接流入补料罐。所述补料罐包括媒介补料罐和辅料补料罐;所述配料罐包括媒介配料罐和辅料配料罐;所述媒介配料罐经支撑架支撑设于媒介补料罐上方,所述辅料配料罐经支撑架支撑设于辅料补料罐上方。所述发酵罐包括发酵罐体,在发酵罐体内设有一第一搅拌杆,在第一搅拌杆上从上向下依次间隔设置第一消泡件、第一搅拌桨叶和第二搅拌桨叶;在发酵罐体内侧壁上均匀间隔设有若干个挡板;空气管路的底端伸至发酵罐体底部并与一空气分布器相连。第一搅拌杆顶端穿出发酵罐的罐盖并经减速机与驱动电机相连;第一搅拌杆的底端经支撑设于发酵罐内底壁上的支撑轴承支撑。所述挡板的数量为3个;各挡板与发酵罐体内侧壁焊接。空气管路经空气储罐与空压机相连。发酵罐上设置的换热夹套经管路与制冷机和/或外部加热设备相连。通过加热设备冷热水进行换热,实现发酵罐内温控。沉淀罐上设置的换热夹套经管路与制冷机相连。所述第一消泡件包括一板体,在板体底面设置若干个柱体;所述第一搅拌桨叶为两交叉设置的搅拌桨片,所述搅拌桨片与板体平行设置;所述第二搅拌桨叶包括一盘体,在盘体外周均匀间隔设置若干个搅拌叶,各搅拌叶与盘体的盘面相垂直设置。所述柱体为竖直柱杆或锥形杆。所述沉淀罐包括沉淀罐体,沉淀罐体的内底壁呈V型设置,在沉淀罐体内部设有第二搅拌杆,在第二搅拌杆上从上向下依次间隔设有第二消泡件、第三消泡件和第三搅拌桨叶。所述第二消泡件和第三消泡件均为一外侧壁设置有锯齿的锯齿杆;第三搅拌桨叶为V形搅拌桨叶。在沉淀罐侧壁上设有用于测定沉淀罐体内部温度的温度计。第二搅拌杆顶端穿出沉淀罐的罐盖并经减速机与驱动电机相连。在所述沉淀罐体侧壁上设有玻璃视窗。玻璃视窗设置,方便操作人员对沉淀罐内沉淀程度进行观察。发酵罐与沉淀罐连接的管路为设于发酵罐上的溢流管路。所述溢流管路设于高于发酵罐内原始培养基液面8-15cm位置处的发酵罐侧壁上。如此,在发酵产物逐渐产出、增多、发酵液面上升的情况下,至该高度即溢流至沉淀罐内,实现发酵产物的沉淀收集。在溢流管路上设有单向阀。本发明的有益效果:该硝化细菌生产工艺操作简单,设计科学,通过连续发酵生产硝化细菌,通过发酵媒介、流加料的合理配制和条件调控,硝化细菌生产效率高。该工艺采用的装置结构设计合理,保证了硝化细菌的规模化生产,整个装置保证了硝化细菌发酵及沉淀过程中对环境条件的要求,生产效率高。通过对流加装置进行结构改进,减少了人工,省时省力,消除了设备损耗,补料及时、顺畅。该生产工艺及装置很好的实现了硝化细菌高效的商业化生产。附图说明图1为本发明装置一种实施方式的结构示意图;图2为图1中发酵罐结构示意图;图3为图2中第一搅拌杆大样图;图4为图1中沉淀罐结构示意图;图5为本发明装置另一种实施方式的结构示意图。图中,1发酵罐、2沉淀罐、3媒介配料罐、4辅料配料罐、5媒介补料罐、6辅料补料罐、7第一搅拌杆、8第一消泡件、8.1板体、8.2柱体、9第一搅拌桨叶、10第二搅拌桨叶、10.1盘体、10.2搅拌叶、11挡板、12空气管路、13空气分布器、14空气储罐、15空压机、16第二搅拌杆、17第二消泡件、18第三消泡件、19第三搅拌桨叶、20温度计、21玻璃视窗、22支撑架、23提升机、24氨水桶、25二氧化碳气瓶、26换热夹套、27溢流管路。具体实施方式为能清楚说明本方案的技术特点,下面通过具体实施方式,并结合其附图,对本发明进行详细阐述。实施例1该硝化细菌生产工艺,包括如下操作步骤:(1)配料1.1发酵媒介A-1000X(终体积50L)名称数量盐酸600g(+/-5g)硼酸142g(+/-5g)氯化锰88.09g(+/-5g)硫酸锌10g(+/-5g)硫酸铜3g(+/-5g)发酵媒介A配制:先在桶中加入30L工艺水;然后将盐酸缓慢加入水中,并不断搅拌,按列表顺序加入其它各个组分;停止搅拌后定容至50L;1.2发酵媒介B-50X(终体积1000L)(微量元素)发酵媒介B配制:先在桶中加入500L工艺水;将盐酸缓慢加入水中并不断搅拌,然后按列表顺序加入每个组分;停止搅拌后定容至1000L;1.3亚硝酸钠:取6KG亚硝酸钠,用水溶解,备用;1.4氨水:5KG,备用;(2)流加料配制50%K2CO3溶液:取1000Kg的碳酸钾,加工艺水配制成质量浓度50%的K2CO3溶液;碳源存储于气瓶内;(3)发酵向发酵罐加入6000升工艺水,然后依次加入前述配制的发酵媒介A120Kg、亚硝酸钠和氨水,并用HCl、CO2或者NaOH调整pH至7.8,控制罐温25-30℃,开启搅拌,搅拌速度设定为30-60rpm,按发酵罐定容体积的3%接种市售购买的硝化细菌菌种;与此同时,连续流加前述配制的50%K2CO3溶液,以及碳源--CO2和洁净空气,控制发酵溶氧50%-70%;K2CO3溶液流量按110-120ml/min,CO2流量按80-90L/H;维持NH4-N和NO2-N的指标分别为:NH4-N:30-100ppm、NO2-N:50-200ppm;(4)发酵过程中测定氨氮,当NH4-N和NO2-N下降到50ppm以下时,开始流加氨水;氨水流量每1小时提高一次,流加量最终约为60ml/min;发酵过程中,每天检测一次SV10,当SV10达到10-20%,开始补加工艺水120-140L/h,同时开始补加发酵媒介B、流速60-70ml/min;整个发酵过程,控制pH7.4-8.0;(5)在流加流加料前开启发酵罐上溢流管路上的阀门,随着发酵进行,发酵产物富集,发酵罐内液面上升,由发酵罐上的溢流管路进入沉淀罐,经沉淀罐沉淀得产物。实施例2该硝化细菌生产工艺,包括如下操作步骤:(1)配料1.1发酵媒介A-1000X(终体积50L)名称数量盐酸500g(+/-5g)硼酸135g(+/-5g)氯化锰77g(+/-5g)硫酸锌5g硫酸铜2g发酵媒介A配制:先在桶中加入30L工艺水;然后将盐酸缓慢加入水中,并不断搅拌,按列表顺序加入其它各个组分;停止搅拌后定容至50L;1.2发酵媒介B-50X(终体积1000L)(微量元素)名称数量盐酸10L磷酸氢二钾6600g硫酸镁3810g氯化钙1810g氯化铁770g1000X媒介50L(+/-0.2L)发酵媒介B配制:先在桶中加入500L工艺水;将盐酸缓慢加入水中并不断搅拌,然后按列表顺序加入每个组分;停止搅拌后定容至1000L;1.3亚硝酸钠:取5KG亚硝酸钠,用水溶解,备用;1.4氨水:2KG,备用;(2)流加料配制30%K2CO3溶液:取1000Kg的碳酸钾,加工艺水配制成质量浓度30%的K2CO3溶液;碳源存储于气瓶内;(3)发酵向发酵罐加入5000升工艺水,然后依次加入前述配制的发酵媒介A70Kg、亚硝酸钠和氨水,并用HCl,CO2或者NaOH调整pH至7.8,控制罐温25-28℃,开启搅拌,搅拌速度设定为30-60rpm,按发酵罐定容体积的3%接种市售购买的硝化细菌菌种;与此同时,连续流加前述配制的30%K2CO3溶液,以及碳源--CO2和洁净空气,控制发酵溶氧20%-40%;K2CO3溶液流量按60-80ml/min,CO2流量按30-50L/H;维持NH4-N和NO2-N的指标分别为:NH4-N:30-100ppm,NO2-N:50-200ppm;(4)发酵过程中测定氨氮,当NH4-N和NO2-N下降到50ppm以下时,开始流加氨水;氨水流量每1小时提高一次,流加量最终约为60ml/min;发酵过程中,每天检测一次SV10,当SV10达到10-20%,开始补加工艺水80-100L/h,同时开始补加发酵媒介B、流速30-50ml/min;整个发酵过程,控制pH7.4-8.0;(5)在流加流加料前开启发酵罐上溢流管路上的阀门,随着发酵进行,发酵产物富集,发酵罐内液面上升,由发酵罐上的溢流管路进入沉淀罐,经沉淀罐沉淀得产物。实施例3该硝化细菌生产工艺,包括如下操作步骤:(1)配料1.1发酵媒介A-1000X(终体积50L)发酵媒介A配制:先在桶中加入30L工艺水;然后将盐酸缓慢加入水中,并不断搅拌,按列表顺序加入其它各个组分;停止搅拌后定容至50L;1.2发酵媒介B-50X(终体积1000L)(微量元素)名称数量盐酸10L磷酸氢二钾6900g硫酸镁3850g氯化钙1870g氯化铁795g1000X媒介50L(+/-0.2L)发酵媒介B配制:先在桶中加入500L工艺水;将盐酸缓慢加入水中并不断搅拌,然后按列表顺序加入每个组分;停止搅拌后定容至1000L;1.3亚硝酸钠:取8KG亚硝酸钠,用水溶解,备用;1.4氨水:8KG,备用;(2)流加料配制50%K2CO3溶液:取1000Kg的碳酸钾,加工艺水配制成质量浓度50%的K2CO3溶液;碳源存储于气瓶内;(3)发酵向发酵罐加入8000升工艺水,然后依次加入前述配制的发酵媒介A140Kg、亚硝酸钠和氨水,并用HCl,CO2或者NaOH调整pH至7.8,控制罐温25-30℃,开启搅拌,搅拌速度设定为30-60rpm,按发酵罐定容体积的3%接种市售购买的硝化细菌菌种;与此同时,连续流加前述配制的50%K2CO3溶液,以及碳源--CO2和洁净空气,控制发酵溶氧70%-80%;K2CO3溶液流量按150-160ml/min,CO2流量按80-100L/H;维持NH4-N和NO2-N的指标分别为:NH4-N:30-100ppm,NO2-N:50-200ppm;(4)发酵过程中测定氨氮,当NH4-N和NO2-N下降到50ppm以下时,开始流加氨水;氨水流量每1小时提高一次,流加量最终约为60ml/min;发酵过程中,每天检测一次SV10,当SV10达到10-20%,开始补加工艺水150-160L/h,同时开始补加发酵媒介B、流速80ml/min;整个发酵过程,控制pH7.4-8.0;(5)在流加流加料前开启发酵罐上溢流管路上的阀门,随着发酵进行,发酵产物富集,发酵罐内液面上升,由发酵罐上的溢流管路进入沉淀罐,经沉淀罐沉淀得产物。实施例4如图1-4所示,该硝化细菌生产线装置包括发酵罐1、流加装置和沉淀罐2,所述流加装置包括配料罐和补料罐,所述配料罐包括媒介配料罐3、辅料配料罐4,辅料配料罐为K2CO3配料罐,所述补料罐包括与所述配料罐对应设置的媒介补料罐5、辅料补料罐6;补料罐内料经输料管路输送至发酵罐内,发酵罐内发酵好的料液由发酵罐中部经管路输出至沉淀罐2内沉淀。在发酵罐上的两进气口位置还连接空气管路12和二氧化碳气瓶25;在发酵罐及沉淀罐外侧壁上均设有换热夹套26,换热夹套上设有冰水进口和冰水出口,通过冰水吸热换热控制发酵罐及沉淀罐内温度,用于保证硝化细菌的生长条件。各配料罐上均经输液管路与自来水源相连,水与原料按配比加入配料罐后进行搅拌配料备料。所述发酵罐1包括发酵罐体,在发酵罐体内设有一第一搅拌杆7,在第一搅拌杆上从上向下依次间隔设置第一消泡件8、第一搅拌桨叶9和第二搅拌桨叶10;在发酵罐体内侧壁上均匀间隔设有若干个挡板11;空气管路12的底端伸至发酵罐体底部并与一空气分布器13相连。第一搅拌杆7顶端穿出发酵罐的罐盖并经减速机与驱动电机相连;第一搅拌杆的底端经支撑设于发酵罐内底壁上的支撑轴承支撑。所述挡板11的数量为3个;各挡板与发酵罐体内侧壁焊接固定。空气管路12经空气储罐14与空压机15相连。发酵罐上设置的换热夹套26的进水口和出水口分别经管路与外部加热设备相连,实现发酵罐内换热,保证发酵罐温。所述第一消泡件8包括一板体8.1,在板体底面设置若干个柱体8.2;所述第一搅拌桨叶9为两交叉设置的搅拌桨片,所述搅拌桨片与板体平行设置;所述第二搅拌桨叶10包括一盘体10.1,在盘体外周均匀间隔设置若干个搅拌叶10.2,各搅拌叶与盘体的盘面相垂直设置。所述柱体8.2为竖直柱杆或锥形杆。所述沉淀罐2包括沉淀罐体,沉淀罐体的内底壁呈V型设置,在沉淀罐体内部设有第二搅拌杆16,在第二搅拌杆上从上向下依次间隔设有第二消泡件17、第三消泡件18和第三搅拌桨叶19。所述第二消泡件17和第三消泡件18均为一外侧壁设置有锯齿的锯齿杆;第三搅拌桨叶19为V形搅拌桨叶。在沉淀罐侧壁上设有用于测定沉淀罐体内部温度的温度计20。第二搅拌杆16顶端穿出沉淀罐的罐盖并经减速机与驱动电机相连。在所述沉淀罐体侧壁上设有玻璃视窗21。玻璃视窗设置,方便操作人员对沉淀罐内沉淀程度进行观察。在发酵罐外侧壁上也设有玻璃视窗。上述发酵罐外侧,还通过管路连接有氨水桶24,根据需要适当添加。发酵罐1与沉淀罐2连接的管路为设于发酵罐上的溢流管路27;所述溢流管路设于高于发酵罐内原始培养基液面8-15cm位置处的发酵罐侧壁上。如此,在发酵产物逐渐产出、增多、发酵液面上升的情况下,至该高度即溢流至沉淀罐内,实现发酵产物的沉淀收集。在溢流管路上设有单向阀。工作过程:向发酵罐内加入一定量工艺水,然后加入发酵媒介A、亚硝酸钠和氨水,控制pH在7.4-8.0,控制罐温并接入菌种,与此同时,按照一定速度,开始流加K2CO3溶液和二氧化碳,通过控制管路12进洁净空气,控制溶氧在30-90%,发酵罐搅拌发酵。上述发酵料液在第一搅拌杆搅拌下,通过挡板11的配合,保证搅拌的均匀性,由空气管路12进入发酵罐体底部的空气进入空气分布器13均匀分散至发酵料液内,保证硝化细菌发酵的好氧生长要求;在搅拌过程中,发酵液上部产生的气泡不断被第一消泡件8打散消除。发酵过程中,持续少量补入二氧化碳气瓶25内的二氧化碳,二氧化碳流加速度按工艺要求进行;发酵过程中,检测氨氮浓度和SV10,根据发酵指标要求,补加氨水,氨水由氨水桶24内经管路向发酵罐内泵送,补加媒介。随着硝化细菌的发酵生长,发酵罐体内料液逐渐增多,通过设于发酵罐体上的溢流管路27,将发酵料液持续输出至沉淀罐2内进行沉淀处理,由于沉淀罐的内底壁呈V型设置,加快了沉淀速度,进入沉淀罐内的发酵料液在第二搅拌杆16作用下逐渐分层沉淀,在沉淀目的的要求下,沉淀罐内的第二搅拌杆16搅拌速度慢,这一较慢搅拌速度决定了其内第二消泡件17采用锯齿杆进行打散消除也能获得较好的消泡效果。由于该发酵生产过程为连续的,期间还需不断向发酵罐内流加发酵媒介和辅料,具体加料标准,根据前述工艺检测指标进行,通过媒介配料罐(发酵媒介B)与媒介补料罐间连接的输料管路上的卫生泵,将媒介配料罐3内媒介泵入媒介补料罐内,通过辅料配料罐4与辅料补料罐间设置的卫生泵,将辅料配料罐内辅料(K2CO3溶液)泵入辅料补料罐内,继而由蠕动泵分别将媒介补料罐和辅料补料罐内的料泵入发酵罐,实现流加操作。整个发酵生产过程中,沉淀罐通过制冷机进行循环换热,沉淀罐内温度保持4℃,保证硝化细菌品质和活性;发酵罐内温度保持最适发酵温度25℃。实施例5如图5所示,省略了与发酵罐相连的除流加装置之外的其他设施,该硝化细菌生产线装置结构同实施例2的硝化细菌生产装置,所不同的是,为了保证生产过程中对卫生泵的损耗,实现配料罐向补料罐内更方便的进料,对流加装置进行了结构改进,具体为:配料罐与其所对应的补料罐上、下设置,即配料罐经支撑架22支撑设于相应补料罐的上方,如此可省去卫生泵,通过重力作用,配料罐内的料可在管路上的阀打开后直接进入补料罐,补料罐内的料再经蠕动泵泵入发酵罐1内,如图5所示,图中省去了与发酵罐相连的其他管路及设施。配料罐配料前通过设于发酵罐外侧的提升机23将物料向上输送进配料罐,同时配料罐进水口经管路与外部自来水相连,经配料罐内搅拌配料,直接向下输入补料罐内,由补料罐继续向发酵罐流加,实现连续生产。工作过程:向发酵罐内加入一定量工艺水,然后加入发酵媒介A、亚硝酸钠和氨水,控制pH在7.4-8.0,控制罐温并接入菌种,与此同时,按照一定速度,开始流加K2CO3溶液和二氧化碳,通过控制管路12进洁净空气,控制溶氧在30-90%,发酵罐搅拌发酵。上述发酵料在第一搅拌杆搅拌下,通过挡板11的配合,保证搅拌的均匀性,由空气管路12进入发酵罐体底部的空气进入空气分布器13均匀分散至发酵料液内,保证硝化细菌发酵的好氧生长要求;在搅拌过程中,发酵液上部产生的气泡不断被第一消泡件8打散消除。发酵过程中,持续少量补入二氧化碳气瓶25内的二氧化碳,作为碳源,二氧化碳流加速度按工艺要求进行;发酵过程中,检测氨氮和SV10,根据发酵指标要求,补加氨水,氨水由氨水桶24内经管路向发酵罐内泵送,补加媒介。随着硝化细菌的发酵生长,发酵罐体内料液逐渐增多,通过设于发酵罐体上的溢流管路27,将发酵料液持续输出至沉淀罐2内进行沉淀处理,由于沉淀罐的内底壁呈V型设置,加快了沉淀速度,进入沉淀罐内的发酵料液在第二搅拌杆16作用下逐渐分层沉淀,在沉淀目的的要求下,沉淀罐内的第二搅拌杆16搅拌速度慢,这一较慢搅拌速度决定了其内第二消泡件17采用锯齿杆进行打散消除也能获得较好的消泡效果。由于该发酵生产过程为连续的,期间还需不断向发酵罐内流加发酵媒介及辅料(K2CO3),而通过媒介补料罐5及设于其上方的媒介配料罐3,以及辅料补料罐6及设于其上方的辅料配料罐4,不再需要卫生泵,能够较好的完成该流加操作。整个发酵生产过程中,沉淀罐通过制冷机进行循环换热,沉淀罐内温度保持4℃,保证硝化细菌品质和活性;发酵罐内温度保持最适发酵温度25℃。产品效果应用案例:案例一:将本发明上述实施例1工艺制得的硝化细菌产物用于垃圾渗滤液氨氮的去除,具体如下:位于某城市郊区的某垃圾卫生填埋场。其工程占地22公顷,设4个作业单元,渗滤液经收集后进入渗滤液处理站。处理站设计能力为日处理渗滤液150m3,采用包括初沉、酸化、生物反应池等组合工艺。使用效果:该垃圾渗滤液处理工程于5月中旬完成生物处理系统的活性污泥培养,系统开始试运转。7月份开始投加市场某常见品牌硝化菌,启动硝化系统。2个月后,效果不佳。9月份使用本发明硝化菌启动硝化作用。之后的2个月内连续添加,运行效果见下表1。表1渗滤液处理运行效果投加本发明硝化菌后,帮助系统快速加强硝化作用,处理后的渗沥液出水氨氮指标持续降低,最终稳定达到国家的排放标准。本发明硝化菌的投加,既可进行系统的恢复,又可减缓有毒有害物质冲击影响,也可提高有机物和氨氮的去除率。案例二、将本发明上述工艺实施例1制得的硝化细菌产物用于某石化污水厂,改善该污水厂COD、氨氮问题。具体如下:某石化污水厂处理能力为6000m3/天,处理系统分为两套平行处理系统。系统的生化效率较差,COD去除效果不稳定,出水氨氮严重超标。经过我单位技术人员的现场分析,对两套平行系统中的一套1#进行增效处理,另外一套2#作为对照。生物增效去除COD:在1#生化池中投加COD降解菌,2#生化池作为对比不投加。自第6天投加COD降解菌。投加后第一个星期已能看到明显的效果:1#生化池比2#生化池出水COD平均低约5%。在增效期效果稳定,投加了COD降解菌的1#生化池出水平均COD为108mg/L,比2#生化池的127mg/L低15%。生物增效去除氨氮:同样,在1#生化池中投加本发明硝化菌,2#生化池作为对比不投加。自第10天投加本发明产品。结果:采用本发明产品降低氨氮前,1#生化池氨氮处理效果明显要比2#生化池差。使用本发明产品后,1#生化池氨氮去除率逐渐提高,一周后优于2#生化池,且效果逐渐明显并稳定。1#生化池出水氨氮比2#生化池平均低42%。上述效果对比如下表:表2生物增效前后二沉池COD、氨氮数据从上表2可以明确看出,在采用本发明产品进行生物增效前,1#生化处理系统COD和氨氮出水水质情况均要比2#生化处理系统差,在采用生物增效后1#生化处理系统COD和氨氮出水水质情况均要远远优于比2#生化处理系统。其中,采用本发明产品进行生物增效前1#系统比2#系统COD高出21.6%,氨氮高出9.5%。生物增效进入稳定期(启动期约十天),则1#系统比2#系统COD低15%,氨氮低42%。由于COD、氨氮去除效果显著,该石化污水厂为确保出水水质稳定达标,开始持续使用本发明产品。上述具体实施方式不能作为对本发明保护范围的限制,对于本
技术领域:
的技术人员来说,对本发明实施方式所做出的任何替代改进或变换均落在本发明的保护范围内。本发明未详述之处,均为本
技术领域:
技术人员的公知技术。当前第1页1 2 3