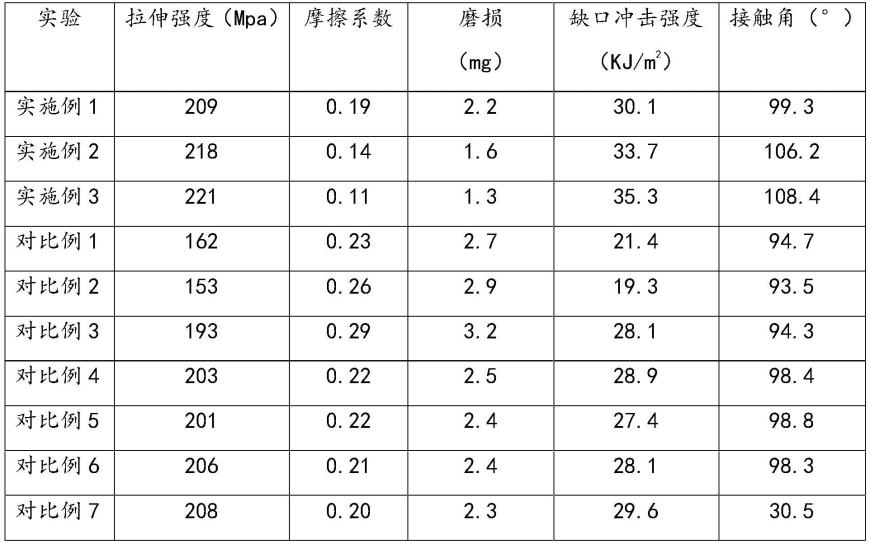
一种高强度超耐磨mc尼龙复合材料及其制备方法
技术领域
1.本发明涉及mc尼龙材料制备技术领域,具体涉及一种高强度超耐磨mc尼龙复合材料及其制备方法。
背景技术:2.mc尼龙又称单体浇铸尼龙(monomer casting nylon),是工程塑料的一种,它是在阴离子催化剂及活化剂存在的条件下,由单体直接浇铸于模具中聚合成型制得的。由于其生产工艺简单,聚合速度快,制品综合性能好,被广泛应用于机械、纺织、交通、石化、冶金等领域;可直接取代部分为铜、不锈钢、铝合金等金属制品,“以塑代钢、性能卓越”。多年来mc尼龙的滑轮、滑块、齿轮、蜗轮、托轮、支承轮、走轮、水泵叶轮、轴套、轴瓦、活阀体、挡胶板、皮带轮、转动轮、棒材、管材、板材等,不仅较好地取代了相应的金属品,降低了成本,并且延长了整机及零件的使用寿命,经济效益得到了显著的提高。
3.mc尼龙的机械强度、刚度、冲击强度和硬度等力学性能优于一般pa6。虽然其自润滑性能、耐磨性较好,但是纯mc尼龙在高载荷作用下使用时,摩擦系数偏高、体积磨损率也较大,在一些低温、高冲击的条件下,其缺口冲击强度较差,难以应用于一些对冲击性能要求较高的大型工程件上。难以满足在无油条件下的工况要求,这些不足限制了其在很多领域的应用。为了提高mc尼龙材料的抗磨减摩性能,通常在基体树脂中添加一些传统润滑剂,比如石墨、纳米管、碳纤维等固体润滑剂,但其分散困难,而且减摩抗磨程度也很有限。
技术实现要素:4.本发明的目的是针对现有技术中mc尼龙在高载荷作用下使用时强度和耐磨性等存在的不足,提供一种新型mc尼龙复合材料,通过在己内酰胺的工作体系中加入abs粉料、金属盐溶液、润滑剂、端羧基聚硅氧烷等,大幅度提高了mc尼龙的强度和耐磨性能。
5.为了实现上述目的,本技术采用如下技术方案:
6.一种高强度超耐磨mc尼龙复合材料,由以下重量份的各组分制成:己内酰胺80-120份,abs粉料2-5份,金属盐溶液0.1-0.3份,催化剂0.5-1.5份,改性润滑剂1-4份,活化剂1-3份,端羧基聚硅氧烷0.1-0.4份;所述abs粉料为300-600目;所述金属盐溶液为0.3-0.6mol/l的氯化锌或氯化铜水溶液;所述催化剂为氢氧化钠或甲醇钠;所述改性润滑剂由介孔二氧化铈、云母粉、桐油、氧化石墨烯纤维制备而成;所述活性剂为n-己酰基己内酰胺或2,4-甲苯二异氰酸酯。
7.优选的,所述己内酰胺100份,abs粉料3.5份,金属盐溶液0.2份,催化剂1.2份,润滑剂2份,活化剂2份,端羧基聚硅氧烷0.2份;所述abs粉料为400-500目;所述金属盐溶液为0.3mol/l的氯化锌水溶液;所述催化剂为氢氧化钠;所述活性剂为2,4-甲苯二异氰酸酯。
8.上述高强度超耐磨mc尼龙复合材料的制备方法,包括如下步骤:
9.s1:将10-20份介孔二氧化铈、2-5份氧化石墨烯纤维、3-5份云母粉和15-25份异丙醇加入反应容器中搅拌20-50min,再向其中加入4-8份桐油,于温度40-60℃超声分散1-3h
使其混合均匀,经离心洗涤干燥,得产物a;对产物a表面进行低温等离子体处理后,获得改性润滑剂;
10.s2:按重量比将在氮气的保护下己内酰胺加热熔融,随后加入abs粉料,升温熔融;再向其中加入金属盐溶液,搅拌反应;
11.s3:通入氮气解除真空,在常压下,按重量比向步骤s2中加入催化剂,继续抽真空;
12.s4:通入氮气解除真空,按重量比向步骤s3中加入步骤s1所得改性润滑剂和活化剂和端羧基聚硅氧烷搅拌均匀后,倒入预先加热的模具中,保温反应,冷却至室温后脱模,即可得高强度超耐磨mc尼龙复合材料。
13.优选的,步骤s1中所述二氧化铈的制备过程为:取0.5-1份氢氧化钠和10-20份乙醇溶液混合,在温度65-75℃下,边搅拌边滴加10-20份正硅酸四乙酯,滴加完毕后保温反应2-4h,离心、洗涤、干燥处理,得二氧化硅模板;将上述二氧化硅模板、3-6份聚乙烯吡咯烷酮和30-50份去离子水混合超声处理5-10min;再加入2-4份硝酸铈和3-6份六次甲基四胺,在温度80-90℃下反应2-3h,经离心、洗涤、干燥后,于温度550-650℃煅烧2.5-3.5h;后经氢氧化钠刻蚀8-12min,洗涤干燥即得二氧化铈。
14.优选的,所述介孔二氧化铈的制备过程具体为:取0.8份氢氧化钠和15份乙醇溶液混合,在温度70℃下,边搅拌边滴加16份正硅酸四乙酯,滴加完毕后保温反应3.5h,离心、洗涤、干燥处理,得二氧化硅模板;将上述二氧化硅模板、5份聚乙烯吡咯烷酮和45份去离子水混合超声处理8min;再加入3份硝酸铈和5份六次甲基四胺,在温度85℃下反应2.5h,经离心、洗涤、干燥后,于温度600℃煅烧3h;后经氢氧化钠刻蚀10min,洗涤干燥即得二氧化铈。
15.优选的,步骤s1中所述氧化石墨烯纤维的单丝直径为10-15μm,长度为4-8mm;所述表面进行低温处理的具体工艺为:按体积比0.8-1:0.8组成的co2和nh3混合气体,将产物a表面在温度50-60℃下进行低温等离子体处理。
16.优选的,步骤s1具体为将15份介孔二氧化铈、4份氧化石墨烯纤维、4份云母粉和22份异丙醇加入反应容器中搅拌35min,再向其中加入6份桐油,于温度55℃min超声分散2.5h使其混合均匀。
17.优选的,步骤s2具体为将己内酰胺在氮气的保护下于110-130℃加热熔融;按份数比向其中加入abs粉料,升温至170-180℃,再向其中加入金属盐溶液,搅拌反应1-2h。
18.优选的,步骤s3具体为加入催化剂,继续通氮气并于0.1-0.2mpa抽真空10-20min。
19.优选的,步骤s4具体按重量比向步骤s3中加入步骤s1所得润滑剂、活化剂和端羧基聚硅氧烷搅拌均匀后,倒入预先加热的模具中,完毕后保温30-40min,冷却至室温后脱模,其中,预热的模具温度为160-180℃。
20.有益效果:
21.1.本发明在制备润滑剂中,通过在二氧化硅模板表面包覆二氧化铈,经焙烧、氢氧化钠溶液蚀刻后制备得到了内部中空、具有较高的比表面积的二氧化铈;随后将内部中空的二氧化铈、氧化石墨烯纤维、云母粉混合,氧化石墨烯纤维和二氧化铈相互穿插缠绕,纤维在基体中起到骨架支撑的作用,二氧化铈可有效强化基体,实现增强体之间的优势互补和耦合效应,从而提高复合材料的强度及耐磨性。同时将云母粉、桐油填充其中,形成了氧化石墨烯纤维/二氧化铈为壳、云母粉/桐油为芯改性润滑剂结构。在温度、摩擦载荷作用下,云母粉的滑动性以及桐油流出,能够在摩擦表面形成连续均匀的润滑膜,进而提高了制
品的耐磨性能。
22.2.为了提高润滑剂与己内酰胺工作体系的连接强度,本发明对改性剂表面采用低温等离子体处理,使其表面获得羟基、羧基、胺基等极性基团,通过化学键连接,提高结合力,更好地发挥协同效应。
23.3.本发明在己内酰胺工作体系中加入abs粉料和金属盐溶液,利用abs粉料提高抗冲击性能等同时,通过酰胺基团与金属盐中的金属离子发生络合配位,影响分子链间的氢键作用,降低结晶度,保证强度的同时提高耐摩擦性能。
24.4.本发明采用端羧基聚硅氧烷(frcas),对其表面进行修饰,进一步提高尼龙材料表面的疏水性能,使其拥有较好的疏水效果。
具体实施方式
25.以下结合下述实施方式进一步说明本发明,下述实施方式仅用于说明本发明,而非限制本发明。
26.实施例1
27.s1:取0.5g氢氧化钠和10g乙醇溶液混合,在温度65℃下,边搅拌边滴加10g正硅酸四乙酯,滴加完毕后保温反应2h,离心、洗涤、干燥处理,得二氧化硅模板;将上述二氧化硅模板、3g聚乙烯吡咯烷酮和30g去离子水混合超声处理5min;再加入2g硝酸铈和3g六次甲基四胺,在温度80℃下反应2h,经离心、洗涤、干燥后,于温度550℃煅烧2.5h;后经氢氧化钠刻蚀8min,洗涤干燥即得二氧化铈;
28.将10g二氧化铈、2g氧化石墨烯纤维、3g云母粉和15g异丙醇加入反应容器中搅拌20min,所述氧化石墨烯纤维的单丝直径为10μm,长度为8mm;再向其中加入4g桐油,于温度40℃超声分散1h使其混合均匀,经离心洗涤干燥,得产物a;按体积比1:0.8组成的co2和nh3混合气体,将产物a表面在温度50℃下进行低温等离子体处理后,获得改性润滑剂;
29.s2:取80g己内酰胺、5gabs粉料和0.1g金属盐溶液,将80g己内酰胺在氮气的保护下于110℃加热熔融;随后加入abs粉料,升温至170℃,再向其中加入0.1g的0.3mo l/l的氯化锌水溶液,搅拌反应2h;
30.s3:通入氮气解除真空,在常压下,向步骤s2中加入0.5g氢氧化钠,继续通氮气并于0.1mpa抽真空10min;
31.s4:通入氮气解除真空,向步骤s3中加入步骤s1所得1g改性润滑剂、1gn-己酰基己内酰胺和0.1g端羧基聚硅氧烷,搅拌均匀,得混合物;将模具预热至160℃,向其中倒入混合物,保温反应30min,冷却至室温后脱模,即可得高强度超耐磨mc尼龙复合材料。
32.实施例2
33.s1:取1g氢氧化钠和20g乙醇溶液混合,在温度75℃下,边搅拌边滴加20g正硅酸四乙酯,滴加完毕后保温反应4h,离心、洗涤、干燥处理,得二氧化硅模板;将上述二氧化硅模板、6g聚乙烯吡咯烷酮和50g去离子水混合超声处理10min;再加入4g硝酸铈和6g六次甲基四胺,在温度90℃下反应3h,经离心、洗涤、干燥后,于温度650℃煅烧3.5h;后经氢氧化钠刻蚀12min,洗涤干燥即得二氧化铈;
34.将20g二氧化铈、5g氧化石墨烯纤维、5g云母粉和25g异丙醇加入反应容器中搅拌50min,所述氧化石墨烯纤维的单丝直径为15μm,长度为8mm;再向其中加入8g桐油,于温度
60℃超声分散3h使其混合均匀,经离心洗涤干燥,得产物a;按体积比1:1组成的co2和nh3混合气体,将产物a表面在温度60℃下进行低温等离子体处理后,获得改性润滑剂;
35.s2:取120g己内酰胺、5gabs粉料和0.3g金属盐溶液,将120g己内酰胺在氮气的保护下于130℃加热熔融;随后加入abs粉料,升温至180℃,再向其中加入0.3g的0.6mol/l的氯化铜水溶液,搅拌反应2h;
36.s3:通入氮气解除真空,在常压下,向步骤s2中加入1.5g甲醇钠,继续通氮气并于0.1-0.2mpa抽真空10-20min;
37.s4:通入氮气解除真空,向步骤s3中加入步骤s1所得4g改性润滑剂、3g2,4-甲苯二异氰酸酯和0.4g端羧基聚硅氧烷,搅拌均匀,得混合物;将模具预热至180℃,向其中倒入混合物,保温反应40min,冷却至室温后脱模,即可得高强度超耐磨mc尼龙复合材料。
38.实施例3
39.s1:取0.8g氢氧化钠和15g乙醇溶液混合,在温度70℃下,边搅拌边滴加16g正硅酸四乙酯,滴加完毕后保温反应3.5h,离心、洗涤、干燥处理,得二氧化硅模板;将上述二氧化硅模板、5g聚乙烯吡咯烷酮和45g去离子水混合超声处理8min;再加入3g硝酸铈和5g六次甲基四胺,在温度85℃下反应2.5h,经离心、洗涤、干燥后,于温度600℃煅烧3h;后经氢氧化钠刻蚀10min,洗涤干燥即得二氧化铈;
40.将15g二氧化铈、4g氧化石墨烯纤维、4g云母粉和22g异丙醇加入反应容器中搅拌35min,所述氧化石墨烯纤维的单丝直径为12μm,长度为6mm;再向其中加入7g桐油,于温度55℃超声分散2.5h使其混合均匀,经离心洗涤干燥,得产物a;按体积比0.9:0.8组成的co2和nh3混合气体,将产物a表面在温度53℃下进行低温等离子体处理后,获得改性润滑剂;
41.s2:将100g己内酰胺在氮气的保护下于115℃加热熔融;随后加入3.5gabs粉料,升温至175℃,再向其中加入0.2g的0.45mol/l的氯化锌水溶液,搅拌反应1.5h;
42.s3:通入氮气解除真空,在常压下,向步骤s2中加入1.2g氢氧化钠,继续通氮气并于0.16mpa抽真空15min;
43.s4:通入氮气解除真空,向步骤s3中加入步骤s1所得2g改性润滑剂、2gn-己酰基己内酰胺和0.2g端羧基聚硅氧烷,搅拌均匀,得混合物;将模具预热至175℃,向其中倒入混合物,保温反应35min,冷却至室温后脱模,即可得高强度超耐磨mc尼龙复合材料。
44.对比例1
45.与实施例1的区别在于,步骤s1中直接采用普通的二氧化铈,而非中空型二氧化铈,其他步骤和条件不变。
46.比照对比例1和实施例可知,因未形成内部中空的二氧化铈,氧化石墨烯纤维未能与二氧化铈相互穿插缠绕,未能有效实现纤维和二氧化铈增强体之间耦合效应,复合材料的强度及耐磨性明显降低。
47.对比例2
48.与实施例1的区别在于,步骤s1中未加入氧化石墨烯纤维,其他步骤和条件不变。
49.比照对比例1和实施例可知,由于缺少氧化石墨烯纤维,仅有二氧化铈,支撑性减弱,复合材料的强度及耐磨性有所降低。
50.对比例3
51.与实施例1的区别在于,步骤s1中未加入桐油,其他步骤和条件不变。
52.比照对比例1和实施例可知,由于缺少桐油,未能形成氧化石墨烯纤维/二氧化铈为壳、云母粉/桐油为芯改性润滑剂结构,在温度、摩擦载荷作用下,无桐油流出形成连续均匀的润滑膜,复合材料的耐磨性能明显降低。
53.对比例4
54.与实施例1的区别在于,步骤s1中未加入云母粉,其他步骤和条件不变。
55.比照对比例1和实施例可知,由于缺少云母粉,在温度、摩擦载荷作用下,缺少云母粉的滑动,复合材料的耐磨性能略有降低。
56.对比例5
57.与实施例1的区别在于,步骤s1中未对改性剂表面采用低温等离子体处理,其他步骤和条件不变。
58.比照对比例1和实施例可知,由于未经过低温等离子体处理表面获得羟基、羧基、胺基等极性基团,改性剂和体系的结合力减弱,复合材料的强度及耐磨性有所降低。
59.对比例6
60.与实施例1的区别在于,步骤s2中未加入金属盐溶液,其他步骤和条件不变。
61.比照对比例1和实施例可知,由于未加入金属盐溶液,酰胺基团与金属盐中的金属离子无法经络合配位降低其结晶度,耐摩擦性能有所降低。
62.对比例7
63.与实施例1的区别在于,步骤s4中未采用端羧基聚硅氧烷进行表面修饰,其他步骤和条件不变。
64.比照对比例1和实施例可知,由于缺少硅氧基团,表面的疏水性能明显下降。
65.将实施例和对比例所得mc尼龙复合材料加工成测试试样;
66.将上述实施例及对比例制得的产品采用万能试验机测试其性能,拉伸性能的测试:gb1040/t-1992,塑料拉伸性能试验方法,拉伸速度5mm/min;缺口冲击强度按gb/t10432008测试;摩擦系数:按gb3960-1983标准测试,施加20千克力,45#钢对磨环;磨损:按gb3960-1983标准测试,施加20千克力,45#钢对磨环,时间2小时。接触角:使用接触角计(协和界面科学株式会社制,dmo-601),在温度为25℃,相对湿度为50%的气氛中,测量所得到表面的纯水的接触角。
[0067][0068]
以上所述仅为本发明的较佳实施方式,本发明的保护范围并不以上述实施方式为限,但凡本领域普通技术人员根据本发明所揭示内容所作的等效修饰或变化,皆应纳入权利要求书中记载的保护范围内。