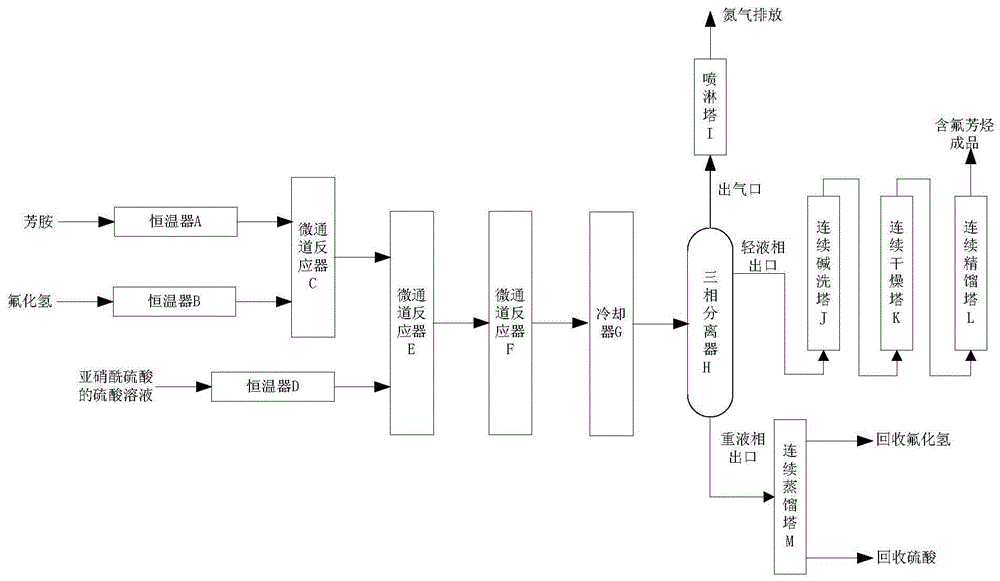
本发明涉及一种含氟芳烃类化合物的全连续流合成工艺,属于卤代烃碳环有机化合物制备
技术领域:
。
背景技术:
:含氟芳烃类化合物,如氟苯、甲基氟苯等,是芳香族氟化物重要的基础原料,不仅可直接用于医药、农药和染料等的合成,而且可以经过硝化、氯化、酰化等反应,合成多种氟苯衍生物用于上述领域,近年来还应用于特种工程塑料制备等领域,用途十分广泛,市场需求逐年增高。含氟芳烃类化合物的工业化生产方法主要有三种:巴兹-席曼法、卤素交换法和氟化氢法。巴兹-席曼法是目前含氟芳烃类化合物生产中常用的一种方法,但其需消耗大量四氟硼酸,热分解过程中不仅产生氮气,而且还释放强腐蚀和有毒的三氟化硼气体,环境污染严重,生产过程安全隐患大,目前逐渐面临淘汰压力。卤素交换法相对于巴兹-席曼法,生产操作更简单,安全风险较低,但其仅适用于苯环上含有强吸电子基团的卤代芳烃,应用范围较窄。氟化氢法,是对巴兹-席曼法的提升,其避免了四氟硼酸的使用,因此在热分解过程中不产生强腐蚀和有毒的三氟化硼气体,在一定程度上提升了反应的安全性和环境的友好性,不足之处在于,反应过程使用过量氟化氢,由于氟化氢的低沸点、高挥发性、高腐蚀性和高毒性,使得生产过程仍存在较大安全隐患,因此,如何降低生产过程中氟化氢持液量和无组织挥发量,提升生产过程的安全性,直接决定着氟化氢法的应用范围。目前,氟化氢法在氟苯生产中已获得应用。传统氟化氢法生产氟苯的工艺过程如下:苯胺首先在氟化氢中成盐,然后与干燥的亚硝酸钠进行重氮化反应,反应温度控制在0~10℃,反应结束后,重氮盐溶液在40℃以下热分解,热分解结束后,静置分层,分出的有机层经水洗、碱洗、水蒸汽蒸馏得到氟苯粗品,最后经无水氯化钙脱水制得氟苯成品,收率约80%,所有过程均采用间歇釜式操作。传统氟化氢法相较于其它工业化氟苯生产法,其优点在于:单位产品耗用原料少、生产流程短、设备投资省、回报周期短、反应收率高、产品质量好(纯度>99%)等优点,具有很强的竞争力,是目前国内外工业生产氟苯的主要方法。尽管如此,传统氟化氢法因采用间歇釜式的生产方式,无可避免存在以下缺点:(1)生产安全性较差。首先,生产过程中氟化氢持液量巨大,而氟化氢具有低沸点、高挥发性、高腐蚀性和高毒性等特点,导致生产过程存在较大的安全隐患;其次,重氮盐对热非常敏感,且在热分解过程有氮气生成,加之氟化氢沸点低挥发快,一旦升温过快,就会引起反应釜内重氮盐快速分解,产生大量挥化性气体,使体系压力急剧上升,造成严重的安全问题,甚至发生爆炸。(2)反应收率偏低。在热分解阶段,为了控制热分解速度,确保氮气有序释放,采用逐步升温的方式,整个重氮盐热分解过程长达6小时以上,在长时间的加热过程中,部分重氮盐发生诸如水解、聚合等副反应,导致反应收率仅能达到80%左右。(3)三废量多,处理困难。重氮盐长时间热分解过程中,部分重氮盐发生诸如水解、聚合等副反应,生成大量焦油状副产物,这些焦油状副产物又会影响氟苯、氟化氢等的分离与回收,进一步增加三废的产生,最终形成大量含氟危险固废,处理难度极大。(4)生产环境较差,不符合ehs的要求。由于采用间歇釜式的生产方式,无法很好做到生产过程的密封性,无法避免氟化氢挥发逸出,对操作工人及周围环境造成危害。人长期吸入低浓度氟化氢会引起慢性中毒、呕吐、头昏等症状,当hf浓度大于30μg/m3时能引起急性中毒,大气中的氟化氢还会导致银杏、苹果、大麦、玉米、水稻等果树和农作物减产。为了克服传统间歇釜式氟化氢法生产氟苯存在的不足,cn110283039a采用管式反应器进行重氮盐热分解反应以替代传统的釜式热分解反应,但由于管式反应器换热效果不佳,为了避免反应热的蓄积,只能采用减慢进料速度和延长热分解时间来克服,导致其热分解反应时间仍较长,热分解反应的失控风险依然存在,也无法很好克服副反应的发生,反应稳定性较差,此外,苯胺与氟化氢的成盐反应以及重氮化反应仍采用间歇釜式工艺,因此对氟化氢法生产氟苯工艺的提升有限。cn111116303a在上述技术的基础上,以亚硝酰硫酸作为重氮化试剂,采用碳化硅材质的微通道反应器,实现苯胺氟化氢盐的氢氟酸溶液与亚硝酰硫酸的连续重氮化反应,重氮化反应液则进入热解器,进行5~60分钟的热分解反应,最后进行一系列的后处理,得到氟苯,该技术在重氮化反应阶段采用碳化硅微通道反应器,解决重氮化反应的连续问题,相对于传统间歇釜式氟化氢法生产工艺有较大提升,但其重氮盐的热分解反应仍使用管式反应器,热分解反应时间仍较长,此外,苯胺与氟化氢成盐反应仍采用间歇釜式操作,生产过程氟化氢的持液量仍然很大,氟化氢的安全风险并未有效降低,后处理也采有传统的间歇方式,仅实现了对间歇釜式氟化氢法生产工艺的部分提升,并未从根本上解决氟化氢法存在的弊端。因此,针对氟化氢法生产工艺存在的不足,仍有大量优化工作需要进行思考与研究。技术实现要素:有鉴于此,针对现有技术存在的不足,本发明提供了一种含氟芳烃类化合物的高效、安全的全连续流合成工艺,具有反应收率高、产品质量优、生产安全性好、污染排放少、可实现全流程连续化生产和自动化控制等优点。本发明采用的技术方案如下:一种含氟芳烃类化合物的全连续流合成工艺,其特征在于,包括以下步骤:(1)依据芳胺与氟化氢的投料比例,将芳胺泵入恒温器a中,将氟化氢泵入恒温器b中,进行物料温度恒定;(2)恒温器中流出的芳胺和氟化氢,流入微通道反应器c中进行成盐反应,得到芳胺氟化氢盐的氢氟酸溶液;(3)依据亚硝酰硫酸与芳胺的投料比例,将亚硝酰硫酸的硫酸溶液泵入恒温器d中,进行物料温度恒定;(4)微通道反应器c中流出的芳胺氟化氢盐的氢氟酸溶液、恒温器d中流出的亚硝酰硫酸的硫酸溶液,流入微通道反应器e中进行重氮化反应,得到芳基重氮盐溶液;(5)微通道反应器e中流出的芳基重氮盐溶液,流入微通道反应器f中进行热分解反应,得到含氟芳烃、氢氟酸、硫酸、氮气组成的混合物;(6)微通道反应器f中流出的含氟芳烃、氢氟酸、硫酸、氮气组成的混合物,流经冷却器g后,进入三相分离器h中进行连续分离,三相分离器h出气口排出氮气,三相分离器h轻液相出口流出含氟芳烃粗品,三相分离器h重液相出口流出氢氟酸与硫酸的混合物;(7)三相分离器h出气口排出的氮气,经喷淋塔i喷淋除酸后排放;(8)三相分离器h轻液相出口流出的含氟芳烃粗品,进连续碱洗塔j碱洗除酸后,经连续干燥塔k脱水、连续精馏塔l精馏,得到含氟芳烃成品;(9)三相分离器h重液相出口流出的氢氟酸与硫酸混合物,经连续蒸馏塔m蒸馏,得到回收氟化氢和回收硫酸。本发明可用如下反应式表示:其中r1~r5分别独立选择h、c1~c3的直链或支链烷基。本发明进一步设置如下:所述的芳胺,选自以下任一种:苯胺、邻甲基苯胺、间甲基苯胺、对甲基苯胺、邻乙基苯胺、间乙基苯胺、对乙基苯胺、2,3-二甲基苯胺、2,4-二甲基苯胺、2,5-二甲基苯胺、2,6-二甲基苯胺、3,4-二甲基苯胺、3,5-二甲基苯胺、2,3,4-三甲基苯胺、2,3,5-三甲基苯胺、2,3,6-三甲基苯胺、2,4,5-三甲基苯胺、2,4,6-三甲基苯胺、3,4,5-三甲基苯胺、2,3,4,5-四甲基苯胺、2,3,5,6-四甲基苯胺、2,3,4,6-四甲基苯胺、五甲基苯胺。所述的氟化氢,要求含水量越低越好,但在实际使用过程中,无法做到氟化氢绝对无水,因此氟化氢含水量要求小于1.0%,优选的氟化氢含水量小于0.5%,更优选的氟化氢含水量小于0.2%。氟化氢含水量的增加,将导致氟化氢腐蚀性增加,增大设备腐蚀损坏的风险,此外,氟化氢中含有的水分,在后续重氮化与热分解反应中,还可能引发重氮盐水解副反应,导致焦油生成,不仅降低反应收率,而且增加微通道反应器堵塞风险。所述的亚硝酰硫酸,为亚硝酰硫酸的硫酸溶液,其中亚硝酰硫酸的有效含量为10%~50%,优选的亚硝酰硫酸的含量为20%~40%。亚硝酰硫酸中的硫酸,仅作为溶剂使用,只有亚硝酰硫酸作为重氮化试剂,与芳胺反应生成相应的重氮盐。芳胺、氟化氢、亚硝酰硫酸的投料比例为:芳胺、氟化氢与亚硝酰硫酸三者的物质的量之比为1:(5~50):(1~1.2)。恒温器a、b、c,用于控制原料芳胺、氟化氢和亚硝酰硫酸进入微通道反应器前的温度,主要目的:(1)稳定进入微通道反应器的物料温度,避免物料温度波动,特别是物料温度随时间、季节、地理位置等变化而变化,有利于系统全天候全地域稳定运行;(2)恒定的物料温度,有利于微通道反应器保持稳定状态,有利于全连续流系统的调试,在调试稳定后,确保全连续流系统长期稳定运行。恒温器的基本原理与换热器一致,通过相互隔离的可调温的换热介质,对进入恒温器的物料进行温度调节,使物料温度恒定在所需温度范围。芳胺经恒温器a后,出口温度控制在-20~70℃,温度波动越小越好,一般要求温度波动小于±2℃,优选的温度波动小于±1℃,更优选的温度波动小于±0.5℃;氟化氢经恒温器b后,出口温度控制在-50~20℃,温度波动越小越好,一般要求温度波动小于±2℃,优选的温度波动小于±1℃,更优选的温度波动小于±0.5℃;亚硝酰硫酸的硫酸溶液经恒温器d恒温后,温度控制在-30~50℃,温度波动越小越好,一般要求温度波动小于±2℃,优选的温度波动小于±1℃,更优选的温度波动小于±0.5℃。根据接触物料性质的不同,恒温器a、b、c的材质选择有所区别,其中恒温器a因接触的物料为芳胺,腐蚀性较低,因此材质的选择范围较广,如碳化硅、蒙耐尔合金、哈氏合金、316l、304l等均可适用,对于恒温器b、c,因接触物料的腐蚀性较高,需选择具有较好耐腐蚀性能的材质,如碳化硅、蒙耐尔合金、哈氏合金等。所述的微通道反应器c,要求具有优良的混合效果和优异的换热效果,能及时将芳胺和氟化氢反应生成芳胺氟化氢盐所产生的热量及时导出,材质要求能耐受氢氟酸的腐蚀,可供选择的材料有:碳化硅、蒙耐尔合金、哈氏合金等。微通道反应器c出口物料温度控制在-10~20℃且温度波动越小越好,一般要求温度波动小于±2℃,优选的温度波动小于±1℃,更优选的温度波动小于±0.5℃。在微通道反应器c中,芳胺与氟化氢反应生成芳胺氟化氢盐,溶解于过量的氢氟酸中,形成芳胺氟化氢盐的氢氟酸溶液,从微通道反应器c出口流出,进入微通道反应器e。所述的微通道反应器e,要求具有优良的混合效果和优异的换热效果,能及时将芳胺氟化氢盐与亚硝酰硫酸发生重氮化反应产生的热量导出,材质要求能耐受氢氟酸和硫酸的腐蚀,可供选择的材料有:碳化硅、蒙耐尔合金、哈氏合金等。微通道反应器e内物料温度控制在-20~20℃,出口物料温度控制在-20~20℃,且温度波动越小越好,一般要求温度波动小于±2℃,优选的温度波动小于±1℃,更优选的温度波动小于±0.5℃。在微通道反应器e中,芳胺氟化氢盐与亚硝酰硫酸反应生成芳基重氮盐,溶解于过量的氢氟酸中,形成芳基重氮盐的氢氟酸溶液,从微通道反应器e出口流出,进入微通道反应器f。所述的微通道反应器f,要求具有优良的混合效果和优异的换热效果,能及时将重氮盐热分解过程中产生的热量导出,材质要求能耐受氢氟酸和硫酸的腐蚀,可供选择的材料有:碳化硅、蒙耐尔合金、哈氏合金等。微通道反应器f内物料温度控制在20~100℃,出口物料温度控制在20~100℃,温度波动小于±2℃。微通道反应器f中,芳基重氮盐经热分解反应,生成含氟芳烃、氢氟酸、硫酸、氮气等组成的混合物,从微通道反应器f出口流出,进入冷却器g。所述的冷却器g,要求具有优异的换热效果,能将热分解后形成的含氟芳烃、氢氟酸、硫酸、氮气等组成的混合物快速降温,避免除氮气外的低沸液体挥发,冷却器g材质要求能耐受氢氟酸和硫酸的腐蚀,可供选择的材料有:碳化硅、蒙耐尔合金、哈氏合金等。冷却器g出口物料温度控制在-20~20℃。由含氟芳烃、氢氟酸、硫酸、氮气等组成的混合物经冷却器g冷却后,进入三相分离器f。所述的三相分离器h,要求能确保由氮气形成气相、由含氟芳烃形成的轻液相、由氢氟酸和硫酸形成的重液相三相充分分离,根据三相的密度差,从三相分离器h的不同位置流出三相分离器,其中氮气作为气相组分从三相分离器h的出气口排出,由含氟芳烃形成的轻液相从三相分离器h的轻液相出口流出,由氢氟酸和硫酸形成的重液相从三相分离器h的重液相出口流出,实现三相连续分离。三相分离器h可采用卧式结构,也可采用立式结构,材质要求能耐受氢氟酸和硫酸的腐蚀,可供选择的材料有:碳化硅、蒙耐尔合金、哈氏合金、ptfe等。三相分离器h内物料温度控制在-20~20℃。从三相分离器h出气口排出的氮气,含有少量氟化氢,采用喷淋塔i喷淋除酸的方式,除去夹带的氟化氢,使氮气符合直接排放标准。喷淋塔i的喷淋方式可以选用单级碱溶液喷淋,或多级碱溶液喷淋,或水、碱溶液综合喷淋等,喷淋塔结构可以为填料塔或者板式塔。所用的碱溶液,为无机碱的水溶液,无机碱选自以下一种或几种:氢氧化钠、氢氧化钾、碳酸钠、碳酸钾,碱溶液的ph值要求大于9。喷淋塔i的操作温度为常温。从三相分离器h轻液相出口流出的含氟芳烃粗品中,夹带有少量的氟化氢和硫酸,经连续碱洗塔j碱洗除酸的方式去除,然后进入连续干燥塔k脱水,最后经连续精馏塔l精馏得到含氟芳烃成品。所述的连续碱洗塔j碱洗除酸,采用液相逆流方式,碱溶液从碱洗塔上部进入,从碱洗塔底部经二相分离后流出,含氟芳烃粗品从碱洗塔下部进入,从碱洗塔顶部经二相分离后流出;所用的碱溶液,为无机碱的水溶液,无机碱选自以下一种或几种:氢氧化钠、氢氧化钾、碳酸钠、碳酸钾,碱溶液的ph值要求大于9;操作温度为常温。所述的连续干燥塔k脱水,干燥塔填装脱水分子筛,含氟芳烃粗品从干燥塔底部连续进入,经过脱水分子筛层,从干燥塔上部流出;操作温度为常温。所述连续精馏塔l精馏,精馏塔结构可以为填料塔或者板式塔,精馏方式为常压精馏,塔顶馏分经冷凝后得到含氟芳烃成品。从三相分离器h重液相出口流出的氢氟酸与硫酸混合物,进入连续蒸馏塔m蒸馏,蒸馏塔结构可以为填料塔或者板式塔,材质要求能耐受氢氟酸和硫酸的腐蚀,可供选择的材料有:碳化硅、蒙耐尔合金、哈氏合金、ptfe等,蒸馏方式采用常压蒸馏,塔顶馏分经冷凝后得到回收氟化氢,塔底浓缩物为回收硫酸。回收氟化氢可循环套用于成盐反应。以主要原料芳胺作为计算基准,采用本发明的含氟芳烃类化合物的全连续流合成工艺,含氟芳烃摩尔收率可达90%以上,纯度99.9%以上,其中部分含氟芳烃,如氟苯、对氟甲苯等收率可达95%以上。本发明提供的一种含氟芳烃类化合物的全连续流合成工艺,与现有技术相比,主要创新点有:(1)原料芳胺、氟化氢、亚硝酰硫酸经恒温器控制在适当温度后,再进入微通道反应器,避免不同原料温度对全连续流体系造成热冲击,确保体系稳定运行;(2)首创微通道反应器进行芳胺与氟化氢的成盐反应,实现了成盐工序的连续化进行,不仅避免了传统釜式成盐反应时,因散热不畅引起的局部过热导致氟化氢挥发,和成盐过程缓慢、设备效率低等不足,更重要的是,为含氟芳烃类化合物的全连续流生产工艺的实现补齐短板,奠定基础;(3)热分解反应,采用微通道反应器替代传统反应釜和管式反应器,以微通道反应器更佳的混合效果、更优的传热效率和更少的持液量,大幅提升热分解反应的安全性、环保性,提高反应收率;(4)、采用新老工艺、新老设备相结合的方式,在采用最新的微通道反应器的基础上,结合传统的连续三相分离器、连续喷淋、连续洗涤、连续精馏等技术,实现从原料进料、物料恒温、成盐反应、重氮反应、热分解反应、物料分离、产品纯化等全生产流程的连续化生产;(5)在采用全连续流含氟芳烃生产工艺后,整个生产过程中采用微通道反应器和全封闭反应体系,最大限度地减少生产设备中氟化氢持液量和氟化氢无组织挥发量,从根本上解决了氟化氢法生产含氟芳烃类化合物存在的安全性问题,大幅提升了生产过程的ehs标准,有利于氟化氢法生产含氟芳烃类化合物的推广应用。以下结合附图和具体实施方式对本发明做进一步说明。在此需要说明的是,下列实施方式,仅用于帮助理解本发明,并不构成对本发明的限定。具体实施方式不可能权尽本发明所有技术特征,只要说明书中所涉及的技术特征,彼此不构成冲突,相互间均可组合,组成新的实施方式。附图说明图1为本申请中的工艺流程示意图。具体实施方式基本实施例:一种含氟芳烃类化合物的全连续流合成工艺,如图1所示,其设备清单和操作流程如下:表1设备清单操作流程:(1)芳胺经计量泵计量后泵入恒温器a中,流速控制在10~100g/min,经恒温器a后,出口温度控制在-20~70℃,温度波动小于±0.5℃。(2)氟化氢经计量泵计量后泵入恒温器b中,流速控制在10~900g/min,经恒温器a后,出口温度控制在-50~20℃,温度波动小于±0.5℃。(3)恒温器a、b中流出的芳胺和氟化氢,立刻流入微通道反应器c中,经成盐反应得到芳胺氟化氢盐溶液,微通道反应器c出口温度控制在-10~20℃,温度波动小于±0.5℃。(4)亚硝酰硫酸的硫酸溶液经计量泵计量后泵入恒温器d中,流速控制在10~800g/min,经恒温器d后,出口温度控制在-30~50℃,温度波动小于±0.5℃。(5)微通道反应器c中流出的芳胺氟化氢盐溶液,与从恒温器d中流出的亚硝酰硫酸的硫酸溶液,一起流入微通道反应器e中进行重氮化反应,反应器内物料温度控制在-20~20℃,出口物料温度控制在-20~20℃,温度波动小于±0.5℃。(6)微通道反应器e中流出的芳基重氮盐溶液,流入微通道反应器f中进行热分解反应,反应器内物料温度控制在20~100℃,出口物料温度控制在20~100℃,温度波动小于±2℃,得到含氟芳烃、氢氟酸、硫酸、氮气组成的混合物。(7)微通道反应器f中流出的含氟芳烃、氢氟酸、硫酸、氮气组成的混合物,流经冷却器g后,出口温度控制-20~20℃。(8)冷却器g流出的含氟芳烃、氢氟酸、硫酸、氮气组成的混合物,进入三相分离器h中进行连续分离,三相分离器h顶部出气口排出氮气,三相分离器h上部轻液相出口流出含氟芳烃粗品,三相分离器h底部重液相出口流出氢氟酸与硫酸的混合物,三相分离器h内物料温度控制在-20~20℃。(9)三相分离器h顶部出气口排出的氮气,经喷淋塔i喷淋除酸后排放。喷淋塔i选用二级串联碱喷淋塔,结构采用填料塔形式,内填环状ptfe填料,喷淋所用的碱溶液为氢氧化钾水溶液,ph值控制在9以上,操作温度为室温。(10)三相分离器h上部轻液相出口流出的含氟芳烃粗品,先经连续碱洗塔j除酸,再经连续干燥塔k脱水、连续精馏塔l精馏后,得到含氟芳烃成品。连续碱洗塔j结构为填料塔结构,采用液相逆流方式,碱液从碱洗塔上部进入,从碱洗塔底部经二相分离后流出,含氟芳烃粗品从碱洗塔下部进入,从碱洗塔顶部经二相分离后流出,操作温度为常温;连续干燥塔k为填料塔结构,内装3a分子筛,采用三塔形式,一用一备一活化,三塔间可灵活切换,含氟芳烃粗品从干燥塔下部进入,从干燥塔上部流出,操作温度为常温;连续精馏塔l采用填料结构,内装不锈钢丝网填料,塔釜加热,常压精馏,塔顶馏分经冷凝后得到含氟芳烃成品。(11)从三相分离器h底部重液相出口流出的氢氟酸与硫酸混合物,经连续蒸馏塔m蒸馏,塔顶馏分经冷凝后得到回收氟化氢,塔釜浓缩液为回收硫酸;连续蒸馏塔m采用填料塔结构,内装环状ptfe填料,塔釜加热,常压蒸馏。以下就本方案实施过程中的原料种类,流速、温度等参数进行具体研究。实施例1本实施例为氟苯的全连续流合成,结合图1,具体步骤以下:(1)苯胺经计量泵计量后泵入恒温器a中,流速控制在50g/min,经恒温器a后,出口温度控制在5±0.5℃;(2)氟化氢经计量泵计量后泵入恒温器b中,流速控制在215g/min,经恒温器a后,出口温度控制在-10±0.5℃;(3)恒温器a、b中流出的苯胺和氟化氢,立刻流入微通道反应器c中,经成盐反应得到苯胺氟化氢盐的氢氟酸溶液,微通道反应器c出口温度控制在0±0.5℃;(4)40%亚硝酰硫酸的硫酸溶液经计量泵计量后泵入恒温器d中,流速控制在181g/min,经恒温器d后,出口温度控制在0±0.5℃;(5)微通道反应器c中流出的苯胺氟化氢盐的氢氟酸溶液,与从恒温器d中流出的亚硝酰硫酸的硫酸溶液,一起流入微通道反应器e中进行重氮化反应,重氮化反应温度控制在5~10℃,出口物料温度控制在10±0.5℃,得到苯基重氮盐溶液;(6)微通道反应器e中流出的苯基重氮盐溶液,流入微通道反应器f中进行热分解反应,热分解温度控制在70±2℃,出口得到氟苯、氢氟酸、硫酸、氮气组成的混合物;(7)微通道反应器f中流出的氟苯、氢氟酸、硫酸、氮气组成的混合物,流入冷却器g降温,冷却器g出口温度控制5~10℃;(8)冷却器g流出的氟苯、氢氟酸、硫酸、氮气组成的混合物,进入三相分离器h中进行连续分离,三相分离器h顶部出气口排出氮气,三相分离器h上部轻液相出口流出氟苯粗品,三相分离器h底部重液相出口流出氢氟酸与硫酸的混合物,三相分离器h内物料温度控制在5~10℃;(9)三相分离器h顶部出气口排出的氮气,经二级串联喷淋塔i喷淋除酸后排放,喷淋塔i操作温度为室温;(10)三相分离器h上部轻液相出口流出的氟苯粗品,先经连续碱洗塔j碱洗除酸,再经连续干燥塔k脱水、连续精馏塔l精馏后,得到氟苯成品;(11)三相分离器h底部重液相出口流出的氢氟酸与硫酸混合物,经连续蒸馏塔m蒸馏,塔顶馏分经冷凝后得到回收氢氟酸,塔釜浓缩液为回收硫酸。本实施例的氟苯高效连续流合成工艺,从开始进料至调试稳定,耗时12小时。从调试完成后开始计时,稳定运行300小时,结果汇总如下:共消耗苯胺900公斤、氢氟酸3870公斤、40%亚硝酰硫酸溶液3258公斤,得到氟苯成品918.5公斤,收率98.9%,纯度99.97%。实施例2本实施例为对甲基氟苯的全连续流合成,结合图1,具体步骤以下:(1)对甲基苯胺经计量泵计量后泵入恒温器a中,流速控制在60g/min,经恒温器a后,出口温度控制在55±0.5℃;(2)氟化氢经计量泵计量后泵入恒温器b中,流速控制在168g/min,经恒温器a后,出口温度控制在-20±0.5℃;(3)恒温器a、b中流出的对甲基苯胺和氟化氢,立刻流入微通道反应器c中,经成盐反应得到对甲基苯胺氟化氢盐的氢氟酸溶液,微通道反应器c出口温度控制在10±0.5℃;(4)30%亚硝酰硫酸的硫酸溶液经计量泵计量后泵入恒温器d中,流速控制在250g/min,经恒温器d后,出口温度控制在-5±0.5℃;(5)微通道反应器c中流出的对甲基苯胺氟化氢盐的氢氟酸溶液,与从恒温器d中流出的亚硝酰硫酸的硫酸溶液,一起流入微通道反应器e中进行重氮化反应,重氮化反应温度控制在0~5℃,出口物料温度控制在5±0.5℃,得到对甲基苯基重氮盐溶液;(6)微通道反应器e中流出的对甲基苯基重氮盐溶液,流入微通道反应器f中进行热分解反应,热分解温度控制在60±2℃,出口得到对甲基氟苯、氢氟酸、硫酸、氮气组成的混合物;(7)微通道反应器f中流出的对甲基氟苯、氢氟酸、硫酸、氮气组成的混合物,流入冷却器g降温,冷却器g出口温度控制0~5℃;(8)冷却器g流出的对甲基氟苯、氢氟酸、硫酸、氮气组成的混合物,进入三相分离器h中进行连续分离,三相分离器h顶部出气口排出氮气,三相分离器h上部轻液相出口流出对甲基氟苯粗品,三相分离器h底部重液相出口流出氢氟酸与硫酸的混合物,三相分离器h内物料温度控制在0~5℃;(9)三相分离器h顶部出气口排出的氮气,经二级串联喷淋塔i喷淋除酸后排放,喷淋塔i操作温度为室温;(10)三相分离器h上部轻液相出口流出的对甲基氟苯粗品,先经连续碱洗塔j碱洗除酸,再经连续干燥塔k脱水、连续精馏塔l精馏后,得到对甲基氟苯成品;(11)三相分离器h底部重液相出口流出的氢氟酸与硫酸混合物,经连续蒸馏塔m蒸馏,塔顶馏分经冷凝后得到回收氢氟酸,塔釜浓缩液为回收硫酸。本实施例的对甲基氟苯高效连续流合成工艺,从开始进料至调试稳定,耗时15小时。从调试完成后开始计时,稳定运行300小时,结果汇总如下:共消耗对甲基苯胺1080公斤、氢氟酸3024公斤、30%亚硝酰硫酸溶液4500公斤,得到对甲基氟苯成品1093.4公斤,收率98.5%,纯度99.93%。实施例3本实施例为邻甲基氟苯的全连续流合成,结合图1,具体步骤以下:(1)邻甲基苯胺经计量泵计量后泵入恒温器a中,流速控制在80g/min,经恒温器a后,出口温度控制在15±0.5℃;(2)氟化氢经计量泵计量后泵入恒温器b中,流速控制在150g/min,经恒温器a后,出口温度控制在-15±0.5℃;(3)恒温器a、b中流出的邻甲基苯胺和氟化氢,立刻流入微通道反应器c中,经成盐反应得到邻甲基苯胺氟化氢盐的氢氟酸溶液,微通道反应器c出口温度控制在-3±0.5℃;(4)20%亚硝酰硫酸的硫酸溶液经计量泵计量后泵入恒温器d中,流速控制在485g/min,经恒温器d后,出口温度控制在5±0.5℃;(5)微通道反应器c中流出的邻甲基苯胺氟化氢盐的氢氟酸溶液,与从恒温器d中流出的亚硝酰硫酸的硫酸溶液,一起流入微通道反应器e中进行重氮化反应,重氮化反应温度控制在-5~0℃,出口物料温度控制在0±0.5℃,得到邻甲基苯基重氮盐溶液;(6)微通道反应器e中流出的邻甲基苯基重氮盐溶液,流入微通道反应器f中进行热分解反应,热分解温度控制在50±2℃,出口得到邻甲基氟苯、氢氟酸、硫酸、氮气组成的混合物;(7)微通道反应器f中流出的邻甲基氟苯、氢氟酸、硫酸、氮气组成的混合物,流入冷却器g降温,冷却器g出口温度控制0~5℃;(8)冷却器g流出的邻甲基氟苯、氢氟酸、硫酸、氮气组成的混合物,进入三相分离器h中进行连续分离,三相分离器h顶部出气口排出氮气,三相分离器h上部轻液相出口流出邻甲基氟苯粗品,三相分离器h底部重液相出口流出氢氟酸与硫酸的混合物,三相分离器h内物料温度控制在0~5℃。;(9)三相分离器h顶部出气口排出的氮气,经二级串联喷淋塔i喷淋除酸后排放,喷淋塔i操作温度为室温;(10)三相分离器h上部轻液相出口流出的邻甲基氟苯粗品,先经连续碱洗塔j碱洗除酸,再经连续干燥塔k脱水、连续精馏塔l精馏后,得到邻甲基氟苯成品;(11)三相分离器h底部重液相出口流出的氢氟酸与硫酸混合物,经连续蒸馏塔m蒸馏,塔顶馏分经冷凝后得到回收氢氟酸,塔釜浓缩液为回收硫酸。本实施例的邻甲基氟苯高效连续流合成工艺,从开始进料至调试稳定,耗时15小时。从调试完成后开始计时,稳定运行300小时,结果汇总如下:共消耗邻甲基苯胺1440公斤、氢氟酸2700公斤、20%亚硝酰硫酸溶液8730公斤,得到邻甲基氟苯成品1451.9公斤,收率98.1%,纯度99.91%。实施例4本实施例为间甲基氟苯的全连续流合成,结合图1,具体步骤以下:(1)间甲基苯胺经计量泵计量后泵入恒温器a中,流速控制在70g/min,经恒温器a后,出口温度控制在-5±0.5℃;(2)氟化氢经计量泵计量后泵入恒温器b中,流速控制在157g/min,经恒温器a后,出口温度控制在0±0.5℃;(3)恒温器a、b中流出的间甲基苯胺和氟化氢,立刻流入微通道反应器c中,经成盐反应得到间甲基苯胺氟化氢盐的氢氟酸溶液,微通道反应器c出口温度控制在0±0.5℃;(4)25%亚硝酰硫酸的硫酸溶液经计量泵计量后泵入恒温器d中,流速控制在359g/min,经恒温器d后,出口温度控制在2±0.5℃;(5)微通道反应器c中流出的间甲基苯胺氟化氢盐的氢氟酸溶液,与从恒温器d中流出的亚硝酰硫酸的硫酸溶液,一起流入微通道反应器e中进行重氮化反应,重氮化反应温度控制在-2~2℃,出口物料温度控制在2±0.5℃,得到间甲基苯基重氮盐溶液;(6)微通道反应器e中流出的间甲基苯基重氮盐溶液,流入微通道反应器f中进行热分解反应,热分解温度控制在40±2℃,出口得到间甲基氟苯、氢氟酸、硫酸、氮气组成的混合物;(7)微通道反应器f中流出的间甲基氟苯、氢氟酸、硫酸、氮气组成的混合物,流入冷却器g降温,冷却器g出口温度控制0~10℃;(8)冷却器g流出的间甲基氟苯、氢氟酸、硫酸、氮气组成的混合物,进入三相分离器h中进行连续分离,三相分离器h顶部出气口排出氮气,三相分离器h上部轻液相出口流出间甲基氟苯粗品,三相分离器h底部重液相出口流出氢氟酸与硫酸的混合物,三相分离器h内物料温度控制在0~10℃。;(9)三相分离器h顶部出气口排出的氮气,经二级串联喷淋塔i喷淋除酸后排放,喷淋塔i操作温度为室温;(10)三相分离器h上部轻液相出口流出的间甲基氟苯粗品,先经连续碱洗塔j碱洗除酸,再经连续干燥塔k脱水、连续精馏塔l精馏后,得到间甲基氟苯成品;(11)三相分离器h底部重液相出口流出的氢氟酸与硫酸混合物,经连续蒸馏塔m蒸馏,塔顶馏分经冷凝后得到回收氢氟酸,塔釜浓缩液为回收硫酸。本实施例的间甲基氟苯高效连续流合成工艺,从开始进料至调试稳定,耗时15小时。从调试完成后开始计时,稳定运行300小时,结果汇总如下:共消耗间甲基苯胺1260公斤、氢氟酸2826公斤、25%亚硝酰硫酸溶液6462公斤,得到间甲基氟苯成品1273公斤,收率98.3%,纯度99.94%。实施例5本实施例为3,5-二甲基氟苯的全连续流合成,氟化氢回收后进行循环套用,结合图1,具体步骤以下:(1)3,5-二甲基苯胺经计量泵计量后泵入恒温器a中,流速控制在40g/min,经恒温器a后,出口温度控制在60±0.5℃;(2)氟化氢经计量泵计量后泵入恒温器b中,流速控制在198g/min,经恒温器a后,出口温度控制在-30±0.5℃;(3)恒温器a、b中流出的3,5-二甲基苯胺和氟化氢,立刻流入微通道反应器c中,经成盐反应得到3,5-二甲基苯胺氟化氢盐的氢氟酸溶液,微通道反应器c出口温度控制在5±0.5℃;(4)35%亚硝酰硫酸的硫酸溶液经计量泵计量后泵入恒温器d中,流速控制在132g/min,经恒温器d后,出口温度控制在-3±0.5℃;(5)微通道反应器c中流出的3,5-二甲基苯胺氟化氢盐的氢氟酸溶液,与从恒温器d中流出的亚硝酰硫酸的硫酸溶液,一起流入微通道反应器e中进行重氮化反应,重氮化反应温度控制在-10~-5℃,出口物料温度控制在-5±0.5℃,得到3,5-二甲基苯基重氮盐溶液;(6)微通道反应器e中流出的3,5-二甲基苯基重氮盐溶液,流入微通道反应器f中进行热分解反应,热分解温度控制在80±2℃,出口得到3,5-二甲基氟苯、氢氟酸、硫酸、氮气组成的混合物;(7)微通道反应器f中流出的3,5-二甲基氟苯、氢氟酸、硫酸、氮气组成的混合物,流入冷却器g降温,冷却器g出口温度控制0~5℃;(8)冷却器g流出的3,5-二甲基氟苯、氢氟酸、硫酸、氮气组成的混合物,进入三相分离器h中进行连续分离,三相分离器h顶部出气口排出氮气,三相分离器h上部轻液相出口流出3,5-二甲基氟苯粗品,三相分离器h底部重液相出口流出氢氟酸与硫酸的混合物,三相分离器h内物料温度控制在5~10℃。;(9)三相分离器h顶部出气口排出的氮气,经二级串联喷淋塔i喷淋除酸后排放,喷淋塔i操作温度为室温;(10)三相分离器h上部轻液相出口流出的3,5-二甲基氟苯粗品,先经连续碱洗塔j碱洗除酸,再经连续干燥塔k脱水、连续精馏塔l精馏后,得到氟苯成品;(11)三相分离器h底部重液相出口流出的氢氟酸与硫酸混合物,经连续蒸馏塔m蒸馏,塔顶馏分经冷凝后得到回收氢氟酸,套用于成盐反应,塔釜浓缩液为回收硫酸。本实施例的3,5-二甲基氟苯高效连续流合成工艺,氟化氢回收后进行循环套用,从开始进料至调试稳定,耗时20小时。从调试完成后开始计时,稳定运行300小时,结果汇总如下:共消耗3,5-二甲基苯胺720公斤、氢氟酸142公斤、35%亚硝酰硫酸溶液2376公斤,得到3,5-二甲基氟苯成品717.8公斤,收率97.3%,纯度99.90%。实施例6本实施例与实施例1操作过程相同,区别在于苯胺与氟化氢的投料比例,研究苯胺与氟化氢的不同投料比例对反应的影响,结果汇总如表2所示。表2苯胺与氟化氢投料比例对反应的影响序号摩尔比苯胺流速氟化氢流速氟苯收率氟苯纯度11:550g/min53.7g/min90.3%99.80%21:850g/min85.9g/min97.1%99.91%31:1050g/min107.4g/min98.3%99.94%41:1250g/min128.9g/min98.6%99.95%51:1450g/min150.3g/min98.7%99.96%61:1650g/min171.8g/min98.8%99.97%71:1850g/min193.3g/min98.9%99.97%81:2050g/min214.8g/min98.9%99.97%91:2550g/min268.4g/min98.8%99.97%101:3050g/min322.1g/min98.5%99.96%111:3550g/min375.8g/min98.3%99.96%121:4050g/min429.5g/min98.0%99.95%131:5050g/min536.9g/min97.2%99.96%从表2可以看出,当苯胺与氟化氢的物质的量之比为1:(5~50)时,反应都能较好地进行,氟苯收率90%以上,纯度99.80%以上。当苯胺与氟化氢的物质的量之比小于1:8时,反应收率出现明显下降,究其原因,氟化氢在反应过程中不仅作为反应原料使用,同时又作为反应溶剂使用,过少的氢化氟用量,不利于苯胺氟化氢盐的溶解和稀释,导致反应液在微通道反应器中运动状况变差,传热与传质能力变弱,副反应增加,因而影响反应收率。过多的氟化氢用量,虽然不存在传热与传质问题,但会增加产品在氟化氢中的夹带损失,降低反应收率,过多的氟化氢用量还会降低合成效率,增加氟化氢回收压力。实施例7本实施例与实施例1操作过程相同,区别在于苯胺与亚硝酰硫酸的投料比例,研究苯胺与亚硝酰硫酸的不同投料比例对反应的影响,结果汇总如表3所示。表3苯胺与亚硝酰硫酸投料比例对反应的影响从表3可知,当苯胺与亚硝酰硫酸的投料配比为1:(1.0~1.2),反应都能较好地进行,氟苯收率90%以上,纯度99.80%以上。随着亚硝酰硫酸投料配比的增加,氟苯收率出现先上升后下降的变化,究其原因,亚硝酰硫酸的理论用量为苯胺物质的量的1当量,在实际反应时,亚硝酰硫酸还存在一定的损耗,当亚硝酰硫酸用量不足时,随着亚硝酰硫酸用量的增加,氟苯收率出现上升,但当亚硝酰硫酸的用量超过实际需要量后,体系中存在的过量的亚硝酰硫酸会引发副反应,导致氟苯收率下降。实施例8本实施例与实施例1相同,区别在于重氮化反应温度,研究不同重氮化温度对反应的影响,结果汇总如表4所示。表4重氮化温度对反应的影响从表4可知,当重氮化反应温度为-20~20℃时,反应都能较好地进行,氟苯收率90%以上,纯度99.80%以上。随着重氮化反应温度的升高,氟苯收率和纯度出现先上升后下降的变化,究其原因,当反应温度过低时,重氮化反应速度较慢,在微通道反应器的持液体积与物料流速固定的情况下,重氮化反应无法彻底进行,导致反应收率下降,而当重氮化反应温度过高时,易引发水解、聚合等一系列副反应,导致反应收率下降。实施例9本实施例与实施例1相同,区别在于热分解反应温度不同,研究不同热分解温度对反应的影响,结果汇总如表5所示。表5热分解温度对反应的影响序号热分解温度氟苯收率氟苯纯度130℃85.8%99.72%240℃91.5%99.91%350℃95.5%99.93%460℃97.8%99.96%570℃98.9%99.97%680℃97.5%99.95%790℃94.9%99.93%8100℃91.1%99.83%9110℃82.6%99.61%从表5可知,当热分解反应温度为40~100℃时,反应都能较好地进行,氟苯收率90%以上,纯度99.8%以上。随着热分解反应温度的升高,氟苯收率和纯度出现先上升后下降的变化,究其原因,当反应温度过低时,热分解反应速度较慢,在微通道反应器的持液体积与物料流速固定的情况下,热分解反应无法彻底进行,导致反应收率下降,而当热分解反应温度过高时,易引发水解、聚合等一系列副反应,导致反应收率下降。实施例10本实施例与实施例1相同,区别在于保持苯胺、氟化氢和亚硝酰硫酸投料比例不变的前提下,改变进料速度,研究不同进料速度对反应的影响,结果汇总如表6所示。表6进料速度对反应的影响对于已固定的全连续流反应装置,由于其设备尺寸已确定,特别是作为主反应设备的微通道反应器c、e和f,其内部结构与持液量已固定,因此,当物料流速变化时,必然引起物料在微通道反应器内运动状态与停留时间的变化。物料流速作为是全连续流反应装置运行的重要参数,其与微通道反应器结构、运行温度、物料配比等组成一组相互关联的复杂参数,决定全连续流合成工艺的成败。在微通道反应器结构、运行温度、物料配比固定的情况下,必然存在最佳流速,与上述已固定的参数相匹配。最佳流速,需要经过较长时间的设备运行调试才能最终获得,在最佳流速下,可确保物料在反应器内最合适的停留时间和最优良的运动状态,使反应在最佳状态下进行,从而获得最优的反应结果。当前第1页12