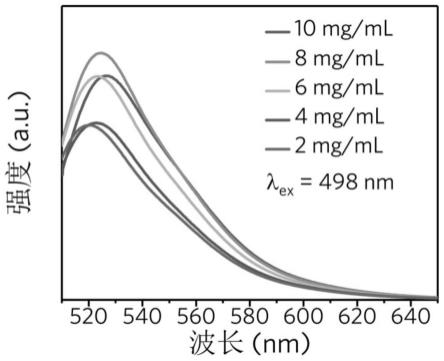
1.本发明涉及功能型发光材料技术领域,尤其涉及一种介孔氧化铝限域的窄带绿光碳点复合荧光粉的制备方法及其在液晶背光源中的应用。
背景技术:2.碳点是一种新型发光材料,具有光致发光可调、荧光寿命短、丰度高、制备方法简单、生物相容性好、毒性低的优点,能够快速、高效且环境友好地发展。目前,合成和设计高量子效率、高光稳定性和窄带的液态荧光碳点方面取得了很大进展。但由于聚集态碳点之间的共振能量转移和直接π
–
π相互作用,固态碳点荧光猝灭严重。为了解决固态碳点聚集诱导猝灭问题,通常将在合成过程中实现碳点的交联网络结构或者将碳点与其他材料复合后进行应用。然而,固态荧光碳点和许多碳点基复合材料容易受到光热氧化的影响,导致光热稳定性差,并且碳点基复合材料中,基质填充量高不可避免地导致固态荧光碳点的量子效率严重下降。
3.此外,wled(white led,白色发光二极管)背光源已经被广泛应用于液晶显示领域。,而绿色发射的cdse/zns量子点、稀土掺杂荧光粉和钙钛矿cspbbr3量子点是目前wled背光源的主流研究材料。然而上述几种绿光材料均具有一定的缺点,cd基量子点具有较高的毒性,且硫化物的稳定性较差。稀土元素的稀缺使掺杂的窄带绿光荧光粉不可持续发展。而cspbbr3钙钛矿量子点不稳定的量子效率、低热猝灭行为和铅对人体的毒害作用等缺点则限制了其商业应用。
4.因此,需要制备一种热稳定性好且不易猝灭的碳点复合材料,并期待将其用于液晶背光源。
技术实现要素:5.(一)要解决的技术问题
6.为了解决现有技术中存在的固态碳点聚集诱导猝灭,稳定性差,以及液晶背光源的主流绿光材料环境不友好且稳定性不佳的问题,本发明提供一种介孔氧化铝限域的窄带绿光碳点复合荧光粉的制备方法。目前碳点材料尚未应用在wled领域,因此,本发明还预期将制备得到的窄带绿光碳点复合材料用于液晶背光源,以获得性能稳定且无毒害,可持续的液晶背光源。
7.(二)技术方案
8.为了达到上述目的,第一方面,本发明提供一种介孔氧化铝限域的窄带绿光碳点复合荧光粉的制备方法,包括如下步骤:
9.s1:将窄带绿光碳点粉末加入去离子水中,进行超声分散,得到碳点溶液;
10.s2:将介孔氧化铝加入碳点溶液中,搅拌均匀,形成窄带绿光碳点与介孔氧化铝的混合液;
11.s3:将步骤s2得到的混合液进行离心,得到沉淀物;
12.s4:将步骤s3得到的沉淀物进行干燥,得到介孔氧化铝限域的窄带绿光碳点复合荧光粉。
13.如上所述的制备方法,优选地,所述窄带绿光碳点为水溶性硅烷化碳点。
14.如上所述的制备方法,优选地,步骤s1中,所述碳点溶液的浓度为0.5mg/ml~50mg/ml。
15.如上所述的制备方法,优选地,步骤s2中,所述介孔氧化铝的孔径为2nm~50nm。
16.如上所述的制备方法,优选地,步骤s2中,窄带绿光碳点与介孔氧化铝的质量比为0.05~1:1。
17.如上所述的制备方法,优选地,步骤s3中,得到沉淀物后,用去离子水对沉淀物洗涤3~5次,直到得到的上清液澄清且在紫外灯照射下不发光。
18.第二方面,本发明提供一种上述制备方法制备得到的介孔氧化铝限域的窄带绿光碳点复合荧光粉在激光投影仪、激光照明,以及液晶背光源的应用。
19.第三方面,本发明提供一种液晶背光源,包括蓝光芯片、以及涂覆在所述蓝光芯片上的介孔氧化铝限域的窄带绿光碳点复合荧光粉和红光荧光粉;所述窄带绿光碳点复合荧光粉、红光荧光粉与环氧树脂混合封装,然后涂覆于所述蓝光芯片,封装得到液晶背光源。
20.如上所述的液晶背光源,优选地,所述窄带绿光碳点复合荧光粉与所述红光荧光粉的质量比为1~7:1;所述窄带绿光碳点复合荧光粉与所述红光荧光粉的总量与环氧树脂的质量比为0.2~5:1,所述蓝光芯片发出的蓝光的波长为445nm~475nm。
21.如上所述的液晶背光源,优选地,完成封装的液晶背光源在60-100℃下进行固化。
22.(三)有益效果
23.本发明的有益效果是:
24.本发明的介孔氧化铝限域的窄带绿光碳点复合荧光粉的制备方法,操作简单,绿色环保,不产生任何污染,且大大节约了成本。
25.通过本发明的制备方法制备得到的窄带绿光碳点复合荧光粉,具有如下优点:1、半峰宽窄、发光量子效率高达70%;热稳定性好,在423k时表现出零热猝灭行为。2、光稳定性好,在蓝光长时间照射下能维持稳定窄带绿光发射。3、水稳定性好,将硅烷化碳点复合荧光粉长时间泡在超纯水中,荧光强度几乎不变。4、生物相容性好,细胞毒性低。
26.本发明的制备方法制备得到的窄带绿光碳点复合荧光粉用途广泛,能够替代传统荧光粉应用于大功率led,或者应用于激光投影仪、激光照明,或者封装成wled,用作液晶显示背光源的灯源。
27.本发明制备得到的窄带绿光碳点复合荧光粉应用于液晶显示背光源时,窄带绿光碳点复合荧光粉具有半峰宽可低于50nm,峰位在530nm,表现出零热猝灭行为,具有优异的光稳定性和水稳定性。窄带绿光碳点复合荧光粉结合红色荧光粉以及蓝光芯片封装得到的wled背光源,其色域覆盖率为ntsc的107%,所封装的液晶显示器呈现的画面色彩饱和度及还原度高,具有广阔的应用前景。
附图说明
28.图1为介孔氧化铝的孔径尺寸分布图;
29.图2为窄带绿光碳点的透射电镜图;
30.图3为实施例1-5制备得到的窄带绿光碳点复合荧光粉的荧光光谱图;
31.图4为实施例4制备得到的窄带绿光碳点复合荧光粉的温度依赖光谱图;
32.图5为实施例4制备得到的窄带绿光碳点复合荧光粉在460nm蓝光照射下在不同时间点收集的荧光光谱图;
33.图6为实施例4制备得到的窄带绿光碳点复合荧光粉泡在去离子水中不同时间点收集的荧光光谱图;
34.图7为实施例6封装的wled的电致发光光谱图;
35.图8为实施例6封装的wled背光源的cie图及计算的色域;
36.图9为对比例1中固态硅烷化碳点的荧光光谱;
37.图10为实施例4中的窄带绿光碳点复合荧光粉与对比例2中的商业绿光荧光粉b-sialon的发射光谱对比图;
38.图11为对比例1中固态硅烷化碳点的热重分析图;
39.图12为实施例4中硅烷化窄带绿光碳点复合荧光粉的热重分析图;
40.图13为对比例1中固态硅烷化碳点在460nm蓝光照射不同时间点收集的荧光光谱图;
41.图14为对比例1中固态硅烷化碳点的温度依赖光谱图。
具体实施方式
42.为了更好的解释本发明,以便于理解,下面结合附图,通过具体实施方式,对本发明作详细描述。
43.本发明提供一种介孔氧化铝限域的窄带绿光碳点复合荧光粉的制备方法,包括如下步骤:
44.s1:将窄带绿光碳点粉末加入去离子水中,进行超声分散,得到碳点溶液。碳点溶液的浓度过低或过高都会导致量子效率显著降低,并且导致光谱的峰位不适合进一步应用于液晶背光源显示、激光照明等光学器件领域。因此,本发明中碳点溶液浓度为0.5mg/ml~50mg/ml。
45.s2:介孔氧化铝加入过多会导致负载过剩而使得量子效率降低,过少则会导致硅烷化碳点剩余而导致浪费。因此,保持窄带绿光碳点与介孔氧化铝的质量比为0.05~1:1,将孔径为2nm~50nm的介孔氧化铝加入碳点溶液中,搅拌均匀,保证硅烷化碳点进入介孔氧化铝的孔道内部,形成窄带绿光碳点与介孔氧化铝的混合液。
46.介孔氧化铝具有高度均匀的孔道、较大的比表面、宽范围可调的孔径以及优异的热稳定性,其用作负载碳点的基质,能够增加碳点粒子之间的空间位阻,从而诱导碳点固态发光。此外,碳点以装载进介孔材料孔道的方式与介孔氧化铝复合,介孔氧化铝还对碳点起到表面保护的作用,提高了复合材料的热稳定性。
47.s3:将步骤s2得到的混合液进行离心,得到沉淀物,并洗涤3-5次。
48.s4:将步骤s3得到的沉淀物干燥,得到介孔氧化铝限域的窄带绿光碳点复合荧光粉。
49.步骤s3中,通过去离子水对沉淀物进行洗涤的目的是去除附着在介孔氧化铝表
面,即物理附着在介孔氧化铝的孔道之外的碳点材料。洗净的标准是最后一次洗涤得到的上清液澄清且在紫外灯照射下不发光。
50.步骤s4中,可以将沉淀物淀放入真空冷冻干燥机中12h~48h,或者放置在80-150℃的烘箱中干燥脱水。
51.本发明的制备方法简单、易重复、成本低且稳定性好、对环境友好。将窄带绿光碳点与介孔氧化铝共组装制备出的碳点复合荧光粉展现出窄带的绿光发射、量子效率高等特点,可以用作激光投影仪、激光照明,以及液晶背光源等。
52.实施例1
53.本实施例提供一种介孔氧化铝限域的窄带绿光碳点复合荧光粉的制备方法,包括如下步骤:
54.s1:将水溶性窄带绿光硅烷化碳点粉末加入去离子水中,超声分散,直至碳化硅碳点粉末完全溶解,获得浓度为2mg/ml的硅烷化碳点溶液。
55.s2:将介孔氧化铝加入步骤s1制备得到的硅烷化碳点溶液中,其中,硅烷化碳点与介孔氧化铝的质量比为0.06:1,搅拌均匀,使硅烷化碳点进入介孔氧化铝的孔道内部,形成硅烷化碳点与介孔氧化铝的混合液。
56.s3:将步骤s2得到的硅烷化碳点与介孔氧化铝的混合液进行离心,弃去上清液,留下沉淀物,将沉淀物用去离子水洗涤3次,直到上清液澄清,且365nm紫外灯照射上清液不发光后结束洗涤。
57.s4:将步骤s3清洗后的沉淀物放入真空冷冻干燥机中干燥24h,得到的窄带绿光硅烷化碳点复合荧光粉。
58.实施例2
59.本实施例提供一种介孔氧化铝限域的窄带绿光碳点复合荧光粉的制备方法,包括如下步骤:
60.s1:将水溶性窄带绿光硅烷化碳点粉末加入去离子水中,超声分散,直至碳化硅碳点粉末完全溶解,获得浓度为4mg/ml的硅烷化碳点溶液。
61.s2:将介孔氧化铝加入步骤s1制备得到的硅烷化碳点溶液中,其中,硅烷化碳点与介孔氧化铝的质量比为0.12:1,搅拌均匀,使硅烷化碳点进入介孔氧化铝的孔道内部,形成硅烷化碳点与介孔氧化铝的混合液。
62.s3:将步骤s2得到的硅烷化碳点与介孔氧化铝的混合液进行离心,弃去上清液,留下沉淀物,将沉淀物用去离子水洗涤3次,直到上清液澄清,且365nm紫外灯照射上清液不发光后结束洗涤。
63.s4:将步骤s3清洗后的沉淀物放入真空冷冻干燥机中干燥24h,得到的窄带绿光硅烷化碳点复合荧光粉。
64.实施例3
65.本实施例提供一种介孔氧化铝限域的窄带绿光碳点复合荧光粉的制备方法,包括如下步骤:
66.s1:将水溶性窄带绿光硅烷化碳点粉末加入去离子水中,超声分散,直至硅烷化碳点粉末完全溶解,获得浓度为6mg/ml的硅烷化碳点溶液。
67.s2:将介孔氧化铝加入步骤s1制备得到的硅烷化碳点溶液中,其中,硅烷化碳点与
介孔氧化铝的质量比为0.18:1,搅拌均匀,使硅烷化碳点进入介孔氧化铝的孔道内部,形成硅烷化碳点与介孔氧化铝的混合液。
68.s3:将步骤s2得到的硅烷化碳点与介孔氧化铝的混合液进行离心,弃去上清液,留下沉淀物,将沉淀物用去离子水洗涤3次,直到上清液澄清,且365nm紫外灯照射上清液不发光后结束洗涤。
69.s4:将步骤s3清洗后的沉淀物放入真空冷冻干燥机中干燥24h,得到的窄带绿光硅烷化碳点复合荧光粉。
70.实施例4
71.本实施例提供一种介孔氧化铝限域的窄带绿光碳点复合荧光粉的制备方法,与实施例1的区别在于,步骤s1中硅烷化碳点溶液的浓度为8mg/ml,步骤s2中硅烷化碳点与介孔氧化铝的质量比为0.24:1。
72.实施例5
73.本实施例提供一种介孔氧化铝限域的窄带绿光碳点复合荧光粉的制备方法,与实施例1的区别在于,步骤s1中硅烷化碳点溶液的浓度为10mg/ml,步骤s2中硅烷化碳点与介孔氧化铝的质量比为0.3:1。
74.实施例6
75.本实施例将实施例4制备得到的窄带绿光硅烷化碳点复合荧光粉用于液晶背光源,制备一种液晶背光源,具体包括如下步骤:
76.s1:将实施例4得到的窄带绿光硅烷化碳点复合荧光粉与商用红光荧光粉ksf:mn
4+
以2:1的质量比混合。然后将混合均匀的窄带绿光硅烷化碳点复合荧光粉和商用红光荧光粉ksf:mn
4+
与环氧树脂混合封装胶以1:1的质量比通过搅拌至完全混合均匀。
77.s2:将步骤s1制备得到的粉胶混合物涂覆ingan蓝光led芯片(λ=460nm)上,置于80℃干燥箱中固化2h,得到wled。
78.s3:将封装好的wled背光源替换掉液晶显示器中的商用白光灯条,将各组件组装成液晶显示器。
79.对比例1
80.本对比例提供一种实施例1-5中所用的固态硅烷化碳点。
81.对比例2
82.本对比例提供一种商业绿光荧光粉β-sialon。
83.对上述实施例以及对比例中的产物进行性能测试,得到如下结果以及分析:
84.由dft模型计算的实施例1-5中所用的介孔氧化铝的孔径,如图1所示,介孔氧化铝的孔径为11.15nm,大于碳点的粒径,可以作为装载碳点的基质。
85.通过透射电镜拍摄实施例1-5所用的硅烷化碳点,如图2所示,硅烷化碳点具有分散性好、颗粒分布均匀、呈类球型的特点,平均粒径为3.2nm,其粒径比上面所述的介孔氧化铝的孔径小,可进入介孔氧化铝的孔道。
86.将实施例1-5制备的介孔氧化铝限域的窄带绿光硅烷化碳点复合荧光粉分别进行荧光光谱测试,得到图3所示的光谱,通过图3可知,各个实施例中的荧光光谱皆表现出窄带绿光性质,半峰宽窄,满足背光光源对绿色发光材料的要求,有望替换液晶背光源中的绿光材料。
87.将实施例1-5制备的介孔氧化铝限域的窄带绿光硅烷化碳点复合荧光粉分别进行热稳定性测试,结果证明,各个实施例的介孔氧化铝限域的窄带绿光硅烷化碳点复合荧光粉皆表现出良好的热稳定性。其中,以实施例4制备的介孔氧化铝限域的窄带绿光硅烷化碳点复合荧光粉在298k-473k下的温度依赖光谱为例,得到图4,通过图4可知,介孔氧化铝限域的窄带绿光硅烷化碳点复合荧光粉在423k下的热稳保留相比初始荧光强度为104.1%,是一种零热猝灭行为,热稳性较好。
88.将实施例1-5分别制备的介孔氧化铝限域的窄带绿光硅烷化碳点复合荧光粉分别进行光稳定性测试,结果证明,各个实施例的介孔氧化铝限域的窄带绿光硅烷化碳点复合荧光粉皆表现出良好的光稳定性。其中,以实施例4制备的介孔氧化铝限域的窄带绿光硅烷化碳点复合荧光粉在460nm蓝光照射不同时间点(0h、12h、24h、36h、48h和60h)的光谱为例,得到图5,通过图5可知,介孔氧化铝限域的窄带绿光硅烷化碳点复合荧光粉在蓝光长时间照射下能维持稳定窄带绿光发射,具有较好的光稳定性。
89.将实施例1-5制备的介孔氧化铝限域的窄带绿光硅烷化碳点复合荧光粉分别进行水稳定性测试,结果证明,各个实施例的介孔氧化铝限域的窄带绿光硅烷化碳点复合荧光粉皆表现出优异的水稳定性。其中,以实施例4制备的介孔氧化铝限域的窄带绿光硅烷化碳点复合荧光粉泡在纯水中不同时间点(0d、2d、4d、6d、8d和10d)的光谱为例,得到图6,如通过图6可知,介孔氧化铝限域的窄带绿光硅烷化碳点复合荧光粉长时间泡在超纯水中,其荧光强度几乎不变,具有较好的水稳定性。
90.对实施例6封装的wled进行相关电致发光光谱、流明效率、色温的测试,得到图7。通过图7可知,wled的流明效率为117.43lm/w,远高于普通产品中的60-70lm/w,能够呈现出更加清晰的图像;wled的色温cct为5803k,证明制备的wled发出了冷白光,满足液晶背光源的要求;wled的色坐标(0.3243,0.3410)代表wled发出的是白光,满足液晶背光源的颜色要求。
91.对实施例6封装的wled背光源进行色域计算,得到图8,通过图8可知,以介孔氧化铝限域的窄带绿光硅烷化碳点复合荧光粉为绿色发光材料的wled背光源表现出色域覆盖率为107%ntsc的宽色域,因此能够呈现出色彩饱和度高、画面生动的图像,适合大规模应用在液晶背光源中。
92.对对比例1的固态硅烷化碳点进行荧光光谱测试,得到图9所示的光谱,通过图9可知,其半峰宽及发射峰位并不适合用于液晶背光源。
93.对实施例4中制备得到的介孔氧化铝限域的窄带绿光硅烷化碳点复合荧光粉(si-cds@mas)以及对比例2的商业绿光荧光粉β-sialon分别进行发射光谱测试,得到图10所示的对比图。通过图10可知,介孔氧化铝限域的窄带绿光硅烷化碳点复合荧光粉具有与商用用荧光粉相媲美的光学性质。
94.对对比例1的固态硅烷化碳点以及实施例4制备得到的介孔氧化铝限域的窄带绿光硅烷化碳点复合荧光粉分别进行热重分析,得到图11以及图12。通过图11可知,固态硅烷化碳点的热重分析图显示其在低于150℃的温度下脱水和部分碳化,加热到451℃后完全分解,重量仅保留61.14%。而实施例4中的介孔氧化铝限域的窄带绿光硅烷化碳点复合荧光粉的热重分析图显示其即使加热到800℃,依然保持99.92%的重量,表明其良好的热稳定性。
95.对对比例1的固态硅烷化碳点进行光稳定性测试,以固态硅烷化碳点在460nm蓝光照射不同时间点(0h、12h、24h、36h、48h和60h)的光谱为例,得到图13。通过图13可知,固态硅烷化碳点在蓝光长时间照射下不能维持稳定的窄带绿光发射,光稳定性较差。
96.对对比例1的固态硅烷化碳点进行热稳定性测试,以固态硅烷化碳点在298k-473k下的温度依赖光谱为例,得到图14。通过图14可知,固态硅烷化碳点的热稳性较差,猝灭严重。
97.以上所述,仅是本发明的较佳实施例而已,并非是对本发明做其它形式的限制,任何本领域技术人员可以利用上述公开的技术内容加以变更或改型为等同变化的等效实施例。但是凡是未脱离本发明技术方案内容,依据本发明的技术实质对以上实施例所作的任何简单修改、等同变化与改型,仍属于本发明技术方案的保护范围。