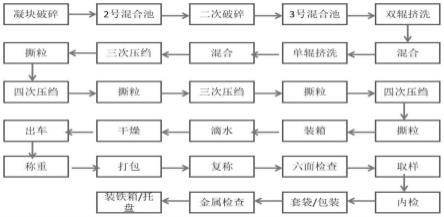
一种高性能tsr9710天然橡胶的制备工艺
技术领域
1.本发明涉及天然橡胶领域,尤其涉及一种高性能tsr9710天然橡胶的制备工艺。
背景技术:2.天然橡胶加工的初级产品主要用于加工轮胎的原料,不同的初级产品由于指标不同,在轮胎厂端使用的部位也不一样,目前国内轮胎厂使用的tsr9710产品,属于通用的指标,一般塑性初值p0大于33,塑性保持率pri大于50,杂质含量低于0.08%,灰分含量小于0.75%,门尼粘度在83
±
10,拉伸强度大于18mpa,扯断伸长率大于680%。
3.申请号为201711293056.0的中国专利公开了一种以标胶为原料生产tsr9710橡胶的方法,先将标胶经技术配方切割成块状后经过干搅破碎、浮洗,再经过双辊糅合、五级压绉、一级造粒解决胶料的杂质、灰分以及非胶异物等去除问题,使胶料的软硬混合均匀,便于烘干,后加入隔离剂,对胶粒进行调粘和抗氧化处理,然后进行干燥烘干。接着通过称胶、压包、取样检验、外观检查挑除异物质、再经金属探测仪检测后包装装箱入库。该发明虽然能有效地提高天然橡胶的一致性和稳定性,该专利得到的tsr9710橡胶杂质含量为0.05~0.07、门尼值为65~85,属于普通tsr9710橡胶制品,该tsr9710橡胶产品对于高抗氧化能的国际十大轮胎厂来说却无法使用。
4.高性能tsr9710橡胶产品的指标要求如下:
5.[0006][0007]
高性能tsr9710与普通tsr9710指标对比,主要体现在杂质含量低小于0.04%;灰分含量低于0.5%;塑性初值高大于38;抗氧化指数高大于70;门尼粘度大于80。
[0008]
目前生产高性能tsr9710天然橡胶的原料主要有两种形态,一种是液态的鲜胶乳,一种是在田间自然或者胶农自行加部分酸凝固的固体凝杂胶原料,这两种原料加工出来的产品在性能指标上有很大的不同。
[0009]
以鲜胶乳原料加工的tsr9710天然橡胶产品的p0、pri、杂质含量低,可以满足普通轮胎厂的要求,但是拉伸强度较低,在13-15之间,却不能满足高性能的要求;
[0010]
以凝杂胶原料生产tsr9710天然橡胶,由于在田间自然凝固的胶块,原料中含有大量的树叶、树皮,胶农自行加酸凝固的凝块,贮存的时间长短不一,所以造成凝杂胶原料每一批次差异大,生产出来的杂质含量超过0.05%,并且pri指标低,也不能满足高端轮胎厂要求。
技术实现要素:[0011]
针对现有技术的不足,本发明提供一种高性能tsr9710天然橡胶的制备工艺,本发明以鲜胶乳为原料,经过特定处理和工艺最终制备出符合指标的高性能tsr9710天然橡胶。
[0012]
为解决上述技术问题,本发明的技术方案如下:一种高性能tsr9710天然橡胶的制备工艺,其特征在于,所述制备工艺操作如下:鲜胶乳进行预处理,预处理后采用水线制备工艺得到高性能tsr9710天然橡胶;
[0013]
所述鲜胶乳预处理包括以下步骤:
[0014]
步骤(1)胶乳进厂称重,过滤,检查胶乳中凝粒情况(出现凝粒则胶乳变质),无凝粒情况则测干含并计算干胶数量,进而计算稀释加水量和计算凝固用酸量;
[0015]
步骤(2)将甲酸稀溶液与稀释后的胶乳一起并流加入长槽凝固;将长槽中的凝块熟化24-84小时,熟化时间过短物性指标达不到要求;熟化时间过长会降低pri。
[0016]
步骤(3)将熟化后的凝块压薄到6-7cm,将薄凝块锯成块,放在太阳下晾晒24-72小时,晾晒过程中翻一次;然后将凝块放入到阴凉的库区贮放;库区贮放时,每2-3天翻一遍原
料,保持库区干燥。
[0017]
作为优选,所述水线工艺操作如下:预处理得到的凝块破碎至20cm以下后进入第一混合池混合,经二次破碎至15cm以下进入第二混合池中混合,依次采用双辊挤洗至8cm以下混合,单辊挤洗至5cm以下混合;之后多次压绉和撕粒交替进行,重复1-5次;然后进行装箱、滴水,滴水后于110-125℃干燥4-5h;出车,胶温控制在50℃以内;称重打包,得到高性能tsr9710天然橡胶。
[0018]
作为优选,单辊挤洗混合后,进行三次压绉、撕粒至0.7cm以下,之后进行四次压绉、撕粒至0.7cm以下;再进行三次压绉、撕粒至0.7cm以下,之后进行四次压绉、撕粒至0.7cm以下。
[0019]
作为优选,所述三次压绉过程中,第一次压绉厚度不超过2cm,第二次压绉厚度不超过1.5cm;第三次压绉厚度不超过1.2cm。
[0020]
所述四次压绉过程中,第一次压绉厚度不超过2cm,第二次压绉厚度不超过1.5cm;第三次压绉厚度不超过1.2cm,第四次压绉厚度不超过1.0cm。
[0021]
作为优选,所述称重打包工序操作如下:将撕粒后的胶料进行称重,胶料重需控制在35.00
±
0.05kg,将称重后的胶料压制成长方体胶包,再进行复称,复称需控制胶包的重量为35.00
±
0.05kg;
[0022]
称重打包后进行质检工序,操作如下:复称后进行六面检查和抽检,对抽检的胶包进行对角取样,取样量为200
±
5g,按高性能tsr9710橡胶的各项指标要求进行质量检测,并对所有胶包进行金属检测,剔除不合格产品。
[0023]
作为优选,鲜胶乳预处理中胶乳稀释至27-32wt%,甲酸溶液的浓度为2.5-4wt%。作为进一步优选,胶乳稀释至27-30wt%,甲酸溶液的浓度为2.8-3.2wt%。
[0024]
作为优选,所述预处理过程中初始压薄片凉晒时检测拉伸强度及扯断伸长率,然后到5-8天检测一次,物性就达到指标要求,拉伸强度大于20,扯断伸长率大于700%,即能作为加工高性能tsr9710的原料;预处理后的凝块库区最长贮放时间不能超过14天。
[0025]
本发明的特点如下:高端轮胎厂对于制胶厂生产的tsr9710产品,提出沙道的问题,要求杂质非常低,并且不能有明显的肉眼可见沙粒异物,本发明申请人为了生产符合要求的产品,曾经用过wf的产品供给轮胎厂,但由于物性指标达不到要求,所以只能放弃,后来在原料无法解决的基础上,更改水线工艺流程,通过两次破碎混合、两次挤洗混合以及多次压绉撕粒多种途径共同作用,能够确保沙粒异物数量(杂质含量)能足要求。
[0026]
本发明还对于原料处理工艺做如下改进:控制胶乳稀释浓度和稀酸的浓度进行凝固,控制熟化时间、太阳晾晒时间以及原料总的贮存时间等,提高原料胶块的拉伸强度和门尼粘度等。其中,太阳晾晒时间和原料总的贮存时间长短对性能影响较大,如果晾晒时间超过72小时或者贮存时间超过14天,制得的产品pri、门尼粘度、和扯断伸长率均不满足要求。
[0027]
最后本发明通过研究原料预处理工艺和水线工艺,最终生产出既满足客户沙粒要求,又满足物性指标要求的高性能tsr9710产品。已发运两车产品给客户,客户对于沙粒异物没有提出异议,性能指标也满足要求。
[0028]
与现有技术相比,本发明具有以下有益效果:本发明通过对新鲜胶乳进行酸化凝固、熟化、晾晒和贮存多个节点进行控制,同时更改水线工艺流程,最终制得高性能tsr9710;本发明工艺制备方法成本低,工艺简单,不需要额外使用隔离剂等添加剂。本发明
制得的高性能tsr9710具有较高的拉伸强度和扯断伸长率,门尼粘度不低于85,杂质含量低于0.03%,具有良好的物理性能,满足高端轮胎客户需求。
附图说明
[0029]
图1为本实施例水线工艺流程图。
具体实施方式
[0030]
下面结合附图和具体实施例对本发明的技术方案做进一步详细说明,但本发明并不局限于以下技术方案。以下实施例选择鲜胶乳原料制做高性能9710产品,采用的新鲜胶乳为正常割胶收集送到胶厂加工的胶乳。
[0031]
实施例
[0032]
鲜胶乳预处理包括以下步骤:
[0033]
步骤(1)胶乳进厂称重
‑‑
过滤
‑‑
检测胶乳中凝粒情况,如无凝粒则向下操作
‑‑
测干含
‑‑
计算干胶数量
‑‑
计算稀释加水量(胶乳稀释浓度大于27%)
‑‑
计算凝固用酸量(甲酸用量按干胶重7-8公斤/吨计算,然后稀释到2.8-4wt%的浓度);
[0034]
步骤(2)将2.8-4wt%稀甲酸溶液与27-30%的稀释胶乳一起并流加入长槽凝固;将长槽中的凝块熟化24-84小时;
[0035]
步骤(3)将熟化后的长槽中凝块压薄到6-7cm(压片厚度),然后将薄凝块锯为一米一块,放在太阳下晒24-72小时,晾晒时间过短,原料水含量较大;晾晒时间超过72小时,会导致产品的门尼粘度和扯断伸长率下降,不能满足要求。晾晒过程中翻一次,晚上不需要收到库中;然后将凝块放入到荫凉的库区贮放;库区贮放时,每2-3天需要翻一遍原料,保持库区干燥;
[0036]
步骤(4)初始压薄片后凉晒前检测一次物性指标(拉伸强度及扯断伸长率),然后到7天检测一次,物性就达到指标要求了(拉伸强度大于20,扯断伸长率大于700),放在库中贮存用于加工产品;
[0037]
预处理后的凝块按照水线工艺操作,流程图如图1所示。所述水线工艺操作如下:从仓库取出预处理后的凝块将其破碎至20cm以下进入2号混合池混合,经二次破碎至15cm以下进入3号混合池中混合,依次采用双辊挤洗至8cm以下混合,单辊挤洗至5cm以下混合;单辊挤洗混合后,进行三次压绉、撕粒至0.7cm以下,之后进行四次压绉、撕粒至0.7cm以下;再进行三次压绉、撕粒至0.7cm以下,之后进行四次压绉、撕粒至0.7cm以下;
[0038]
所述三次压绉过程中,第一次压绉厚度不超过2cm,第二次压绉厚度不超过1.5cm;第三次压绉厚度不超过1.2cm。
[0039]
所述四次压绉过程中,第一次压绉厚度不超过2cm,第二次压绉厚度不超过1.5cm;第三次压绉厚度不超过1.2cm,第四次压绉厚度不超过1.0cm。
[0040]
然后进行装箱、滴水,滴水后于110-125℃干燥4-5h;出车,胶温控制在50℃以内;称重打包,所述称重打包工序操作如下:将撕粒后的胶料进行称重,胶料重需控制在35.00
±
0.05kg,将称重后的胶料压制成长方体胶包,再进行复称,复称需控制胶包的重量为35.00
±
0.05kg;
[0041]
称重打包后进行质检工序,操作如下:复称后进行六面检查和抽检,对抽检的胶包
进行对角取样,取样量为200
±
5g,按高性能tsr9710橡胶的各项指标要求进行质量检测,并对所有胶包进行金属检测,剔除不合格产品。
[0042]
按照上述工艺操作,本技术做出5批原料胶,每批原料的预处理操作工艺要点如表1所示。
[0043]
表1预处理操作工艺要点
[0044][0045][0046]
将上述五批原料预处理前,晾晒起7天和加工成tsr9710分别进行质量检测,试验方法按照表2中的国标方法进行检测,检测结果如表3-表5所示。
[0047]
表2检测标准
[0048][0049]
表3初始原料检测
[0050][0051]
表4 7天原料检测数据
[0052][0053]
表5加工后tsr9710成品检测指数
[0054][0055][0056]
由表3-表4可知,采用本技术预处理工艺处理鲜胶乳后,塑性初值、门尼粘度和拉伸强度均由较大提升,尤其是门尼粘度和拉伸强度。预处理后的凝块按照水线工艺生产tsr9710产品如表5所示,第二批、第四批和第五批均达到了指标要求,杂质含量均在0.03%以下,扯断伸长率均在730%以上,拉伸强度均在20mpa以上,门尼粘度均在85以上,达到了高性能tsr9710的指标要求,能够满足高端轮胎厂需求。
[0057]
由上述也可知,对于预处理工艺来讲,其核心控制点优选条件如下:胶乳稀释浓度27-30%;稀甲酸的浓度3%
±
0.2;熟化时间24-48小时;凝块在太阳晒24-72小时;通风的库区贮存7-14天;每3天翻一次,保持库区干燥,上述实验条件是生产合格高性能tsr9170的必要条件。
[0058]
由表5可看出第一批和第三批产品不合格,不合格原因主要是第一批原料在仓库贮存时间超过14天,导致pri、门尼粘度和扯断伸长率均达不到标准,而第三批的晾晒时间过长,超过72小时,导致门尼粘度和扯断伸长率达不到要求。因此太阳晾晒时间和原料总的贮存时间长短对tsr9710产品性能影响较大。
[0059]
以上所揭露的仅为本发明的较佳实施例而已,并不能以此来限定本发明之权利范围,因此依本发明权利要求所作的等同变化,仍属于本发明所涵盖的范围。