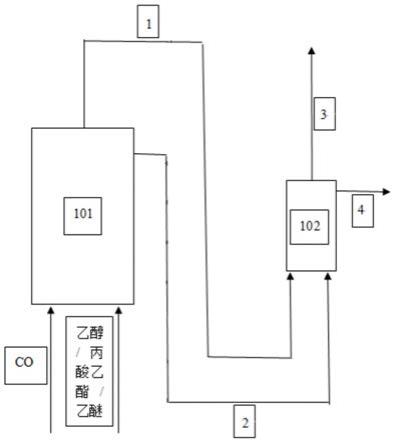
1.本发明属于有机化工技术领域,具体为一种用乙醇液相羰基合成制丙酸的反应系统。
背景技术:2.丙酸,是三个碳饱和脂肪酸,主要用作食品防腐剂和防霉剂。
3.目前已工业化生产方法主要有三种:一是低碳烷烃转化法,该方法由于选择性低,分离复杂,已逐步被淘汰;二是丙醛氧化法,三是乙烯羰基合成法。目前国际上基本采用后两种方法生产。这两种方法均采用乙烯作为原料,我国是贫油国家,石油储量有限,而我国粮食乙醇技术成熟,采用可再生的植物资源,所以对乙醇羰基合成制丙酸,研究较多,特别是甲醇液相羰基合成制醋酸技术的工业化,为乙醇液相羰基合成制丙酸的工业化奠定了基础。
4.乙醇液相羰基合成制丙酸,实验室研究较多,主要有:
5.美国杜邦公司首先采用乙醇羰基化得到丙酸:在180
‑
400℃、35.5
‑
70.9mpa条件下,三氟化硼、四氯化碳、乙酸铜、锰或铝、镍、钴、铁的卤化物,以及铬、钼、钨酸等为催化剂,在酸性介质中,乙醇和一氧化碳反应生成丙酸。丙酸收率为72%,此法由于反应速率/收率/催化剂损耗及高温高压设备腐蚀等工艺问题未获解决,至今未工业化。
6.1968年美国monsanto公司的f.e.paulik等报道了可溶性的羰基铑
‑
碘化物催化体系,对甲醇羰基合成醋酸有着很高的选择性和催化活性,反应条件温和。由于铑均相催化甲醇羰基化制备醋酸获得成功,人们发现用铑均相催化乙醇羰基化乙醇制备丙酸也是一个可行的方法。1985年,thomas w.等报道了甲醇、乙醇及正丙醇等在铑催化剂存在下羰基化动力学及反应机理的研究。报道中指出乙醇羰基化速度仅为甲醇的1/20左右。
7.1994年南开大学的赵维君等合成了含有膦配体的钴和镍的络合物,考察了这些络合物对乙醇羰基化制丙酸乙酯的催化性能;比较了这些不同配体对催化反应的影响。在此基础上在1995年合成了含膦及膦氮配体的镍、钴、钯络合物,对催化活性进行评价,发现镍和钴的活性相当,但是不及钯。
8.1996年华南理工大学的王大为等报道了在氢气气氛中合成镍的催化剂,用于液相乙醇羰基化制丙酸及丙酸乙酯,考察了反应时间、络合配位体及溶剂等因素对催化剂活性和选择性的影响,取得了一定成效。
9.2004年英国bp公司的专利指出,一种生产丙酸的方法是在铱催化剂、促进剂铑或锇的卤化物存在下,以可羰基化反应物乙醇或其衍生物如丙酸乙酯为原料合成丙酸。
10.2008年,西南化工研究设计院在甲醇羰基化制醋酸催化剂基础上,用乙醇液相羰基合成丙酸,丙酸的时空收率为1mol/l.h。
11.2013年,上海华谊集团技术研究院赖春波报道了在铱催化剂体系中乙醇液相羰基合成丙酸,丙酸的时空收率超过3mol/l.h。
12.2013年,山东华鲁恒升化工股份有限公司宋望一报道了在铑催化体系中乙醇羰基
合成丙酸,研究了进料速度、水含量对羰基合成的影响,得到最大的时空收率是5.2mol/l.h.
13.2014年,江苏索普化工股份有限公司/中国院化学所邵守言/袁国卿等公开了一种二丙烯三胺/羰基铑催化剂的制备方法及在乙醇羰基合成制丙酸中的应用。
14.2016年,上海华谊能源化工有限公司唐斌等公开了一种铑钌催化剂在乙醇低压羰基合成制丙酸中的应用。
15.乙醇液相羰基合成制丙酸技术,目前大部分都停留在催化剂研制方面,在实际操作部分还需要大量开发利用。
技术实现要素:16.本发明的发明目的在于根据乙醇液相羰基合成制丙酸反应的特性,提出了一种可以工业化的乙醇液相羰基合成制丙酸的反应系统:即采用两个反应器串联,第一反应器采用全返混的反应器,维持较高的反应速度;第二反应器采用全返混或平推流反应器,使丙酸乙酯和一氧化碳进一步转化,减少丙酸乙酯的循环量和提高一氧化碳的利用率。该反应系统与相同体积的单反应器相比,在相同条件下能获得更大的产能。
17.为了实现以上发明目的,本发明的具体技术方案为:
18.一种乙醇液相羰基合成制丙酸的反应系统,包括第一反应器和第二反应器;原料乙醇与一氧化碳进入第一反应器,在含有催化剂的溶液中羰基合成丙酸,未反应完的丙酸乙酯与未反应完的一氧化碳及催化剂溶液进入第二反应器继续反应,以提高原料一氧化碳及乙醇、丙酸乙酯、乙醚的转化率。
19.原料乙醇可替换为丙酸乙酯或乙醚;乙醇进入反应器后与丙酸酯化成丙酸乙酯,乙醚进入反应器后水解成乙醇,乙醇与丙酸酯化成丙酸乙酯。
20.作为本技术中一种较好的实施方式,所述的第一反应器为全返混反应器,该反应器保持高的反应速度;第二反应器为全返混反应器或平推流反应器,该反应器保持原料高的转化率,这样可以比相同体积的单反应器在相同条件下获得更大的产能。
21.作为本技术中一种较好的实施方式,第二反应器的压力低于第一反应器的反应压力;通过压差使物料从第一反应器输送至第二反应器,无需消耗多余的能量。
22.作为本技术中一种较好的实施方式,第一反应器的压力为1.0
‑
10.0mpa,优选1.2
‑
8.0mpa,更进一步优选1.5
‑
5.0mpa。
23.作为本技术中一种较好的实施方式,第一反应器和第二反应器的反应温度均为170
‑
220℃。
24.作为本技术中一种较好的实施方式,第一反应器中丙酸乙酯浓度为1%
‑
20%,优选1.5
‑
10%;第二反应器出口物料中丙酸乙酯浓度为0.5
‑
10%,优选1.0
‑
5%。
25.作为本技术中一种较好的实施方式,催化剂体系为主活性成分为铑或铱,助剂为碘乙烷的催化剂,该催化剂为市售产品。
26.通过对乙醇液相羰基合成制丙酸进行深入研究,针对该反应的特性,本发明中提出了一种可以工业化的反应系统方案:即采用两个反应器串联,第一反应器采用全返混的反应器(乙醇为原料,该反应器中涉及的主反应见(2)(3);丙酸乙酯为原料,该反应器中涉及的反应式见(3);乙醚为原料,该反应器中涉及的反应式见(1)(2)(3)),维持较高的反应
速度;第二反应器采用全返混或平推流反应器(该反应器中涉及的的反应式见(3)),使丙酸乙酯和一氧化碳进一步转化,减少丙酸乙酯的循环量和提高一氧化碳的利用率。这样可以比相同体积的单反应器在相同条件下获得更大的产能。
[0027][0028][0029]
ch3ch2cooch2ch3+h2o+co
→
2ch3ch2cooh
ꢀꢀꢀ
(3)与现有技术相比,本发明的积极效果体现在:
[0030]
(一)采用两个反应器串联,第一反应器采用全返混的反应器,维持较高的反应速度;第二反应器采用全返混或平推流反应器,使丙酸乙酯和一氧化碳进一步转化,减少丙酸乙酯的循环量和提高一氧化碳的利用率。
[0031]
(二)可以利用本发明对乙醇液相羰基制丙酸的反应系统做工业化设计,可以获得比相同体积的单反应器获得更大的产能。
附图说明
[0032]
图1为实施例1中所述乙醇液相羰基合成制丙酸的反应系统中采用两个全返混反应器串联的流程示意图;
[0033]
其中,101为第一反应器,102为第二反应器,1为第一反应器汽相物料,2为第一反应器液相物料,3为第二反应器气相物料,4为第二反应器液相物料。
[0034]
图2为全返混反应器和平推流反应器串联示意图;
[0035]
图2为实施例2所述乙醇液相羰基合成制丙酸的反应系统示意图(第一反应器为全返混反应器,第二反应器为平推流反应器);
[0036]
其中,101为第一反应器,102为第二反应器,1为第一反应器汽相物料,2为第一反应器液相物料,3/4为第二反应器气液相物料。
具体实施方式
[0037]
一种乙醇液相羰基合成制丙酸的反应系统,其步骤为:原料乙醇或丙酸乙酯或乙醚等反应性原料与一氧化碳输送进入第一反应器,第一反应器中包含有催化剂,助催化剂的丙酸溶液,在此反应器中,如果采用乙醚进料,则乙醚首先水解成乙醇(见反应式(1)),然后乙醇与丙酸发生酯化反应(见反应式(2)),生成丙酸乙酯,最后丙酸乙酯部分羰基化生成丙酸(见反应式(3));如果采用乙醇进料,则首先乙醇与丙酸发生酯化反应(见反应式(2)),生成丙酸乙酯,然后丙酸乙酯部分羰基化生成丙酸(见反应式(3));如果采用丙酸乙酯进料,则丙酸乙酯部分羰基化生成丙酸(见反应式(3));第一反应器中未反应完的一氧化碳及有机蒸汽及副产的氢气和二氧化碳(物料1)进入第二反应器,第一反应器中的液相(物料2)也进入第二反应器,在第二反应器中,丙酸乙酯继续与co羰基合成生成丙酸,通过两个反应器后,提高了一氧化碳的利用率和丙酸乙酯的转化率。
[0038][0039]
[0040]
ch3ch2cooch2ch3+h2o+co
→
2ch3ch2cooh
ꢀꢀꢀ
(3)
[0041]
该发明涉及的乙醇液相羰基合成制丙酸的反应系统,包括第一反应器和第二反应器,第一反应器为全返混反应器,保持高的反应速度;第二反应器为全返混或平推流反应器;保持原料高的转化率,这样可以比相同体积的单反应器在相同条件下获得更大的产能。
[0042]
该发明涉及的乙醇液相羰基合成制丙酸的反应系统,第一反应器压力1.0
‑
10.0mpa,优选1.2
‑
8.0mpa,更优选1.5
‑
5.0mpa。第二反应器的压力低于第一反应器的反应压力;通过压差使物料从第一反应器输送至第二反应器,而无需消耗多余的能量。压差的大小,以能使第一反应器的物料顺利输入第二反应器为原则。
[0043]
该发明涉及的乙醇液相羰基合成制丙酸的反应系统,第一反应器反应温度170
‑
220℃,第二反应器102温度170
‑
220℃。两个反应器的温度可以相同,也可以不同。
[0044]
该发明涉及的乙醇液相羰基合成制丙酸的反应系统,第一反应器中丙酸乙酯浓度优选1.0%
‑
20%,更优选1.5
‑
10%;第二反应器出口物料中丙酸乙酯浓度优选0.5
‑
10%,更优选1.0
‑
5.0%。
[0045]
该发明涉及的乙醇液相羰基合成制丙酸的反应系统,原料为乙醇或丙酸乙酯,乙醚等。
[0046]
该发明涉及的乙醇液相羰基合成制丙酸的反应系统,催化剂体系为铑或铱,助剂为碘乙烷,水和丙酸做溶剂,碘离子作为催化剂稳定剂,该催化剂为市售产品。
[0047]
本具体实施方式中提供一种乙醇液相羰基合成制丙酸的反应系统,包括以下步骤:
[0048]
(1)配置含原料和催化剂、助催化剂的溶液,由于该反应系统没有与分离系统联动,造成催化剂和助催化剂不能返回反应系统,所以在进料中配置催化剂和助催化剂,模拟连续反应过程。
[0049]
(2)为了保持催化剂浓度恒定,所以在反应器中初始加入的物料与配置的物料相同,由于配置的物料乙醇含量较高,所以在升温反应一段时间后,待反应液组成达到预定值以后,再连续加入配料,以使反应一直维持在预定状态。
[0050]
(3)对比示例的目的是与该发明的示例对照,所以通过改变进料流量使反应器出口物料组成与发明示例的第二反应器出口反应液一致。
[0051]
为了使本发明的目的、技术方案及优点更加清楚明白,以下结合附图及实施例,对本发明进行进一步详细说明。本说明书中公开的所有特征,或公开的所有方法或过程中的步骤,除了互相排斥的特征和/或步骤以外,均可以以任何方式组合。
[0052]
以下实施例反应器中采用的催化剂为市售产品。
[0053]
实施例1:
[0054]
配置含乙醇10%(wt)的反应液原料(详细组成见表1原料行),在两个串联的搅拌反应器(第一反应器,1l)和(第二反应器,200ml)中加入配置好的反应液,用一氧化碳置换三次,用一氧化碳加压至0.3mpa,加热两个搅拌釜至200℃,补加一氧化碳至第一反应器压力4.0mpa,第二反应器压力3.7mpa,1小时后启动进料泵,以15g/min的速度加入配置的反应液,稳定运行30分钟后取第一、第二反应器汽相出口,液相出口,(汽相、液相取样均采用冷冻水冷却取样),用气相色谱测定尾气组成和反应液组成。测定结果见表1:
[0055]
表1:两个全返混釜串联运行时各釜气液组成
[0056][0057][0058]
实施例2:
[0059]
配置含乙醇10%(wt)的反应液(详细组成见表2原料行),在1l的搅拌反应器和200ml管式反应器中(两釜串联,搅拌式反应在前(第一反应器),管式反应器在后(第二反应器)),加入配置好的反应液,用一氧化碳置换三次,用一氧化碳加压至0.3mpa,加热两个釜至200℃,补加一氧化碳至4mpa,第二反应器压力3.7mpa,启动进料泵,以15g/min的速度加入配置的反应液,30分钟后取第一、第二反应器汽相出口,液相出口,(汽相、液相取样均采用冷冻水冷却取样),用气相色谱测定尾气组成和反应液组成。测定结果见表2:
[0060]
表2:全返混反应釜与平推流反应器串联运行时各釜气液组成
[0061][0062]
对比例1(对比实施例1)
[0063]
配置含乙醇10%(wt)的反应液原料(详细组成见表3原料行),在1.2l搅拌反应器中,加入配置好的反应液,用一氧化碳置换三次,用一氧化碳加压至0.3mpa,加热反应器至200℃,补加一氧化碳至反应器压力4mpa,1小时后启动进料泵,以12g/min的速度加入配置的反应液,稳定运行30分钟后取反应器汽相出口,液相出口,(汽相、液相取样均采用冷冻水冷却取样),用气相色谱测定尾气组成和反应液组成。测定结果见表3:
[0064]
表3:单全返混釜运行时气液组成(对比实施例1)
[0065][0066]
对比实施例1可知,想要获得相同的出口组成,单釜的进料量(12g/min)是低于双釜的进料量的(15g/min)。
[0067]
对比例2(对比实施例2)
[0068]
配置含乙醇10%(wt)的反应液原料(详细组成见表4原料行),在1.2l搅拌反应器中,加入配置好的反应液,用一氧化碳置换三次,用一氧化碳加压至0.3mpa,加热反应器至200℃,补加一氧化碳至反应器压力4mpa,1小时后启动进料泵,以11g/min的速度加入配置的反应液,稳定运行30分钟后取反应器汽相出口,液相出口,(汽相、液相取样均采用冷冻水冷却取样),用气相色谱测定尾气组成和反应液组成。测定结果见表4:
[0069]
表4:单全返混釜运行时气液组成(对比实施例2)
[0070][0071][0072]
对比实施例2可知,想要获得相同的出口组成,单釜的进料量(11g/min)是低于双釜的进料量的(15g/min)。
[0073]
以上所述仅为本发明的较佳实施例而已,并不用以限制本发明,凡在本发明的精神和原则之内所作的任何修改、等同替换和改进等,均应包含在本发明的保护范围之内。