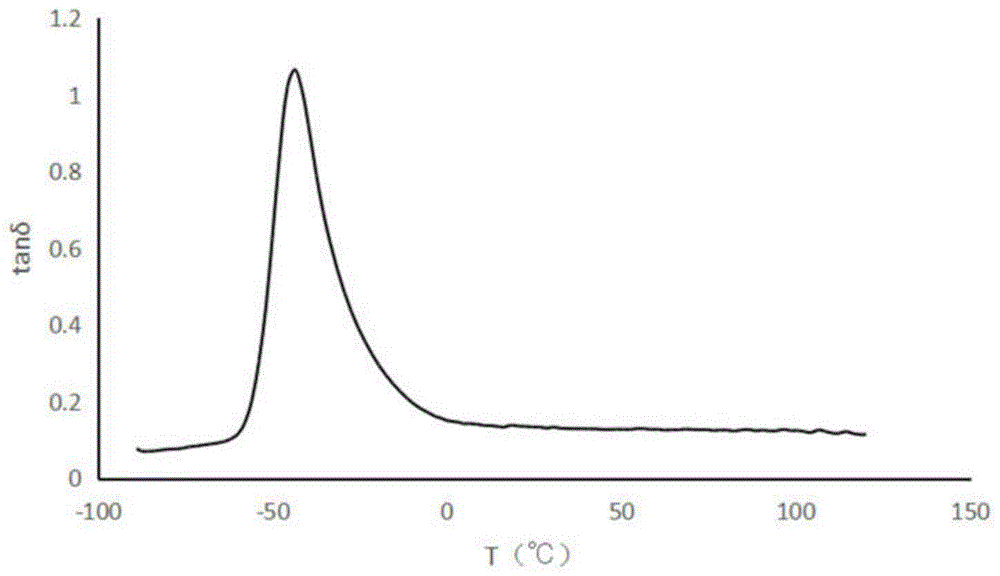
本发明涉及复合材料领域,尤其提供了一种优良加工性的高强度橡胶复合材料及其制备方法。
背景技术:
:反应型增塑剂是一种能与基材(如:nr、ir、iir、sbr、br、nbr、cr、epdm等高分子橡胶材料)在硫化过程中,用硫磺或过氧化物进行共同硫化的液体材料。常见的反应型增塑剂大都为低分子量的双烯烃聚合物,常温下为高粘度液体,分子结构中的不饱和键为其提供了共交联反应活性基团,而且硫化后在制品中无迁移及制品在溶剂中无抽出,提高了制品耐老化及耐化学性能,现作为环保型增塑材料现已逐渐替代传统增塑剂,广泛应用于各种橡胶制品中。液体异戊橡胶是低分子量的顺1,4-聚异戊二烯材料,通常是采用阴离子溶液聚合方法制备的线形聚异戊二烯,作为反应型增塑剂,近年来已应用于轮胎、粘合剂、压敏胶、密封件、医疗器件等绿色橡胶制品中。北京化工大学的赵素合和张兴英教授研究团队,报道了反应型增塑剂液体异戊二烯在天然橡胶、异戊橡胶、丁苯橡胶、顺丁橡胶等橡胶共混体系的性能,研究结果表明,液体异戊橡胶在提高胶料加工性能的同时,还可以改善炭黑粒子在硫化胶中的分散。但是在应用中,普遍存在随着液体异戊橡胶添加量的增加,硫化胶的拉伸强度和撕裂强度显著降低的问题,该问题限制了其应用领域和消费量。特别是在使用过程中受到动态受力应变的产品,如轮胎,耐压胶管等,力学性能的降低也会导致产品动态性能和疲劳性能降低。因此,寻找开发一种具有增强复合材料力学性能的反应型增塑剂,并用其制备混炼工艺简单、机械性能优良、疲劳性能优异的橡胶复合材料仍是目前橡胶制品领域中一个亟待解决的技术难题。技术实现要素:为解决以上技术难题,本发明提供了一种优良加工性的高强度橡胶复合材料及其制备方法。该复合材料采用硅氧烷封端改性的低分子量聚异戊二烯替代胎面胶配方体系中的增塑剂,在改善橡胶复合材料的加工性能和气味的同时,显著提高复合材料的力学性能,从而提升材料的抗疲劳性能,另外该复合材料也具有较低的滚动阻力。为实现上述目的,本发明的技术方案具体如下:一种优良加工性的高强度橡胶复合材料,各组分按重量份计包括:其中所述的二烯烃类橡胶包括天然橡胶、丁苯橡胶、顺丁橡胶、异戊橡胶和丁腈橡胶中的一种或多种并用。所述的改性聚异戊二烯分子结构如下所示:其中,r1为r2为烷氧基;r3,r4为烷基或烷氧基;r5为低分子量聚异戊二烯前聚体,其结构单元的微观结构主要为1,4-结构或3,4-结构或1,2-结构;a≥0;b≥2。所述的改性聚异戊二烯由低分子量聚异戊二烯经过硅氧烷封端改性而成,具体采用带有环氧基的烷氧基硅烷偶联剂终止低分子量聚异戊二烯前聚体得到。所述的低分子量聚异戊二烯(pip)分子量在1×103g/mol-10×104g/mol之间,其微观结构包括:1,4-聚异戊二烯,3,4-聚异戊二烯,1,2-聚异戊二烯中的一种或多种;优选的,所述的低分子量聚异戊二烯分子中结构分布为:1,4-结构含量:15%-95%、3,4-结构含量:5%-80%、1,2-结构含量:0-20%或3,4-结构含量:85%-50%、1,2-结构含量:5-20%、1-4结构含量:0-30%。更为优选的,所述的低分子量聚异戊二烯分子中结构分布为3,4-结构含量:85%-50%、1,2-结构含量:5-20%、1-4结构含量:0-30%。本发明所述的改性聚异戊二烯制备方法:将异戊二烯单体通过阴离子溶液聚合法合成低分子量聚异戊二烯前聚体,然后加入带有环氧基的硅烷偶联剂,终止前聚体端部的阴离子活性中心;然后加入试剂脱去末端金属,最后用乙醇凝聚,恒温干燥得到改性聚异戊二烯。其中,带有环氧基的硅烷偶联剂选自kh560、kh-561、kh-563、信越kbe-303等,优选带有乙氧基kh-561和信越kbe-303,因其在后续的硅烷化反应中释放出的乙醇是无毒性的;脱去末端金属所采用的试剂可以是水、盐酸、醋酸等。优选的,低分子量聚异戊二烯前聚体的制备方法如下:在除水除氧的聚合反应瓶中,在氮气的保护下导入异戊二烯单体,之后加入约单体质量2-4倍的反应溶剂,再加入单体质量0%-40%的结构调节剂,充分混合后,加入单体摩尔数0.002-0.015%摩尔的烷基锂引发剂;在30-50℃搅拌下聚合2~6小时,得到聚异戊二烯前聚体。所述的反应溶剂为己烷、环己烷、戊烷等烷烃溶剂;所述的结构调节剂为四氢呋喃、二乙二醇二甲醚(2g)、甲基乙基醚、烷基四氢糠醚等醚类,优选四氢呋喃;烷基锂引发剂选自正丁基锂、仲丁基锂、戊基锂等,优选正丁基锂。聚合过程中加入结构调节剂可以制备不同微观结构的聚异戊二烯,满足不同复合材料的应用需求。优选的,制备分子中结构分布为3,4-结构含量:85%-50%、1,2-结构含量:5-20%、1-4结构含量:0-30%的低分子量聚异戊二烯时,结构调节剂加入量为单体质量的10%-40%。本发明中,所述硅烷偶联剂配合白炭黑使用,硅烷偶联剂用量为白炭黑质量的2%-15%。本发明中补强剂主要为白炭黑,所述白炭黑为气相法;白炭黑优选高分散性白炭黑,其能提高复合材料的力学性能,保证材料具有较好的使用价值。其他补强剂选自炭黑、滑石粉、重质碳酸钙中的一种或多种。所述的硫化剂选自硫磺类硫化剂或过氧化物类硫化剂或其混合物。其中所述的硫磺类硫化剂选自硫磺或载硫体,其对应的硫化促进剂选自秋兰姆类、噻唑类、次磺酰胺类中的一种或多种,具体选自n-氧联二亚乙基-2-苯并噻唑次磺酰胺(促进剂nobs)、n,n-二环己基-2-苯并噻唑次磺酰胺(促进剂dz)、n-环己基-2-苯并噻唑次磺酰胺(促进剂cz)、n-叔丁基-2-苯并噻唑次磺酰胺(促进剂ns)、2-叔戊基苯并噻唑次磺酰胺、n-环己基-双-(2-苯并噻唑)次磺酰胺、n-叔丁基-2-双苯并噻唑次磺酰胺中的一种或多种。所述的过氧化物硫化剂为三烯丙基异氰脲酸酯(taic)、双叔丁过氧异丙基苯(bipb),n,n'-间苯撑双马来酰亚胺(hva-2)中的一种或多种;硫化促进剂能缩短硫化时间,提高生产效率,改善橡胶复合材料的力学性能。本发明所采用的硫化体系为普通硫化体系或半有效硫黄硫化体系。用于轮胎、胶带等方面动态下使用的产品,配方采用普通硫化体系,该硫化体系可为硫化胶提供较优良的疲劳性能和动态性能。用于橡胶密封制品、胶管等方面的产品,配方优选采用半有效硫化体系,该硫化体系可为硫化胶提供较优良的静态性能和较好的耐热氧老化性能。本发明所述的防老剂为苯二胺系列为主的防老剂,防老剂4010na、防老剂bm、防老剂4020、防老剂rd中的一种或多种并用,提升材料的抗氧和抗臭氧老化性能。本发明所述优良加工性的高强度橡胶复合材料可用开炼机或密炼机混炼制备,具体步骤如下:开炼机混炼:在双辊混炼机上加入二烯烃类橡胶,使胶料包辊,塑炼均匀,然后将氧化锌、硬脂酸、防老剂一并加入,然后依次加入三分之一的补强剂、硅烷偶联剂、改性聚异戊二烯、剩余补强剂,左右割刀三次,最后依次加入硫化剂和硫化促进剂,左右割刀三次,打三角包五次,下片,制得混炼胶放置16小时以后硫化,最后制得硫化胶。密炼机混炼:一段混炼:在密炼机中,填料系数控制在0.7-0.8之间,50℃依次投入二烯烃类橡胶、小料(氧化锌、硬脂酸、防老剂)、改性聚异戊二烯、补强剂白炭黑、硅烷偶联剂和其他补强剂进行混炼,混炼时胶温控制在100-130℃,混炼时间共计5-10分钟,混炼均匀后卸料,开炼机压片,得到预混胶,室温调节16-24h;二段混炼:在密炼机上依次加入硫化剂和硫化促进剂,混炼温度控制在80-110℃,混炼时间共计3-5分钟,混炼均匀后卸料,开炼机压片,得到混炼胶,室温调节16-24h。本发明中,首先通过对低分子量聚异戊二烯经过硅氧烷封端改性得到改性聚异戊二烯,经过改性后,聚异戊二烯分子链末端在混炼和硫化过程中可与白炭黑表面的活性基团发生反应键合,有效的减少聚异戊二烯自由末端数,加固硫化体系的交联网络,大大提高了硫化胶的机械力学性能和动态性能。将改性聚异戊二烯按照本发明的配比量添加到橡胶复合材料体系中,显著改善了采用现有技术中液体异戊橡胶作为反应型增塑剂的橡胶复合材料的加工性能和机械性能,并能够使硅烷偶联剂发挥更高的效率,减少用量,并且不用另外加入增塑剂。综上所述,利用本发明的改性聚异戊二烯及配方体系,能够得到混炼工艺简单且机械性能优良、疲劳性能优异的橡胶复合材料,尤其是显著提升了材料的撕裂强度,定伸应力和拉伸强度。附图说明图1实施例1硫化胶样品的动态力学性能图。具体实施方式下面通过具体的制备实施例进一步说明本发明,但应理解为,这些实施例仅仅是用于更详细具体地说明之用,而不应理解为用于以任何形式限制本发明。基于本
技术领域:
人员依据本发明所能够改变、重组方法得到的与发明相关的技术,都在本发明的保护范围内。各实施例根据本发明的配方体系,配置各组分,并按照以下方法制备硫化胶:方法一:在双辊混炼机上加入二烯烃类橡胶,使胶料包辊,塑炼均匀,然后将氧化锌、硬脂酸、防老剂一并加入,然后依次加入三分之一的补强剂、硅烷偶联剂、改性聚异戊二烯、剩余补强剂,左右割刀三次,最后依次加入硫化剂和硫化促进剂,左右割刀三次,打三角包五次,下片,制得混炼胶放置16小时以后硫化,最后制得硫化胶。方法二:一段混炼:在密炼机中,填料系数控制在0.7-0.8之间,50℃依次投入二烯烃类橡胶、小料(氧化锌、硬脂酸、防老剂)、改性聚异戊二烯、补强剂白炭黑、其他补强剂和硅烷偶联剂进行混炼,混炼时胶温控制在100-130℃,混炼时间共计5-10分钟,混炼均匀后卸料,开炼机压片,得到预混胶,室温调节16-24h;二段混炼:在密炼机上依次加入硫化剂和硫化促进剂,混炼温度控制在80-110℃,混炼时间共计3-5分钟,混炼均匀后卸料,开炼机压片,得到混炼胶,室温调节16-24h,硫化制得硫化胶。实施例1与对比例1-3采用方法一混炼,实施例2-3采用方法二进行混炼制备混炼胶。各实施例与对比例的配方体系,按照重量份计,如下表所示:s1:将洁净的聚合瓶中的空气在高温烘烤的条件下置换为高纯氮气,置换至少三次,待其冷却后,在氮气的保护下导入148g精制后无水无氧的己烷,之后加入41g聚合级异戊二烯单体,使两者充分混合。s2:在聚合瓶中用注射器计量加入聚合和杀杂用的n-buli共计4.2ml,在50℃搅拌下聚合4小时。s3:将s2聚合后的聚合液转出95.32g用甲醇终止凝聚,干燥至恒重后得到低分子量聚异戊二烯(用于对比例1)。s4:s2聚合后的聚合液经s3部分转出后剩余的聚合液中加入0.77ml硅烷偶联剂kh560,继续反应2小时,最后加入含有少量盐酸的乙醇溶液终止反应,凝聚聚合物,40-50℃下恒温干燥后得到改性聚异戊二烯(用于实施例1和实施例4)。上述s3步骤后所制得的低分子量聚异戊二烯通过凝胶渗透色谱法测得分子量为1.48×104g/mol,分子量分布指数为1.46,通过核磁氢谱吸收谱图分析方法测得微观结构含量为:1,4-结构含量占93.02%(顺-1,4-结构:66.49%,反-1,4-结构26.53%),3,4-结构含量占6.98%。上述s4步骤后所制得的改性聚异戊二烯的分子量为1.73×104g/mol,分子量分布指数为1.572,微观结构含量:1,4-结构含量占93.14%(顺-1,4-结构:66.59%,反-1,4-结构26.55%),3,4-结构含量占6.86%。实施例2和实施例3中改性聚异戊二烯通过阴离子聚合反应制得,聚合溶剂中加入了结构调节剂四氢呋喃,制备过程与实施例1的相同。具体物料投入量为:聚合级异戊二烯单体22.4g,己烷67.2g,四氢呋喃5.8g,0.99mol/l的n-buli引发剂2.6ml,聚合后期加入0.86ml硅烷偶联剂kh561。所得改性聚异戊二烯的分子量为1.36×104g/mol,分子量分布指数为1.52,微观结构含量:3,4-结构含量占68.65%,1,2-结构含量占12.10%,1,4-结构含量占19.25%。测试各实施例及对比例混炼胶的硫化特性,确定硫化时间,进行硫化胶样品制备,获得其机械物理性能和动态力学性能。主要包括应用橡胶加工分析仪rpa2000评价混炼胶的硫化特性;用万能电子拉力试验机、邵a硬度计等测试硫化胶的定伸应力、拉伸强度、扯断伸长率、撕裂强度、硬度等力学性能;用动态力学分析仪(dma)测试硫化胶动态力学性能,评估胶料的抗湿滑性能。各实施例和对比例的硫化胶硫化条件:150℃×t90。评价结果如下表所示:实施例1实施例2实施例3实施例4对比例1对比例2对比例3硬度60686762595955拉伸强度/mpa19.6629.6727.1118.4318.3818.0011.68断裂伸长率/%590628614516638614572100%定伸/mpa1.122.723.052.390.961.000.69300%定伸/mpa4.629.7910.068.23.234.002.58撕裂强度/kn/m81.8841.4154.1864.8868.3636.9921.07由上述本发明实施例性能可知,本发明添加kh560封端的改性聚异戊二烯的硫化胶物理机械性能有很大的提升,尤其可以看出实施例1的硫化胶的物理机械性能最佳,显著提升了材料的撕裂强度,定伸应力和拉伸强度也较其他添加物和不添加情况的高。这充分说明,添加kh560封端改性的低分子量聚异戊二烯后,可以有效提高硫化胶的强度。当前第1页12