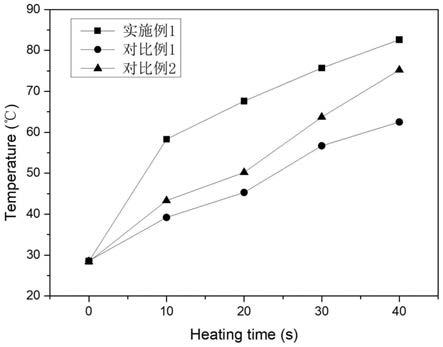
[0001]
本发明涉及橡胶材料技术领域,尤其是涉及一种高导热天然橡胶复合材料的制备方法。
背景技术:[0002]
天然橡胶是目前世界上使用时间最长、应用范围最广的通用橡胶,它的主要成分为异戊二烯,分子式是(c
5
h
8
)
n
,摩尔质量一般介于1000-100000之间,天然橡胶的聚异戊二烯含量通常在97%以上,除此之外,它还含有少量的蛋白质、糖类和灰飞等非橡胶物质。天然橡胶具有一些列优秀的物质特性,如良好的回弹性、绝缘性、隔水性、气密性、抗拉性等。除此之外,它还具有耐碱、耐酸、耐热等优良的化学特性,被广泛应用在各个领域。如交通运输业的汽车轮胎、发动机密封圈,日常生活中的雨鞋、暖水袋、医疗卫生上的外科手套、输液管,甚至国防尖端科技上的导弹、火箭、人造卫星、航空航母的零部件。随着科技技术的发展,人们对橡胶的应用又提出新的需求,在电子封装领域,电子元器件工作时会产生大量的热量,这些热量需要及时散去,传统的散热材料为金属导电材质,不能与电子元器件直接接触,因此散热效果不佳,而柔软的天然橡胶却可以与电子元器件直接接触,这使得它成为金属散热材料更合适的替代品,但天然橡胶散热性较差,这就需要提高它的导热性能。又如轮胎是天然橡胶应用的重要领域,在汽车高速行驶过程中轮胎会产生大量的热量,由于天然橡胶较差的导热性能,使得轮胎内部温度急剧上升,加速轮胎的老化,引发交通事故。因此,提高橡胶的导热性,降低轮胎温度也是交通运输行业亟待解决的问题。
[0003]
中国专利文献公开号cn103589005公开了一种伊蒙混层粘土/天然橡胶复合橡胶的制备方法,先将天然伊蒙混层粘土制成料浆,将料浆加入天然胶乳悬浊液中,经过絮凝、造粒得到伊蒙混层粘土/天然橡胶复合胶粒,对胶粒进行干燥,得到伊蒙混层粘土/天然橡胶复合橡胶。中国专利公开号cn105348585公开了一种白炭黑/天然橡胶母炼胶、制备方法及白炭黑/天然橡胶复合材料,将白炭黑分散液与天然胶乳混合,得到共混乳液,然后将共混乳液与凝固剂混合,得到的共沉凝胶与蛋白酶进行消化反应,得到白炭黑/天然胶乳母炼胶。上述专利文献中之别得到的橡胶复合材料虽然具有较好的力学性能,但是导热性能差,限制了橡胶材料的应用范围。
[0004]
中国专利文献公开号cn111499935公开了一种改性氧化石墨烯/天然橡胶高导热复合材料,先将制备的六方氮化硼纳米片改性,与氧化石墨烯分散液混合后形成六方氮化硼纳米片改性氧化石墨烯分散液,将六方氮化硼纳米改性氧化石墨烯分散液与天然胶乳共混,破乳形成母胶,将母胶塑炼、混炼并硫化,形成高导热天然橡胶复合材料。虽然六方氮化硼纳米片改性氧化石墨烯在橡胶中形成导电网络,但是六方氮化硼纳米片改性氧化石墨烯在橡胶中的分散性能不佳,且导热粒子与导热粒子之间由于间距较大,导致导热粒子与导热粒子之间的热传递较慢,限制橡胶导热性能的进一步提高。
技术实现要素:[0005]
本发明是为了克服以上现有技术问题,提供一种高导热天然橡胶复合材料的制备方法。本发明制备得到的天然橡胶复合材料不仅具有良好的导热性能,还显著提高了橡胶复合材料的力学强度。
[0006]
为了实现上述目的,本发明采用以下技术方案:一种高导热天然橡胶复合材料的制备方法,包括以下步骤:1)将六方氮化硼置于马弗炉中进行高温处理,冷却后得到六方氮化硼粉末,将六方氮化硼粉末添加到乙醇胺溶剂中,置于超声波清洗器中进行超声震荡,经过离心、洗涤、干燥得到六方氮化硼纳米片;2)将六水合硝酸锌加入甲醇溶液中搅拌溶解,得到硝酸锌溶液,向硝酸锌溶液中加入六方氮化硼纳米片和碳纳米管,超声震荡分散均匀,得到悬浮液;将2-甲基咪唑加入甲醇溶液中搅拌溶解,得到2-甲基咪唑溶液,将2-甲基咪唑溶液滴加到悬浮液中,在避光条件下室温搅拌反应1-3h,反应完成后经过离心、洗涤、干燥,得到金属有机框架-六方氮化硼复合粒子;3)将金属有机框架-六方氮化硼复合粒子加入去离子水中,搅拌分散均匀,得到金属有机框架-六方氮化硼复合粒子悬浮液,将金属有机框架-六方氮化硼复合粒子悬浮液加入天然胶乳中,搅拌混合均匀,得到天然胶乳混合液,向天然胶乳混合液中滴加氯化钙溶液进行破乳,然后置于烘箱中干燥,得到橡胶母料;将橡胶母料依次进行混炼、开炼,制得高导热天然橡胶复合材料。
[0007]
六方氮化硼纳米片和碳纳米管具有优异的导热性,六方氮化硼纳米片超高的比表面积和高纵横比使得其可以在较低的填充量下提高材料的导热性能。直接将六方氮化硼纳米片和碳纳米管填充到橡胶材料中存在的问题是六方氮化硼纳米片与碳纳米管杂乱无章的分散在橡胶材料中,不容易形成规整的导热网络结构,导热粒子之间的热量传递效率较低,且六方氮化硼纳米片与碳纳米管容易发生团聚,从而影响六方氮化硼纳米片和碳纳米管对橡胶材料的导热性能的改善作用。对此,本发明先通过超声震荡剥离的方法制备六方氮化硼纳米片,通过2-甲基咪唑与硝酸锌反应制备金属有机框架,利用金属有机框架为载体将六方氮化硼纳米片和碳纳米管嵌入金属有机框架内部和表面,从而将六方氮化硼纳米片和碳纳米管与金属有机框架结合,部分碳纳米管直立嵌插在金属有机框架表面,形成“刺凸”结构,制备得到具有导热性能和碳纳米管刺凸结构的金属有机框架-六方氮化硼复合粒子。金属有机框架-六方氮化硼复合粒子表面由于具有刺凸结构,使金属有机框架-六方氮化硼复合粒子之间不容易发生团聚,从而提高导热粒子在橡胶材料中的分散性,提高橡胶材料的导热性能。
[0008]
金属有机框架-六方氮化硼复合粒子内部六方氮化硼纳米片与六方氮化硼纳米片通过碳纳米管连接,提高六方氮化硼纳米片之间的导热效率,进而得到具有高导热性能的金属有机框架-六方氮化硼复合粒子,有利于提高橡胶材料的导热性能。另一方面,具有碳纳米管导热刺凸结构的金属有机框架-六方氮化硼复合粒子均匀分散在橡胶材料内部,能够形成具有一定规整结构的导热网络,提高橡胶材料的导热效率;另外,金属有机框架-六方氮化硼导热复合粒子表面由碳纳米管组成的导热刺凸结构能够缩短导热粒子与导热粒子之间的间隔,进一步提高橡胶材料的导热效率,进而提高橡胶材料的导热性能。
[0009]
作为优选,所述步骤1)中六方氮化硼置于马弗炉中高温处理温度为100-300℃,高温处理时间为3-6h。
[0010]
作为优选,所述步骤1)中超声震荡功率为80-100w,超声震荡时间控制在10-15h。
[0011]
作为优选,所述步骤2)中六水合硝酸锌、六方氮化硼纳米片、碳纳米管三者的质量比为1:0.3-0.5:0.06-0.1。
[0012]
作为优选,所述步骤2)中六水合硝酸锌与2-甲基咪唑的混合质量比为1:6-9。
[0013]
作为优选,所述步骤3)中金属有机框架-六方氮化硼复合粒子与天然胶乳的质量比为1:60-80。
[0014]
作为优选,所述步骤1)中六方氮化硼纳米片经过预处理,包括以下步骤:将六方氮化硼纳米片加入氢氧化钠溶液中,油浴加热至100-120℃,搅拌反应3-5h,经过离心分离、洗涤、干燥,得到羟基化六方氮化硼纳米片;将环氧基硅烷偶联剂加入乙醇与水的混合溶液中,调节体系ph至4-6,水浴加热至50-60℃,搅拌进行水解30-50min,得到环氧基硅烷偶联剂水解液,将羟基化六方氮化硼纳米片加入环氧基硅烷偶联剂水解液中,搅拌反应1-3h,经过离心分离、洗涤、干燥,得到烷基化六方氮化硼纳米片;将透明质酸加入去离子水中搅拌溶解配制成透明质酸水溶液,将烷基化六方氮化硼纳米片加入透明质酸水溶液中,加入四氯化锡催化剂,在75-85℃下搅拌反应2-5h,经过离心分离、洗涤、干燥,即得。
[0015]
本发明在制备金属有机框架-六方氮化硼复合粒子过程中,遇到的问题是制备得到的金属有机框架-六方氮化硼复合粒子中六方氮化硼纳米片的负载量较低,从而影响金属有机框架-六方氮化硼复合粒子的导热性能,这是由于金属有机框架-六方氮化硼复合粒子制备过程中,金属有机框架与六方氮化硼纳米片的结合作用较弱,造成金属有机框架上负载的六方氮化硼纳米片较少。为进一步解决此问题,本发明先对六方氮化硼纳米片进行碱性处理,使六方氮化硼纳米片负载羟基,然后利用环氧基硅烷偶联剂水解得到羟基与六方氮化硼纳米片上负载羟基发生脱水缩合,从而将环氧硅烷偶联剂接枝在六方氮化硼纳米片上,使六方氮化硼纳米片负载环氧基团,利用环氧基团与透明质酸分子上的羟基发生开环反应,从而将透明质酸接枝在六方氮化硼纳米片表面,使六方氮化硼纳米片表面负载透明质酸,负载透明质酸的六方氮化硼纳米片与金属有机框架上的zn
2+
产生静电相互作用,从而在金属有机框架-六方氮化硼复合粒子制备过程中使更多的六方氮化硼纳米片与金属有机框架结合,提高金属有机框架上六方氮化硼纳米片的负载量,进而提高金属有机框架-六方氮化硼复合粒子的导热性能。
[0016]
作为优选,所述氢氧化钠溶液的质量浓度为0.5-1.0%。
[0017]
作为优选,所述羟基化六方氮化硼纳米片与环氧基硅烷偶联剂的质量比为1:0.2-0.6。
[0018]
作为优选,所述透明质酸水溶液的质量浓度为0.1-0.5%。
[0019]
因此,本发明相对现有技术具有如下有益效果:(1)属有机框架-六方氮化硼复合粒子表面由于具有刺凸结构,使金属有机框架-六方氮化硼复合粒子之间不容易发生团聚,从而提高导热粒子在橡胶材料中的分散性,提高橡胶材料的导热性能;(2)金属有机框架-六方氮化硼复合粒子内部六方氮化硼纳米片与六方氮化硼纳米片通过碳纳米管连接,提高六方氮化硼纳米片之间的导热效率,进而得到具有高导热性能的金属有机框架-六方氮化硼复合粒子,有利于提高橡胶材料的导热性;(3)具
有碳纳米管导热刺凸结构的金属有机框架-六方氮化硼复合粒子均匀分散在橡胶材料内部,能够形成具有一定规整结构的导热网络,提高橡胶材料的导热效率;金属有机框架-六方氮化硼导热复合粒子表面由碳纳米管组成的导热刺凸结构能够缩短导热粒子与导热粒子之间的间隔,进一步提高橡胶材料的导热效率,进而提高橡胶材料的导热性能。
附图说明
[0020]
图1为实施例1、对比例1和对比例2橡胶复合材料红外热成像升温测试过程中材料表面温度随时间变化曲线图。
具体实施方式
[0021]
下面通过具体实施例,对本发明的技术方案做进一步说明。本发明中若非特指,所采用的原料和设备等均可从市场购得或是本领域常用的,实施例中的方法,如无特别说明均为本领域的常规方法。
[0022]
实施例1高导热天然橡胶复合材料的制备方法,包括以下步骤:1)将六方氮化硼置于马弗炉中在300℃下进行高温处理3h,冷却后得到六方氮化硼粉末,将六方氮化硼粉末按照质量体积比1g/70ml的比例添加到乙醇胺溶剂中,置于超声波清洗器中在100w下进行超声震荡10h,经过离心、洗涤、干燥得到六方氮化硼纳米片;六方氮化硼纳米片预处理:将六方氮化硼纳米片加入质量浓度为0.5%的氢氧化钠溶液中,油浴加热至100℃,搅拌反应5h,经过离心分离、洗涤、干燥,得到羟基化六方氮化硼纳米片;将乙醇与水按照体积比10:2的比例混合得到乙醇与水的混合溶液,将环氧基硅烷偶联剂kh-560加入乙醇与水的混合溶液中,环氧基硅烷偶联剂kh-560与混合溶液的质量比为1:30,调节体系ph至6,水浴加热至50℃,搅拌进行水解50min,得到环氧基硅烷偶联剂水解液,将羟基化六方氮化硼纳米片加入环氧基硅烷偶联剂水解液中,羟基化六方氮化硼纳米片与环氧基硅烷偶联剂kh-560的质量比为1:0.5,搅拌反应2h,经过离心分离、洗涤、干燥,得到烷基化六方氮化硼纳米片;将透明质酸加入去离子水中搅拌溶解配制成质量浓度为0.4%的透明质酸水溶液,将烷基化六方氮化硼纳米片按照质量体积比1g/80ml的比例加入透明质酸水溶液中,加入四氯化锡催化剂,四氯化锡添加量为透明质酸的3wt%,在80℃下搅拌反应4h,经过离心分离、洗涤、干燥,得到预处理的六方氮化硼纳米片;2)将六水合硝酸锌加入按照质量体积比1g/70ml的比例加入到甲醇溶液中搅拌溶解,得到硝酸锌溶液,向硝酸锌溶液中加入经过预处理的六方氮化硼纳米片和碳纳米管,六水合硝酸锌、六方氮化硼纳米片、碳纳米管三者的质量比为1:0.4:0.09,超声震荡分散均匀,得到悬浮液;将2-甲基咪唑按照质量体积比1g/50ml的比例加入甲醇溶液中搅拌溶解,得到2-甲基咪唑溶液,将2-甲基咪唑溶液滴加到悬浮液中,六水合硝酸锌与2-甲基咪唑的混合质量比为1:8,在避光条件下室温搅拌反应2.5h,反应完成后经过离心、洗涤、干燥,得到金属有机框架-六方氮化硼复合粒子;3)将金属有机框架-六方氮化硼复合粒子按照质量体积比1g/100ml的比例加入去离子水中,搅拌分散均匀,得到金属有机框架-六方氮化硼复合粒子悬浮液,将金属有机框架-六
方氮化硼复合粒子悬浮液加入固含量为50%的天然胶乳中,金属有机框架-六方氮化硼复合粒子与天然胶乳的质量比为1:65,搅拌混合均匀,得到天然胶乳混合液,向天然胶乳混合液中滴加质量浓度为3%的氯化钙水溶液进行破乳,然后置于烘箱中干燥,得到橡胶母料;将橡胶母料依次进行混炼、开炼,制得高导热天然橡胶复合材料。
[0023]
实施例2高导热天然橡胶复合材料的制备方法,包括以下步骤:1)将六方氮化硼置于马弗炉中在100℃下进行高温处理6h,冷却后得到六方氮化硼粉末,将六方氮化硼粉末按照质量体积比1g/70ml的比例添加到乙醇胺溶剂中,置于超声波清洗器中在80w下进行超声震荡15h,经过离心、洗涤、干燥得到六方氮化硼纳米片;六方氮化硼纳米片预处理:将六方氮化硼纳米片加入质量浓度为1.0%的氢氧化钠溶液中,油浴加热至120℃,搅拌反应3h,经过离心分离、洗涤、干燥,得到羟基化六方氮化硼纳米片;将乙醇与水按照体积比10:2的比例混合得到乙醇与水的混合溶液,将环氧基硅烷偶联剂kh-560加入乙醇与水的混合溶液中,环氧基硅烷偶联剂kh-560与混合溶液的质量比为1:30,调节体系ph至4,水浴加热至60℃,搅拌进行水解30min,得到环氧基硅烷偶联剂水解液,将羟基化六方氮化硼纳米片加入环氧基硅烷偶联剂水解液中,羟基化六方氮化硼纳米片与环氧基硅烷偶联剂kh-560的质量比为1:0.3,搅拌反应1.5h,经过离心分离、洗涤、干燥,得到烷基化六方氮化硼纳米片;将透明质酸加入去离子水中搅拌溶解配制成质量浓度为0.2%的透明质酸水溶液,将烷基化六方氮化硼纳米片按照质量体积比1g/80ml的比例加入透明质酸水溶液中,加入四氯化锡催化剂,四氯化锡添加量为透明质酸的3wt%,在80℃下搅拌反应3h,经过离心分离、洗涤、干燥,得到预处理的六方氮化硼纳米片;2)将六水合硝酸锌加入按照质量体积比1g/70ml的比例加入到甲醇溶液中搅拌溶解,得到硝酸锌溶液,向硝酸锌溶液中加入经过预处理的六方氮化硼纳米片和碳纳米管,六水合硝酸锌、六方氮化硼纳米片、碳纳米管三者的质量比为1:0.4:0.07,超声震荡分散均匀,得到悬浮液;将2-甲基咪唑按照质量体积比1g/50ml的比例加入甲醇溶液中搅拌溶解,得到2-甲基咪唑溶液,将2-甲基咪唑溶液滴加到悬浮液中,六水合硝酸锌与2-甲基咪唑的混合质量比为1:7,在避光条件下室温搅拌反应2h,反应完成后经过离心、洗涤、干燥,得到金属有机框架-六方氮化硼复合粒子;3)将金属有机框架-六方氮化硼复合粒子按照质量体积比1g/100ml的比例加入去离子水中,搅拌分散均匀,得到金属有机框架-六方氮化硼复合粒子悬浮液,将金属有机框架-六方氮化硼复合粒子悬浮液加入固含量为50%的天然胶乳中,金属有机框架-六方氮化硼复合粒子与天然胶乳的质量比为1:75,搅拌混合均匀,得到天然胶乳混合液,向天然胶乳混合液中滴加质量浓度为3%的氯化钙水溶液进行破乳,然后置于烘箱中干燥,得到橡胶母料;将橡胶母料依次进行混炼、开炼,制得高导热天然橡胶复合材料。
[0024]
实施例3高导热天然橡胶复合材料的制备方法,包括以下步骤:1)将六方氮化硼置于马弗炉中在200℃下进行高温处理5h,冷却后得到六方氮化硼粉末,将六方氮化硼粉末按照质量体积比1g/70ml的比例添加到乙醇胺溶剂中,置于超声波清洗器中在90w下进行超声震荡12h,经过离心、洗涤、干燥得到六方氮化硼纳米片;
六方氮化硼纳米片预处理:将六方氮化硼纳米片加入质量浓度为0.8%的氢氧化钠溶液中,油浴加热至110℃,搅拌反应4h,经过离心分离、洗涤、干燥,得到羟基化六方氮化硼纳米片;将乙醇与水按照体积比10:2的比例混合得到乙醇与水的混合溶液,将环氧基硅烷偶联剂kh-560加入乙醇与水的混合溶液中,环氧基硅烷偶联剂kh-560与混合溶液的质量比为1:30,调节体系ph至5,水浴加热至55℃,搅拌进行水解40min,得到环氧基硅烷偶联剂水解液,将羟基化六方氮化硼纳米片加入环氧基硅烷偶联剂水解液中,羟基化六方氮化硼纳米片与环氧基硅烷偶联剂kh-560的质量比为1:0.6,搅拌反应3h,经过离心分离、洗涤、干燥,得到烷基化六方氮化硼纳米片;将透明质酸加入去离子水中搅拌溶解配制成质量浓度为0.5%的透明质酸水溶液,将烷基化六方氮化硼纳米片按照质量体积比1g/80ml的比例加入透明质酸水溶液中,加入四氯化锡催化剂,四氯化锡添加量为透明质酸的3wt%,在85℃下搅拌反应5h,经过离心分离、洗涤、干燥,得到预处理的六方氮化硼纳米片;2)将六水合硝酸锌加入按照质量体积比1g/70ml的比例加入到甲醇溶液中搅拌溶解,得到硝酸锌溶液,向硝酸锌溶液中加入经过预处理的六方氮化硼纳米片和碳纳米管,六水合硝酸锌、六方氮化硼纳米片、碳纳米管三者的质量比为1:0.5:0.1,超声震荡分散均匀,得到悬浮液;将2-甲基咪唑按照质量体积比1g/50ml的比例加入甲醇溶液中搅拌溶解,得到2-甲基咪唑溶液,将2-甲基咪唑溶液滴加到悬浮液中,六水合硝酸锌与2-甲基咪唑的混合质量比为1:9,在避光条件下室温搅拌反应3h,反应完成后经过离心、洗涤、干燥,得到金属有机框架-六方氮化硼复合粒子;3)将金属有机框架-六方氮化硼复合粒子按照质量体积比1g/100ml的比例加入去离子水中,搅拌分散均匀,得到金属有机框架-六方氮化硼复合粒子悬浮液,将金属有机框架-六方氮化硼复合粒子悬浮液加入固含量为50%的天然胶乳中,金属有机框架-六方氮化硼复合粒子与天然胶乳的质量比为1:60,搅拌混合均匀,得到天然胶乳混合液,向天然胶乳混合液中滴加质量浓度为3%的氯化钙水溶液进行破乳,然后置于烘箱中干燥,得到橡胶母料;将橡胶母料依次进行混炼、开炼,制得高导热天然橡胶复合材料。
[0025]
实施例4高导热天然橡胶复合材料的制备方法,包括以下步骤:1)将六方氮化硼置于马弗炉中在200℃下进行高温处理5h,冷却后得到六方氮化硼粉末,将六方氮化硼粉末按照质量体积比1g/70ml的比例添加到乙醇胺溶剂中,置于超声波清洗器中在90w下进行超声震荡12h,经过离心、洗涤、干燥得到六方氮化硼纳米片;六方氮化硼纳米片预处理:将六方氮化硼纳米片加入质量浓度为0.8%的氢氧化钠溶液中,油浴加热至110℃,搅拌反应4h,经过离心分离、洗涤、干燥,得到羟基化六方氮化硼纳米片;将乙醇与水按照体积比10:2的比例混合得到乙醇与水的混合溶液,将环氧基硅烷偶联剂kh-560加入乙醇与水的混合溶液中,环氧基硅烷偶联剂kh-560与混合溶液的质量比为1:30,调节体系ph至5,水浴加热至55℃,搅拌进行水解40min,得到环氧基硅烷偶联剂水解液,将羟基化六方氮化硼纳米片加入环氧基硅烷偶联剂水解液中,羟基化六方氮化硼纳米片与环氧基硅烷偶联剂kh-560的质量比为1:0.2,搅拌反应1h,经过离心分离、洗涤、干燥,得到烷基化六方氮化硼纳米片;将透明质酸加入去离子水中搅拌溶解配制成质量浓度为0.1%的透明质酸水溶液,将烷
基化六方氮化硼纳米片按照质量体积比1g/80ml的比例加入透明质酸水溶液中,加入四氯化锡催化剂,四氯化锡添加量为透明质酸的3wt%,在75℃下搅拌反应2h,经过离心分离、洗涤、干燥,得到预处理的六方氮化硼纳米片;2)将六水合硝酸锌加入按照质量体积比1g/70ml的比例加入到甲醇溶液中搅拌溶解,得到硝酸锌溶液,向硝酸锌溶液中加入经过预处理的六方氮化硼纳米片和碳纳米管,六水合硝酸锌、六方氮化硼纳米片、碳纳米管三者的质量比为1:0.3:0.06,超声震荡分散均匀,得到悬浮液;将2-甲基咪唑按照质量体积比1g/50ml的比例加入甲醇溶液中搅拌溶解,得到2-甲基咪唑溶液,将2-甲基咪唑溶液滴加到悬浮液中,六水合硝酸锌与2-甲基咪唑的混合质量比为1:6,在避光条件下室温搅拌反应1h,反应完成后经过离心、洗涤、干燥,得到金属有机框架-六方氮化硼复合粒子;3)将金属有机框架-六方氮化硼复合粒子按照质量体积比1g/100ml的比例加入去离子水中,搅拌分散均匀,得到金属有机框架-六方氮化硼复合粒子悬浮液,将金属有机框架-六方氮化硼复合粒子悬浮液加入固含量为50%的天然胶乳中,金属有机框架-六方氮化硼复合粒子与天然胶乳的质量比为1:80,搅拌混合均匀,得到天然胶乳混合液,向天然胶乳混合液中滴加质量浓度为3%的氯化钙水溶液进行破乳,然后置于烘箱中干燥,得到橡胶母料;将橡胶母料依次进行混炼、开炼,制得高导热天然橡胶复合材料。
[0026]
对比例1对比例1与实施例1的区别在于缺少步骤2),同时将步骤3)中金属有机框架-六方氮化硼复合粒子替换为六方氮化硼纳米片。
[0027]
对比例2对比例2与实施例1的区别在于步骤1)中六方氮化硼纳米片没有经过预处理。
[0028]
对比例3对比例3与实施例1的区别在于橡胶中没有添加导热填料。
[0029]
橡胶复合材料性能测试1.力学性能测试:使用万能拉伸试验机测量橡胶复合材料的拉伸强度和拉伸断裂伸长率,采用gb/t528-2009标准进行测试,所用试样为哑铃型样条,拉伸速率为500mm/10min,使用万能拉伸试验机测量橡胶复合材料的撕裂强度,采用gb/t529-2008标准进行测试,所使用的样品为y型样条。
[0030]
2.导热性能测试:导热系数是指在稳定传热条件下,材料两侧面表面的温差微滤1k时,在一定的时间内,通过1平方米面积所传递的热量,单位为w/m
·
k,它是表征材料导热性能的一项主要的物理参数。本发明采用稳态法测试天然橡胶的导热系数,将橡胶样品裁剪成厚度为2mm,直径为30mm的小圆片,通过drl-i导热系数测试仪测量样品的导热率,每一样品测试三次,取平均值,得到最后结果。
[0031]
3.红外热成像升温测试:使用红外热成像仪记录物体在相同时间内升高或者下降的温度,从而反映物体的导热性能。首先准备一块5mm厚度的不锈钢钢板,使用加热板将钢板的温度保持在90℃,钢板表面的温度要均匀一致,然后将大小厚度相同的样品放置于钢板的表面,使用红外热成像仪
每间隔10s记录下样品表面的温度。每间隔10s记录下样品表面的温度。
[0032]
由上述测试结果可以得到实施例制备得到的橡胶复合材料的导热系数和综合力学性能优于对比例1-3制备得到的橡胶材料。证明本发明通过在天然橡胶中添加金属有机框架-六方氮化硼复合粒子不仅能够大幅提高橡胶材料的导热性能,还能够提高橡胶材料的综合力学强度。实施例制备得到的橡胶复合材料导热性能优于对比例1,这是由于具有碳纳米管导热刺凸结构的金属有机框架-六方氮化硼复合粒子均匀分散在橡胶材料内部,能够形成具有一定规整结构的导热网络,提高橡胶材料的导热效率;金属有机框架-六方氮化硼导热复合粒子表面由碳纳米管组成的导热刺凸结构能够缩短导热粒子与导热粒子之间的间隔,进一步提高橡胶材料的导热效率,进而提高橡胶材料的导热性能。实施例制备得到的橡胶材料的导热性能优于对比例2,证明通过对六方氮化硼纳米片进行预处理能够提高橡胶材料的导热性能。实施例制备得到的橡胶复合材料的拉伸强度和撕裂强度优于对比例1和对比例3,这是由于金属有机框架-六方氮化硼复合粒子能够起到对橡胶材料起到增强作用,且金属有机框架-六方氮化硼复合粒子上的刺凸结构能够增加天然橡胶与导热粒子的结合作用力,进一步提高橡胶复合材料的力学强度。
[0033]
由图1红外热成像升温测试材料表面温度随时间变化曲线图可以得到,在温升过程中实施例1橡胶复材料表面温度相对于对比例1和对比例2在相同的时间内具有更高的温度,证明实施例1制备得到的橡胶复合材料具有更好的导热性能。