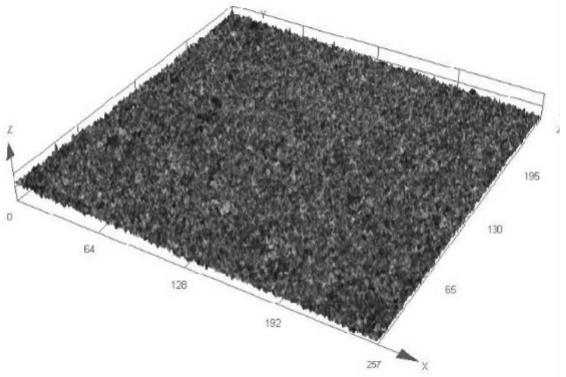
1.本发明涉及热传导材料领域,具体涉及一种高强度高导热低粗糙度石墨烯/铜复合材料及其制备方法。
背景技术:2.随着集成电路等电子元器件的特征尺寸逐渐减小,电子元器件的耗散功率和发热量越来越大,因此,电子元器件的导热散热能力成为亟需解决的关键问题。
3.铜基复合材料由于具有良好的导热性能与导电性能,并且抗磨损能力及力学性能优异,在结构材料、电子设备和航天领域等方面展现了广泛的应用。
4.目前,石墨烯金属基复合材料的制备主要有粉末冶金法、水热法、化学气相沉积法和电化学沉积法等。粉末冶金法操作简单,但模具单一,可控性较差;水热法设备要求高,技术难度大;化学气相沉积法制备的镀层虽然致密均匀,但镀层较薄,不利于实际应用。电化学沉积法是在配制的特定比例的溶液中,通过氧化还原反应制备复合材料的方法,该方法工艺简单,成本较低且产品质量较好,但在制备过程中由于极板的选取、工艺参数的调节以及电沉积液成分的配比等问题会直接影响制备的复合材料的组织与性能。现有的工艺配方及参数调控制备的石墨烯/铜复合材料的晶粒粗大,容易产生开裂和翘曲等问题,且性能相对纯铜来说没有明显的提升。
技术实现要素:5.为了解决背景技术中指出的技术问题,本发明提供了一种具有高导热及力学性能优异的低粗糙度复合材料及其制备方法。本发明的目的在于提供一种配比合理、绿色环保、节约成本、镀层厚度可控的石墨烯/铜复合材料的电沉积溶液,以及所需要的工艺方法和参数,且经过合适的轧制退火工艺后,获得一种性能优良的石墨烯/铜复合材料。
6.本发明的技术解决方案是:
7.电沉积制备石墨烯/铜复合材料,实施如下:
8.(1)配制石墨烯/铜复合材料的电沉积液,按照质量浓度的组成为:
9.电沉积液a:五水合硫酸铜60~240g/l,2-巯基苯并咪唑40~80mg/l,cl-(由盐酸提供)40~80mg/l,石墨烯(gr)0~0.45g/l,余量为去离子水。
10.电沉积液b:五水合硫酸铜60~240g/l,健那绿(jgb)10~30mg/l,石墨烯(gr)0~0.45g/l,余量为去离子水。
11.电沉积溶液的配制方法为:将石墨烯溶液进行超声分散,再进行高速匀质机分散,速度为5000r/min;分别加入2-巯基苯并咪唑和cl-与健那绿(jgb)进行机械搅拌后和五水合硫酸铜溶液混合,然后采用电动搅拌机搅拌及高速匀质机分散,得到石墨烯/铜-2-巯基苯并咪唑/cl-和石墨烯/铜-健那绿复合电沉积溶液。
12.其中,2-巯基苯并咪唑在酸性镀铜的低ph值条件下,氯化物会以高覆盖率吸附在
阴极铜上,持续向表面位置移动,吸附的氯离子并不会妨碍铜的沉积,甚至可以吸引铜离子并作为电子转移的通道,加速电化学反应作用,一定程度上有利于获得更致密的铜层;此外,cl-能与2-巯基苯并咪唑进行协同作用,优化了提高复合箔的致密性及表面粗糙度。
13.jgb能有效提高石墨烯的分散性减少团聚,且jgb分子较高的能隙和在阴极表面的吸附,使得铜离子沉积需要更高的过电位,促进形核并细化晶粒,优化了复合箔的沉积率及表面粗糙度。
14.(2)使用金相砂纸打磨阳极(铜板)与阴极(钛板),去掉油污及氧化膜,后用10%的稀盐酸溶液对极板进行活化处理,活化时长5~20min。
15.(3)使用配制好的沉积液进行沉积,以钛板为基板,采用脉冲电沉积法,先在含2-巯基苯并咪唑和cl-的沉积液中沉积10min,随后再在含健那绿的沉积液中沉积10min,循环两次,共沉积40min。
16.工艺参数为:脉冲宽度比为3:1~6:1(正/反),脉冲电压为1~2.5v/0.5~1v,脉冲电流频率500hz。工艺环境为:沉积液温度25~45℃,沉积液ph为1.0~3.0。沉积液温度、ph、电流密度等参数的改变,均会影响材料的沉积速率及质量。
17.(4)将制备的石墨烯/铜复合材料进行异步轧制及再结晶退火处理,工艺条件为:异速比1.0~2.0,最终变形量10~30%,退火温度150~300℃,退火时间15~120min。
18.本发明使用的硫酸铜-石墨烯复合沉积液成分配比合理且可循环使用,不仅节约成本,而且绿色环保;用该沉积液制备的石墨烯/铜复合材料表面平整光滑,组织均匀致密。
19.采用交替电沉积工艺,复合材料可形成具有独特的二维结构和优良的性能的层状结构,对石墨烯增强复合材料的性能有更好的改善效果。
20.异步轧制能有效降低铜的再结晶温度,有利于退火过程中的形核,且能形成剪切带,细化晶粒,提高材料的力学性能,合适的退火工艺参数能有效提高复合材料的综合性能。
21.本发明的主要优点是:
22.(1)本发明提供了一种石墨烯/铜复合材料的制备方法,即交替脉冲电沉积+异步轧制+再结晶退火,工艺简单,成本低,电解液可反复使用,且制备的复合材料平整致密,力学性能,导热性能及表面粗糙度优异。
23.(2)本发明提供了一种新型的沉积液配方:2-巯基苯并咪唑和健那绿的加入可以有效改善基体与增强相之间的润湿性,提高结合强度;同时有利于改善沉积层表面质量,提高镀层表面平整度。本发明制备的复合材料应用于热传导材料领域,提高材料的散热效率,此外,脉冲电沉积技术还可应用于制作电子元器件散热膜、散热线等,如电子设备内部散热板,gpu芯片等。
24.(3)本发明提供了异步轧制及再结晶退火处理工艺,能有效优化提高材料的抗拉强度,导热及表面粗糙度,该复合镀层的抗拉强度最高可达524mpa,热导率最高可以达到1180w/m
·
k,表面粗糙度最好可达0.3
±
0.1μm,更好的满足了热传导领域的需求。
附图说明:
25.图1为本发明实施例3沉积态的石墨烯/铜复合材料的表面形貌三维图;
26.图2为本发明实施例3异步轧制+退火后的石墨烯/铜复合材料的表面形貌三维图;
27.图3为本发明实施例3沉积态的石墨烯/铜复合材料的表面扫描电镜图。
具体实施方式
28.本发明下面结合实施例作进一步详述:这些实施仅用于说明本发明而不用于限制发明范围。
29.实施例1
30.石墨烯/铜复合电沉积液的成分配比为:
31.电沉积液a:五水合硫酸铜60g/l,2-巯基苯并咪唑40mg/l,cl-(由盐酸提供)40mg/l,石墨烯(gr)0.05g/l,余量为去离子水。
32.电沉积溶液的配制方法为:将石墨烯溶液进行超声分散,再进行高速匀质机分散,速度为5000r/min;加入2-巯基苯并咪唑和cl-进行机械搅拌后和五水合硫酸铜溶液混合,然后采用电动搅拌机搅拌及高速匀质机分散,得到石墨烯/铜-2-巯基苯并咪唑/cl-复合电沉积溶液。
33.电沉积液b:五水合硫酸铜60g/l,健那绿(jgb)10mg/l,石墨烯(gr)
34.0.05g/l,余量为去离子水。
35.电沉积溶液的配制方法为:将石墨烯溶液进行超声分散,再进行高速匀质机分散,速度为5000r/min;加入健那绿(jgb)进行机械搅拌后和五水合硫酸铜溶液混合,然后采用电动搅拌机搅拌及高速匀质机分散,得到石墨烯/铜-健那绿复合电沉积溶液。
36.使用金相砂纸打磨阳极(铜板)与阴极(钛板),去掉油污及氧化膜,后用10%的稀盐酸溶液对极板进行活化处理,活化时长10min。
37.采用脉冲电沉积法,先在含2-巯基苯并咪唑和cl-的沉积液中沉积10min,随后再在含jgb的沉积液中沉积10min,循环两次,共沉积40min。沉积液的工艺环境为:温度25℃,ph=3;电沉积工艺参数为:脉冲宽度比为3:1(正/反),脉冲电压为2.5v/0.6v,脉冲电流频率500hz。这种情况以及该工艺条件下所制备的沉积层厚度均匀,厚度约为20μm,表面有少量凸起颗粒,平整性一般,致密性一般,表面粗糙度2.8
±
0.1μm;轧制退火的工艺参数为:异速比1.2,最终变形量为10%,退火温度150℃,退火时间15min,所得复合镀层抗拉强度为341mpa,热导率为440w/m
·
k,表面粗糙度1.2
±
0.1μm。
38.实施例2
39.电沉积液a:五水合硫酸铜100g/l,2-巯基苯并咪唑50mg/l,cl-(由盐酸提供)50mg/l,石墨烯(gr)0.15g/l,余量为去离子水。
40.电沉积液b:五水合硫酸铜100g/l,健那绿(jgb)20mg/l,石墨烯(gr)0.15g/l,余量为去离子水。
41.使用金相砂纸打磨阳极(铜板)与阴极(钛板),去掉油污及氧化膜,后用10%的稀盐酸溶液对极板进行活化处理,活化时长10min。
42.采用脉冲电沉积法,先在含2-巯基苯并咪唑和cl-的沉积液中沉积10min,随后再在含jgb的沉积液中沉积10min,循环两次,共沉积40min。沉积液工艺环境为:沉积液温度30℃,沉积液ph为2.5。电沉积工艺参数为:脉冲宽度比为4:1(正/反),脉冲电压为2.5v/0.6v,脉冲电流频率500hz。这种情况以及该工艺条件下所制备的沉积层厚度均匀,厚度约为30μm,表面有少量凸起颗粒,平整性一般,致密性一般,表面粗糙度2.2
±
0.1μm。轧制退火的工
艺参数为:异速比1.4,最终变形量为30%,退火温度200℃,退火时间30min,所得复合镀层抗拉强度为466mpa,热导率为720w/m
·
k,表面粗糙度0.9
±
0.1μm。
43.石墨烯/铜复合沉积液的配制方法同实施例1。
44.实施例3
45.电沉积液a:五水合硫酸铜140g/l,2-巯基苯并咪唑60mg/l,cl-(由盐酸提供)60mg/l,石墨烯(gr)0.25g/l,余量为去离子水。
46.电沉积液b:五水合硫酸铜140g/l,健那绿(jgb)25mg/l,石墨烯(gr)0.25g/l,余量为去离子水。
47.使用金相砂纸打磨阳极(铜板)与阴极(钛板),去掉油污及氧化膜,后用10%的稀盐酸溶液对极板进行活化处理,活化时长10min。
48.采用脉冲电沉积法,先在含2-巯基苯并咪唑和cl-的沉积液中沉积10min,随后再在含jgb的沉积液中沉积10min,循环两次,共沉积40min。沉积液工艺环境为:沉积液温度30℃,沉积液ph为2.0。电沉积工艺参数为:脉冲宽度比为5:1(正/反),脉冲电压为2.5v/0.6v,脉冲电流频率500hz。这种情况以及该工艺条件下所制备的沉积层厚度均匀,厚度约为50μm,表面光滑,基本无凸起颗粒,致密性良好,表面粗糙度0.8
±
0.1μm。轧制退火的工艺参数为:异速比1.6,最终变形量为30%,退火温度250℃,退火时间45min,所得复合镀层抗拉强度为509mpa,热导率可以达到1180w/m
·
k,表面粗糙度0.3
±
0.1μm。
49.石墨烯/铜复合沉积液的配制方法同实施例1。
50.实施例4
51.电沉积液a:五水合硫酸铜180g/l,2-巯基苯并咪唑70mg/l,cl-(由盐酸提供)70mg/l,石墨烯(gr)0.35g/l,余量为去离子水。
52.电沉积液b:五水合硫酸铜180g/l,健那绿(jgb)30mg/l,石墨烯(gr)0.35g/l,余量为去离子水。
53.使用金相砂纸打磨阳极(铜板)与阴极(钛板),去掉油污及氧化膜,后用10%的稀盐酸溶液对极板进行活化处理,活化时长10min。
54.采用脉冲电沉积法,先在含2-巯基苯并咪唑和cl-的沉积液中沉积10min,随后再在含jgb的沉积液中沉积10min,循环两次,共沉积40min。沉积液工艺环境为:沉积液温度35℃,沉积液ph为1.5。电沉积工艺参数为:脉冲宽度比为6:1(正/反),脉冲电压为2.5v/0.6v,脉冲电流频率500hz。这种情况以及该工艺条件下所制备的沉积层厚度均匀,厚度约为60μm,表面有较少凸起颗粒,平整性一般,致密性良好,表面粗糙度1.2
±
0.1μm。轧制退火的工艺参数为:异速比1.8,最终变形量为30%,退火温度300℃,退火时间60min,所得复合镀层抗拉强度为483mpa,热导率为850w/m
·
k,表面粗糙度0.5
±
0.1μm。
55.石墨烯/铜复合沉积液的配制方法同实施例1。
56.实施例5
57.电沉积液a:五水合硫酸铜220g/l,2-巯基苯并咪唑80mg/l,cl-(由盐酸提供)80mg/l,石墨烯(gr)0.45g/l,余量为去离子水。
58.电沉积液b:五水合硫酸铜220g/l,健那绿(jgb)30mg/l,石墨烯(gr)0.45g/l,余量为去离子水。
59.使用金相砂纸打磨阳极(铜板)与阴极(钛板),去掉油污及氧化膜,后用10%的稀
盐酸溶液对极板进行活化处理,活化时长10min。
60.采用脉冲电沉积法,先在含2-巯基苯并咪唑和cl-的沉积液中沉积10min,随后再在含jgb的沉积液中沉积10min,循环两次,共沉积40min。沉积液工艺环境为:沉积液温度35℃,沉积液ph为1.0。电沉积工艺参数为:脉冲宽度比为6:1(正/反),脉冲电压为2.5v/0.6v,脉冲电流频率500hz。这种情况以及该工艺条件下所制备的沉积层厚度均匀,厚度约为50μm,表面良好有较少凸起颗粒,平整性良好一般,致密性良好一般,表面粗糙度1.0
±
0.1μm。轧制退火的工艺参数为:异速比2.0,最终变形量为30%,退火温度300℃,退火时间90min,所得复合镀层抗拉强度为524mpa,热导率为845w/m
·
k,表面粗糙度0.5
±
0.1μm。
61.石墨烯/铜复合沉积液的配制方法同实施例1。
62.对比实施例1
63.电沉积液a:五水合硫酸铜60g/l,2-巯基苯并咪唑40mg/l,cl-(由盐酸提供)40mg/l,余量为去离子水。
64.电沉积液b:五水合硫酸铜60g/l,健那绿(jgb)10mg/l,余量为去离子水。
65.使用金相砂纸打磨阳极(铜板)与阴极(钛板),去掉油污及氧化膜,后用10%的稀盐酸溶液对极板进行活化处理,活化时长10min。
66.采用脉冲电沉积法,先在含2-巯基苯并咪唑和cl-的沉积液中沉积10min,随后再在含jgb的沉积液中沉积10min,循环两次,共沉积40min。电沉积工艺环境为:沉积液温度25℃,沉积液ph为3.0。电沉积工艺参数为:脉冲宽度比为3:1(正/反),脉冲电压为2.5v/0.6v,脉冲电流频率500hz。这种情况以及该工艺条件下所制备的沉积层厚度均匀,厚度约为4020μm,表面较光滑,有较少凸起颗粒,致密性一般,表面粗糙度1.9
±
0.1μm。轧制退火的工艺参数为:异速比1.2,最终变形量为10%,退火温度150℃,退火时间15min,所得复合镀层抗拉强度为298mpa,热导率为280w/m
·
k,表面粗糙度0.8
±
0.1μm。
67.对比实施例2
68.电沉积液a:五水合硫酸铜100g/l,2-巯基苯并咪唑50mg/l,cl-(由盐酸提供)50mg/l,石墨烯(gr)0.15g/l,余量为去离子水。
69.使用金相砂纸打磨阳极(铜板)与阴极(钛板),去掉油污及氧化膜,后用10%的稀盐酸溶液对极板进行活化处理,活化时长10min。
70.采用脉冲电沉积法,在cuso
4-石墨烯-2-巯基苯并咪唑和cl-沉积液中沉积40min。沉积液工艺环境为:沉积液温度30℃,沉积液ph为2.5。电沉积工艺参数为:脉冲宽度比为4:1(正/反),脉冲电压为2.5v/0.6v,脉冲电流频率500hz这种情况以及该工艺条件下所制备的沉积层厚度均匀,厚度约为30μm,表面光滑,基本无凸起颗粒,致密性良好,表面粗糙度1.4
±
0.1μm。轧制退火的工艺参数为:异速比1.4,最终变形量为30%,退火温度200℃,退火时间30min,所得复合镀层抗拉强度为433mpa,热导率为734w/m
·
k,表面粗糙度0.7
±
0.1μm。
71.对比实施例3
72.电沉积液b:五水合硫酸铜140g/l,健那绿(jgb)25mg/l,石墨烯(gr)0.25g/l,余量为去离子水。
73.使用金相砂纸打磨阳极(铜板)与阴极(钛板),去掉油污及氧化膜,后用10%的稀盐酸溶液对极板进行活化处理,活化时长10min。
74.采用脉冲电沉积法,在cuso
4-石墨烯-jgb沉积液中沉积40min。沉积液工艺环境为:沉积液温度30℃,沉积液ph为2.0。电沉积工艺参数为:脉冲宽度比为5:1(正/反),脉冲电压为2.5v/0.6v,脉冲电流频率500hz。这种情况以及该工艺条件下所制备的沉积层厚度均匀,厚度约为50μm,表面光滑,基本无凸起颗粒,致密性良好,表面粗糙度1.1
±
0.1μm。轧制退火的工艺参数为:异速比1.6,最终变形量为30%,退火温度250℃,退火时间120min,所得复合镀层抗拉强度为495mpa,热导率为697w/m
·
k,表面粗糙度0.5
±
0.1μm。
75.对比实施例4
76.电沉积液a:五水合硫酸铜180g/l,2-巯基苯并咪唑70mg/l,cl-(由盐酸提供)70mg/l,石墨烯(gr)0.35g/l,余量为去离子水。
77.电沉积液b:五水合硫酸铜180g/l,健那绿(jgb)30mg/l,石墨烯(gr)0.35g/l,余量为去离子水。
78.使用金相砂纸打磨阳极(铜板)与阴极(钛板),去掉油污及氧化膜,后用10%的稀盐酸溶液对极板进行活化处理,活化时长10min。
79.采用脉冲电沉积法,先在含2-巯基苯并咪唑和cl-的沉积液中沉积10min,随后再在含jgb的沉积液中沉积10min,循环两次,共沉积40min。沉积液工艺环境为:沉积液温度35℃,沉积液ph为1.5。电沉积工艺参数为:脉冲宽度比为6:1(正/反),脉冲电压为2.5v/0.6v,脉冲电流频率500hz。这种情况以及该工艺条件下所制备的沉积层厚度均匀,厚度约为60μm,表面有较少凸起颗粒,平整性一般,致密性良好。所得复合镀层抗拉强度为410mpa,热导率为750w/m
·
k,表面粗糙度1.2
±
0.1μm。
80.石墨烯/铜复合沉积液的配制方法同实施例1。
81.上述实例均为本发明优选的实施方式,但本发明并不限于上述实施方式,在不背离本发明的实质内容的情况下,本领域技术人员能够做出的任何显而易见的改进、替换或变形均属于本发明的保护范围。