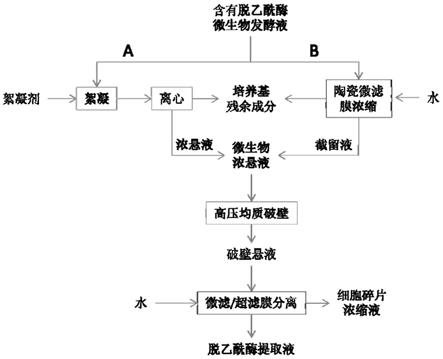
一种n
‑
乙酰氨基葡萄糖脱乙酰酶的提取方法
技术领域
1.本发明涉及一种n
‑
乙酰氨基葡萄糖脱乙酰酶的提取方法,属于生物工程技术领域。
背景技术:2.d
‑
葡萄糖胺在人体内具有重要的生理意义,应用于医药、食品和化妆品等领域。甲壳素广泛分布于虾壳、蟹壳等生物原料中,但生产过程需要使用强酸和强碱,易造成严重的环境污染。利用基因工程技术可以构建生产n
‑
乙酰氨基葡萄糖的重组微生物,可以实现n
‑
乙酰氨基葡萄糖的大规模生产,但距离d
‑
葡萄糖胺仍有一步之遥,需要n
‑
乙酰氨基葡萄糖脱乙酰酶催化水解后才能得到。
3.n
‑
乙酰氨基葡萄糖脱乙酰酶(ec 3.5.1.33)是一种重要的脱乙酰酶,分子量为30~60kda,一些酶复合体的分子量在160~200kda之间。催化的生物反应式为:n
‑
乙酰
‑
d
‑
葡萄糖胺+h2o=d
‑
葡萄糖胺+乙酸。roseman于1957年首次发现该酶催化和参与d
‑
葡萄糖胺的代谢过程。同族中相近功能的脱乙酰酶还包括甲壳糖脱乙酰酶(ec 3.5.1.41),二乙酰壳二糖脱乙酰酶(ec 3.5.1.105)和n
‑
乙酰氨基葡糖
‑6‑
磷酸脱乙酰酶(ec 3.5.1.25)。目前已发现的存在n
‑
乙酰氨基葡萄糖脱乙酰酶基因的微生物主要有大肠杆菌、乳酸乳球菌、柯达卡热球菌、堀越热球菌等(j.biol.chem.2004,279,30021
‑
30027)。通过重组大肠杆菌、重组枯草芽孢杆菌等微生物经过好氧发酵可实现高效表达和生产得到。提取n
‑
乙酰氨基葡萄糖脱乙酰酶是生产d
‑
葡萄糖胺的关键步骤之一。
4.1993年美国专利(us 5219749)公开了一种纯化甲壳糖脱乙酰酶的方法,利用硫酸铵沉淀法富集鲁氏毛霉发酵液中的甲壳糖脱乙酰酶,再依次经过疏水色谱、强阴离子交换色谱和强阳离子交换色谱三个单元,最终得到较纯的甲壳糖脱乙酰酶。
5.2002年希腊克里特大学bouriotis等从酿酒酵母中提取出甲壳糖脱乙酰酶,其提取步骤主要包括:以硫酸铵沉淀法富集粗酶后,加入到苯基
–
sepharosehiload(疏水)色谱柱,梯度洗脱后再载入到mono s阳离子交换色谱柱上分离,最终得到较纯的甲壳糖脱乙酰酶,回收率24.5%。
6.2006年武汉大学蔡军利用短柄帚霉好氧发酵获得甲壳糖脱乙酰酶,利用硫酸铵沉淀法富粗酶,再依次经过sephadex g
‑
25和sephadex g
‑
100两个色谱单元,最终得到较纯的甲壳糖脱乙酰酶。
7.2012年美国专利(us2012009627a1)和中国专利(cn 105039464a)公布了n
‑
乙酰氨基葡萄糖
‑6‑
磷酸脱乙酰基酶(ec 3.5.1.25)、n
‑
乙酰氨基葡萄糖脱乙酰基酶(ec 3.5.1.33)、壳多糖脱乙酰酶和酰基转移酶的基因修饰、发酵工艺和酶反应条件。
8.酶提取效率的高低一方面取决于原料中杂质的成分组成、目标物和杂质的理化性质差异、目标产物的相对浓度等因素。目前关于n
‑
乙酰氨基葡萄糖脱乙酰酶提取方法的公开文献比较少,与之性质和功能相近的甲壳糖脱乙酰酶则相对较多,但仍主要是在实验室规模下实现,基本步骤包括盐沉析富集和多级色谱纯化,分离步骤多,提取相关的材料昂
贵,且分离过程使用的试剂通常为有机溶剂,不利于绿色安全生产,且最终产品的回收率较低。
技术实现要素:9.针对现有技术存在的高物耗、低效率等缺陷,本发明提供了一种新的n
‑
乙酰氨基葡萄糖脱乙酰酶提取方法,以富含n
‑
乙酰氨基葡萄糖脱乙酰酶的重组微生物发酵液为原料,通过陶瓷膜微滤或絮凝沉淀实现固液分离,收集得到微生物菌体并同时去除培养基中残留的营养物等细胞外杂质;利用高压均质法使细胞壁破裂,释放出包含有n
‑
乙酰氨基葡萄糖脱乙酰酶的细胞内容物;最后采用陶瓷微滤膜或陶瓷超滤膜截留细胞碎片等,使n
‑
乙酰氨基葡萄糖脱乙酰酶透析出来,得到较纯的酶溶液。
10.本发明的第一个目的是提供一种n
‑
乙酰氨基葡萄糖脱乙酰酶的分离纯化方法,所述方法包括如下步骤:
11.(1)以含有n
‑
乙酰氨基葡萄糖脱乙酰酶的微生物发酵液为原料,采用陶瓷微滤膜浓缩法或者絮凝离心法实现固液分离,得到内含有n
‑
乙酰氨基葡萄糖脱乙酰酶的微生物浓悬液;
12.(2)将微生物浓悬液进行高压均质处理,使微生物细胞壁破裂并从细胞内释放出n
‑
乙酰氨基葡萄糖脱乙酰酶,得到含有n
‑
乙酰氨基葡萄糖脱乙酰酶的破壁悬液;
13.(3)将破壁悬液经过陶瓷微滤膜或陶瓷超滤膜分离,透出液中得到纯度较高的n
‑
乙酰氨基葡萄糖脱乙酰酶提取液。
14.在一种实施方式中,所述步骤(1)中的微生物发酵液是微生物在含碳源、氮源和无机盐的培养基中发酵一段时间后的发酵液,含有n
‑
乙酰氨基葡萄糖脱乙酰酶、细胞代谢物和未消耗完全的培养基成分;所述微生物发酵液可以是重组大肠杆菌发酵液,也可以是重组枯草杆菌发酵液,也可以是乳球菌发酵液,也可以是重组酵母发酵液。
15.在一种实施方式中,所述述步骤(1)中的微滤膜是陶瓷材质的膜组件,所述微滤膜的平均孔径为1
‑
5μm,操作压力为0.3~0.8mpa,操作过程的温度控制在4~30℃。
16.在一种实施方式中,所述步骤(1)所用的絮凝剂是食品安全的絮凝剂,包括但不限于有机絮凝剂或无机絮凝剂;
17.在一种实施方式中,所述絮凝剂是聚丙烯酰胺、二甲基胺
‑
表氯醇共聚物、聚合氯化铁、氯化铁、硫酸铁、硫酸亚铁中的一种或两种以上的组合;
18.在一种实施方式中,所述絮凝剂的添加方式为(a)或(b):
19.(a)按如下剂量添加单一组分的絮凝剂:聚丙烯酰胺的添加量为原料中生物量干重的0.01~0.2%;二甲基胺
‑
表氯醇共聚物的添加量为生物量干重的0.01~0.1%;聚合氯化铁的添加量为生物量干重的0.1~2.0%;氯化铁的添加量为生物量干重的0.1~1.0%;硫酸铁的添加量为生物量干重的0.1~1.5%;硫酸亚铁的添加量为生物量干重的0.2~2.0%;
20.(b)添加含有两种以上组分的絮凝剂时,每种絮凝剂的添加量为单一组分按照(a)所述用量的20
‑
50%。
21.在一种实施方式中,所述步骤(1)所述的离心设备可以是连续操作的离心机或间歇操作的离心机;连续离心的设备可以为碟片式离心机,离心因子在8000~15000g;间歇操
作的离心机可以是自动卸料离心机,离心因子在4000~8000g。
22.在一种实施方式中,所述步骤(2)所述的高压均质破壁设备的操作条件是,高压均质的压强为60
‑
120mpa,均质次数为1
‑
3次,温度控制在4
‑
30℃。
23.在一种实施方式中,所述步骤(3)所述的陶瓷膜分离设备可以是微滤膜或者超滤膜,微滤膜的孔径是0.1~1.0μm,超滤膜的截留分子量为300
‑
1000kda,操作压力为0.3~0.8mpa,操作过程的温度控制在4~30℃。
24.在一种实施方式中,所述步骤(3)所述的陶瓷膜分离过程中添加的水量是原料液体积的1
‑
5倍。透出液中得到较高纯度的n
‑
乙酰氨基葡萄糖脱乙酰酶。
25.在一种实施方式中,在步骤(3)完成后,利用蒸汽对所述使用的生产设备和管道进行灭菌或消毒处理,防止生产过程中产生微生物污染,所述蒸汽的压强为0.2~0.6mpa,灭菌时间为5~40min。
26.有益效果:
27.本发明与现有技术相比,具有如下优点:
28.(1)本发明在工业生产规模下实现了n
‑
乙酰氨基葡萄糖脱乙酰酶的高效提纯。生产工艺具有高回收率、低原料消耗和环保安全的优势,产物回收率最高可达到88%,生产的n
‑
乙酰氨基葡萄糖脱乙酰酶的比活力最高可达到22u/g蛋白;
29.(2)本发明所采用的酶提取条件温和,未使用有机溶剂和高浓度的盐析,通过膜分离和高压均质实现细胞破壁,使酶得到高效提取,排放污染物质的量较少,工艺过程比较环保安全;
30.(3)本发明通过蒸汽对分离设备和管道进行灭菌和消毒,采用纯物理方法实现和维持生产过程的清洁卫生,有效解决酶提取过程中易发生染菌和卫生安全问题。
31.(4)本发明的工艺适用于不同规模下的n
‑
乙酰氨基葡萄糖脱乙酰酶的生产,具有广泛的工业化应用价值。
附图说明
32.图1n
‑
乙酰氨基葡萄糖脱乙酰酶的提取工艺路线。
具体实施方式
33.技术术语:
34.微生物浓悬液:含有微生物细胞的呈流动状态的絮凝沉淀物。
35.截流液:经超滤膜截留的含有大于超滤膜截留分子量的蛋白的溶液。
36.生物量(以干重计):是指单位体积中微生物细胞干物质的重量。将一定体积的发酵液置于离心管中,8000r/min离心10min去除上清液、清水洗涤沉淀物2~3次后,所得沉淀物在105℃烘干至恒重后测定的微生物干物质的重量。单位为g/l。
37.酶活回收率:酶活回收率按如下方法计算,
[0038][0039]
脱乙酰酶活性单位(u)定义为:在30℃,以n
‑
乙酰氨基葡萄糖为底物,以50mmol/l磷酸钠缓冲液(ph 7.5)的环境下,每1min反应得到1mmol氨基葡萄糖所需的酶量为1u酶活
单位。
[0040]
脱乙酰酶的纯度以每克蛋白质中含有的酶活性单位表示,记为u/g蛋白。
[0041]
分析方法:
[0042]
脱乙酰酶活性的测定方法参考j.microbiol.biotechnol.2018,28(11),1850
–
1858;蛋白质的测定方法为二辛可宁酸(bicinchoninic acid)比色法。
[0043]
实施例1
[0044]
按图1中a去路所示工艺路线,以含有n
‑
乙酰氨基葡萄糖脱乙酰酶的重组大肠杆菌发酵液为原料,
[0045]
含有n
‑
乙酰氨基葡萄糖脱乙酰酶的重组大肠杆菌发酵液是将重组大肠杆菌在含葡萄糖、蛋白胨、酵母粉、硫酸铵、磷酸氢二钾、磷酸二氢钠、碳酸钙等成分的培养基中经好氧发酵获得的发酵液,发酵液中含有部分未代谢完全的培养基成分,并含有重组微生物细胞及一些细胞残留碎片和代谢副产物,如乙酸、丙酸、氨基酸、色素等。
[0046]
操作步骤如下:
[0047]
(1)取50m3含有n
‑
乙酰氨基葡萄糖脱乙酰酶的重组大肠杆菌发酵液(发酵液酶活为101u/l),每l发酵液的生物量干重为60g,向发酵液储罐中泵入浓度为100g/l硫酸铁溶液20l,泵入浓度为10g/l食品级聚丙烯酰胺溶液25l,搅拌混合完全后絮凝20min;
[0048]
(2)将步骤(1)絮凝后含有微生物细胞的混凝液连续泵入转速为12000rpm的碟片式离心机中,收集到的12m3微生物浓悬液进入暂储槽中;清液流入清液罐中,经检测后排放至污水处理单元。
[0049]
(3)将步骤(2)收集到的微生物浓悬液进行高压均质处理,使微生物细胞壁破裂并从细胞内释放出n
‑
乙酰氨基葡萄糖脱乙酰酶,得到含有n
‑
乙酰氨基葡萄糖脱乙酰酶的破壁悬液;高压均质的压强为110mpa,进料流速为3m3/h,温度控制在10℃,均质完成后重复均质操作1次,共进行2次均质。
[0050]
(4)将步骤(3)所得的12m3破壁悬液经过陶瓷超滤膜分离。超滤膜的截留分子量为500kda,操作压力为0.5mpa,操作过程的温度控制在4~30℃。当截留液体积约为10m3时,分3次间歇添加去离子水共36m3对截留液进行洗涤,收集到38m3透出液,得到纯度为18u/g蛋白的n
‑
乙酰氨基葡萄糖脱乙酰酶提取液,截留液排放至污水处理单元。
[0051]
(5)利用蒸汽对所述使用的生产设备和管道进行灭菌或消毒处理,防止生产过程中产生微生物污染,所述蒸汽的压强为0.3mpa,灭菌时间为20min。提取效果见表1。
[0052]
实施例2
[0053]
按图1中b去路所示工艺路线,以含有n
‑
乙酰氨基葡萄糖脱乙酰酶的重组大肠杆菌发酵液为原料,操作步骤如下:
[0054]
(1)取50m3含有n
‑
乙酰氨基葡萄糖脱乙酰酶的重组大肠杆菌发酵液,(发酵液酶活为111u/l),泵入陶瓷微滤膜组件进行固液分离,收集微生物浓悬液,微滤膜的平均孔径为2μm,操作压力为0.4mpa,操作过程的温度控制在4~30℃。当截留液体积约为20m3时,分3次间歇添加去离子水共50m3进行浓缩,收集到20m3洗涤后的微生物浓悬液,透出液排放至污水处理单元。
[0055]
(2)将步骤(1)收集到的微生物浓悬液进行高压均质处理,使微生物细胞壁破裂并从细胞内释放出n
‑
乙酰氨基葡萄糖脱乙酰酶,得到含有n
‑
乙酰氨基葡萄糖脱乙酰酶的破壁
悬液;高压均质的压强为100mpa,进料流速为3m3/h,温度控制在15℃,均质完成后重复均质操作1次,共进行2次均质。
[0056]
(3)将步骤(2)所得的20m3破壁悬液经过陶瓷超滤膜分离。超滤膜的截留分子量为500kda,操作压力为0.4mpa,操作过程的温度控制在4~30℃。当截留液体积约为10m3时,分3次间歇添加去离子水共30m3对截留液进行洗涤,收集到40m3透出液,得到纯度较高的n
‑
乙酰氨基葡萄糖脱乙酰酶提取液,截留液排放至污水处理单元。
[0057]
(4)利用蒸汽对所述使用的生产设备和管道进行灭菌或消毒处理,防止生产过程中产生微生物污染,所述蒸汽的压强为0.3mpa,灭菌时间为20min。提取效果见表1。
[0058]
实施例3
[0059]
具体实施方式同实施例1,区别在于,对步骤(3)获得的12m3破壁悬液经过陶瓷微滤膜分离。微滤膜的孔径为0.2μm,操作压力为0.4mpa,操作过程的温度控制在4~10℃。当截留液体积约为8m3时,分3次间歇添加去离子水共24m3对截留液进行洗涤,收集到24m3透出液,得到纯度较高的n
‑
乙酰氨基葡萄糖脱乙酰酶提取液,截留液排放至污水处理单元。提取效果见表1。
[0060]
实施例4
[0061]
具体实施方式同实施例2,区别在于,对步骤(2)获得的20m3破壁悬液经过陶瓷微滤膜分离。微滤膜的孔径为0.1μm,操作压力为0.5mpa,操作过程的温度控制在4~30℃。当截留液体积约为10m3时,分3次间歇添加去离子水共25m3对截留液进行洗涤,收集到25m3透出液,得到纯度较高的n
‑
乙酰氨基葡萄糖脱乙酰酶提取液,截留液排放至污水处理单元。提取效果见表1。
[0062]
表1采用不同工艺的n
‑
乙酰氨基葡萄糖脱乙酰酶提取效果
[0063][0064]
实施例5
[0065]
具体实施方式同实施例1,区别在于,用聚丙烯酰胺、二甲基胺
‑
表氯醇共聚物、聚合氯化铁、氯化铁、硫酸亚铁中的一种或两种以上的组合替换实施例1中的絮凝剂硫酸铁;
[0066]
其中,絮凝剂的添加方式为(a)或(b):
[0067]
(a)按如下剂量添加单一组分的絮凝剂:聚丙烯酰胺的添加量为原料中生物量干重的0.01~0.2%;二甲基胺
‑
表氯醇共聚物的添加量为生物量干重的0.01~0.1%;聚合氯化铁的添加量为生物量干重的0.1~2.0%;氯化铁的添加量为生物量干重的0.1~1.0%;硫酸铁的添加量为生物量干重的0.1~1.5%;硫酸亚铁的添加量为生物量干重的0.2~2.0%;
[0068]
(b)添加含有两种以上组分的絮凝剂时,每种絮凝剂的添加量为单一组分按照(a)所述用量的20
‑
50%。
[0069]
虽然本发明已以较佳实施例公开如上,但其并非用以限定本发明,任何熟悉此技术的人,在不脱离本发明的精神和范围内,都可做各种的改动与修饰,因此本发明的保护范围应该以权利要求书所界定的为准。