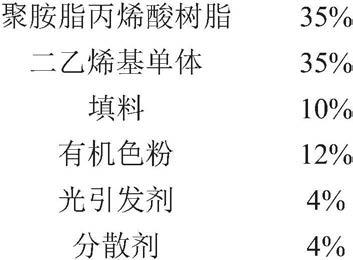
1.本发明涉及铅蓄电池材料技术领域,特别是涉及一种紫外光固化色胶及其制备方法。
背景技术:2.铅蓄电池的组装时,需要在塑壳上添加底胶完成塑壳中盖体和槽体的装配,之后又需要在盖体顶面的胶槽中滴加色胶,两次胶水的使用需要进2次烘灶窑进行胶水的高温固化,使得产线效率低,并且功耗大,同时占地面积又大,总体成本偏高。
3.比如,公开号为cn109735269a的发明公开了一种铅蓄电池用的丙烯酸树脂胶水、制备方法及铅蓄电池。所述丙烯酸树脂胶水,其原料配方包括以下重量份的组分:丙烯酸异辛酯130~140份、丙烯酸异丁酯25~30份、丙烯酸异甲酯15~20份、羟乙酯10~15份、甘油酯0.5~1份、丙烯酸1~2份、有机溶剂200~260份、引发剂0.3~0.5份、过氧化al
13
n 0.1~0.5份。
4.公开号为cn110718651a的发明公开了一种蓄电池端子二合一胶水,包括有a胶:环氧树脂:50~70%、稀释剂:20~30%、颜料:5%~8%,b胶:聚酰胺:60~80%、稀释剂:20~40%。蓄电池两个端子分别采用两种不同的a胶,两种不同的a胶的颜料不同,分别为红色颜料和蓝色颜料,分别对应正极端子和负极端子,起到标识作用。a胶和b胶分开存储,涂胶时再混合。使用时,包括有以下步骤:步骤一:首先进行焊端子,在蓄电池的电极处焊接上接电的两个端子;步骤二:量取同量的a胶和b胶,充分搅拌混合在一起,得到二合一胶水;步骤三:搅拌后的二合一胶水涂在蓄电池的两个端子处,避免多涂;步骤四:将涂胶后的蓄电池运输到固化室内进行固化,得到涂胶密封端子后的蓄电池;步骤五:对涂胶密封端子后的蓄电池进行气密性检测,合格出料,不合格,返修。
5.光固化技术只需要进行光照就能完成固化,但目前光固化技术有2个门槛,一方面是做不了厚度,绝大多数只能形成薄膜,第二方面是硬度和防酸性能弱。
技术实现要素:6.本发明针对现有技术中存在的上述不足,提供了一种用于铅蓄电池端子处胶槽内的色胶,为一种紫外光固化色胶,不用分成a胶合b胶两种组分,且固化时不需要进烘箱进行高温固化,只需要进行紫外光照射即能完成固化。
7.一种紫外光固化色胶,包括以下质量百分比的组分:
8.聚胺脂丙烯酸树脂45%;
9.二乙烯基单体25%;
10.填料10%;
11.有机色粉10%;
12.光引发剂4%;
13.分散剂4%;
14.玻璃纤维2%。
15.优选的,所述填料为铝硅酸盐。铝硅酸盐具备高强度、高透光度和高硬度的特点。铝硅酸盐是一类无机物,分子式为xal2o3·
ysio2,外观为无色晶体,氧化铝和氧化硅的比例不恒定。本技术中氧化铝∶氧化硅=1∶1,即两者摩尔比为1∶1。
16.优选的,所述光引发剂为三芳基硫鎓盐。更优选的,三芳基硫鎓盐具体为三芳基锍六氟磷酸盐。三芳基硫鎓盐的热稳定性好,加热至300℃不分解,与单体混合加热也不会引发聚合。
17.优选的,所述分散剂为丙烯酸酯和聚氨酯的混合物。更优选的,丙烯酸酯和聚氨酯按质量比1∶1混合。丙烯酸酯和聚氨酯相容性很好,因为具有很好的空间位阻效应,可以有效防止硬沉淀发生,防沉的效果非常好。
18.优选的,所述有机色粉为耐晒大红或永固黄,其中耐晒大红为红色,用于作为电池正极颜色;永固黄为黄色,用于作为电池负极颜色。
19.本发明又提供了所述紫外光固化色胶在作为铅蓄电池生产时色胶槽内色胶的应用。
20.本发明还提供了所述紫外光固化色胶的制备方法,包括以下步骤:
21.(1)在二乙烯基单体中逐渐添加分散剂,边搅拌边添加,混合均匀;
22.(2)在聚胺脂丙烯酸树脂中添加步骤(1)获得的添加了分散剂的二乙烯基单体,搅拌均匀;
23.(3)然后再向步骤(2)得到的产物中,添加光引发剂、填料和玻璃纤维,搅拌均匀;
24.(4)添加有机色粉,搅拌均匀;
25.(5)使用时,将步骤(4)得到的产物滴加到电池的胶槽中,然后进行紫外光进行光照,完成固化。紫外光照射时间不小于3min。固化厚度由成分决定,紫外光照达到一定时长后,再增加照射时间固化的厚度也不再增加。
26.同现有技术相比,本发明的有益效果体现在:
27.(1)聚胺脂丙烯酸树脂、二乙烯基单体100%固含量,无溶剂挥发,无碳排放,保护环境;
28.(2)固化条件是用紫外固化灯,固化速度很快3min即可完成,热功耗很小,提高成产效率,节省能源;
29.(3)整个生产装置设计就更加紧凑,容易加工,节省场地面积,提高空间利用率;
30.(4)形成的一体色胶,硬度,防酸腐蚀性能良好。
具体实施方式
31.实施例1
32.调配紫外光固化色胶,包括以下质量百分比的组分:
[0033][0034]
其中,填料是:铝硅酸盐(氧化铝∶氧化硅=1∶1);光引发剂是:三芳基锍六氟磷酸盐;分散剂是丙烯酸酯和聚氨酯(质量各占比50%);有机色粉是耐晒大红(红色)和永固黄(黄色),分别作为电池正、负极颜色。
[0035]
以总体100g为单位,各组分的添加量按上述比例添加,调配特种光固化一体色胶:
[0036]
(1)在二乙烯基单体中逐渐添加分散剂,搅拌速度控制在400转/min;
[0037]
(2)在聚胺脂丙烯酸树脂中添加步骤(1)获得的添加了分散剂的二乙烯基单体,搅拌速度控制在200转/min;保证主体材料的粘稠度;
[0038]
(3)然后再向步骤(2)得到的产物中,添加光引发剂和填料,搅拌均匀;
[0039]
(4)添加有机色粉,保证材料颜色均匀度一致,用于正、负极的色胶分别添加一种颜色的有机色粉。
[0040]
(5)最后进行紫外光进行光照:把选用添加红色和黄色色浆(有机色粉)的紫外光固化色胶分别倒入玻璃管中,光源从正上方照射3分钟,红色材料固化厚度达到5mm,黄色材料达到5mm。防酸、密封性、硬度等性能均达不到。
[0041]
实施例2
[0042]
调配紫外光固化色胶,包括以下质量百分比的组分:
[0043][0044]
其中,填料是:铝硅酸盐(氧化铝∶氧化硅=1∶1);光引发剂是:三芳基锍六氟磷酸盐;分散剂是丙烯酸酯和聚氨酯(质量各占比50%);有机色粉是耐晒大红(红色)和永固黄(黄色),分别作为电池正、负极颜色。
[0045]
以总体100g为单位,各组分的添加量按上述比例添加,调配特种光固化一体色胶:
[0046]
(1)在二乙烯基单体中逐渐添加分散剂,搅拌速度控制在400转/min;
[0047]
(2)在聚胺脂丙烯酸树脂中添加步骤(1)获得的添加了分散剂的二乙烯基单体,搅拌速度控制在200转/min;保证主体材料的粘稠度;
[0048]
(3)然后再向步骤(2)得到的产物中,添加光引发剂和填料,搅拌均匀;
[0049]
(4)添加有机色粉,保证材料颜色均匀度一致,用于正、负极的色胶分别添加一种
颜色的有机色粉。
[0050]
(5)最后进行紫外光进行光照:把选用添加红色和黄色色浆(有机色粉)的紫外光固化色胶分别倒入玻璃管中,光源从正上方照射3分钟,红色材料固化厚度达到5mm,黄色材料达到5mm。防酸、密封性、硬度等性能均达不到。
[0051]
实施例3
[0052]
调配紫外光固化色胶,包括以下质量百分比的组分:
[0053][0054]
其中,填料是:铝硅酸盐(氧化铝∶氧化硅=1∶1);光引发剂是:三芳基锍六氟磷酸盐;分散剂是丙烯酸酯和聚氨酯(质量各占比50%);有机色粉是耐晒大红(红色)和永固黄(黄色),分别作为电池正、负极颜色。
[0055]
以总体100g为单位,各组分的添加量按上述比例添加,调配特种光固化一体色胶:
[0056]
(1)在二乙烯基单体中逐渐添加分散剂,搅拌速度控制在400转/min;
[0057]
(2)在聚胺脂丙烯酸树脂中添加步骤(1)获得的添加了分散剂的二乙烯基单体,搅拌速度控制在200转/min;保证主体材料的粘稠度;
[0058]
(3)然后再向步骤(2)得到的产物中,添加光引发剂和填料,搅拌均匀;
[0059]
(4)添加有机色粉,保证材料颜色均匀度一致,用于正、负极的色胶分别添加一种颜色的有机色粉。
[0060]
(5)最后进行紫外光进行光照:把选用添加红色和黄色色浆(有机色粉)的紫外光固化色胶分别倒入玻璃管中,光源从正上方照射3分钟,红色材料固化厚度达到20mm,黄色材料达到8mm。硬度可以,但防酸、密封性性能不佳。
[0061]
实施例4
[0062]
调配紫外光固化色胶,包括以下质量百分比的组分:
[0063][0064]
其中,填料是:铝硅酸盐(氧化铝∶氧化硅=1∶1);光引发剂是:三芳基锍六氟磷酸盐;分散剂是丙烯酸酯和聚氨酯(质量各占比50%);有机色粉是耐晒大红(红色)和永固黄
(黄色),分别作为电池正、负极颜色。
[0065]
以总体100g为单位,各组分的添加量按上述比例添加,调配特种光固化一体色胶:
[0066]
(1)在二乙烯基单体中逐渐添加分散剂,搅拌速度控制在400转/min;
[0067]
(2)在聚胺脂丙烯酸树脂中添加步骤(1)获得的添加了分散剂的二乙烯基单体,搅拌速度控制在200转/min;保证主体材料的粘稠度;
[0068]
(3)然后再向步骤(2)得到的产物中,添加光引发剂、填料和玻璃纤维,搅拌均匀;
[0069]
(4)添加有机色粉,保证材料颜色均匀度一致,用于正、负极的色胶分别添加一种颜色的有机色粉。
[0070]
(5)最后进行紫外光进行光照:把选用添加红色和黄色色浆(有机色粉)的紫外光固化色胶分别倒入玻璃管中,光源从正上方照射3分钟,红色材料固化厚度达到25mm,黄色材料达到11mm。基本性能显示优异。
[0071]
实施例5
[0072]
对实施例1~4制备的4种紫外光固化色胶(每种分红、黄两种颜色)进行性能检测,检测项目为:(1)附着力(gb/t1720)、(2)冲击(gb/t1732)、(3)漆膜硬度(5b
‑
4h/gb6739)、(4)耐溶剂(gb/t23989
‑
2009a)、(5)正面涂层厚度、(6)密封性、(7)滴酸测试。
[0073]
其中第(1)~(4)项按相应国标方法进行检测。(5)正面涂层厚度检测在经紫外光光照固化完成紫外光固化色胶的制备后,直接用尺量。
[0074]
(6)密封性检验:
[0075]
将浇铸完24h内的铅极柱放入塑料容器内,将配好的密封胶导入容器,使极柱有部分裸露在密封胶外,然后将试样在55
‑
60℃下固化2h,固化后带有铅极柱的环氧快树脂在80℃环境下浸泡在1.35g/cm3(25℃)硫酸溶液中48h,取出清液,烘干后强行将环氧树脂与铅极柱分开,观察铅极柱与环氧树脂接触面状况。
[0076]
铅极柱与环氧树脂接触面需有轻微被破坏的痕迹且为光亮富有金属光泽,没有腐蚀痕迹。
[0077]
(7)耐酸性的检验:
[0078]
样品冷却至室温,检查外观合格后。在固话号的样块上,滴上1.35g/cm3(25℃)硫酸2
‑
3滴。将样块放置在干净的玻璃杯内,烧杯内用表面皿或缠绕膜密封,置于60℃烘箱中48h,然后取出冷却室温,再以自来水冲洗干净,晾干。检查样块变化:
[0079]
a)样块表面滴酸处虽有液痕,但颜色无明显加深,当以硬质塑料片刮滴酸处时,无块状腐蚀物被刮下或明显腐蚀凹面,则样品耐酸腐蚀性合格;
[0080]
b)样块滴酸处颜色明显加深,如变成褐色或黑色等,用硬质塑料片刮滴酸处时,有块状腐蚀物刮落或明显凹面,则胶样耐酸腐蚀性为不合格。
[0081]
表1性能测试结果比对
[0082][0083][0084]
性能测试结果如表1所示,通过实施例1~3比较,调和聚氨酯丙烯酸树脂和二乙烯基单体的最佳比例为聚胺脂丙烯酸树脂45%、二乙烯基单体25%。通过在优化了聚氨酯丙烯酸树脂和二乙烯基单体的最佳比例的基础上,实施例4中再添加玻璃纤维进行优化,制得的紫外光固化色胶与终端产品贴合度更好,产品性能呈现最优。