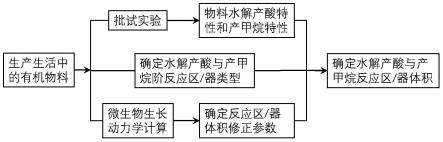
1.本发明属于厌氧处理技术领域,具体为一种确定两阶段厌氧发酵系统中水解产酸和产甲烷反应区或反应器体积参数的方法。
背景技术:2.厌氧发酵作为一项成熟的废弃物和污水处理技术,已经得到了广泛的应用。两阶段厌氧发酵或者两相厌氧发酵系统通过将水解产酸和产甲烷阶段独立在两个条件不同的反应区或反应器中,使各阶段的功能微生物代谢效率最大化,从而提升有机废弃物厌氧转化的总体效率。因此两阶段厌氧发酵系统相对于传统单阶段厌氧发酵具有更好的处理效果,受到学术界和工程界的广泛关注。但是目前两阶段或两相厌氧发酵系统中水解产酸和产甲烷阶段反应区或反应器体积比例缺乏明确的计算设计方法,在研究和实际工程中难以很好地耦合两个功能阶段,实现物料转化效率最大化。两阶段厌氧发酵反应系统的中的水解产酸与产甲烷反应区或反应器难以达到各自最佳的运行状态,也就是设计出来的两阶段厌氧发酵系统中的水解产酸阶段与产甲烷阶段很容易存在有效工作空间不足或者浪费的情况。如果水解产酸阶段工作空间不足,则不能在进入产甲烷单元之前将底物充分转化,从而使一部分底物的分解转移到产甲烷反应器中,这将容易导致产甲烷阶段酸化而被抑制。但是如果为了避免工作空间不足可能产生的负面影响而刻意将各单元的工作空间设计得过大,则是一种浪费,容易导致建设和运行维护成本过高。反应区构型和体积决定了反应区的水力停留时间和微生物停留特点,一旦确定就限制了有机负荷的利用效率。尤其是两阶段一体化厌氧发酵系统,在运行过程中难以再次调整。所以最理想的两阶段厌氧发酵系统应该是在充分发挥水解产酸与产甲烷反应区或反应器有效工作空间和尽可能减少各工作阶段反应区或反应器空间的浪费的基础上进行设计。
3.此外,两阶段厌氧发酵处理的各种原料之间存在差异,不同原料厌氧发酵转化过程中的微生物特征与生化反应类型和速率也存在不同。因此,需要充分结合发酵原料的物料特性和不同反应器构型中的微生物特征等因素才能设计出更符合实际应用需求的两阶段厌氧发酵系统。
4.在发明人所查知的范围内,目前关于解决上述两阶段厌氧发酵系统中所存在的问题的研究和专利十分有限。相关类似的专利和研究主要关注于提出某些特定组合或结构的发酵系统,而缺乏相应的反应器构型选择理由和体积参数确定等设计方法。例如:
5.cn103421678a公开了一种以cstr为制氢反应器和uasb为制甲烷反应器的生物质混合制氢烷系统及生产方法。水解产酸反应器与产甲烷反应器通过物料管道相连,体积比为1:1~10。通过外加物料回流装置调节控制产酸反应器和产甲烷反应器的底物转化率和产气率,最终可以提高生物钟转化为氢烷的比例并得到合适比例的氢烷。该两阶段反应器主要用于处理含固率高的生物质,包括木材、秸秆、落叶、锯末、动物尸体和粪便、市政垃圾和生活有机垃圾、农作物废料、木质纤维、有机废弃物或污泥、陆生和水生植物,以及它们的混合物。
6.cn102796765a公开了一种两相产氢产甲烷耦合反应处理易降解有机废弃物的方法。其主要特点是将有机废弃物在第一阶段充分水解产酸后的固液气产物都用于第二阶段产甲烷。其中第一阶段的气体产物经变压吸附脱碳后使氢气浓度达到80%,最后用于第二阶段提升甲烷产量20%左右,并消耗部分二氧化碳。该专利中产甲烷反应器包括所有高效厌氧反应器,但是对水解产酸反应器没有限制。
7.cn101172710a公开了一种两级两相厌氧工艺处理高浓度有机废水的方法。该方法是一种酸化反应器和产甲烷反应器相互独立的两阶段反应器。其中主要产酸反应器和产甲烷反应器的运行参数(ph、温度、循环、搅拌、回流比、容积负荷、进水流速等),而对反应器构型的选择和体积参数设计没有明确的方法限制。
8.cn102115258a公开了一种两相一体化厌氧反应器。该两相一体化反应器由左边的产酸池和右边的产甲烷池通过下部连通构成,酸化池里面布置有导流板和隔板构成的s形水流通道,产甲烷池内有填料用于富集微生物形成生物膜,减少微生物流失。但是产甲烷区域与水解产酸区与的比例,以及各自的结构特点未必适合相应的功能微生物生长和不同底物的转化。
9.cn102603124a公开了一种处理废水的两相两阶段厌氧生物反应器。该两相两阶段反应器将酸化反应室和甲烷反应室设计在同一个反应器中,酸化反应高径比≤1,甲烷化反应器高径比≥2。该两相一体化厌氧反应器结构复杂(例如加碱装置、漏斗旋流布水装置、进水和循环装置。内外复合结构等),一旦建成则难以改变,所以根据不同的底物特性提前确定合理的反应器设计参数十分必要。
10.cn106282243a公开了一种改进的两相厌氧发酵产甲烷的方法。该方法主要针对处理高含固率有机废弃物(餐厨垃圾、剩余污泥、农作物秸秆等)的两相厌氧发酵,其改进技术方案是控制水解产酸反应器顶空气体压力并将顶空气体用于产甲烷,最终提高水解产酸效率和甲烷回收率。
技术实现要素:11.本发明的目的在于提供一种确定两阶段厌氧系统反应区或反应器体积参数的方法,以解决两阶段厌氧系统中水解产酸阶段与产甲烷阶段反应区或反应器体积参数的确定缺乏理论指导,导致反应区或反应器工作空间过载甚至不能正常运行而失败,或工作空间富余而浪费反应区或反应器搭建、运行和维护成本等问题。
12.为了达到上述目的,本发明提供了如下技术方案:
13.一种确定两阶段厌氧系统反应区或反应器体积参数的方法,所述方法包括以下步骤:
14.步骤1、通过批试实验确定物料水解产酸与产甲烷特性;
15.通过实验室内小规模、短时间的批试实验,确定拟用于两阶段发酵处理的实际物料依次完成水解产酸和产甲烷所需时间、延滞期、产气潜力和有机物去除效率;再通过物料转化时间与两阶段厌氧系统反应区或反应器水力停留时间和体积之间的比例关系确定水解产酸反应区或反应器与产甲烷反应区或反应器的水力停留时间比例和体积比例;
16.批试实验结果与反应区或反应器水力停留时间和体积的换算关系如下:
[0017][0018]
其中,bhp是水解产酸批试实验,bmp是产甲烷批试实验;t
bhp
为水解产酸批试实验中,物料水解产酸所需时间,单位为h;t
bmp
为产甲烷批试实验中,产甲烷所需时间,单位为h;hrt1为水解产酸阶段反应区或反应器中的水力停留时间,单位为h;hrt2为产甲烷阶段反应区或反应器中的水力停留时间,单位为h;v1为水解产酸阶段反应区或反应器体积,单位为l;v2为产甲烷阶段反应区或反应器体积,单位为l;x1和x2分别为水解产酸和产甲烷反应区或反应器构型的体积修正参数;d为产甲烷反应器的进料浓度与水解产酸阶段的出料浓度之比;
[0019]
水解产酸批试实验和产甲烷批试实验的物料类型、发酵浓度、物料来源与拟用于两阶段厌氧发酵系统的物料一致;水解产酸批试实验和产甲烷批试实验的发酵条件也与拟设计的两阶段厌氧发酵系统的运行条件一致;批试实验中产甲烷批试实验bmp的底物是水解产酸批试实验bhp结束后的发酵物;
[0020]
步骤2、通过微生物生长动力学计算得到水解产酸过程和产甲烷过程功能微生物在不同类型反应器中的生长分布特点,进而确定水解产酸过程和产甲烷过程功能微生物所适应的反应区或反应器需具有的特点;
[0021]
所采用的微生物生长动力学计算模型如下:
[0022][0023]
其中,θ
cmin
为微生物细胞平均最小停留时间,单位为d-1
;y为细胞产率,单位为g细胞/g cod;k为比底物利用率,单位为mg cod/g vss/d;ks为半饱和常数,单位为mg cod/l;s0为进水中的底物浓度,单位为mg cod/l;b为比细胞衰减速率,单位为d-1
;
[0024]
其中的动力学参数k、ks、b由现有文献已知;y通过微生物生长半反应方程的吉布斯自由能计算所得,水解产酸微生物y为0.03-0.4,单位为g细胞/g cod;产甲烷微生物y为0.01-0.2,单位为g细胞/g cod;底物浓度s0根据两阶段厌氧发酵代谢途径中底物、中间产物、终产物之间的转化率计算而得,也能够取实验或经验所得具体数据;
[0025]
由于反应区或反应器平均污泥停留时间srt小于θ
cmin
时,对应的微生物能在该反应区或反应器中正常生长;而当平均污泥停留时间srt大于θ
cmin
时,对应的微生物则会随污泥一起被冲出反应区或反应器;因此,由以上微生物生长热动力学计算可知平均污泥停留时间srt较小的反应区或反应器就能够满足水解产酸微生物的正常生长代谢,而产乙酸和乙酸营养型产甲烷微生物适合在平均污泥停留时间srt较大的反应区或反应器生长;
[0026]
步骤3、结合实际物料理化特点、运行环境选取于两阶段厌氧发酵系统中水解产酸反应区或反应器和产甲烷反应区或反应器的具体构型;
[0027]
步骤4、结合步骤2和步骤3确定水解产酸反应区或反应器与产甲烷反应区或反应器的体积修正参数x1、x2;
[0028]
根据步骤2,平均污泥停留时间srt较小的反应区或反应器就能够满足水解产酸微生物的正常生长代谢,而产乙酸和乙酸营养型产甲烷微生物适合在平均污泥停留时间srt较大的反应区或反应器生长;
[0029]
根据各种构型厌氧反应器平均水力停留时间hrt和平均污泥停留时间srt的关系,将厌氧反应器区分为常规厌氧反应器和高效厌氧反应器;其中,常规厌氧反应器:3>srt/hrt≥1,高效厌氧反应器:srt/hrt≥3;
[0030]
根据步骤3所选择的两阶段厌氧发酵系统中水解产酸反应区或反应器和产甲烷反应区或反应器的具体构型:
[0031]
当选择常规厌氧反应器作为两阶段厌氧发酵系统水解产酸反应区或反应器时,对应的体积修正系数x1应满足:x1≥1;
[0032]
当选择高效厌氧反应器作为两阶段厌氧发酵系统水解产酸反应区或反应器时,对应的体积修正系数x1应满足1>x1>0;
[0033]
当选择常规厌氧反应器作为两阶段厌氧发酵系统产甲烷阶段反应区或反应器时,对应的体积修正系数x2应满足x2≥3;
[0034]
当选择高效厌氧反应器作为两阶段厌氧发酵系统产甲烷阶段反应区或反应器时,对应的体积修正系数x2应满足0<x2<30;
[0035]
步骤5、将步骤1批试实验所得的物料特性与步骤3所选择的反应器构型以及步骤4得到的相应的体积修正参数结合,确定拟设计的两阶段厌氧发酵系统中水解产酸和产甲烷反应区或反应器体积参数。
[0036]
步骤1中,批试实验中的水解产酸时间t
bhp
与产甲烷时间t
bmp
取完全反应时间的70-85%,以保证两阶段厌氧发酵系统连续运行时的处理效率。
[0037]
步骤1中,所述运行条件包括但不限于反应区或反应器接种物、运行温度、ph、碱度、添加剂含量和种类。
[0038]
步骤1中,所述运行条件还包括接种物预处理步骤,其中接种物预处理包括加热预处理、加酸预处理和加碱预处理。步骤1中,所述0《d≤1。
[0039]
步骤2中,水解产酸阶段微生物正常生长代谢需反应区或反应器满足36h>srt≥1.2h;产甲烷阶段微生物正常生长代谢需反应区或反应器满足srt≥36h。
[0040]
步骤4中,所述常规厌氧反应器包括连续搅拌罐反应器、厌氧生物滤池和厌氧序批式反应器。步骤4中,所述高效厌氧反应器包括上流式厌氧污泥床、填充床反应器、内循环反应器、膨胀颗粒污泥床和膜生物反应器。
[0041]
步骤4中,常规厌氧反应器的体积修正系数x1为1-2之间,高效厌氧反应器的体积修正系数x1为0.2-1之间;常规厌氧反应器的体积修正系数x2为10-30之间,高效厌氧反应器的体积修正系数x2为0.5-5之间。
[0042]
与现有技术相比,本发明的有益效果在于:
[0043]
相对于以往的两阶段厌氧发酵系统的设计方法和过程,本技术提出的设计思路,只需要进行简单、少量、低成本、短时间的批试实验和基于参数推导计算,就可使设计的两阶段厌氧反应器契合实际和基础理论,具有相当的可靠性。基于此,本发明提出的设计思路有利于大大减少为了不断探索优化两阶段发酵系统所需要的进行的大量实验或尝试所花费的人力、物力等成本,并科学合理地设计出更高效稳定的两阶段厌氧发酵系统。
附图说明
[0044]
图1为本发明的确定两阶段厌氧系统反应区或反应器体积参数的方法流程图。
具体实施方式
[0045]
下面结合附图对本发明的具体实施方式作进一步说明。
[0046]
一种确定两阶段厌氧系统反应区或反应器体积参数的方法,包括以下步骤:
[0047]
步骤1、通过批试实验确定物料水解产酸与产甲烷特性。
[0048]
通过实验室内小规模、短时间的批试实验,确定拟用于两阶段发酵处理的实际物料依次完成水解产酸和产甲烷所需时间、延滞期、产气潜力和有机物去除效率。再通过物料转化时间与两阶段厌氧系统反应区或反应器水力停留时间和体积之间的比例关系确定水解产酸反应区或反应器与产甲烷反应区或反应器的水力停留时间比例和体积比例。
[0049]
批试实验结果与反应区或反应器水力停留时间和体积的换算关系如下:
[0050][0051]
其中,bhp是水解产酸批试实验,bmp是产甲烷批试实验;t
bhp
为水解产酸批试实验中,物料水解产酸所需时间,单位为h;t
bmp
为产甲烷批试实验中,产甲烷所需时间,单位为h;hrt1为水解产酸阶段反应区或反应器中的水力停留时间,单位为h;hrt2为产甲烷阶段反应区或反应器中的水力停留时间,单位为h;v1为水解产酸阶段反应区或反应器体积,单位为l;v2为产甲烷阶段反应区或反应器体积,单位为l;x1和x2分别为水解产酸和产甲烷反应区或反应器构型的体积修正参数;d为产甲烷反应器的进料浓度与水解产酸阶段的出料浓度之比。
[0052]
批试实验中的水解产酸时间t
bhp
与产甲烷时间t
bmp
取完全反应时间的70-85%,以保证两阶段厌氧发酵系统连续运行时的处理效率。两阶段厌氧发酵系统中的水解产酸与产甲烷反应区或反应器的水力停留时间和批试实验中的t
bhp
与t
bmp
成比例,如公式1所示。但是,由于水解产酸阶段和产甲烷阶段可能选择不同的反应区或反应器构型,所以需要考虑反应区或反应器自身的体积修正系数x1和x2。
[0053]
还需要注意的是,本发明的水解产酸批试实验和产甲烷批试实验的物料类型、发酵浓度、物料来源与拟用于两阶段厌氧发酵系统的物料一致。水解产酸批试实验和产甲烷批试实验的发酵条件也与拟设计的两阶段厌氧发酵系统的运行条件一致,所述运行条件包括但不限于反应区或反应器接种物、运行温度、ph、碱度、添加剂含量和种类等。根据两阶段厌氧发酵系统的运行特点,批试实验中产甲烷批试实验bmp的底物是水解产酸批试实验bhp结束后的发酵物。优选地,所述运行条件还包括接种物预处理,其中接种物预处理包括加热预处理、加酸预处理和加碱预处理。
[0054]
两阶段厌氧发酵系统中水解产酸反应区或反应器与产甲烷反应区或反应器体积与水力停留时间成比例。考虑在某些特定情况下,物料从水解产酸反应区或反应器到产甲烷反应区或反应器可能需要进行固液分离或稀释。将产甲烷阶段的进料浓度与水解产酸阶段的出料浓度之比作为两阶段系统中水解产酸反应区或反应器与产甲烷反应区或反应器之间的比例系数d,所述0《d≤1,使水解产酸阶段与产甲烷阶段反应区或反应器体积比例更符合实际。
[0055]
步骤2、通过微生物生长动力学计算得到水解产酸过程和产甲烷过程功能微生物在不同类型反应器中的生长分布特点,进而确定水解产酸过程和产甲烷过程功能微生物所适应的反应区或反应器需具有的特点。
[0056]
所采用的微生物生长动力学计算模型如下:
[0057][0058]
其中,θ
cmin
为微生物细胞平均最小停留时间,单位为d-1
;y为细胞产率,单位为g细胞/g cod;k为比底物利用率,单位为mg cod/g vss/d;ks为半饱和常数,单位为mg cod/l;s0为进水中的底物浓度,单位为mg cod/l;b为比细胞衰减速率,单位为d-1
。
[0059]
其中的动力学参数k、ks、b由现有文献已知;y通过微生物生长半反应方程的吉布斯自由能计算所得,水解产酸微生物y为0.03-0.4,单位为g细胞/g cod;产甲烷微生物y为0.01-0.2,单位为g细胞/g cod;底物浓度s0可根据两阶段厌氧发酵代谢途径中底物、中间产物、终产物之间的转化率计算而得,也可取实验或经验数据。
[0060]
由于反应区或反应器平均污泥停留时间srt小于θ
cmin
时,对应的微生物能在该反应区或反应器中正常生长;而当平均污泥停留时间srt大于θ
cmin
时,对应的微生物则会随污泥一起被冲出反应区或反应器。因此,由以上微生物生长热动力学计算可知平均污泥停留时间srt较小的反应区或反应器就能够满足水解产酸微生物的正常生长代谢,而产乙酸和乙酸营养型产甲烷微生物适合在平均污泥停留时间srt较大的反应区或反应器生长。优选地,水解产酸阶段微生物正常生长代谢需反应区或反应器满足36h>srt≥1.2h;产甲烷阶段微生物正常生长代谢需反应区或反应器满足srt≥36h。
[0061]
步骤3、结合实际物料理化特点、运行环境选取于两阶段厌氧发酵系统中水解产酸反应区或反应器和产甲烷反应区或反应器的具体构型。
[0062]
步骤4、结合步骤2和步骤3确定水解产酸反应区或反应器与产甲烷反应区或反应器的体积修正参数x1、x2。
[0063]
根据步骤2,平均污泥停留时间srt较小的反应区或反应器就能够满足水解产酸微生物的正常生长代谢,而产乙酸和乙酸营养型产甲烷微生物适合在平均污泥停留时间srt较大的反应区或反应器生长。
[0064]
根据各种构型厌氧反应器平均水力停留时间hrt和平均污泥停留时间srt的关系,将厌氧反应器区分为常规厌氧反应器和高效厌氧反应器。其中,常规厌氧反应器:3>srt/hrt≥1,高效厌氧反应器:srt/hrt≥3。
[0065]
优选地,所述供选择的常规厌氧反应器包括但不限于连续搅拌罐反应器continuous stirred tank reactor,cstr、厌氧生物滤池anaerobic biological filter,af、厌氧序批式反应器anaerobic sequencing batch reactor,asbr。
[0066]
优选地,所述高效厌氧反应器包括但不限于上流式厌氧污泥床up-flow anaerobic sludge blanket,uasb、填充床反应器packed bed reactor,pbr、内循环反应器internal circulation,ic、膨胀颗粒污泥床expanded granular sludge bed,egsb、膜生物反应器membrane bioreactor,mbr。
[0067]
根据步骤3所选择的两阶段厌氧发酵系统中水解产酸反应区或反应器和产甲烷反应区或反应器的具体构型:
[0068]
当选择常规厌氧反应器作为两阶段厌氧发酵系统水解产酸反应区或反应器时,对应的体积修正系数x1应满足:x1≥1;
[0069]
当选择高效厌氧反应器作为两阶段厌氧发酵系统水解产酸反应区或反应器时,对应的体积修正系数x1应满足1>x1>0;
[0070]
当选择常规厌氧反应器作为两阶段厌氧发酵系统产甲烷阶段反应区或反应器时,对应的体积修正系数x2应满足x2≥3;
[0071]
当选择高效厌氧反应器作为两阶段厌氧发酵系统产甲烷阶段反应区或反应器时,对应的体积修正系数x2应满足0<x2<30。
[0072]
优选地,常规厌氧反应器的体积修正系数x1为1-2之间,高效厌氧反应器的体积修正系数x1为0.2-1之间;常规厌氧反应器的体积修正系数x2为10-30之间,高效厌氧反应器的体积修正系数x2为0.5-5之间。
[0073]
步骤5、将步骤1批试实验所得的物料特性与步骤3所选择的反应器构型以及步骤4得到的相应的体积修正参数结合,确定拟设计的两阶段厌氧发酵系统中水解产酸和产甲烷反应区或反应器体积参数。
[0074]
实施例1
[0075]
目的:确定一套处理蜜糖废水的一体化两阶段厌氧发酵系统中水解产酸区与产甲烷反应区构型和体积参数。该系统每天需处理污水1m3,污水浓度为5g cod/l,有机负荷要求达到40g cod/l/d,发酵温度为35-37℃。
[0076]
步骤1、用蜜糖废水开展水解产酸和产甲烷批试实验,将水解产酸批试实验结束后的废水继续用于产甲烷批试实验。
[0077]
批试实验中所用蜜糖废水有机物浓度为5g cod/l,水解产酸批试实验温度为35-37℃,ph调节为4.5-6.5。水解产酸批试实验结束后得到用于产甲烷批试实验的水相有机物浓度为4g cod/l,产甲烷实验温度为35-37℃,ph为6.5-8.5。
[0078]
水解产酸批试实验和产甲烷批试实验得到该蜜糖废水充分水解产酸所需的时间为12h,水解产酸实验水相充分产甲烷所需时间为96h。取水解产酸和产甲烷所需最大时间的80%为设计值,则得到再根据批试实验结果估算水解产酸反应区与产甲烷反应区hrt比例关系和体积比例关系。由步骤1得到的可得
[0079]
步骤2、通过微生物生长动力学计算得到水解产酸过程和产甲烷过程功能微生物在不同类型反应器中的生长分布特点,进而确定水解产酸过程和产甲烷过程功能微生物所适应的反应区或反应器需具有的特点。
[0080]
根据微生物生长动力学计算结果判断水解产酸和产甲烷微生物分别适应的水解产酸反应区和产甲烷反应区结构特点。其中hrt和srt较小的反应区就能够满足水解产酸微生物的正常生长代谢,而产乙酸和乙酸营养型产甲烷微生物适合在hrt和srt较大的反应区生长。
[0081]
步骤3、结合实际物料理化特点、运行环境选取于两阶段厌氧发酵系统中水解产酸反应区或反应器和产甲烷反应区或反应器的具体构型。
[0082]
从已知的常规厌氧反应器和高效厌氧反应器中选择填充床pbr作为该两阶段厌氧发酵系统的水解产酸反应区,选择上流式厌氧污泥床uasb作为该两阶段厌氧系统的产甲烷反应区。
[0083]
步骤4、结合步骤2和步骤3确定水解产酸反应区或反应器与产甲烷反应区或反应
器的体积修正参数x1、x2。
[0084]
由于填充床pbr和上流式污泥床uasb都是高效厌氧反应器,取x1=0.5、x2=1。
[0085]
步骤5、将步骤1批试实验所得的物料特性与步骤3所选择的反应器构型以及步骤4得到的相应的体积修正参数结合,确定拟设计的两阶段厌氧发酵系统中水解产酸和产甲烷反应区或反应器体积参数。
[0086]
根据步骤3选择的水解产酸反应区和产甲烷反应区的构型和步骤1中得到的比例关系以及步骤4得到的相应的体积修正参数,最终确定两阶段厌氧发酵系统中水解产酸反应区与产甲烷反应区体积比例。
[0087]
因为是一体化厌氧发酵系统,不考虑固液分离和稀释,则d=1。综上可得该两阶段厌氧发酵系统中水解产酸反应区体积v1与产甲烷反应区体积v2应满足
[0088]
根据拟设计的一体化两阶段厌氧发酵系统进水量、进水浓度和拟达到的有机负荷40g cod/l/d,确定该系统总体积为125l。因此,由该可知反发酵系统水解产酸反应区体积v1=25l,产甲烷反应区体积v2=100l。
[0089]
实施例2
[0090]
目的:确定一套用于处理食品废弃物的两阶段厌氧反应系统中水解产酸阶段反应器与产甲烷阶段反应器的体积参数。需要该系统每天处理100kg食品废弃物(主要性质见表1),并且水解产酸阶段有机负荷达到17.5kg vs/m3/d,运行温度为35-37℃。
[0091]
表1拟处理食品废弃物的主要特点
[0092][0093]
ts:总固体(total solids);vs:挥发性固体(volatile solids);tcod:总化学需氧量(total chemical oxygen demand);scod:溶解性化学需氧量(soluble chemical oxygen demand)
[0094]
步骤1、用拟处理的食品废弃物开展水解产酸和产甲烷批试实验,将水解产酸批试实验结束后的废水继续用于产甲烷批试实验。
[0095]
水解产酸批试实验所用食品废弃物性质与拟设计的两阶段厌氧系统需要处理的食品废弃物相同(表1),温度为35-37℃,ph调节为4.5-6.5。水解产酸批试实验结束后得到vs为14%w/w的水相产物(scod为0.58
±
0.03g cod/g vs)用于产甲烷批试实验,产甲烷批试实验温度为35-37℃,ph为6.5-8.5。
[0096]
水解产酸批试实验和产甲烷批试实验得到该食品废弃物充分水解产酸所需的时间为36h,水解产酸实验水相充分产甲烷所需时间为720h。分别取完全水解产酸和产甲烷所需时间的80%和70%为设计值,则得到再由批试实验结果估算水解产酸反应器
与产甲烷反应器hrt比例关系和体积比例关系。得到
[0097]
步骤2、通过微生物生长动力学计算得到水解产酸过程和产甲烷过程功能微生物在不同类型反应器中的生长分布特点,进而确定水解产酸过程和产甲烷过程功能微生物所适应的反应区或反应器需具有的特点。
[0098]
根据微生物生长动力学计算结果判断水解产酸和产甲烷微生物分别适应的水解产酸反应器和产甲烷反应器结构特点。其中hrt和srt较小的反应器就能够满足水解产酸微生物的正常生长代谢,而产乙酸和乙酸营养型产甲烷微生物适合在hrt和srt较大的反应器生长。
[0099]
步骤3、结合实际物料理化特点、运行环境选取于两阶段厌氧发酵系统中水解产酸反应区或反应器和产甲烷反应区或反应器的具体构型。
[0100]
考虑到食品废弃物ts较大,因此可以从已知的常规厌氧反应器和高效厌氧反应器中选择连续搅拌罐反应器cstr作为该两阶段厌氧发酵系统的水解产酸反应器,选择上流式污泥床uasb作为该两阶段厌氧系统的产甲烷反应器。
[0101]
步骤4、结合步骤2和步骤3确定水解产酸反应区或反应器与产甲烷反应区或反应器的体积修正参数x1、x2。
[0102]
连续搅拌罐反应器cstr是常规厌氧反应器,上流式厌氧污泥床uasb是高效厌氧反应器,取x1=1.5、x2=0.5。
[0103]
步骤5、根据步骤3选择的水解产酸反应器和产甲烷反应器构型和步骤1中得到的比例关系以及步骤4得到的相应的体积修正参数,最终确定两阶段厌氧发酵系统中水解产酸反应器与产甲烷反应器体积比例。
[0104]
为了保证产甲烷反应器正常运行,需要对水解产酸反应器中的剩余物进行固液分离和稀释。根据水解产酸批试实验结束后得到的水相产物浓度(14%vs),稀释10倍可以保证产甲烷阶段不因为有机负荷过高而被抑制。因此,由稀释前后的浓度比例关系得到d=0.1。综上可得该两阶段厌氧发酵系统中水解产酸反应区体积v1与产甲烷反应区体积v2应满足
[0105]
根据拟设计的一体化两阶段厌氧发酵系统进料量、进料浓度和拟达到的有机负荷确定该发酵系统水解产酸阶段的反应器体积v1=1m3,再根据可计算出该发酵系统产甲烷反应器体积v2=5.91m3。
[0106]
上述实施例仅用于说明本发明,本专利的保护范围不限于此。任何熟悉本技术领域的技术人员在本发明提出的方法范围内可轻易想到的变化或替换,都应涵盖在本发明的保护范围内。因此,本专利的保护范围应以所述权利要求为准。