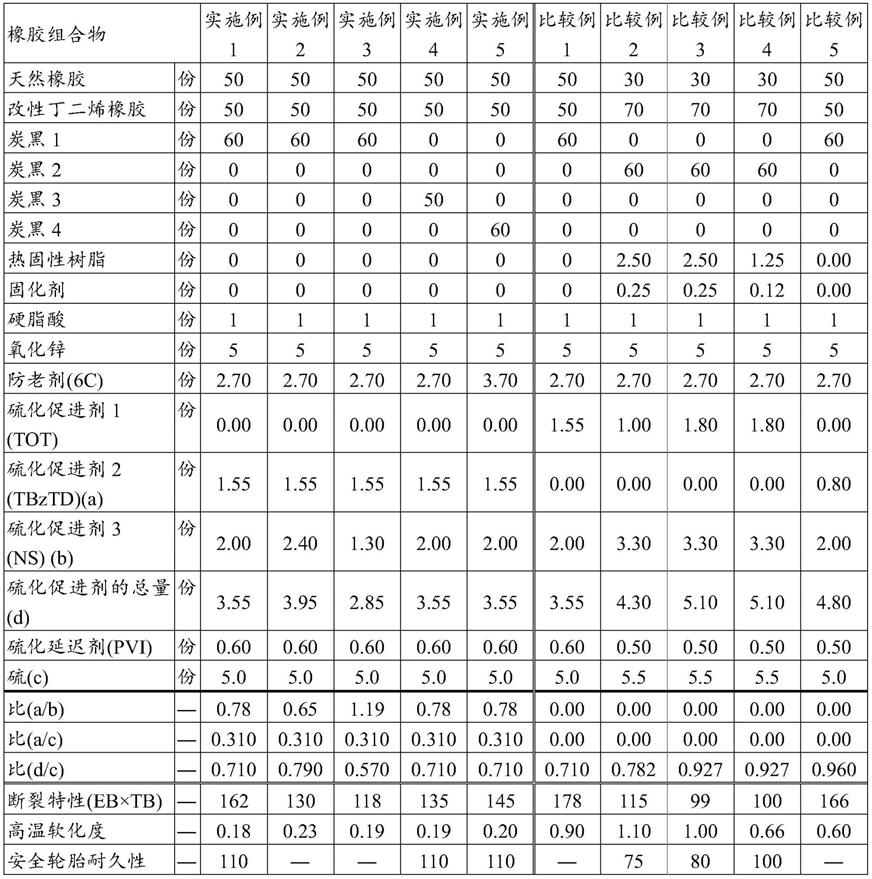
1.本发明涉及橡胶组合物和安全轮胎。
背景技术:2.迄今为止,在轮胎中,尤其是在安全轮胎中,为了提高胎侧壁部的刚性,设置由单独的橡胶组合物或橡胶组合物和纤维的复合物形成的胎侧加强层。
3.关于该安全轮胎,例如,公开了一种如下方法,即:通过使用橡胶组合物制造具有预定的拉伸强度的胎侧加强橡胶层,以提高安全耐久性的方法。该橡胶组合物是通过分别以预定量将橡胶成分、加强填料、热固性树脂、秋兰姆类硫化促进剂、秋兰姆类硫化促进剂以外的硫化促进剂和含硫的硫化剂共混而获得的(例如,参见专利文献1~3)。
4.此外,从提高橡胶组合物的挤出加工性的同时同时兼备高弹性模量和适合于安全运行的低发热性的观点出发,公开了一种通过将含有聚丁二烯(含有高结晶性间同立构聚丁二烯)的橡胶成分、秋兰姆类硫化促进剂和次磺酰胺类硫化促进剂以预定量共混来制备橡胶组合物的方法(例如,参见专利文献4)。
5.引用文献列表
6.专利文献
7.专利文献1:wo 2016/143755
8.专利文献2:wo 2016/143756
9.专利文献3:wo 2016/143757
10.专利文献4:jp 2005-263916a
技术实现要素:11.本发明要解决的技术问题
12.然而,通过专利文献1~4所记载的方法获得的轮胎需要进一步提高硫化橡胶的高温软化抑制性。
13.本发明的一个目的是提供一种高温软化抑制性优异的安全轮胎,以及一种能够制造出该轮胎的橡胶组合物。
14.解决问题的技术方案
15.《1》一种橡胶组合物,包含橡胶成分、填料、硫化剂和硫化促进剂,所述硫化促进剂含有次磺酰胺类硫化促进剂以及相对于100质量份的所述橡胶成分为1.0~2.0质量份的二硫化四苄基秋兰姆,其中,所述二硫化四苄基秋兰姆的含量(a)与所述次磺酰胺类硫化促进剂的含量(b)的质量比(a/b)为0.60~1.25。
16.《2》在根据《1》所述的橡胶组合物中,所述二硫化四苄基秋兰姆的含量(a)与所述硫化剂的含量(c)的质量比(a/c)为0.22~0.32。
17.《3》在根据《1》或《2》所述的橡胶组合物中,所述硫化促进剂的总含量小于所述硫化剂的总含量。
18.《4》在根据《1》至《3》中任一项所述的橡胶组合物中,所述硫化促进剂的总含量(d)与所述硫化剂的总含量(c)的质量比(d/c)为0.55~0.99。
19.《5》在根据《1》至《4》中任一项所述的橡胶组合物中,所述填料含有氮吸附比表面积为15~39m2/g的炭黑。
20.《6》在根据《1》至《5》中任一项所述的橡胶组合物中,所述填料含有dbp吸油量为120~180ml/100g的炭黑。
21.《7》在根据《1》至《6》中任一项所述的橡胶组合物中,相对于100质量份的所述橡胶成分,软化剂和热固性树脂的总含量为5质量份或更低。
22.《8》在根据《1》至《7》中任一项所述的橡胶组合物中,相对于100质量份的所述橡胶成分,软化剂和热固性树脂的总含量为1质量份或更低。
23.《9》一种安全轮胎,其中,根据《1》至《8》中任一项所述的橡胶组合物用于选自由胎侧加强橡胶层和胎圈填料所组成的组中的至少一种部件。
24.本发明的效果
25.根据本发明,能够提供一种高温软化抑制性优异的安全轮胎,以及一种能够制造出该轮胎的橡胶组合物。
附图说明
26.图1是示出了根据本发明的实施方式的安全轮胎的截面的示意图。
具体实施方式
27.在下文中,将基于本发明的实施方式对本发明进行详细说明和描述。
28.在以下描述中,表示数值范围的“a~b”的描述表示以a和b为端点的数值范围,并且表示“a以上且b以下”(a<b的情况)或“b以上且a以下”(b《a的情况)。
29.此外,质量份和质量%分别与重量份和重量%同义。
30.《橡胶成分》
31.本发明的橡胶组合物含有橡胶成分、填料、硫化剂和硫化促进剂,所述硫化促进剂含有次磺酰胺类硫化促进剂以及相对于100质量份的所述橡胶成分为1.0~2.0质量份的二硫化四苄基秋兰姆,其中,所述二硫化四苄基秋兰姆的含量(a)与所述次磺酰胺类硫化促进剂的含量(b)的质量比(a/b)为0.60~1.25。
32.由于本发明的橡胶组合物具有上述结构,因此由从该橡胶组合物获得的硫化橡胶制成的轮胎在高温软化抑制性方面优异。其原因尚不清楚,但推测这是由以下原因引起的。
33.在将橡胶组合物硫化而得到的硫化橡胶中,橡胶成分通过硫交联而形成三维网状结构,而根据网状结构中的结合状态,耐热性有时会降低。当轮胎内部的空气因轮胎爆胎而释放时,轮胎会弯曲并且其温度会升高。然而,安全轮胎会支撑车身并使其能够行驶。此外,考虑到乘坐舒适性、行驶性能等,即使轮胎在高温(例如,180℃)下容易发生软化时具有刚性,也希望该刚性在轮胎发热前后不发生变化。
34.专利文献1~3中所记载的轮胎虽然在180℃时的拉伸应力高,但是未证明硫化橡胶强度的温度依赖性,并且在轮胎发热前后无法维持轮胎的强度。在专利文献4中,仅验证了硫化橡胶在100℃下的储能模量e'。据认为,即使将专利文献4中所记载的硫化橡胶应用
于安全轮胎,也难以维持在诸如180℃等高温下的刚性。
35.然而,由于本发明的橡胶组合物含有二硫化四苄基秋兰姆以及在上述范围内的二硫化四苄基秋兰姆作为硫化促进剂,因此据认为能够形成单硫键和二硫键的比例高的网状结构。据认为,由此能够获得在高温下几乎不软化的硫化橡胶。进一步地,据说如果单硫键和二硫键的比例高,则硫化橡胶的机械性能降低。然而,与此相反,认为在由本发明的橡胶组合物得到的硫化橡胶的机械性能降低却少。因此,据认为,硫化橡胶的强度从发热前一直维持到至发热后达到高温。
36.作为结果,据认为,由本发明的橡胶组合物得到的轮胎的高温软化抑制性优异。
37.在下文中,描述橡胶组合物的详情。
38.[橡胶成分]
[0039]
本发明的橡胶组合物含有橡胶成分。
[0040]
橡胶成分的实例包括二烯系橡胶和非二烯系橡胶。
[0041]
二烯系橡胶可以是选自由天然橡胶(nr)和合成二烯橡胶所组成的组中的至少一种。
[0042]
具体而言,合成二烯橡胶的实例包括:聚异戊二烯橡胶(ir)、聚丁二烯橡胶(br)、苯乙烯-丁二烯共聚物橡胶(sbr)、丁二烯-异戊二烯共聚物橡胶(bir)、苯乙烯-异戊二烯共聚物橡胶(sir)和苯乙烯-丁二烯-异戊二烯共聚物橡胶(sbir)。
[0043]
作为二烯系橡胶,优选天然橡胶、聚异戊二烯橡胶、苯乙烯-丁二烯共聚橡胶、聚丁二烯橡胶、异丁烯异戊二烯橡胶,更优选天然橡胶和聚丁二烯橡胶。
[0044]
非二烯系橡胶的实例包括:乙丙橡胶(epdm(也称为epm))、马来酸改性乙丙橡胶(m-epm)、丁基橡胶(iir)、异丁烯与芳族乙烯基或二烯单体的共聚物、丙烯酸系橡胶(acm)和离聚物。
[0045]
作为橡胶成分,可以单独使用一种,也可以混合使用两种或更多种。
[0046]
橡胶成分可以是改性的或未改性的。在使用两种或更多种的橡胶成分的情况下,可以将未改性的橡胶成分和改性的橡胶成分混合使用。
[0047]
橡胶成分可以含有二烯系橡胶,也可以含有非二烯系橡胶,但是,从获得具有高温耐软化性和机械强度优异的网状结构的硫化橡胶的观点出发,优选至少含有二烯系橡胶,更优选由二烯系橡胶组成。
[0048]
此外,作为二烯系橡胶,可以仅使用天然橡胶和合成二烯系橡胶中的一种,也可以使用两者,但是,从提高诸如抗拉强度和断裂伸长率等断裂特性的观点来看,希望的是组合使用天然橡胶和合成二烯系橡胶。
[0049]
从抑制硫化橡胶的发热的观点出发,希望的是橡胶成分不含苯乙烯-丁二烯共聚橡胶(橡胶成分中的含量为0质量%)。
[0050]
因此,从提高轮胎的高温软化抑制性且提高低发热性的观点出发,橡胶成分优选由天然橡胶、聚异戊二烯橡胶、聚丁二烯橡胶、异丁烯异戊二烯橡胶组成,更优选由天然橡胶、聚异戊二烯橡胶和聚丁二烯橡胶组成,进一步优选由天然橡胶和聚丁二烯橡胶组成。如上所述,橡胶成分可以是改性的,或者可以是未改性的。例如,“由天然橡胶和聚丁二烯橡胶组成”包括使用未改性的天然橡胶和改性的聚丁二烯橡胶的方式、以及使用改性的天然橡胶和改性的聚丁二烯橡胶的方式。
[0051]
从进一步提高诸如拉伸强度、断裂伸长率等断裂特性的观点出发,橡胶成分中的天然橡胶的比例优选为10质量%或更高,更优选为20~80质量%。
[0052]
从提高硫化橡胶的低发热性的观点出发,作为橡胶成分,优选的是使用含改性基团的橡胶(有时称为改性橡胶),更优选的是使用含改性基团的合成橡胶。
[0053]
从提高胎侧加强橡胶层的加强性能的观点出发,橡胶组合物含有填料。为了提高与填料(尤其是炭黑)的相互作用,希望的是橡胶成分含有含改性基团的聚丁二烯橡胶(改性聚丁二烯橡胶)作为含改性基团的合成橡胶。
[0054]
如下所述,填料优选至少含有炭黑,并且改性的聚丁二烯橡胶优选为具有至少一种与炭黑相互作用的官能团的改性的聚丁二烯橡胶。与炭黑相互作用的官能团优选为对炭黑具有亲和性的官能团,特别优选为选自由含锡官能团、含硅官能团和含氮官能团所组成的组中的至少一种。
[0055]
在改性的聚丁二烯橡胶为具有选自由含锡官能团、含硅官能团和含氮官能团所组成的组中的至少一种官能团的改性的聚丁二烯橡胶的情况下,优选地,含锡官能团、含硅官能团或含氮官能团通过用诸如含锡化合物、含硅化合物或含氮化合物等进行改性而被引入改性的聚丁二烯橡胶中。
[0056]
在用改性剂对丁二烯橡胶的聚合活性部位进行改性时,所使用的改性剂优选为含氮化合物、含硅化合物或含锡化合物。在这种情况下,可以通过改性反应引入含氮官能团、含硅官能团或含锡官能团。
[0057]
这种用于改性的官能团可以存在于聚丁二烯的聚合起始末端、主链和聚合活性末端中的任何位置。
[0058]
可用作上述改性剂的含氮化合物优选具有取代或未取代的氨基、酰胺基、亚氨基、咪唑基、腈基或吡啶基。适用于上述改性剂的含氮化合物的实例包括:异氰酸酯化合物,例如,二苯基甲烷二异氰酸酯、粗mdi、三甲基六亚甲基二异氰酸酯和甲苯二异氰酸酯;和4-(二甲氨基)二苯甲酮、4-(二乙氨基)二苯甲酮、4-二甲氨基亚苄基苯胺、4-二甲氨基亚苄基丁胺、二甲基咪唑啉酮和n-甲基吡咯烷酮六亚甲基亚胺。
[0059]
此外,可用作上述改性剂的含硅化合物的实例包括:3-环氧丙氧基丙基三甲氧基硅烷、3-环氧丙氧基丙基三乙氧基硅烷、n-(1-甲基亚丙基)-3-(三乙氧基甲硅烷基)-1-丙胺、n-(1,3-二甲基亚丁基)-3-(三乙氧基甲硅烷基)-1-丙胺、n-(3-三乙氧基甲硅烷基丙基)-4,5-二氢咪唑、3-甲基丙烯酰氧基丙基三甲氧基硅烷、3-异氰酸基丙基三乙氧基硅烷、3-三乙氧基甲硅烷基丙基琥珀酸酐、3-(1-六亚甲基亚氨基)丙基(三乙氧基)硅烷、(1-六亚甲基亚氨基)甲基(三甲氧基)硅烷、3-二乙基氨基丙基(三乙氧基)硅烷、3-二甲基氨基丙基(三乙氧基)硅烷、2-(三甲氧基甲硅烷基乙基)吡啶、2-(三乙氧基甲硅烷基乙基)吡啶、2-氰乙基三乙氧基硅烷和四乙氧基硅烷。作为含硅化合物,可以单独使用一种,也可以混合使用两种或更多种。此外,也可使用含硅化合物的部分缩合物。
[0060]
进一步地,作为改性剂,还优选下式(i)表示的改性剂:
[0061]r1a
zxbꢀꢀꢀꢀ(i)[0062]
其中,r1各自独立地选自由具有1~20个碳原子的烷基、具有3~20个碳原子的环烷基、具有6~20个碳原子的芳基和具有7~20个碳原子的芳烷基所组成的组;z代表锡或硅;x各自独立地代表氯或溴;a为0~3,b为1~4,其中,a+b=4]。通过用式(i)的改性剂进行
改性所获得的改性聚丁二烯橡胶含有至少一种锡-碳键或硅-碳键。
[0063]
具体而言,式(i)中的r1的实例包括:甲基、乙基、正丁基、苯基叔丁基(neophyl)、环己基、正辛基和2-乙基己基。进一步地,具体而言,作为式(i)的改性剂,优选是sncl4、r1sncl3、r
12
sncl2、r
13
sncl、sicl4、r1sicl3、r
12
sicl2和r
13
sicl,特别优选是sncl4和sicl4。
[0064]
上述之中,从降低硫化橡胶的发热和延长耐久寿命的观点出发,改性的聚丁二烯橡胶优选为具有含氮官能团的改性聚丁二烯橡胶,更优选为胺改性的聚丁二烯橡胶。
[0065]
(胺改性的聚丁二烯橡胶的改性基团)
[0066]
在胺改性的聚丁二烯橡胶中,用于改性的胺类官能团优选为伯氨基或仲氨基。更优选地,引入被可消除基团保护的伯氨基或被可消除基团保护的仲氨基,进一步优选还引入除这样的氨基之外的含硅原子的官能团。
[0067]
被可消除基团保护的伯氨基(也称为被保护的伯氨基)的实例包括n,n-双(三甲基甲硅烷基)氨基,并且被可消除基团保护的仲氨基的实例包括n,n-(三甲基甲硅烷基)烷基氨基。含n,n-(三甲基甲硅烷基)烷基氨基的基团可以是非环残基或环残基。
[0068]
在胺改性的聚丁二烯橡胶中,更优选用被保护的伯氨基改性的伯胺改性的聚丁二烯橡胶。
[0069]
含硅原子的官能团的实例包括烃氧基甲硅烷基;和/或烃氧基和/或羟基与硅原子键合的硅烷醇基。
[0070]
这样的改性用官能团优选在丁二烯橡胶的聚合末端,更优选在其相同的聚合活性末端,具有被可消除基团保护的氨基、和一个或更多个(例如1个或2个)与烃氧基或羟基键合的硅原子。
[0071]
在通过与被保护的伯胺反应来改性丁二烯橡胶的活性末端时,优选地,丁二烯橡胶中聚合物链的至少10%具有活性或拟活性。具有这种活性的聚合反应的实例包括:通过使用有机碱金属化合物作为引发剂,使共轭二烯化合物单独或共轭二烯化合物与芳族乙烯基化合物在有机溶剂中进行阴离子聚合的反应;或在含有镧系稀土元素化合物的催化剂存在下,使共轭二烯化合物单独或共轭二烯化合物与芳族乙烯基化合物在有机溶剂中进行配位阴离子聚合的反应。前者比后者优选,因为能够获得在共轭二烯部分中具有高乙烯基键含量的聚合物。通过增加乙烯基键含量,能够提高硫化橡胶的耐热性。
[0072]
(聚合引发剂)
[0073]
可用作阴离子聚合引发剂的有机碱金属化合物优选为有机锂化合物。虽然没有特别限制,但是优选使用烃基锂和氨基化锂化合物作为有机锂化合物。在使用前者烃基锂的情况下,可获得在聚合起始末端具有烃基且另一末端为聚合活性部位的丁二烯橡胶。此外,在使用后者氨基化锂化合物的情况下,可获得在聚合起始末端具有含氮基团且另一末端为聚合活性部位的丁二烯橡胶。
[0074]
烃基锂优选为具有碳原子数为2~20的烃基的烃基锂,并且其实例包括:乙基锂、正丙基锂、异丙基锂、正丁基锂、仲丁基锂、叔辛基锂、正癸基锂、苯基锂、2-萘基锂、2-丁基苯基锂、4-苯基丁基锂、环己基锂、环戊基锂、二异丙基苯和丁基锂的反应产物。其中,特别优选的是正丁基锂。
[0075]
同时,氨基化锂化合物的实例包括:六亚甲基亚氨基锂、吡咯烷锂、哌啶锂、七亚甲基亚氨基锂、十二亚甲基亚氨基锂、二甲基氨基锂、二乙基氨基锂、二丁基氨基锂、二丙基氨
基锂、二庚基氨基锂、二己基氨基锂、二辛基氨基锂、二-2-乙基己基氨基锂、二癸基氨基锂、n-甲基哌嗪锂、乙基丙基氨基锂、乙基丁基氨基锂、乙基苄基氨基锂和甲基苯乙基氨基锂。其中,从与炭黑的相互作用效果及其聚合引发性能的观点出发,优选环状氨基化锂如六亚甲基亚氨基锂、吡咯烷锂、哌啶锂、七亚甲基亚氨基锂和十二亚甲基亚氨基锂,并且特别优选六亚甲基亚氨基锂和吡咯烷锂。
[0076]
对于这些氨基化锂化合物,通常可以使用预先由仲胺和锂化合物制备的那些化合物进行聚合,但这样的化合物也可以在聚合系统中(原位)制备。进一步地,聚合引发剂的用量优选在0.2~20mmol/100g单体的范围内选择。
[0077]
根据通过使用有机锂化合物作为聚合引发剂的阴离子聚合来制备丁二烯橡胶的方法没有特别限制,其可采用任何常规已知的方法。
[0078]
具体而言,在对反应非活性的有机溶剂中,例如,在诸如脂肪族、脂环族、芳族烃化合物等烃溶剂中,使用锂化合物作为聚合引发剂,在根据需要使用的无规化剂的存在下使共轭二烯化合物或共轭二烯化合物与芳族乙烯基化合物进行阴离子聚合,以得到具有预期活性末端的丁二烯橡胶。
[0079]
此外,与使用含有上述镧系稀土元素化合物的催化剂的情况相比,在使用有机锂化合物作为聚合引发剂的情况下,不仅可以有效地获得具有活性末端的丁二烯橡胶,还可以有效地获得具有活性末端的共轭二烯化合物与芳族乙烯基化合物的共聚物。
[0080]
烃溶剂优选为具有3~8个碳原子的烃溶剂,其实例包括:丙烷、正丁烷、异丁烷、正戊烷、异戊烷、正己烷、环己烷、丙烯、1-丁烯、异丁烯、反式-2-丁烯、顺-2-丁烯、1-戊烯、2-戊烯、1-己烯、2-己烯、苯、甲苯、二甲苯和乙苯。其中,可以单独使用一种,也可以混合使用两种或更多种。
[0081]
此外,溶剂中的单体浓度优选为5~50质量%,更优选为10~30质量%。在使用共轭二烯化合物和芳族乙烯基化合物进行共聚的情况下,投入的单体混合物中的芳族乙烯基化合物的含量优选落入55质量%或更低的范围内。
[0082]
(改性剂)
[0083]
在本发明中,在如上所述得到的具有活性末端的丁二烯橡胶中,可以通过使活性末端与作为改性剂的被保护的伯胺化合物反应来制备伯胺改性的聚丁二烯橡胶,并且可以使活性末端与被保护的仲胺化合物反应来制备仲胺改性的聚丁二烯橡胶。上述被保护的伯胺化合物优选为具有被保护的伯氨基的烷氧基硅烷化合物,并且上述被保护的仲胺化合物优选为具有被保护的仲氨基的烷氧基硅烷化合物。
[0084]
用作获得胺改性的聚丁二烯橡胶的改性剂的具有被保护的伯氨基的烷氧基硅烷化合物的实例包括:n,n-双(三甲基甲硅烷基)氨基丙基甲基二甲氧基硅烷、1-三甲基甲硅烷基-2,2-二甲氧基-1-氮杂-2-硅代环戊烷、n,n-双(三甲基甲硅烷基)氨基丙基三甲氧基硅烷、n,n-双(三甲基甲硅烷基)氨基丙基三乙氧基硅烷、n,n-双(三甲基甲硅烷基)氨基丙基甲基二乙氧基硅烷、n,n-双(三甲基甲硅烷基)氨基乙基三甲氧基硅烷、n,n-双(三甲基甲硅烷基)氨基乙基三乙氧基硅烷、n,n-双(三甲基甲硅烷基)氨基乙基甲基二甲氧基硅烷和n,n-双(三甲基甲硅烷基)氨基乙基甲基二乙氧基硅烷。优选的是n,n-双(三甲基甲硅烷基)氨基丙基甲基二甲氧基硅烷、n,n-双(三甲基甲硅烷基)氨基丙基甲基二乙氧基硅烷或1-三甲基甲硅烷基-2,2-二甲氧基-1-氮杂-2-硅代环戊烷。
[0085]
此外,用于获得胺改性的聚丁二烯橡胶的改性剂的实例还包括:具有被保护的仲氨基的烷氧基硅烷化合物,例如,n-甲基-n-三甲基甲硅烷基氨基丙基(甲基)二甲氧基硅烷、n-甲基-n-三甲基甲硅烷基氨基丙基(甲基)二乙氧基硅烷、n-三甲基甲硅烷基(六亚甲基亚胺-2-基)丙基(甲基)二甲氧基硅烷、n-三甲基甲硅烷基(六亚甲基亚胺-2-基)丙基(甲基)二乙氧基硅烷、n-三甲基甲硅烷基(吡咯烷-2-基)丙基(甲基)二甲氧基硅烷、n-三甲基甲硅烷基(吡咯烷-2-基)丙基(甲基)二乙氧基硅烷、n-三甲基甲硅烷基(哌啶-2-基)丙基(甲基)二甲氧基硅烷、n-三甲基甲硅烷基(哌啶-2-基)丙基(甲基)二乙氧基硅烷、n-三甲基甲硅烷基(咪唑-2-基)丙基(甲基)二甲氧基硅烷、n-三甲基甲硅烷基(咪唑-2-基)丙基(甲基)二乙氧基硅烷、n-三甲基甲硅烷基(4,5-二氢咪唑-5-基)丙基(甲基)二甲氧基硅烷和n-三甲基甲硅烷基(4,5-二氢咪唑-5-基)丙基(甲基)二乙氧基硅烷;具有亚氨基的烷氧基硅烷化合物,例如,n-(1,3-二甲基亚丁基)-3-(三乙氧基甲硅烷基)-1-丙胺、n-(1-甲基亚乙基)-3-(三乙氧基甲硅烷基)-1-丙胺、n-亚乙基-3-(三乙氧基甲硅烷基)-1-丙胺、n-(1-甲基亚丙基)-3-(三乙氧基甲硅烷基)-1-丙胺、n-(4-n,n-二甲基氨基亚苄基)-3-(三乙氧基甲硅烷基)-1-丙胺和n-(亚环己基)-3-(三乙氧基甲硅烷基)-1-丙胺;和具有氨基的烷氧基硅烷化合物,例如,3-二甲基氨基丙基(三乙氧基)硅烷、3-二甲基氨基丙基(三甲氧基)硅烷、3-二乙基氨基丙基(三乙氧基)硅烷、3-二乙基氨基丙基(三甲氧基)硅烷、2-二甲基氨基乙基(三乙氧基)硅烷、2-二甲氨基乙基(三甲氧基)硅烷、3-二甲基氨基丙基(二乙氧基)甲基硅烷和3-二丁基氨基丙基(三乙氧基)硅烷。
[0086]
作为这些改性剂,可以单独使用一种,也可以混合使用两种或更多种。进一步地,改性剂可以是部分缩合物。
[0087]
这里,部分缩合物是指sior(r为烷基等)的一部分(但不是全部)以siosi键的形式缩合而成的改性剂。
[0088]
在与改性剂的改性反应中,改性剂的用量优选为0.5~200mmol/kg丁二烯橡胶。该用量更优选为1~100mmol/kg丁二烯橡胶,特别优选为2~50mmol/kg丁二烯橡胶。这里,丁二烯橡胶是指不含诸如在制造时或制造后添加的防老剂等添加剂的丁二烯橡胶块。当改性剂的用量在上述范围内时,填料(尤其是炭黑)的分散性优异,并且硫化橡胶的耐断裂性和低发热性得以改善。
[0089]
改性剂的添加方法没有特别限制,并且其实例包括集中添加的方法、分批添加的方法或连续添加的方法,但优选集中添加的方法。
[0090]
此外,改性剂不仅可以与聚合起始末端或聚合终止末端结合,还可以与聚合物主链或侧链中的任何一方结合,但从抑制聚合物末端的能量损失以提高低发热性的观点出发,优选引入到聚合起始末端或聚合终止末端。
[0091]
(缩合促进剂)
[0092]
在本发明中,优选使用缩合促进剂来促进缩合反应,在该缩合反应中,涉及使用含有被保护的伯氨基的烷氧基硅烷化合物作为改性剂。
[0093]
作为这样的缩合促进剂,可以使用含有叔氨基的化合物,或含有属于周期表(长周期表)的第3族、第4族、第5族、第12族、第13族、第14族和第15族中任一族的一种或更多种元素的有机化合物。此外,作为这样的缩合促进剂,优选的是含有选自由钛(ti)、锆(zr)、铋(bi)、铝(al)和锡(sn)所组成的组中的至少一种或更多种的金属的烷氧化物、羧酸盐或乙
酰丙酮络合物盐。
[0094]
本文使用的缩合促进剂可以在改性反应之前添加,但优选在改性反应中和/或改性反应结束后添加到改性反应体系中。在改性反应之前添加的情况下,可能发生与活性末端的直接反应,使得在某些情况下具有被保护的伯氨基的烃氧基不会被引入所述活性末端。
[0095]
缩合促进剂的加入时间一般是在改性反应开始后5分钟至5小时,优选在改性反应开始后15分钟至1小时。
[0096]
具体而言,缩合促进剂的实例包括含钛化合物,例如,四甲氧基钛、四乙氧基钛、四正丙氧基钛、四异丙氧基钛、四正丁氧基钛、四正丁氧基钛低聚物、四仲丁氧基钛、四叔丁氧基钛、四(2-乙基己基)钛、双(辛二油酸)双(2-乙基己基)钛、四(辛二油酸)钛、乳酸钛、二丙氧基双(三乙醇胺)钛、二丁氧基双(三乙醇胺)钛、三丁氧基硬脂酸钛、三丙氧基硬脂酸钛、乙基己基二油酸钛、三丙氧基乙酰丙酮钛、二丙氧基双(乙酰丙酮)钛、三丙氧基乙基乙酰乙酸钛、丙氧基乙酰丙酮双(乙基乙酰乙酸)钛、三丁氧基乙酰丙酮钛、二丁氧基双(乙酰丙酮)钛、三丁氧基乙基乙酰乙酸钛、丁氧基乙酰丙酮双(乙基乙酰乙酸)钛、四(乙酰丙酮)钛、二乙酰丙酮双(乙基乙酰乙酸)钛、双(2-乙基己酸)氧化钛、双(月桂酸)氧化钛、双(环烷酸)氧化钛、双(硬脂酸)氧化钛、双(油酸)氧化钛、双(亚油酸)氧化钛、四(2-乙基己酸)钛、四(月桂酸)钛、四(环烷酸)钛、四(硬脂酸)钛、四(油酸)钛、四(亚油酸)钛和四(2-乙基-1,3-己二油酸)钛。
[0097]
此外,其实例包括含铋或锆的化合物,例如,三(2-乙基己酸)铋、三(月桂酸)铋、三(环烷酸)铋、三(硬脂酸)铋、三(油酸)铋、三(亚油酸)铋、四乙氧基锆、四正丙氧基锆、四异丙氧基锆、四正丁氧基锆、四仲丁氧基锆、四叔丁氧基锆、四(2-乙基己基)锆、三丁氧基硬脂酸锆、三丁氧基乙酰丙酮锆、二丁氧基双(乙酰丙酮)锆、三丁氧基乙基乙酰乙酸锆、丁氧基乙酰丙酮双(乙基乙酰乙酸)锆、四(乙酰丙酮)锆、二乙酰丙酮双(乙基乙酰乙酸)锆、双(2-乙基己酸)氧化锆、双(月桂酸)氧化锆、双(环烷酸)氧化锆、双(硬脂酸)氧化锆、双(油酸)氧化锆、双(亚油酸)氧化锆、四(2-乙基己酸)锆、四(月桂酸)锆、四(环烷酸)锆、四(硬脂酸)锆、四(油酸)锆和四(亚油酸)锆。
[0098]
此外,其实例包括含铝化合物,例如,三乙氧基铝、三正丙氧基铝、三异丙氧基铝、三正丁氧基铝、三仲丁氧基铝、三叔丁氧基铝、三(2-1乙基己基)铝、二丁氧基硬脂酸铝、二丁氧基乙酰丙酮铝、丁氧基双(乙酰丙酮)铝、二丁氧基乙基乙酰乙酸铝、三(乙酰丙酮)铝、三(乙基乙酰乙酸)铝、三(2-乙基己酸)铝、三(月桂酸)铝、三(环烷酸)铝、三(硬脂酸)铝、三(油酸)铝和三(亚油酸)铝。
[0099]
在上述缩合促进剂中,优选钛化合物,并且特别优选钛金属醇盐、钛金属羧酸盐或钛金属乙酰丙酮络合物盐。
[0100]
关于缩合促进剂的用量,该化合物的摩尔数相对于反应体系内存在的烃氧基的总量的摩尔比优选为0.1~10,特别优选为0.5~5。当缩合促进剂的量设定在上述范围内时,缩合反应有效地进行。
[0101]
缩合反应时间一般为5分钟至10小时,优选为约15分钟至5小时。当缩合反应时间设定在上述范围内时,缩合反应可以顺利完成。
[0102]
此外,缩合反应时的反应体系中的压力通常为0.01~20mpa,优选为0.05~10mpa。
[0103]
从提高硫化橡胶的低发热性和耐高温软化性的观点出发,橡胶成分中的改性橡胶的含量优选为10~90质量%,更优选为20~80质量%。
[0104]
[填料]
[0105]
从提高硫化橡胶的刚性以及获得高温耐软化性的观点出发,本发明的橡胶组合物含有填料。
[0106]
填料的实例包括:金属氧化物,例如,氧化铝、二氧化钛和二氧化硅;以及加强填料,例如,粘土、碳酸钙和炭黑,并且优选使用二氧化硅和炭黑。从即使轮胎内部的空气被释放,胎侧加强橡胶层、胎圈填料等弯曲并且构成这些部件的硫化橡胶发热的情况下,也能抑制硫化橡胶的发热的观点出发,希望的是使用具有低发热性的填料。
[0107]
(炭黑)
[0108]
当橡胶组合物含有炭黑时,能够提高硫化橡胶的强度。
[0109]
此外,从提高硫化橡胶的低发热性的观点出发,炭黑优选具有15~39m2/g的氮吸附比表面积(n2sa)。在本说明书中,氮吸附比表面积为39m2/g或更低的炭黑被称为大粒径的炭黑。
[0110]
当氮吸附比表面积为39m2/g或更低时,能够通过抑制由炭黑引起的发热来抑制硫化橡胶的发热。当氮吸附比表面积为15m2/g或更高时,能够提高硫化橡胶的加强性能。从提高硫化橡胶的低发热性和加强性以及提高轮胎的高温软化抑制性的观点出发,炭黑的氮吸附比表面积更优选为18~37m2/g,进一步优选为21~35m2/g。
[0111]
此外,炭黑的dbp吸油量(邻苯二甲酸二丁酯吸油量)优选为120~180ml/100g。
[0112]
dbp吸油量被用作表示炭黑的聚集体结构的发育程度(有时被称为“结构”)的指标,并且有dbp吸油量越大则聚集体越大的趋势。在本说明书中,dbp吸油量为120ml/100g或更高的炭黑被称为高结构炭黑。
[0113]
当dbp吸油量为120ml/100g或更高时,能够提高硫化橡胶的拉伸强度和抗压强度,并且能够提高轮胎的高温软化抑制性。当dbp吸油量为180ml/100g或更低时,能够抑制发热并且提高高温软化抑制性。
[0114]
炭黑的dbp吸油量更优选为122~170ml/100g,进一步优选为125~165ml/100g。
[0115]
希望的是,本发明的橡胶组合物含有大粒径且高结构的炭黑。一般来说,炭黑的结构会随着粒径的增加而降低。然而,通过使用即使是大粒径也具有高结构的炭黑,从而能够进一步抑制发热性,并且进一步提高抗拉强度和抗压强度。因此,能够进一步提高安全轮胎的高温耐软化性。
[0116]
具体而言,希望的是本发明的橡胶组合物含有氮吸附比表面积为15~39m2/g、dbp吸油量为120~180ml/100g的炭黑。
[0117]
炭黑优选具有50%或更高的甲苯着色透光率。
[0118]
当甲苯着色透光率为50%或更高时,存在于炭黑表面的焦油含量,特别是芳族成分得到抑制,能够充分加强橡胶成分。然后,能够提高硫化橡胶的耐磨性等。炭黑的甲苯着色透光率更优选为60%或更高,进一步优选为75%或更高。炭黑的甲苯着色透光率可以为100%,但一般低于100%。
[0119]
甲苯着色透光率通过jis k 6218:1997第8b部分中所描述的方法进行测量,并以相对于纯甲苯的百分比来表示。
[0120]
从进一步提高硫化橡胶的高温耐软化性,并由此进一步提高安全耐久性的观点出发,相对于100质量份的橡胶成分,橡胶组合物中的炭黑的含量优选为30~100质量份,更优选为35~80质量份,进一步优选为40~70质量份。
[0121]
(二氧化硅)
[0122]
二氧化硅没有特别限定,并且其实例包括:湿式二氧化硅(含水硅酸)、干式二氧化硅(无水硅酸)和胶体二氧化硅。二氧化硅可以是市售品,例如,东曹
·
二氧化硅公司的nipsil aq(商品名)、罗地亚公司(rhodia)的zeosil 1115mp(商品名)和赢创德固赛公司(evonik degussa)的vn-3(商品名)。
[0123]
此外,当使用二氧化硅作为填料时,橡胶组合物可以还含有硅烷偶联剂以加强二氧化硅与橡胶成分之间的结合并提高加强性,从而提高橡胶组合物中二氧化硅的分散性。
[0124]
作为填料,可以单独使用一种,也可以混合使用两种或更多种。进一步地,填料可以含有炭黑和二氧化硅中的任一种,也可以含有这两者,但优选至少含有炭黑,更优选单独使用一种炭黑或混合使用两种或更多种炭黑。
[0125]
从进一步提高硫化橡胶的高温耐软化性,并由此进一步提高安全耐久性的观点出发,相对于100质量份的橡胶成分,本发明的橡胶组合物中的填料的含量(总量)优选为30~100质量份,优选为30~100质量份,更优选为35~80质量份,进一步优选为40~70质量份。
[0126]
[硫化剂]
[0127]
本发明的橡胶组合物含有硫化剂。
[0128]
硫化剂没有特别限制,并且通常使用硫。其实例包括:粉末硫、沉淀硫、胶体硫、表面处理硫和不溶性硫。
[0129]
相对于100质量份的橡胶成分,橡胶组合物中硫化剂的含量优选为2~12质量份。当含量为2质量份或更高时,能够充分地进行硫化;当含量为12质量份或更低时,能够抑制硫化橡胶的防老性。
[0130]
相对于100质量份的橡胶成分,橡胶组合物中硫化剂的含量更优选为3~10质量份,进一步优选为4~8质量份。
[0131]
[硫化促进剂]
[0132]
该橡胶组合物含有次磺酰胺类硫化促进剂和二硫化四苄基秋兰姆作为硫化促进剂。这里,相对于100质量份的橡胶成分,橡胶组合物中的二硫化四苄基秋兰姆的含量为1.0~2.0质量份,并且二硫化四苄基秋兰姆的含量(a)与次磺酰胺类硫化促进剂的含量(b)的质量比(a/b)为0.60~1.25。
[0133]
当本发明的橡胶组合物含有上述量的次磺酰胺类硫化促进剂和二硫化四苄基秋兰姆作为硫化促进剂时,据认为由本发明的橡胶组合物获得的安全轮胎的高温软化抑制性优异,因此安全耐久性优异。据认为,这是因为通过在所述组合物中使用硫化促进剂,在硫化橡胶中形成单硫键和二硫键的比例高的网状结构。从而,硫化橡胶在高温下的耐软化性变得优异,并且即使硫化橡胶在高温下被压缩或拉伸也能维持刚性。
[0134]
当以100质量份的橡胶成分为基准,橡胶组合物中的二硫化四苄基秋兰姆的含量(a)小于1.0质量份时,无法获得足够的高温软化抑制性;并且当含量(a)大于2.0质量份时,容易发生橡胶燃烧,并且硫化橡胶的机械强度降低。
[0135]
从进一步提高轮胎的高温软化抑制性的观点出发,含量(a)优选为1.2~1.8质量
份,更优选为1.3~1.7质量份。
[0136]
此外,当二硫化四苄基秋兰姆的含量(a)与次磺酰胺类硫化促进剂的含量(b)的质量比(a/b)小于0.60时,无法获得硫化橡胶在高温下的耐软化性,因此无法获得安全耐久性。进一步地,当质量比(a/b)大于1.25时,断裂特性降低。
[0137]
从进一步提高轮胎的高温软化抑制性的观点出发,质量比(a/b)优选为0.62~1.22,更优选为0.64~1.20。
[0138]
此外,所述二硫化四苄基秋兰姆的含量(a)与所述硫化剂的含量(c)的质量比(a/c)优选为0.22~0.32。
[0139]
当质量比(a/c)落入上述范围内时,硫化橡胶的高温耐软化性优异,且安全耐久性优异。
[0140]
质量比(a/c)更优选为0.25~0.32,进一步优选为0.27~0.32。
[0141]
此外,在本发明的橡胶组合物中,希望的是硫化促进剂的总含量小于硫化剂的总含量。更具体而言,希望的是硫化促进剂的总含量(d)与硫化剂的总含量(c)的质量比(d/c)为0.55~0.99。
[0142]
一般来说,为了提高硫化橡胶的网状结构中的单硫键和二硫键的比例,会使硫化促进剂的总含量高于硫化剂的总含量。但相反,在本发明中,希望的是硫化促进剂的总含量小于硫化剂的总含量。此外,在某些情况下,据认为,由于使用秋兰姆类硫化促进剂而使单硫键和二硫键的比例大的硫化橡胶具有优异的耐热性,但机械强度降低。然而,在本发明中,能够同时实现高温耐软化性和机械强度。其原因尚不清楚,但据认为在本发明中,由于以上述特定量含有次磺酰胺类硫化促进剂和二硫化四苄基秋兰姆作为硫化促进剂,因此能够兼顾高温耐软化性和机械强度。
[0143]
从进一步提高轮胎的高温软化抑制性的观点出发,质量比(d/c)更优选为0.55~0.95,进一步更优选为0.55~0.90,甚至更优选为0.55~0.85。
[0144]
(次磺酰胺类硫化促进剂)
[0145]
次磺酰胺类硫化促进剂的实例包括:n-环己基-2-苯并噻唑基次磺酰胺、n,n-二环己基-2-苯并噻唑基次磺酰胺、n-叔丁基-2-苯并噻唑基次磺酰胺、n-氧二乙烯-2-苯并噻唑基次磺酰胺、n-甲基-2-苯并噻唑基次磺酰胺、n-乙基-2-苯并噻唑基次磺酰胺、n-丙基-2-苯并噻唑基次磺酰胺、n-丁基-2-苯并噻唑基次磺酰胺、n-戊基-2-苯并噻唑基次磺酰胺、n-己基-2-苯并噻唑基次磺酰胺、n-庚基-2-苯并噻唑基次磺酰胺、n-辛基-2-苯并噻唑基次磺酰胺、n-2-乙基己基-2-苯并噻唑基次磺酰胺、n-癸基-2-苯并噻唑基次磺酰胺、n-十二烷基-2-苯并噻唑基次磺酰胺、n-硬脂基-2-苯并噻唑基次磺酰胺、n,n-二甲基-2-苯并噻唑基次磺酰胺、n,n-二乙基-2-苯并噻唑基次磺酰胺、n,n-二丙基-2-苯并噻唑基次磺酰胺、n,n-二丁基-2-苯并噻唑基次磺酰胺、n,n-二戊基-2-苯并噻唑基次磺酰胺、n,n-二己基-2-苯并噻唑基次磺酰胺、n,n-二庚基-2-苯并噻唑基次磺酰胺、n,n-二辛基-2-苯并噻唑基次磺酰胺、n,n-二-2-乙基己基苯并噻唑基次磺酰胺、n,n-二癸基-2-苯并噻唑基次磺酰胺、n,n-二十二烷基-2-苯并噻唑基次磺酰胺和n,n-二硬脂基-2-苯并噻唑基次磺酰胺。
[0146]
作为次磺酰胺类硫化促进剂,可以单独使用一种,也可以混合使用两种或更多种。
[0147]
从同时获得硫化橡胶的高温耐软化性和机械强度,并进一步提高安全耐久性的观点出发,作为次磺酰胺类硫化促进剂,上述之中优选的是n-环己基-2-苯并噻唑基次磺酰胺
和n-叔丁基-2-苯并噻唑基次磺酰胺,更优选n-叔丁基-2-苯并噻唑基次磺酰胺。
[0148]
次磺酰胺类硫化促进剂可以在上述质量比(a/b)为0.60~1.25的范围内自由使用,相对于100质量份的橡胶成分,橡胶组合物中的次磺酰胺类硫化促进剂的含量优选为0.80~3.33质量份。从进一步提高高温软化抑制性的观点出发,相对于100质量份的橡胶成分,次磺酰胺类硫化促进剂的含量更优选为1.00~3.00质量份,进一步优选为1.10~2.80质量份。
[0149]
本发明的橡胶组合物不仅还可以含有除二硫化四苄基秋兰姆以外的秋兰姆类硫化促进剂,而且还可以含有诸如胍类、醛胺类、醛氨类、噻唑类、硫脲类、二硫代氨基甲酸盐类和黄原酸盐类硫化促进剂等硫化促进剂。
[0150]
然而,在硫化促进剂的总含量小于硫化剂的总含量的成分组合物中,从提高单硫键和二硫键的比例以及提高硫化橡胶的高温耐软化性且同时提高机械强度的观点出发,希望的是硫化促进剂由二硫化四苄基秋兰姆和次磺酰胺类硫化促进剂组成。
[0151]
(硫化延迟剂)
[0152]
本发明的橡胶组合物可以含有硫化延迟剂。当橡胶组合物含有硫化延迟剂时,能够抑制在制备橡胶组合物时由橡胶组合物过热引起的橡胶燃烧。进一步地,能够提高橡胶组合物的焦烧稳定性,并且能够容易地将橡胶组合物从捏合机中挤出。
[0153]
本发明的橡胶组合物的门尼粘度(ml
1+4
,130℃)优选为40~100,更优选为50~90,进一步优选为60~85。当门尼粘度落入上述范围内时,能够充分获得硫化橡胶的物理性能(包括抗断裂性能),而不会损害制造加工性。
[0154]
硫化延迟剂的实例包括:邻苯二甲酸酐、苯甲酸、水杨酸、n-亚硝基二苯胺、n-(环己硫基)-邻苯二甲酰亚胺(ctp)、磺酰胺衍生物、二苯脲和双(十三烷基)季戊四醇二亚磷酸酯。作为硫化延迟剂,可以使用市售品,并且例如可以举出由孟山都公司制造的“santoguard pvi”[n-(环己硫基)-邻苯二甲酰亚胺](产品名)。
[0155]
以上之中,作为硫化延迟剂,优选使用n-(环己硫基)-邻苯二甲酰亚胺(ctp)。
[0156]
从在不干扰硫化反应的情况下抑制橡胶组合物的橡胶燃烧和提高焦烧稳定性的观点出发,当使用硫化延迟剂时,相对于100质量份的橡胶成分,橡胶组合物中硫化延迟剂的含量优选为0.1~1.0质量份。
[0157]
[软化剂、热固性树脂]
[0158]
希望的是本发明的橡胶组合物实质上不含软化剂和热固性树脂。具体而言,相对于100质量份的橡胶成分,软化剂和热固性树脂各自的含量优选为5质量份或更低;相对于100质量份的橡胶成分,软化剂和热固性树脂的总含量更优选为5质量份或更低;总含量进一步优选为1质量份或更低;特别优选不含软化剂和热固性树脂(相对于100质量份的橡胶成分,软化剂和热固性树脂的总含量为0质量份)。
[0159]
(软化剂)
[0160]
由于橡胶组合物实质上不含软化剂,因此能够提高硫化橡胶在高温下的弹性模量相对于室温下的弹性模量之比。因此,当硫化橡胶应用于轮胎的胎侧加强橡胶时,能够抑制轮胎侧壁的挠曲。因此,从提高安全行驶时的耐久性的观点出发,希望的是不含软化剂。
[0161]
软化剂的实例包括加工油和热塑性树脂。
[0162]
加工油的实例包括:源自矿物的矿物油、源自石油的芳香油、石蜡油、环烷油和源
自天然产物的棕榈油。
[0163]
热塑性树脂的实例包括在高温下软化或以液态存在,然后软化硫化橡胶的树脂。具体实例包括:增粘剂(不含固化剂),例如,各种石油类树脂如c5-(包括环戊二烯树脂和二环戊二烯树脂)c9-和c5/c9混合类树脂、萜烯类树脂、萜烯-芳族化合物类树脂、松香类树脂、酚醛树脂和烷基酚醛树脂。
[0164]
(热固性树脂)
[0165]
由于橡胶组合物实质上不含热固性树脂,因此硫化橡胶变得柔软,并且使用本发明的橡胶组合物的安全轮胎的静态垂直弹簧常数变小。因此,提高了安全轮胎的乘坐舒适性。
[0166]
热固性树脂的实例包括诸如酚醛树脂、三聚氰胺树脂、尿素树脂和环氧树脂等树脂。作为酚醛树脂的固化剂,可以举出六亚甲基四胺。
[0167]
除了这些成分之外,本发明的橡胶组合物还可以含有在通常的橡胶组合物中混合和使用的配合剂。其实例包括:通常共混的各种配合剂,例如,硫化促进剂氧化锌(氧化锌)、硬脂酸、防老剂、相容剂、加工性改进剂、润滑剂、增粘剂、分散剂和均化剂。
[0168]
作为防老剂,可以使用任何已知的防老剂,没有特别限制,并且实例包括酚类防老剂、咪唑类防老剂和胺类防老剂。相对于100质量份的橡胶成分,防老剂的共混量通常为0.5~10质量份,优选为1~5质量份。
[0169]
[橡胶组合物的制造方法]
[0170]
如上所述,本发明的橡胶组合物是通过捏合上述成分而获得的。捏合方法可以遵循本领域技术人员通常进行的方法。在捏合时,可以使用辊、密炼机、班伯里转子等捏合机。进一步地,在成型为片状、带状等时,可以使用挤出成型机、压力机等常规已知的成型机。
[0171]
例如,在100~200℃将硫、硫化促进剂(以及必要时添加的硫化延迟剂)、氧化锌以外的全部成分捏合后,添加硫、硫化促进剂和氧化锌(必要时,可添加硫化延迟剂),然后通过使用捏合辊机等在60~130℃下进行捏合。
[0172]
《安全轮胎》
[0173]
本发明的安全轮胎是通过将本发明的橡胶组合物用于选自由胎侧加强橡胶层和胎圈填料所组成的组中的至少一种部件而获得的。
[0174]
在下文中,通过使用图1来描述具有胎侧加强橡胶层的安全轮胎的结构的实例。
[0175]
图1是示出本发明的实施方式的安全轮胎的截面的示意图,并且示出胎圈填料7、胎侧加强橡胶层8等各部件的布置。安全轮胎可被简称为轮胎。
[0176]
在图1中,根据本发明的优选实施方式的轮胎是如下的轮胎,该轮胎包括:胎体层2,其由在一对胎圈芯1和1'(1'未示出)之间呈环形延伸的至少一个子午线胎体帘布层形成,其中胎体帘布层的两端可以从轮胎内侧向外侧缠绕在胎圈芯1上;胎侧橡胶层3,其布置在胎体层2的胎侧区域的轮胎轴向外侧以形成外侧部分;胎面橡胶层4,其布置在胎体层2的胎冠区域的轮胎径向外侧以形成胎面部;带束层5,其布置在胎面橡胶层4和胎体层2的胎冠区域之间以形成加强带束;气密层6,其布置在轮胎内部的胎体层2的整个表面上以形成气密膜;胎圈填料7,其布置在从一个对应的胎圈芯1延伸到另一个胎圈芯1'的胎体层2的主体部与缠绕在胎圈芯1上的卷绕部之间;以及至少一个胎侧加强橡胶层8,其在胎体层2和气密层6之间从胎体层的胎侧区域中的胎圈填料7的侧部到胎肩区域10,其中沿轮胎旋转轴线截
取的横截面大致呈新月形。
[0177]
当将本发明的橡胶组合物用于选自胎侧加强橡胶层8和胎圈填料7的至少一种部件时,本发明的安全轮胎的高温软化抑制性优异,因此安全耐久性优异。本发明的橡胶组合物的硫化橡胶也可以用于胎圈填料7和胎侧加强橡胶层8之外的部分,例如,胎面像胶层4等。
[0178]
本发明的轮胎的胎体层2由至少一层胎体帘布层形成,但也可以具有两层或更多层的胎体帘布层。进一步地,胎体帘布层的加强帘线可以以相对于轮胎周向大致呈90
°
的角度布置,并且待驱动的加强帘线的数量可以是35~65根/50mm。进一步地,由第一带束层5a和第二带束层5b的两层构成的带束层5布置在胎体层2的胎冠区域的轮胎径向外侧,但带束层5的数量不受于此。作为第一带束层5a和第二带束层5b,可以使用多根钢丝帘线在轮胎宽度方向上平行排列而不加捻并埋入橡胶中的带束层。例如,第一带束层5a和第二带束层5b可以布置成在层之间相互交叉,以形成交叉带束。
[0179]
进一步地,在本发明的轮胎中,也可以在带束层5的轮胎径向外侧布置带束加强层(未图示)。作为带束加强层的加强帘线,出于确保轮胎周向的拉伸刚性的目的,优选使用由具有高弹性的有机纤维构成的帘线。有机纤维帘线可以是诸如芳族聚酰胺(芳酰胺)、聚萘二甲酸乙二醇酯(pen)、聚对苯二甲酸乙二醇酯、人造丝、zylon(注册商标)(聚对苯并二噁唑(pbo)纤维)、脂肪族聚酰胺(尼龙)等有机纤维帘线。
[0180]
进一步地,在本发明的轮胎中,虽然未图示,但除了胎侧加强层以外,还可以布置任何其他加强构件如嵌件或钢圈包布。这里,嵌件是从胎圈部到胎侧部沿轮胎周向布置的加强材料(未图示),其中,布置有多根高弹性有机纤维帘线并在其上涂覆有橡胶。钢圈包布是设置在在胎圈芯1或1'之间延伸的胎体帘布层的主体部分与围绕胎圈芯1或1'折叠的折叠部分之间的加强材料,其包括胎圈芯1或1’和布置在其轮胎径向外侧的胎圈填料7的至少一部分。在钢圈包布中,布置有多根高弹性有机纤维帘线并在其上涂覆有橡胶。嵌件和钢圈包布的角度优选相对于圆周方向为30~60
°
。
[0181]
在一对胎圈部中分别埋入有胎圈芯1和1’,并且胎体层2被锁定成围绕胎圈芯1和1'从轮胎内侧向外侧折叠,但是胎体层2的锁定方法也不限于此。例如,构成胎体层2的胎体帘布层中的至少一层胎体帘布层可以围绕胎圈芯1和1'在轮胎宽度方向上从内侧向外折叠,并且折叠端可以位于带束层5和胎体层2的胎冠区域之间,从而形成所谓的包络结构。进一步地,胎面花纹可以适当地形成在胎面像胶层4的表面上,并且气密层6可以形成在最内层上。在本发明的轮胎中,作为填充到轮胎内的气体,可以是普通空气或改变了氧分压的空气、或者非活性气体如氮气。
[0182]
(安全轮胎的制造方法)
[0183]
通过在胎圈填料7和胎侧加强橡胶层8中的任一个或两个中使用本发明的橡胶组合物的硫化橡胶,并由常规的安全轮胎的制造方法来制造本发明的安全轮胎。
[0184]
也就是说,将含有各种化学品的橡胶组合物在未硫化的阶段加工成各部件,通过常规方法在轮胎成型机上进行糊状成型,然后成型为生胎。该生胎在硫化机内进行加热和加压,以获得安全轮胎。
[0185]
[实施例]
[0186]
《实施例1~5,比较例1~7》
[0187]
[橡胶组合物的制造]
[0188]
实施例1和3~5以及比较例1~7的橡胶组合物是通过根据以下表1和表2中记载的配混组成捏合各成分来制备的。此外,实施例2的橡胶组合物是通过根据表1中记载的配混组成捏合各成分来制备的。
[0189]
表1中记载的比较例4和表2中记载的比较例6具有相同的橡胶组合物含量,但用于下述断裂特性(eb
×
tb)评价的硫化橡胶与用于安全耐久性评价的轮胎尺寸不同。因此,对其应用不同的编号。
[0190]
用于制备实施例1和3~5和比较例1~7的橡胶组合物的改性聚丁二烯橡胶和用于制备实施例2的橡胶组合物的改性聚丁二烯橡胶通过以下方法制备。
[0191]
[伯胺改性的聚丁二烯橡胶p的制造]
[0192]
(1)未改性的聚丁二烯的制造
[0193]
在氮气下,将1.4kg的环己烷、250g的1,3-丁二烯和2,2-二四氢呋喃基丙烷(0.285mmol)的环己烷溶液注入氮气吹扫过的5-l高压釜中,并将2.85mmol的正丁基锂(buli)加入其中并在设置为50℃且配备有搅拌器的热水浴中聚合4.5小时。1,3-丁二烯的反应转化率几乎为100%。取出一部分聚合物溶液并将其放入含有1.3g的2,6-二叔丁基-对甲苯酚的甲醇溶液中,以停止聚合。然后通过汽提除去溶剂,并将残余物在110℃下用辊干燥,以得到未改性的聚丁二烯。对所得的未改性聚丁二烯测定微观结构(乙烯基键含量),结果乙烯基键含量为30质量%。
[0194]
(2)伯胺改性的聚丁二烯橡胶p的制造
[0195]
在聚合催化剂不失活的情况下将上述(1)中得到的聚合物溶液保持在50℃的温度下,并且将1129mg(3.364mmol)的伯氨基被保护的n,n-双(三甲基甲硅烷基)氨基丙基甲基二乙氧基硅烷加入其中,以进行15分钟的改性反应。
[0196]
接着,加入8.11g的缩合促进剂四(2-乙基-1,3-己二油酸)钛,再搅拌15分钟。
[0197]
最后,在反应后,将242mg的作为金属卤化物化合物的四氯化硅添加到聚合物溶液中,并且添加2,6-二叔丁基-对甲苯酚。接着,通过汽提而除去溶剂且使被保护的伯氨基脱保护,然后用温度被调整至110℃的热辊干燥橡胶,以得到伯胺改性的聚丁二烯橡胶p。
[0198]
分析所得的经改性的聚丁二烯的微观结构(乙烯基键量),结果乙烯基键量为30质量%。
[0199]
进一步地,经改性的聚丁二烯橡胶(伯胺改性的聚丁二烯橡胶p)以外的各成分的详细情况如下。
[0200]
(1)橡胶成分
[0201]
天然橡胶:rss#1
[0202]
(2)填料
[0203]
炭黑1:由旭碳株式会社制造,产品名“asahi#52”[0204]
[氮吸附法比表面积28m2/g,dbp吸油量128ml/100g,甲苯着色透过率=65%]
[0205]
炭黑2:由旭碳株式会社制造,产品名“asahi#60”[0206]
[氮吸附法比表面积40m2/g,dbp吸油量114ml/100g,甲苯着色透过率=80%]
[0207]
炭黑3:由东海碳素株式会社制造,产品名“seast fy”[0208]
[氮吸附法比表面积29m2/g,dbp吸油量152ml/100g,甲苯着色透过率=80%]
[0209]
炭黑4:由卡博特公司(cabot)制造,产品名“sp5000a”[0210]
[氮吸附法比表面积28m2/g,dbp吸油量120ml/100g,甲苯着色透过率=99%]
[0211]
(3)树脂
[0212]
热固性树脂:酚醛树脂,由住友电木株式会社制造,产品名“smiliteresin pr-50731”[0213]
固化剂:六甲氧基甲基三聚氰胺,由富士胶片和光纯药株式会社制造
[0214]
(4)硫化促进剂、硫化剂、硫化延迟剂
[0215]
硫化促进剂1(tot):二硫化四(2-乙基己基)秋兰姆,由大内新兴化学工业株式会社制造,商品名“nocceler tot-n”[0216]
硫化促进剂2(tbztd):二硫化四苄基秋兰姆,由三新化学工业株式会社制造,产品名“sanceler tbztd”[0217]
硫化促进剂3(ns):n-叔丁基-2-苯并噻唑次磺酰胺,由大内新兴化学工业株式会社制造,产品名“nocceler ns”[0218]
硫化延迟剂(pvi):由孟山都公司制造,产品名“santoguard pvi”[n-(环己硫基)-邻苯二甲酰亚胺]
[0219]
硫:由鹤见化学工业株式会社制造,产品名“粉末硫黄”[0220]
(5)各种成分
[0221]
硬脂酸:由新日本理化株式会社制造,产品名“硬脂酸50s”[0222]
氧化锌:白水科技(hakusui tech)公司制造,产品名“3号氧化锌”[0223]
防老剂(6c):n-苯基-n'-(1,3-二甲基丁基)-对苯二胺,由大内新兴化学工业株式会社制造,产品名“nocrac 6c”[0224]
[安全轮胎的制造及硫化橡胶物理性能的测定与评价]
[0225]
(a)尺寸a的轮胎的制造
[0226]
将得到的橡胶组合物制备为图1所示的胎侧加强橡胶层8和胎圈填料7,并且根据常规方法分别制造轮胎尺寸255/65f18(尺寸a)的用于乘用车的子午线安全轮胎。在原型轮胎中,胎侧加强橡胶层的最大厚度为14.0mm,并且所有胎侧加强橡胶层均形成为相同的形状。
[0227]
(b)尺寸b的轮胎的制造
[0228]
将得到的橡胶组合物制备为图1所示的胎侧加强橡胶层8和胎圈填料7,并且根据常规方法分别制造轮胎尺寸235/65r17(尺寸b)的用于乘用车的子午线安全轮胎。在原型轮胎中,胎侧加强橡胶层的最大厚度为11.8mm,并且所有胎侧加强橡胶层均形成为相同的形状。
[0229]
1.高温软化度
[0230]
将实施例1和3~5以及比较例1~7的橡胶组合物硫化而得到的硫化橡胶的动态拉伸储能模量e’是在初始拉伸应变为5%、动态拉伸应变为1%且频率为52hz的条件下于25℃~180℃测定的。计算动态拉伸储能模量e'的最大值(e'
max
)与180℃下的动态拉伸储能模量e'(e'
180℃
)之间的差(δe'=e'
max-e'
180℃
),作为高温软化度。将比较例1的高温软化度δe'设为1.000,然后求出表1和表2中记载的实施例和比较例中每一个的高温软化度δe'的指数。高温软化度δe'越小,则硫化橡胶在高温下越难软化。这意味着机械强度得以保持。
[0231]
实施例2的高温软化度的评价如下进行。
[0232]
将橡胶组合物硫化而得到的硫化橡胶的动态拉伸储能模量e'是在初始拉伸应变为5%、动态拉伸应变为1%且频率为52hz的条件下于25℃~180℃测定的。计算动态拉伸储能模量e'的最大值(e'
max
)与180℃下的动态拉伸储能模量e'(e'
180℃
)之间的差(δe'=e'
max-e'
180℃
),作为高温软化度。将比较例1的高温软化度δe'设为1.000,然后求出高温软化度δe'的指数。高温软化度δe'越小,则硫化橡胶在高温下越难软化。这意味着机械强度得以保持。
[0233]
2.安全轮胎耐久性
[0234]
在表1的实施例1、4和5以及比较例2~4中,使用了尺寸a的原型轮胎;并且在表2的比较例6和7中,使用了尺寸b的原型轮胎。然后,在未施加内压的状态下,进行转鼓行驶(速度80km/h),然后将直到轮胎不能行驶的转鼓行驶距离设定为安全行驶距离。
[0235]
在表1(实施例1、4、5和比较例2~4)中,用将比较例4的安全轮胎的安全行驶距离设为100时的指数来表示;并且在表2(比较例6和7)中,用将比较例6的安全轮胎的安全行驶距离设为100时的指数来表示。该指数越大,则安全轮胎的安全耐久性越好。
[0236]
在实施例2、实施例3、比较例1和比较例5中,未进行安全耐久性评价。
[0237]
3.断裂特性(eb
×
tb)
[0238]
在表1的实施例1和3~5以及比较例1~5中,硫化橡胶是在145℃、26分钟的硫化条件下制造的。在表2的比较例6和7中,硫化橡胶是在160℃、12分钟的硫化条件下制造的。将各硫化橡胶加工成no.8哑铃状试验片,并且通过使用拉伸试验装置(岛津制作所)求出断裂伸长率(eb)和拉伸强度(tb)。
[0239]
将试片在25℃以100mm/min的速度拉伸,并且测定当试片断裂时的长度。然后,将相对于拉伸前长度(100%)的长度(单位:%)作为断裂伸长率(eb)。
[0240]
以规定速度(500
±
25mm/min)在25℃下拉伸试片直至试片断裂,并且以jis k 6251(2017)为基准,将断裂所需的最大拉伸力(单位:mpa)作为拉伸强度(tb)。
[0241]
将由实施例和比较例中得到的断裂伸长率(eb)(%)和抗拉强度(tb)(mpa)分别相乘来计算eb
×
tb。
[0242]
在表1(实施例1和3~5和比较例1~5)中,用将比较例4的eb
×
tb值设为100时的指数来表示eb
×
tb值。在表2(比较例6和7)中,用将比较例6的eb
×
tb值设为100时的指数来表示eb
×
tb值。该指数越大,则硫化橡胶的断裂特性越优异。
[0243]
在表1的实施例2中,硫化橡胶是在145℃、26分钟的硫化条件下制造的。将各硫化橡胶加工成no.8哑铃状试验片,并且通过使用拉伸试验装置(岛津制作所)求出断裂伸长率(eb)和拉伸强度(tb)。
[0244]
将试片在25℃以100mm/min的速度拉伸,并且测定当试片断裂时的长度。然后,将相对于拉伸前长度(100%)的长度(单位:%)作为断裂伸长率(eb)。
[0245]
以规定速度(500
±
25mm/min)在25℃下拉伸试片直至试片断裂,并且以jis k 6251(2017)为基准,将断裂所需的最大拉伸力(单位:mpa)作为拉伸强度(tb)。
[0246]
将断裂伸长率(eb)(%)和抗拉强度(tb)(mpa)相乘来计算eb
×
tb。
[0247]
用将比较例4的eb
×
tb值设为100时的指数来表示eb
×
tb的值。该指数越大,则硫化橡胶的断裂特性越优异。
[0248]
表1
[0249][0250]
表2
[0251][0252]
由表1和表2可知,本发明的橡胶组合物的硫化橡胶与比较例相比高温软化度小,其中,在本发明的橡胶组合物中,相对于100质量份的橡胶成分,硫化促进剂2(二硫化四苄基秋兰姆)的含量为1.0~2.0质量份,并且比(a/b)为0.60~1.25。由此可知,本发明的橡胶组合物的硫化橡胶在高温下不易软化,则机械强度得以维持。进一步地,由于实施例1、4和5的安全耐久性指数大于100,可以发现使用高温软化度小的硫化橡胶的轮胎的安全耐久性
优异。
[0253]
工业实用性
[0254]
本发明的橡胶组合物的硫化橡胶在高温下不易软化,并且具有优异的机械强度,因此能够选择性地用于各种轮胎,特别是安全轮胎的胎侧加强橡胶和胎圈填料。
[0255]
附图标记列表
[0256]
1:胎圈芯,2:胎体层,3:胎侧橡胶层,4:胎面橡胶层,5:带束层,6:气密层,7:胎圈填料,8:胎侧加强橡胶层,10:胎肩区域。