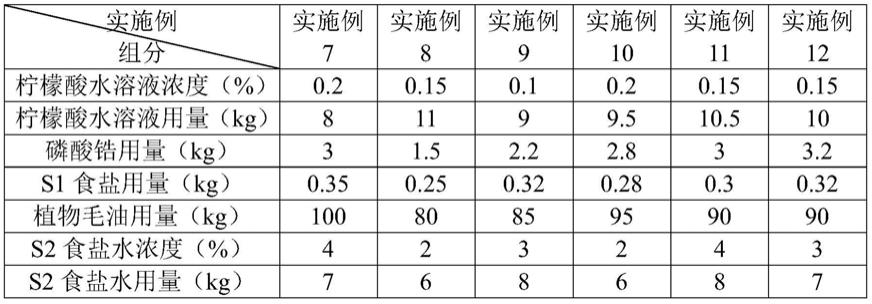
1.本申请涉及植物油加工技术领域,尤其涉及一种植物油脱胶工艺及其制备的植物油。
背景技术:2.植物油是用植物的果实、种子、胚芽等加工得到的油脂,如花生油、豆油、亚麻油、蓖麻油、菜子油等。植物油的主要成分是直链高级脂肪酸和甘油生成的酯,脂肪酸除软脂酸、硬脂酸和油酸外,还含有多种不饱和酸,如芥酸、桐油酸、蓖麻油酸等。植物油含有丰富的维生素e、维生素k、钙、铁、磷、钾等营养物质,植物油已逐渐成为人们食物烹调的首选。
3.在植物油加工过程中,一般先将果实、胚芽等原料通过压榨或浸出工艺制成毛油,毛油中含有一定量的磷脂,在植物油煎炸使用过程中,磷脂容易产生泡沫或沉淀物,影响油品质量。因此,为了提高植物油品质,毛油一般需脱胶处理以脱除磷脂。
4.cn107245375a公开了一种菜籽油水化脱胶方法,包括以下步骤:(1)将经过滤去除残存饼粕的菜籽毛油加热至80
‑
90℃后储存于储油罐并维持油温80
‑
90℃;(2)配制质量浓度为10
‑
15%的食盐水,加热至80
‑
90℃储存于盐水罐并维持盐水温度为80
‑
90℃;(3)将储油罐中的毛油以0.01
‑
0.03m/s的速度通过输油管输送至水化储罐,在距离水化储罐4.0
‑
5.0m的输油管中心加入盐水罐中的食盐水,使毛油与食盐水混合后继续流入水化储罐,食盐水加入输油管的速度为0.01
‑
0.03m/s;(4)将水化储罐中的毛油与食盐水的混合物进行离心分离除去胶质沉淀物,即得水化脱胶油。该技术方案通过使用食盐水,改变磷脂的表面电荷,使菜籽油中磷脂水化并聚集沉降,完成磷脂的脱除。
5.针对上述相关技术,发明人认为,植物油中含有亲水性磷脂和疏水性磷脂,对疏水性磷脂改性改善其亲水性转化成亲水性磷脂,在植物油脱胶处理过程中,水相中存在一定量的溶解态的磷脂,限制了疏水性磷脂向亲水性磷脂的转化,在一定程度上影响了脱胶效果。
技术实现要素:6.为了改善植物油脱胶工艺的脱胶效果,本申请提供一种植物油脱胶工艺及其制备的植物油。
7.第一方面,本申请提供一种植物油脱胶工艺,采用如下的技术方案:一种植物油脱胶工艺,包括以下步骤:s1水化:取质量浓度为0.1
‑
0.2%的有机酸的水溶液,加入水化促进剂,混合均匀,制得水化复合物;向水化复合物中加入植物毛油,加热至50
‑
70℃搅拌不少于30min,保温静置不少于60min,分离油相和水相,水相为油脚,油相为脱磷油;所述水化促进剂包括磷酸锆;所述有机酸为可溶性有机酸;s2水洗:向脱磷油中加入70℃
‑
80℃的质量浓度为2
‑
4%的食用盐水,搅拌不少于5min,分离油相和水相,制得脱胶油;
s3干燥:将脱胶油干燥至含水率不大于0.05%为止,制得植物油;所述步骤s1
‑
s2中的物料按如下重量份配比投料:有机酸的水溶液80
‑
120份,磷酸锆10
‑
35份,植物毛油800
‑
1000份,食用盐水60
‑
80份。
8.通过采用上述技术方案,磷酸锆是一种含有磷元素的固体酸,具有高比表面积的特点,对磷脂上的磷酸基团具有极强的亲和力;植物毛油中含有亲水性磷脂和疏水性磷脂,有机酸为可溶性的有机酸,有机酸可对植物毛油中的疏水性磷脂进行改性,改变疏水性磷脂的密度,使疏水性磷脂向亲水性磷脂转化。当将植物毛油加入至水化复合物中并进行搅拌时,会同时发生以下几种物理化学反应:磷酸锆上的固体酸会对植物毛油中的亲水性磷脂和疏水性磷脂进行吸附;有机酸对疏水性磷脂进行改性将疏水性磷脂转化成亲水性磷脂;亲水性磷脂发生水化反应聚集形成胶体;亲水性磷脂发生水化反应聚集形成的胶体吸附在高比表面积的磷酸锆表面,降低水相中游离态的亲水性磷脂含量,促使疏水性磷脂转化成亲水性磷脂的反应平衡正向移动,进一步降低油相中的疏水性磷脂含量,提高脱胶效果。当磷酸锆对大部分的磷脂完成吸附后,停止搅拌并开始保温静置处理,磷酸锆的密度约为3.3g/cm3,水相密度约为1g/cm3,油相密度约为0.92g/cm3,磷酸锆沉降在最下层,水相在中间,油相在最上层,水相中还存在一定量的游离态的亲水性磷脂,游离态亲水性磷脂继续聚集并吸附在磷酸锆表面,进一步降低水相中游离态亲水性磷脂浓度,促使油水界面中继续发生疏水性磷脂转化成亲水性磷脂的化学反应,反应平衡正向移动,进一步降低油相中的磷脂含量;而疏水性磷脂转化成亲水性磷脂的化学反应是可逆的,但由于磷酸锆中的路易斯酸对疏水性磷脂具有极强的吸附性,同时水相将磷酸锆与油相分隔开,疏水性磷脂无法溶解至水相中,疏水性磷脂无法迁移至能与疏水性磷脂互溶的油相中,因此,即使发生亲水性磷脂转化成疏水性磷脂的逆向反应,疏水性磷脂也无法进入油相中,有助于进一步降低油相中的磷脂含量,提高脱胶效果。
9.优选的,所述步骤s1
‑
s2中的物料按如下重量份配比投料:有机酸的水溶液95
‑
105份,磷酸锆25
‑
35份,植物毛油850
‑
950份,食用盐水60
‑
80份。
10.通过采用上述技术方案,使用更优的原料投料配比,有助于各物质之间更好地发生反应,有助于进一步改善脱胶效果。
11.优选的,所述磷酸锆的比表面积大于25
㎡
/g,孔容大于0.7ml/g。
12.通过采用上述技术方案,当比磷酸锆的比表面积较低或孔容较小时,不利于磷酸锆更好地吸附磷脂,影响脱脂效果。本申请使用大比表面积和大孔容的磷酸锆,有助于更好地吸附磷脂,更好地改善脱胶效果。
13.优选的,所述水化促进剂还包括2.5
‑
3.5重量份的食盐。
14.通过采用上述技术方案,在水化复合物中加入一定量的食盐,食盐是电解质,一方面可以改变植物毛油的电荷性能,有助于防止植物毛油发生乳化现象而影响水相与油相的分离效果;另一方面,食盐溶解在有机酸的水溶液中,增大水相密度,增大油相与水相的密度差,有助于更好地分离油相与水相,降低脱磷油中杂质含量,改善脱胶效果。
15.优选的,所述有机酸为柠檬酸、草酸或酒石酸。更优的,所述有机酸为柠檬酸。
16.通过采用上述技术方案,选用合适的有机酸,有助于更好地对疏水性磷脂进行改性,有助于更好地改善脱胶效果。
17.优选的,所述植物油脱胶工艺还包括磷酸锆再生处理步骤:将步骤s1产生的油脚
进行一次过滤,将滤饼烘干至含水率不大于2%为止,加入不少于3倍磷酸锆重量的氯仿,混合均匀,进行二次过滤,将二次过滤的滤饼用不少于0.5倍磷酸锆重量的食品级无水乙醇淋洗,烘干,制得再生磷酸锆。优选的,干燥温度不低于100℃,干燥至恒重。更优的,二次过滤的滤饼烘干后于不低于400℃焙烧不少于60min。
18.通过采用上述技术方案,用氯仿溶解磷酸锆上吸附的磷脂,过滤脱除磷脂,再通过用食品级无水乙醇淋洗脱除氯仿,再通过干燥脱除无水乙醇,通过烘干或焙烧可彻底脱除氯仿等有机物,实现磷酸锆的再生利用,减少固废排放,降低工艺成本。
19.优选的,所述步骤s3中的干燥为真空干燥,干燥压力为
‑
0.095mpa至
‑
0.08mpa,干燥温度为102℃
‑
108℃。
20.通过采用上述技术方案,通过真空干燥脱除脱胶油中残留的水分,有助于减少杂质,提高植物油品质。
21.第二方面,本申请提供一种植物油,采用如下的技术方案:一种植物油,由上述的植物油脱胶工艺制得。
22.通过采用上述技术方案,使用本申请公开的植物油脱胶工艺制备植物油,可降低植物油中磷脂含量,提高植物油品质,有利于植物油产品市场推广。
23.综上所述,本申请包括以下至少一种有益技术效果:1.本申请通过使用含磷酸锆和有机酸的水化复合物,有机酸对植物毛油中的疏水性磷脂进行改性,磷酸锆对磷脂进行吸附,再采用合适的水化处理工艺,三者相互配合,有助于降低植物油中磷脂含量,改善植物油脱胶工艺的脱胶效果;2.本申请通过采用选取合适的有机酸、在水化复合物中加入食盐、选取合适的干燥工艺条件、控制磷酸锆的比表面积和孔容等方式,有助于降低植物油中杂质含量,提高植物油品质,有利于产品市场推广;3.本申请通过对磷酸锆进行再生处理,可对磷酸锆回收循环利用,有助于减少固废排放,有助于提高环保性和降低工艺成本。
具体实施方式
24.发明人在研究中发现,用常规的食盐水脱胶工艺对植物毛油进行脱胶处理时,植物油中还会残留一定量的磷脂,脱胶效果欠佳。本申请基于上述技术背景,提出一种可改善脱胶效果的技术方案,具体通过以下具体实施方式说明。
25.相比于常规的食盐水脱胶工艺,由于磷酸锆、有机酸与合适的水化处理工艺共同作用具有良好的脱胶效果,可降低水化温度,本申请水化温度较低,有助于减少能耗,降低工艺成本。
26.在脱胶工艺中,油相和水相的分离可用离心机进行离心分离;也可使用脱胶设备进行分离,脱胶设备的底部设置排水口,磷酸锆和水相先从排水口排出,实现油水分离。
27.植物毛油为植物的果实、种子、胚芽进压榨获得的毛油,可以是花生毛油、大豆毛油、亚麻毛油、蓖麻毛油、菜籽毛油、玉米毛油和米糠毛油中的一种或多种。实际生产过程中,可根据植物毛油中磷脂含量选择合适的磷酸锆用量,植物毛油中磷脂含量较高时可增加磷酸锆用量,植物毛油中磷脂含量较低时,可适当减少磷酸锆用量。
28.可根据实际经济效益选择是否对磷酸锆进行再生回收利用。在实际生产过程中,
植物毛油经脱胶处理后还需经脱色、脱臭、养晶脱脂和脱蜡处理达标后方可进行包装并销售。可使用常规的食品级白土脱色剂进行脱色处理,可采用高温(如脱臭温度230℃)脱臭处理,低温(低于5℃)养晶并过滤完成脱蜡处理。
29.步骤s1水化温度为50
‑
70℃,优选60℃。步骤s2水洗温度为70
‑
80℃,优选75℃。步骤s3真空干燥的干燥压力为
‑
0.095mpa至
‑
0.08mpa,优选
‑
0.09mpa;干燥温度为102℃
‑
108℃,优选105℃。
30.以下实施例中使用的植物毛油为大豆毛油,磷脂含量为2.56%,由四川省川海晨洋有限公司提供,以下实施例中使用同一批次的植物毛油。以下实施例中使用的磷酸锆比表面积为26.4
㎡
/g,孔容为0.74ml/g,粒径目数为200目。实施例
31.实施例1:一种植物油脱胶工艺,包括以下步骤:s1水化:取草酸配制成质量浓度为0.1%的草酸水溶液。取12kg草酸水溶液,加入1kg磷酸锆,混合均匀,制得水化复合物。将水化复合物转入脱胶设备中,脱胶设备的底部设置有排水口,脱胶设备带有加热和搅拌装置。加入90kg植物毛油,以100转/分钟的转速搅拌,加热至60℃搅拌30min,停止搅拌,保温静置60min,从排水口分离出水相,水相为油脚,油相为脱磷油。
32.s2水洗:向脱磷油中加入7kg的75℃质量浓度为3%的食用盐水,75℃保温搅拌10min,静置15min,从排水口分离出水相,完成一次水洗;重复上述水洗过程,完成二次水洗,制得脱胶油。
33.s3干燥:将脱胶油在
‑
0.09mpa压力条件下,105℃抽真空干燥30min,制得植物油,含水率为0.04%。
34.实施例2实施例2与实施例1的区别在于,实施例2用等质量的相同质量浓度的柠檬酸水溶液代替草酸水溶液,其它均与实施例1保持一致。
35.实施例3实施例3与实施例2的区别在于,实施例3的水化复合物中加入了0.3kg食盐,其它均与实施例2保持一致。
36.实施例4实施例4与实施例3的区别在于,实施例4将磷酸锆的用量从1kg提高至2kg,其它均与实施例3保持一致。
37.实施例5实施例5与实施例3的区别在于,实施例5将磷酸锆的用量从1kg提高至2.5kg,其它均与实施例3保持一致。
38.实施例6实施例6与实施例3的区别在于,实施例6将磷酸锆的用量从1kg提高至3.5kg,其它均与实施例3保持一致。
39.实施例7
‑
12实施例7
‑
12与实施例5的区别在于,实施例7
‑
12各原料的添加量不同,其它均与实施例5保持一致,实施例7
‑
12各原料的添加量见表1。
40.表1实施例7
‑
12的各原料的添加量制备例1磷酸锆再生:收集实施例4
‑
6的油脚并合并,进行一次过滤,将滤饼于100℃干燥240min,含水率1.2%,加入24kg氯仿,混合均匀,进行二次过滤,将二次过滤的滤饼用4kg食品级无水乙醇淋洗,然后于100℃干燥至恒重,于400℃焙烧120min,完成磷酸锆的再生,制得再生磷酸锆。
41.实施例13实施例13与实施例5的区别在于,实施例13用等质量的制备例1制得的再生磷酸锆代替普通磷酸锆,其它均与实施例5保持一致。
42.对比例对比例1对比例1与实施例1的区别在于,对比例1不加入磷酸锆,其它均与实施例1保持一致。
43.对比例2对比例2与实施例1的区别在于,对比例2不加入草酸水溶液,对比例2将1kg磷酸锆加入12kg水中,制得水化复合物,其它均与实施例1保持一致。
44.对比例3对比例3与实施例1的区别在于,对比例3步骤s1加热至70℃搅拌30min完成后,保温静置10min后立即进行油水分离,其它均与实施例1保持一致。
45.性能检测1、磷脂含量:磷脂含量测定参照gb/t5537
‑
2008《粮油检验磷脂含量的测定》公开的钼蓝比色法,实验结果如表2。
46.表2不同脱胶工艺制备的植物油中磷脂含量对比表样品编号磷脂含量(mg/kg)实施例1132实施例2116实施例385实施例441实施例58实施例66实施例77
实施例860实施例924实施例106实施例115实施例127实施例1310对比例1468对比例2725对比例3214相比于实施例1,对比例1不加入磷酸锆,用单一的草酸水溶液完成水化,制得的产品中磷脂含量较高,脱胶效果不佳。对比例2不加入有机酸,直接用磷酸锆吸附脱除磷脂,脱胶效果不佳。对比例3的水化步骤完成后,没有充分静置,制得的产品中磷脂含量偏高,脱胶效果不佳。
47.对比实施例1和对比例1
‑
3的实验结果,可以看出,有机酸水溶液和磷酸锆同时使用,且采用合适的水化处理工艺,制得的产品中磷脂含量显著降低,脱硫效果较好。
48.对比实施例1和实施例2的实验结果,实施例2用柠檬酸代替草酸,脱胶效果更好。对比实施例1和实施例3的实验结果,实施例3的水化复合物中加入了食盐,有助于进一步改善脱胶效果。实施例3
‑
6是不同磷酸锆用量的对比试验,磷酸锆用量较少时,增大磷酸锆用量可明显改善脱胶效果,当磷酸锆用量增加至一定量后,再增加磷酸锆用量对脱胶效果影响不大。相比于实施例5,实施例7
‑
12中各原料的添加量不同,其中实施例8
‑
9中磷酸锆用量较少,脱胶效果欠佳,实施例7、实施例10
‑
12中磷酸锆用量合适,脱胶效果较好。
49.相比于实施例5,实施例13用再生后的磷酸锆水化处理植物毛油,制得的产品中磷脂含量较低,脱胶效果较好,可将油脚中的磷酸锆再生处理后回收利用,实现固体废弃物的循环利用,减少固废排放,可降低植物油脱胶工艺的工艺成本。
50.本具体实施方式的实施例均为本申请的较佳实施例,并非依此限制本申请的保护范围,故:凡依本申请的结构、形状、原理所做的等效变化,均应涵盖于本申请的保护范围之内。