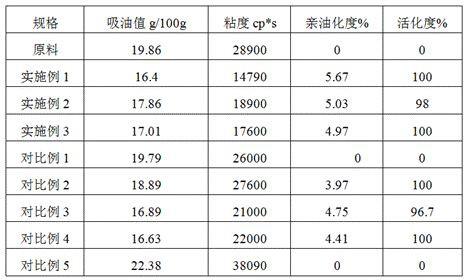
1.本发明涉及无机材料制备领域,特别是一种超疏水高流动性的导热硅脂用球形氧化铝的表面改性方法。
背景技术:2.随着5g通讯的发展,电子、通讯集成化程度越高,并朝着体积小、质量轻、功能复杂和智能化方向发展,并且对材料的散热也要求越来越高,导热材料应用在电子产品上比较广泛,最为常见应该是导热硅脂、导热垫片是高性能间隙填充导热材料,因此要求所使用的垫片、硅脂的导热也要求越来越高。为提高材料的导热率,垫片、硅胶在制备的过程中需使用填充比例更大的传统导热填料,例如氧化铝。如何提高在乙烯基硅油体系中氧化铝的填充量和改善氧化铝在硅油中的流动性是行业研究的关键问题。但是,普通的氧化铝填料与硅油的结合力较差,导致配方体系粘度剧增,很难将填料均匀分散在硅油当中,填料的添加量受到限制。本方法以不同硅烷偶联剂种类之间的协同反应为重点,研究硅烷偶联剂的改性工艺,同时考虑下游导热材料的基材、主体配方及技术要求,经综合考虑选择合理的改性剂及改性工艺。
技术实现要素:3.本发明的目的是针对现有技术的不足,提供一种具有优异流动性能和超疏水导热硅脂用球形氧化铝的表面改性制备方法。制得的产品疏水性好,具有高活性和高流动性,并在乙烯基硅油体系中的分散性强,具有较好的工艺操作性,便于生产。
4.本发明所要解决的技术问题是通过以下的技术方案来实现的,本发明是一种超疏水高流动性的导热硅脂用氧化铝的表面改性方法,其特点是,所述方法包括以下步骤:(1)原料:采用球形氧化铝和角形氧化铝的混合物作原料;(2)协同偶联剂制备:将硅烷偶联剂3
‑
缩水甘油醚氧基丙基三甲氧基硅烷(kbm
‑
403)、乙醇和水按质量比1:0.8-1.5:0.8-2.5的比例混合,调节ph至4.0
‑
5.0,搅拌水解10
‑
40min形成水解液;然后向水解液中加入硅烷偶联剂十二烷基三乙氧基硅烷(sico
ꢀ‑
n1223),混合搅拌10
‑
50min,形成混合液;混合液中3
‑
缩水甘油醚氧基丙基三甲氧基硅烷与十二烷基三乙氧基硅烷的质量比为4
‑
8:2
‑
4;(3)改性:将步骤(2)制备的偶联剂混合液喷雾到原料氧化铝混合物表面进行改性,改性温度为80℃
‑
130℃,改性时间为10
‑
40min,3
‑
缩水甘油醚氧基丙基三甲氧基硅烷的用量为氧化铝质量的4
‑8‰
,十二烷基三乙氧基硅烷的用量为氧化铝质量的2
‑4‰
。
5.本发明所述的一种超疏水高流动性的导热硅脂用氧化铝的表面改性方法:其进上步优选的技术方案是:1、步骤(2)中,水解时3
‑
缩水甘油醚氧基丙基三甲氧基硅烷、乙醇与水的质量比为1:1:2。
6.2、步骤(2)中,调节ph至4.5。
7.3、步骤(2)中,搅拌水解时间为30min。
8.4、步骤(2)中,调节ph用化学级醋酸。
9.5、步骤(3)改性中,改性温度为110℃。
10.6、步骤(3)改性中,改性时间为20min。
11.7、步骤(3)改性中,3
‑
缩水甘油醚氧基丙基三甲氧基硅烷的用量为氧化铝质量的6
‰
,十二烷基三乙氧基硅烷的用量为氧化铝质量的2
‰
。
12.8、步骤(1)原料中,角形氧化铝占氧化铝混合物质量的3
‑
6%,最优选占氧化铝混合物质量的6%。
13.与现的技术相比,本发明具有以下有益效果:本发明方法改性后所制得的产品具有较高的疏水性和优异的亲油化度,由于偶联剂kbm
‑
403具有降低体系粘度的特性,且硅烷偶联剂的水解能够使改性剂的效果提高至最佳,但其亲水性的特点使得改性后的填料颗粒表面不能形成疏水的薄膜,通过将2种偶联剂进行协同处理,在水解液中加入疏水性偶联剂sico
ꢀ‑
n1223,使得改性后的产品既具有低粘度高分散性的特点,又兼顾高疏水性,解决了氧化铝与乙烯基硅油结合力差的问题,且改性工艺简单,具有较高的经济效益。
14.本发明先将偶联剂进行水解,这是由于偶联剂在水解时硅烷基遇水会分解成硅烷醇,然后与无机材料表面的羟基和氢相结合,如硅微粉、氧化铝填料表面具有较多的羟基,无机材料表面的活性羟基越多越容易发生反应,从而提升填料在硅油体系中的分散性。
具体实施方式
15.以下进一步描述本发明的具体技术方案,以便于本领域的技术人员进一步地理解本发明,而不构成对其权利的限制。
16.实施例1,超疏水高流动性的导热硅脂用氧化铝的表面改性实验一:将4kg氧化铝填料投入高速混合搅拌器中,将设备预热到110℃,加入已水解的混合液(24gkbm
‑
403、24乙醇、48g纯水,水解30min,水解ph为4.5 再加入8gsico
ꢀ‑
n1223,混合搅拌10min),搅拌改性20min,得到导热硅脂用超疏水高流动性的氧化铝填料。
17.实施例2,超疏水高流动性的导热硅脂用氧化铝的表面改性实验二:将4kg氧化铝填料投入高速混合搅拌器中,将设备预热到80℃,加入已水解的混合液(24gkbm
‑
403、24乙醇、48g纯水,水解30min,水解ph为4.5 再加入8gsico
ꢀ‑
n1223,混合搅拌10min),搅拌改性20min,得到导热硅脂用超疏水高流动性的氧化铝填料。
18.实施例3,超疏水高流动性的导热硅脂用氧化铝的表面改性实验三:将4kg氧化铝填料投入高速混合搅拌器中,将设备预热到130℃,加入已水解的混合液(24gkbm
‑
403、24乙醇、48g纯水,水解30min,水解ph为4.5 再加入8gsico
ꢀ‑
n1223,混合搅拌10min),搅拌改性20min,得到导热硅脂用超疏水高流动性的氧化铝填料。
19.对比例1,氧化铝的表面改性对比实验一:将4kg氧化铝填料投入高速混合搅拌器中,将设备预热到110℃,加入水解的混合液(24gkbm
‑
403、24乙醇、48g纯水,水解30min,水解ph为4.5),搅拌改性20min,得到导热硅脂用氧化铝填料。与实施例1不同的是去除疏水性的偶联剂sico
ꢀ‑
n1223。
20.对比例2,氧化铝的表面改性对比实验二:
将4kg氧化铝填料投入高速混合搅拌器中,将设备预热到130℃,加入偶联剂sico
ꢀ‑
n1223 10g,搅拌改性20min,得到导热硅脂用氧化铝填料。与实施例1不同的是去除了偶联剂kbm
‑
403的水解液。
21.对比例3,氧化铝的表面改性对比实验三:将4kg氧化铝填料投入高速混合搅拌器中,将设备预热到110℃,加入已水解的混合液(24gkbm
‑
403、24乙醇、48g纯水,水解30min,水解ph为7 再加入8gsico
ꢀ‑
n1223,混合搅拌10min),搅拌改性20min,得到导热硅脂用超疏水高流动性的氧化铝填料。与实施例1不同的是水解液ph调节为中性。
22.对比例4,氧化铝的表面改性对比实验四将4kg氧化铝填料投入高速混合搅拌器中,将设备预热到110℃,加入已水解的混合液(24gkbm
‑
403、24乙醇、48g纯水,水解30min,水解ph为9 再加入8gsico
ꢀ‑
n1223,混合搅拌10min),搅拌改性20min,得到导热硅脂用超疏水高流动性的氧化铝填料。与实施例1不同的是水解液ph调节为碱性。
23.对比例5,氧化铝的表面改性对比实验五将4kg氧化铝填料投入高速混合搅拌器中,将设备预热到110℃,加入已水解的混合液(24gkbm
‑
403、24乙醇、48g纯水,水解30min,水解ph为4.5 再加入8gsico
ꢀ‑
n1223,混合搅拌10min),搅拌改性20min,得到导热硅脂用超疏水高流动性的氧化铝填料。与实施例1不同的是氧化铝填料中去除了6%的角形氧化铝。
24.将上述实施例、对比例进行性能测试,具体数据如表一:表1表面处理氧化铝性能测试从上述数据可以看出,相对比于未改性和未协同改性的氧化铝,协同改性过后的氧化铝的活化度和亲油化度有较大的提升,应用于时,协同改性过后的氧化铝的粘度大大降低,改善了氧化铝在乙烯基硅油中的分散性,提高了乙烯基硅油的加工性能。本发明将疏水性的偶联剂sico
ꢀ‑
n1223加入到水解后的kbm403溶液中,可以使得粉体既具有环氧偶联剂的降粘效果,又拥有超强疏水性的特点,对比实验例1
‑
3,改性温度对于粉体综合的性能具有较大的影响,其中本发明最佳的改性工艺为改性温度110℃。同时本发明对硅烷偶联剂进行水解时,不仅选择酸性条件进行水解,而是综合对比水解液在酸性、中性、碱性条件的水解效果,优选酸性为最佳条件,既缩短了水解时间,同时也使得粉体具有优异的性能。并且本发明对氧化铝填料的比例进行了优选,从对比例五的数据可以看出,添加角形氧化铝
的作用是改善球形氧化铝中大球与大球之间的流动性,提升在乙烯基硅油体系中的填充量,使得填料的导热得到提升。
25.将上述实施例应用于终端产品,具体性能测试结果如表二:表2各实施例和比较例改性后产品的应用性能从上述数据可以看出,相对比于未处理的氧化铝填料,经过协同改性后的氧化铝,其导热系数和弯曲强度均有较大的提升,球形氧化铝的加入能较大程度的增加复合材料的弯曲强度,在受到外力作用时,外力能通过包覆结构的氢键从基体有效的传递到增强体,由于3
‑
缩水甘油醚氧基丙基三甲氧基硅烷偶联剂能够提升粉体的分散效果,提高在体系中填充量,并且十二烷基三乙氧基硅烷由于其长链的化学结构而具有突出的力学性能,充分吸收能量,从而使复合材料能够更好的抵抗外界应力,防止应力集中。特别是当温度合适时,增强体与基体的两相界面形成了网状的交联点,提高了界面的抵抗应力的能力,增大了材料的弯曲强度和弯曲模量。所以,偶联剂之间的协同反应和改性温度控制在100
‑
110℃这两个条件对于终端产品的弯曲强度和导热性能有极大的增强。
26.实施例4,一种超疏水高流动性的导热硅脂用氧化铝的表面改性方法,所述方法包括以下步骤:(1)原料:采用球形氧化铝和角形氧化铝的混合物作原料;角形氧化铝占氧化铝混合物质量的3%;(2)协同偶联剂制备:将硅烷偶联剂3
‑
缩水甘油醚氧基丙基三甲氧基硅烷、乙醇和水按质量比1:0.8:2.5的比例混合,调节ph至4.0,搅拌水解10min形成水解液;然后向水解液中加入硅烷偶联剂十二烷基三乙氧基硅烷,混合搅拌50min,形成混合液;混合液中3
‑
缩水甘油醚氧基丙基三甲氧基硅烷与十二烷基三乙氧基硅烷的质量比为4:2;(3)改性:将步骤(2)制备的偶联剂混合液喷雾到原料氧化铝混合物表面进行改性,改性温度为80℃,改性时间为10min,3
‑
缩水甘油醚氧基丙基三甲氧基硅烷的用量为氧化铝质量的4
‰
,十二烷基三乙氧基硅烷的用量为氧化铝质量的2
‰
。
27.实施例5,一种超疏水高流动性的导热硅脂用氧化铝的表面改性方法,所述方法包括以下步骤:(1)原料:采用球形氧化铝和角形氧化铝的混合物作原料;角形氧化铝占氧化铝混合物质量的6%;(2)协同偶联剂制备:将硅烷偶联剂3
‑
缩水甘油醚氧基丙基三甲氧基硅烷、乙醇和
水按质量比1:1.5:0.8的比例混合,调节ph至5.0,搅拌水解40min形成水解液;然后向水解液中加入硅烷偶联剂十二烷基三乙氧基硅烷,混合搅拌10min,形成混合液;混合液中3
‑
缩水甘油醚氧基丙基三甲氧基硅烷与十二烷基三乙氧基硅烷的质量比为8:2;(3)改性:将步骤(2)制备的偶联剂混合液喷雾到原料氧化铝混合物表面进行改性,改性温度为130℃,改性时间为40min,3
‑
缩水甘油醚氧基丙基三甲氧基硅烷的用量为氧化铝质量的8
‰
,十二烷基三乙氧基硅烷的用量为氧化铝质量的2
‰
。
28.实施例6,一种超疏水高流动性的导热硅脂用氧化铝的表面改性方法,所述方法包括以下步骤:(1)原料:采用球形氧化铝和角形氧化铝的混合物作原料;角形氧化铝占氧化铝混合物质量的5%;(2)协同偶联剂制备:将硅烷偶联剂3
‑
缩水甘油醚氧基丙基三甲氧基硅烷、乙醇和水按质量比1:1:1.5的比例混合,调节ph至4.8,搅拌水解30min形成水解液;然后向水解液中加入硅烷偶联剂十二烷基三乙氧基硅烷,混合搅拌40min,形成混合液;混合液中3
‑
缩水甘油醚氧基丙基三甲氧基硅烷与十二烷基三乙氧基硅烷的质量比为4:4;(3)改性:将步骤(2)制备的偶联剂混合液喷雾到原料氧化铝混合物表面进行改性,改性温度为120℃,改性时间为30min,3
‑
缩水甘油醚氧基丙基三甲氧基硅烷的用量为氧化铝质量的4
‰
,十二烷基三乙氧基硅烷的用量为氧化铝质量的4
‰
。
29.对公开的实施例的上述说明,使本领域专业技术人员能够实现或者使用本发明。对这些实施例的多种修改对本领域的专业技术人员来说将是显而易见的,本文所提到的方法可以在不脱离本发明的精神或者范围的情况下,在其他实施例中实现。因此,本发明不会被限制于本文所示的这些实施例,而是要符合与本文公开的原理和新颖特点相一致的最宽范围。