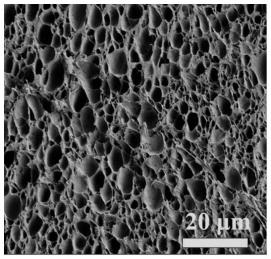
1.本发明涉及聚合物发泡材料技术领域,具体涉及一种聚丁烯发泡材料及其制备方法、预制品及应用。
背景技术:2.聚合物发泡材料因其多孔结构及轻量化、冲击韧性好、隔热、吸音等性能而广泛应用于包装、建筑、隔热、吸音、组织支架、吸油等领域。相比于含单峰泡孔结构的发泡材料,具有双峰泡孔结构的聚合物微发泡材料因小泡孔可以提供良好的力学性能、隔热性能等,而大泡孔能够降低材料的表观密度,从而表现出更优异的性能。
3.目前,制备具有双峰泡孔结构的泡沫材料的主要方法有两步间歇发泡法和双发泡剂连续挤出发泡法。专利cn105385024a公开了一种制备具有双峰分布的聚丙烯发泡材料及其制备方法,其通过添加多孔无机粒子来制备具有双峰泡孔结构的泡沫材料。专利cn105419093a公开了一种含双峰泡孔结构的泡沫材料及其制备方法,其特点是采用连续挤出发泡法,共混两种或多种聚合物以及单甘脂,通过超临界co2发泡制备了含双峰泡孔结构的泡沫材料。
4.聚丁烯作为珍贵的c4资源产物,在我国的利用率却比较低,而且聚丁烯具有良好的物理力学性能,突出的抗蠕变性,耐化学药品性、耐低温性,耐环境应力开裂性,而且有很好的机械强度和高韧性。为得到一种聚丁烯发泡材料,其具有双峰泡孔结构,拓展聚丁烯的应用领域,提高其利用率,促进我国聚丁烯产业的发展具有较好的现实意义。
技术实现要素:5.本发明为了得到一种聚丁烯发泡材料,其具有双峰泡孔结构,提供了一种聚丁烯发泡材料及其制备方法、预制品及应用。本发明制备方法所得到的聚丁烯发泡材料的双峰泡孔结构尺寸可控,拓宽了聚丁烯发泡材料在隔热、吸声等领域的应用。
6.本发明是通过下列技术方案解决上述技术问题。
7.本发明提供了一种聚丁烯发泡材料的制备方法,包括如下步骤:
8.(1)对聚丁烯类树脂微粒进行退火处理,得到预制品;
9.所述退火处理的方式包括超临界co2退火处理或常温常压退火处理;
10.当所述退火处理的方式为超临界co2退火处理时,所述超临界co2退火处理包括:在超临界co2的存在下,对聚丁烯类树脂微粒进行保温保压,泄压,即得;
11.其中,所述保温保压的温度为80℃~140℃,所述保温保压的压力为5mpa~20mpa;
12.当所述聚丁烯类树脂微粒的尺寸为a≤5mm,b≤5mm,c≤5mm时,所述保温保压的时间为5min~85min;其中,a、b、c表示聚丁烯类树脂微粒在坐标系中x轴方向、y轴方向和z轴方向的最大尺寸;
13.所述泄压的速率为0.1~1mpa/min;
14.当所述退火处理的方式为常温常压退火处理时,所述常温常压退火处理包括:将
聚丁烯类树脂微粒熔融,在常温常压下冷却,即得;
15.(2)发泡:在超临界co2的存在下,将所述预制品进行保温保压,泄压,即得;其中,所述泄压的速率为5~300mpa/s。
16.本发明步骤(1)中,所述聚丁烯类树脂可为等规聚丁烯、间规聚丁烯和聚丁烯合金中的一种或多种。
17.其中,所述聚丁烯合金为1-丁烯/丙烯共聚物,所述1-丁烯/丙烯共聚物的分子量分布较佳地为mw/mn=1~10;较佳地,所述1-丁烯/丙烯共聚物中1-丁烯的摩尔含量为70-99%,丙烯的摩尔含量为1-30%。
18.本发明中步骤(1)中,所述聚丁烯类树脂的等规度可为50~99%,例如95%。所述聚丁烯类树脂的结晶度可为20~60%,例如45%。所述聚丁烯类树脂的熔融指数可为0.1g~5g/10min,例如0.5g/10min。
19.本发明步骤(1)中,所述聚丁烯类树脂微粒可具有单一晶型或具有两种晶型。
20.和/或,所述聚丁烯类树脂微粒的形状可为颗粒或片材。
21.经研究发现,熔融指数过小时基体流动性较差难以发泡,熔融指数超过5g/10min时表现出高流动性,熔体强度降低导致泡孔破裂。
22.本发明中,当所述退火处理的方式为超临界co2退火处理时,所述聚丁烯类树脂微粒的尺寸可为a≤50mm,b≤50mm,c≤30mm,所述聚丁烯类树脂微粒的保温保压时间为5~150min。
23.较佳地,所述聚丁烯类树脂微粒的尺寸为5mm≤a≤30mm,5mm≤b≤30mm,2mm≤c≤30mm,所述聚丁烯类树脂微粒的保温保压时间为20~140min。
24.较佳地,所述聚丁烯类树脂微粒的尺寸为10mm≤a≤20mm,10mm≤b≤20mm,5mm≤c≤20mm,所述聚丁烯类树脂微粒的保温保压时间为40~120min。
25.较佳地,所述聚丁烯类树脂微粒的尺寸为1mm≤a≤4mm,1mm≤b≤4mm,1mm≤c≤4mm,所述聚丁烯类树脂微粒的保温保压时间为10min~80min。
26.较佳地,所述聚丁烯类树脂微粒的尺寸为a=2mm,b=2mm,c=2mm,所述聚丁烯类树脂微粒的保温保压时间为20min~60min,例如30min、40min或50min。
27.本发明步骤(1)中,所述保温保压的温度可为90℃~120℃,例如100℃、105℃、110℃或115℃。
28.本发明步骤(1)中,所述保温保压的压力可为6mpa~18mpa,例如10mpa或15mpa。
29.本发明步骤(1)中,所述超临界co2退火处理过程中,一般进行缓慢泄压。所述泄压的速率较佳地为0.3mpa/min。缓慢泄压是为了保证退火过程中样品未发泡。
30.本发明中,所述超临界co2是指温度压力在临界温度(31.1℃)和临界压力(7.37mpa)以上时该状态下对应的co2流体。
31.本发明步骤(1)中,所述超临界co2退火处理一般在高压釜中进行。
32.本发明步骤(1)中,当所述退火处理的方式为常温常压退火处理时,所述理冷却的时间可为1h~168h,较佳地为2h~72h,例如24h。
33.本发明中,所述常温常压为温度是20-25℃,压力是101kpa。
34.本发明步骤(1)中,当所述退火处理的方式为常温常压退火处理时,所述熔融的方式可为热压熔融或熔融挤出。其中,所述熔融挤出一般采用双螺杆挤出机进行。
35.在发明人研究过程中发现,对聚丁烯类树脂微粒进行退火处理,可以使得聚丁烯类树脂中形成两种不同的晶型。由于不同的晶型在相同温度下表现出不同的熔体强度,其中第一种晶型的晶区基本熔融,因此泡孔直径较大;第二种晶型的晶区大量存在限制了泡孔生长,因此泡孔直径较小,所以在不同晶型中泡孔孔径的差异使得发泡材料具有双峰泡孔结构。调节退火条件可获得具有不同比例的两种晶型的聚丁烯类树脂,从而经间歇物理发泡后可制备具有不同双峰分布的发泡材料。
36.步骤(1)中,当采用超临界co2退火处理时,通过超临界co2与聚丁烯类树脂微粒的相互作用,使聚丁烯类树脂微粒部分熔融,可以使得聚丁烯类树脂微粒形成两种不同的晶型。根据退火时间不同制得具有不同晶型比例的预制品。
37.步骤(1)中,当采用常温常压退火处理时,聚丁烯类树脂熔融后生成不稳定的第三种晶型,在常温常压冷却过程中,第三种晶型自发地向第二种晶型转变,通过控制室温退火时间调控晶型转变的比例,获得具有与两种不同的晶型的预制品,从而制备出具有双峰泡孔结构聚丁烯发泡材料。
38.本发明步骤(2)中,所述保温保压的压力可为5mpa~20mpa,较佳的为7mpa~18mpa,例如10mpa。
39.本发明步骤(2)中,所述保温保压的时间可为10min~60min;较佳地为20min~50min,例如40min。
40.本发明步骤(2)中,所述保温保压的温度可为90℃~115℃,较佳地为100℃~110℃,例如105℃。
41.本发明步骤(2)中,所述泄压速率较佳地为10~200mpa/s,例如100mpa/s。
42.本发明步骤(2)中,所述发泡的发泡倍率可为6~32,较佳地为10~28,例如12.1、15.3、20.8、27.6或27.7。
43.本发明步骤(2)中,所述发泡一般在高压釜中进行。
44.本发明还提供了一种聚丁烯发泡材料的预制品,其由上述聚丁烯发泡材料制备方法的步骤(1)制得。
45.本发明还提供一种由上述聚丁烯发泡材料制备方法制得的聚丁烯发泡材料。
46.本发明还提供了一种上述聚丁烯发泡材料在隔热领域或吸声领域的应用。
47.本发明还提供了一种聚丁烯发泡材料,所述聚丁烯发泡材料具有双峰泡孔结构,大泡孔的平均直径为12μm~200μm,小泡孔的平均直径为1.5μm~40μm;其相对密度为0.038g/cm3~0.18g/cm3。
48.在符合本领域常识的基础上,上述各优选条件,可任意组合,即得本发明各较佳实例。
49.本发明所用试剂和原料均市售可得。
50.本发明的积极进步效果在于:
51.本发明的制备方法通过在发泡前进行退火处理,调控聚丁烯发泡材料预制品中的晶型结构,进而制备出具有可调节尺寸的双峰泡孔结构的聚丁烯发泡材料,拓宽了聚丁烯发泡材料在隔热、吸声等领域的应用。
52.另外,本发明的制备方法还可以降低聚丁烯发泡温度,同时发泡材料中保留的两种晶型能够降低二次成型加工温度,为聚丁烯发泡材料的成型加工奠定了基础。
附图说明
53.图1为实施例1制得的聚丁烯发泡材料的扫描电镜图。
54.图2为实施例2制得的聚丁烯发泡材料的扫描电镜图。
55.图3为实施例3制得的聚丁烯发泡材料的扫描电镜图。
56.图4为实施例4制得的聚丁烯发泡材料的扫描电镜图。
57.图5为实施例5制得的聚丁烯发泡材料的扫描电镜图。
58.图6为实施例6制得的聚丁烯发泡材料的扫描电镜图。
59.图7为实施例7制得的聚丁烯发泡材料的扫描电镜图。
60.图8为对比例1制得的聚丁烯发泡材料的扫描电镜图。
61.图9为对比例2制得的聚丁烯发泡材料的扫描电镜图。
具体实施方式
62.下面通过实施例的方式进一步说明本发明,但并不因此将本发明限制在所述的实施例范围之中。下列实施例中未注明具体条件的实验方法,按照常规方法和条件,或按照商品说明书选择。
63.本发明实施例1~7及对比例1所用聚丁烯类树脂微粒为实验用等规聚丁烯微粒,满足以下条件:具有单一晶型,等规度均为95%,结晶度均为50%,熔融指数均为0.5g/10min;尺寸为a=2mm,b=2mm,c=2mm。
64.本发明对比例2所用聚丁烯类树脂微粒为聚丁烯合金微粒,具体为:丁烯的摩尔含量为90%;丙烯的摩尔含量为10%,等规度为95%,结晶度为48%,熔融指数为0.2g/10min;尺寸为a=2mm,b=2mm,c=2mm。
65.实施例1
66.(1)将实验用等规聚丁烯微粒投入到高压釜中,利用压力小于1mpa的co2对高压釜进行吹扫,排除釜内空气以及水分;然后将高压釜的温度升高至115℃后,充入超临界co2压力升高至15mpa,达到温度和压力后,保温保压10min,使等规聚丁烯微粒部分熔融,以0.3mpa/min的速度缓慢泄压,得到具有两种晶型的预制品1;
67.(2)再次将高压釜温度升至90℃,维持高压釜压力为10mpa,保温保压40min;将高压釜可控泄压,泄压速率为100mpa/s,然后将高压釜置于水浴中冷却,冷却完毕后取出聚丁烯发泡材料,发泡倍率在5~10之间。
68.实施例2
69.(1)将实验用等规聚丁烯微粒投入到高压釜中,利用压力小于1mpa的co2对高压釜进行吹扫,排除釜内空气以及水分;然后将高压釜的温度升高至110℃,压力升高至15mpa,达到温度和压力后,保温保压20min,使等规聚丁烯微粒部分熔融,以0.3mpa/min的速度缓慢泄压,得到预制品1;
70.(2)再次将高压釜温度升至103℃,维持高压釜压力为10mpa,保温保压40min;将高压釜可控泄压,泄压速率为100mpa/s。然后将高压釜置于水浴中冷却,冷却完毕后取出聚丁烯发泡材料,发泡倍率在15~25之间。
71.实施例3
72.(1)将实验用等规聚丁烯微粒投入到高压釜中,利用压力小于1mpa的co2对高压釜
进行吹扫,排除釜内空气以及水分;然后将高压釜的温度升高至110℃,压力升高至15mpa,达到温度和压力后,保温保压30min,使等规聚丁烯微粒部分熔融,以0.3mpa/min的速度缓慢泄压,得到预制品1;
73.(2)再次将高压釜温度升至109℃,维持高压釜压力为10mpa,保温保压40min;将高压釜可控泄压,泄压速率为100mpa/s。然后将高压釜置于水浴中冷却,冷却完毕后取出聚丁烯发泡材料,发泡倍率在30~35之间。
74.实施例4
75.(1)将实验用等规聚丁烯微粒投入到高压釜中,利用压力小于1mpa的co2对高压釜进行吹扫,排除釜内空气以及水分;然后将高压釜的温度升高至110℃,压力升高至15mpa,达到温度和压力后,保温保压40min,使等规聚丁烯微粒部分熔融,以0.3mpa/min的速度缓慢泄压,得到预制品1;
76.(2)再次将高压釜温度升至100℃,维持高压釜压力为10mpa,保温保压40min;将高压釜可控泄压,泄压速率为100mpa/s。然后将高压釜置于水浴中冷却,冷却完毕后取出聚丁烯发泡材料,发泡倍率在10~15之间。
77.实施例5
78.(1)将实验用等规聚丁烯微粒投入到高压釜中,利用压力小于1mpa的co2对高压釜进行吹扫,排除釜内空气以及水分;然后将高压釜的温度升高至110℃,压力升高至15mpa,达到温度和压力后,保温保压50min,使等规聚丁烯微粒部分熔融,以0.3mpa/min的速度缓慢泄压,得到预制品1;
79.(2)再次将高压釜温度升至109℃,维持高压釜压力为10mpa,保温保压60min;将高压釜可控泄压,泄压速率为100mpa/s。然后将高压釜置于水浴中冷却,冷却完毕后取出聚丁烯发泡材料,发泡倍率在25~30之间。
80.实施例6
81.(1)将实验用等规聚丁烯微粒置于双螺杆挤出机中进行熔融挤出,得到a=5mm,b=5mm,c=2mm的聚丁烯类树脂材料,常温常压退火24h后得到预制品2;
82.(2)将上述样品置于高压釜中,利用压力小于1mpa的co2对高压釜进行吹扫三次,排除釜内空气以及水分;然后将高压釜的温度升高至100℃,压力升高至15mpa,保温保压40min,将高压釜泄压,泄压的速率为100mpa/s,然后将高压釜置于水浴中冷却,冷却完毕后取出聚丁烯发泡材料,发泡倍率在5~10之间。
83.实施例7
84.(1)将实验用等规聚丁烯微粒置于双螺杆挤出机中进行熔融挤出,得到a=5mm,b=5mm,c=2mm的聚丁烯类树脂材料,常温常压退火2h后得到预制品2;
85.(2)将上述样品置于高压釜中,利用压力小于1mpa的co2对高压釜进行吹扫三次,排除釜内空气以及水分;然后将高压釜的温度升高至105℃,压力升高至12.5mpa,保持40min,然后将高压釜泄压,泄压速率为100mpa/s,然后将高压釜置于水浴中冷却,冷却完毕后取出聚丁烯发泡材料,发泡倍率在25~30之间。
86.对比例1
87.将实验用等规聚丁烯微粒投入到高压釜中,利用压力小于1mpa的co2对高压釜进行吹扫,排除釜内空气以及水分;然后将高压釜的温度升高至110℃,压力升高至15mpa,达
到温度和压力后,保持40min,使co2渗透到等规聚丁烯微粒中;保压时间结束后,将高压釜可控泄压,泄压速率为100mpa/s。然后将高压釜置于水浴中冷却,冷却完毕后取出聚丁烯发泡材料,发泡倍率在15~20之间。
88.对比例2
89.(1)将聚丁烯合金微粒投入到高压釜中,利用压力小于1mpa的co2对高压釜进行吹扫,排除釜内空气以及水分;然后将高压釜的温度升高至115℃,压力升高至15mpa,达到温度和压力后,保持90min,使聚丁烯合金微粒完全熔融,经0.3mpa/min的速率泄压后得到具有单一晶型的预制品;
90.(2)再次将高压釜的温度升高至97℃,压力升高至10mpa,达到温度和压力后,保持40min,冷却完毕后取出聚丁烯发泡材料,发泡倍率在25~30之间。
91.效果实施例
92.通过jsm-6360lv扫描电子显微镜对实施例1~7和对比例1~2所得到的聚丁烯发泡材料进行电子扫描,扫描电镜图如图1~9所示。根据扫描电镜图获得聚丁烯发泡材料的泡孔尺寸和泡孔结构,利用astm d792-00经阿基米德排水法获得发泡倍率,结果见表1。
93.表1
[0094][0095][0096]
由图1~7与图8~9以及上表的数据可知,本发明的制备方法可通调控退火时间制备出具有可调节尺寸的双峰泡孔结构的聚丁烯发泡材料。