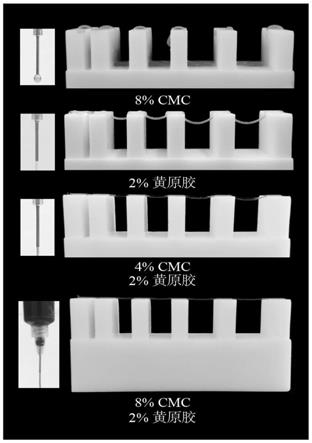
一种3d打印水凝胶及其制备方法
技术领域
1.本发明涉及一种3d打印水凝胶及其制备方法,属于材料科学领域。
背景技术:2.直写3d打印是一种通过气压或机械压力将材料通过注射器挤出并结合计算机程序制备特定结构的增材制造技术,在模具制造和生物工程等领域有着广泛的应用前景。理想的直写3d打印材料应该具备较好的打印精度和稳定性,在3d打印后通过热固或其他形式物理,化学变化使其形状可以长期稳定保持。
3.现阶段大多数直写3d打印后均采用热固方式获得稳定结构,少数使用光交联技术实现3d打印墨水由溶液向凝胶的转变。
技术实现要素:4.[技术问题]
[0005]
在现有的3d打印直写光交联墨水中普遍存在所得到的3d打印结构较脆,缺乏弹性,在外力作用下易破碎,并且其往往存在一定的细胞毒性,不能满足生物工程及医疗卫生领域的应用需求。而且现有直写3d打印得到的生物材料普遍存在机械性能较差、打印精度不高的问题。
[0006]
[技术方案]
[0007]
为了解决上述至少一个问题,本发明以gelma为光交联组分,加入黄原胶和羧甲基纤维素钠cmc作为打印性能调解组分,得到3d打印的墨水;而且本发明得到的3d打印墨水在满足理想打印性能的同时没有显著降低其gelma的光交联效率,充分利用了gelma较好的生物相容性和光交联效率高的优势,同时借助其他组分的优势改善了gelma水凝胶脆性、易碎的不足,并赋予其理想的打印精度。
[0008]
本发明的第一个目的是提供一种3d打印墨水,其组分包括:gelma、黄原胶、cmc、光引发剂、水,其中gelma、黄原胶、cmc、光引发剂的质量比为5~20:1.5~2.5:7~10:0.5~1:100。
[0009]
在本发明的一种实施方式中,所述的gelma、黄原胶、cmc、光引发剂、水的质量比为15:2:8:0.5:100。
[0010]
在本发明的一种实施方式中,所述的gelma的制备方法为:
[0011]
将明胶溶于水中,溶胀;随后向溶液中滴加甲基丙烯酸酐进行反应,反应结束后加水终止反应,透析、干燥,得到甲基丙烯酸酰化明胶gelma。
[0012]
在本发明的一种实施方式中,所述的gelma的制备方法具体为:
[0013]
取10g明胶,溶于100ml水中,溶胀1小时,随后在50℃下向溶液中滴加甲基丙烯酸酐6ml,反应3h后使用400ml水稀释溶液终止反应,使用截留分子量8000~15000的透析袋在50℃条件下透析3天,期间每6h更换水,最后将溶液冷冻干燥2天,得到甲基丙烯酸酰化明胶gelma。
[0014]
在本发明的一种实施方式中,所述的光引发剂包括2
‑
羟基
‑2‑
甲基
‑1‑
[4
‑
(2
‑
羟基乙氧基)苯基]
‑1‑
丙酮(irgacure 2959)、苯基
‑
2,4,6
‑
三甲基苯甲酰基膦酸锂光引发剂。
[0015]
本发明的第二个目的是提供一种制备本发明所述的3d打印墨水的方法,包括如下步骤:
[0016]
将gelma、黄原胶、cmc、光引发剂、水按照质量比混合均匀即可得到3d打印墨水。
[0017]
在本发明的一种实施方式中,所述混合均匀的温度不能低于20℃。
[0018]
本发明的第三个目的是提供一种制备3d打印水凝胶的方法,所述方法是将本发明所述的3d打印墨水在365nm、10w的紫外光,距离为8
‑
12cm的条件下照射15min以上。
[0019]
本发明的第四个目的是本发明所述的方法制备得到的3d打印水凝胶。
[0020]
本发明的第五个目的是一种制备3d打印模型的方法,包括如下步骤:
[0021]
将本发明所述的3d打印墨水进行3d打印得到3d打印模型。
[0022]
在本发明的一种实施方式中,所述的3d打印的参数为:
[0023]
针头直径0.5mm,压力180~200千帕,打印速度2mm/s,每层提升高度0.5mm,打印尺寸20.0
×
20.0mm,间距1.5mm。
[0024]
在本发明的一种实施方式中,打印得到3d模型之后需要放置在365nm、10w的紫外光,距离为8
‑
12cm的条件下照射15min以上,得到固形的效果。
[0025]
本发明的第六个目的是本发明所述的方法得到的3d打印模型。
[0026]
[有益效果]
[0027]
(1)本发明以gelma为光交联组分,加入黄原胶和cmc作为打印性能调解组分,在满足理想打印性能的同时没有显著降低其gelma的光交联效率。
[0028]
(2)本发明以gelma为主要光交联组分充分利用了其较好的生物相容性和光交联效率高的优势,同时借助其他组分的优势改善了gelma水凝胶脆性、易碎的不足,并赋予其理想的打印精度。
附图说明
[0029]
图1为黄原胶浓度对3d打印性能的影响。
[0030]
图2为实施例1、对照例3~5得到的3d打印墨水的打印效果。
[0031]
图3为实施例1的墨水制备的固形后打印模型,其中,(a)为立体图;(b)为俯视图。
[0032]
图4为实施例1的墨水制备的固形后打印模型的弹性测试。
[0033]
图5为实施例1的墨水制备的固形后打印模型的网格截面。
[0034]
图6为黄原胶用量对于固形后的3d打印网格截面空隙面积的影响。
[0035]
图7为黄原胶浓度对3d打印墨水中光交联效率的影响。
[0036]
图8为cmc用量对于固形后3d打印网格截面空隙面积的影响。
[0037]
图9为cmc浓度对3d打印墨水中光交联效率的影响。
[0038]
图10为对照例7的测试结果。
具体实施方式
[0039]
以下对本发明的优选实施例进行说明,应当理解实施例是为了更好地解释本发明,不用于限制本发明。
[0040]
实施例中3d打印的参数为:
[0041]
针头直径0.7mm,压力180~200千帕,打印速度2mm/s,每层提升高度0.5mm,打印尺寸20.0
×
20.0mm,间距1.0mm。
[0042]
实施例1
[0043]
一种制备3d打印墨水的方法,包括如下步骤:
[0044]
将gelma、黄原胶、cmc、光引发剂irgacure 2959、水按照质量比为15:2:8:0.5:100,混合均匀,即得到3d打印墨水。
[0045]
对照例1黄原胶用量的优化
[0046]
调整实施例1中gelma、黄原胶、cmc、光引发剂irgacure 2959、水的质量比为15:1:8:0.5:100;其他和实施例1保持一致,得到3d打印墨水。
[0047]
对照例2黄原胶用量的优化
[0048]
调整实施例1中gelma、黄原胶、cmc、光引发剂irgacure 2959、水的质量比为15:3:8:0.5:100;其他和实施例1保持一致,得到3d打印墨水。
[0049]
将实施例1和对照例1、2得到的3d打印墨水进行3d打印,得到的3d打印模型;3d打印模型的测试结果如下:
[0050]
图1为黄原胶浓度对3d打印性能的影响。从图1可以看出:在使用黄原胶进行3d打印性能调节的过程中发现:低浓度(黄原胶相对于水的质量浓度为1%)的黄原胶制备的3d打印墨水的清晰度较差,没有办法形成结构精度较高的3d打印结构。而高浓度(黄原胶相对于水的质量浓度为3%)的黄原胶会导致溶液粘度过大,影响打印连续性。适当浓度的黄原胶(黄原胶相对于水的质量浓度为2%)具有相对较好的3d打印清晰度,打印过程稳定连续。
[0051]
对照例3
[0052]
省略实施例1中的黄原胶,其他和实施例1保持一致,得到3d打印墨水。
[0053]
对照例4
[0054]
省略实施例1中的cmc,其他和实施例1保持一致,得到3d打印墨水。
[0055]
对照例5
[0056]
调整实施例1中的gelma、黄原胶、cmc、光引发剂irgacure 2959、水的质量比为15:2:4:0.5:100,其他和实施例1保持一致,得到3d打印墨水。
[0057]
将实施例1和对照例3~5得到的3d打印墨水进行打印,结果如下:
[0058]
图2为实施例1、对照例3~5得到的3d打印墨水的打印效果。从图2可以看出:单一使用cmc(对照例3)作为打印性能调节剂无法得到连续的打印线条,墨滴从针头挤出为独立的小墨滴。单一使用黄原胶制备的3d打印墨水(对照例4)虽然可以制备连续稳定的线条,但是其存在明显的塌缩现象,这在实际应用之中将会造成所制备的3d打印结构迅速坍塌,同样影响了3d打印的精度。将两者共同引入3d打印墨水配方所制备的墨水经过3d打印形成的线条没有表现出明显的塌缩性能,并在gelma、黄原胶、cmc、光引发剂irgacure 2959、水的质量比为15:2:8:0.5:100的时候获得较理想的打印性能。
[0059]
将实施例1的墨水制备得到的3d打印模型在365nm、10w的紫外光,距离为10cm的条件下照射15min,得到固形后的3d打印模型。
[0060]
图3为实施例1的墨水制备的固形后打印模型,从图3可以看出:打印模型的打印层数为14层,观察到其没有出现显著的塌缩现象;从俯视图中可以观察到样品的网格结构清
晰,没有出现空隙被阻塞的情况。
[0061]
图4为实施例1的墨水制备的固形后打印模型的弹性测试,从图4可以看出:实施例1的3d打印模型可以较大程度弯曲,14层网格结构可以弯曲到41
°
并恢复,没有出现明显的结构损伤。这说明实施例1制备的3d打印产品具有一定的弹性,在发生形变后可以恢复。这一优势提升了该材料在生物工程等领域的应用潜力。
[0062]
图5为实施例1的墨水制备的固形后打印模型的网格截面。具体测试方法是通过使用超景深显微镜拍摄并测量3d打印网格结构的截面空隙情况,将制备的网格结构的截面空隙情况与参数设计后应该获得的空隙面积理论值对比,每个样品取9个空隙,计算平均值(如图5)。这一参数可以有效反应墨水的塌缩性能和其3d打印的精度,空隙相较于理论值越低,则说明该墨水易塌缩,没有办法获得清晰地多层3d打印结构,反之亦然。
[0063]
实施例2黄原胶用量的优化
[0064]
一种制备3d打印墨水的方法,包括如下步骤:
[0065]
将gelma、黄原胶、光引发剂irgacure 2959、水按照质量比为10:2:0.5:100、10:2:1:100、10:2:2:100、10:2:3:100、10:2:4:100、10:2:5:100,混合均匀,即得到3d打印墨水。
[0066]
将实施例2得到的3d打印墨水进行打印,得到3d打印模型,之后3d打印模型在365nm、10w的紫外光,距离为10cm的条件下照射15min,得到固形后的3d打印模型(3d打印水凝胶),再进行性能测试,结果如下:
[0067]
图6为黄原胶用量对于固形后的3d打印网格截面空隙面积的影响。从图6可以看出:实施例2所得固形后的3d打印网格截面空隙在黄原胶相对于水的质量浓度1%即可具有明显空隙,而在2%时达到67%,后续继续提升黄原胶浓度,空隙面积提升相对较小,这说明黄原胶的引入可以显著改善墨水的3d打印清晰度,浓度越高提升效果越明显。
[0068]
图7为黄原胶浓度对3d打印墨水光交联效率的影响。从图7可以看出:随着黄原胶浓度的提升,形成水凝胶所需的光交联时间逐渐延长。黄原胶浓度为2%的时候,水凝胶可以在15min内完成光交联,形成稳定的水凝胶。黄原胶本身是具有淡黄色的,而光交联的过程中如果溶液是有颜色的,会降低光的利用率,导致光交联形成凝胶的时间变长。
[0069]
实施例3cmc用量的优化
[0070]
一种制备3d打印墨水的方法,包括如下步骤:
[0071]
将gelma、黄原胶、cmc、光引发剂irgacure 2959、水按照质量比为10:2:1:0.5:100、10:2:2:0.5:100、10:2:3:0.5:100、10:2:4:0.5:100、10:2:5:0.5:100、10:2:6:0.5:100、10:2:7:0.5:100、10:2:8:0.5:100、10:2:9:0.5:100、10:2:10:0.5:100,混合均匀,即得到3d打印墨水。
[0072]
将实施例2得到的3d打印墨水进行打印,得到3d打印模型,之后3d打印模型在365nm、10w的紫外光,距离为10cm的条件下照射15min,得到固形后的3d打印模型,再进行性能测试,结果如下:
[0073]
图8为cmc用量对于固形后的3d打印网格截面空隙面积的影响。从图8可以看出:实施例3所得固形后的3d打印网格截面空隙随着cmc浓度的增加呈现持续增长的趋势,当cmc相对于水的质量浓度超过8%,增长则相对较小,所以该浓度被选为优化配比。
[0074]
图9为cmc浓度对3d打印墨水中光交联效率的影响。从图9可以看出:cmc浓度的提升不会显著影响溶液的光交联效率,主要原因可能是由于cmc溶液呈现无色透明状,不会影
响光交联过程中对于光的有效利用。
[0075]
对照例6
[0076]
调整实施例1中的黄原胶为“卡拉胶”,其他和实施例1保持一致,得到3d打印墨水。
[0077]
将得到的3d打印墨水进行性能测试,测试结果如下:
[0078]
在高温(60℃)环境下,卡拉胶在高温(60℃)会产生可逆的凝胶化现象,而且粘度调节作用较差,无法获得很好的清晰度。
[0079]
对照例7
[0080]
调整实施例1中的黄原胶为“海藻酸钠”、“壳聚糖”,其他和实施例1保持一致,得到3d打印墨水。
[0081]
将得到的3d打印墨水进行性能测试,测试结果如下:
[0082]
如图10,将黄原胶替换为壳聚糖后,所打印得到的线条中有部分凝胶颗粒,这可能是由于壳聚糖在溶液配制过程中自身形成的微凝胶,严重影响了打印线条的精度,同时其塌缩明显。而海藻酸钠同样出现了显著的塌缩,这说明达黄原胶在对于3d打印清晰度有着至关重要的作用,海藻酸钠等常见多糖大分子无法将其取代。