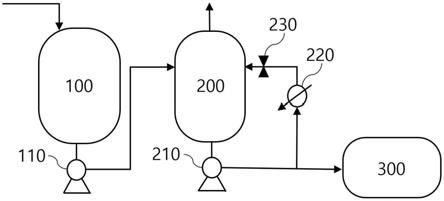
1.相关申请的交叉引用
2.本技术要求于2020年7月22日提交的韩国专利申请第10-2020-0091151号和2020年12月24日提交的韩国专利申请第10-2020-0183357号的优先权的权益,其全部内容作为说明书的一部分并入本文中。
3.技术领域
4.本发明涉及一种回收溶剂的方法及溶剂回收设备,更具体地,涉及一种从通过溶液聚合制备的聚合物溶液回收溶剂的方法及溶剂回收设备。
背景技术:5.溶液聚合是通过将单体溶解在适当的溶剂中而在溶液状态下进行的聚合方法,并且用于自由基聚合和离子聚合中。作为通过溶液聚合制备聚合物的代表性示例,可以包括通过苯乙烯和丁二烯的阴离子聚合反应制备苯乙烯-丁二烯共聚物。通常将正丁基锂用作阴离子聚合引发剂,并将环己烷用作溶剂。
6.这样,在阴离子聚合完成之后,获得状态为聚合物溶解或分散在溶剂中的聚合物溶液,并且为了获得固相聚合物产物,基本上执行以下回收聚合物溶液中的溶剂的过程。聚合完成后,将聚合溶液转移到减压排料罐中,并利用聚合反应的余热将一部分溶剂作为气体回收。将具有较高聚合物组成的聚合物溶液转移到蒸汽汽提处理单元中,并且在蒸汽汽提处理单元中,使溶液与蒸汽直接接触以回收作为气体的溶剂,从而使聚合物中的残留溶剂减至最少。通过汽提在固相中获得的聚合物与水一起转移到制造过程中以获得粒料。
7.然而,在蒸汽汽提过程中,引入了大量的蒸汽,从而在聚合物制备过程中消耗了大部分能量。引入的蒸汽量取决于引入到蒸汽汽提处理单元中的溶剂的量,并且当蒸汽的量不足时,聚合物中残留的溶剂的量增加,从而增加了随后的制造过程中的气体溶剂处理成本,并且产生对产物有不利影响的问题,例如聚合物的总挥发性有机化合物(tvoc)的增加。
技术实现要素:8.技术问题
9.本发明的目的是减少聚合物制备过程中使用的能量,同时使引入制造过程中的残留溶剂减至最少,以便解决背景技术中提到的问题。
10.即,本发明的目的是提供一种回收溶剂的方法和溶剂回收设备,其在聚合物溶液的蒸汽汽提处理之前使用分离器和加热装置使聚合物溶液中的溶剂挥发,以减少蒸汽汽提处理中使用的蒸汽量,从而减少聚合物制备过程中使用的能量,同时使引入制造过程中的残留溶剂减至最少。
11.技术方案
12.在一个总的方面,一种回收溶剂的方法包括:将包括一种或多种单体以及溶剂的聚合反应物供应给反应器以获得聚合物溶液(s10);将包括聚合物溶液的流供应给分离器
以分离包括作为气相的溶剂的上部排出流和包括聚合物溶液的下部排出流(s20);以及通过加热装置将从来自分离器的下部排出流的一部分分流的分支流加热,并使分支流回流到分离器,并且将包括来自分离器的下部排出流的残余物的残余物流供应给蒸汽汽提处理单元(s30),其中,通过压力调节阀调节在被加热装置加热后回流到分离器的分支流的蒸汽质量分数。
13.在另一个示例性实施例中,一种聚合物制备设备包括:反应器,被供给包括一种或多种单体以及溶剂的聚合反应物,并且排出包括通过聚合反应物的聚合而获得的聚合物溶液的流;分离器,被供给从反应器中排出的流,并且排出包括作为气相的溶剂的上部排出流和包括聚合物溶液的下部排出流;加热装置,将从来自分离器的下部排出流的一部分分流的分支流加热,以使分支流回流到分离器;压力调节阀,调节被加热装置加热后回流到分离器的分支流的蒸汽质量分数;以及蒸汽汽提处理单元,被供给包括来自分离器的下部排出流的残余物的残余物流,并且使聚合物溶液中的溶剂挥发。
14.有益效果
15.根据本发明的回收溶剂的方法和溶剂回收设备可以提供一种回收溶剂的方法和一种溶剂回收设备,其中在聚合物溶液的蒸汽汽提过程之前,使用分离器和加热装置使聚合物溶液中的溶剂挥发,以减少蒸汽汽提过程中使用的蒸汽量,从而减少聚合物制备过程中使用的能量,同时最大程度地减少引入制造过程中的残留溶剂。
附图说明
16.图1是示出根据本发明示例性实施例的回收溶剂的方法的工艺流程图。
17.图2是示出根据本发明的比较例1的回收溶剂的方法的工艺流程图。
18.图3是示出根据本发明的比较例2的回收溶剂的方法的工艺流程图。
具体实施方式
19.基于发明人能够适当地定义术语的概念以便以最佳方式描述他们自己的发明的原则,在本发明的说明书和权利要求书中使用的术语和词语不应被限制性地解释为具有一般或词典的含义,而应被解释为具有符合本发明的技术思想的含义和概念。
20.在本发明中,术语“上部”是指对应于容器或设备的总高度的50%以上的高度的部分,术语“下部”是指对应于小于容器或设备的总高度的50%的部分。
21.在本发明中,术语“流”可以指过程中的流体流,或者可以指在管道中流动的流体本身。具体地,“流”既可以指在连接每个设备的管道中流动的流体本身,也可以指流体流。另外,流体可以指气体或液体。
22.在下文中,将参考图1更详细地描述本发明,以便更好地理解本发明。
23.根据本发明的示例性实施例,提供了一种回收溶剂的方法。该回收溶剂的方法包括:将包括一种或多种单体以及溶剂的聚合反应物供应给反应器100以获得聚合物溶液(s10);将包括聚合物溶液的流供应给分离器200,以分离包括气相形式的溶剂的上部排出流和包括聚合物溶液的下部排出流(s20);以及通过加热装置220将从来自分离器200的下部排出流的一部分分流的分支流加热,并使分支流回流到分离器200,并且将包括来自分离器的下部排出流的残余物的残余物流供应给蒸汽汽提处理单元300(s30),其中可以通过压
力调节阀230调节在被加热装置220加热之后回流到分离器200的分支流的蒸汽质量分数。
24.根据本发明的示例性实施例,s10可以是如下步骤:将包括一种或多种单体和溶剂的聚合反应物供应给反应器100以获得聚合物溶液,该聚合物溶液包括通过一种或多种单体在溶剂中的聚合反应形成的聚合物。这样获得的聚合物溶液可以经过稍后描述的用于制造的溶剂回收的步骤,从而获得固相聚合物。
25.一种或多种单体可以包括:芳族乙烯基单体,该芳族乙烯基单体包括选自由苯乙烯、α-甲基苯乙烯、3-甲基苯乙烯、4-甲基苯乙烯、4-丙基苯乙烯、异丙烯基萘、1-乙烯基萘、被具有1至3个碳原子的烷基取代的苯乙烯、4-环己基苯乙烯、4-(对甲基苯基)苯乙烯和被卤素取代的苯乙烯组成的组中的一种或多种;以及共轭二烯基单体,该共轭二烯基单体包括选自由1,3-丁二烯、1,4-丁二烯、2,3-二甲基-1,3-丁二烯、2-乙基-1,3-丁二烯、1,3-戊二烯、间戊二烯、3-丁基-1,3-辛二烯、2-苯基-1,3-丁二烯和异戊二烯组成的组中的一种或多种。作为示例,一种或多种单体可以包括苯乙烯和丁二烯,因此,通过聚合反应产生的聚合物可以是苯乙烯-丁二烯共聚物。
26.溶剂可以包括选自由环己烷、n,n-二甲基甲酰胺、n,n-二甲基乙酰胺、n-甲基-2-吡咯烷酮、n-环己基-2-吡咯烷酮、n-甲基-ε-己内酰胺、1,3-二烷基-2-咪唑啉酮、四甲基脲和六甲基磷酸三酰胺(hexamethylphosphosphoric triamide)组成的组中的一种或多种。作为示例,有机溶剂可以包括环己烷。在这种情况下,可以容易地进行苯乙烯-丁二烯共聚物的聚合。
27.聚合反应可以通过进一步包含例如离子交换水、引发剂、分子量调节剂、活化剂和氧化还原催化剂的添加剂来进行。
28.引发剂可以包括例如选自由叔丁基锂、过氧化氢二异丙苯、叔丁基过氧化氢、过氧化氢异丙苯(cumene hydroperoxide)、过氧化氢对薄荷烷(p-menthane hydroperoxide)、过氧化二叔丁基、过氧化叔丁基异丙苯(t-butylcumyl peroxide)、过氧化乙酰、过氧化异丁酯、过氧化辛酰(octanoylperoxide)、过氧化二苯甲酰、过氧化3,5,5-三甲基己醇和过氧化叔丁基异丁酯组成的组中的一种或多种。
29.作为分子量调节剂,可以使用例如选自由α-甲基苯乙烯二聚体、叔十二烷基硫醇(t-dodecylmercaptan)、正十二烷基硫醇、辛基硫醇、四氯化碳、二氯甲烷、二溴甲烷、二硫化四甲基秋兰姆(tetramethyl diuram disulfide)、二硫化双亚戊基秋兰姆(dipentamethylene diuram doisulfide)、二异丙基黄原二硫化物(diisopropylxanthogen disulfide)组成的组中的一种或多种。
30.作为活化剂,可以使用选自由连二亚硫酸钠、甲醛次硫酸氢钠、乙二胺四乙酸钠、硫酸亚铁、乳糖、葡萄糖、亚麻酸钠和硫酸钠组成的组中的一种或多种。
31.作为氧化还原催化剂,可以使用选自由甲醛次硫酸氢钠、硫酸亚铁、乙二胺四乙酸二钠和硫酸铜组成的组中的一种或多种。
32.添加剂不限于以上所描述的那些,并且还可以使用用于聚合反应的常用添加剂。作为具体示例,正丁基锂可以用作引发剂。在这种情况下,可以容易地进行苯乙烯-丁二烯共聚物的聚合。
33.根据本发明的示例性实施例,除了所述组成以外,如果需要,还可以在不损害共聚物的物理特性的范围内引入添加剂,例如活化剂、螯合剂、分散剂、ph调节剂、脱氧剂、粒径
调节剂、抗老化剂、抗氧化剂、消泡剂和除氧剂。
34.根据本发明的示例性实施例,在如本文所述的s10之后且s20之前,还可以包括将聚合物溶液供应到排料罐(未示出)并且利用聚合反应的余热排出气相形式的溶剂的步骤。由于聚合反应的余热残留在供应给排料罐(未示出)的聚合物溶液中,因此聚合物溶液中的溶剂可以在减压条件下以气相回收,其中排料罐(未示出)中不供应单独的蒸汽。回收的溶剂被供应给纯化单元(未示出),并且部分地去除了溶剂的聚合物溶液被排出到下部,并且可以进行稍后描述的以下步骤以进一步回收溶剂。
35.常规方法包括通过将从排料罐(未示出)排出的部分地去除了溶剂的聚合物溶液直接供应到蒸汽汽提处理单元300中并回收与蒸汽接触的气相形式的溶剂来获得固相聚合物。然而,在这种情况下,大量的蒸汽被引入到蒸汽汽提处理单元300中,使得能量消耗很高。引入到蒸汽汽提处理单元300中的蒸汽量取决于引入到蒸汽汽提处理单元300中的聚合物溶液中的溶剂的量,并且当引入的蒸汽量不足时,残留在固相聚合物中的溶剂的量增加,这使在随后的制造处理单元中对气相溶剂的处理成本增加,并且产物受到不利影响,例如聚合物的总挥发性有机化合物(tvoc)的增加。
36.因此,在本发明中,在聚合物溶液的蒸汽汽提处理之前,可以使用分离器200和加热装置220使聚合物溶液中的溶剂挥发,从而使引入到随后的制造过程中的残留溶剂最少,并减少蒸汽汽提处理单元300中使用的蒸汽量,因此,在该回收溶剂的方法中,减少了在聚合物制备工艺中使用的能量。
37.即,根据本发明,可以将来自反应器100的排出流供应给分离器200,或者可以使来自反应器100的排出流通过排料罐(未示出),然后供应给分离器200。具体地,在本发明中,可以在s10之后执行s20和s30。
38.根据本发明的示例性实施例,s20可以是将来自反应器100的包括聚合物溶液的排出流供应给分离器200,以分离包括气相形式的溶剂的上部排出流和包括聚合物溶液的下部排出流的步骤。这样,来自反应器100的排出流中包括的聚合物溶液可以在通过分离器200的同时作为下部排出流中聚合物浓度增大的聚合物溶液排出。
39.根据本发明的示例性实施例,s30是将来自分离器200的下部排出流供应给蒸汽汽提处理单元300的步骤,并且包括通过加热装置220将从来自分离器200的下部排出流的一部分分流的分支流加热然后使该分支流回流到分离器200,以及将包括来自分离器200的下部排出流的残余物的残余物流供应给蒸汽汽提处理单元300。在此,可以通过压力调节阀230来调节通过加热装置220加热然后回流到分离器200的分支流的蒸汽质量分数。具体地,压力调节阀230可以用于调节分支流的蒸汽质量分数,直到从下部排出流的一部分分流的分支流被加热装置220加热然后回流到分离器200为止。在此,蒸汽质量分数可以指在包括液体和蒸汽的流中蒸汽与液体和蒸汽的重量比。即,可以通过调节压力调节阀230的打开关闭程度来调节在被加热装置220加热之后直到回流到分离器200的分支流的蒸汽质量分数。
40.更具体地,压力调节阀230可以在分支流被加热装置220加热之后并且分支流通过压力调节阀230之前调节分支流的蒸汽质量分数。即,可以在分支流被加热装置220加热之后并且在分支流通过压力调节阀230之前调节在分支流中的蒸汽与液体和蒸汽的重量比。在此,可以通过压力调节阀230将在分支流被加热装置220加热之后并且在分支流通过压力调节阀230之前的分支流的蒸汽质量分数调节为0至5重量%、0至2重量%或0重量%。在该
蒸汽质量分数范围内,由于具有调节后的蒸汽质量分数的分支流以包括最小量气体的液态存在,因此分支流可具有优异的传热效率以改进分离器200的溶剂挥发能力,并且还可以防止其中分支流被蒸发以堵塞加热装置220的结垢现象。
41.另外,对分离器200的分支流加热的加热装置220可以是热交换器,即再沸器。
42.作为在加热装置220中使用的热源,可以使用高温蒸汽,并且可以通过从蒸汽中获得热量来加热分离器200的分支流。在此,分离器不具有溶剂挥发功能,并且由于通过加热装置220而被加热的分支流回流到分离器200中,因此可以通过提高在分离器200中存在的聚合物溶液的温度来使溶剂挥发。在管道和分离器200内部,在流通过压力调节阀230之后,分支流的蒸汽质量分数趋于增大。这样,具有增大的蒸汽质量分数的分支流可以在回流到分离器200中的同时被喷射到分离器200中,因此,热量可以被均匀地传递到存在于分离器200内部的聚合物溶液中。
43.挥发的溶剂被回收并供应给纯化单元(未示出),并且聚合物浓度增大的聚合物溶液被排出到下部,并经过以下的后续步骤来进一步回收溶剂。
44.根据本发明的示例性实施例,在s30中,从来自分离器的下部排出流分流并回流到分离器的分支流相对于来自分离器200的下部排出流的总流量的流量比可以为80%至90%。
45.当分支流的流量比为80%以上时,可以使引入到随后的蒸汽汽提处理单元300中的流中残留的溶剂的量减至最少,从而获得具有高纯度的最终获得的固相聚合物产物。同时,当分支流的流量比为90%以下时,防止了回流到分离器200的流的温度过度降低,即,可以防止加热装置220中所需的蒸汽量过多。因此,因为容易进行存在于分离器200中的聚合物溶液中的溶剂的挥发,所以可以减少在随后的蒸汽汽提处理单元300中消耗的蒸汽量,并且防止了分支流的量被过多地引入分离器200并从分离器200中排出,因此,防止了由于液压不稳定和压差增加而引起的管道中的结垢现象。
46.例如,该比率可以是80%至95%、80%至90%、85%至90%或88%至90%。当在聚合期间将环己烷用作溶剂并且将酚基、硫基或磷基抗氧化剂用作添加剂时,防止了通过加热装置220并回流到分离器200的分支流的温度在该范围内过度降低,因此,可以容易地发挥溶剂中的抗氧化剂的作用。因此,可以防止最终获得的固相聚合物的变色,从而获得具有高质量和高纯度的产物。
47.作为示例,抗氧化剂可以是选自由丁羟甲苯(butylated hydroxyl toluene)、三(壬苯基)亚磷酸酯(tris(nonylphenyl)phosphite)、n,n-1,6-己二基双[3,5-双(1,1-二甲基乙基)-4-羟苯基丙酰胺](n,n-1,6-hexanediylbis[3,5-bis(1,1-dimethylethyl)-4-hydoxyphenylpropanaimd])和(十八烷基-3-[3,5-二叔丁基-4-羟基苯基]丙酸酯)组成的组中的一种或多种。
[0048]
根据本发明的示例性实施例,在s30中,从分离器200供应给蒸汽汽提处理单元300的下部排出流中的聚合物溶液的聚合物浓度可以为20至40重量%、30至40重量%或35至40重量%。即,从分离器200供应给蒸汽汽提处理单元300的残余物流中的聚合物溶液的聚合物浓度可以为20至40重量%、30至40重量%或35至40重量%。
[0049]
当聚合物溶液的聚合物浓度为20重量%以上时,可以使供应给蒸汽汽提处理单元的流中的聚合物溶液的溶剂量减至最少,以获得具有高纯度的最终获得的固相聚合物产
物,并减少在随后的蒸汽汽提处理单元300中消耗的蒸汽量。同时,当聚合物溶液的聚合物浓度为40重量%以下时,可以防止由于聚合物沉淀在将加热装置220和分离器200以及蒸汽汽提处理单元300连接的管道中而造成的结垢现象,从而使热交换效率和溶剂回收效率优异。
[0050]
作为具体示例,供应给加热装置220的流的流量与来自反应器100的排出流(在通过排料罐时,来自排料罐的下部排出流)中的聚合物溶液中包括的溶剂的流量之比可以为0.005至0.110、0.017至0.110或0.052至0.110,并且在该范围内,可以容易地将聚合物溶液的聚合物浓度调节至上述范围。
[0051]
根据本发明的示例性实施例,在s30中,供应给蒸汽汽提处理单元300的来自分离器200的下部排出流中的聚合物溶液的粘度可以为1000至10000cp、1000至8000cp或1000至5000cp。即,供应给蒸汽汽提处理单元的分离器的残余物流中的聚合物溶液的粘度可以为1000至10000cp、1000至8000cp或1000至5000cp。
[0052]
当聚合物溶液的粘度为1000cp以上时,可以使供应给蒸汽汽提处理单元的流中的聚合物溶液的溶剂量减至最少,以获得具有高纯度的最终获得的固相聚合物产物,并减少在随后的蒸汽汽提处理单元300中消耗的蒸汽量。同时,当聚合物溶液的粘度为10000cp以下时,可以防止由于聚合物在将加热装置220和分离器200以及蒸汽汽提处理单元300连接的管道中积聚而产生的结垢现象,从而可以防止分离器200的操作停止。
[0053]
例如,当来自反应器100的排出流中的聚合物溶液的粘度为100至1000cp时,在溶剂在分离器200中挥发之后,从分离器200的下部排出的下部排出流中的聚合物溶液的聚合物浓度可以为20至40重量%,而聚合物溶液的粘度为1000至10000cp。在此,假设在分离器200内部保持稳定状态,则分离器200内部包含的聚合物溶液与来自分离器200的下部排出流中包含的聚合物溶液的聚合物浓度和粘度可以相同。
[0054]
同时,例如,从反应器100排出的包括聚合物溶液的流不是供应给根据本发明的分离器200而是供应给普通的蒸馏塔,可能不容易排出聚合物浓度和粘度在上述范围内的聚合物溶液。即使有意使用蒸馏塔通过溶剂挥发来排出聚合物浓度和粘度在上述范围内的聚合物溶液,也会由于设有塔盘或填充床的普通蒸馏塔的复杂内部结构而发生聚合物沉淀或积聚引起的结垢现象,使得聚合物溶液不能很好地流动,并且驻留时间可能局部不同,从而使传热效率劣化。因此,排出的聚合物溶液中的聚合物的物理特性可能受到不利影响。
[0055]
同样地,当将从反应器100排出的包括聚合物溶液的流供应给普通蒸馏塔,而不是根据本发明的分离器200,以使聚合物溶液中的溶剂挥发时,因为如上所述蒸馏塔的复杂内部结构引起聚合物沉淀或积聚造成结垢现象可能导致各种问题,因此,当使来自蒸馏塔的下部排出流回流时,即使在使用压力调节阀230调节回流的下部排出流的蒸汽质量分数的情况下,也不能表现出与本发明相同或相似的效果。
[0056]
根据本发明的示例性实施例,在s30中,由加热装置220加热并回流到分离器200的分支流的温度可以为80至110℃。
[0057]
当回流的流的温度为80℃以上时,防止了回流到分离器200的分支流的温度过度降低,从而使在分离器200中存在的聚合物溶液中的溶剂的挥发能够容易地进行,由此减少了在随后的蒸汽汽提处理单元300中消耗的蒸汽量。同时,当回流的分支流的温度为110℃以下时,可以使引入到随后的蒸汽汽提处理单元300中的流中残留的溶剂的量减至最少,从
而获得具有高纯度的最终获得的固相聚合物产物。
[0058]
例如,回流的分支流的温度可以为80至110℃、85至105℃或90至100℃。当在聚合期间将环己烷用作溶剂并且将酚基、硫基或磷基抗氧化剂用作添加剂时,防止了通过加热装置220并回流至分离器200的分支流的温度在该范围内过度降低,因此,可以容易地发挥溶剂中的抗氧化剂的作用。因此,可以防止最终获得的固相聚合物的变色,从而获得具有高质量和高纯度的产物。
[0059]
根据本发明的示例性实施例,在s30之后,还可以包括从分离器200的供应给蒸汽汽提处理单元300的残余物流中挥发溶剂以获得固相聚合物(s40)。如上所述,在本发明中,在将排出流从反应器100供应给汽提处理单元300之前,来自反应器100的排出流通过分离器200和加热装置220以使聚合物溶液中的溶剂挥发,从而减少了在蒸汽汽提处理单元300中使用的蒸汽量,并且减少了在该工艺中使用的总能量的量。在汽提处理单元300中被挥发和回收的溶剂被供应给纯化单元(未示出),并且包括固相聚合物的流被排出到下部,并且可以经过以下的后续步骤来进一步回收溶剂。
[0060]
根据本发明的示例性实施例,根据本发明的回收溶剂的方法还可以包括在制造过程中将包括固相聚合物的下部排出流从蒸汽汽提处理单元300引入干燥器中,以排出残留溶剂(s50)。作为具体示例,在蒸汽汽提处理单元300中,用于转移固相聚合物的循环水(水)是循环的,并且可以在制造过程中将来自蒸汽汽提处理单元300的包括固相聚合物的下部排出流和循环水引入到干燥器,以将残留的溶剂和水分作为废气排出并丢弃,并获得最终的固相聚合物产物。
[0061]
根据本发明的示例性实施例,提供了一种溶剂回收设备。该溶剂回收设备可以包括:反应器100,被供给包括一种或多种单体和溶剂的聚合反应物,并且排出包括通过聚合反应物的聚合而获得的聚合物溶液的流;分离器200,被供给从反应器排出的流,并且排出包括气相形式的溶剂的上部排出流和包括聚合物溶液的下部排出流;加热装置220,将从来自分离器200的下部排出流的一部分分流的分支流加热,以使该流回流到分离器200;压力调节阀230,调节由加热装置加热后回流到分离器的分支流的蒸汽质量分数;以及蒸汽汽提处理单元300,被供给包括来自分离器200的下部排出流的残余物的残余物流,并使聚合物溶液中的溶剂挥发。
[0062]
根据本发明的示例性实施例,根据本发明的溶剂回收设备可以是用于根据本文所述的回收溶剂的方法执行处理的设备。
[0063]
根据本发明的示例性实施例,可以参考图1来描述根据本发明的溶剂回收设备。具体地,溶剂回收设备可以包括反应器100、分离器200、加热装置220、压力调节阀230和蒸汽汽提处理单元300。
[0064]
根据本发明的示例性实施例,反应器100可以被供给包括一种或多种单体和溶剂的聚合反应物,以获得包含通过一种或多种单体在溶剂中的聚合反应形成的聚合物的聚合物溶液。
[0065]
一种或多种单体和溶剂的种类可以与本文所述的回收溶剂的方法中使用的单体和溶剂的种类相同。
[0066]
聚合反应可以通过进一步包括离子交换水、引发剂、分子量调节剂、活化剂、氧化还原催化剂以及其他附加添加剂来进行。添加剂的种类可以与上述回收溶剂的方法中使用
的添加剂的种类相同。
[0067]
根据本发明的示例性实施例,根据本发明的溶剂回收设备还可以包括排料罐(未示出),该排料罐被供给来自反应器100的排出流,利用聚合反应的余热排出作为气相的溶剂,并将包括聚合物溶液的下部排出流排出到分离器200。由于聚合反应的余热残留在供应给排料罐(未示出)的聚合物溶液中,因此聚合物溶液中的溶剂可以在减压条件下以气相回收,其中排料罐(未示出)中不供应单独的蒸汽。回收的溶剂被供应给纯化单元(未示出),并且部分地去除了溶剂的聚合物溶液被排出到下部,并且可以被供应到用于进一步回收溶剂的设备。
[0068]
即,根据本发明,可以将来自反应器100的排出流供应给分离器200,或者可以使来自反应器100的排出流通过排料罐(未示出),然后供应给分离器200。
[0069]
根据本发明的示例性实施例,分离器200可以被供给来自反应器的排出流,并排出包括气相形式的溶剂的上部排出流和包括聚合物溶液的下部排出流。这样,来自反应器100的排出流中包括的聚合物溶液可以在通过分离器200的同时作为下部排出流中聚合物浓度增大的聚合物溶液排出。
[0070]
根据本发明的示例性实施例,加热装置220可以将从来自分离器200的下部排出流的一部分分流的分支流加热,以使该流回流到分离器。具体地,在将来自分离器200的下部排出流供应给随后的蒸汽汽提处理单元300的过程中,来自分离器200的下部排出流的一部分可分流,被加热装置220加热,然后回流到分离器,并且可以将包括来自分离器的下部排出流的残余物的残余物流供应给汽提处理单元300。在此,加热装置220可以是热交换器,即,再沸器。
[0071]
作为在加热装置220中使用的热源,可以使用高温蒸汽,并且可以通过从蒸汽中获得热量来加热来自分离器200的下部排出流的分支流。因此,从来自分离器200的下部排出流分流的分支流可以通过加热装置220,并以加热的状态回流到分离器200,从而使分离器200内部的聚合物溶液中包含的溶剂挥发。
[0072]
通过加热装置加热然后回流到分离器200的分支流可具有通过压力调节阀230调节的蒸汽质量分数。具体地,压力调节阀230可以用于在从来自分离器200的下部排出流的一部分分流的分支流被加热装置220加热之后并且在分支流通过压力调节阀230之前调节分支流的蒸汽质量分数。
[0073]
根据本发明的示例性实施例,蒸汽汽提处理单元300可以被供应给包括来自分离器200的下部排出流的残余物的残余物流,并使聚合物溶液中的溶剂挥发,从而获得固相聚合物。如本文所述,在本发明中,在将来自反应器100的排出流供应给蒸汽汽提处理单元300之前,可以使来自反应器100的排出流通过分离器200和加热装置220以使溶剂挥发,从而减少了在蒸汽汽提处理单元300中使用的蒸汽量,因此,减少了在该工艺中使用的总能量。
[0074]
根据本发明的示例性实施例,根据本发明的溶剂回收设备可以包括干燥器(未示出),该干燥器被供给来自蒸汽汽提处理单元300的包括固相聚合物的下部排出流并排出残留溶剂。干燥器(未示出)可以被包括在制造工艺(未示出)中。作为具体示例,在蒸汽汽提处理单元300中,用于转移固相聚合物的循环水(水)是循环的,并且可以在制造过程中将来自蒸汽汽提处理单元300的包括固相聚合物的排出流和循环水引入干燥器,以将残留溶剂和水分作为废气排出和丢弃,并获得最终的固相聚合物产物。
[0075]
根据本发明的示例性实施例,根据本发明的溶剂回收设备可以设置有反应器100、排料罐(未示出)、分离器200、加热装置220、压力调节阀230、蒸汽汽提处理单元300以及在制造工艺中连接干燥器(未示出)的管道,并且为了容易地将来自每个配置的下部排出流供应给随后的装置的配置,泵110或210(或未示出)可以进一步设置在管道上。
[0076]
根据本发明的示例性实施例,根据本发明的溶剂回收设备可以包括分离器200、泵210、加热装置220和压力调节阀230中的至少一个或多个。
[0077]
根据本发明的示例性实施例,在根据本发明的回收溶剂的方法和溶剂回收设备中,如果需要,还可以安装蒸馏塔(未示出)、冷凝器(未示出)、再沸器(未示出)、泵(未示出)、压缩机(未示出)、混合器(未示出)、分离装置(未示出)等。
[0078]
以上,已经描述并在附图中示出了根据本发明的回收溶剂的方法和溶剂回收设备,但是该描述和附图中图示仅是为了理解本发明的核心组成的描述和图示,除了以上描述和附图所示的方法和设备之外,未单独描述和图示的方法和设备可以适当地应用并用于实施根据本发明的回收溶剂的方法和溶剂回收设备。
[0079]
在下文中,将通过示例更详细地描述本发明。然而,提供以下示例是为了说明本发明。对于本领域技术人员显而易见的是,在不脱离本发明的范围和精神的情况下可以进行各种修改和变型,并且本发明的范围不限于此。
[0080]
《示例》
[0081]
示例1
[0082]
如图1所示的工艺流程图中所示,苯乙烯单体、丁二烯单体、作为溶剂的环己烷和作为引发剂的正丁基锂被供应至包括搅拌器和夹套(jacket)的反应器100中,并被聚合以获得完成了聚合的聚合物溶液。在此,聚合物溶液中的聚合物浓度为20重量%(5吨聚合物和20吨溶剂)。然后,排料罐(未示出)被供给来自反应器100的包括聚合物溶液的流,以利用残留的聚合物溶液的余热在减压条件下回收一部分气相形式的溶剂,并排出从中部分地去除了溶剂的聚合物溶液。在此,作为气相回收的该部分溶剂的量为2.8吨,并且从中部分去除了溶剂的聚合物溶液的浓度为22.5重量%。然后,将包括部分去除了溶剂的聚合物溶液的流从排料罐(未示出)转移到通过排出管线中的泵(未示出)连接的分离器200,以进一步使溶剂挥发从而获得具有增大的聚合物浓度的聚合物溶液。在此,分离器200中的溶剂的进一步挥发通过以下方式来进行:对从来自分离器200的下部排出流(其包括具有增大的聚合物浓度的聚合物溶液)的80%分流的分支流进行加热并使其回流到分离器200,将包括来自分离器200的下部排出流的残余物的残余物流供应给蒸汽汽提处理单元300,使用压力调节阀230将在被热交换器220加热之后并且通过压力调节阀230之前的分支流的蒸汽质量分数调节为0重量%。在此,供应给热交换器220的蒸汽量为0.3吨,进一步挥发的溶剂量为2.2吨,并且具有增大的聚合物浓度的聚合物溶液的浓度为25.0重量%。
[0083]
然后,将包括具有增大的聚合物浓度的聚合物溶液的残余物流转移到蒸汽汽提处理单元300,以通过直接蒸汽接触回收蒸汽和气相形式的溶剂,以获得固相聚合物。在此,蒸汽汽提处理单元300中使用的蒸汽量为12.0吨。然后,在制造过程中将固相聚合物与用于在蒸汽汽提处理单元300中转移固相聚合物的循环水(水)一起引入到干燥器(未示出),以将残留溶剂和水分作为废气排出并丢弃,并获得最终的固相聚合物产物。在此,在制造过程中引入到干燥器(未示出)中的固相聚合物中的残留溶剂为0.5重量%。
[0084]
示例2
[0085]
除了向热交换器220供应0.9吨的蒸汽以外,以与示例1相同的方式模拟了该过程。
[0086]
示例3
[0087]
除了向热交换器220供给1.3吨的蒸汽以外,以与示例1相同的方式模拟了该过程。
[0088]
示例4
[0089]
除了向热交换器220供给1.7吨的蒸汽以外,以与示例1相同的方式模拟了该过程。
[0090]
示例5
[0091]
除了向热交换器220供给1.9吨的蒸汽以外,以与示例1相同的方式模拟了该过程。
[0092]
示例6
[0093]
除了来自分离器200的下部排出流的90%分流、被热交换器220加热并且回流到分离器之外,以与示例3相同的方式模拟了该过程。
[0094]
示例7
[0095]
除了来自分离器200的下部排出流的90%分流、被热交换器220加热并且回流到分离器之外,以与示例4相同的方式模拟了该过程。
[0096]
示例8
[0097]
除了来自分离器200的下部排出流的90%分流、被热交换器220加热并且回流到分离器之外,以与示例5相同的方式模拟了该过程。
[0098]
示例9
[0099]
除了来自分离器200的下部排出流的95%分流、被热交换器220加热并且回流到分离器之外,以与示例3相同的方式模拟了该过程。
[0100]
示例10
[0101]
除了来自分离器200的下部排出流的95%分流、被热交换器220加热并且回流到分离器之外,以与示例4相同的方式模拟了该过程。
[0102]
示例11
[0103]
除了来自分离器200的下部排出流的95%分流、被热交换器220加热并且回流到分离器之外,以与示例5相同的方式模拟了该过程。
[0104]
比较例1
[0105]
如图2所示的工艺流程图中所示,苯乙烯单体、丁二烯单体、作为溶剂的环己烷和作为引发剂的正丁基锂被供应至包括搅拌器和夹套的反应器100中,并被聚合以获得完成了聚合的聚合物溶液。在此,聚合物溶液中的聚合物浓度为20重量%(5吨聚合物和20吨溶剂)。然后,排料罐(未示出)被供给来自反应器100的包括聚合物溶液的流,以利用残留的聚合物溶液的余热在减压条件下回收一部分气相形式的溶剂,并排出从中部分去除了溶剂的聚合物溶液。在此,作为气相回收的该部分溶剂的量为2.8吨,并且从中部分去除了溶剂的聚合物溶液的浓度为22.5重量%。然后,将包括部分去除了溶剂的聚合物溶液的流从排料罐(未示出)转移到蒸汽汽提处理单元300,以通过直接蒸汽接触回收蒸汽和气相形式的溶剂且获得固相聚合物。在此,蒸汽汽提处理单元300中使用的蒸汽量为13.8吨。然后,在制造过程中将固相聚合物与用于在蒸汽汽提处理单元中转移固相聚合物的循环水(水)一起引入到干燥器(未示出),以将残留溶剂和水分作为废气排出并丢弃,并获得最终的固相聚合物产物。在此,引入到干燥器(未示出)中的固相聚合物中的残留溶剂为0.5重量%。
[0106]
比较例2
[0107]
如图3所示的工艺流程图中所示,苯乙烯单体、丁二烯单体、作为溶剂的环己烷和作为引发剂的正丁基锂被供应至包括搅拌器和夹套的反应器100中,并被聚合以获得完成了聚合的聚合物溶液。在此,聚合物溶液中的聚合物浓度为20重量%(5吨聚合物和20吨溶剂)。然后,排料罐(未示出)被供给来自反应器100的包括聚合物溶液的流,以利用残留的聚合物溶液的余热在减压条件下回收一部分气相形式的溶剂,并排出从中部分去除了溶剂的聚合物溶液。在此,作为气相回收的该部分溶剂的量为2.8吨,并且从中部分去除了溶剂的聚合物溶液的浓度为22.5重量%。然后,将包括部分去除了溶剂的聚合物溶液的流从排料罐(未示出)转移到通过排出管线中的泵(未示出)连接的分离器200,以进一步使溶剂挥发以获得具有增大的聚合物浓度的聚合物溶液。在此,分离器200中的溶剂的进一步挥发通过以下方式来进行:对从来自分离器200的下部排出流(其包括具有增大的聚合物浓度的聚合物溶液)的80%分流的分支流进行加热并使其回流到分离器200,将包括来自分离器200的下部排出流的残余物的残余物流供应给蒸汽汽提处理单元300。在此,供应给热交换器220的蒸汽量为0.3吨,进一步挥发的溶剂为2.2吨,具有增大的聚合物浓度的聚合物溶液的浓度为2.5重量%,并且被热交换器220加热然后回流到分离器200的分支流的蒸汽质量分数为7重量%。
[0108]
与示例不同,分支流的蒸汽质量分数是没有通过压力调节阀230进行蒸汽质量分数调节的结果,并且由于被热交换器220加热然后回流的分支流中的溶剂的挥发现象,发生结垢(由于聚合物的积聚而导致的热交换器的堵塞现象),因此,应该停止溶剂回收设备的操作。
[0109]
实验例
[0110]
在示例1-11和比较例1中的聚合物的制备工艺中,测量热交换器220中使用的热量(a)、蒸汽量(b)和排出温度(c),聚合物的浓度(d)和转移到蒸汽汽提处理单元300的蒸汽量(e),过程中使用的蒸汽总量(f),固相聚合物中的残余溶剂量(g)和最终固相聚合物产物的颜色(h),以及确定设备中是否有结垢现象(i),并示于下表1中。
[0111]
[表1]
[0112]
[0113][0114]
参照表1,证实了随着转移到蒸汽汽提处理单元300的聚合物溶液中聚合物的浓度(重量%)增大,蒸汽汽提处理单元300中使用的蒸汽量减少,从而过程中使用的总蒸汽量减少。
[0115]
另外,证实了当引入到蒸汽汽提处理单元300的聚合物的浓度大于40重量%时(示例5和8),在热交换器220和循环至热交换器220的泵210和管道中发生结垢。如此,当发生结垢时,热交换效率降低从而停止工艺操作,因此经济可行性劣化。
[0116]
另外,证实了当由热交换器220加热并排出的蒸汽的温度高于110℃时(示例4和5),最终获得的固相聚合物发生了颜色变化。
[0117]
另外,证实了在示例9至11中,当来自分离器200的下部排出流的95%分流,被热交换器220加热,然后回流到分离器中时,过量的流被引入和排出分离器200,从而由于流量不稳定和压差增加而在管道中造成结垢现象。