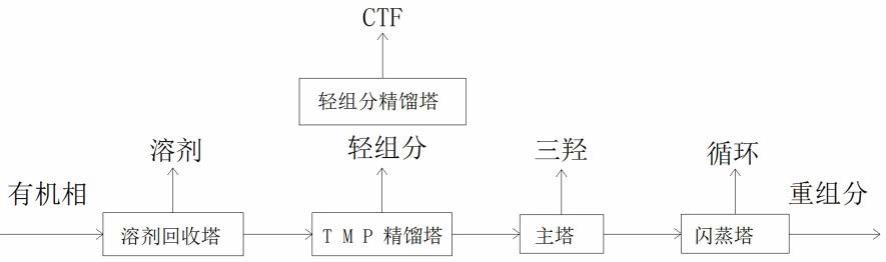
1.本发明属于化工生产方法技术领域,具体的说是涉及一种三羟甲基丙烷多塔串联萃取精馏除杂精制的方法。
背景技术:2.甲醛、正丁醛在氢氧化钙的条件下,发生缩合反应生成三羟甲基丙烷。缩合副反应产生高沸点杂质和低沸点杂质。生产中根据杂质沸点的不同,采用精馏的方式进行分离。现有技术中传统的精馏工艺,轻组分分离不彻底,三羟甲基丙烷中含有部分轻组分,采出的三羟甲基丙烷含量较低,不能满足生产要求。缩合副反应生成部分重组分,重组分粘度高,分离难,易夹带三羟及双三羟,影响双三羟产量和质量。现有技术中的产品质量仅能够达到99.1%。
技术实现要素:3.本发明为了克服现有技术存在的不足,提供一种三羟甲基丙烷多塔串联萃取精馏除杂精制的方法。
4.本发明是通过以下技术方案实现的:本发明公开了一种三羟甲基丙烷多塔串联萃取精馏除杂精制的方法,在钙法三羟甲基丙烷生产中,利用多塔串联和负压反应精馏除杂精制,分离轻组分,同时利用精馏系统的热能,用酸性催化剂反应处理重组分,从而得到有经济价值的三羟甲基丙烷环状缩甲醛ctf;本发明萃取精馏除杂精制的方法具体包括如下步骤:(1)萃取:缩合液经过提浓分离甲酸钙后得到精制原料,向精制原料中加入溶剂萃取精制原料中的有机相与水相分离;(2)溶剂回收塔:塔釜温度180℃~190℃,塔顶温度115℃~125℃,回收溶剂;(3)tmp精馏塔:向脱除溶剂的有机相中加入酸性催化剂进入tmp精馏塔,塔釜温度180℃~190℃,塔顶温度110℃~130℃,在高温下处理高沸点杂质得到ctf与物料中的轻组分从塔顶分离一同进入轻组分回收塔,,塔釜物料进入tmp主塔;(4)主塔:塔釜温度180℃~190℃,塔顶温度110℃~130℃,物料基本为三羟甲基丙烷,通过精馏精制,含量达到99.5%;(5)闪蒸塔:主塔内塔釜物料以高沸点杂质及双三羟为主,含少量三羟甲基丙烷,通过闪蒸回收部分三羟。
5.作为本发明的优选实施方式,步骤(1)萃取中,精制原料与酸性催化剂的比例为15~20:1。酸性催化剂为甲酸、乙酸、磷酸、次磷酸、甲基磺酸和阳离子交换树脂中的一种或几种。
6.塔釜进入主塔回收三羟,主塔侧线回流采出tmp;通过这种精馏的方式,三羟产品质量达到99.5%,主塔塔釜闪蒸得到少量重组分,得到双三羟甲基丙烷粗品。
7.作为本发明的优选实施方式,步骤(2)溶剂回收塔中,塔釜温度185℃,塔顶温度
120℃。步骤(3)tmp精馏塔中,塔釜温度185℃,塔顶温度120℃。步骤(4)主塔中,塔釜温度185℃,塔顶温度120℃。
8.本发明方法主要用到的设备有用于回收溶剂的溶剂回收塔、用于分离轻组分的tmp精馏塔、用于提高三羟甲基丙烷质量的tmp主塔以及用于回收残余三羟甲基丙烷的闪蒸塔。
9.本发明的有益效果是:本发明三羟甲基丙烷采用多塔串联与反应精馏除杂精制共同精制,公开了一种三羟甲基丙烷多塔串联、萃取精馏除杂精制的方法,本发明采用多塔串联工艺,先经过溶剂回收塔回收溶剂,脱出溶剂后物料进入tmp精馏塔分离物料中的轻组分,在进料过程中添加酸性催化剂,利用tmp精馏塔塔底的热能,分解重组分,生成有经济价值的ctf,随轻组分进入轻组分精馏塔。钙法三羟甲基丙烷生产中,产生较多的高沸点杂质(重组分),采用反应催化精馏技术,选用合适的催化剂去除部分高沸点杂质。高沸点杂质易溶于有机溶剂,采用多塔串联技术,提高精馏分离效率,提高三羟甲基丙烷精馏质量。本发明利用自动控制,减少精馏塔波动,通过以上措施得到的三羟甲基丙烷质量能够达到99.5%。
附图说明
10.图1是三羟甲基丙烷多塔串联萃取精馏除杂精制方法的流程方框图。
具体实施方式
11.以下结合附图和具体实施方式对本发明作详细描述。
12.实施例1:如图1所示,萃取后的有机相(60℃)先经过溶剂回收塔,塔顶(110℃)回收溶剂,塔釜(180℃)脱溶剂后物料。按物料:酸性催化剂=15:1添加酸性催化剂,酸性催化剂为甲酸、乙酸、磷酸、次磷酸、甲基磺酸和阳离子交换树脂等,进入tmp精馏塔, tmp精馏塔塔顶(温度110℃)分离物料中的轻组分,进入轻组分精馏塔。tmp精馏塔的塔釜温度180℃,反应分解重组分,得到ctf,由塔顶进入轻组分精馏塔精制。tmp精馏塔反应后的物料进入主塔回收三羟,主塔塔顶温度110℃,主塔侧线回流采出tmp,得到的三羟产品质量达到99.5%。主塔的塔釜温度180℃,去闪蒸塔。闪蒸塔塔釜得到重组分,塔顶循环利用。
13.实施例2:如图1所示,萃取后的有机相(72℃)先经过溶剂回收塔,塔顶(115℃)回收溶剂,塔釜(185℃)脱溶剂后物料,按物料:酸性催化剂=18:1添加酸性催化剂(甲酸、乙酸、磷酸、次磷酸、甲基磺酸或阳离子交换树脂等),进入tmp精馏塔,塔顶(温度125℃)分离物料中的轻组分,进入轻组分精馏塔。塔釜温度185℃,反应分解重组分,得到ctf,由塔顶进入轻组分精馏塔精制(精制塔塔顶采出65%的ctf),反应后的物料进入主塔回收三羟,塔顶温度115℃,主塔侧线回流采出tmp,得到的三羟产品质量达到99.5%,塔釜温度190℃,去闪蒸塔闪蒸,得到重组分,塔顶循环利用。
14.实施例3:如图1所示,萃取后的有机相(90℃)先经过溶剂回收塔,塔顶(125℃)回收溶剂,塔釜(190℃)脱溶剂后物料。按物料:酸性催化剂=20:1添加酸性催化剂,酸性催化剂为甲酸、乙酸、磷酸、次磷酸、甲基磺酸和阳离子交换树脂等,进入tmp精馏塔, tmp精馏塔塔顶(温度130℃)分离物料中的轻组分,进入轻组分精馏塔。tmp精馏塔的塔釜温度190℃,反应分解重组分,得到ctf,由塔顶进入轻组分精馏塔精制。tmp精馏塔反应后的物料进入主
塔回收三羟,主塔塔顶温度130℃,主塔侧线回流采出tmp,得到的三羟产品质量达到99.5%。主塔的塔釜温度190℃,去闪蒸塔。闪蒸塔塔釜得到重组分,塔顶循环利用。
15.最后应当说明的是,以上内容仅用以说明本发明的技术方案,而非对本发明保护范围的限制,本领域的普通技术人员对本发明的技术方案进行的简单修改或者等同替换,均不脱离本发明技术方案的实质和范围。
技术特征:1.一种三羟甲基丙烷多塔串联萃取精馏除杂精制的方法,其特征在于:在钙法三羟甲基丙烷生产中,利用多塔串联和负压反应精馏除杂精制,分离轻组分,同时利用精馏系统的热能,用酸性催化剂反应处理重组分,从而得到有经济价值的三羟甲基丙烷环状缩甲醛ctf;所述萃取精馏除杂精制的方法具体包括如下步骤:(1)萃取:缩合液经过提浓分离甲酸钙后得到精制原料,向精制原料中加入溶剂,萃取物料中的三羟甲基丙烷、双三羟甲基丙烷以及高沸点杂质等有机相与水相分离;(2)溶剂回收塔:萃取后的有机相进入溶剂回收塔,塔釜温度180℃~190℃,塔顶温度115℃~125℃,回收溶剂;(3)tmp精馏塔:向脱除溶剂后的物料中加入酸性催化剂,进入tmp精馏塔,塔釜温度180℃~190℃,塔顶温度110℃~130℃,在高温下处理高沸点杂质得到ctf与物料中的轻组分从塔顶分离一同进入轻组分回收塔,塔釜物料进入tmp主塔;(4)主塔:塔釜温度180℃~190℃,塔顶温度110℃~130℃,物料基本为三羟甲基丙烷,通过精馏精制,含量达到99.5%;(5)闪蒸塔:主塔内的塔釜物料以高沸点杂质及双三羟为主,含少量三羟甲基丙烷,通过闪蒸回收部分三羟。2.根据权利要求1所述的一种三羟甲基丙烷多塔串联萃取精馏除杂精制的方法,其特征在于:所述步骤(1)萃取中,脱除溶剂后的物料与酸性催化剂的比例为15~20:1。3.根据权利要求1或2所述的一种三羟甲基丙烷多塔串联萃取精馏除杂精制的方法,其特征在于:所述酸性催化剂为甲酸、乙酸、磷酸、次磷酸、甲基磺酸和阳离子交换树脂中的一种或几种。4.根据权利要求1或2所述的一种三羟甲基丙烷多塔串联萃取精馏除杂精制的方法,其特征在于:塔釜进入主塔回收三羟,主塔侧线回流采出tmp;通过这种精馏的方式,三羟产品质量达到99.5%,主塔塔釜闪蒸得到少量重组分,得到双三羟甲基丙烷粗品。5.根据权利要求1或2所述的一种三羟甲基丙烷多塔串联萃取精馏除杂精制的方法,其特征在于:步骤(2)溶剂回收塔中,塔釜温度185℃,塔顶温度120℃。6.根据权利要求1或2所述的一种三羟甲基丙烷多塔串联萃取精馏除杂精制的方法,其特征在于:步骤(3)tmp精馏塔中,塔釜温度185℃,塔顶温度120℃。7.根据权利要求1或2所述的一种三羟甲基丙烷多塔串联萃取精馏除杂精制的方法,其特征在于:步骤(4)主塔中,塔釜温度185℃,塔顶温度120℃。
技术总结本发明公开了一种三羟甲基丙烷多塔串联萃取精馏除杂精制的方法,在钙法三羟甲基丙烷生产中,利用多塔串联和负压反应精馏除杂精制,分离轻组分,同时利用精馏系统的热能,用酸性催化剂反应处理重组分,从而得到有经济价值的三羟甲基丙烷环状缩甲醛CTF。本发明方法具体包括萃取、溶剂回收塔、TMP精馏塔、主塔和闪蒸塔这5个步骤。在钙法三羟甲基丙烷生产中,产生较多的高沸点杂质,采用反应催化精馏技术,选用合适的催化剂去除部分高沸点杂质。高沸点杂质易溶于有机溶剂,采用多塔串联技术,提高精馏分离效率,提高三羟甲基丙烷精馏质量。本发明利用自动控制,减少精馏塔波动,通过以上措施得到的三羟甲基丙烷质量能够达到99.5%。措施得到的三羟甲基丙烷质量能够达到99.5%。措施得到的三羟甲基丙烷质量能够达到99.5%。
技术研发人员:叶陆仟 杨秀国 李鸿雁 全宏冬 李权 周椿杰 李小鹤 解田 杨立方 陈晓玲
受保护的技术使用者:赤峰瑞阳化工有限公司
技术研发日:2022.12.16
技术公布日:2023/3/28